Modern Rodding TECH
InTheGarageMedia.com
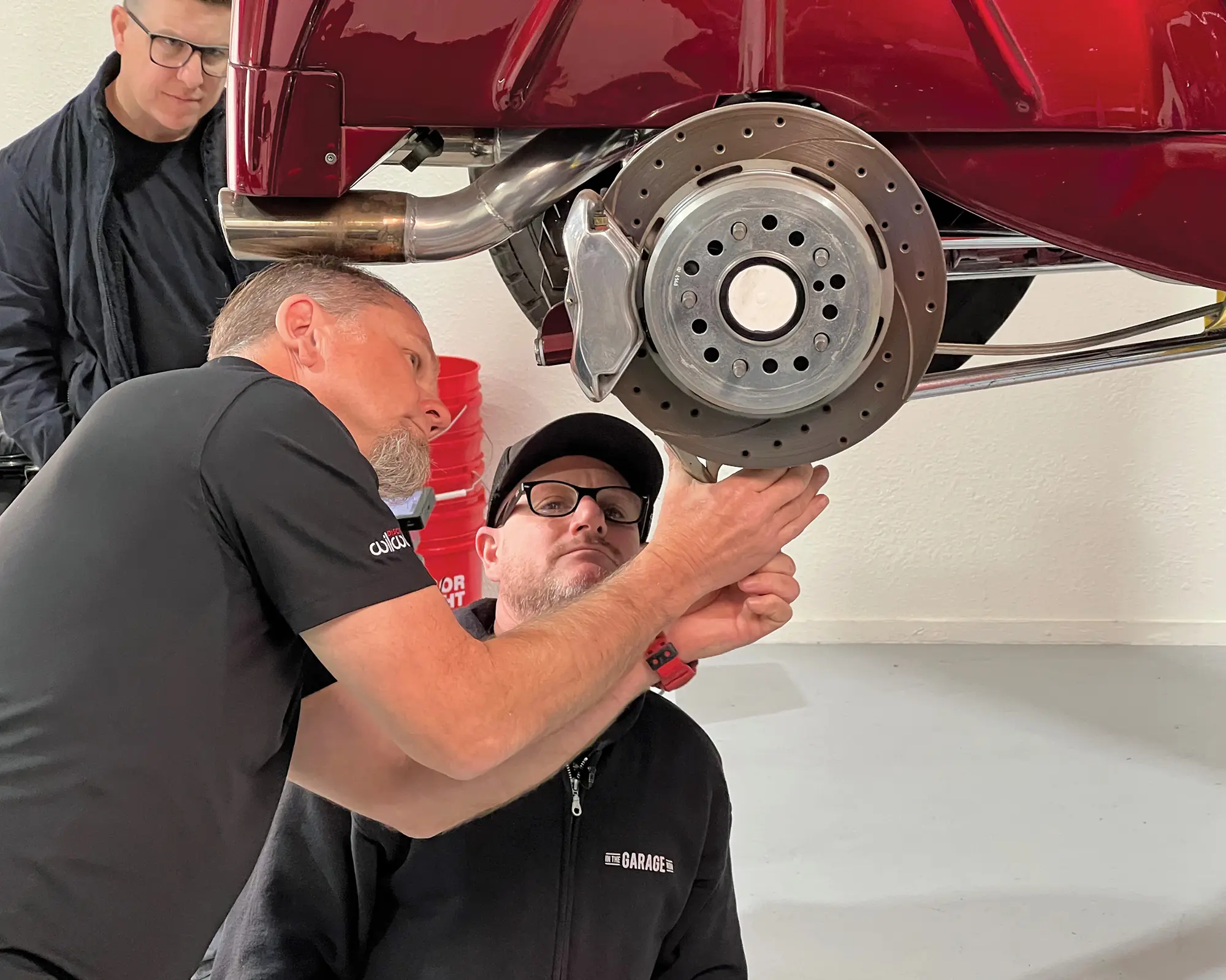
Photography by BRIAN BRENNAN
Videography by RYAN FOSS PRODUCTIONS

nyone who has been around performance vehicles recognizes the name Wilwood Engineering. Founded by Bill Wood in 1977, Wilwood is a leading manufacturer of cutting-edge, high-performance disc brakes and related components. One of their newest products is the Electric Parking Brake (EPB) system that eliminates cables and