Modern Rodding TECH
InTheGarageMedia.com
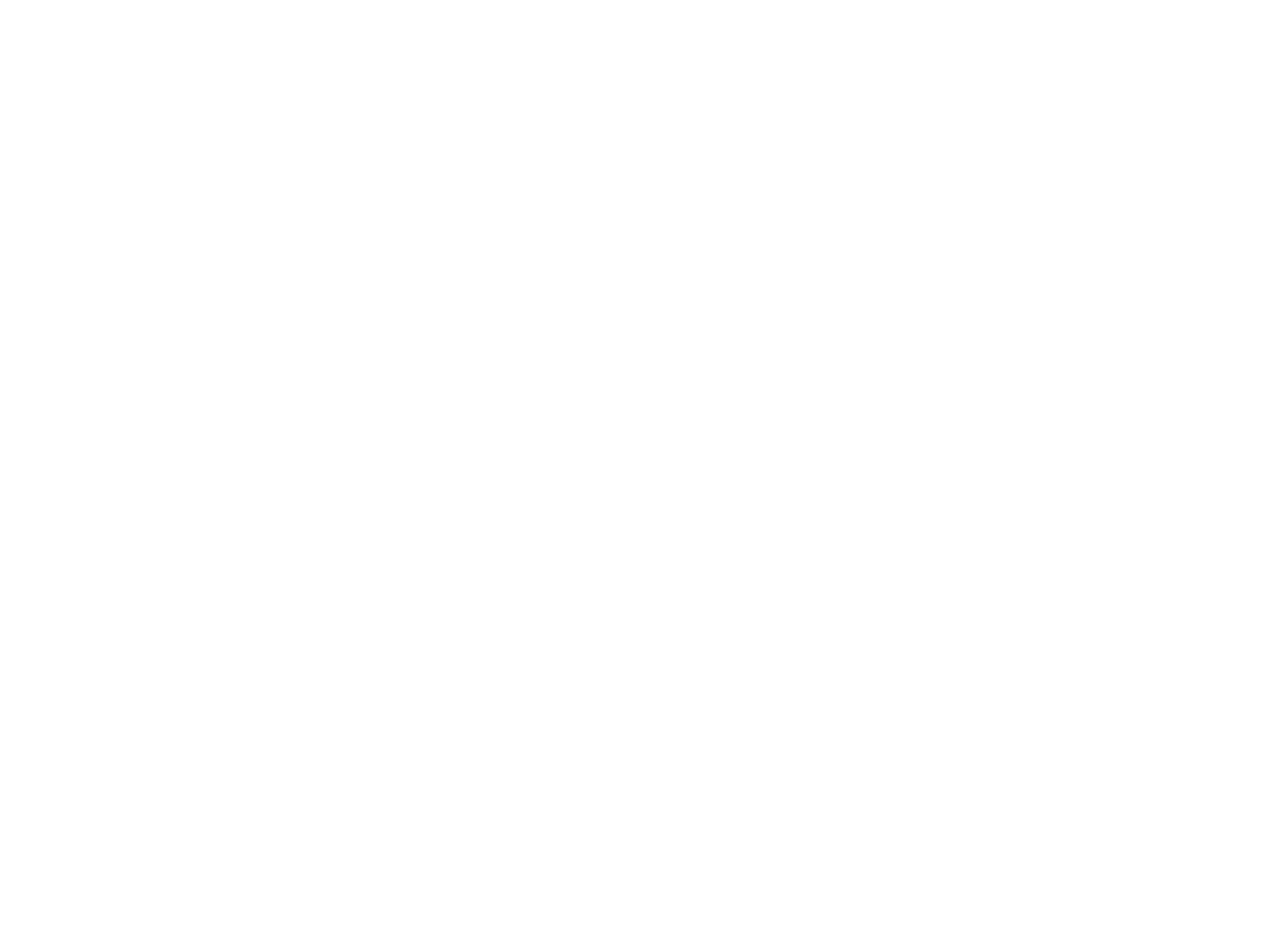
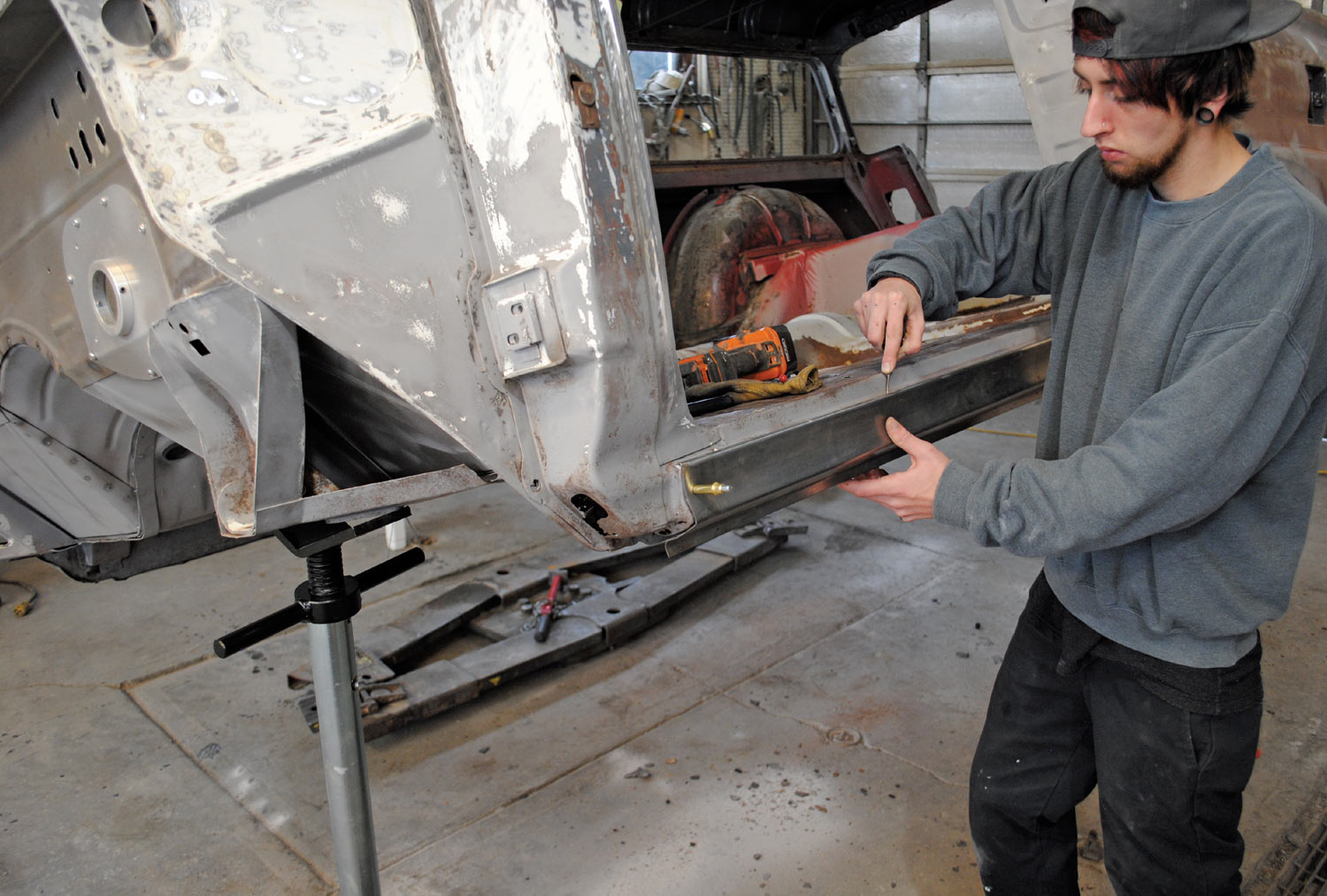
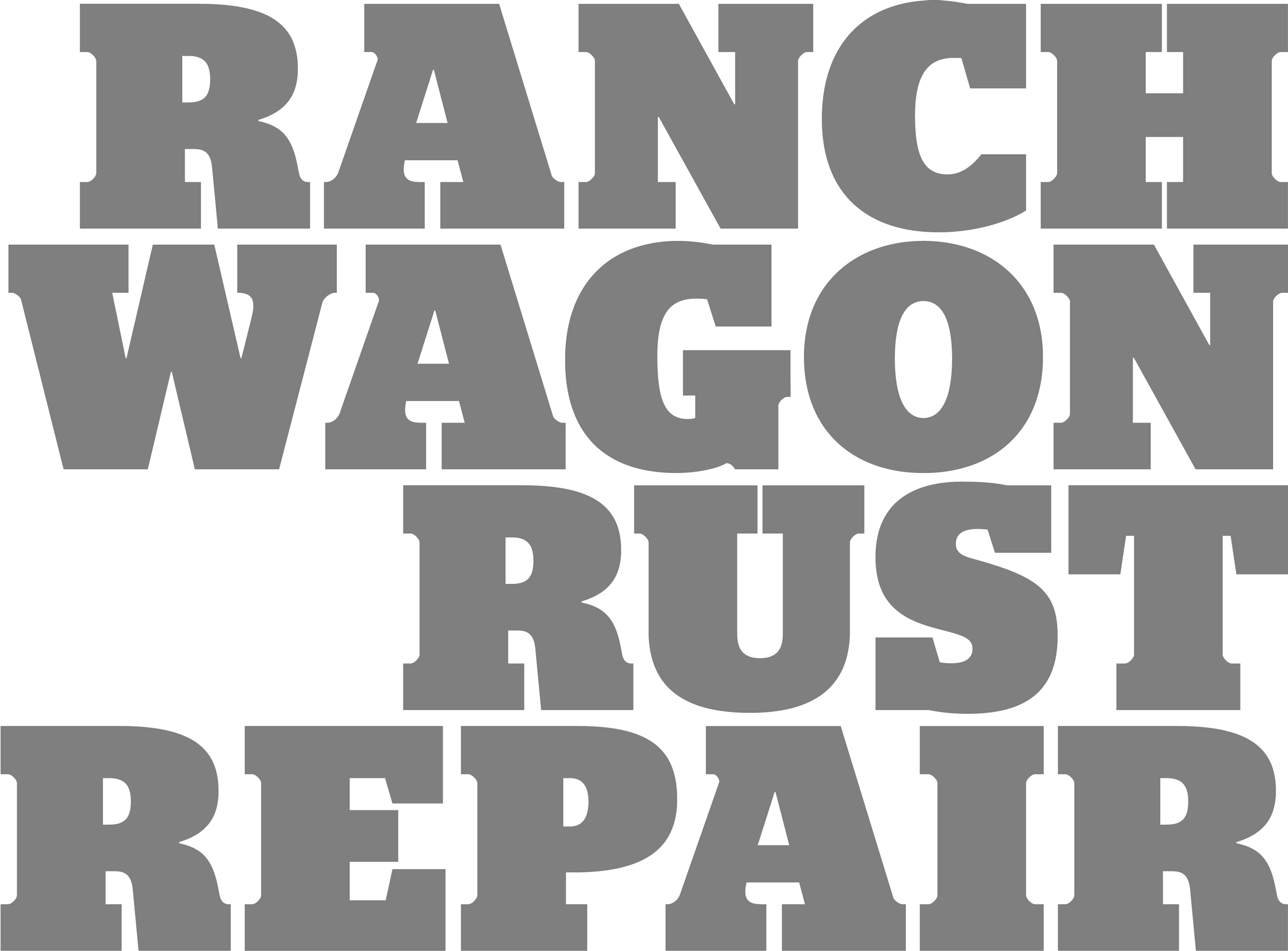

et’s take a step back to a time when the ’57 Ford Del Rio station wagon shown here rolled off the end of the assembly line. Because it was 1 of 46,105 examples of a Deluxe two-door Ranch Wagon with Fairlane trim that was built that year, it had a base price of around $2,500. To put things in perspective, the average family income that year was $5,000 and the average price for a home was $12,220.
We can only imagine how happy the beautiful, new, shiny station wagon made its original owners. But eventually, the Ford’s useful life was over; the stylish yet practical family hauler lost its luster, eventually becoming what most people considered to be just another old used car. And like most old cars of its age, the ’57 had suffered the ravages of time and needed a fair amount of TLC, but Colin and Sue Radford saw it as a diamond in the rough. A station wagon would be perfect for hauling their grandkids around, going to swap meets, and making the family’s yearly trips to the Bonneville Salt Flats—and just like that a new project was born.
Collaborating with Colin on the wagon from the beginning has been their grandson, Tate. So far, the duo has updated the chassis with suspension components from Art Morrison Enterprises, brakes from Wilwood, and slipped in a Ford Performance Coyote V-8 and Gearstar 4R70W transmission in the space a Y-block and Ford-O-Matic once occupied.
