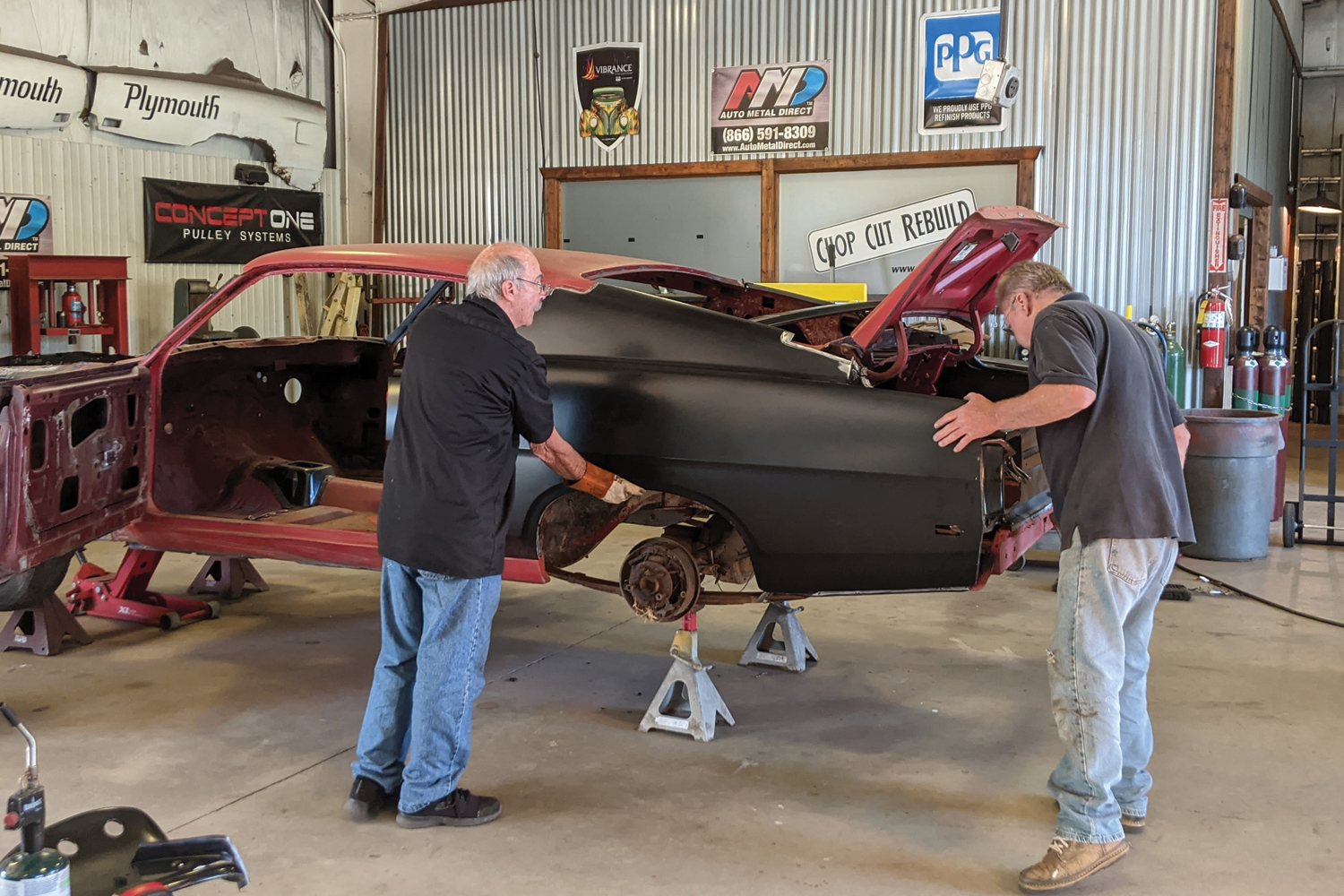

e’re back! Our ’69 Ford Torino Fastback Q-code continues to have its “skin” refurbished. This time we take a look at the wheelhouse and trunk floor extension. It should be noted that while we are working on a ’69 Ford Torino Fastback the parts and the work required will be the same for ’66-’69 Ford Fairlanes and Torinos and other years and models … but more on that later.
