Modern Rodding TECH
InTheGarageMedia.com

avid Goodwin and the team at MetalWorks Speed Shop in Eugene, Oregon, are putting together one very tasteful, Pro Touring–style ’55 Chevy hardtop. Like most top-shelf hot rods, this one does a fine job of hiding all the cool fabrication, making it look like the car could have been built this way in 1955.
He has had a string of cool cars since the ’60s, so he has learned there is no better money spent than on the original car. Paying a bit more up front for a good example saves you money in the end and leads to a better finished product. Armed with that wisdom, he found a good example of a ’55 Chevrolet Bel Air hardtop. While the car was not a 100-point restoration, it was a good, solid start.
First, team MetalWorks rolled the original chassis out from under the car and the Art Morrison Enterprises GT Sport chassis was rolled into place. Four-wheel independent suspension, Wilwood Pro-II disc brakes, and Flaming River rack-and-pinion steering are just some of the highlights under the car. It is obvious from these specs that Goodwin enjoys spirited performance. One of his past cars was a ’67 427 Corvette. Once you’ve had a 427 you never get over it. Goodwin thought another 427 would be perfect for his latest project, but this time it would be 427 inches wrapped in a tighter and lighter package, namely a modern small-block LS3.
To facilitate the new engine the team at MetalWorks decided a new firewall was in order. The original firewall was in solid condition, but MetalWorks Speed Shop believes a slick motor, such as an LS3 built out to 427 ci, should be sitting in front of a slick firewall.
