Modern Rodding TECH
InTheGarageMedia.com


s you get into any metal repair or replacement work on your project you must always balance time versus money. Sometimes you may have more of one than the other (with rarely an abundance of both) but doing rust repair work on a vehicle can eat up a lot of time and money. Luckily for Tri-Five owners, Texas-based Golden Star Classic Auto Parts can save you a bit of both.
Golden Star is a family owned/operated business that sells a huge amount of replacement parts and pieces for everything from old Ford Broncos, Mustangs, Chevelles, GTOs, A- and G-body GMs, to ’60s VW Buses and Mercedes-Benzes, but they also carry a full line of ’55-57 Chevy replacement panels to make repair work more manageable.
At Orange County Hot Rods (Corona, California) owner Aaron Hamusek had a customer’s ’56 Bel Air hardtop in his shop that needed some major repair work done, including quarter-panel and floor replacement but, as he turned his attention to the back end of the car, he found a large amount of heavily rusted and Swiss-cheesed metal that was beyond repair, so he decided to do a full replacement of the car’s tailpan section—basically everything below and between the taillights, including the trunklid, which is a common place for Tri-Fives to rust. After an order to Golden Star for the seven pieces needed, Hamusek started the removal process documented here.
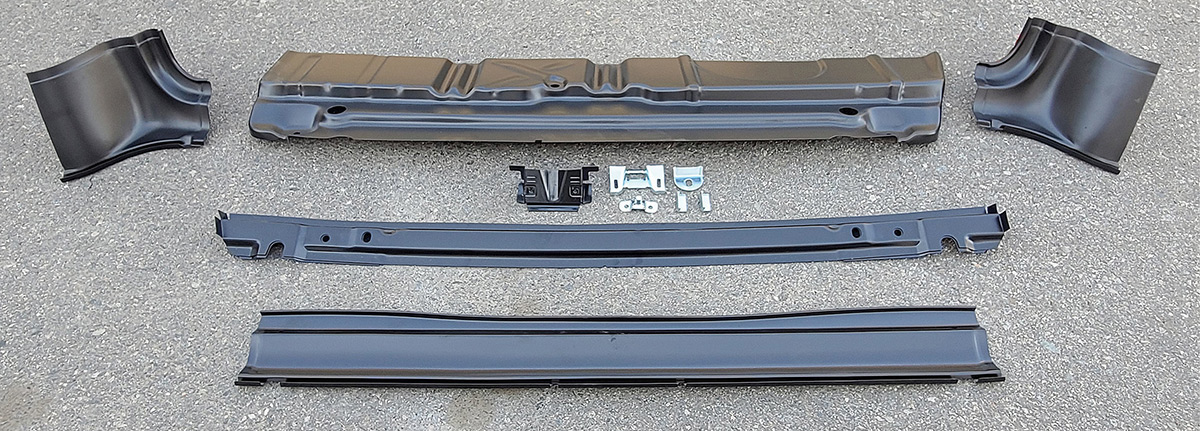
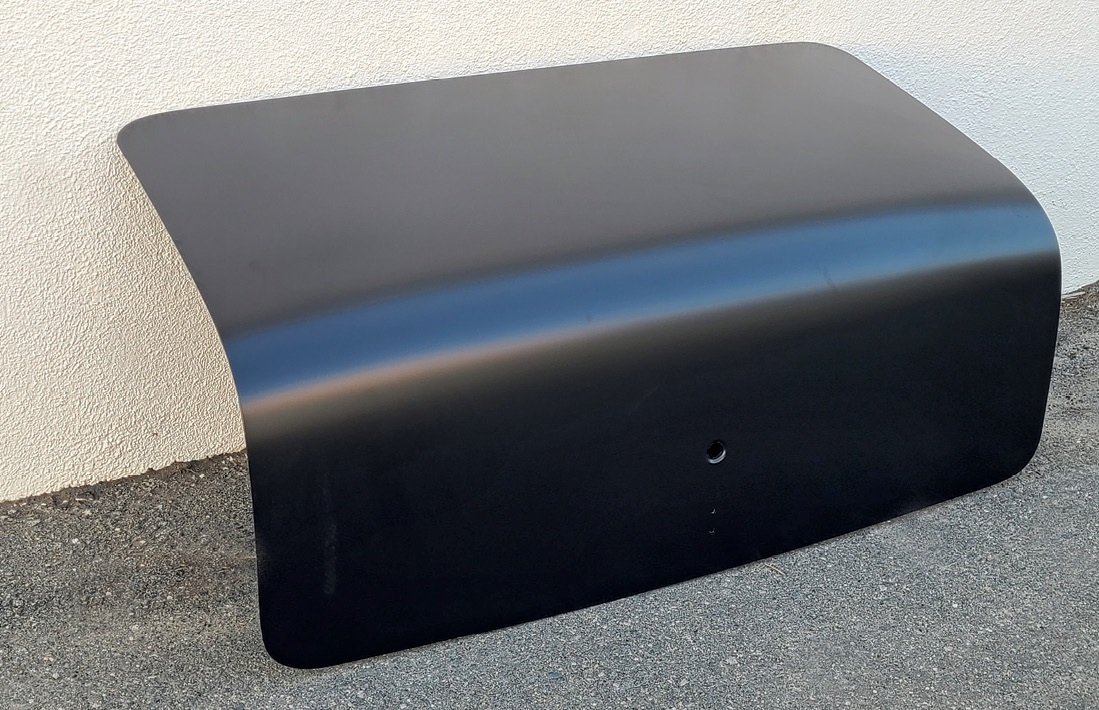