We find ourselves once again back at The Installation Center (TIC) in Cleveland, Georgia, watching Craig Hopkins continue the resurrection of our Torino while using Auto Metal Direct (AMD) sheetmetal. In the past two articles we have looked at replacing entire rear quarter-panels and the core support. Both of those projects required a good bit of effort and expertise. This time we are looking at patch panels; it’s been our experience this is something virtually any rodder who has dabbled in sheetmetal work has done some patch panel work.
Let us first familiarize ourselves with the parts at hand.
(PN 770-8468-R).
These pieces are stamped for AMD out of a high-quality heavy-gauge steel on AMD-exclusive tooling. It should be noted that AMD went to great lengths to make sure that their replicated parts feature correct-as-original shape, size, bends, tabs, and holes. This AMD component replaces Ford PN C8OZ-5427895-B. The wheelhouse will come to you with an EPD coating to protect against rust and corrosion. We have spoken about EPD, as it stands for electrophoretic deposition. E-coating, as it is commonly referred to, is an immersion wet paint process that uses electrical current to attract material (paint) to the metal surface. It’s great for protecting metal during the build process right up and until the body- and paintwork begins.
This component is stamped from the same high-quality heavy-gauge steel and each of these pieces features the same correct shape, size, bends, ribs, holes, and tabs like the factory. It arrives EPD coated to help protect against rust and corrosion. This AMD component also replaces Ford PN D0OZ-65112A23-A and comes with the same EPD coating.
Follow along with the photos as it will pretty much be a step-by-step process on how to remove the tired and rusted-out sheetmetal and replace it with the fresh sheetmetal from AMD.
