Modern Rodding TECH
InTheGarageMedia.com
Photography by Rodger Lee
ARTWORK BY TAVIS Highlander
n this installment, we’ll wrap up our coverage of the outstanding build on Danny Shaffer’s ’57 Ford Ranch Wagon that’s being constructed at Ironworks Speed & Kustom.
One-off wheels were designed for this project, inspired by Halibrand racing wheels of the ’50s. As with many other components on this car, the wheels were rough sketched by hand, then final design was done in CAD, and they were printed in plastic to make sure everything was spot-on before machining from billet aluminum. The wheels were machined by EVOD then polished to perfection and chrome plated for durability.
A huge amount of work went to the underhood area, with the goal of cleaning up every surface while keeping an OEM flavor. After exploring several variations, the inlet tube for the fuel injection was routed diagonally across the driver side cylinder head, which required a specially machined adapter to position the throttle body at a precise angle. It is ribbed and contoured so it is consistent with the styling theme used underhood. Special covers were machined to hide the plug wires and the injector wiring, and special grilles with curvaceous louvers were machined for the inner wheelwells.
Perhaps the crowning touch under the hood is the elaborate cover that stretches between the fenders just forward of the radiator. This elegant construction fits closely around the hood hinges and features a custom-machined badge that closely resembles what Ford might have put on such a cover.
The heads and the entire engine block were painstakingly ground smooth, so they would be as nicely finished as any other detail on this top-level build.
You may remember from the last article that the interior of the car was modeled on the style of the ’60 Ford Thunderbird. A special hood scoop was designed and fabricated to pay further homage to the vintage ’bird, and as with many other details it was first freehand sketched, then