With the chassis work completed, the body was lifted off the frame and mounted on a rotisserie to provide access to all the areas that required repair and Colin and Tate went to work. The worst damage was rust in the rocker panel below the driver door. Not only was the outer skin rusted, but the inner structure was destroyed and would have to be replaced as well. Fortunately, the floor supports were in good condition and will remain in place.
To repair the rusted rocker panel, a new inner portion was fabricated from sheetmetal and formed to fit in a brake. The replacement piece would be welded to the floor braces and the sill below the door opening. With the inner structure repaired, a replacement outer panel was trimmed to fit and welded in place. To ensure no moisture could infiltrate the repaired rocker panel and cause more rust, all the joints received a bead of panel adhesive as they were installed.
While the driver side rocker panel required replacement, the passenger side was in relatively good shape and needed only minor repair. With all the damage to the rocker panels resolved, the next chore was to repair the bottom of the left quarter-panel behind the wheel opening. Again, all the rotted metal was cut away, which left a larger hole to patch than it first appeared, but a two-piece patch panel cured that problem.
This wagon is destined to be driven, so every effort has been made to make the Ford fit for what lies ahead. To that end, the bottom of the body was prepped and covered in epoxy primer followed by an application of Raptor pickup bedliner and then a topcoat of single-stage black urethane gloss paint was applied.
With the rusted areas repaired the body was reunited with the frame that was previously covered in gloss black urethane. Next Team Radford will turn its attention to finish bodywork and paint, which means the Del Rio Ranch Wagon is well on its way to its new life—and with all the improvements that new life will be even better than the first.