To that end, team MetalWorks set about fabricating and installing one very smooth, recessed firewall, that, when finally painted, will provide the perfect reflection of performance.
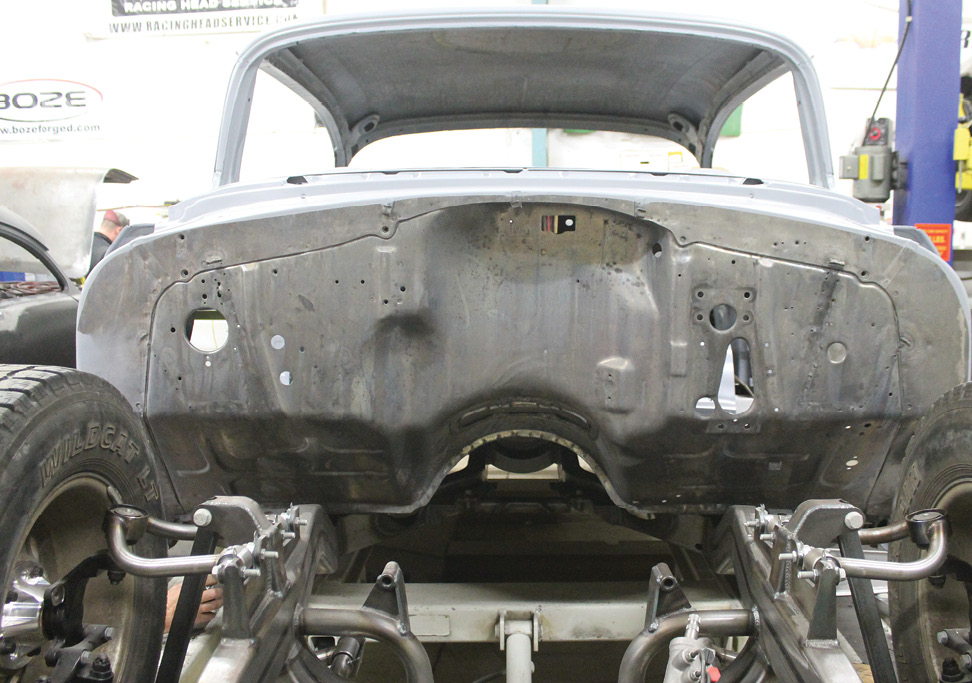
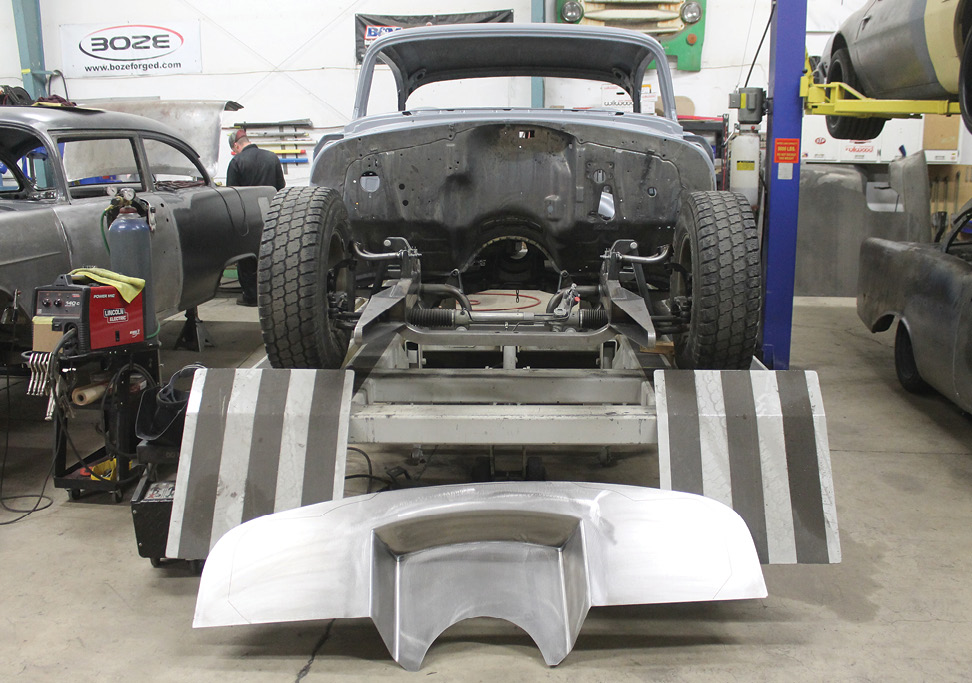
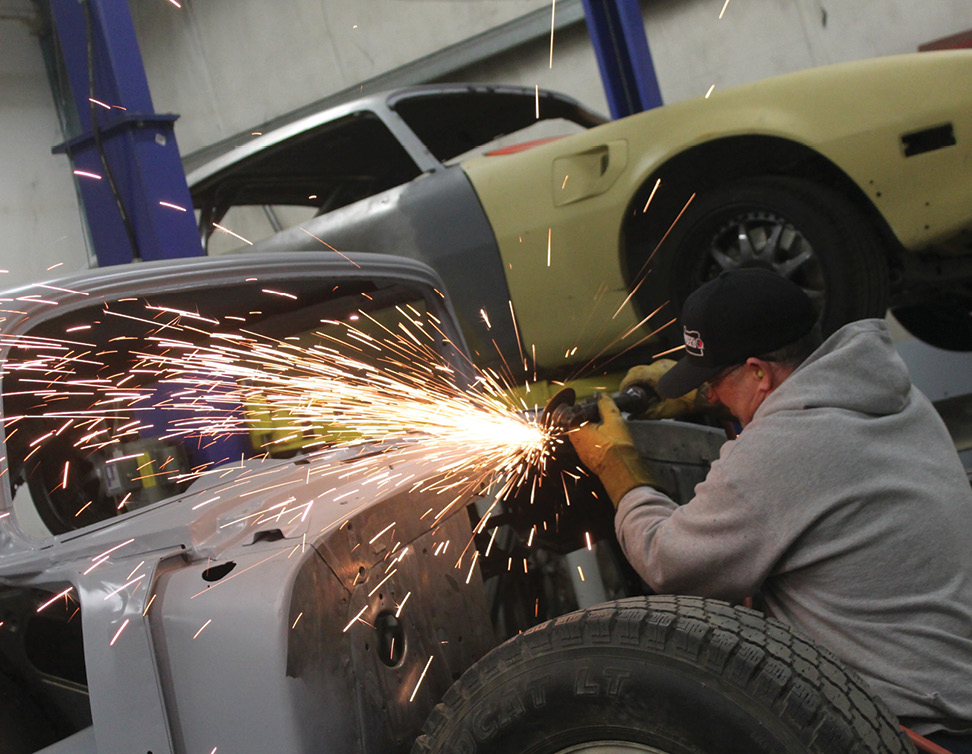