conventional actuation levers. Wilwood’s EPB kits include calipers, pads, brackets, hardware, control module, switch, wiring harness, and detailed installation instructions.
It’s interesting how the description of some automotive parts has changed over the years. As an example, the term emergency brake was once used to describe the system that was originally intended to be used in the case of a main brake system failure (not to mention Brennan by name, but lots of older editors still call it the emergency brake). Of course, as automobile technology evolved there was often a change in nomenclature as well and the emergency brake came to be more accurately described as the parking brake for obvious reasons. But regardless of what you call it, hot rods need one. Relying on leaving your car in gear or in Park can be risky. Take it from someone who watched his roadster try to roll away when it was assumed to be in Park and wasn’t as proof positive that an effective parking brake is a wise addition to any car.
Current is only required to turn the EPB calipers on and off. So should something unexpected happen, such as the wiring harness being damaged by a hot exhaust pipe while traveling, there is no chance that the system will apply with the car in motion. In addition, the indicator light on the control switch will flash if there is a fault in the system, such as damaged wiring.
Another obvious question is, “What happens if I store my car with the EPB set and the battery goes dead. As Mike Hamrick from Wilwood explains it, there are two simple solutions: charge the battery enough to release the brakes or take the wheels off and release the two 1/4-20 bolts that hold the electric motors in place so the pistons will release and the car may be moved.
Like every other brake product Wilwood offers, the EPB system is well designed, extremely effective, and good looking to boot. Some