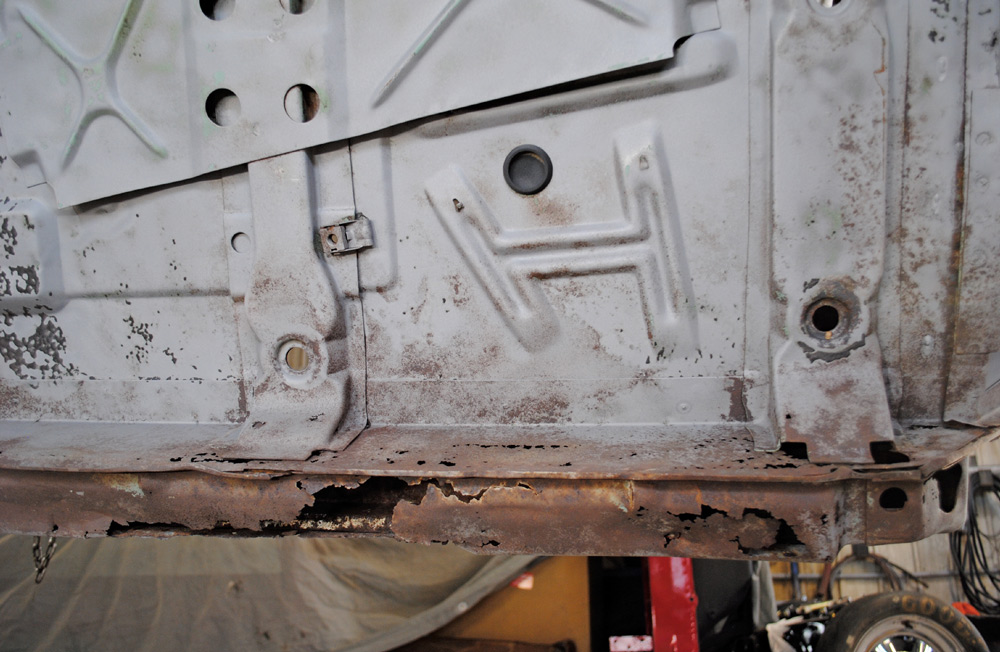

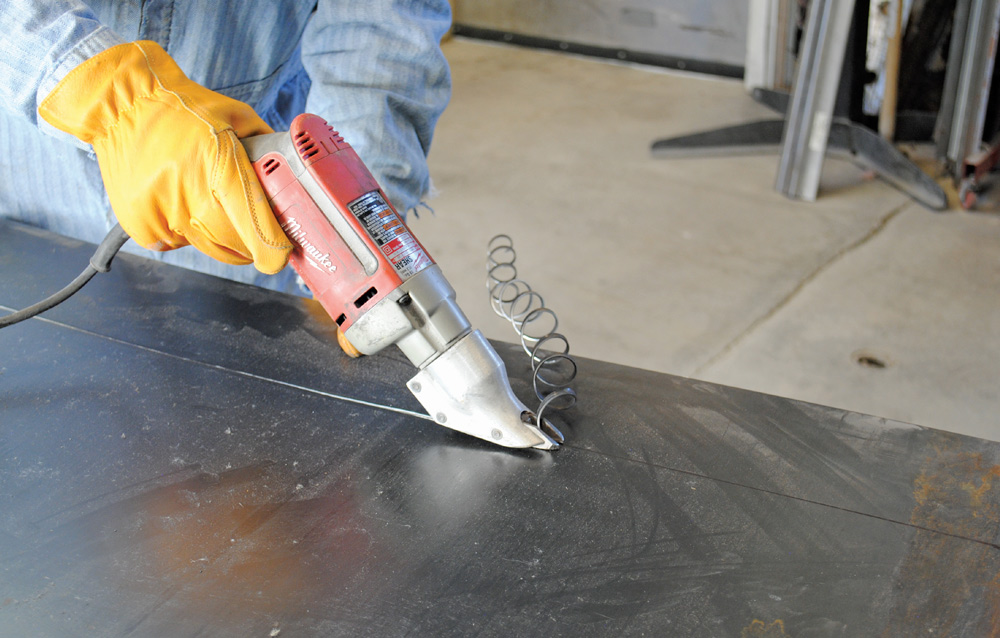
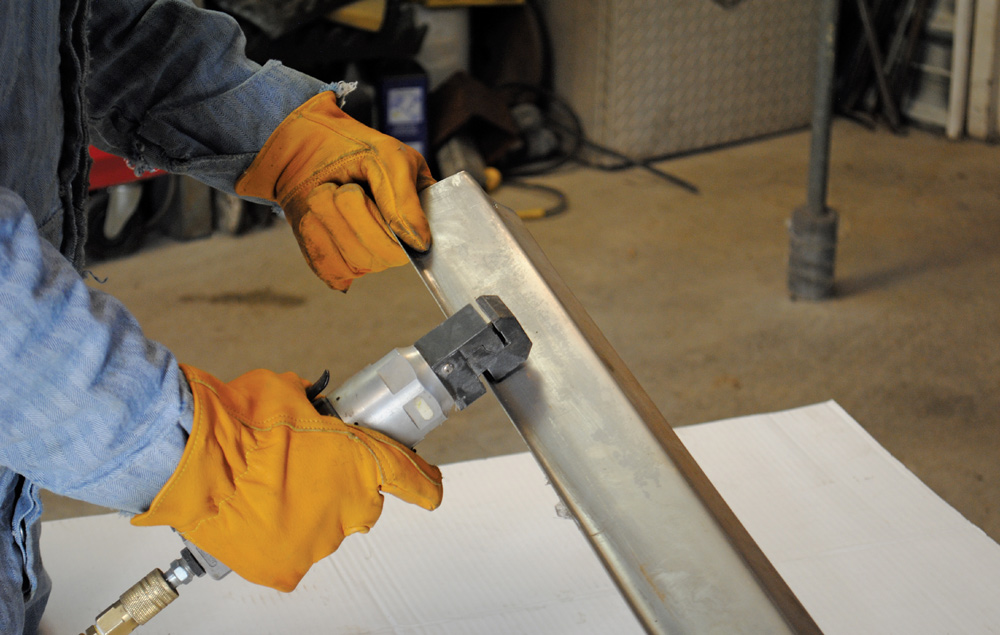