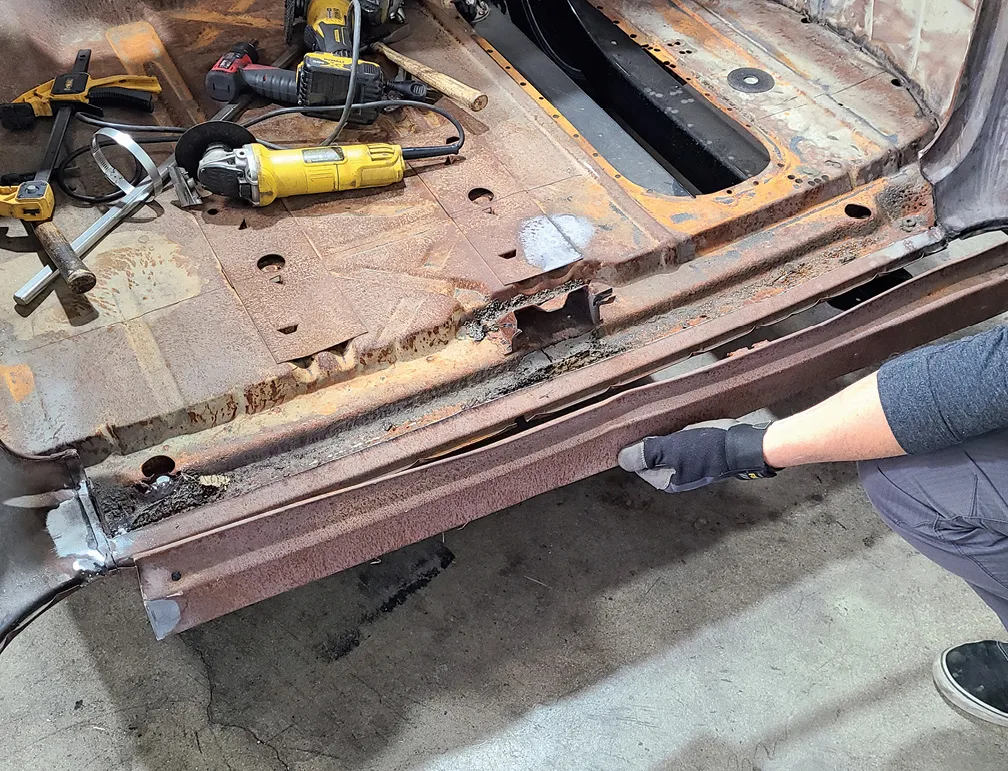
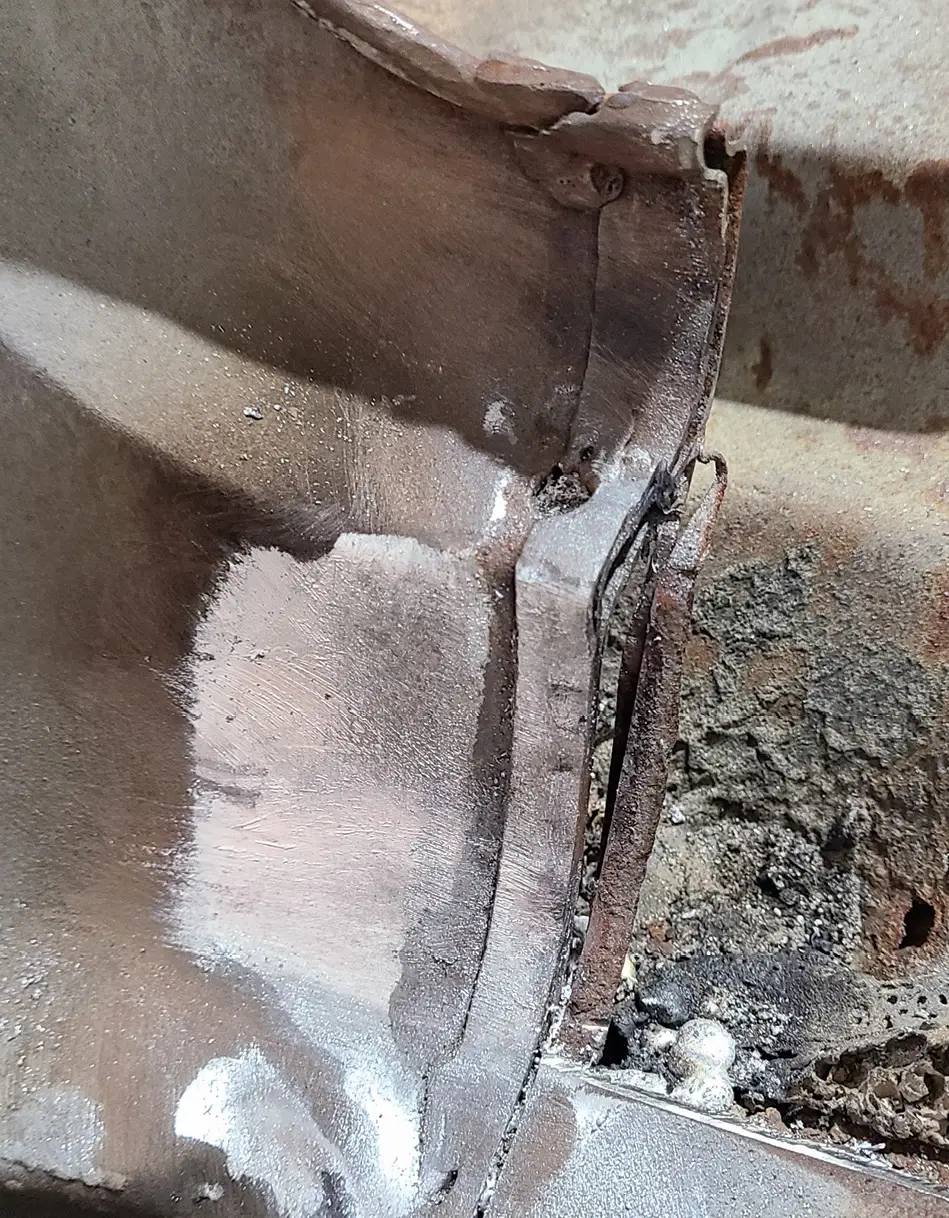
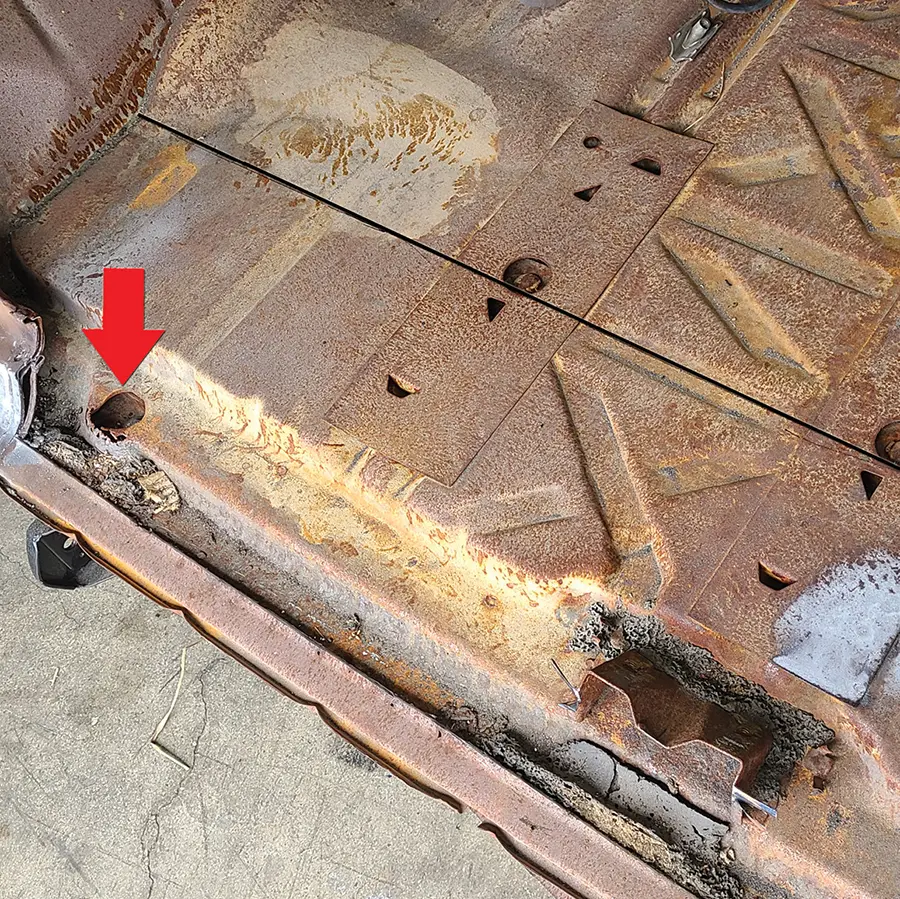
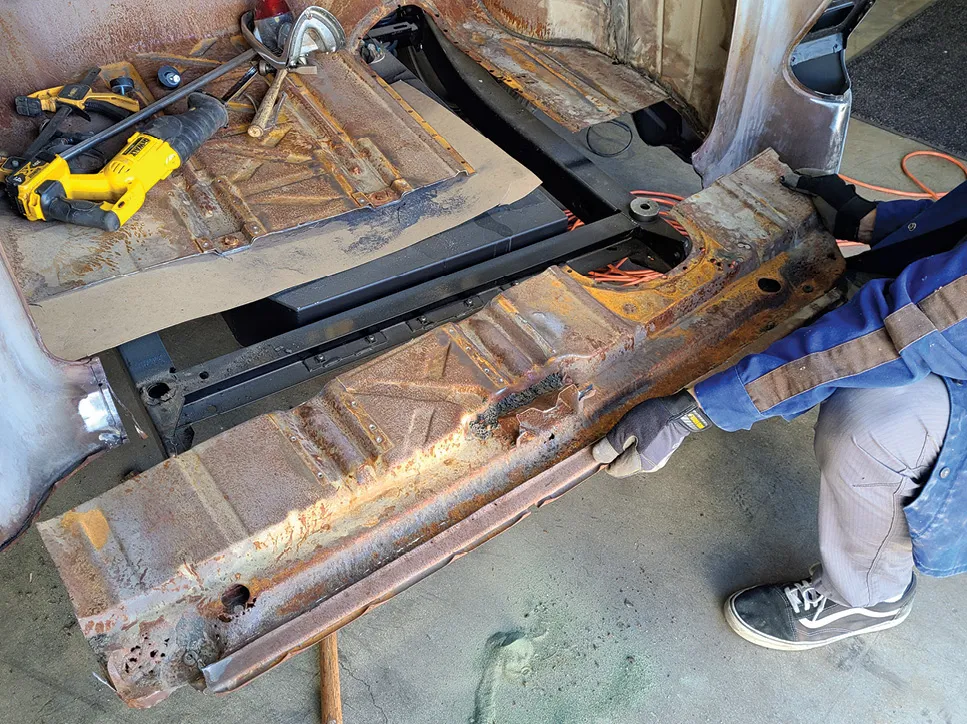

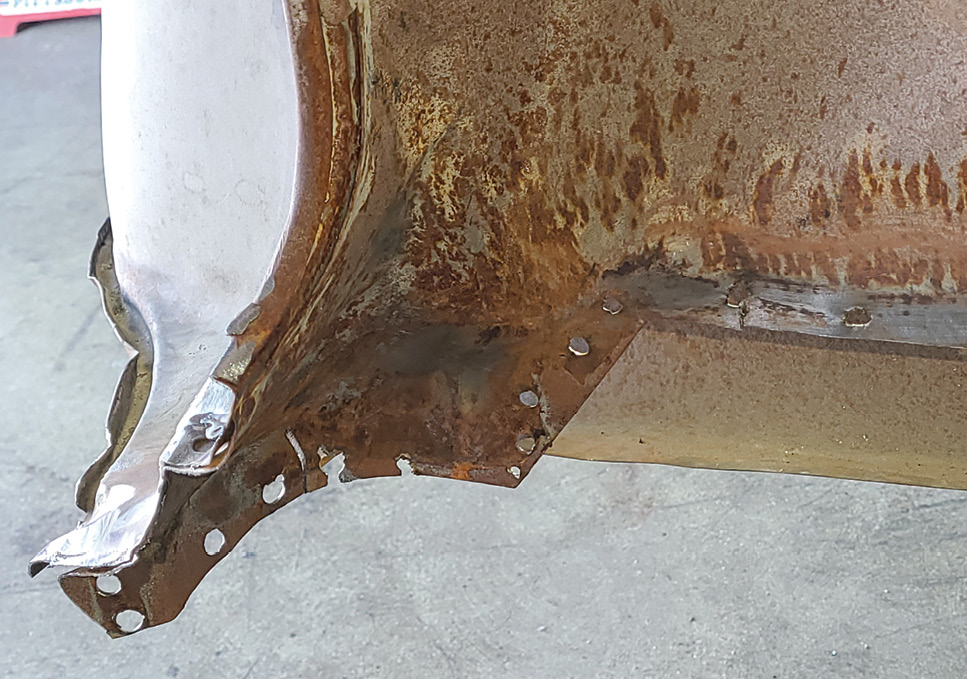
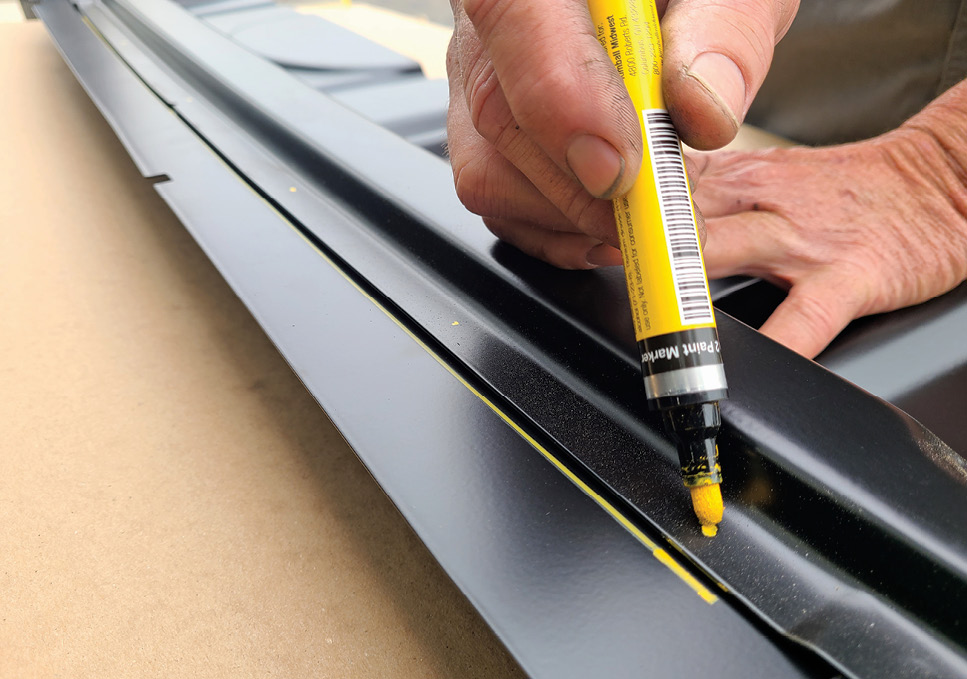
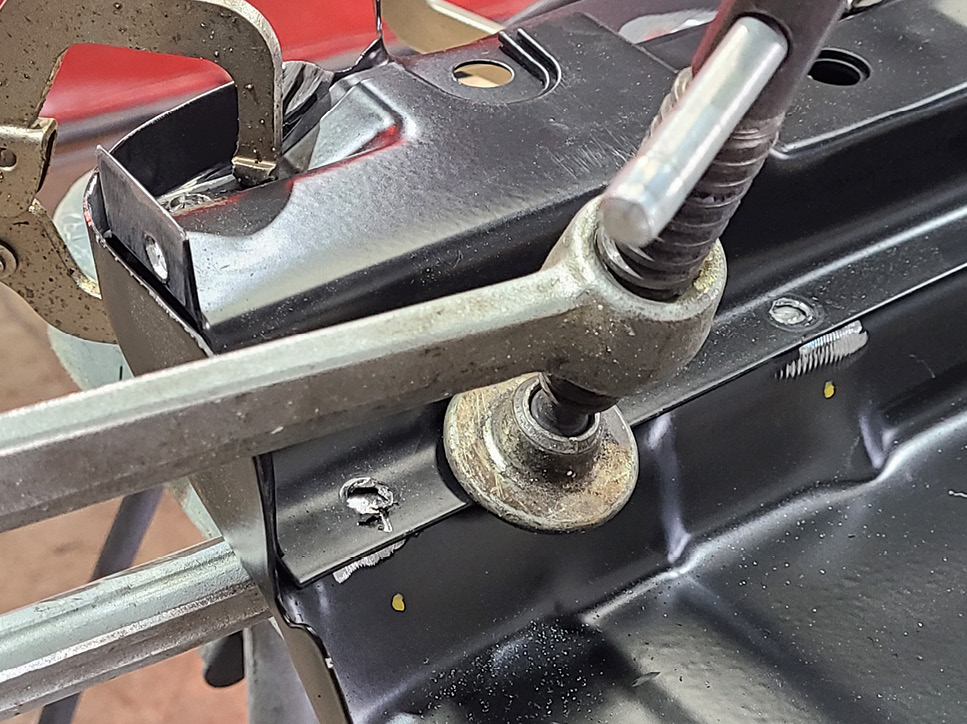

