Modern Rodding TECH
InTheGarageMedia.com
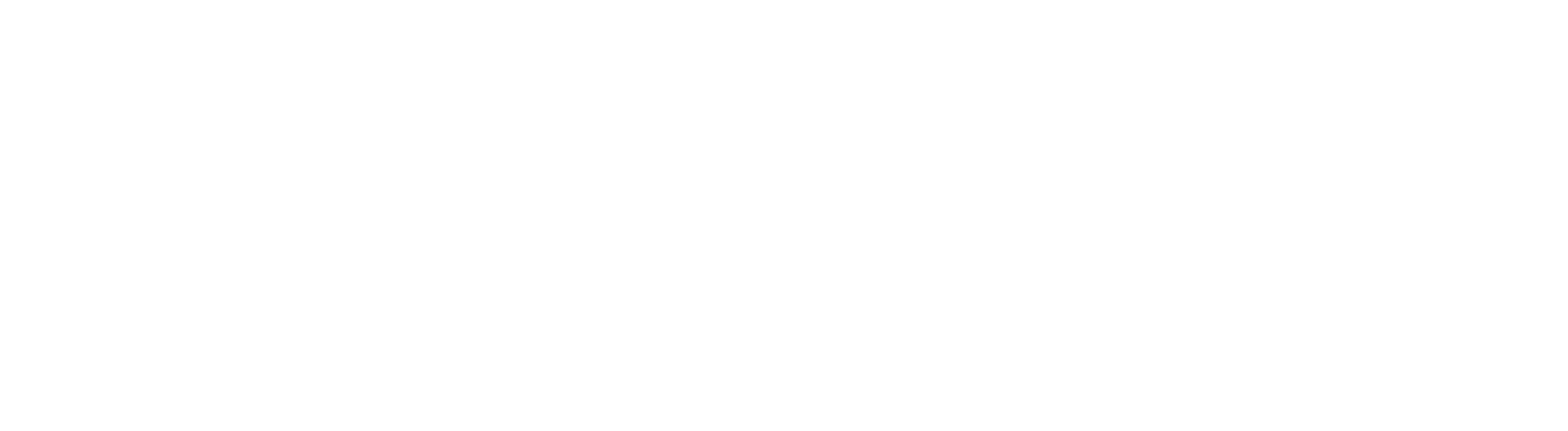
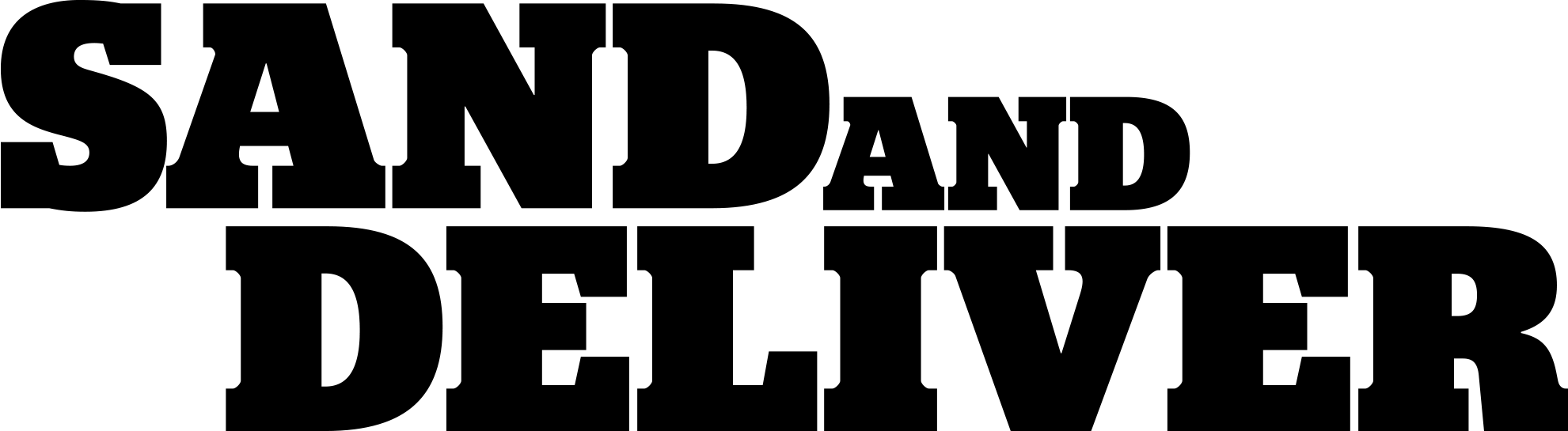

hey may not make ’em like they used to. But they sure never finished ’em the way we can now. The quality of contemporary body- and paintwork is truly unprecedented. More than straighten a panel, we can straighten an entire body from tip to tail.
Of course, nobody said it was easy. Prepping a straightened body for paint is a labor-intensive process of raising low spots with fillers and milling the surface to a consistent level. And historically speaking, it was a rinse-and-repeat process of filling and sanding interspersed with long cure times.
The act will always eat up time, money, and energy, but today’s techs figured out ways to minimize the investment. Rather than incrementally build up the surface of a panel bit by bit, they discovered that they could just skim vast sections of a panel with filler and knock it all down to the panel’s highest level in one fell swoop. When done properly, the filler ends up no thicker than it would by any other method. But the process reduces time and minimizes material that ends up on the floor as dust. And at today’s labor and material costs, that’s saying something.