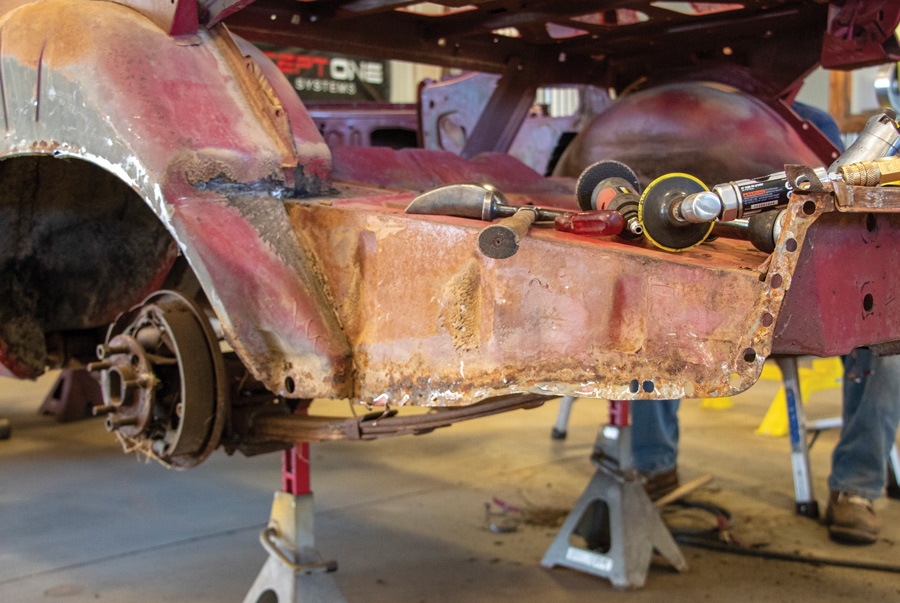
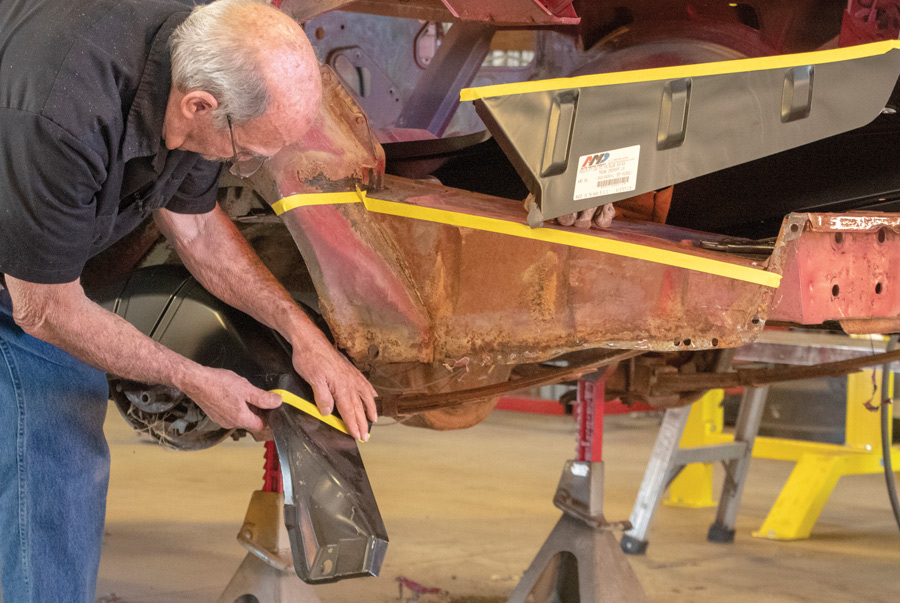
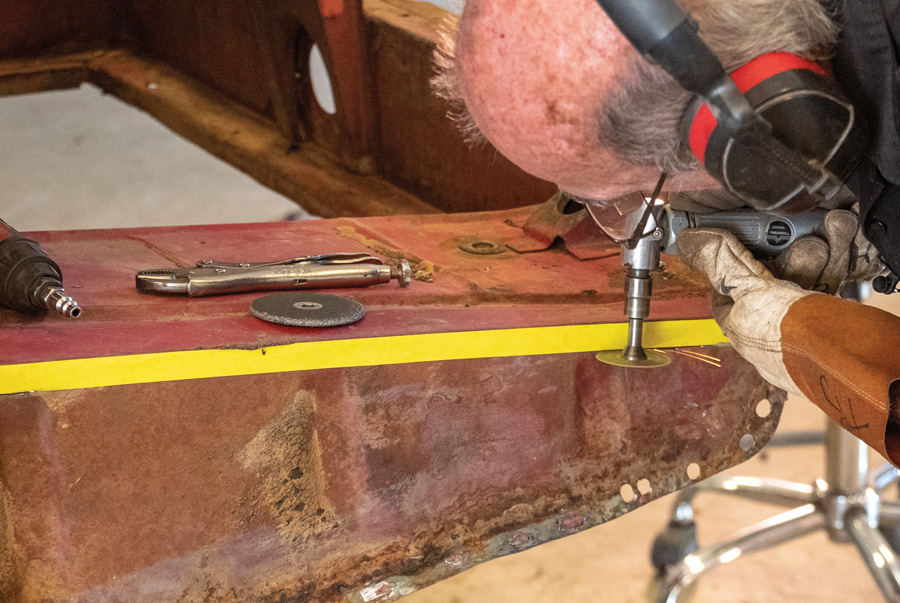

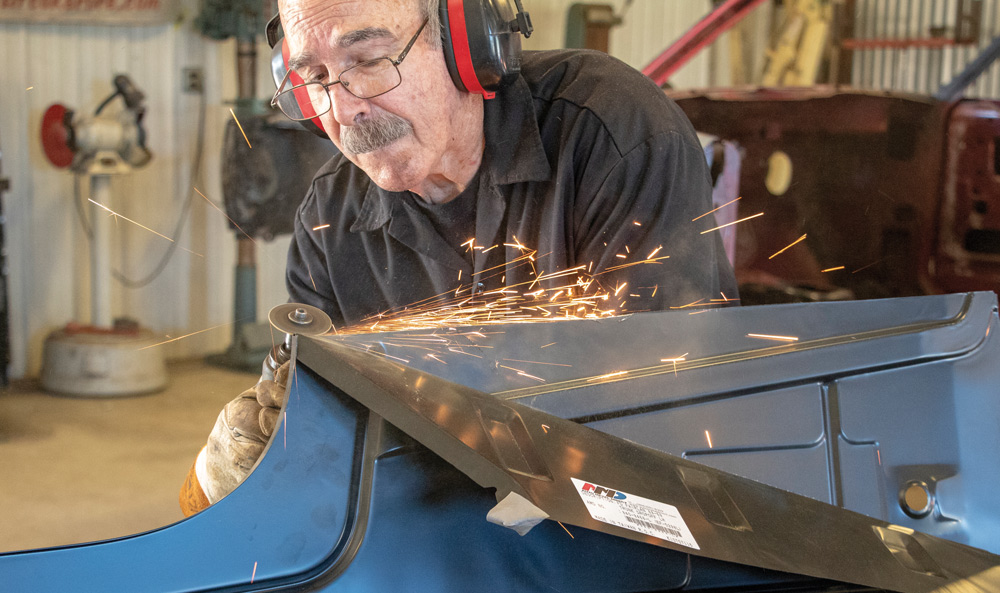
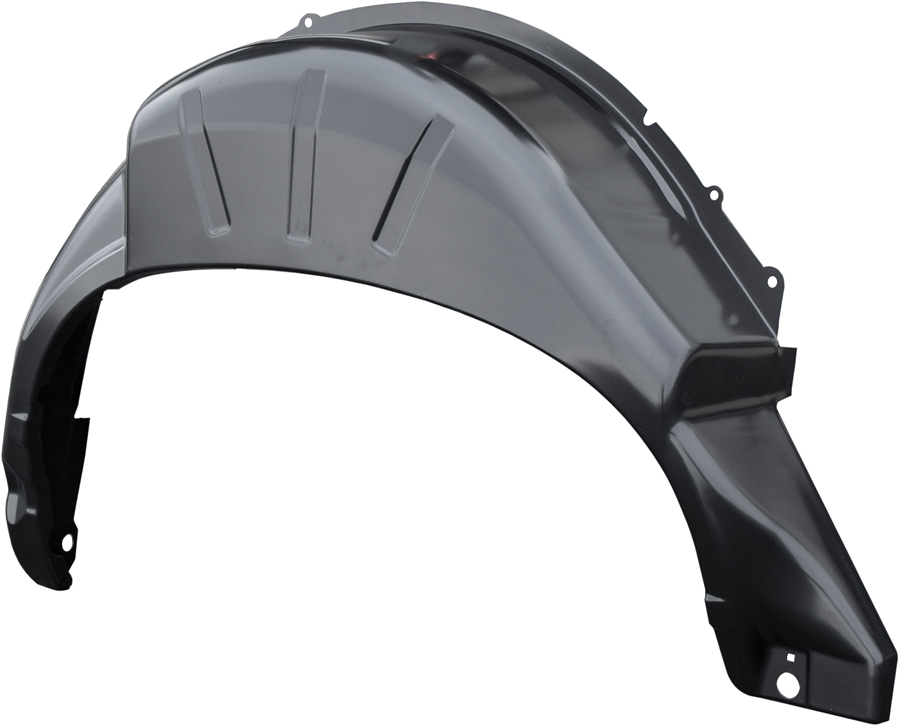
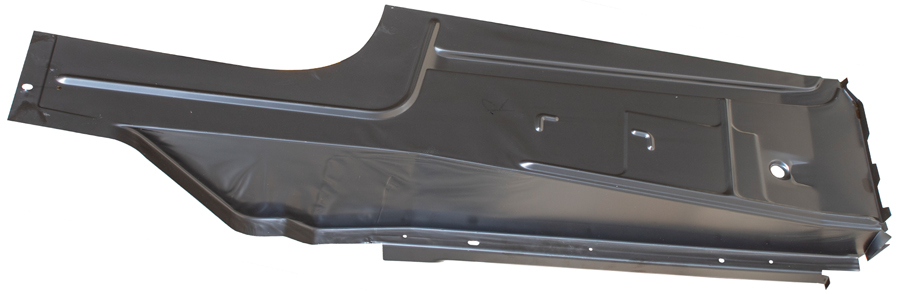
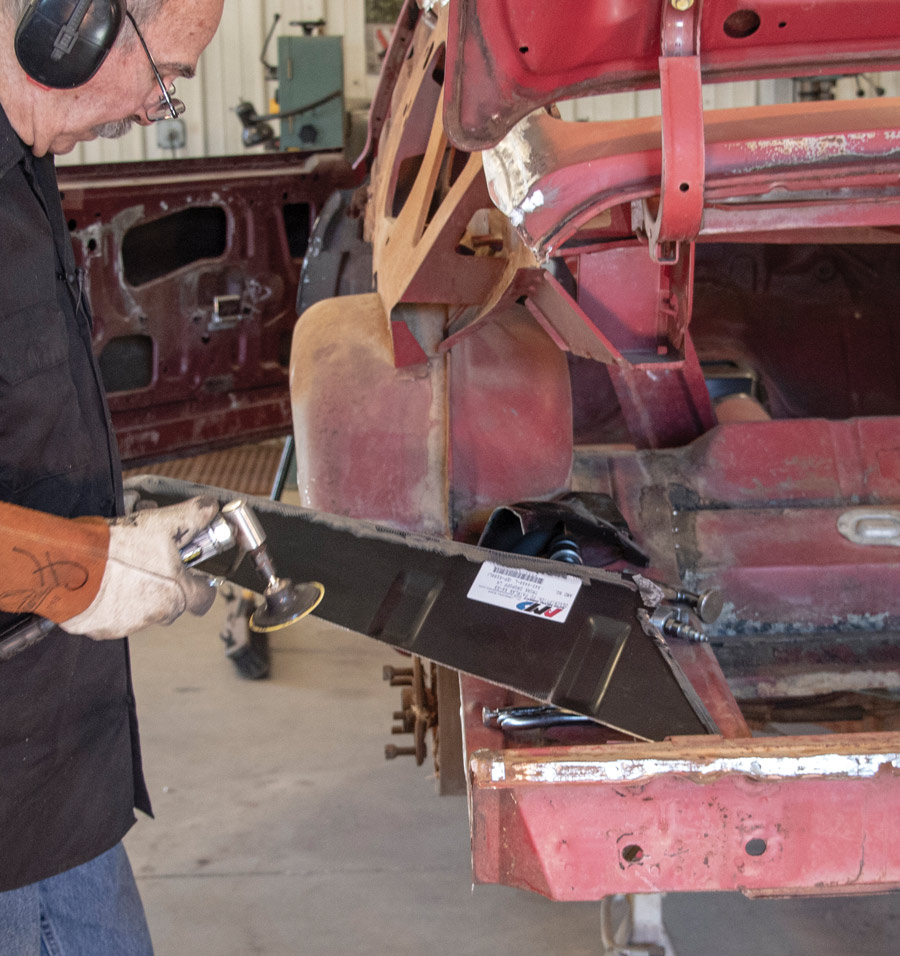
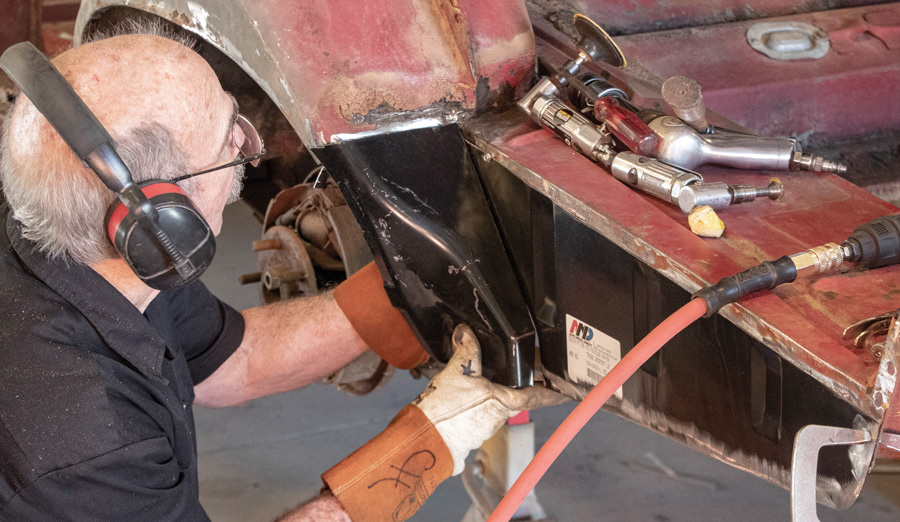
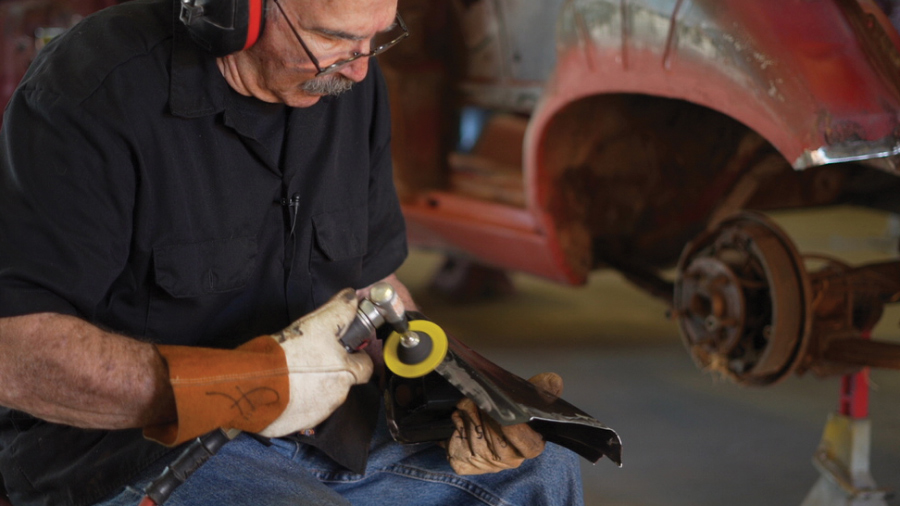