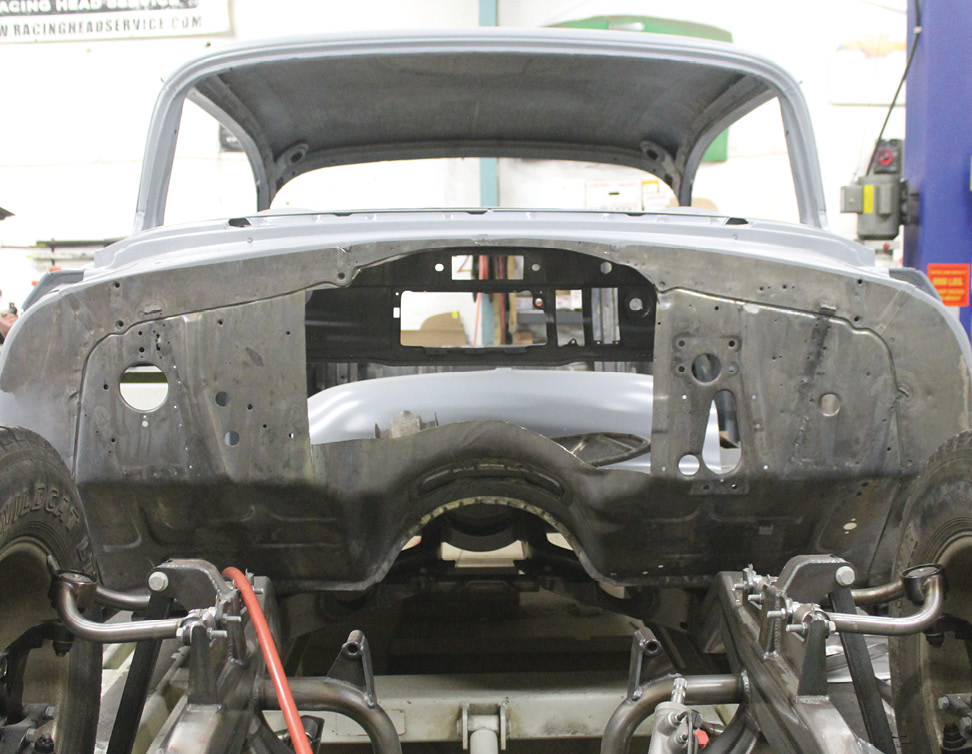
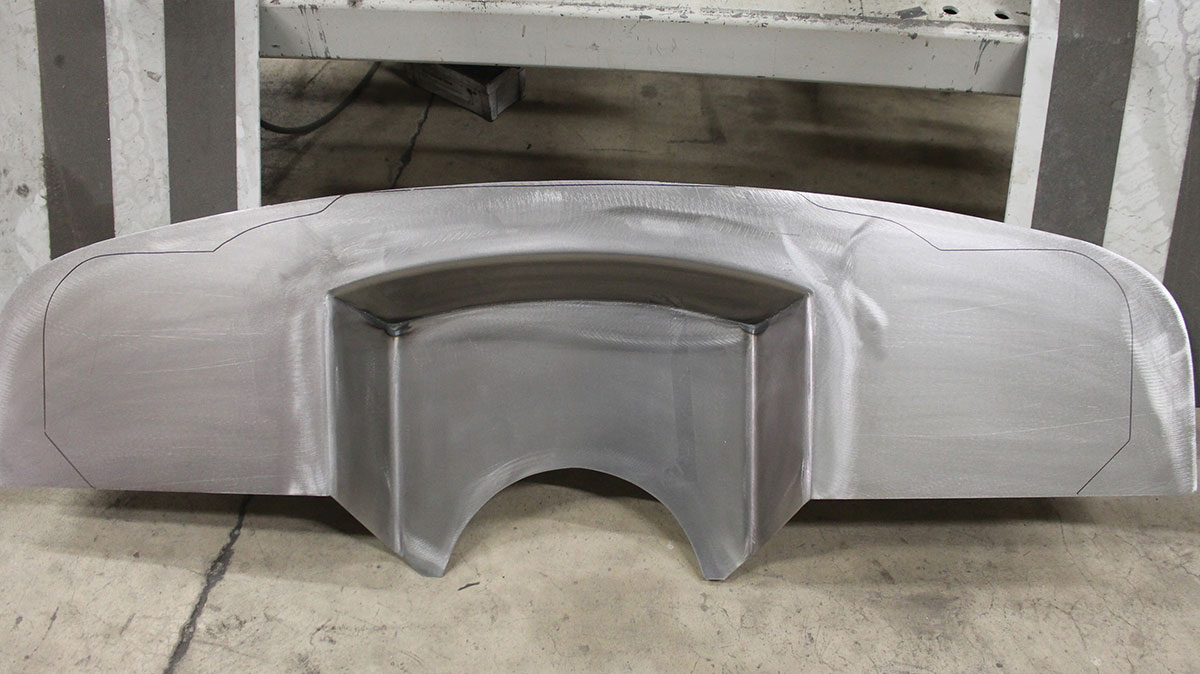
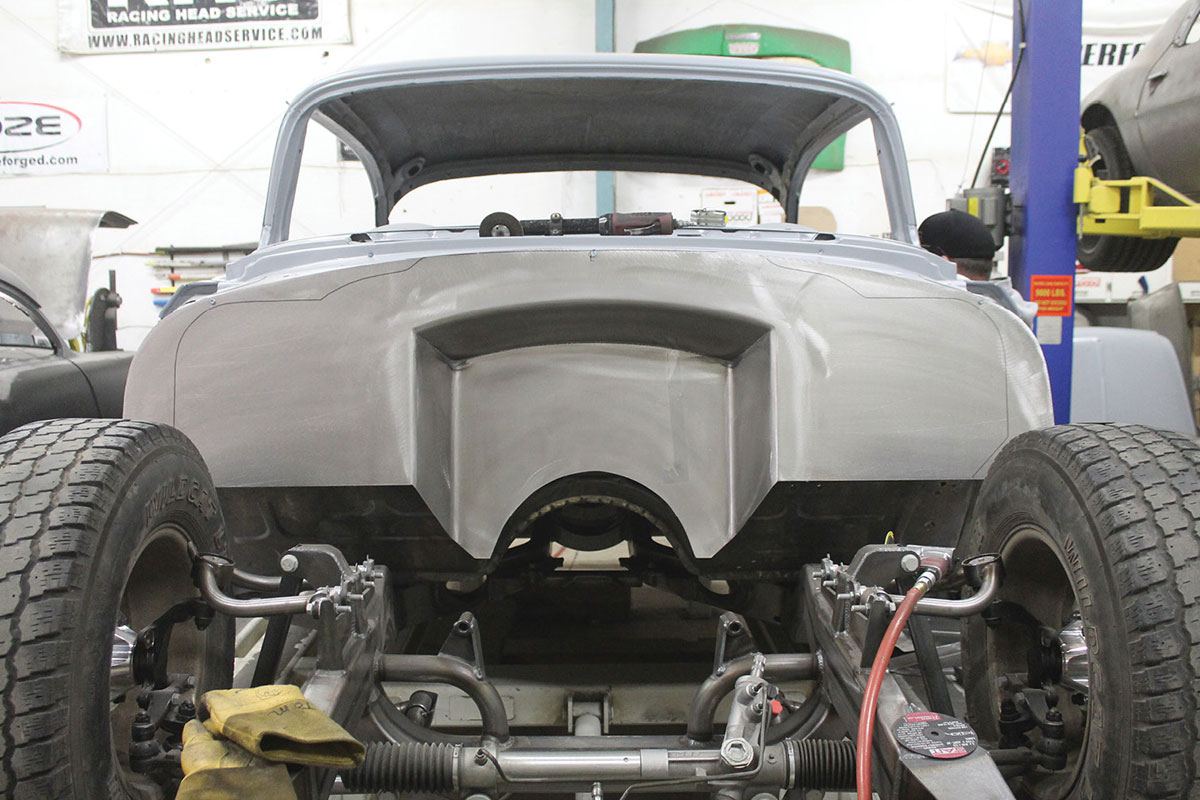
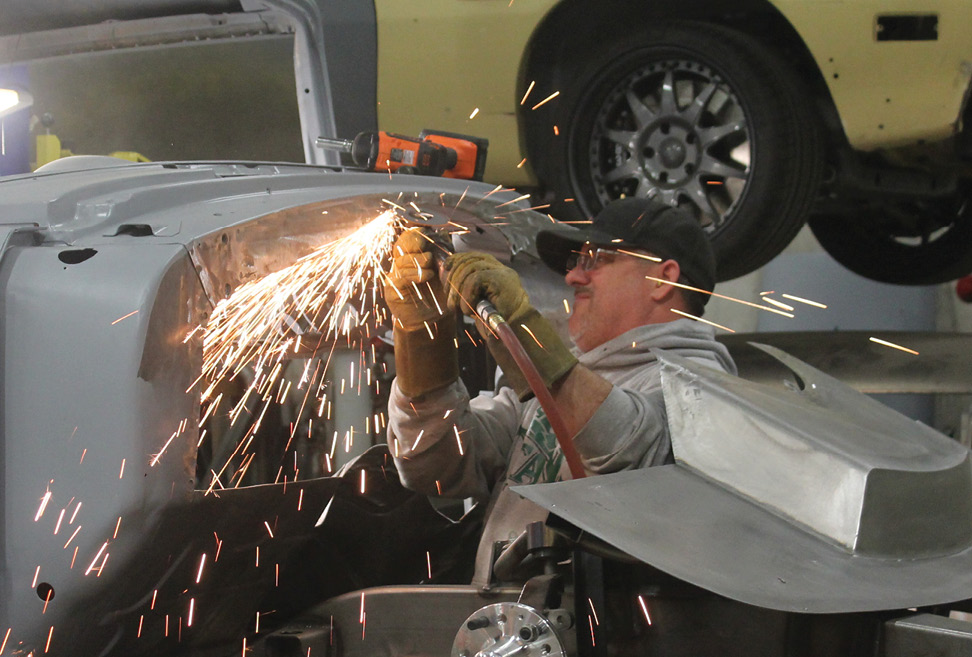
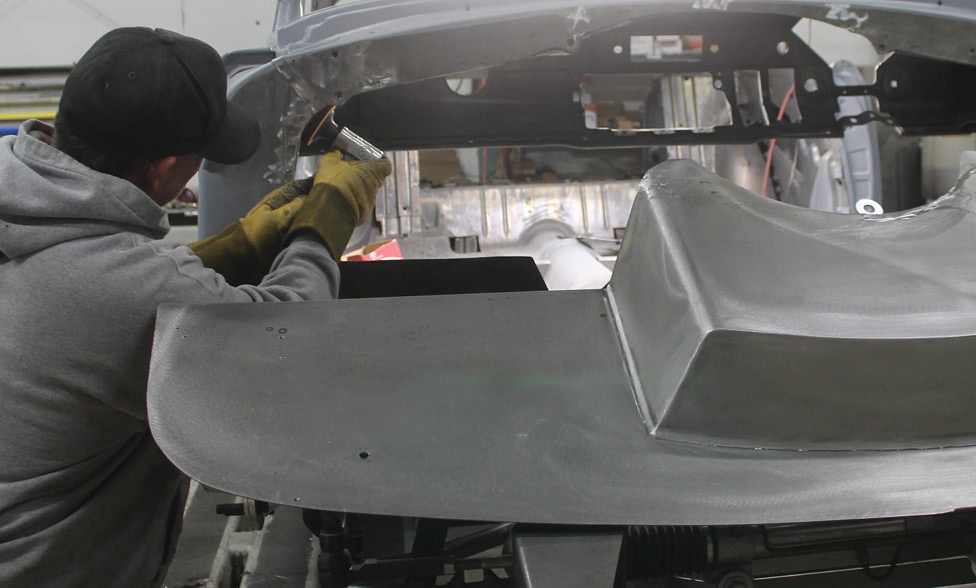

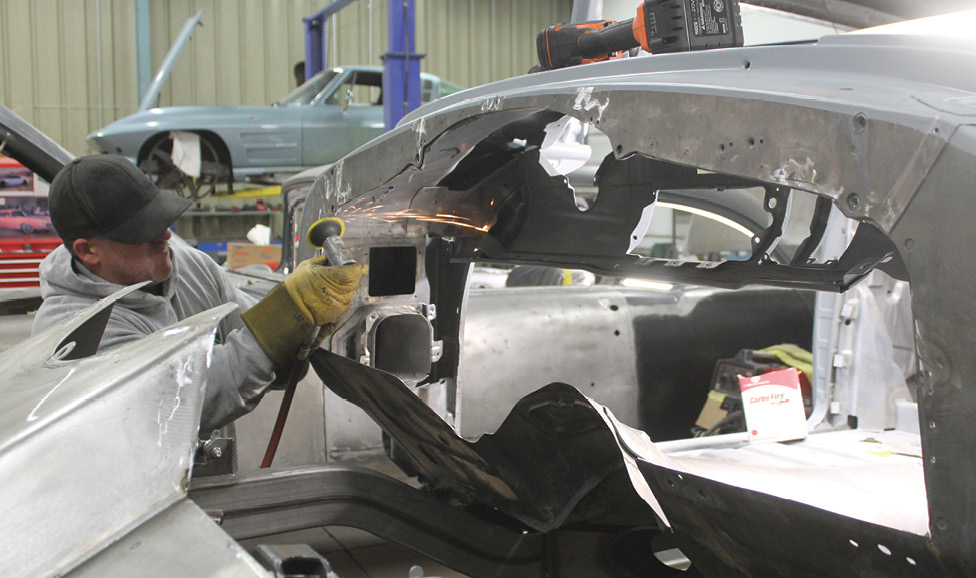
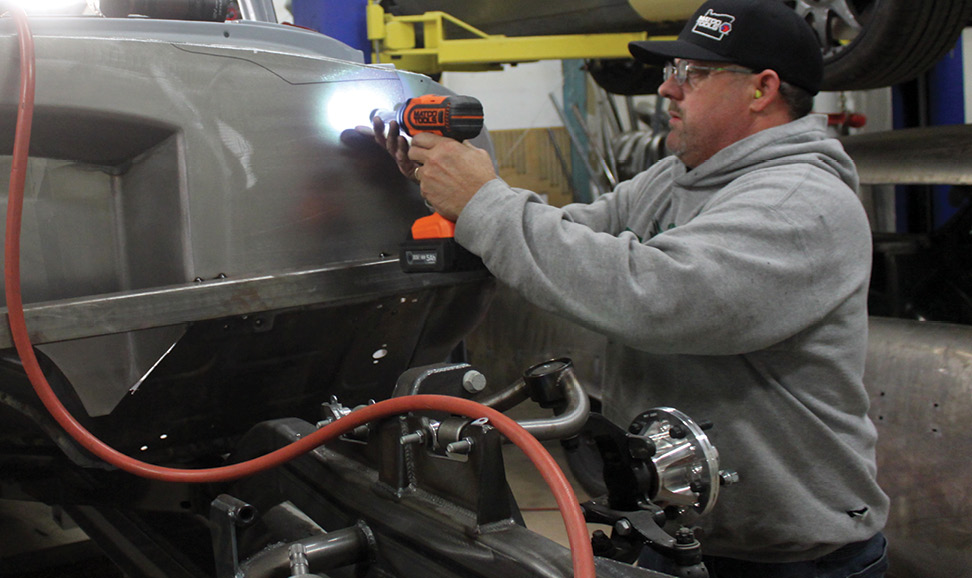
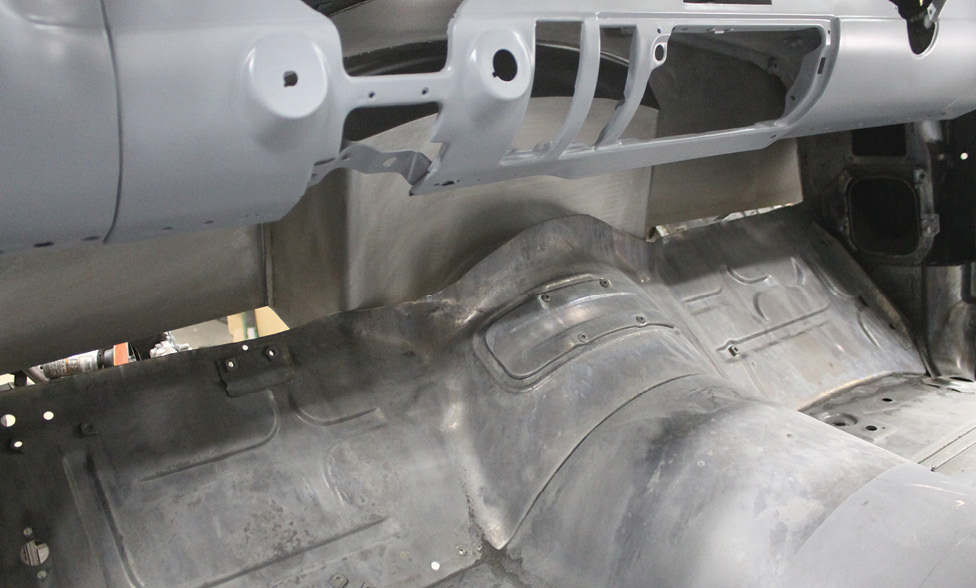