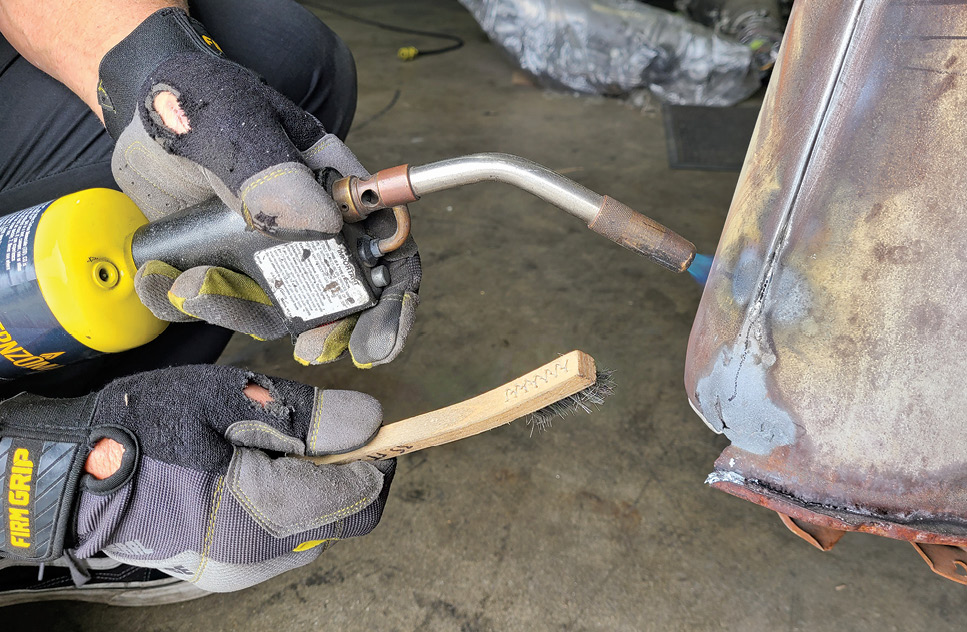

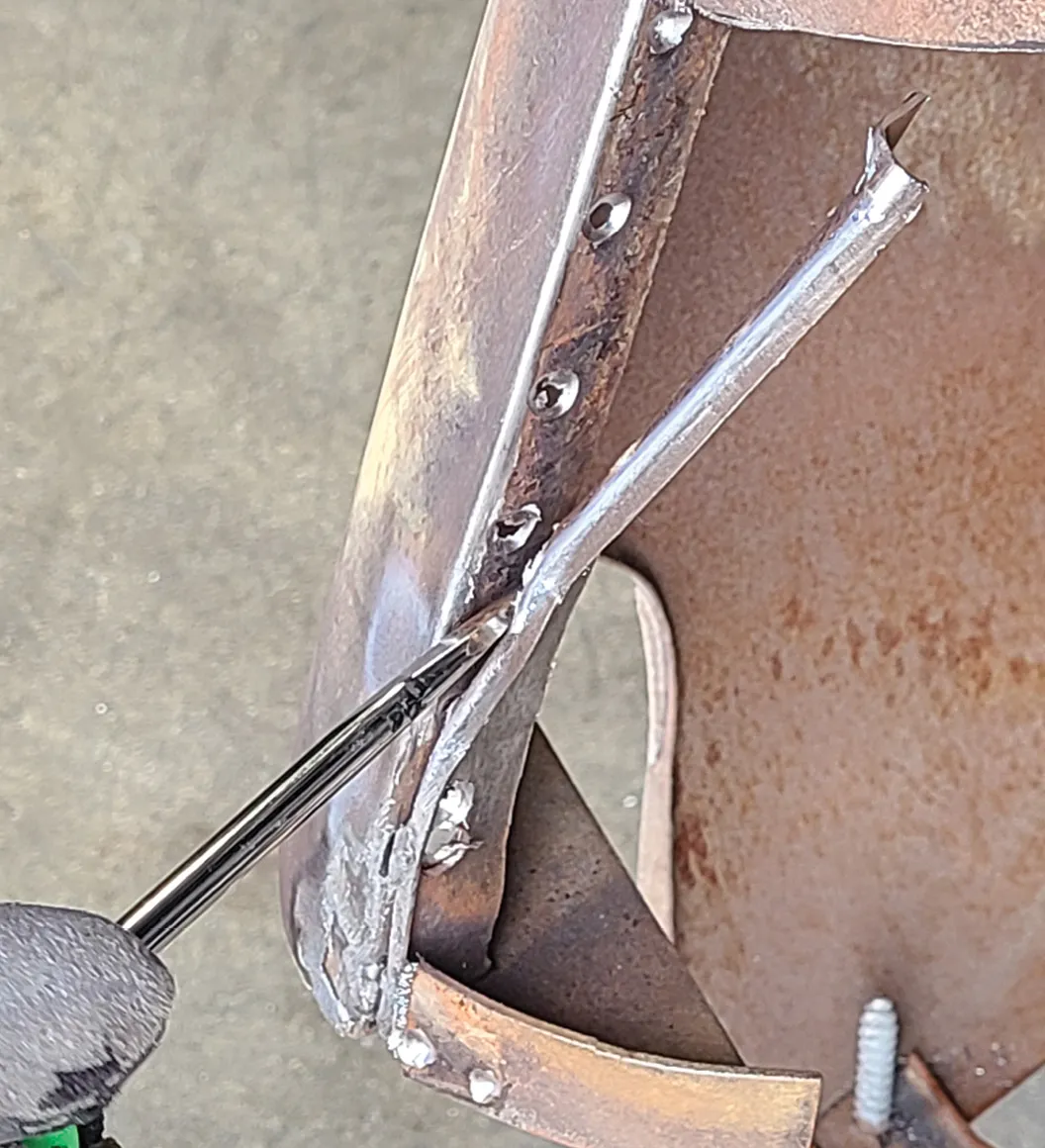
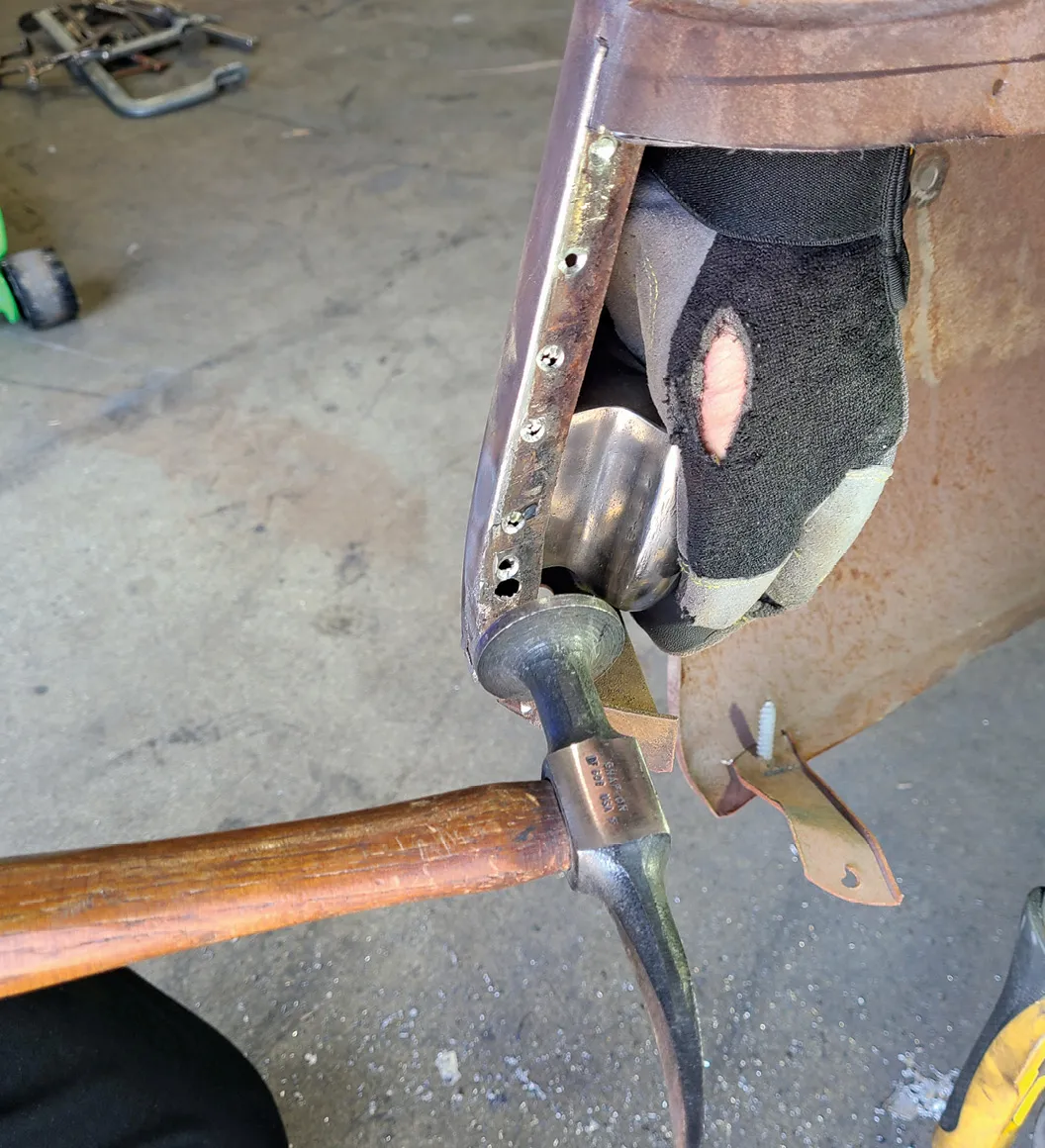




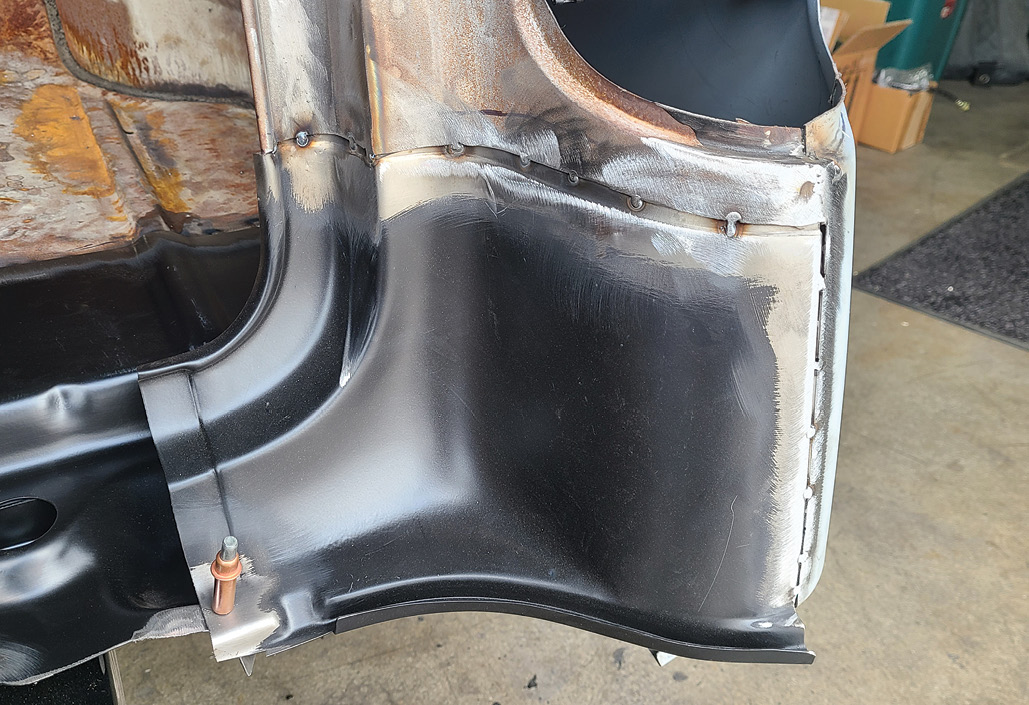
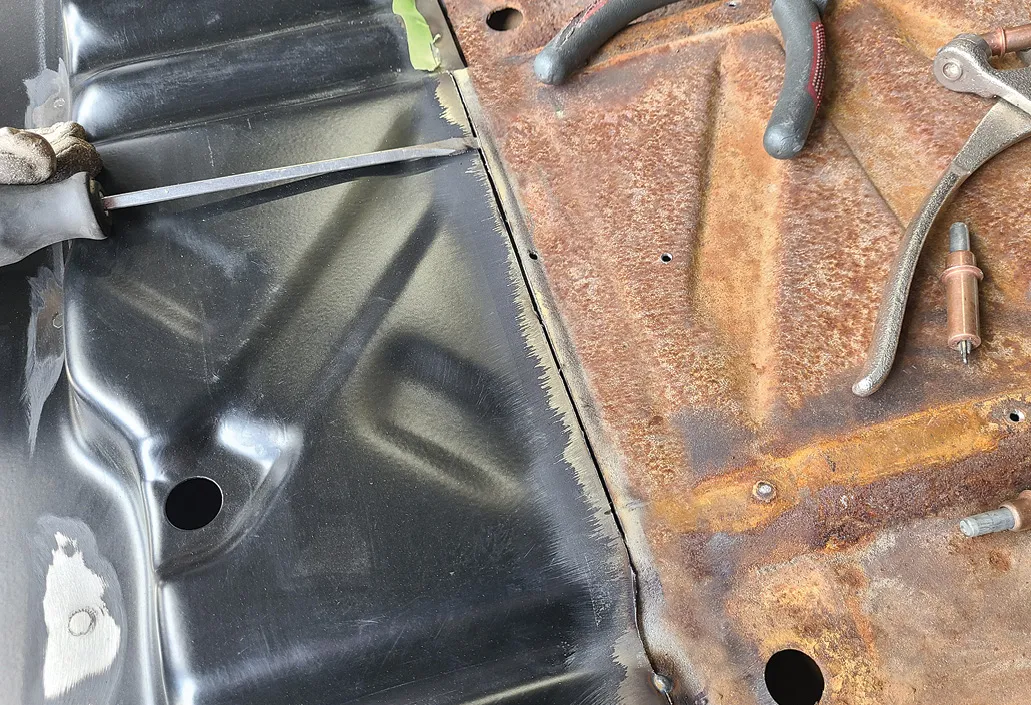
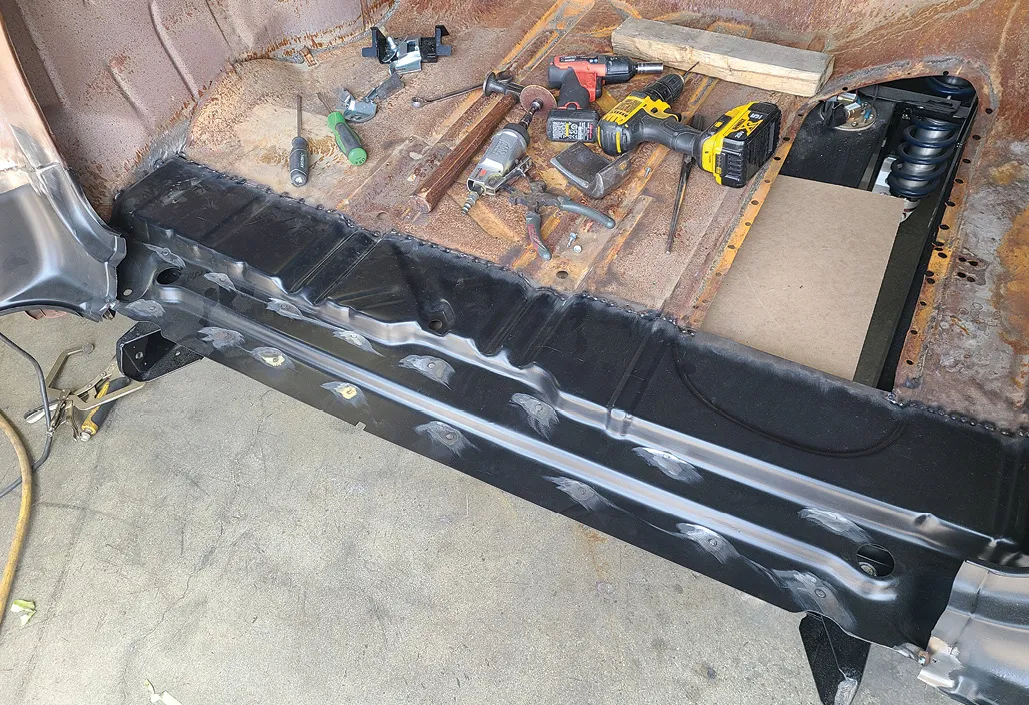

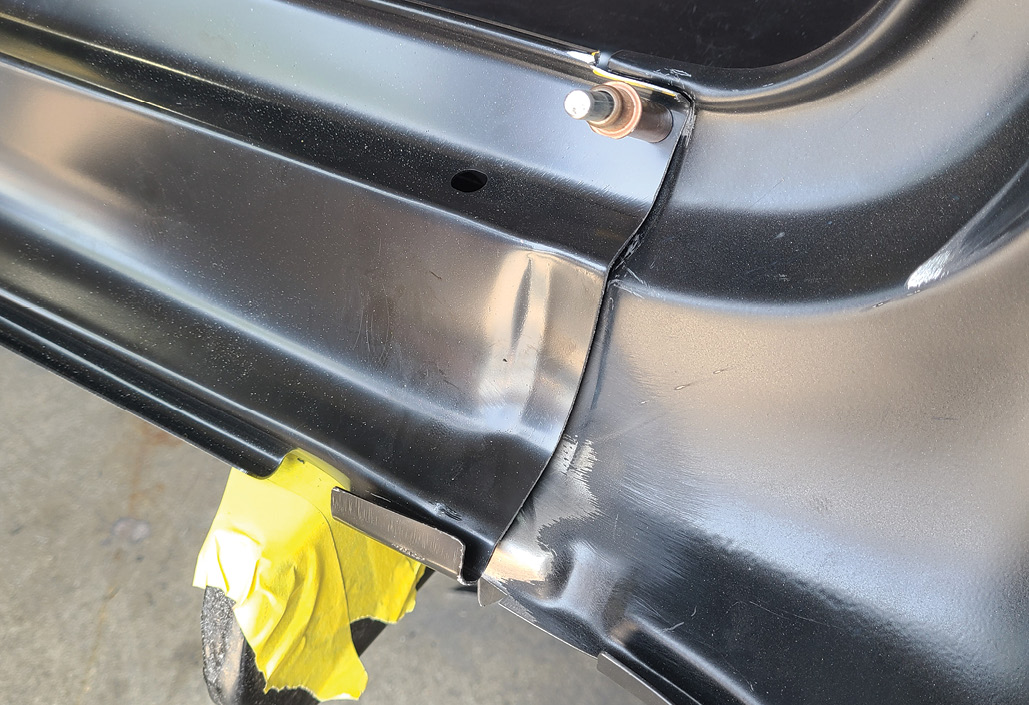