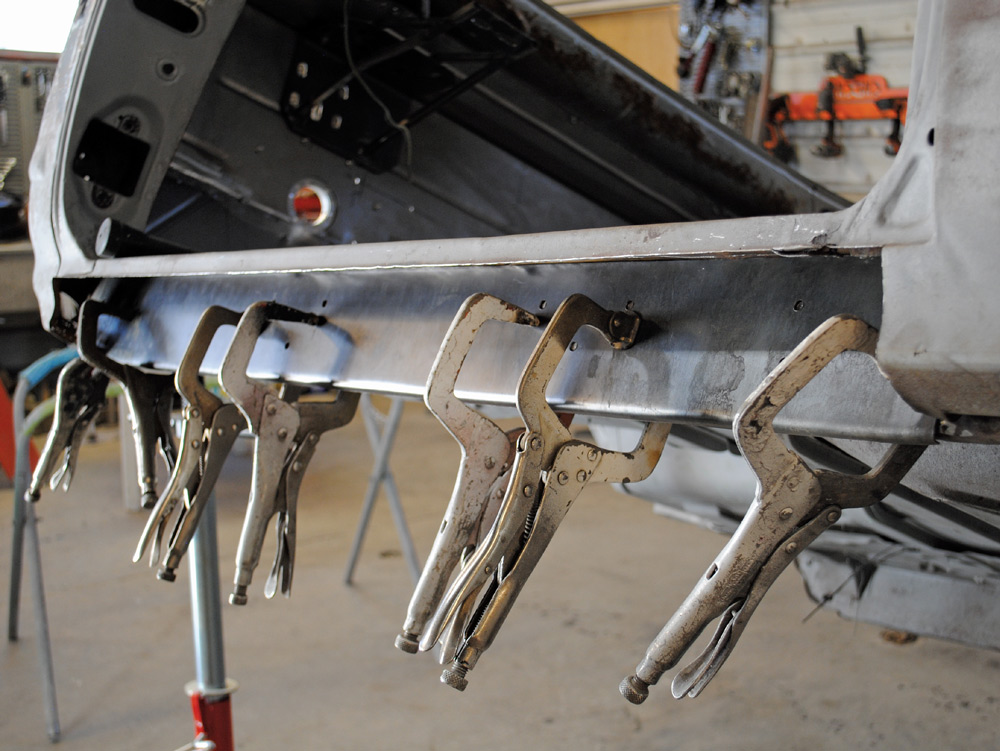
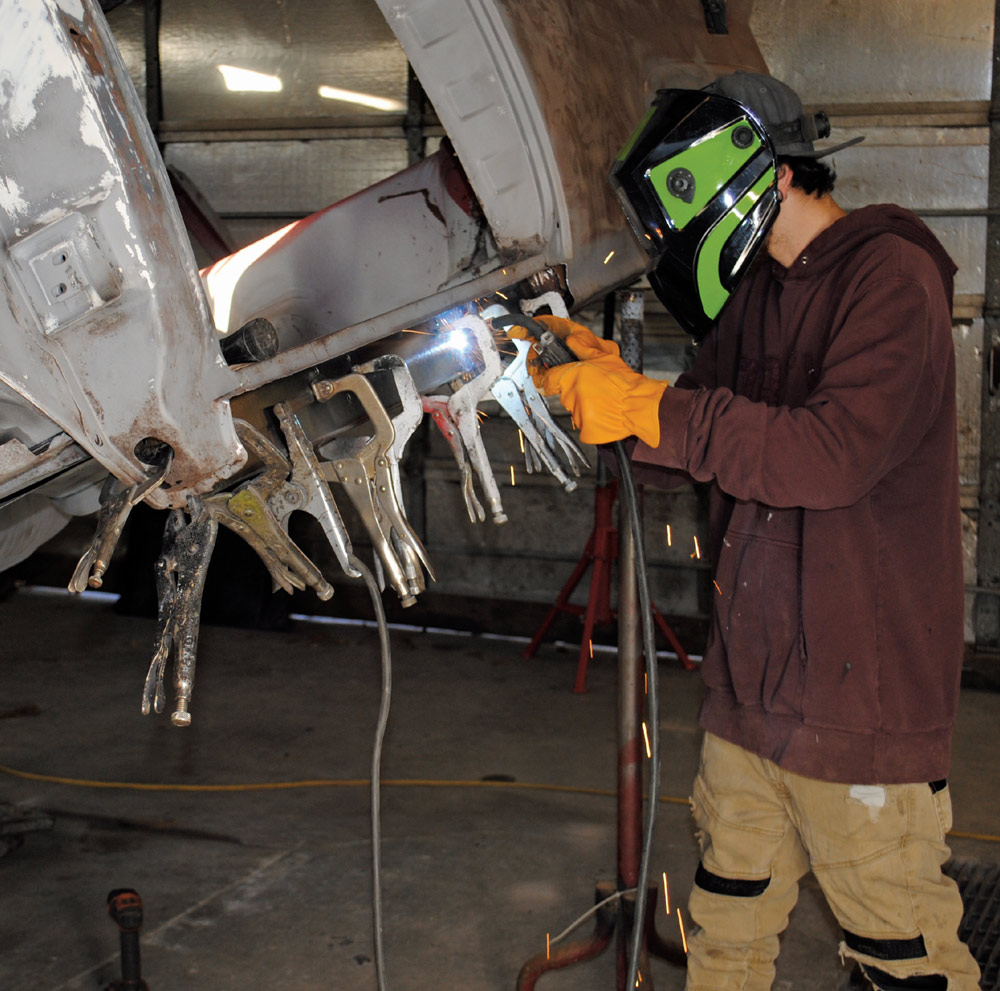
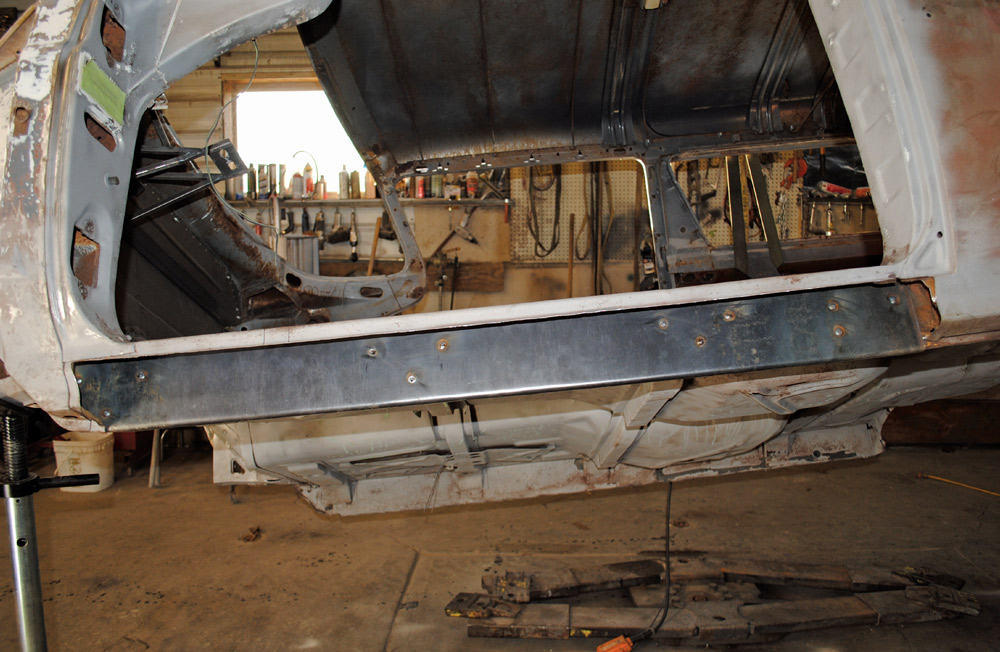

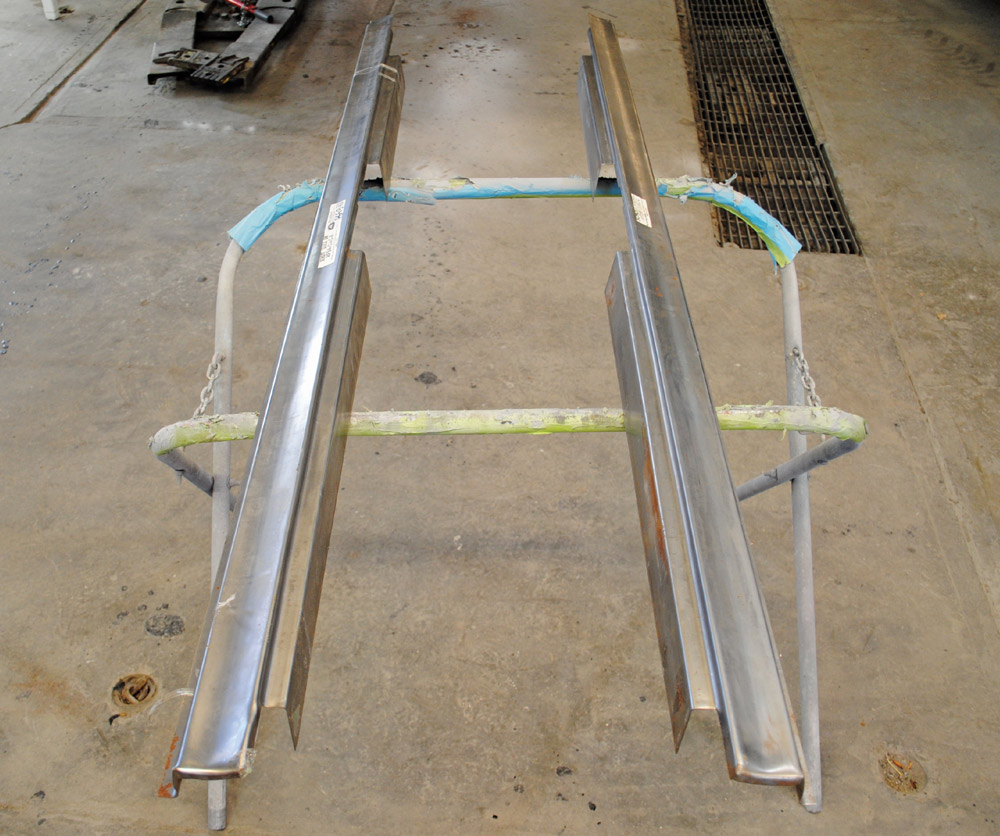