may still call a parking brake an emergency brake, but whatever you call it your hot rod should have one.
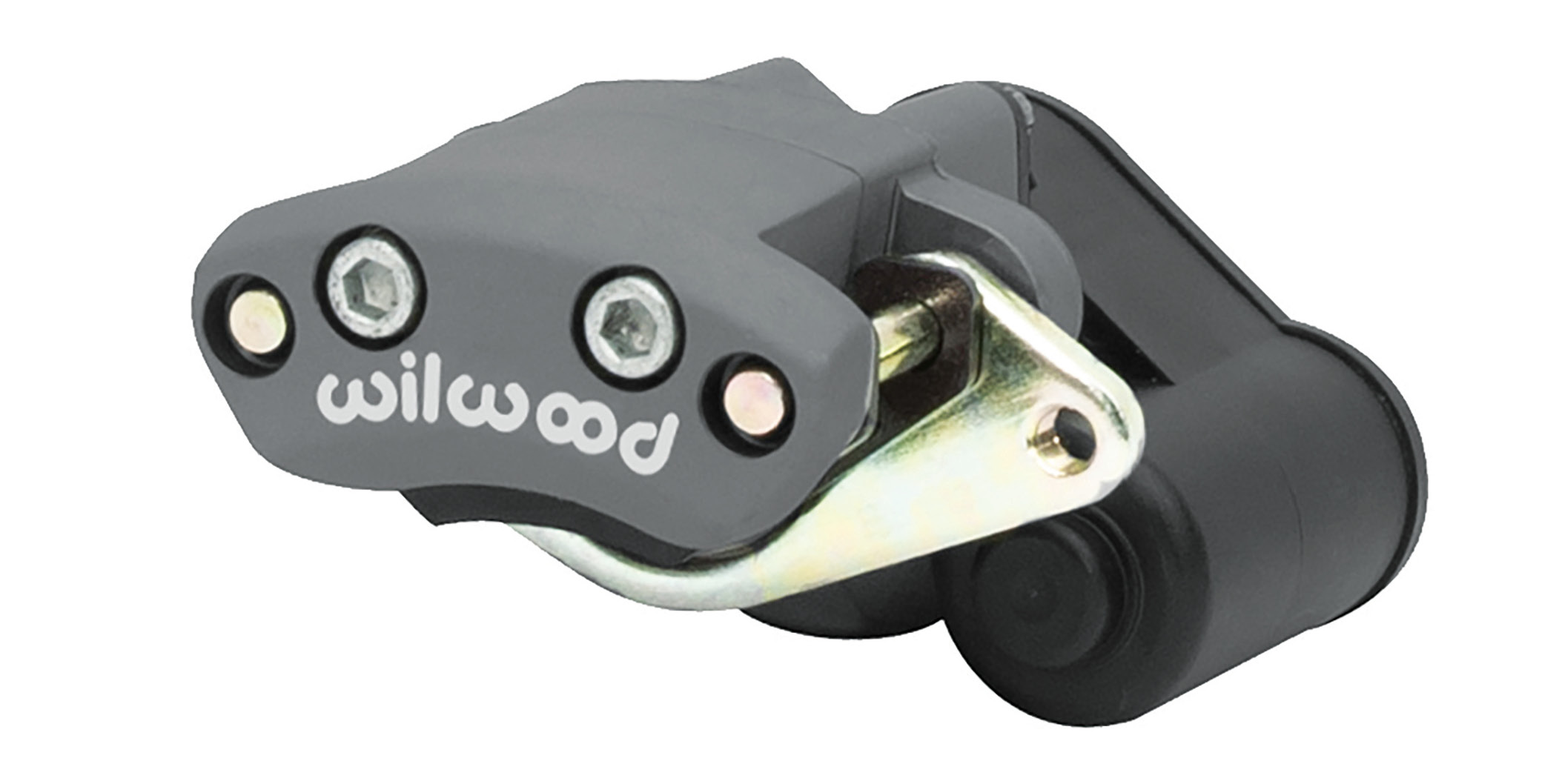
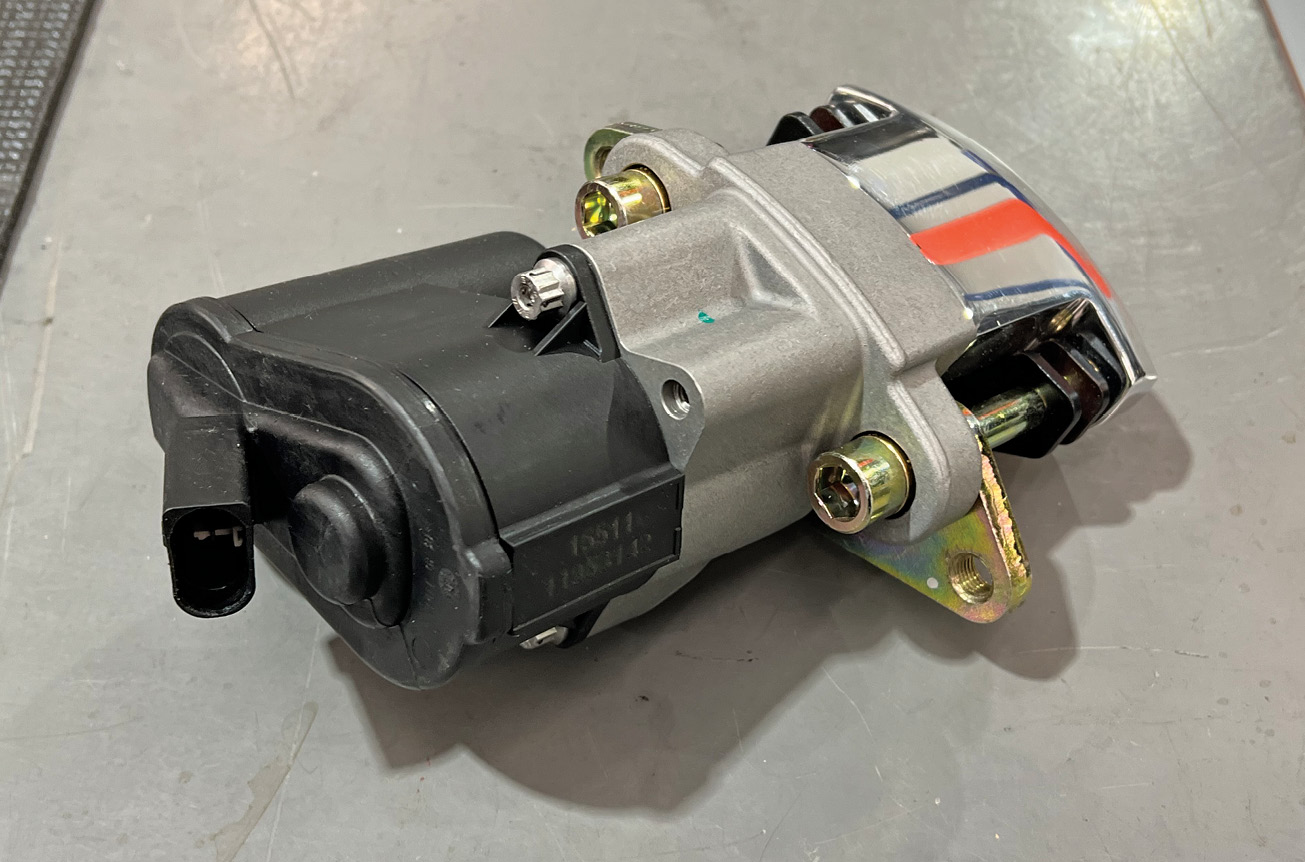
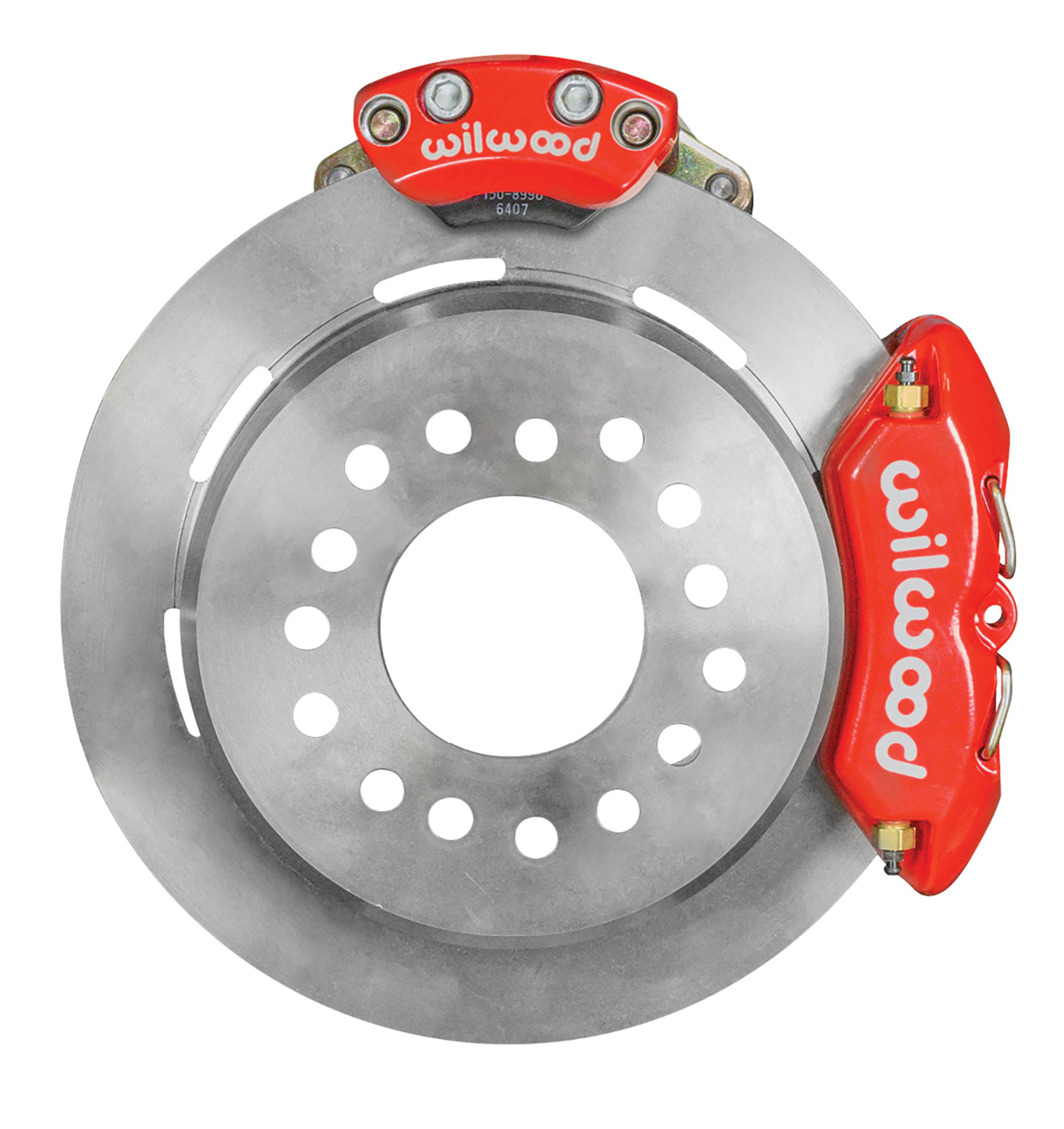
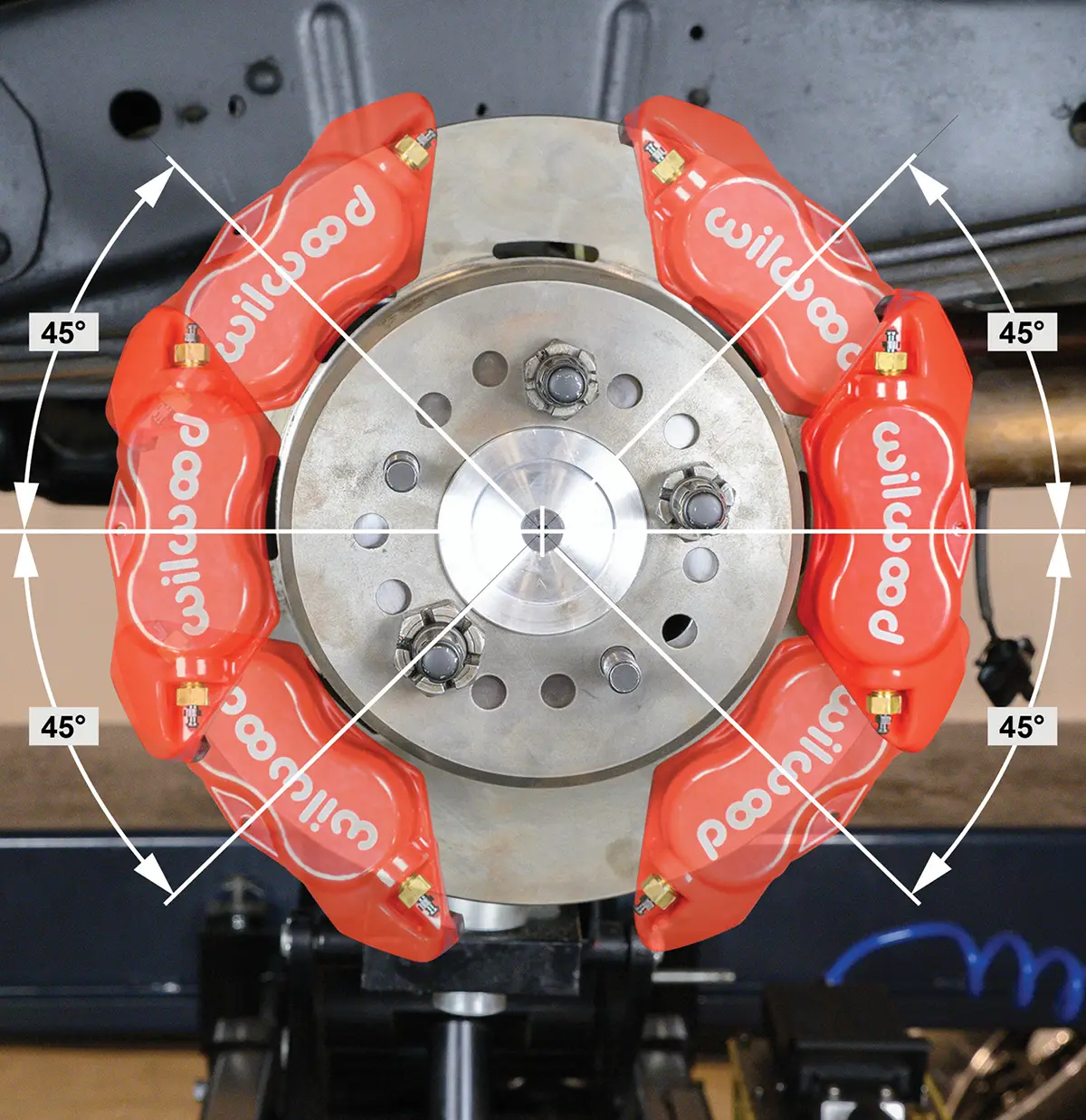
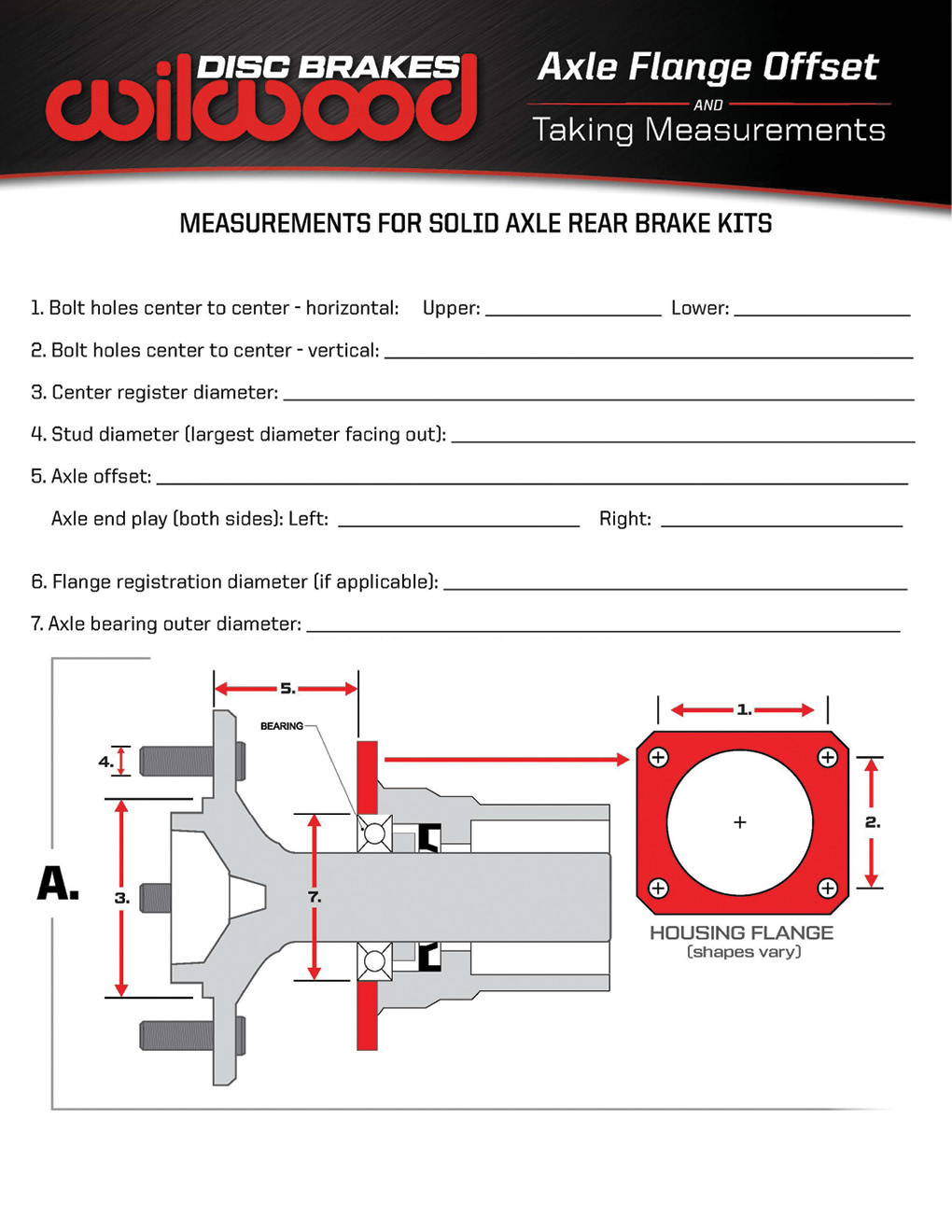
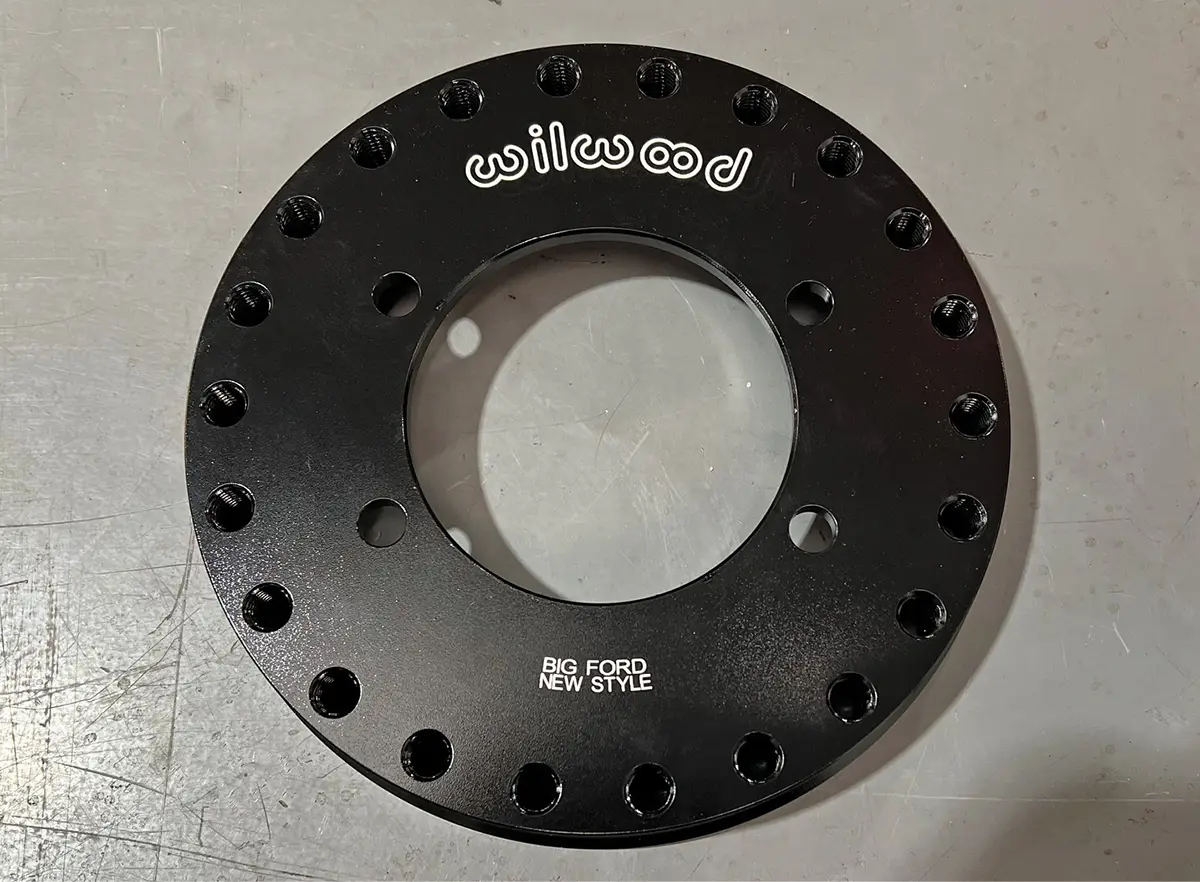
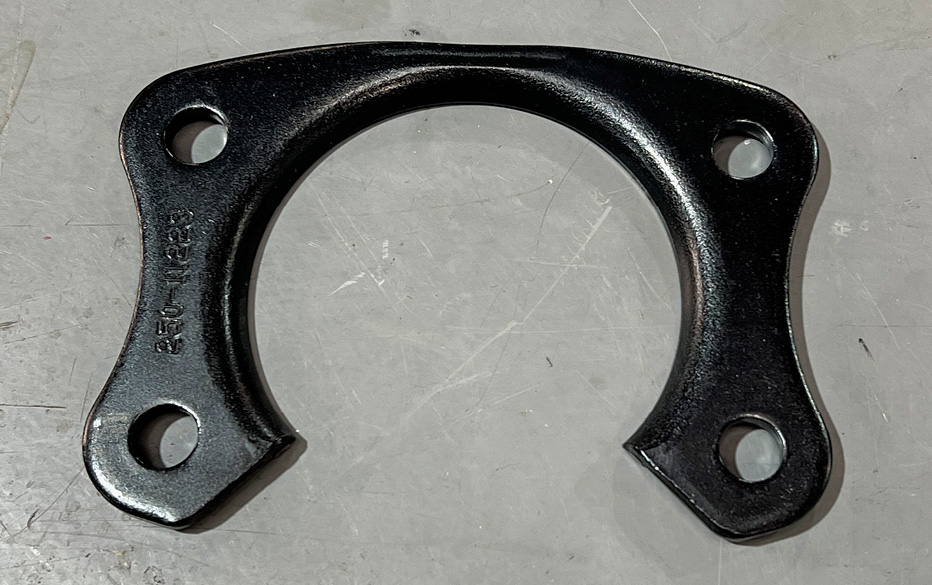
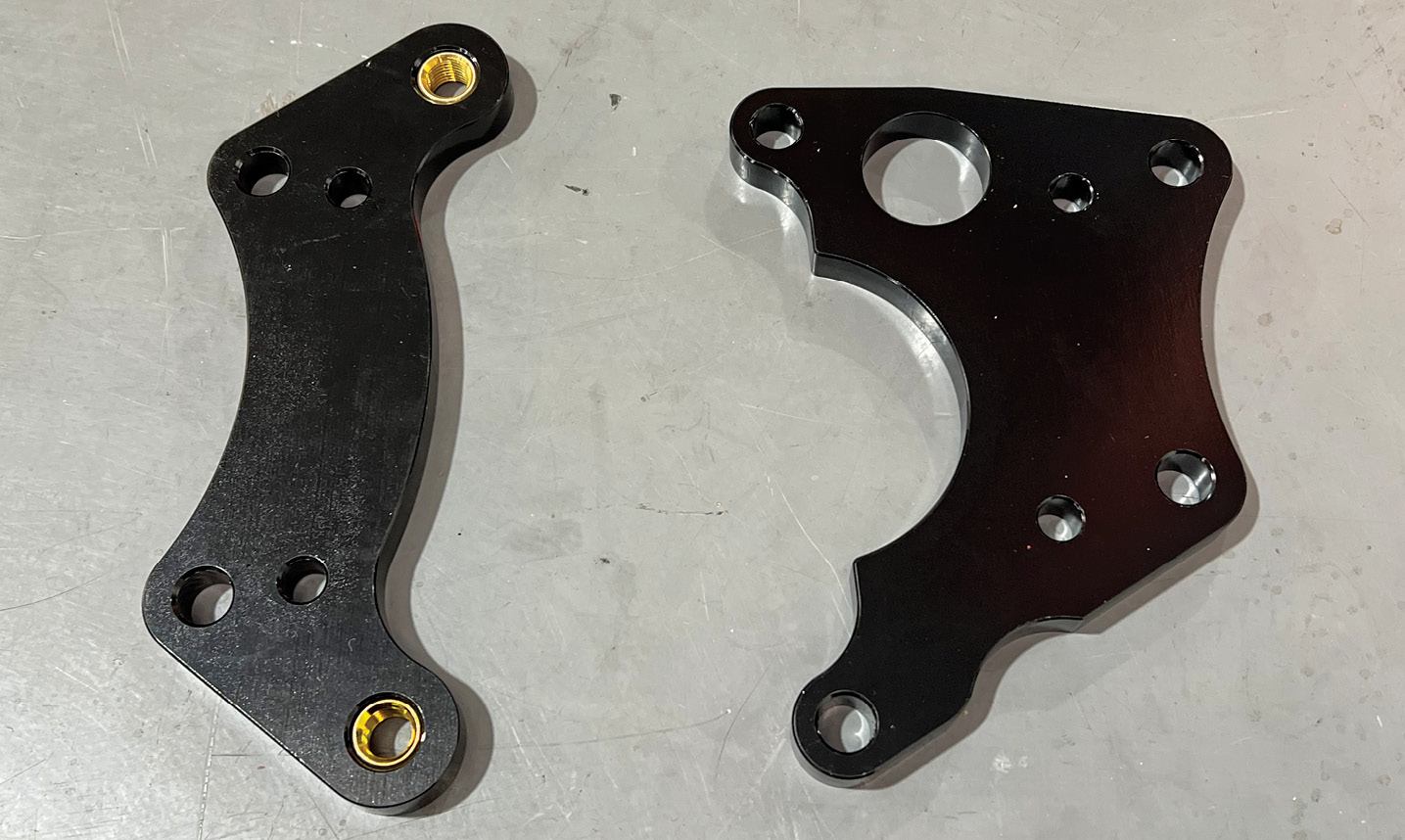
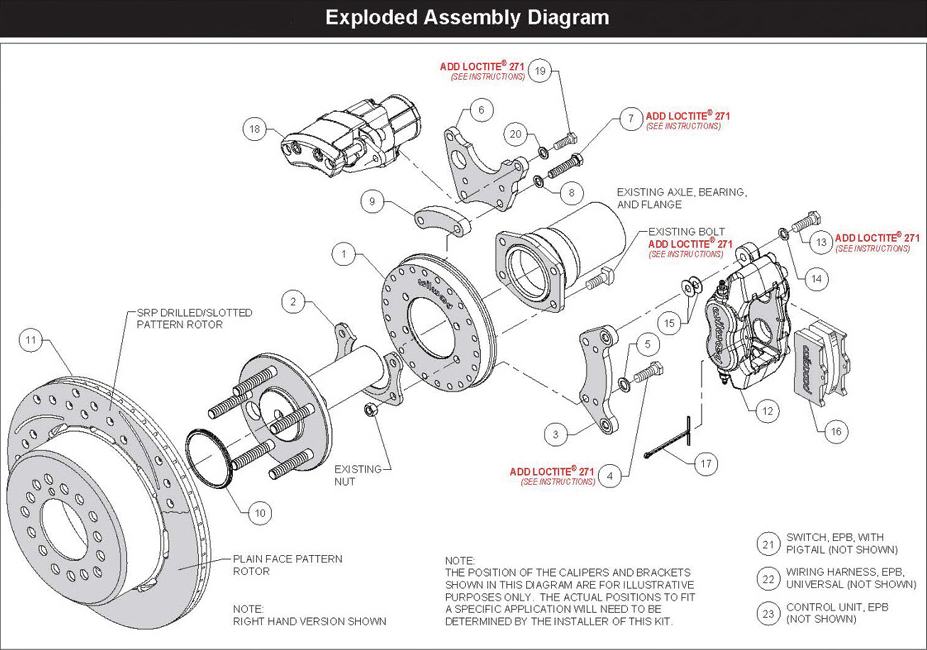