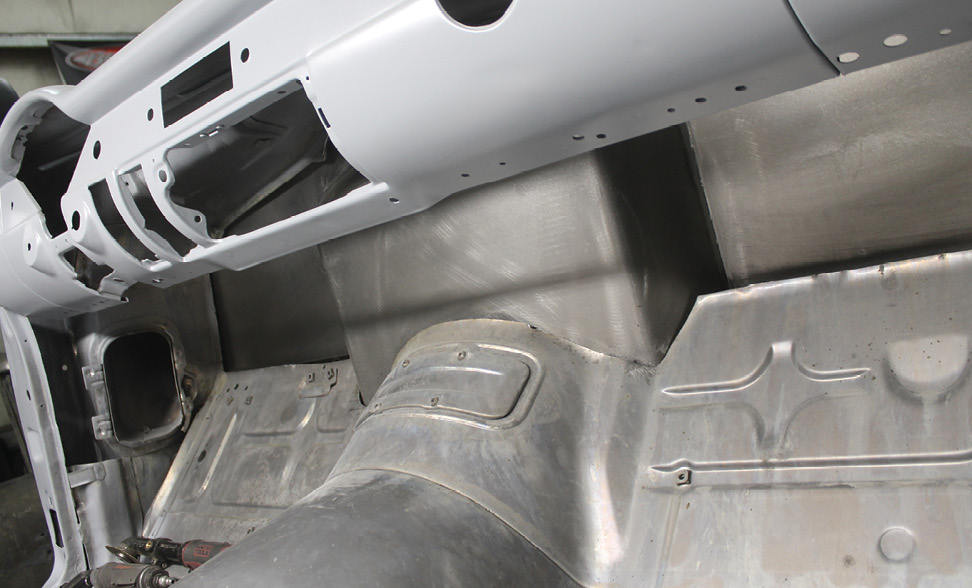
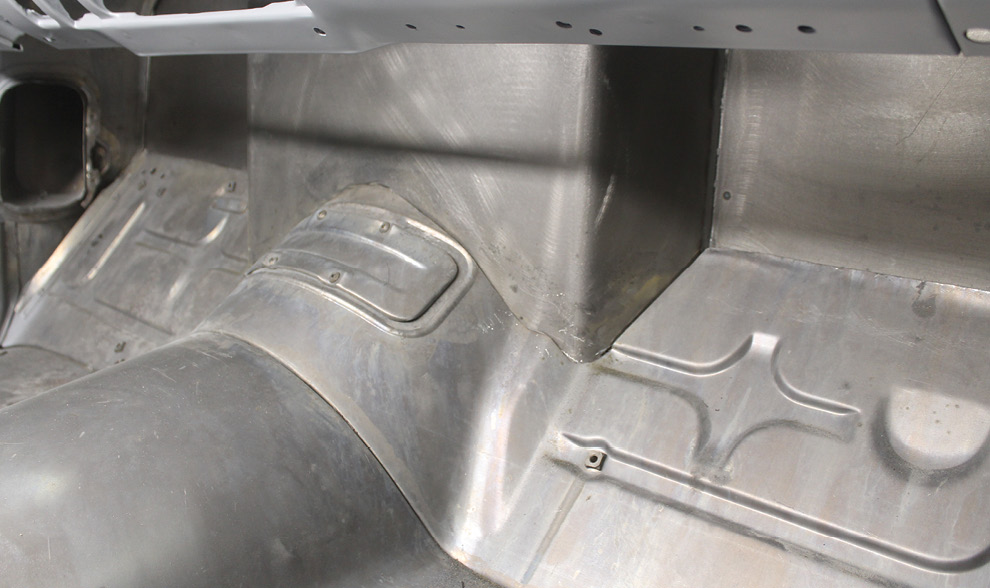
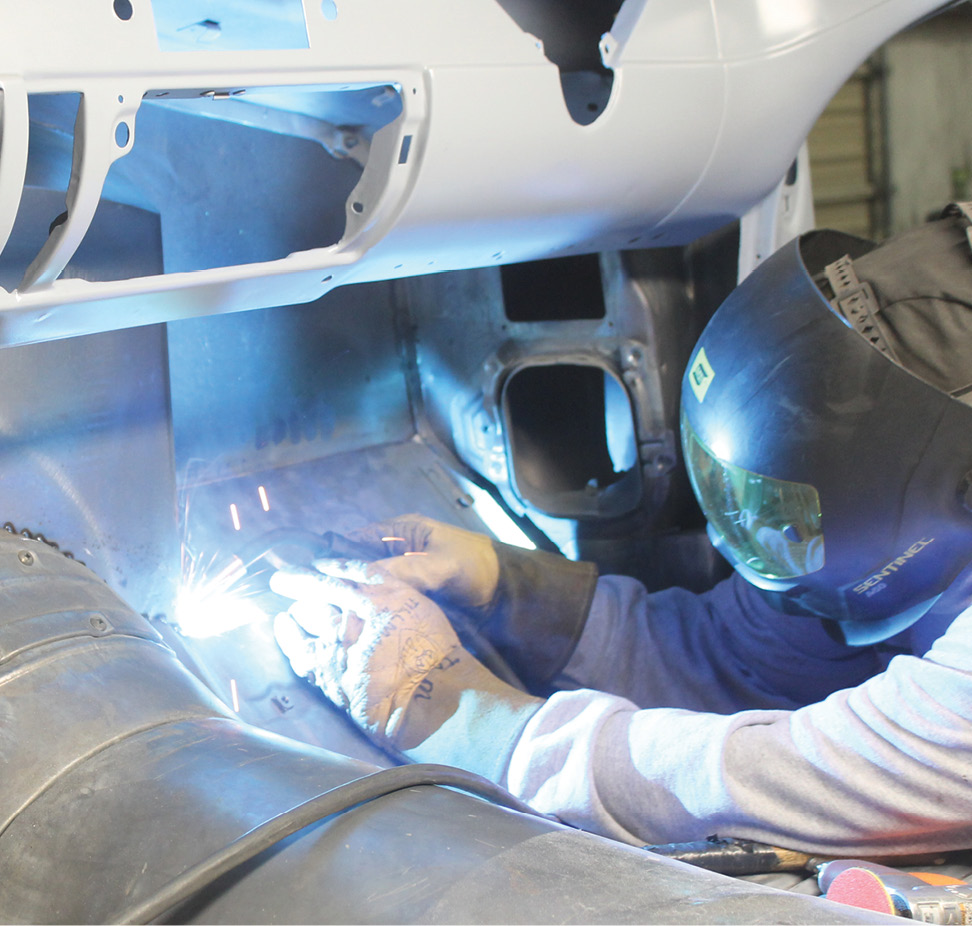
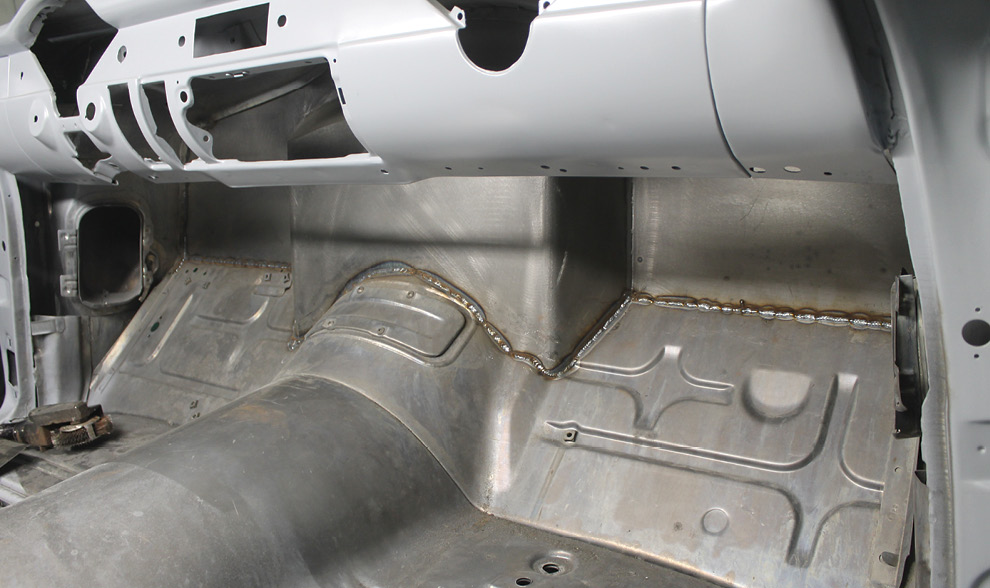
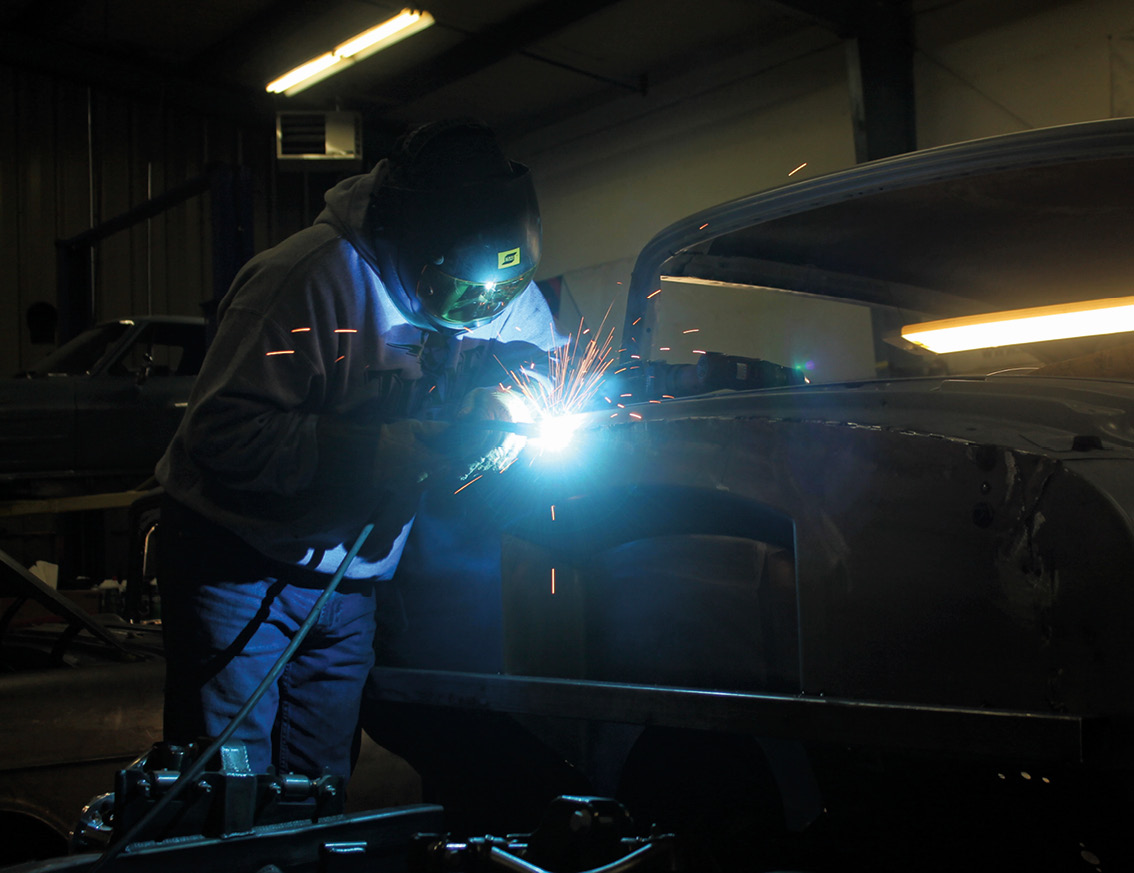
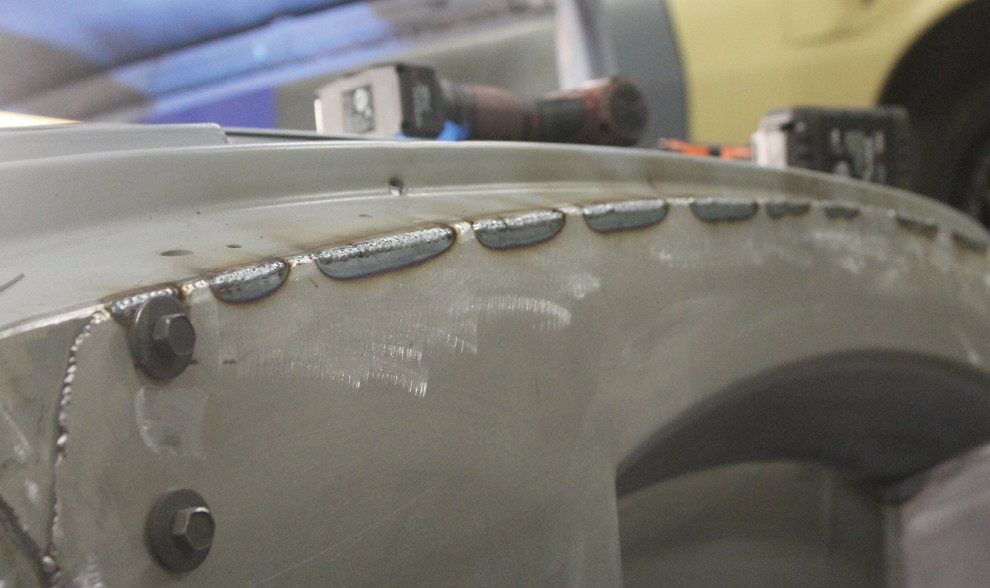
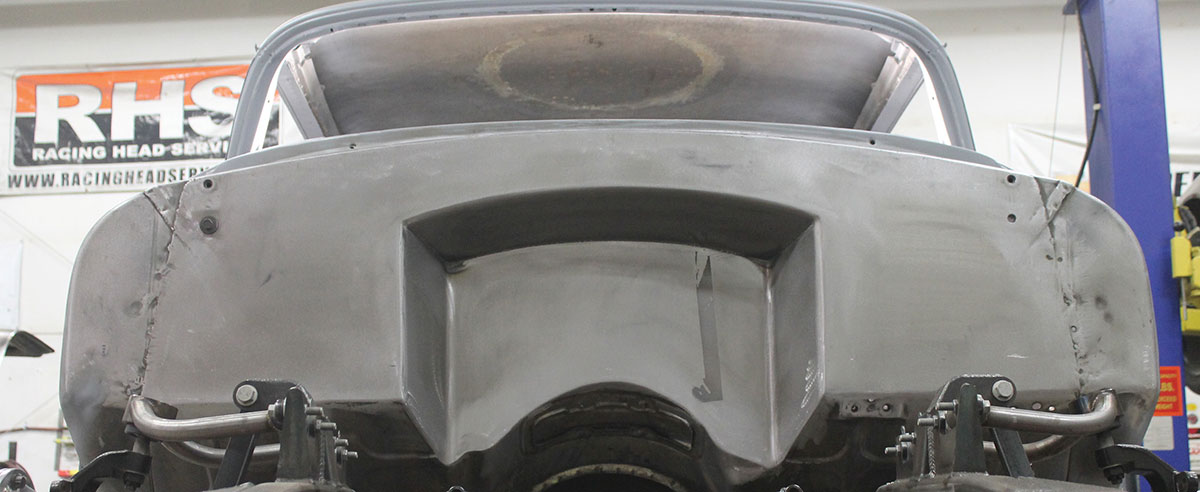

VOLUME 4 • ISSUE 36 • 2023