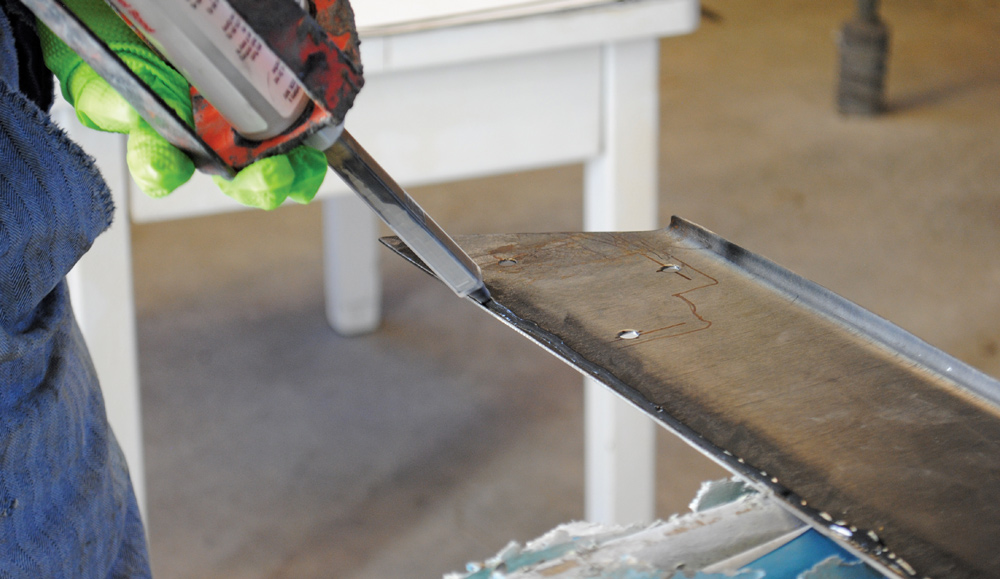
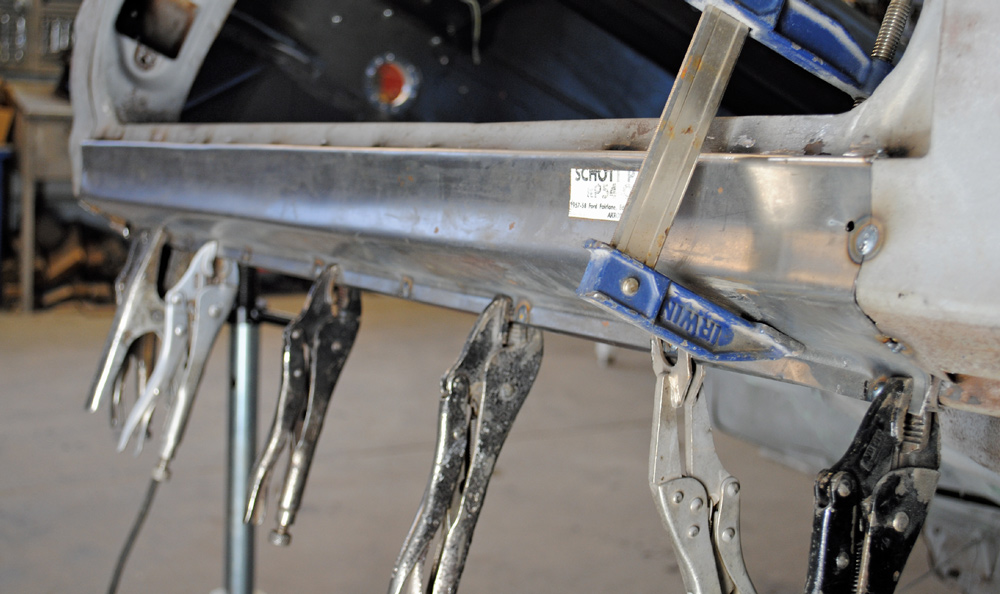
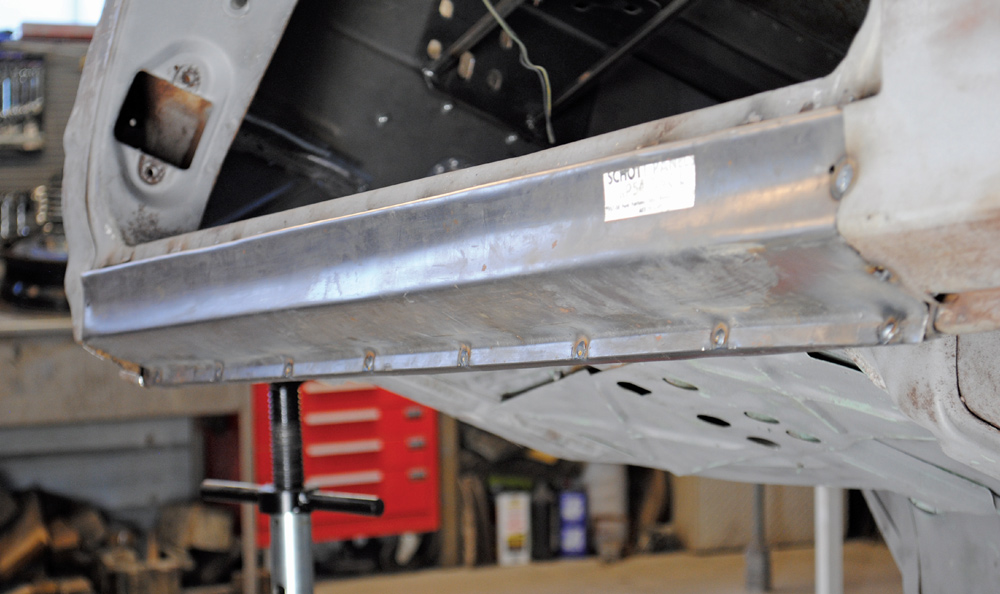