Then real progress came when techs started treating the body in groups of panels rather than individually. Old body panels—even pristine ones—are far from perfect. The simpler panels often bulge, and that makes valleys where those panels meet. Creases and ridges on more complex panels don’t always line up precisely, either.
But by treating bodies in groups rather than individual panels, we can correct a multitude of corporeal indiscretions. More than align those wonky character features, we can sharpen them. We can raise the valleys between bulging panels. Using these contemporary techniques, we can even tune the width of gaps among those panels.
To get an idea what this process looks like, we followed Nick “Hubcap” Sinoris prep a ’65 Chevelle for paint at Hot Rods by Dean in Phoenix. It’s a big undertaking and to do it justice here means breaking it up into multiple entries. It should go without saying that they started with a body as straight as possible. Body fillers are wonderful, but they’re not remedies for sloppy bodywork. Also, as with any other material applied to a body, they require a perfectly clean substrate, be it metal, fiberglass, or primer. Just as it will under paint, the tiniest spec of just surface rust will fester under filler, and that can wreck a finish.
It’s not the easiest work in the world. But prepping a restored body for paint is within reach of the ambitious among us. If nothing else, the following should explain just why those prep bills add up the way they do!
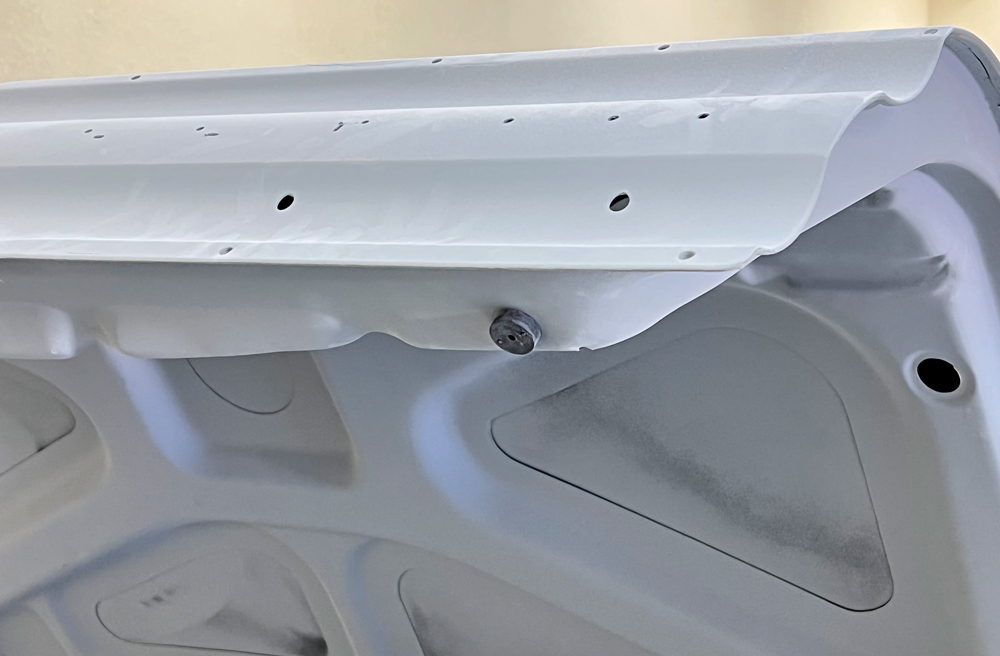