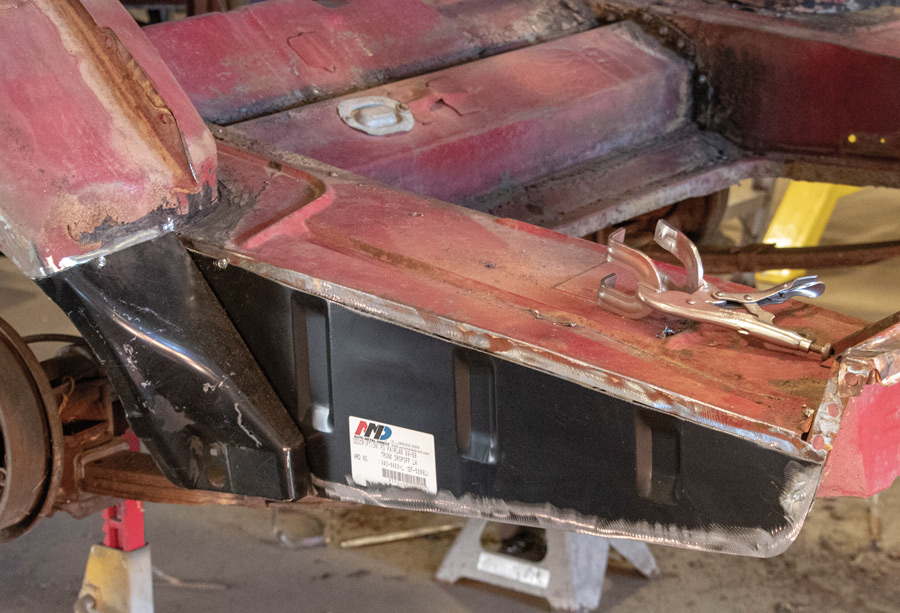
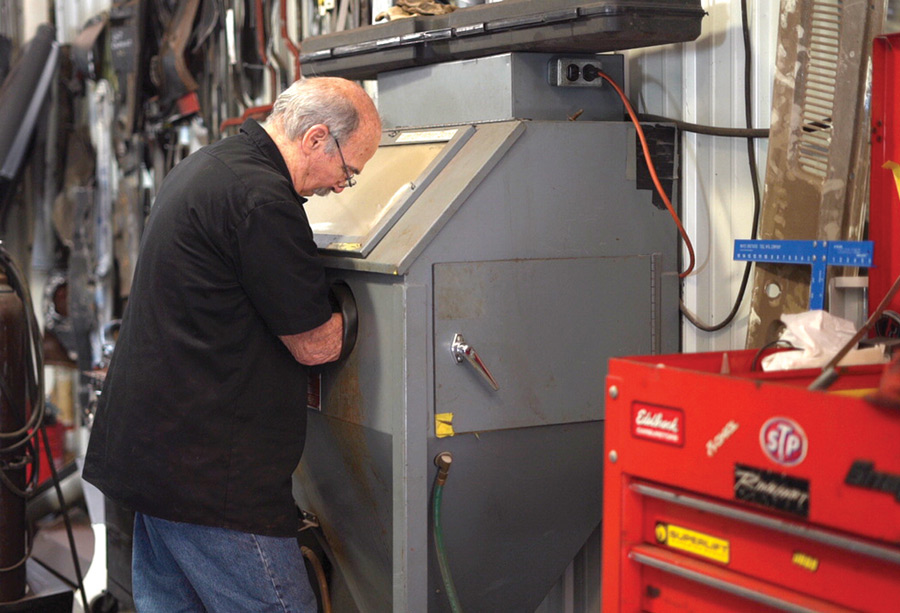
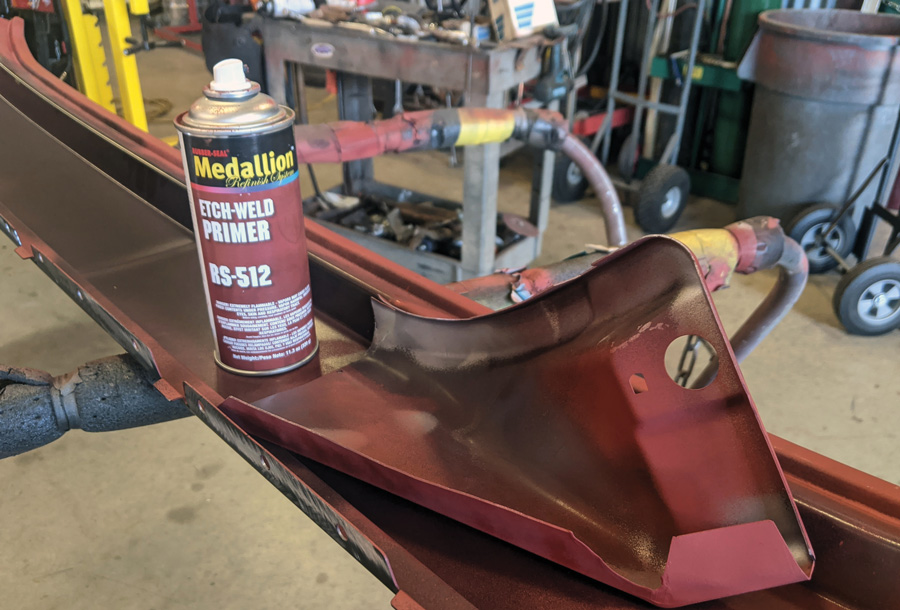
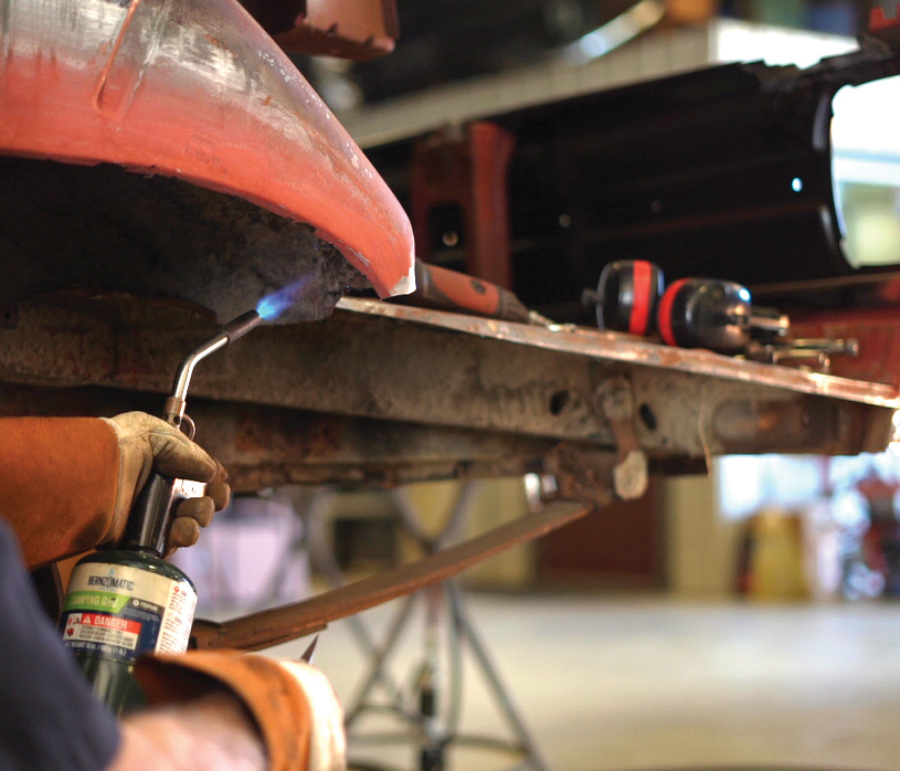
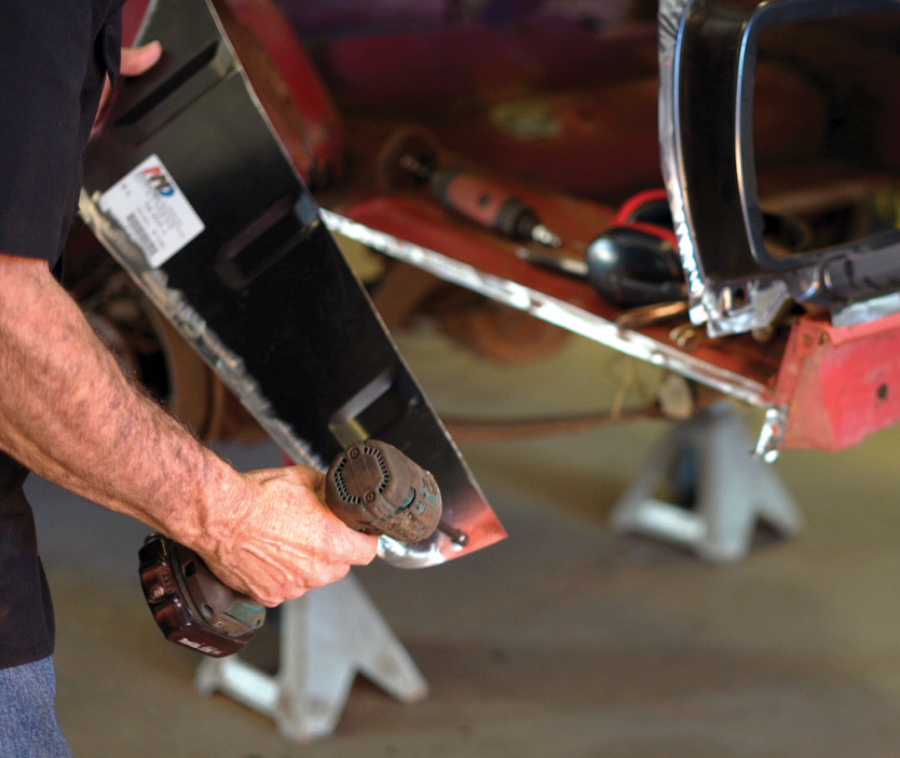
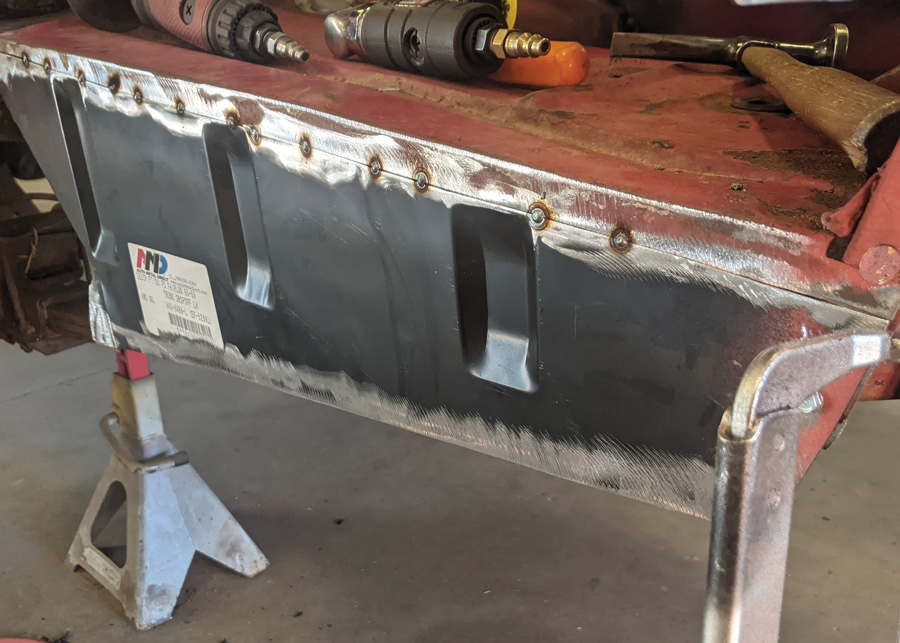
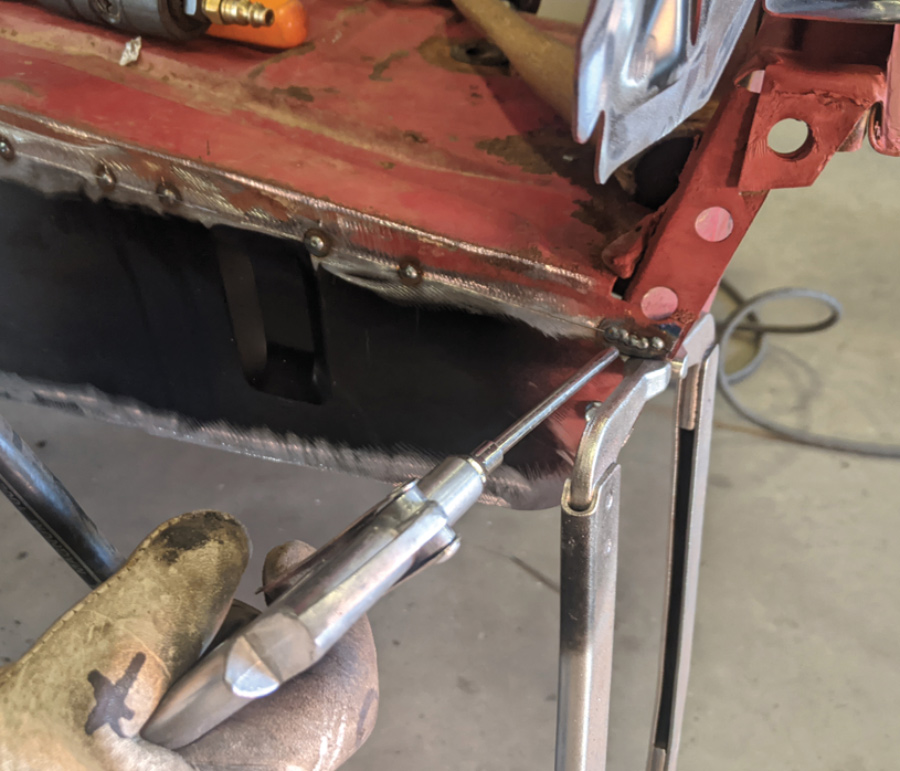
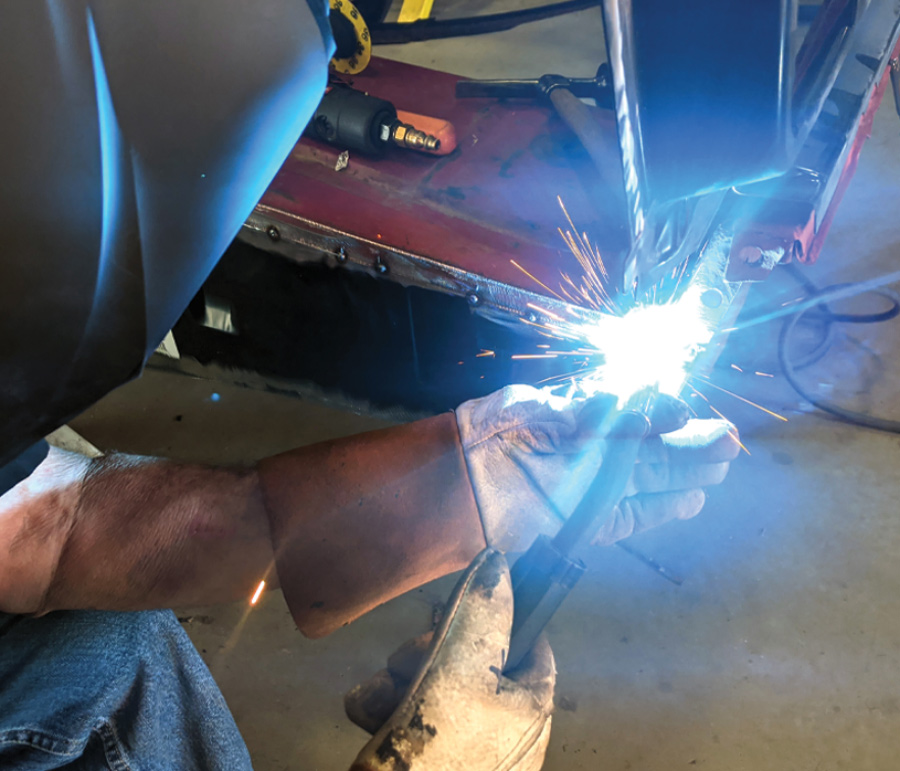
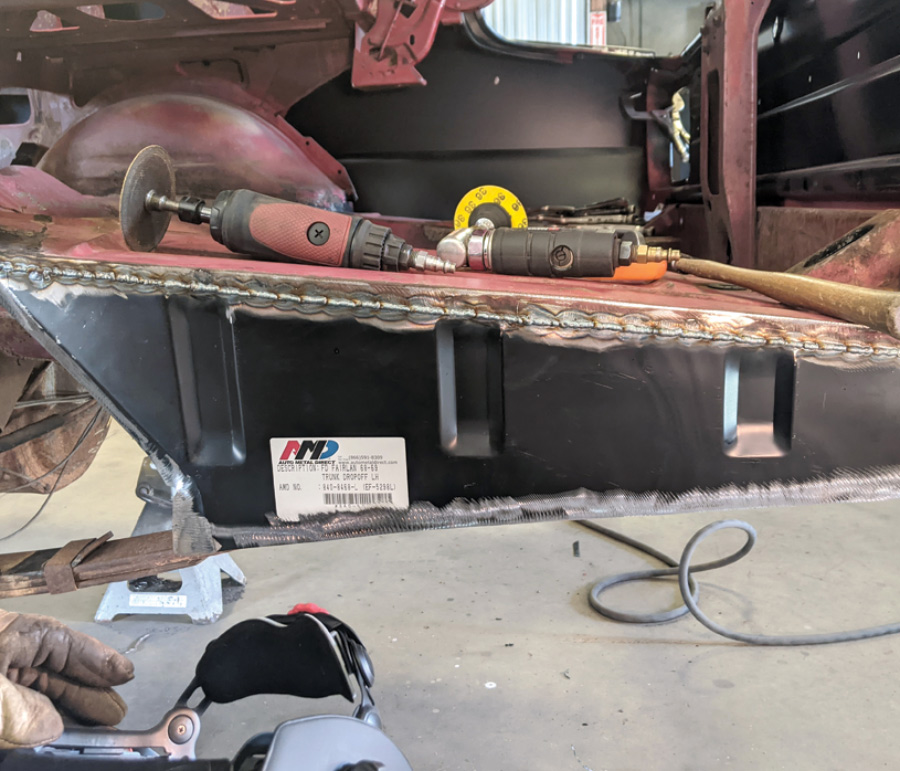
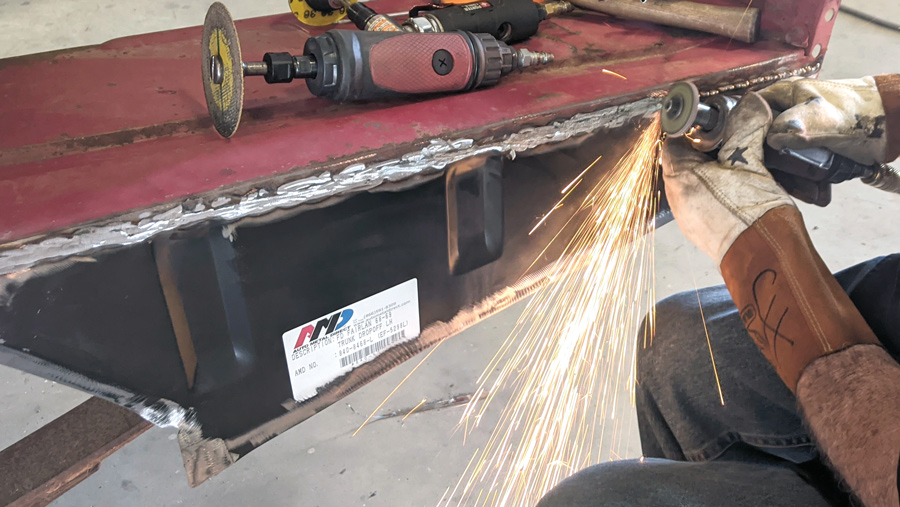
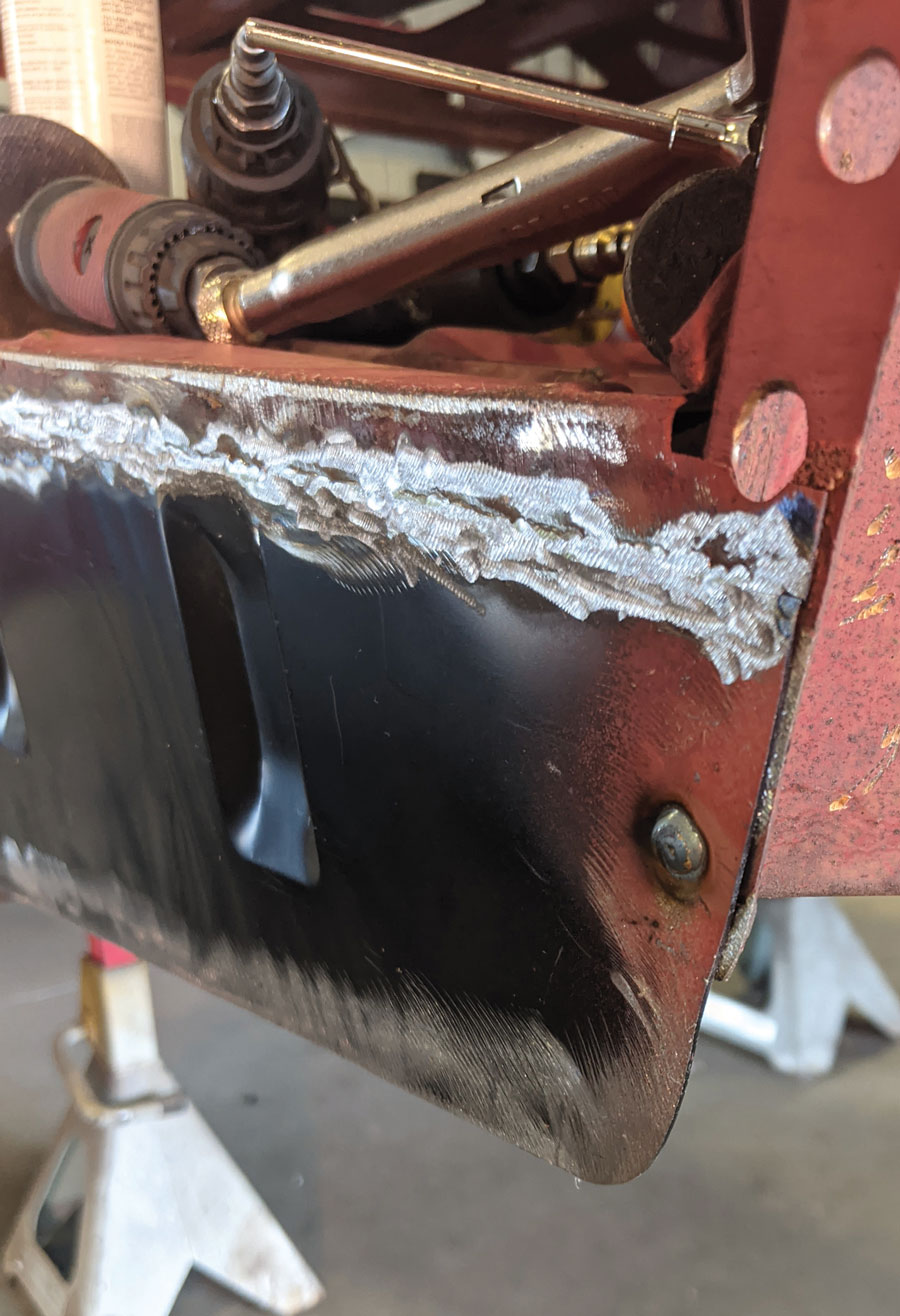