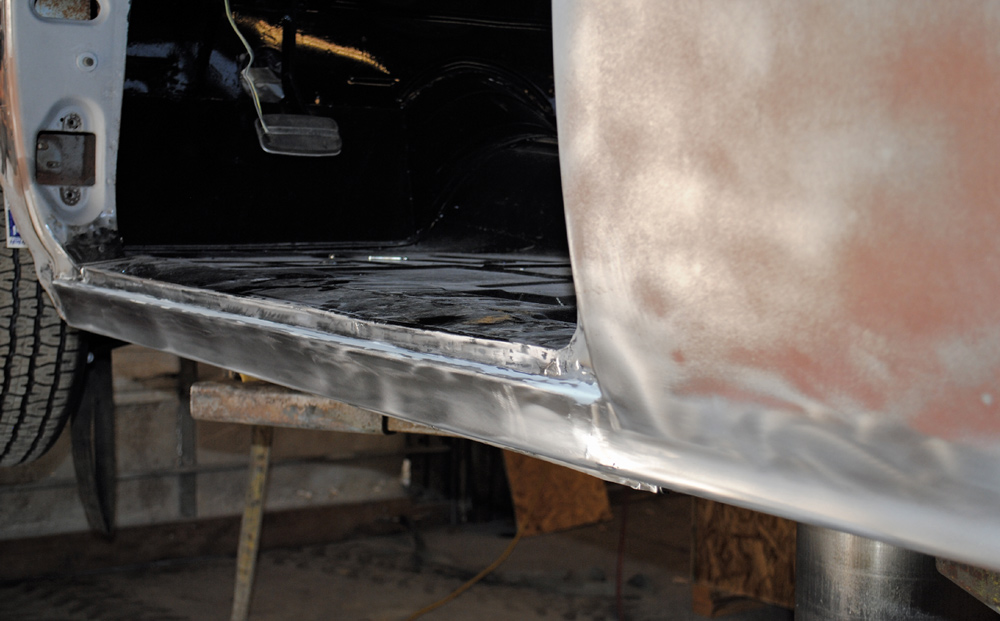

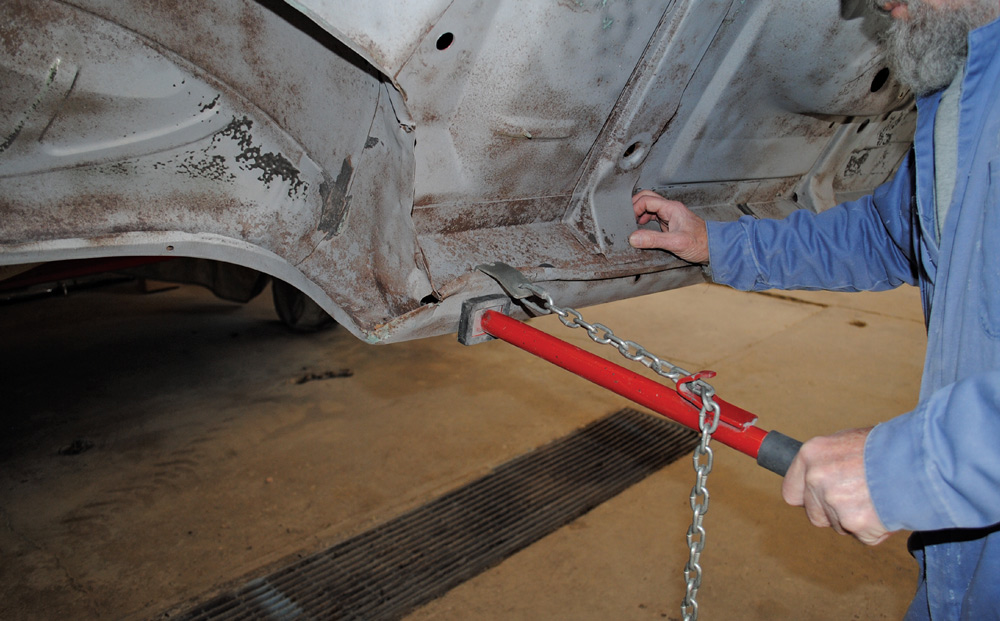
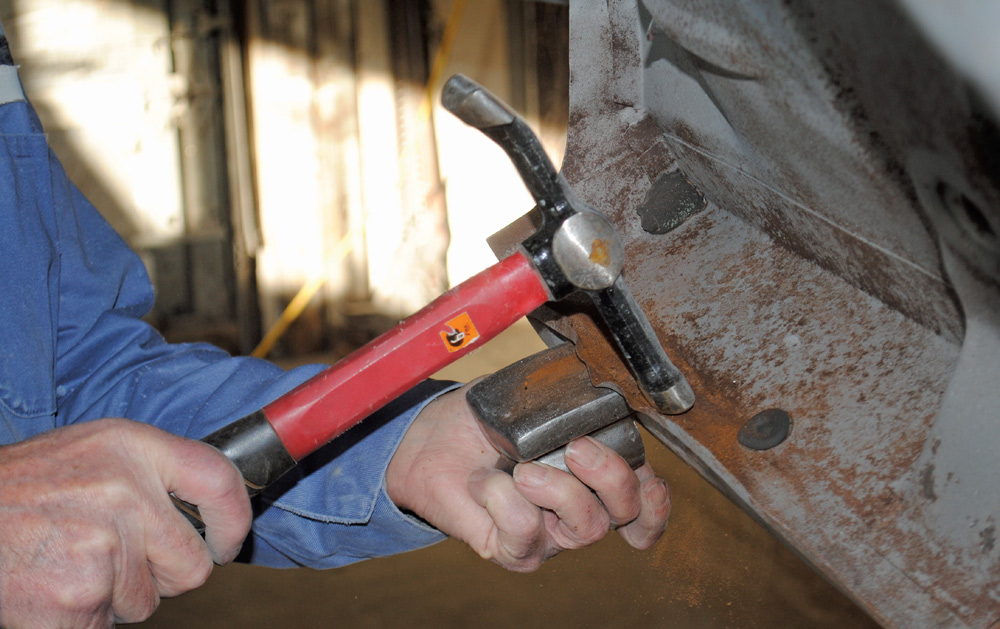

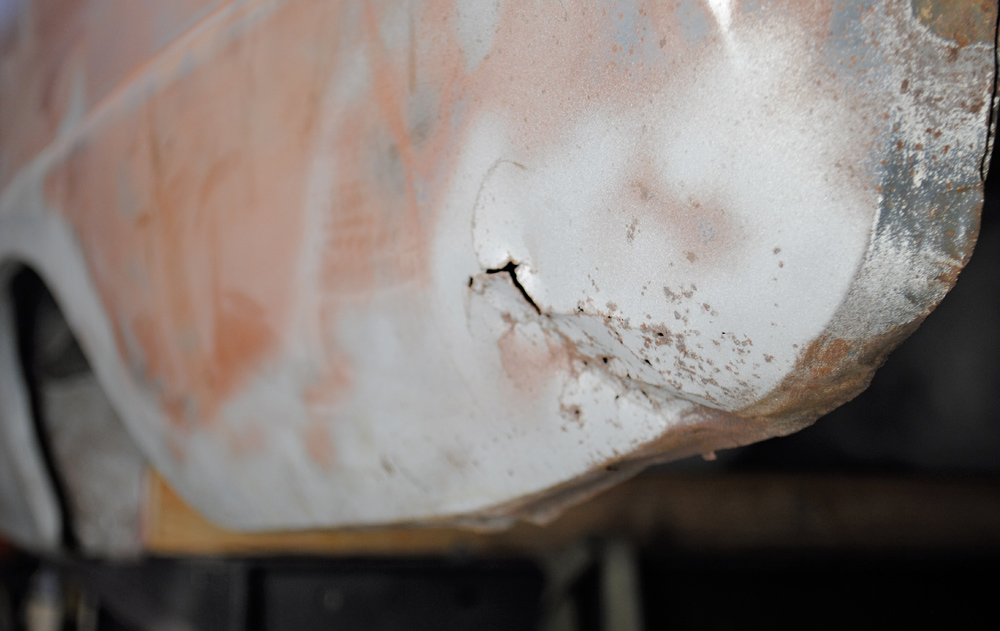