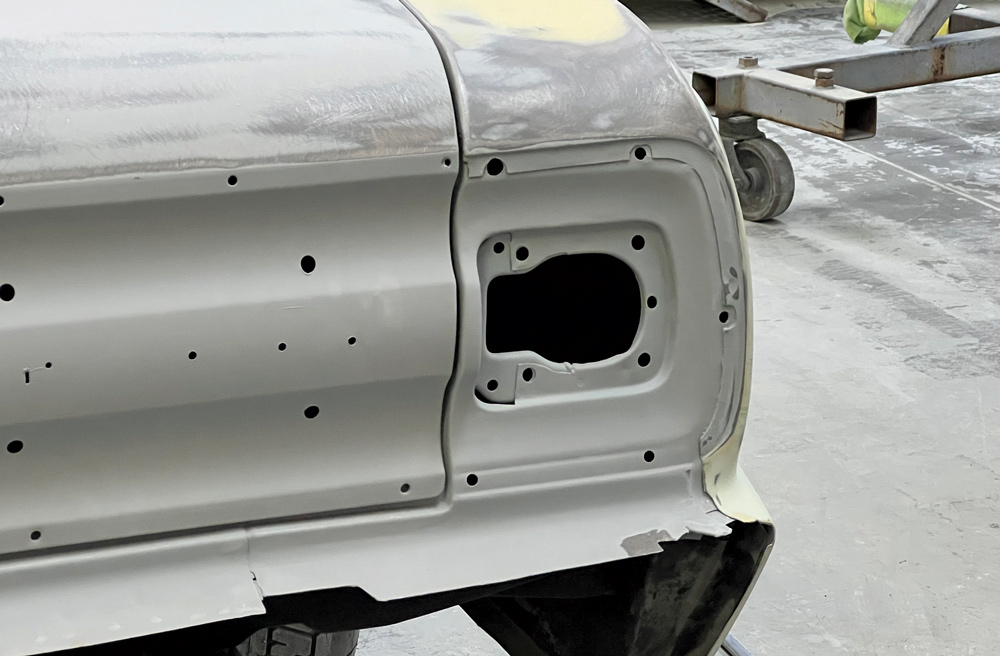
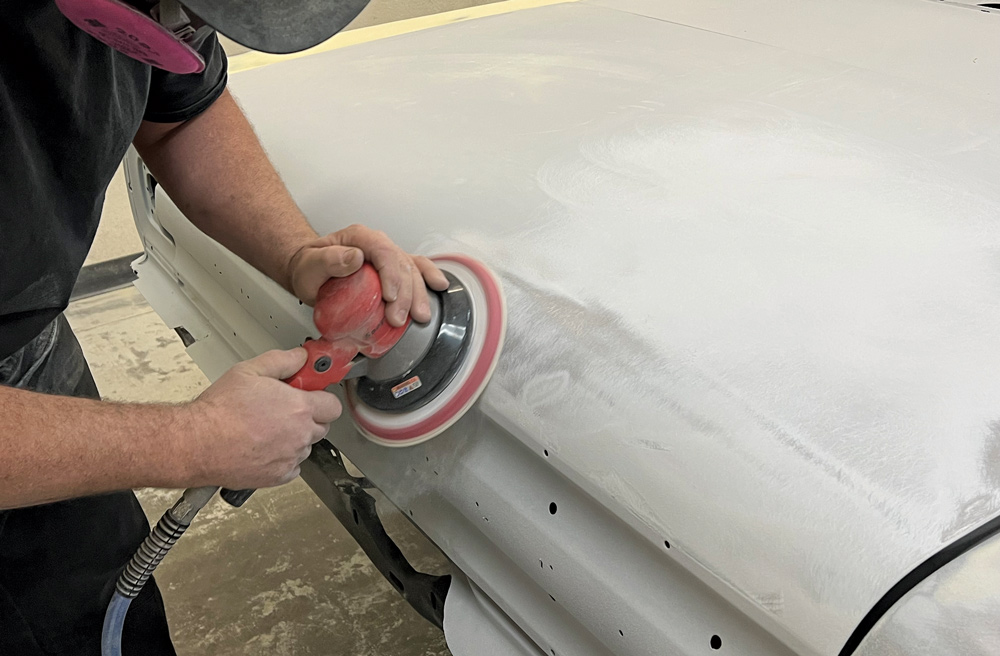
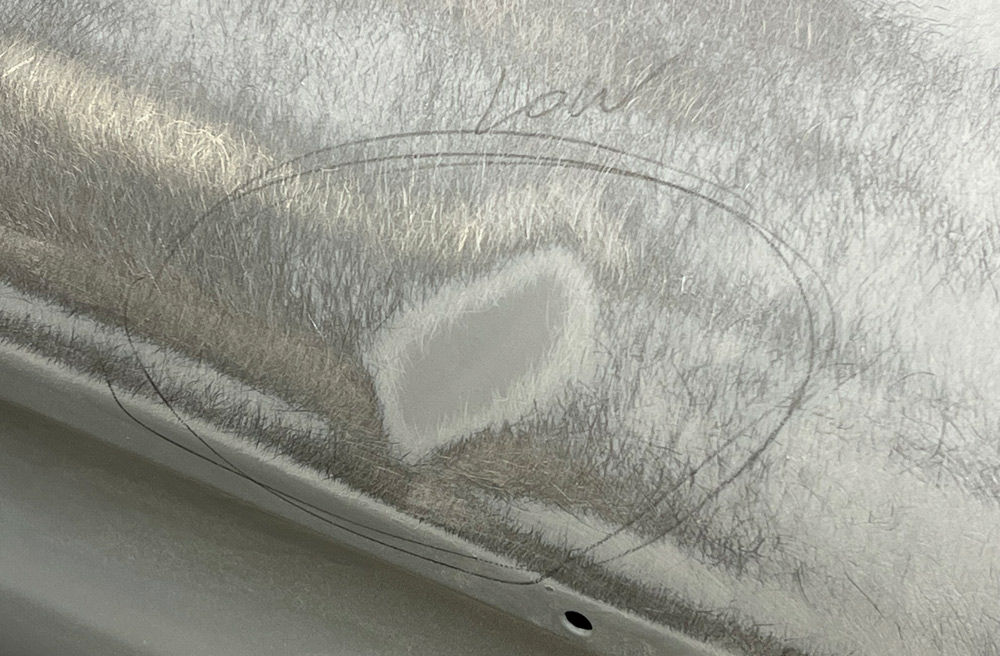

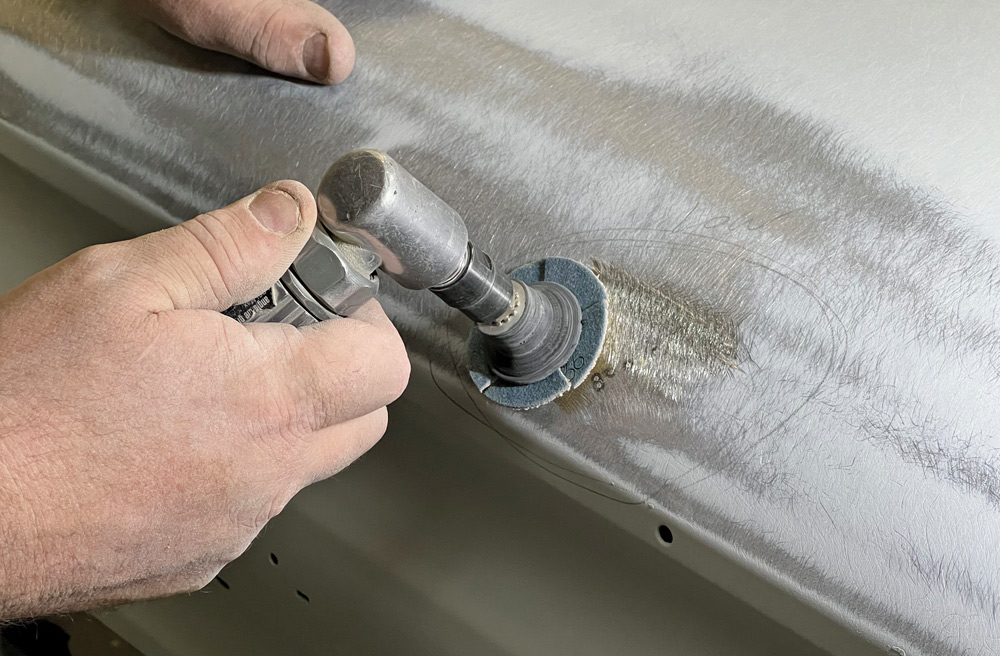
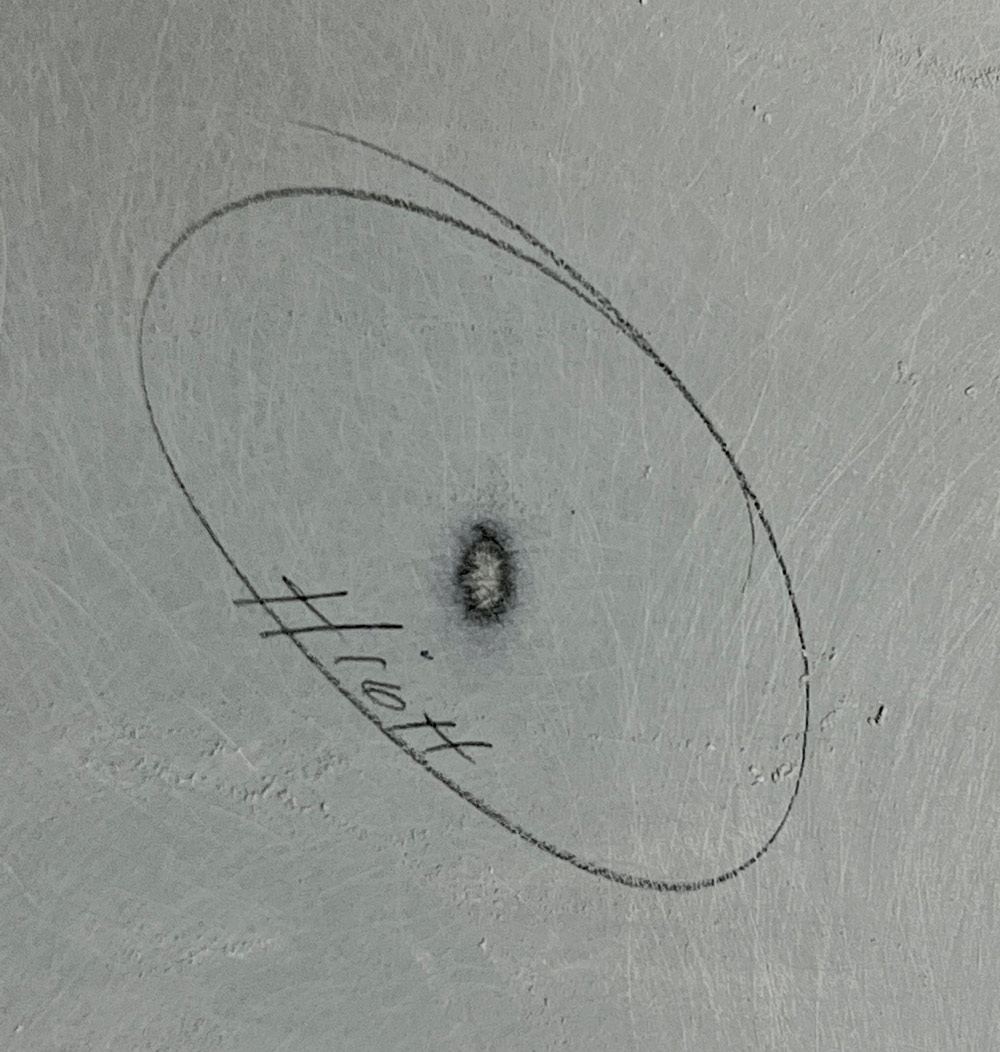
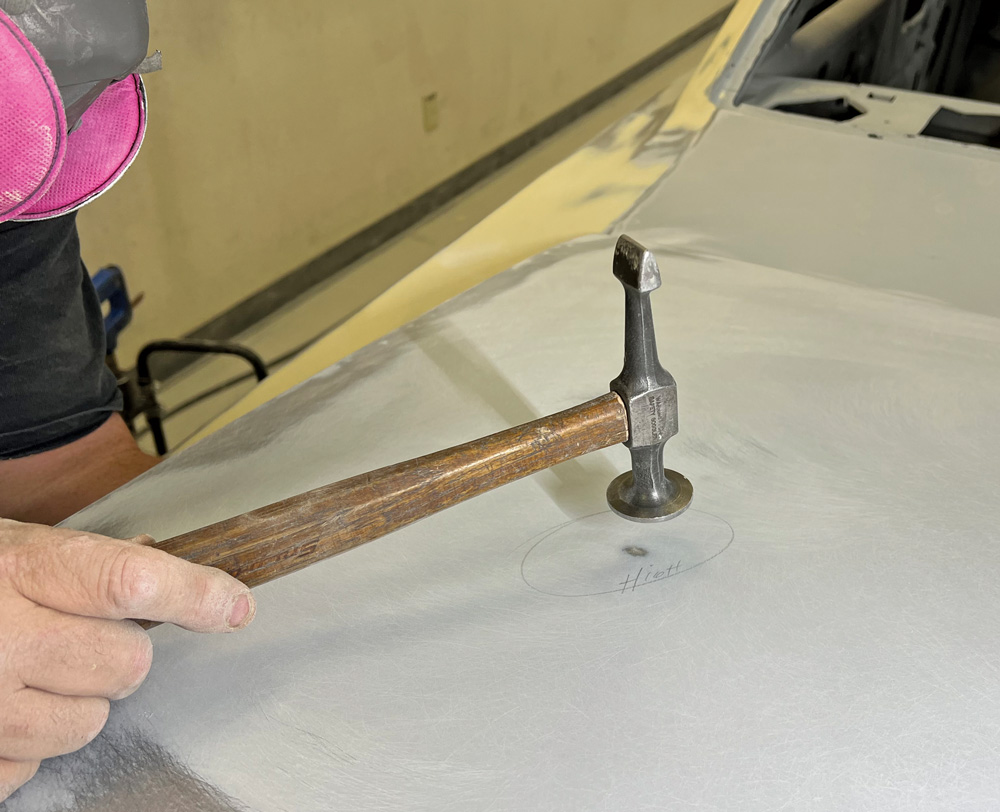
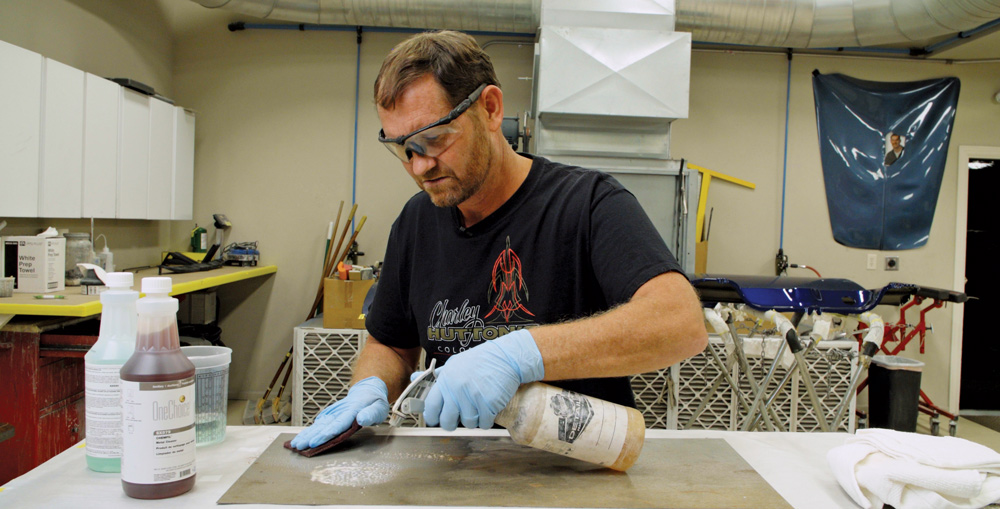
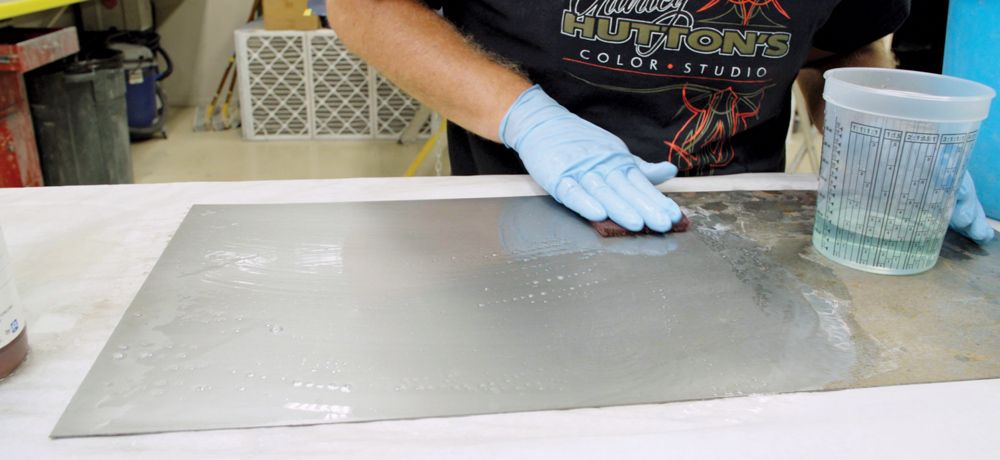