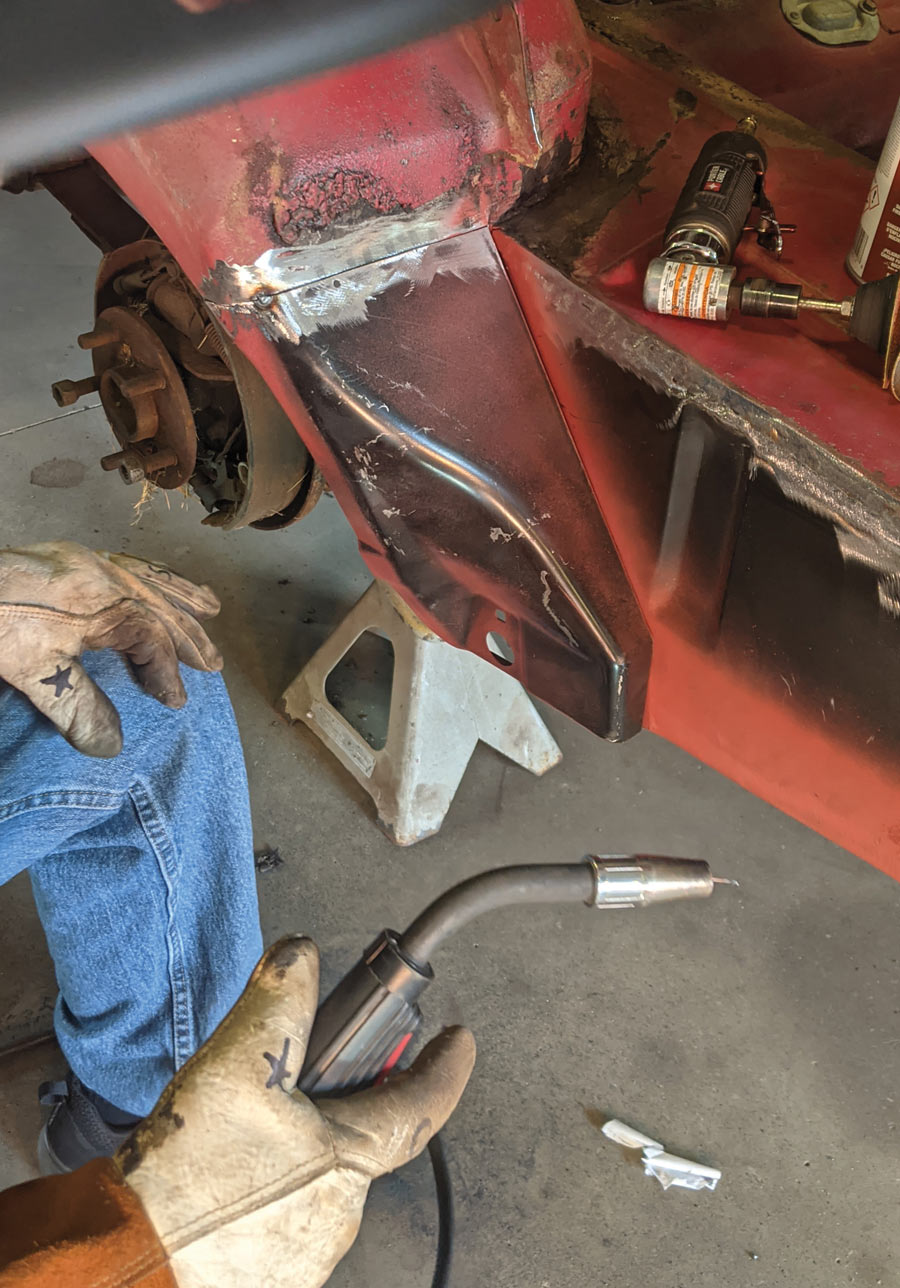
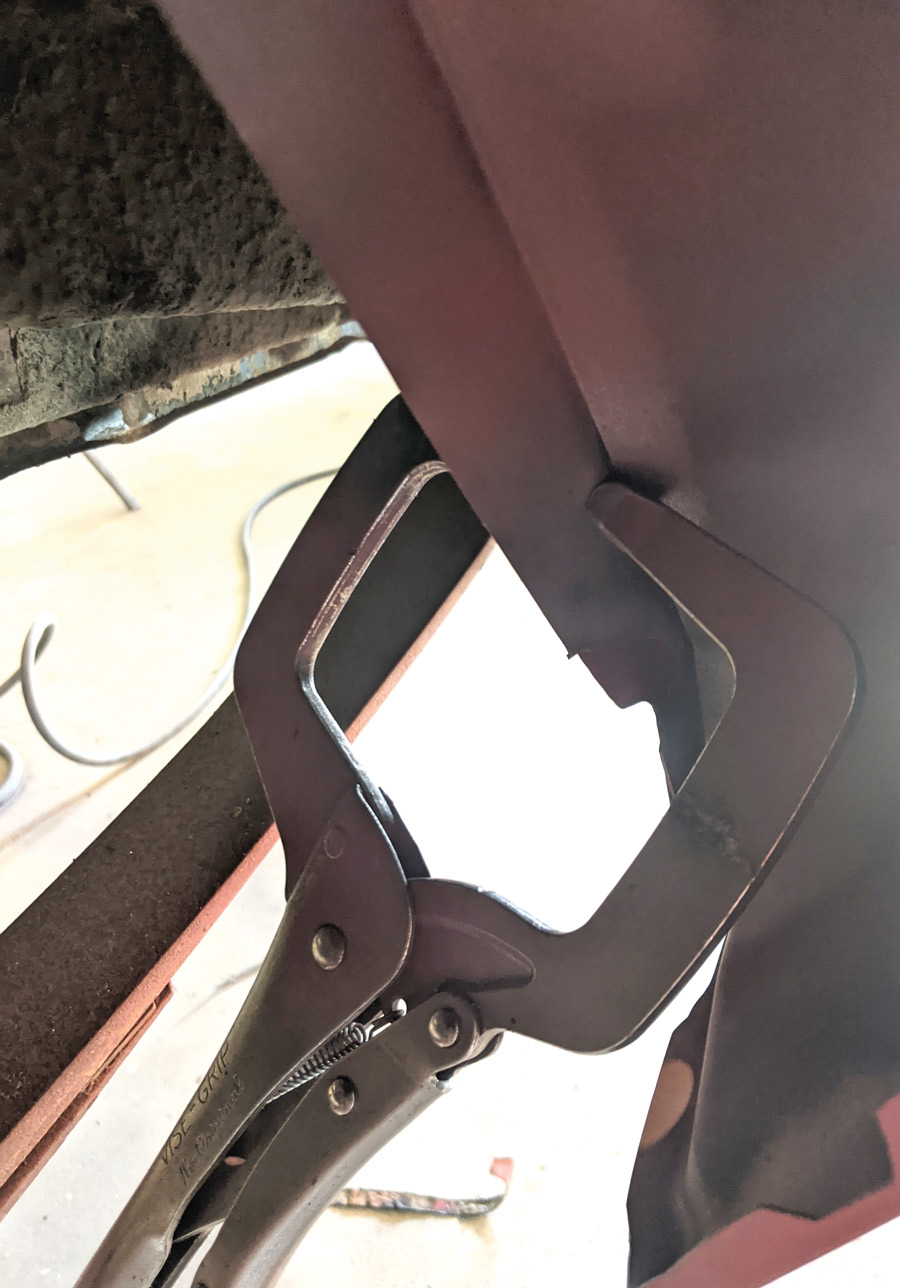
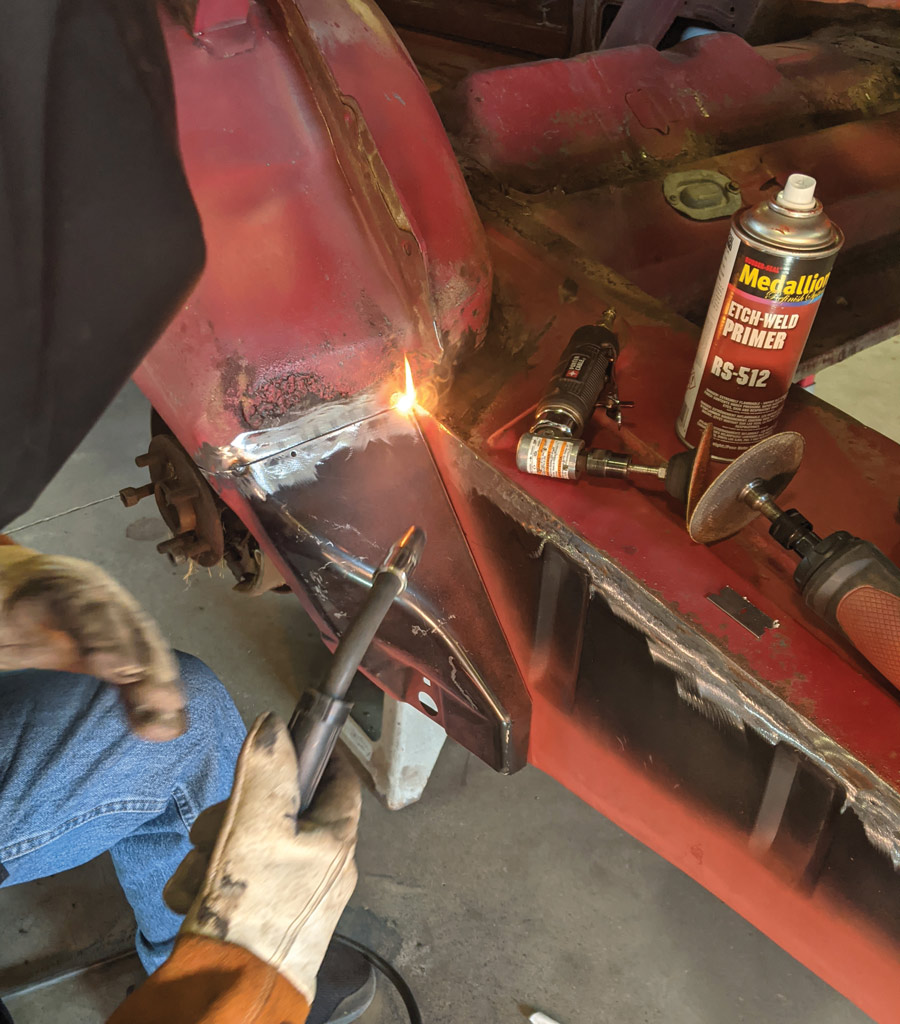
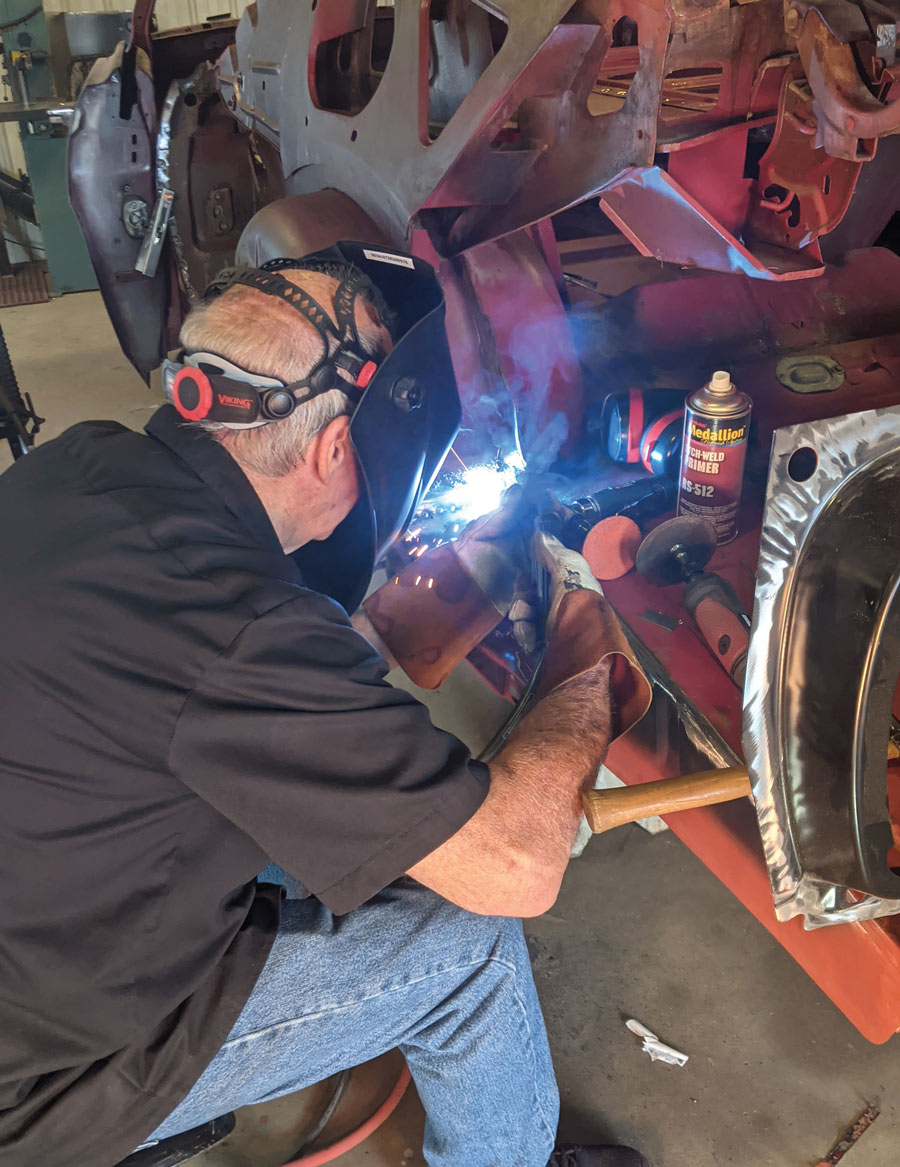

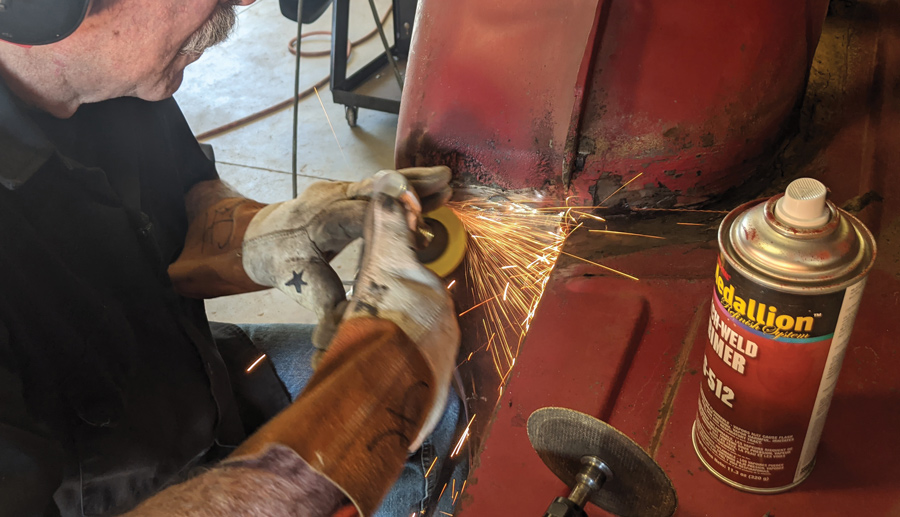
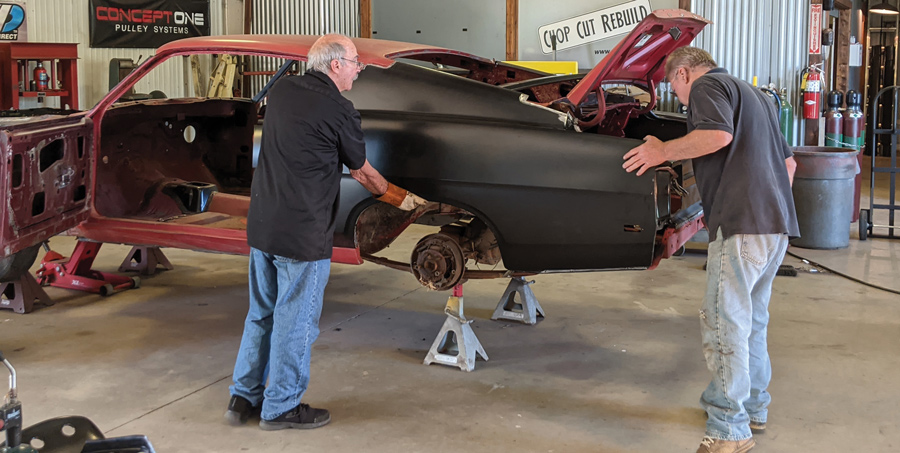
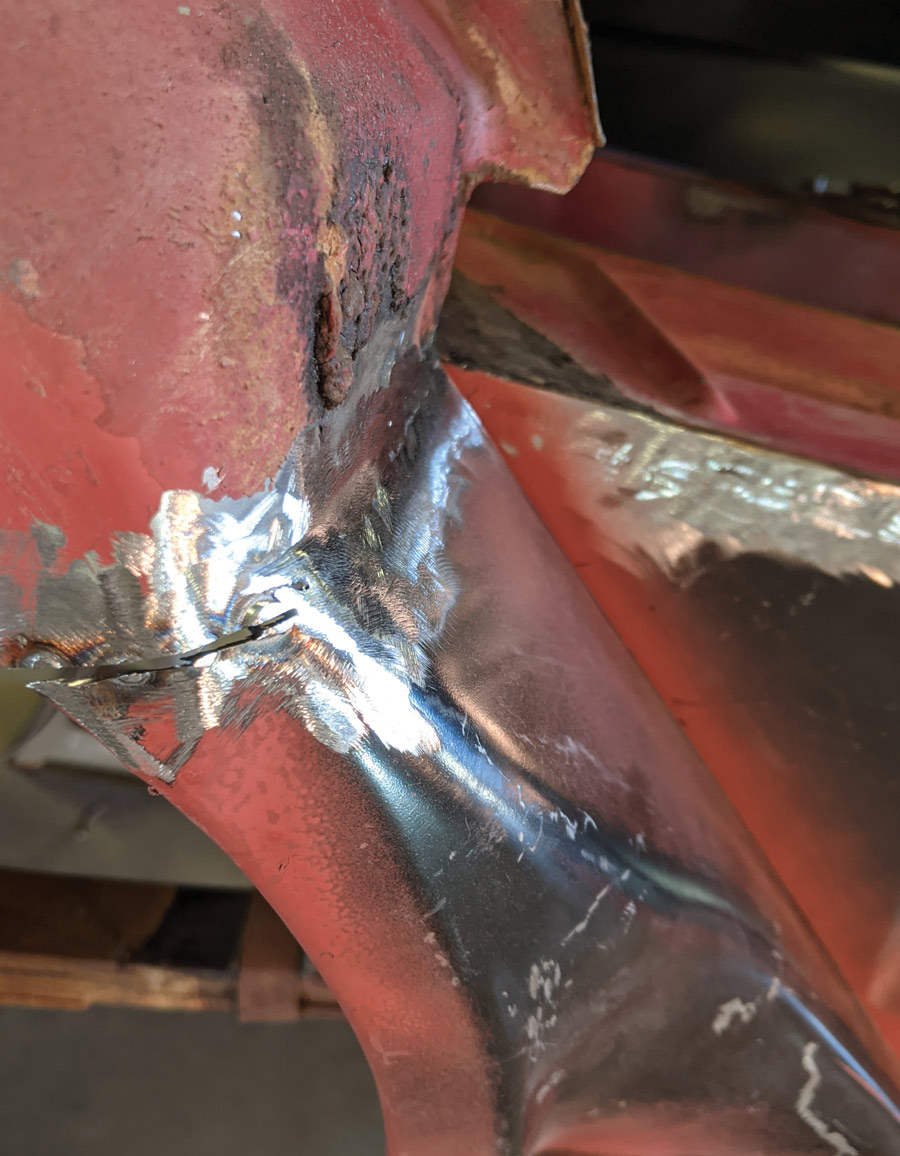
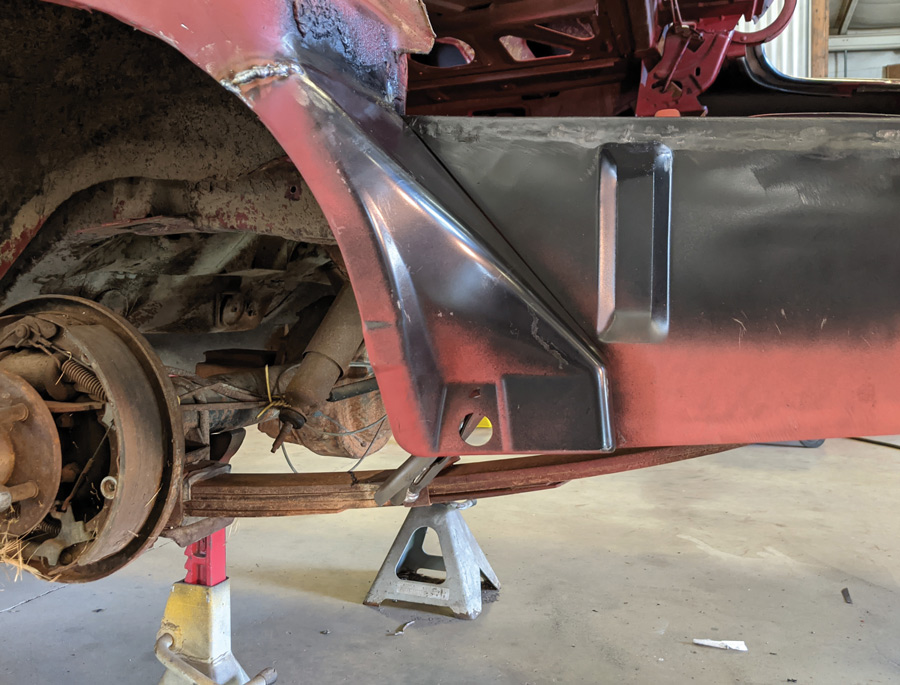
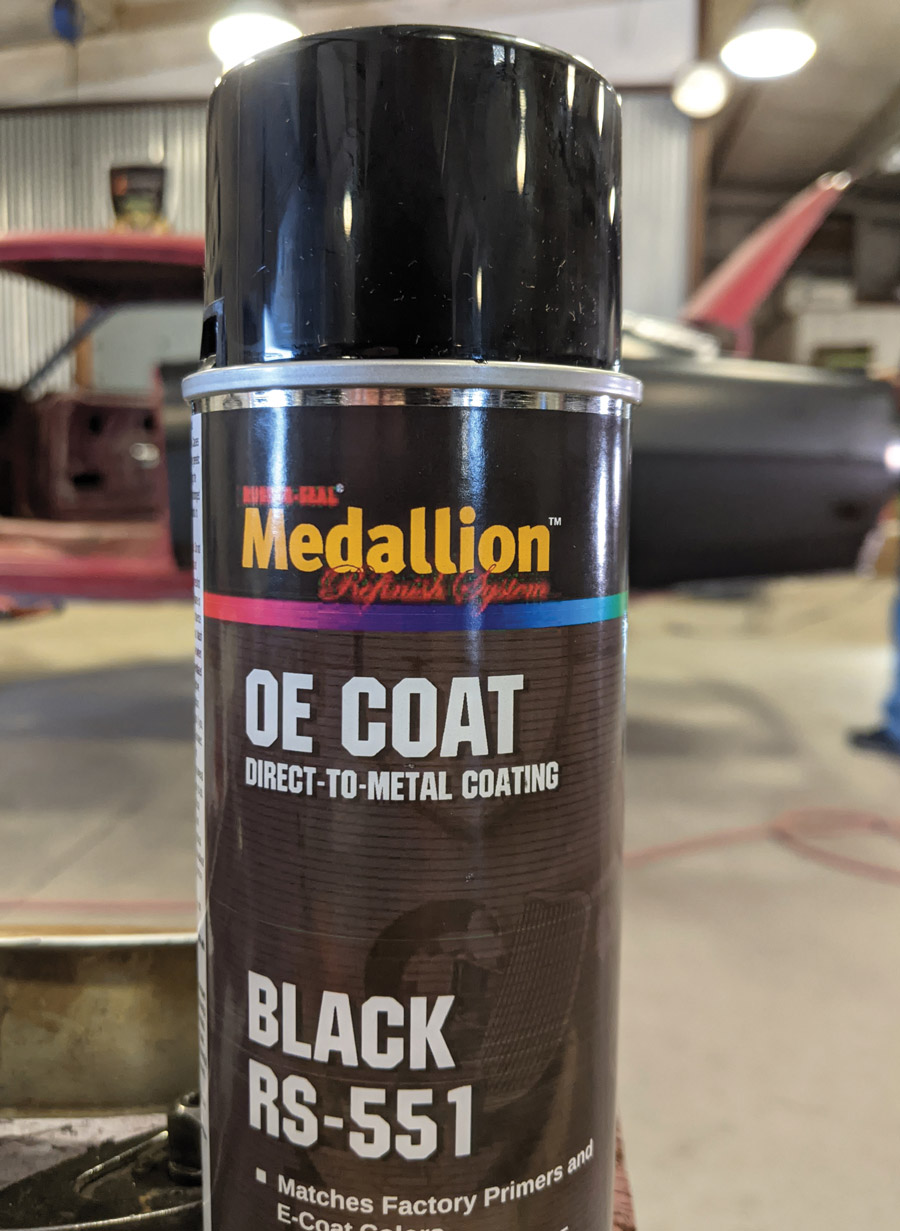
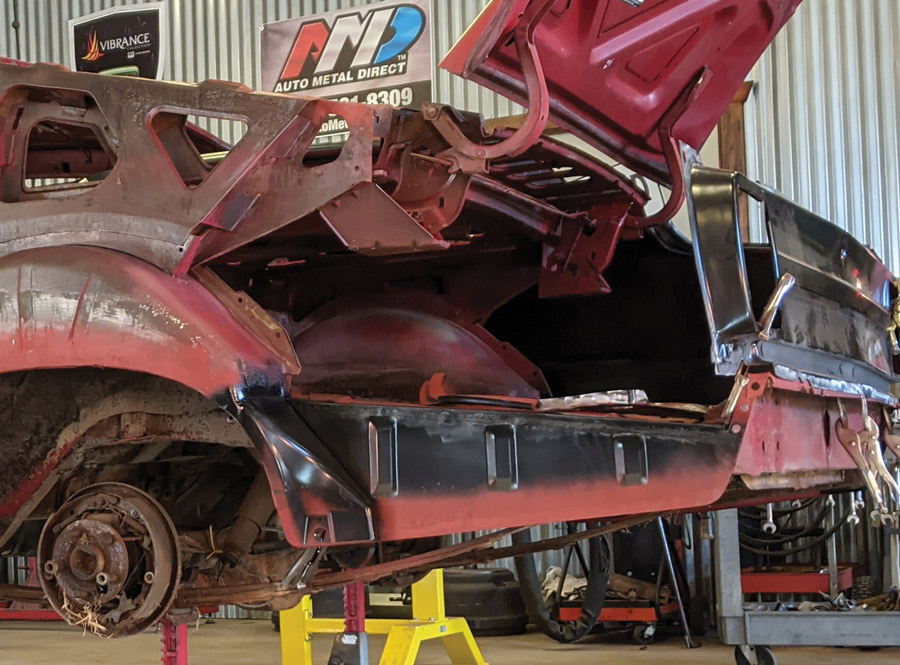
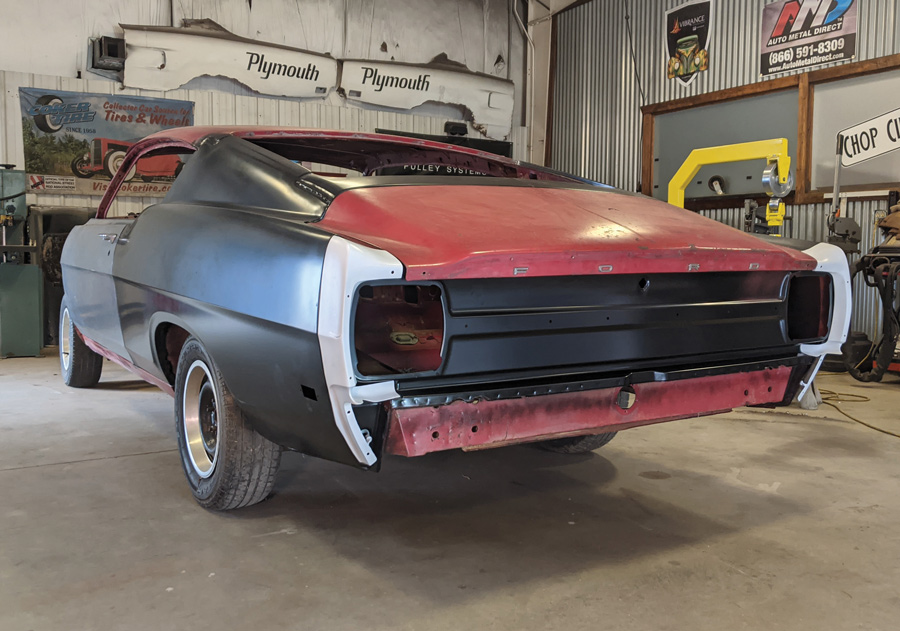