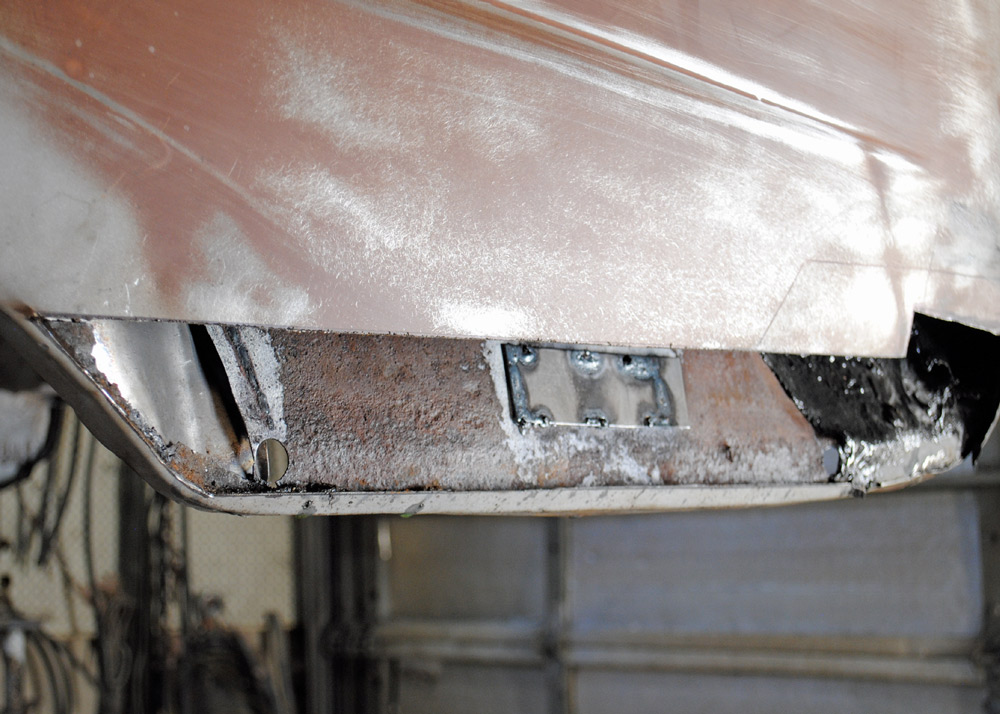
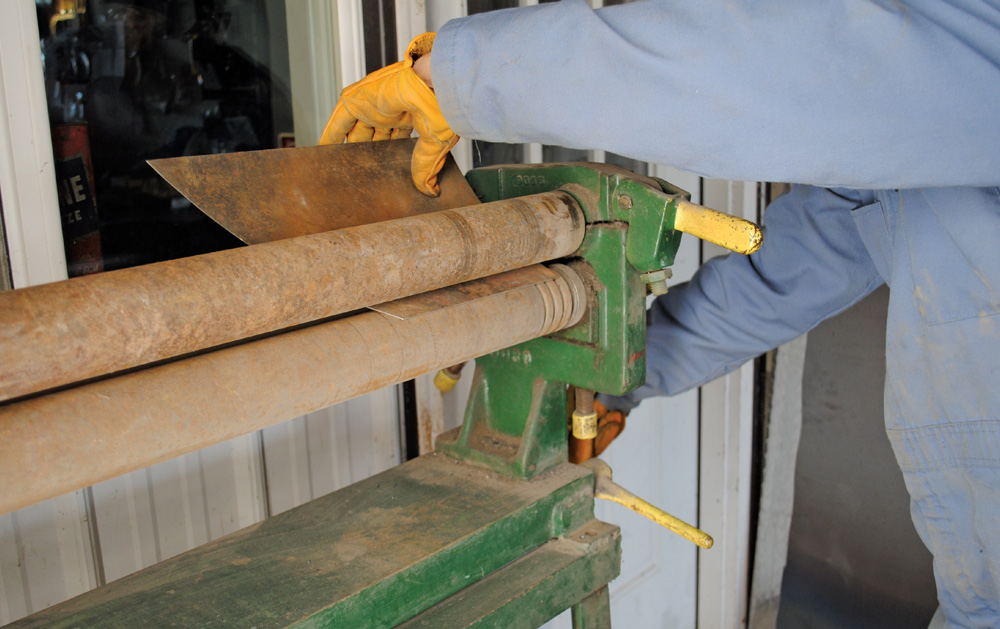
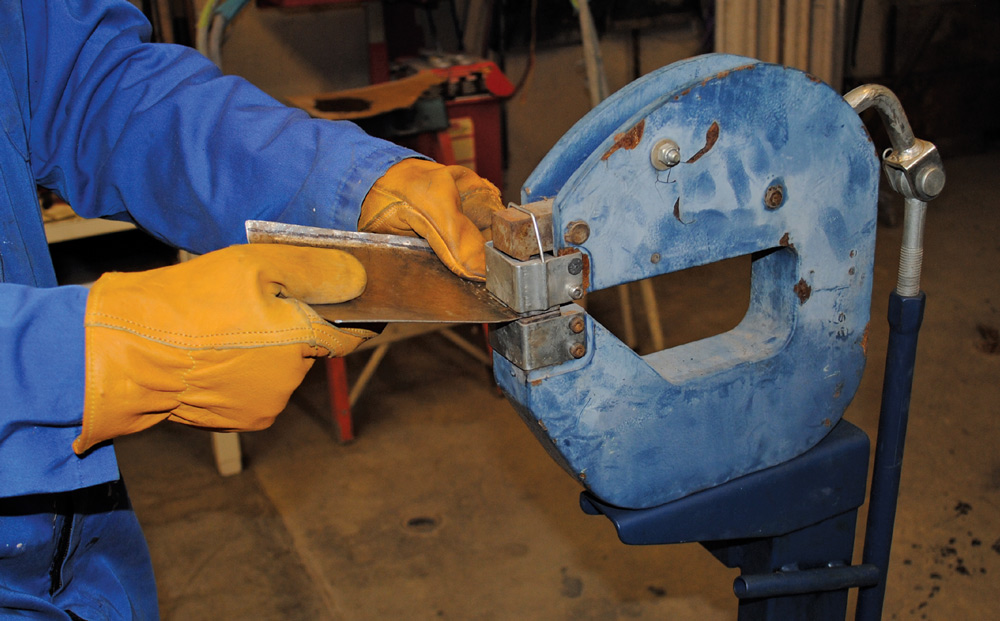