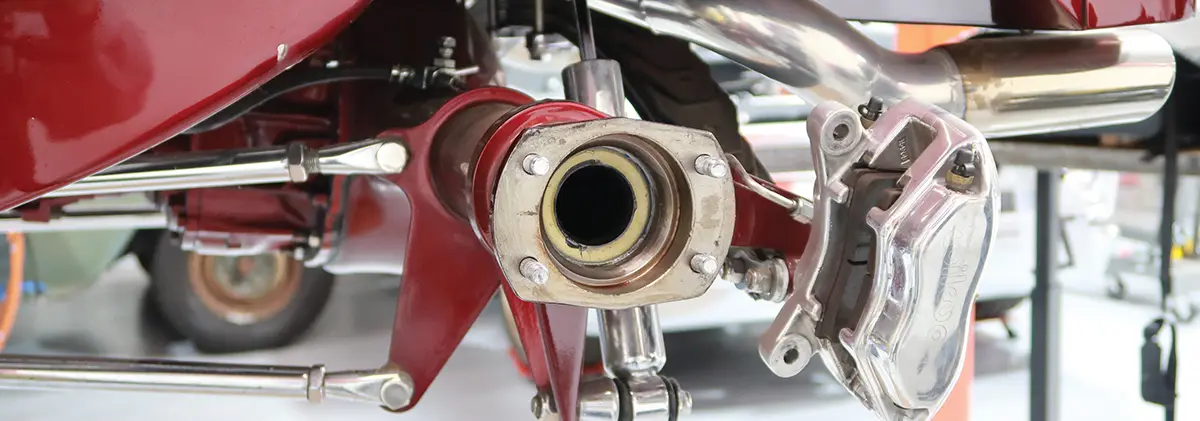
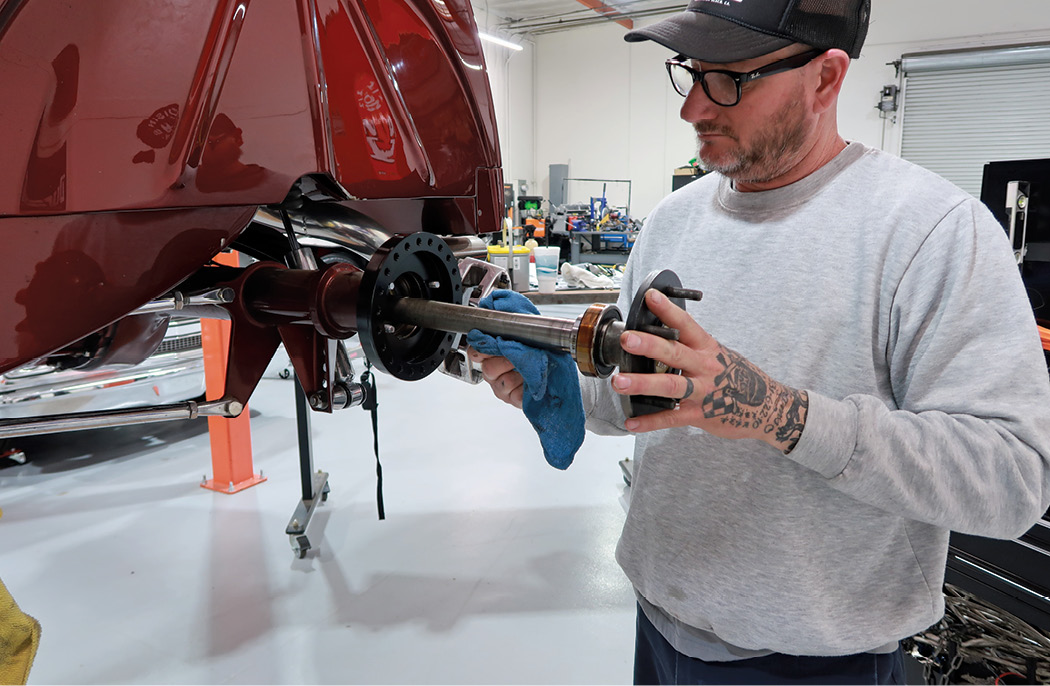
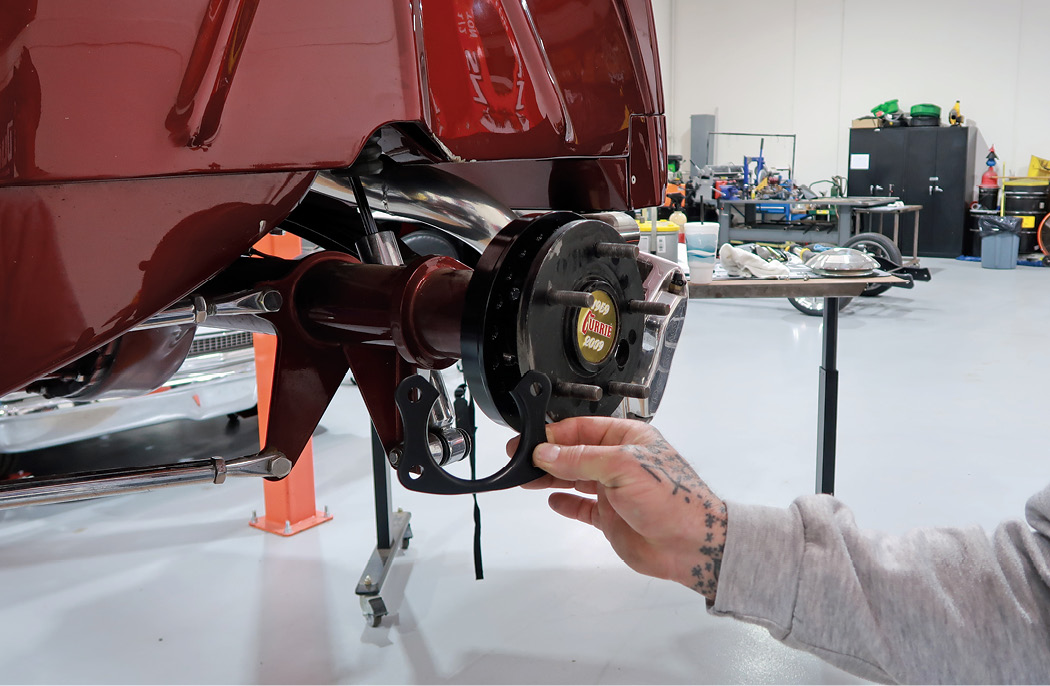
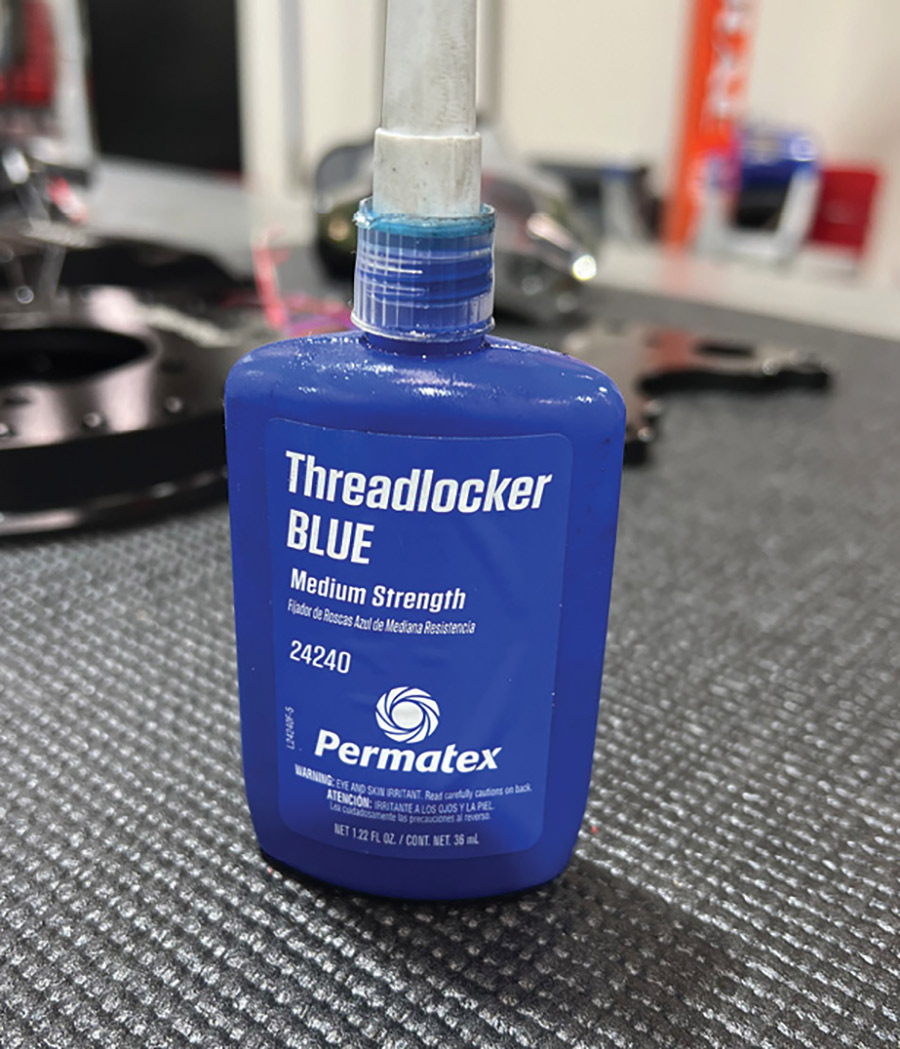
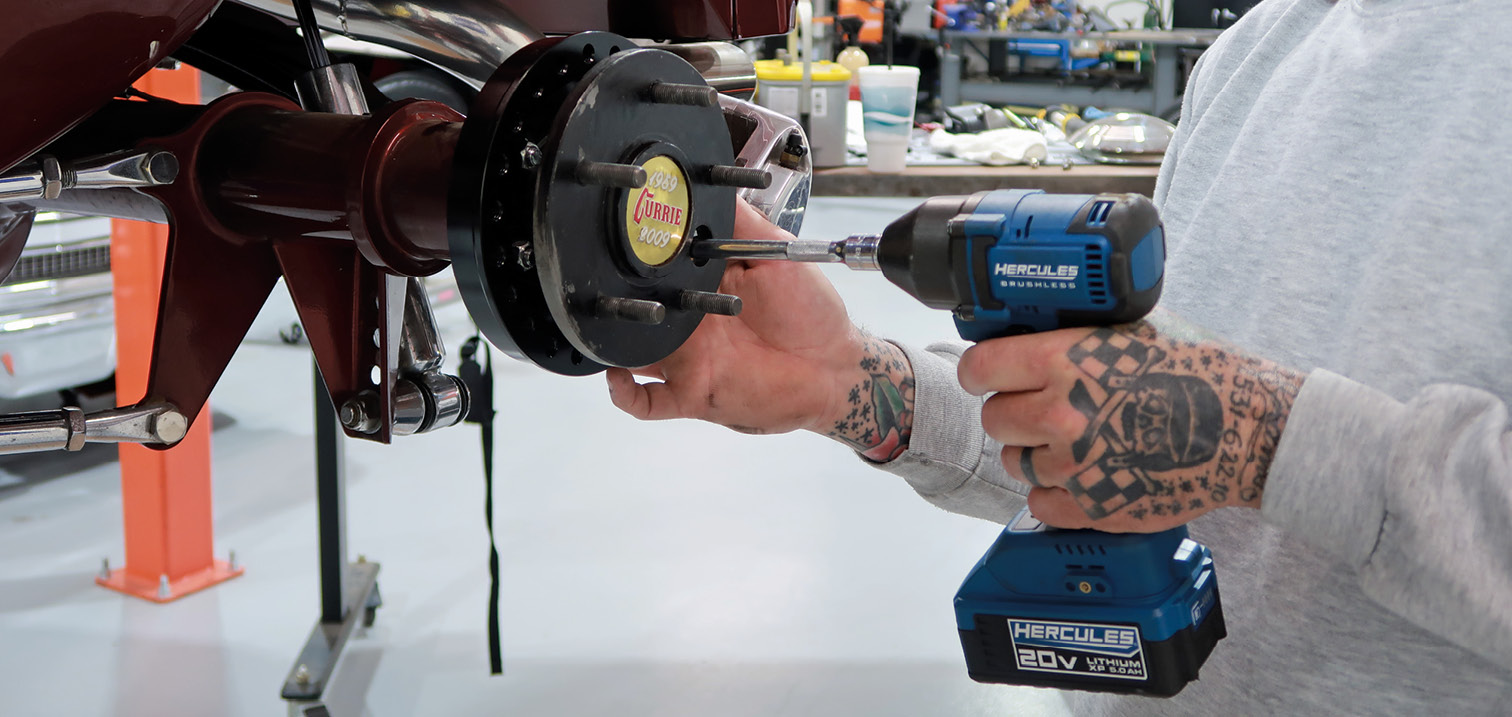
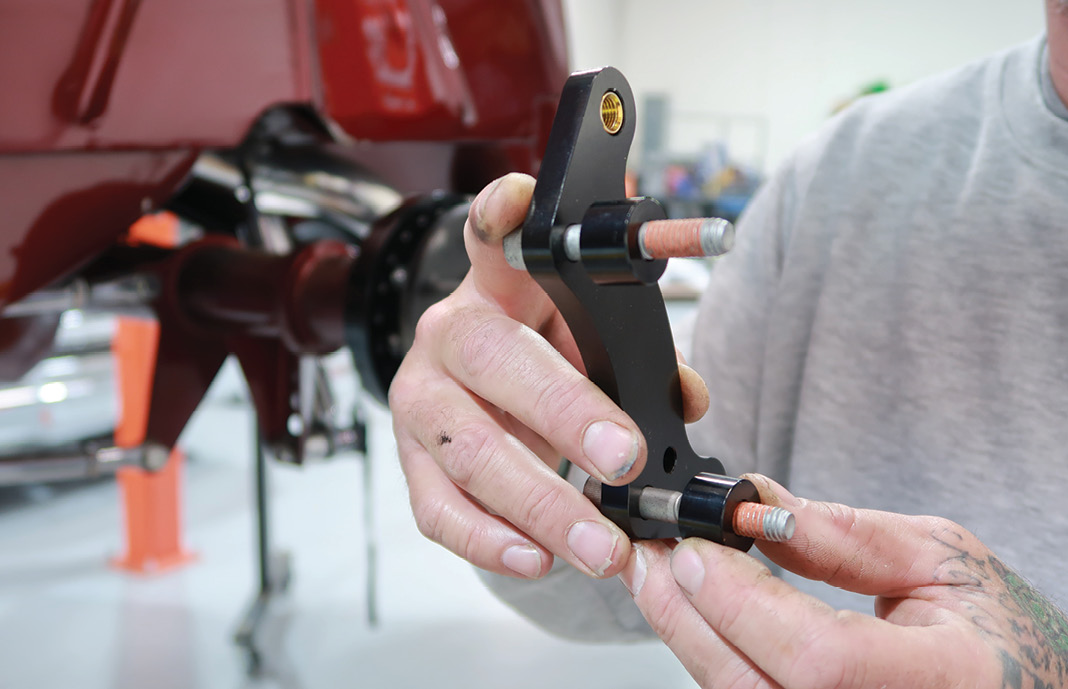
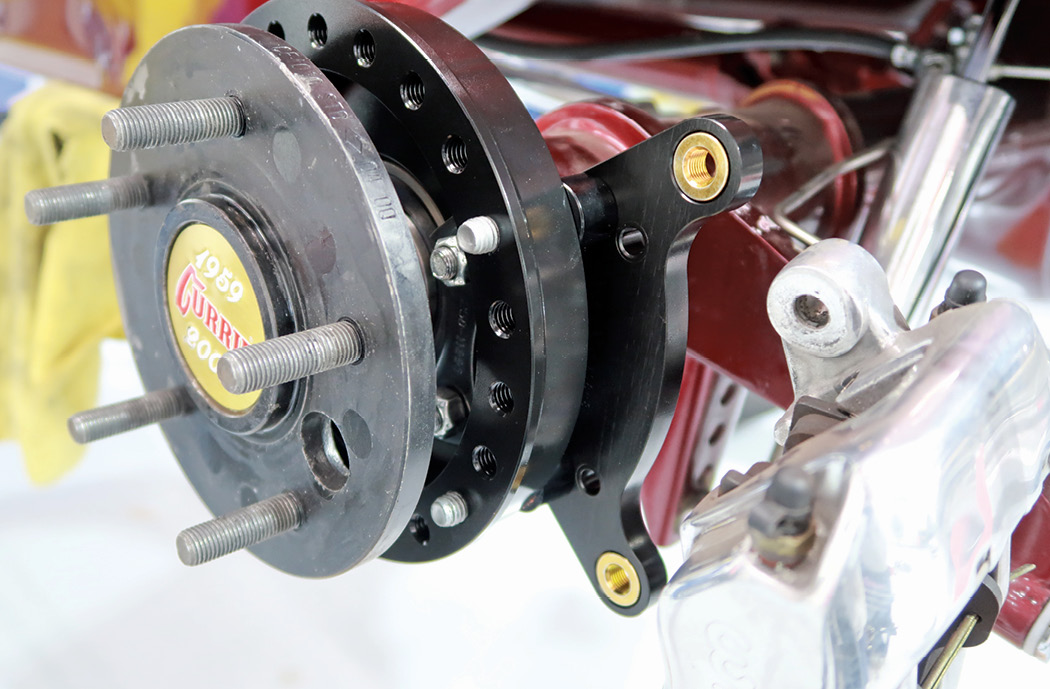
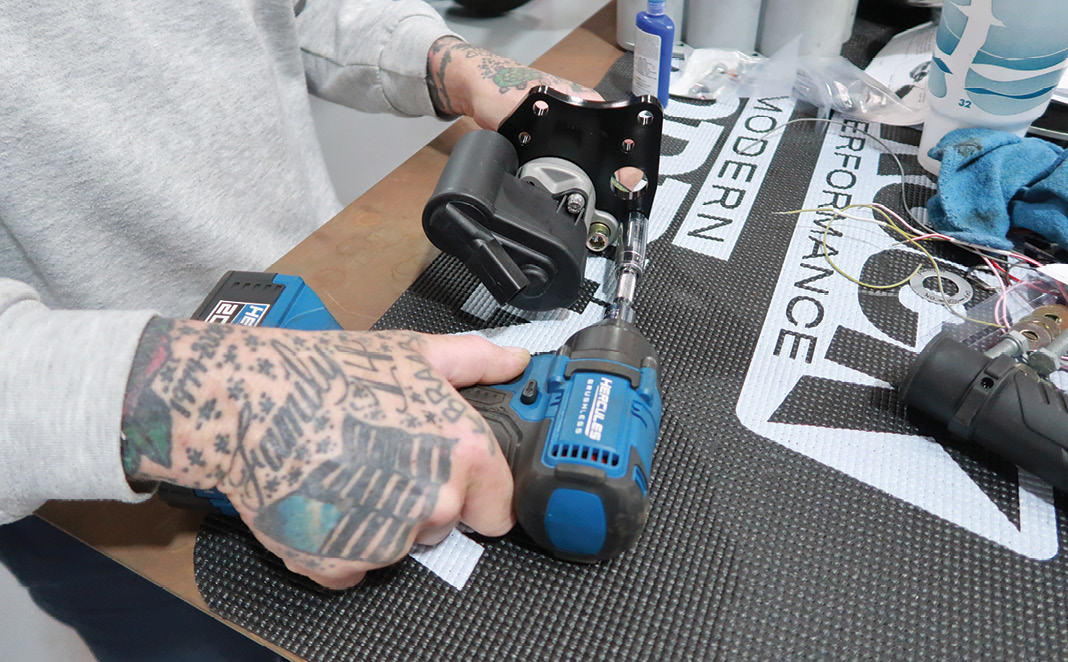
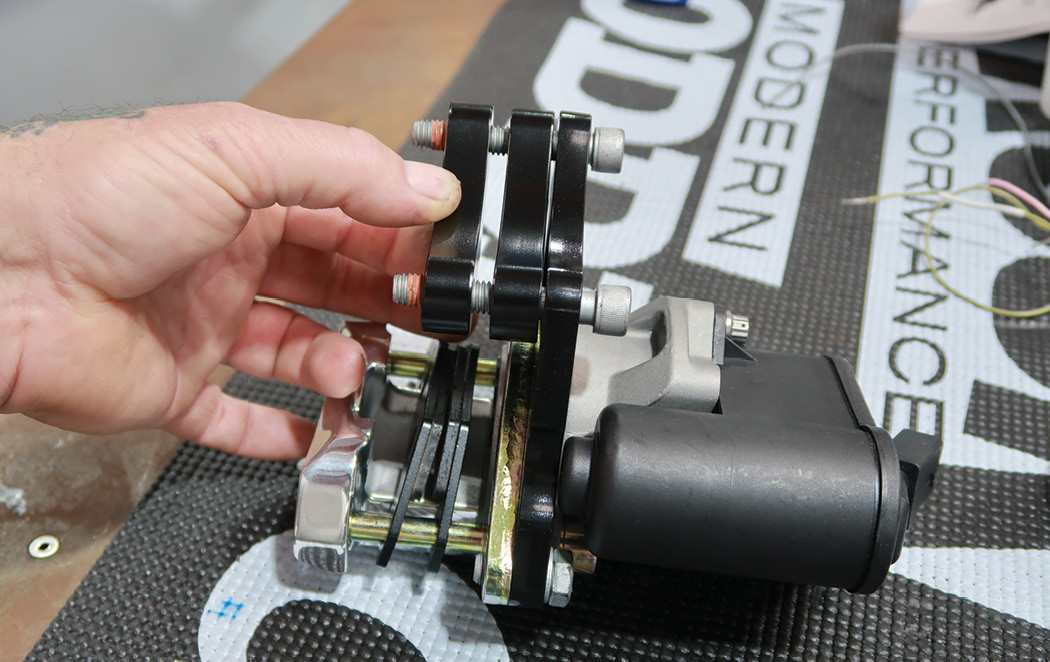
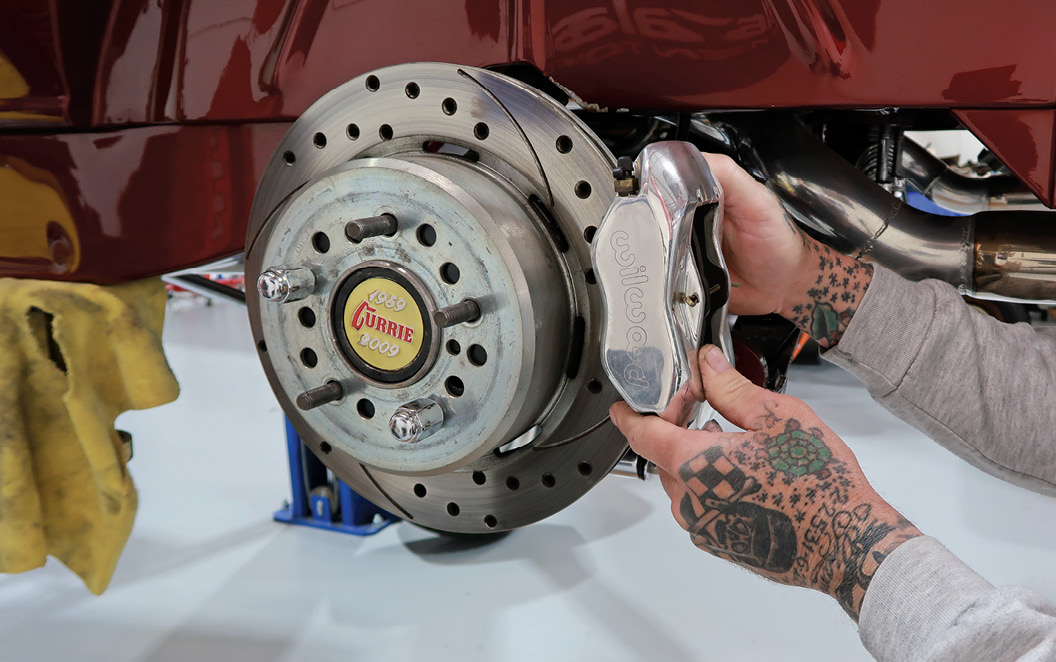
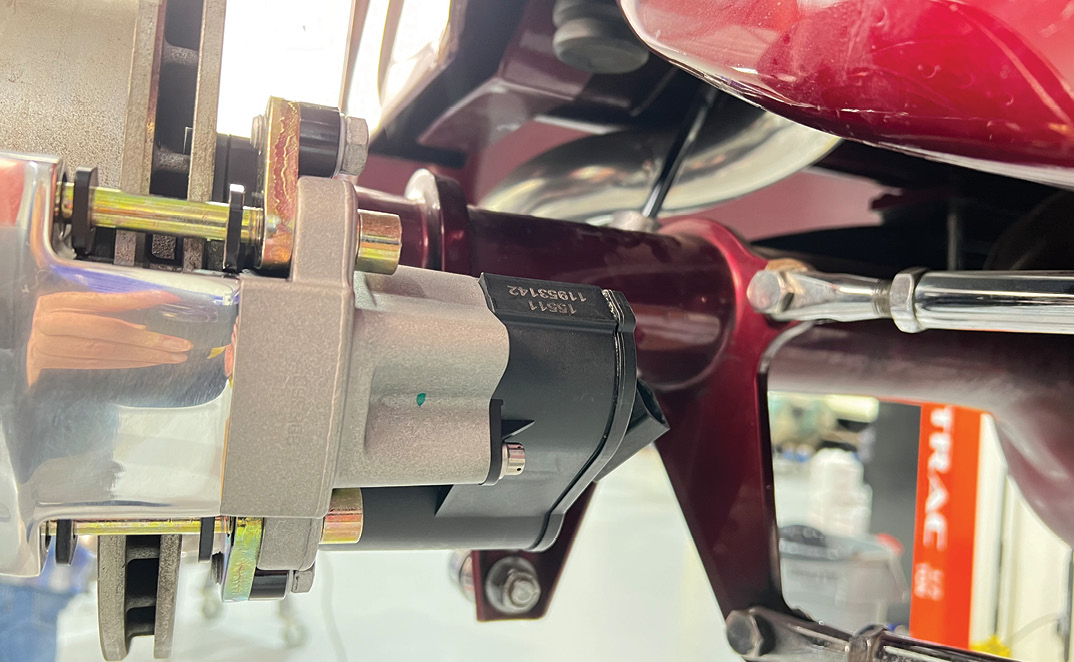