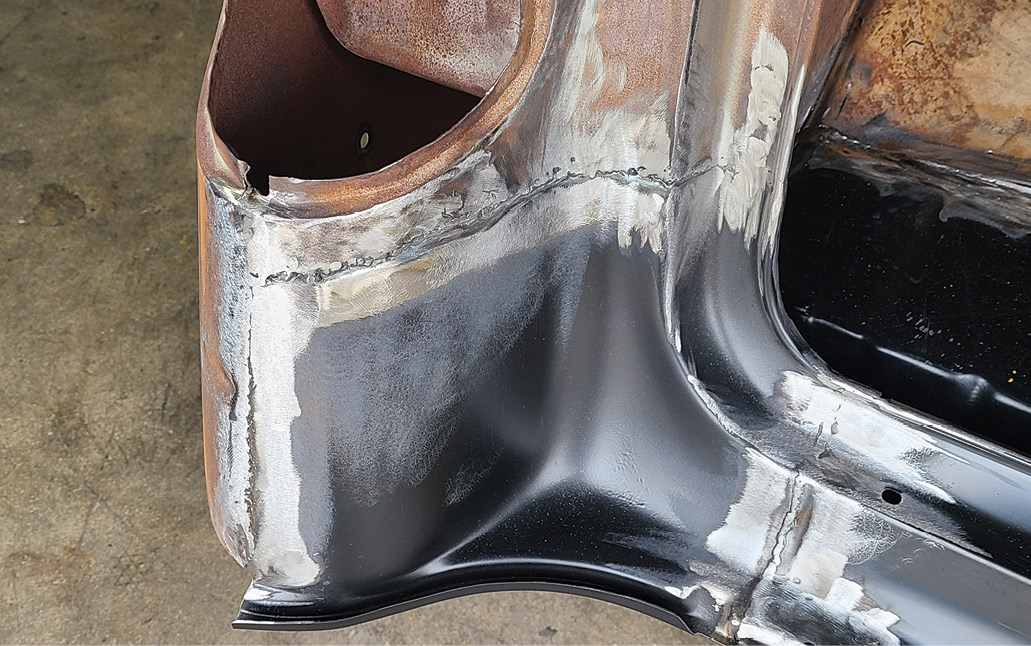
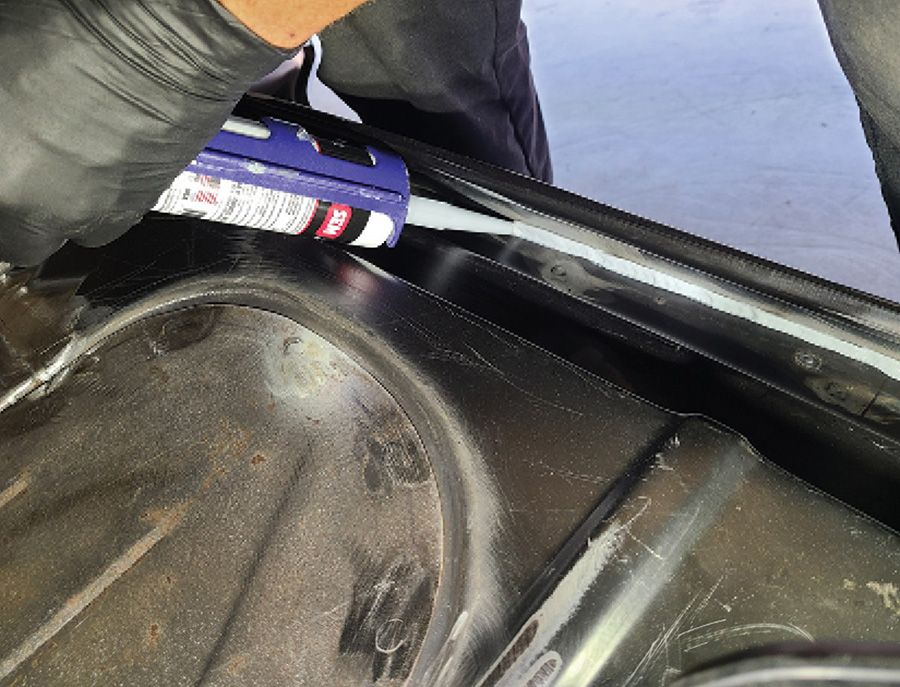
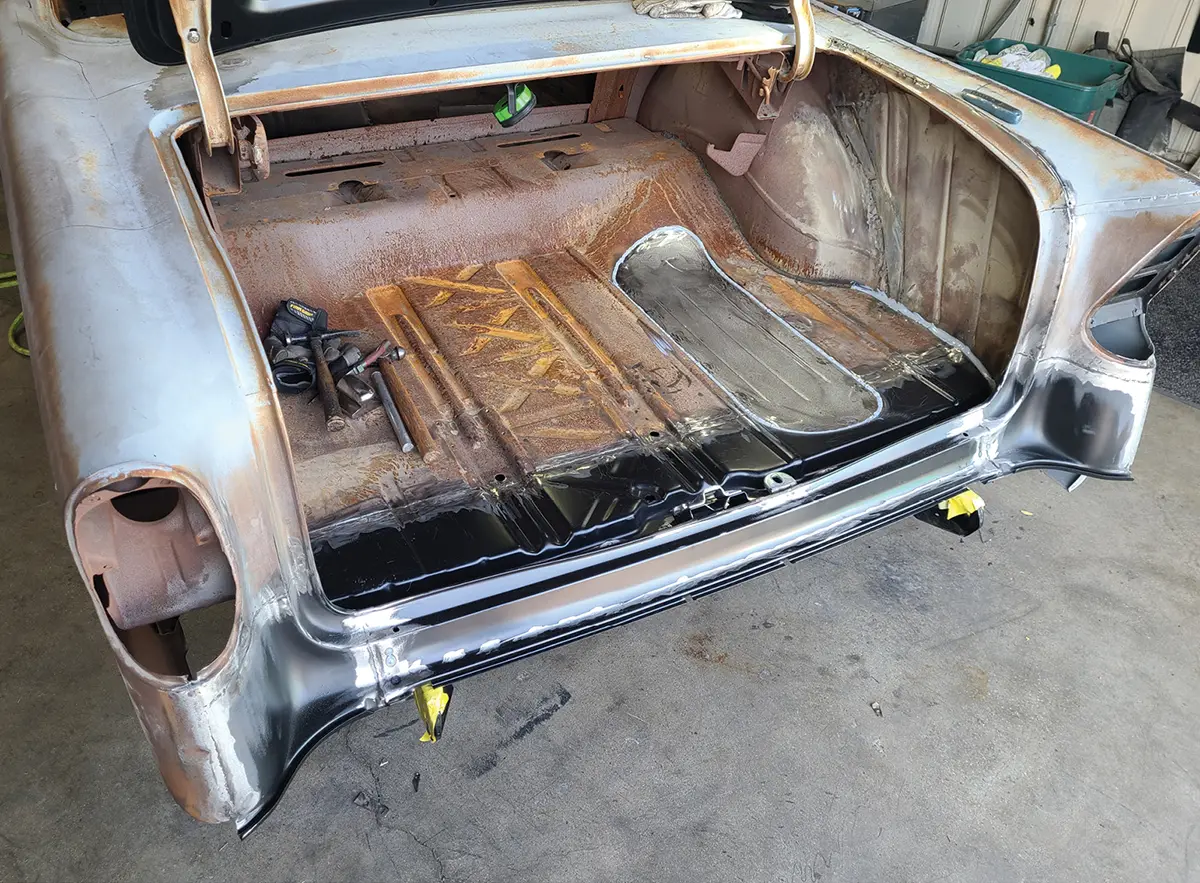
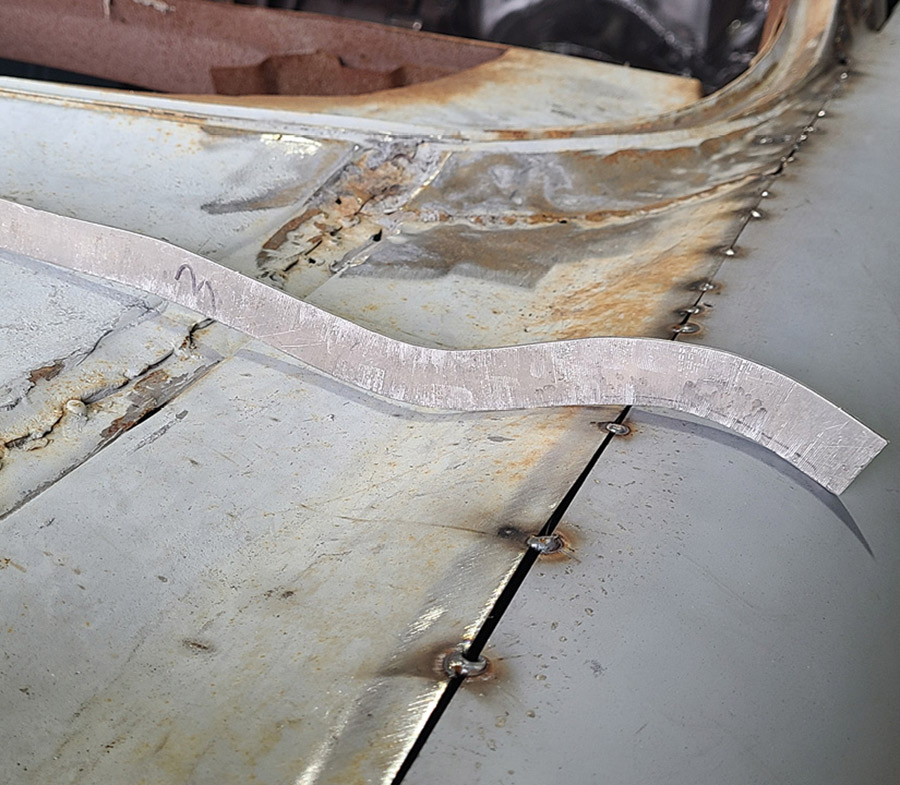
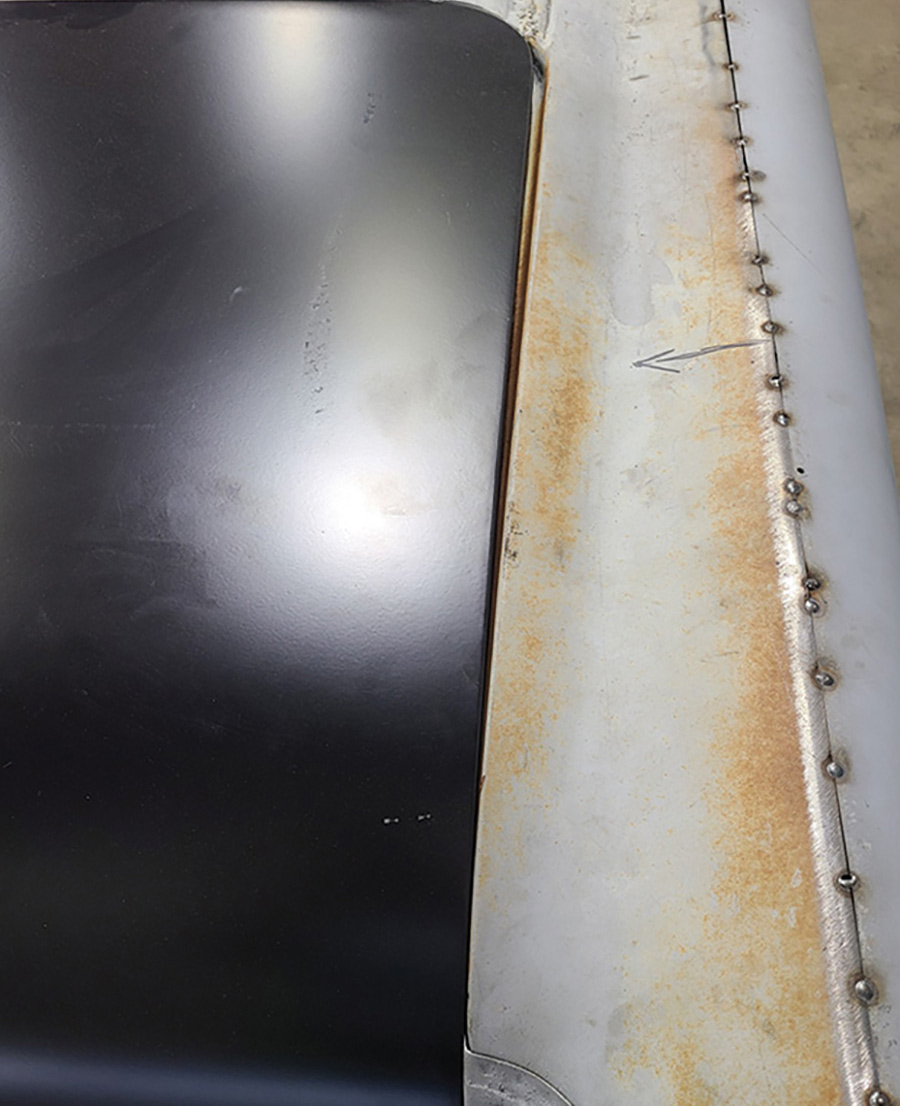

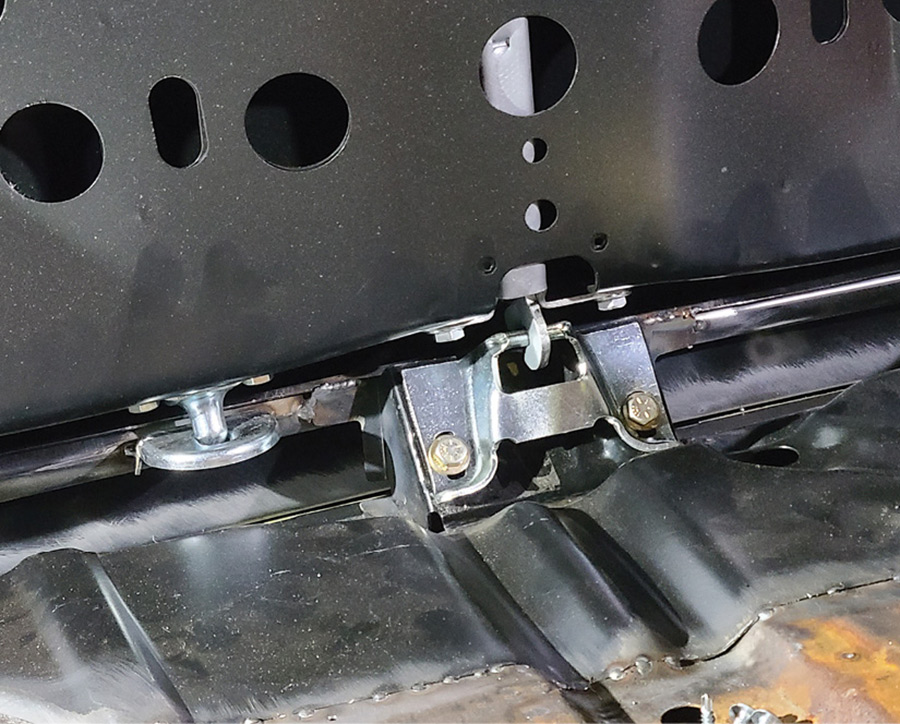
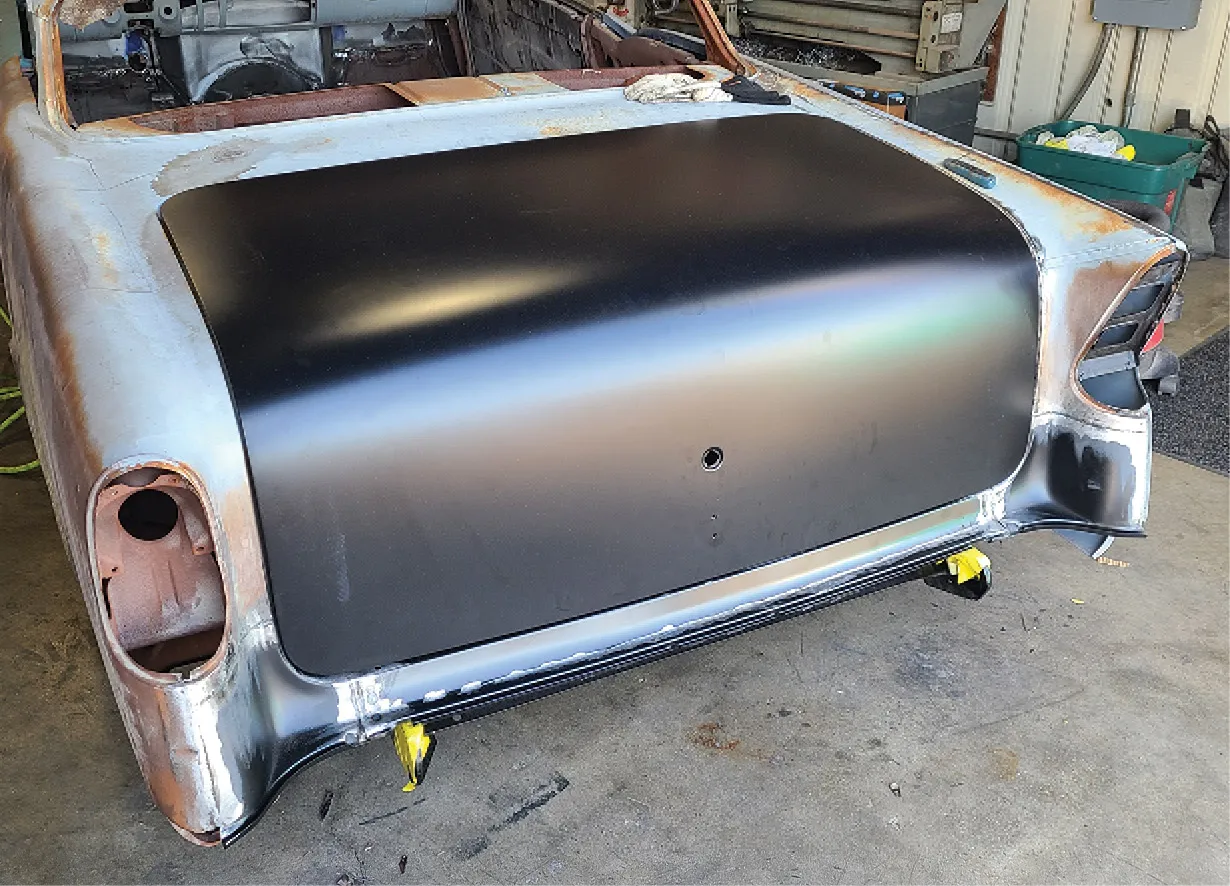

VOLUME 4 • ISSUE 37 • 2023