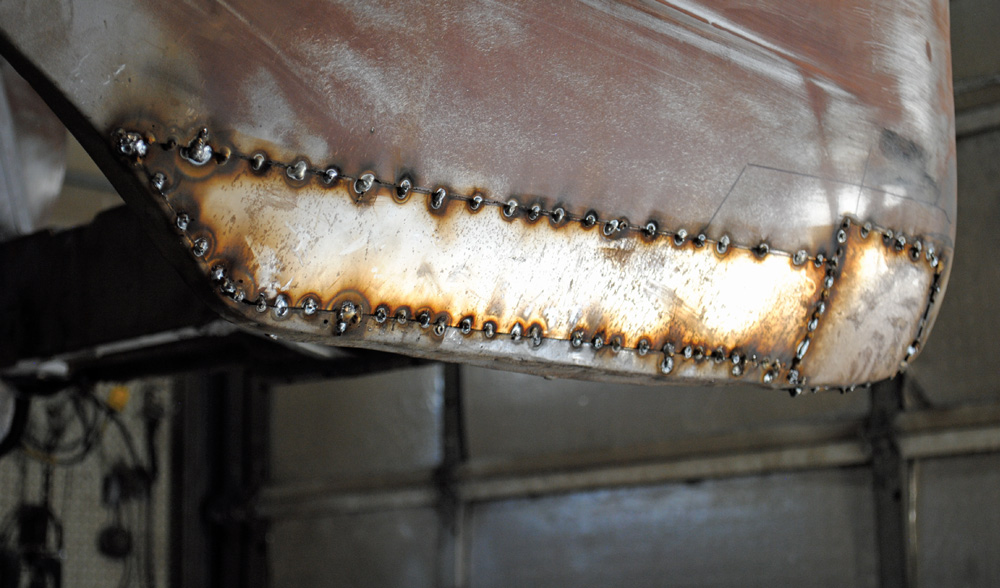
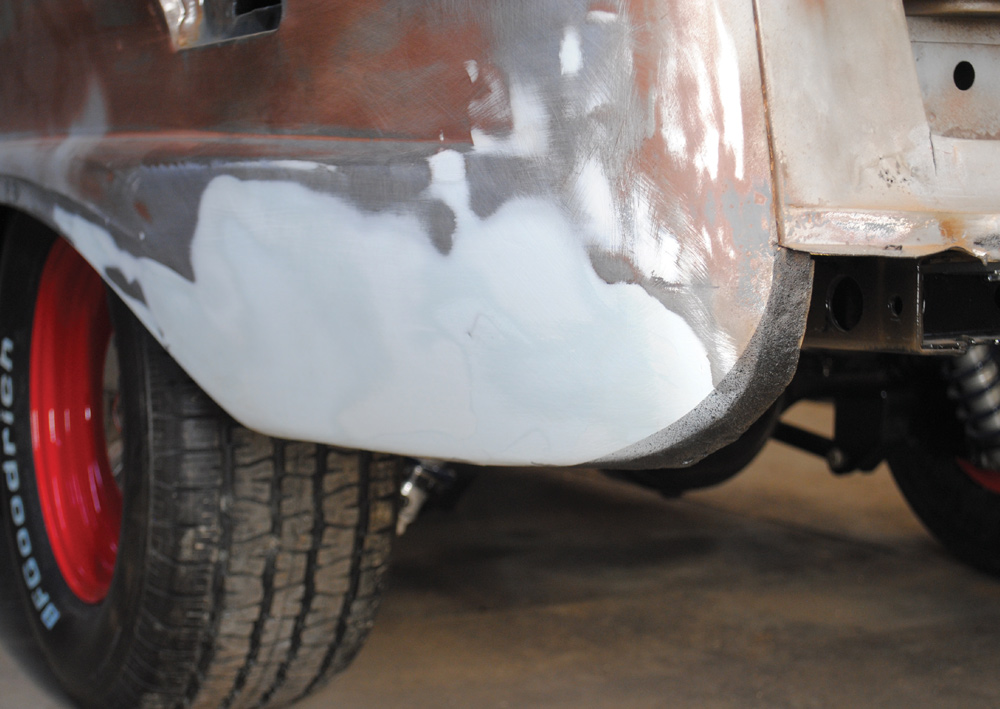
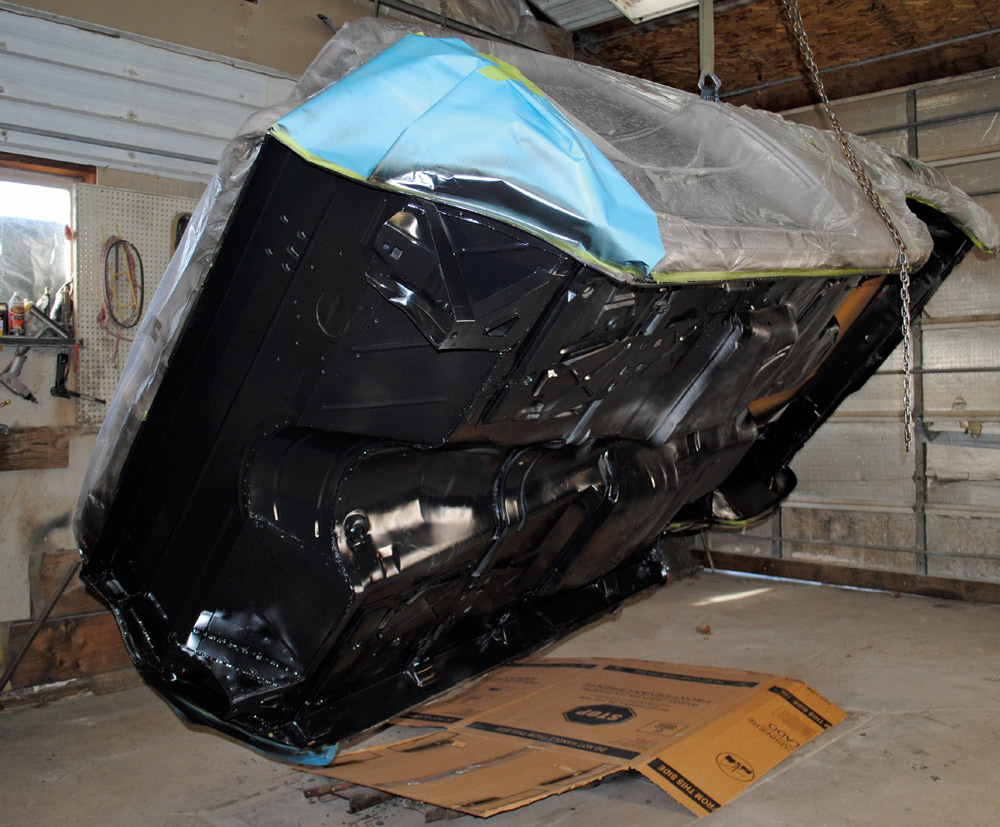
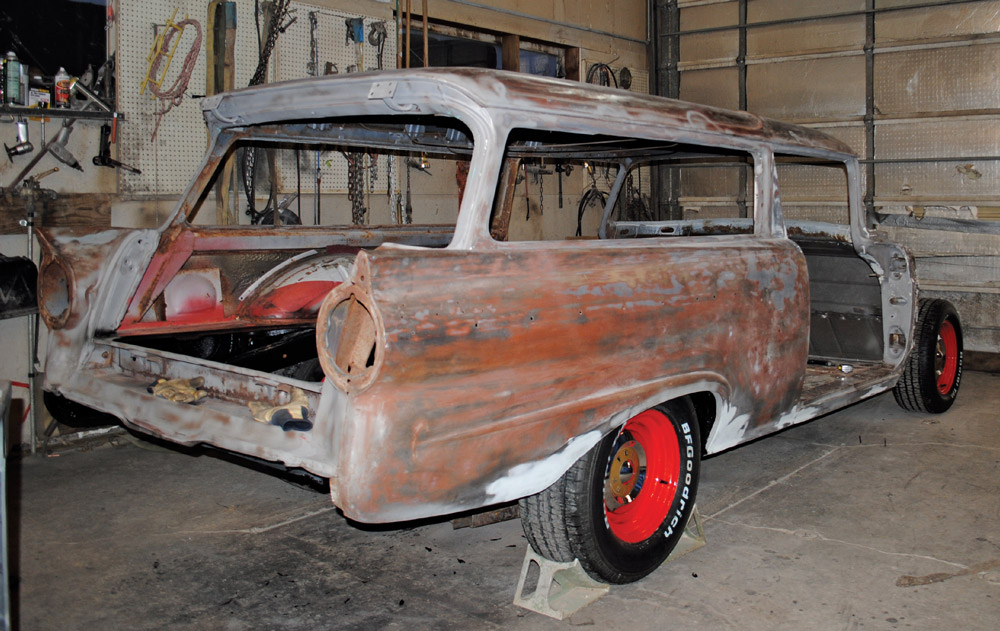