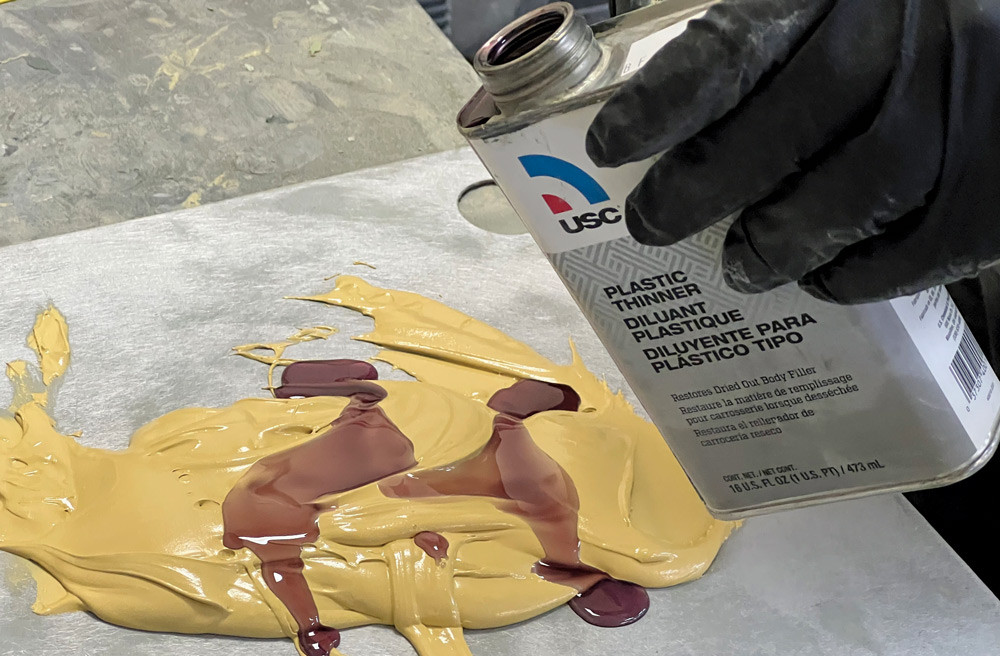
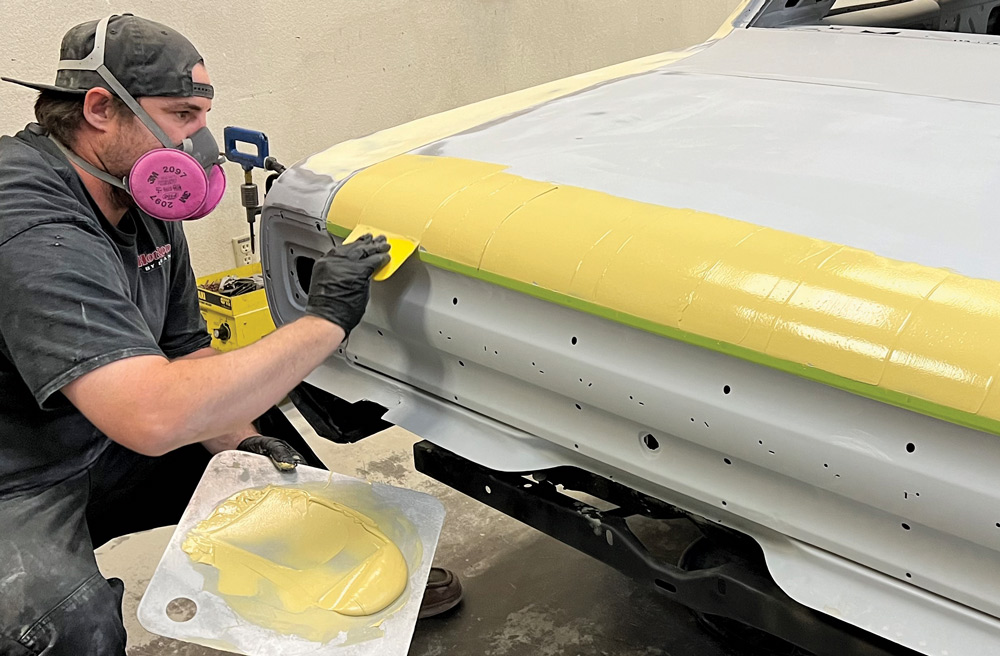
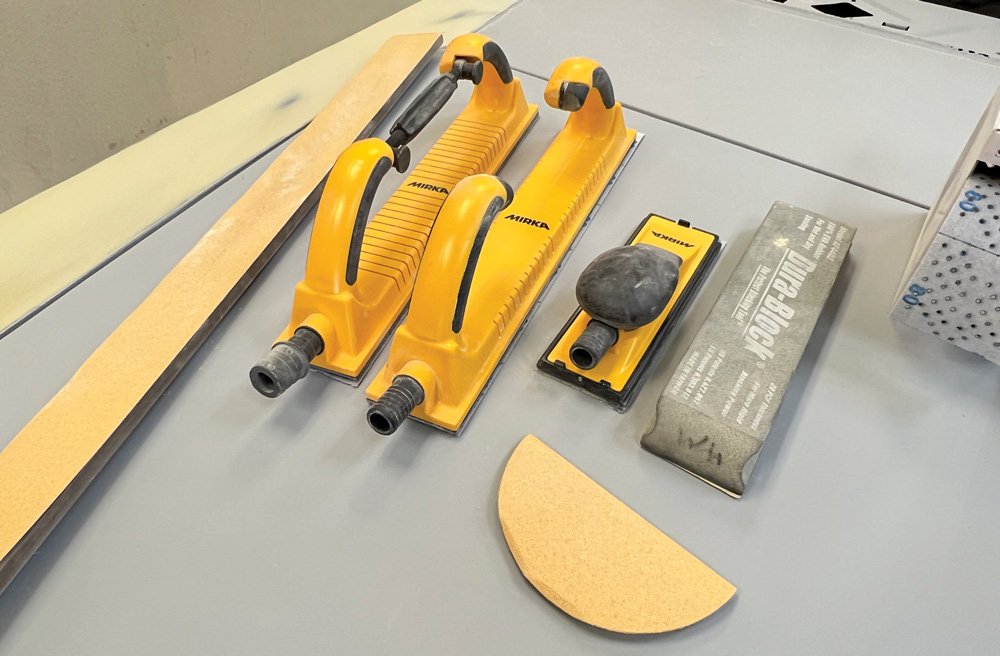
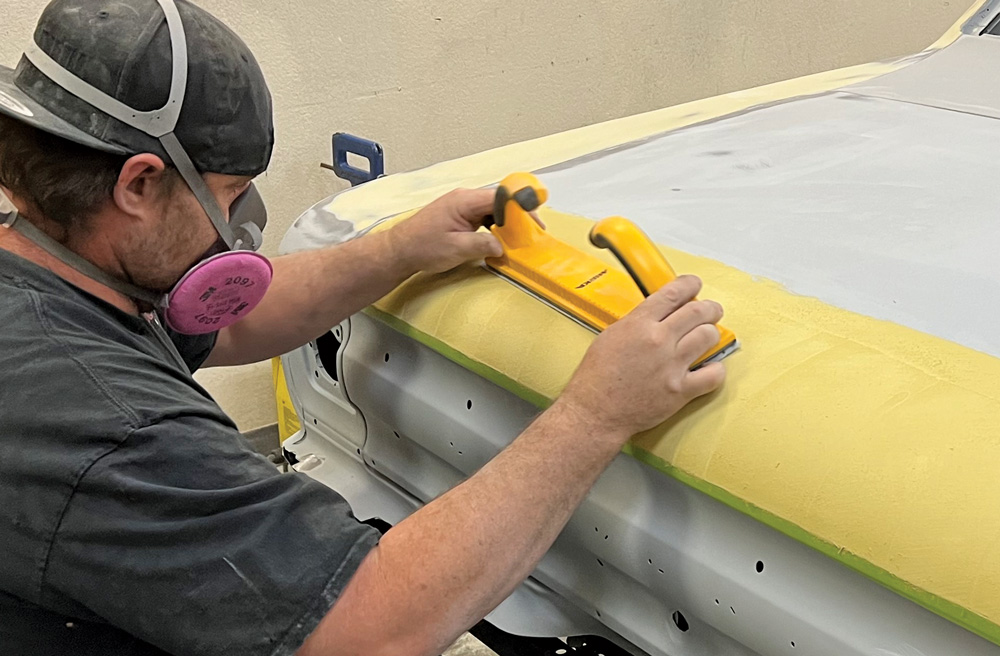
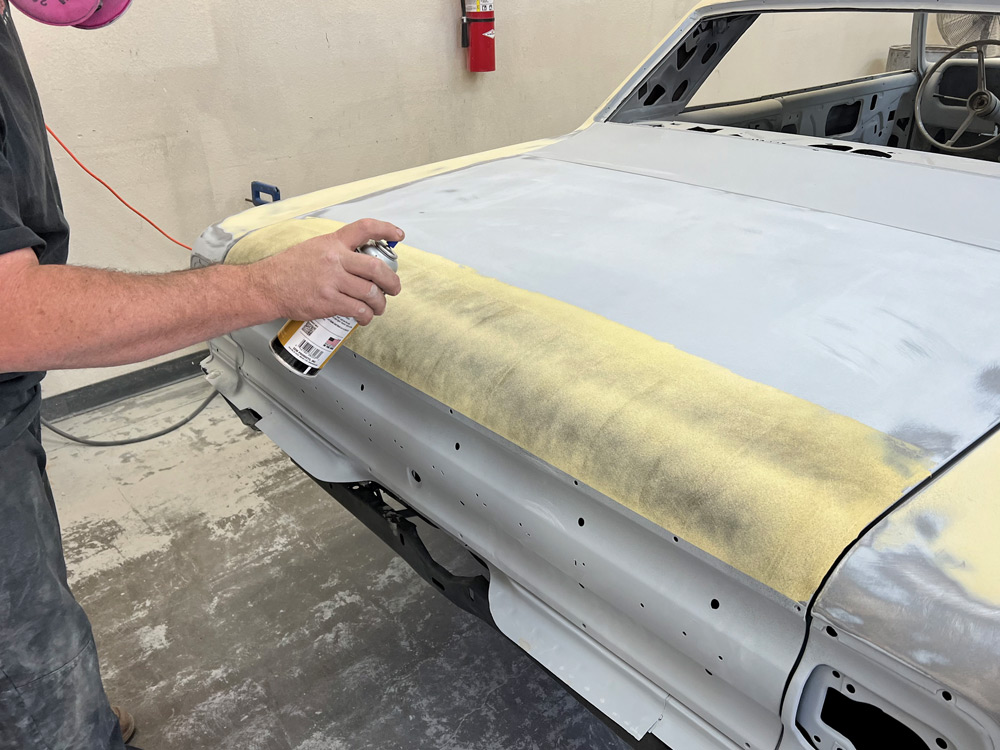
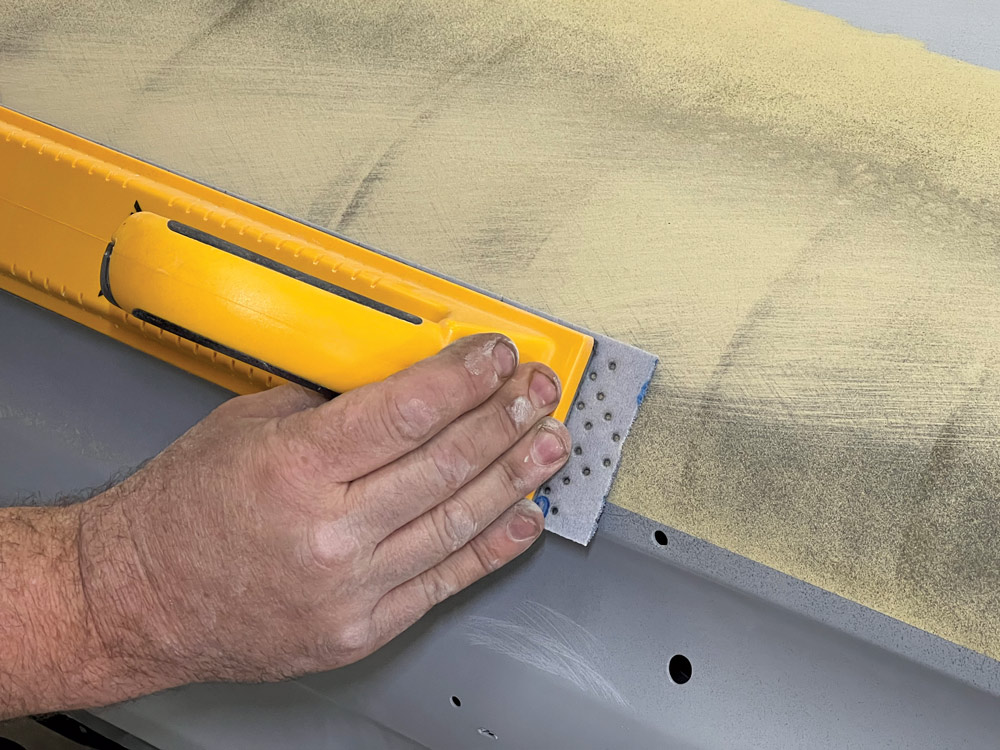
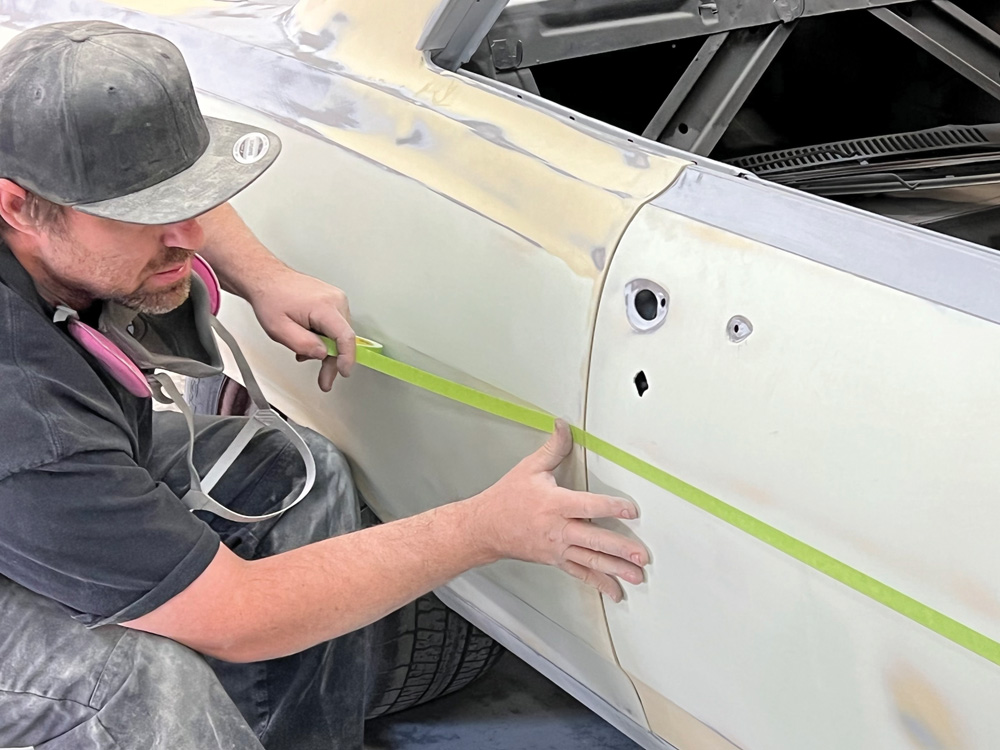


VOLUME 4 • ISSUE 38 • 2023