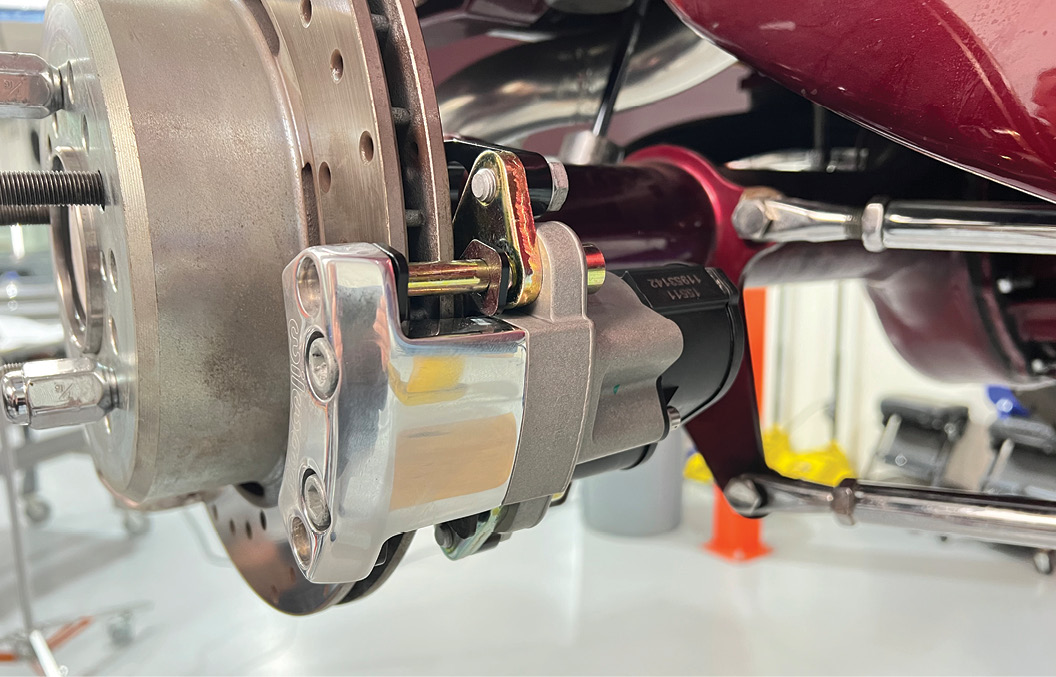
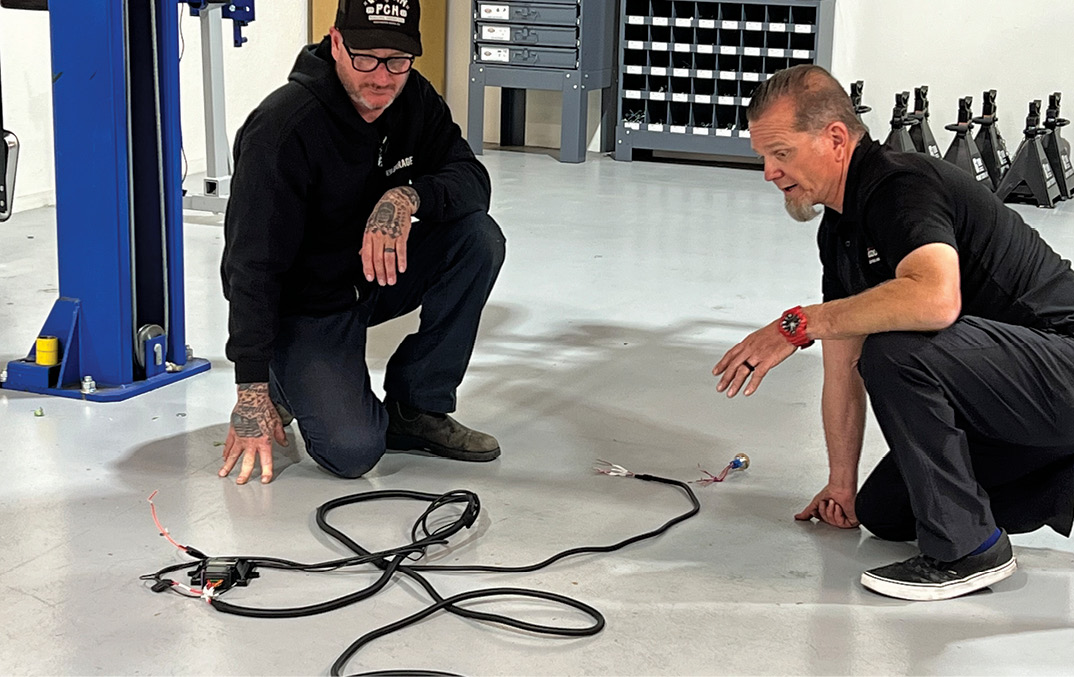
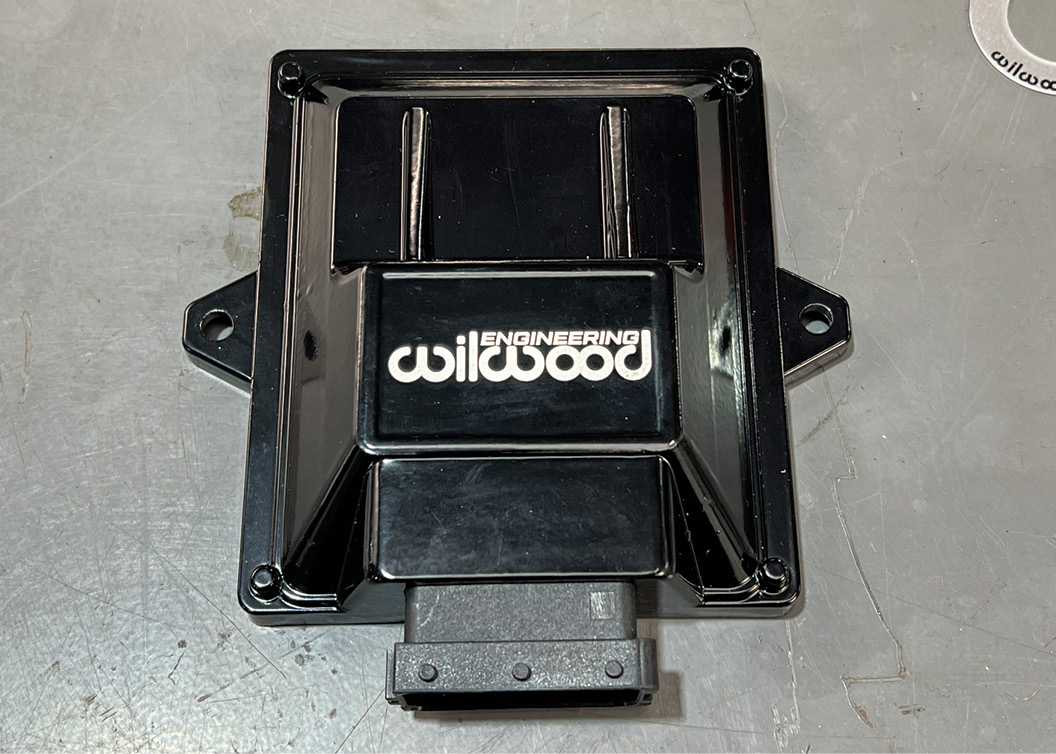
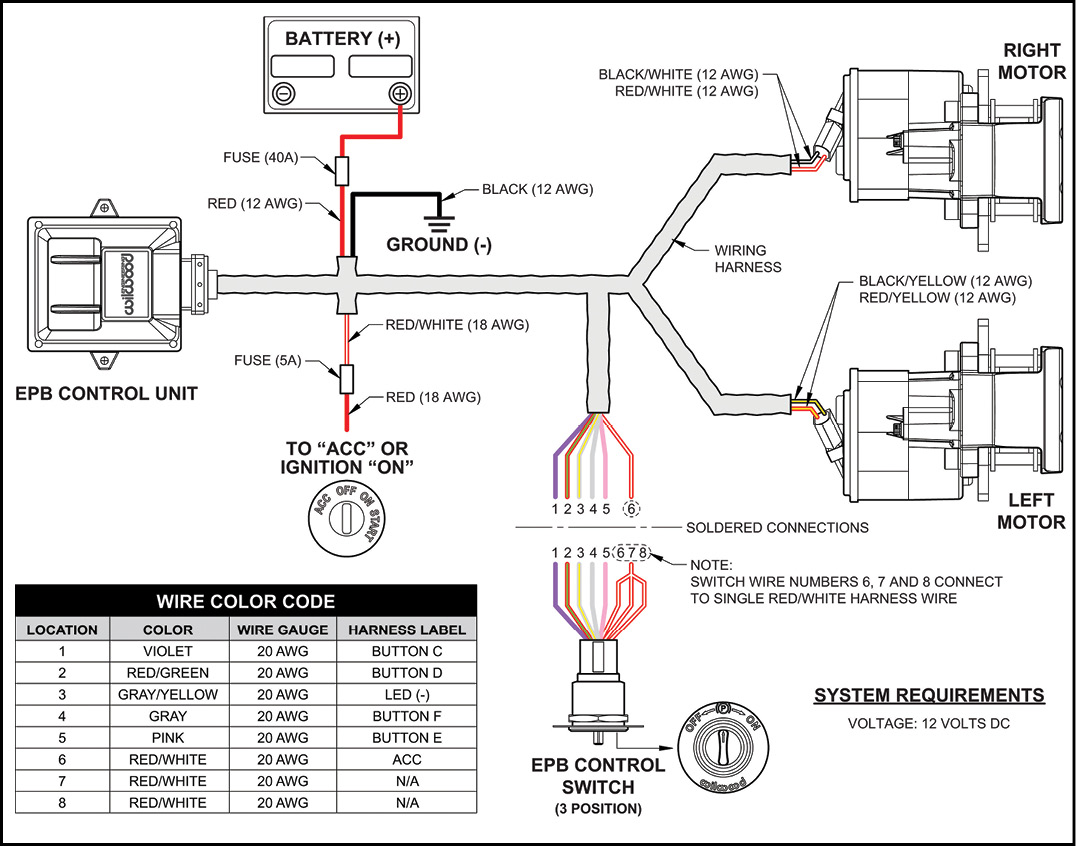
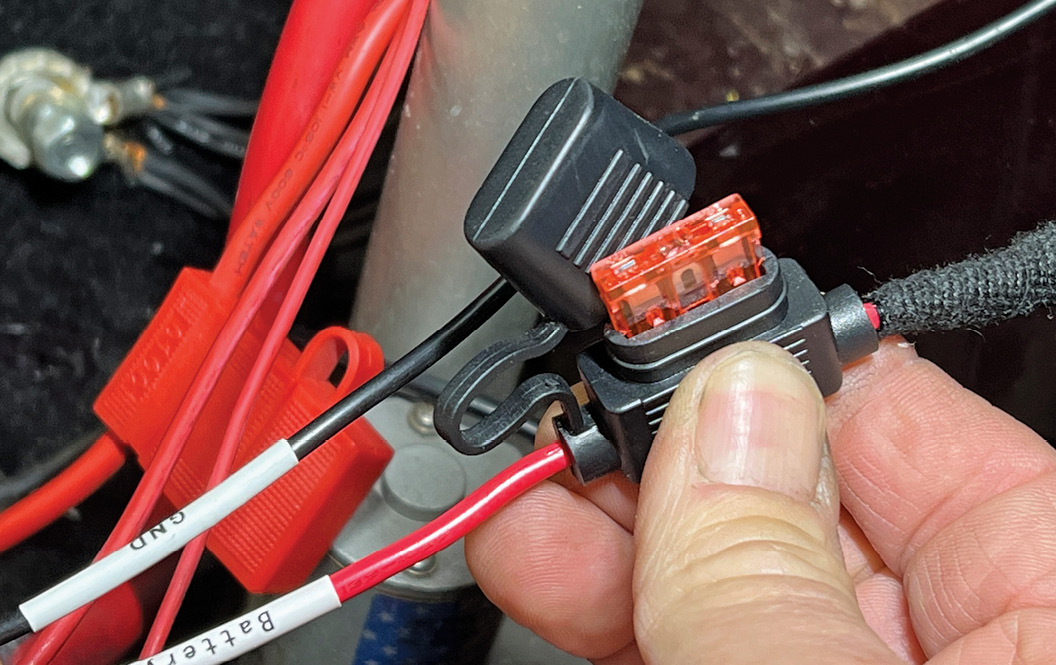
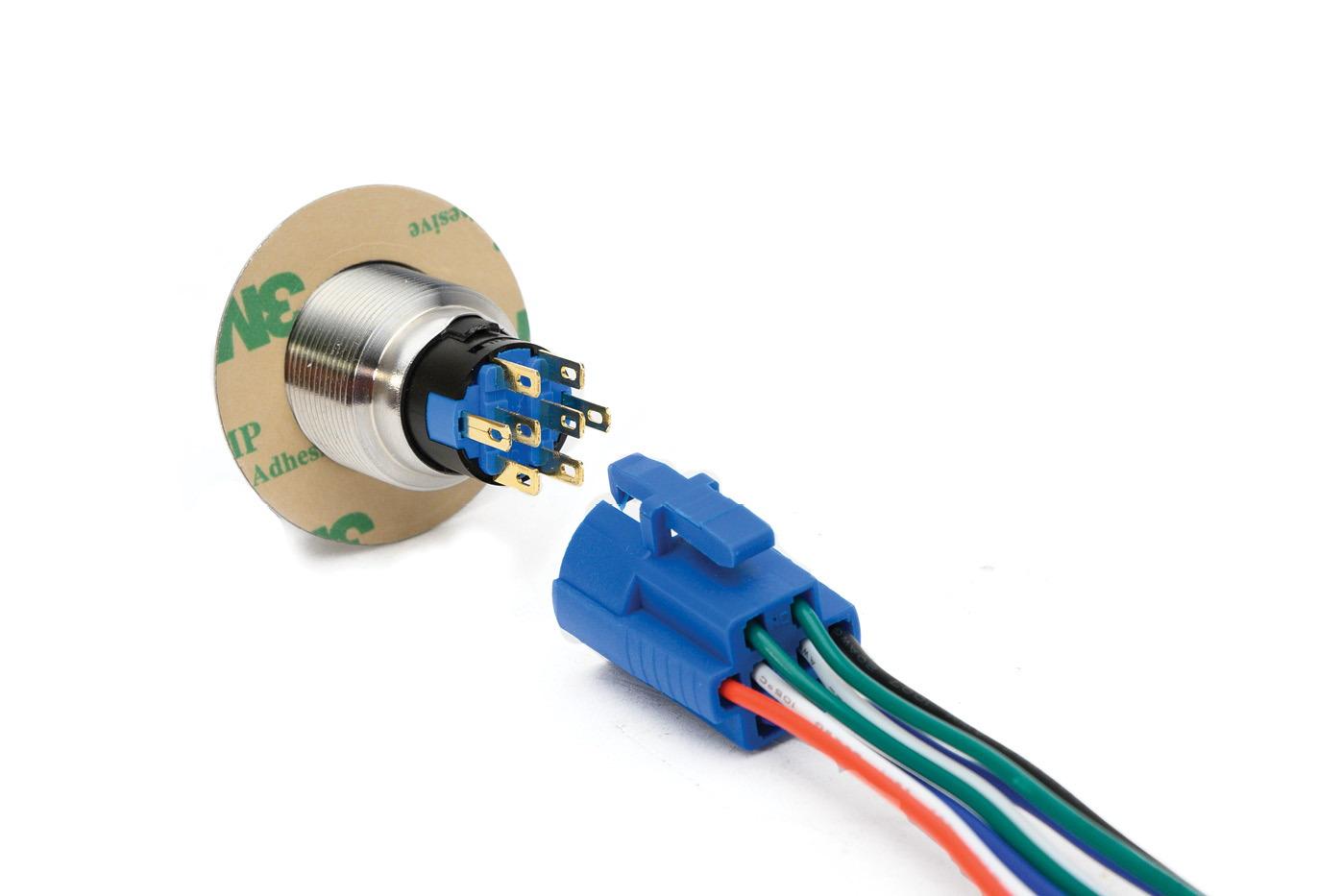
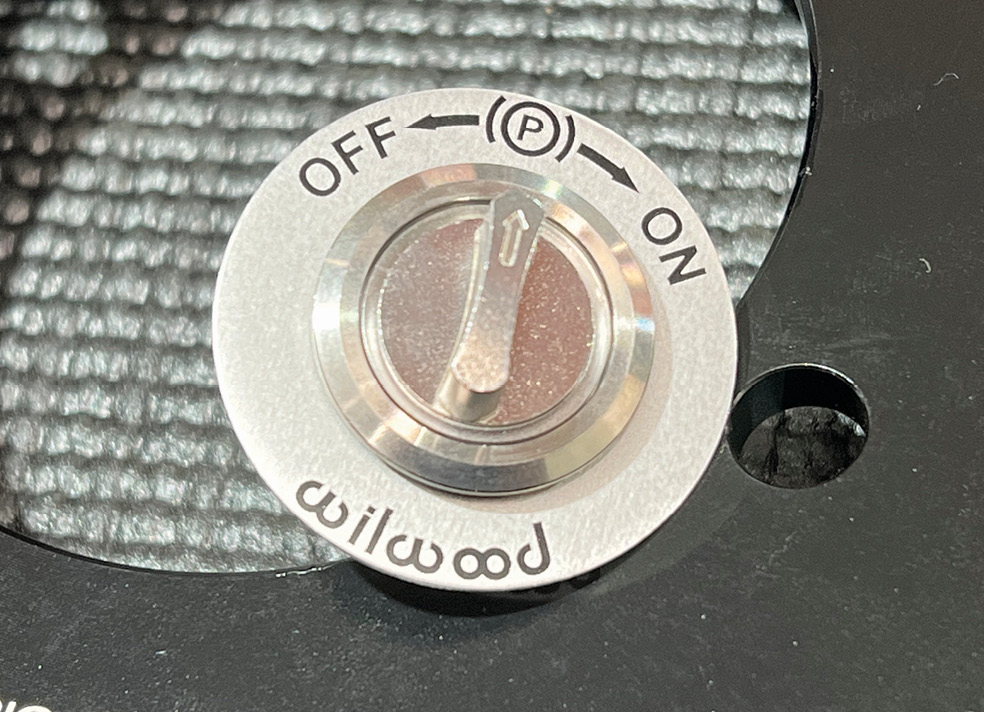
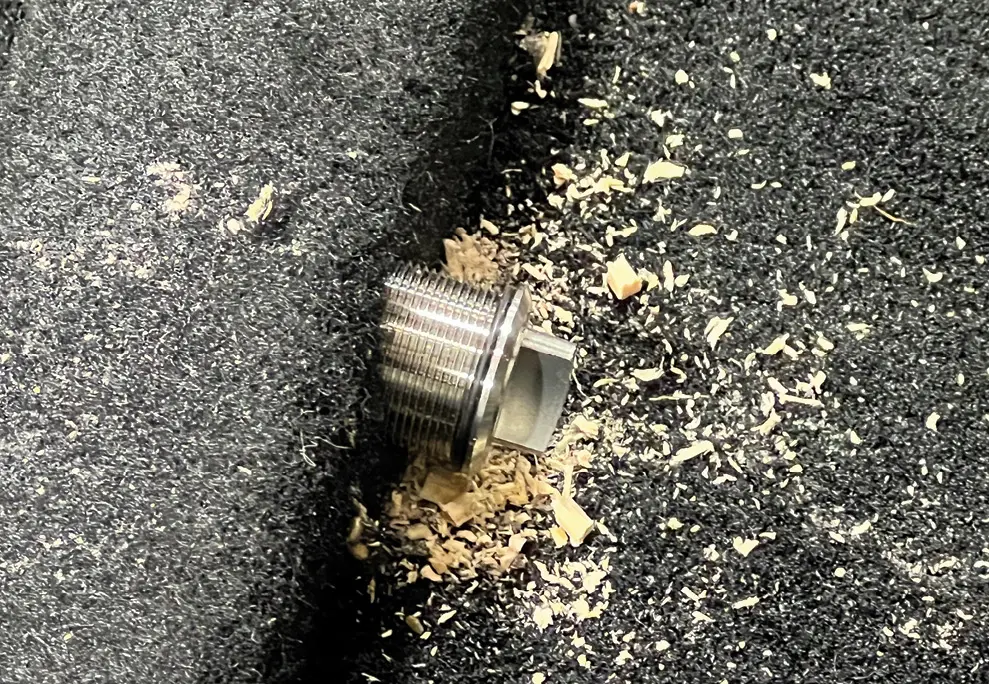
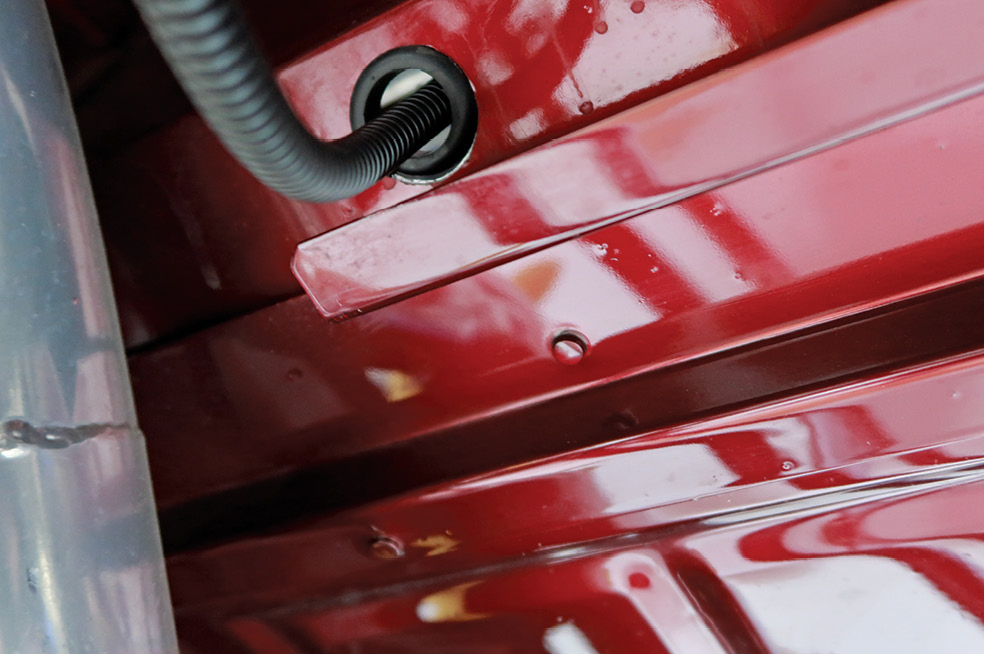
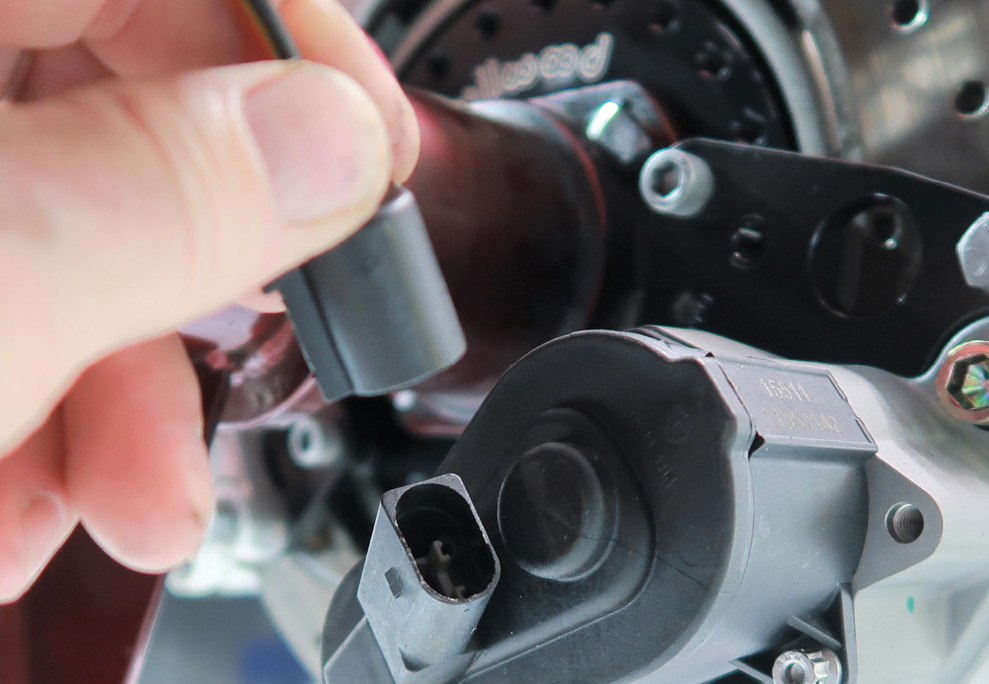
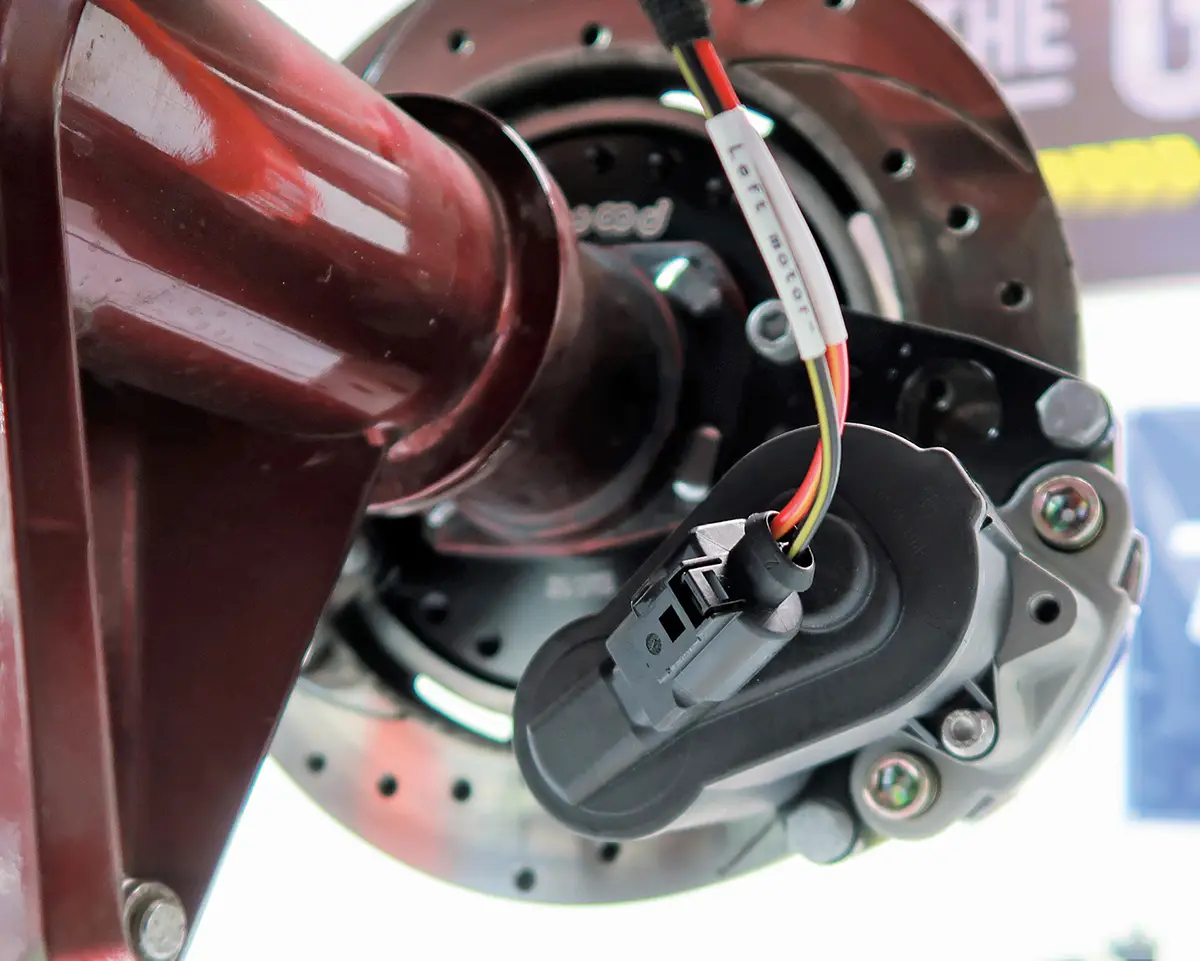

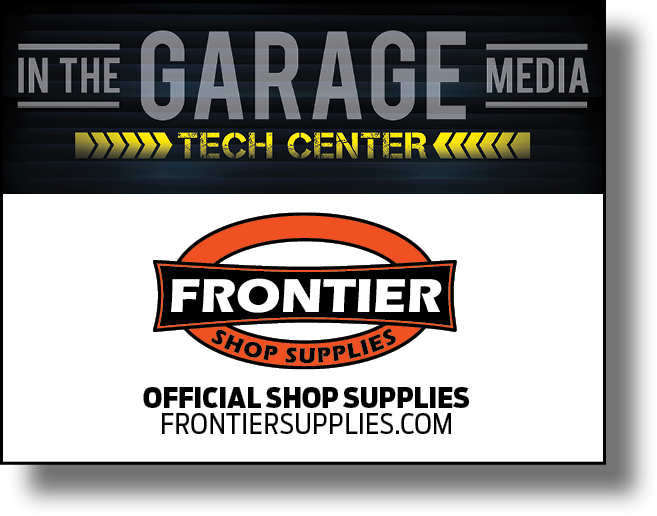