computer modeled, and printed in plastic to check the fit and design before any metal was cut. This was a major undertaking and comprises the biggest change to the exterior sheetmetal. The results are outstanding, and the scoop and its bezel look like they were factory-designed for this car.
The finished bodywork is just being completed as we wrap up this article, and it won’t be long until you see the finished result on these pages. Be sure to tune in for that!
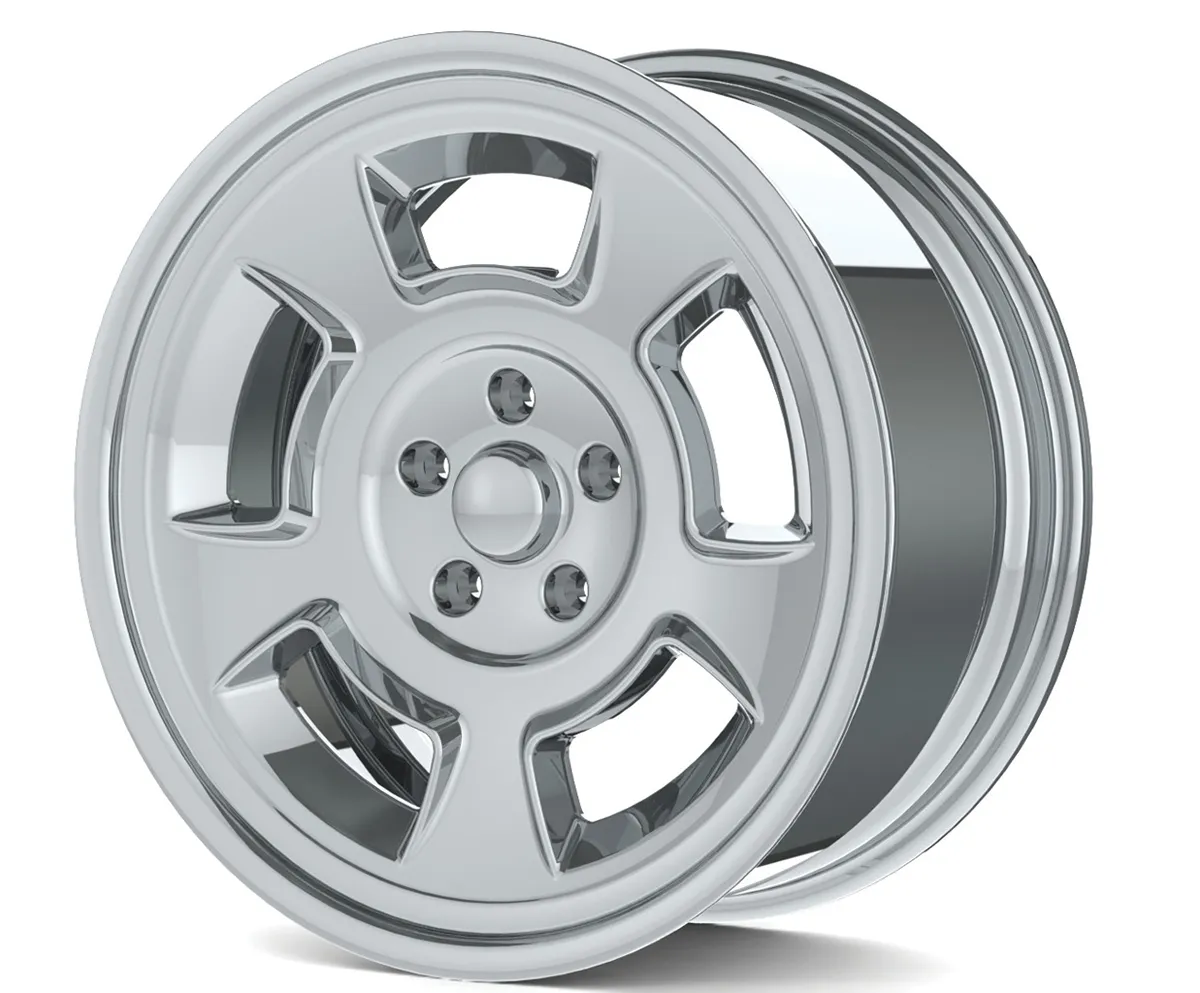
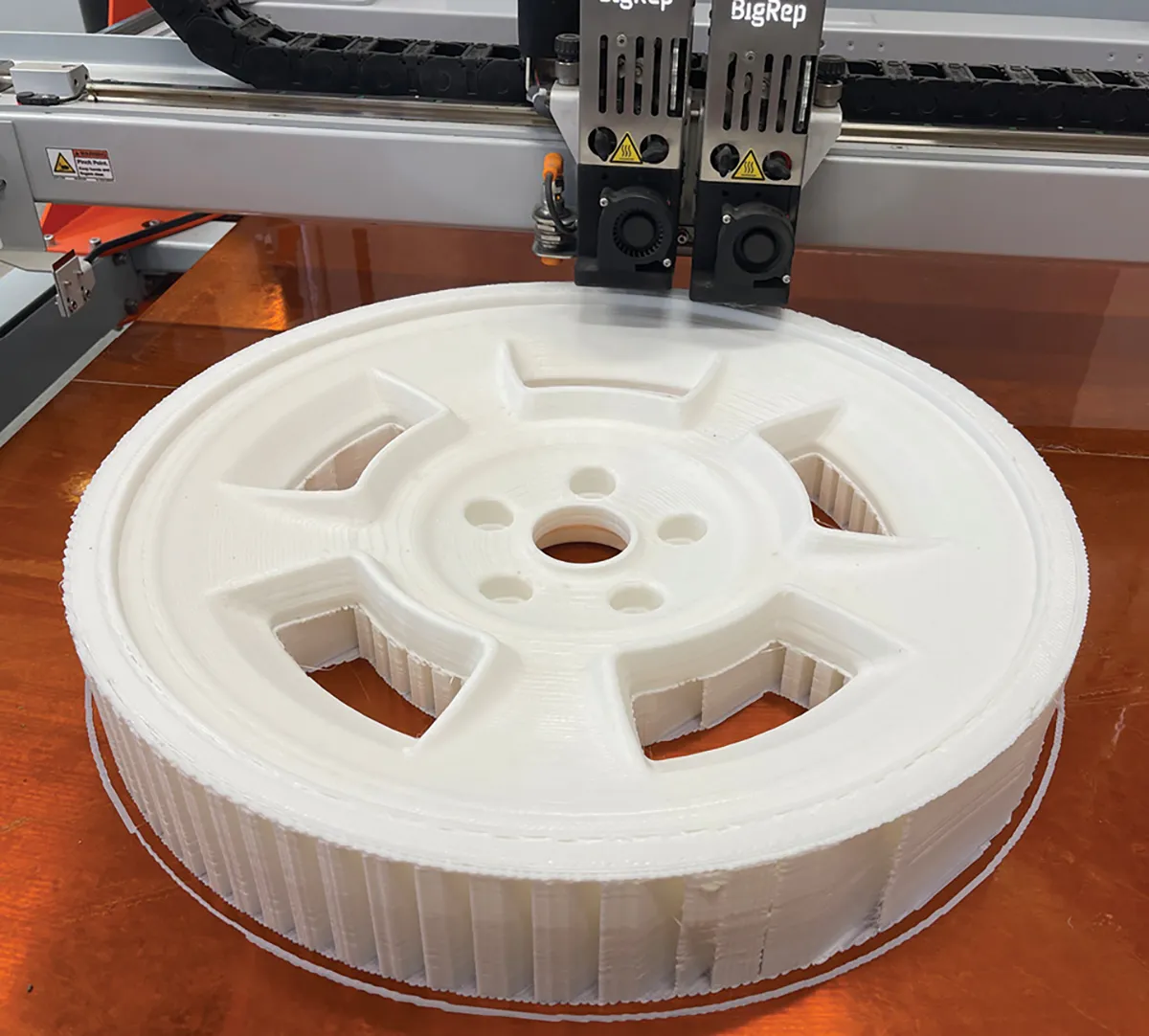
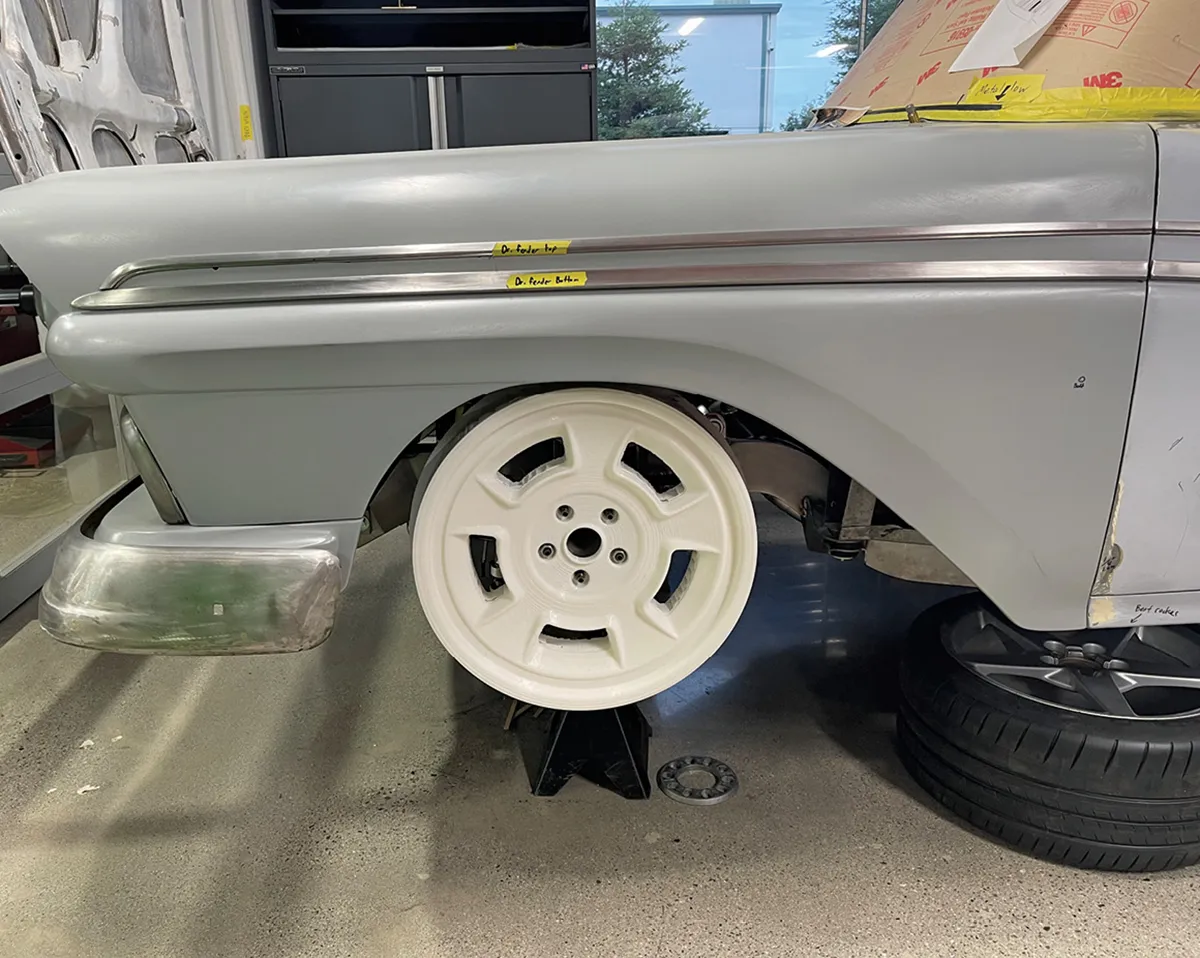
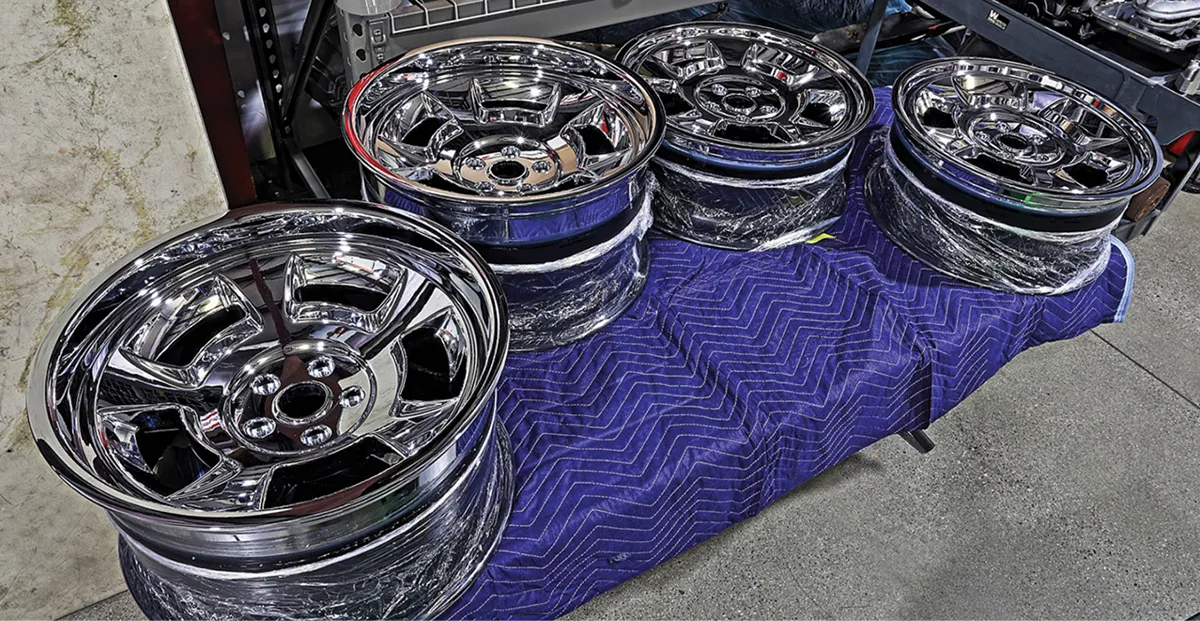


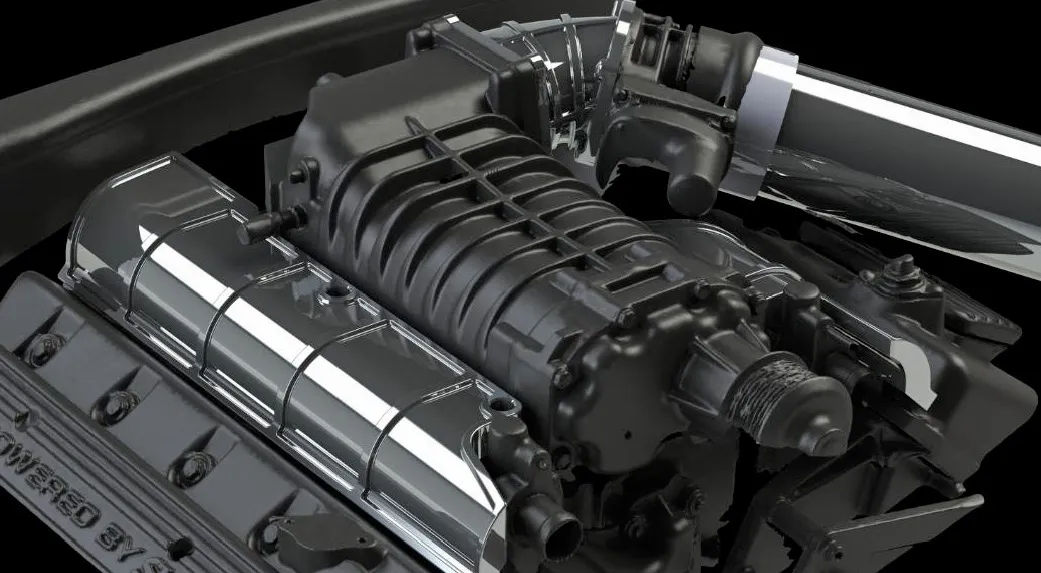
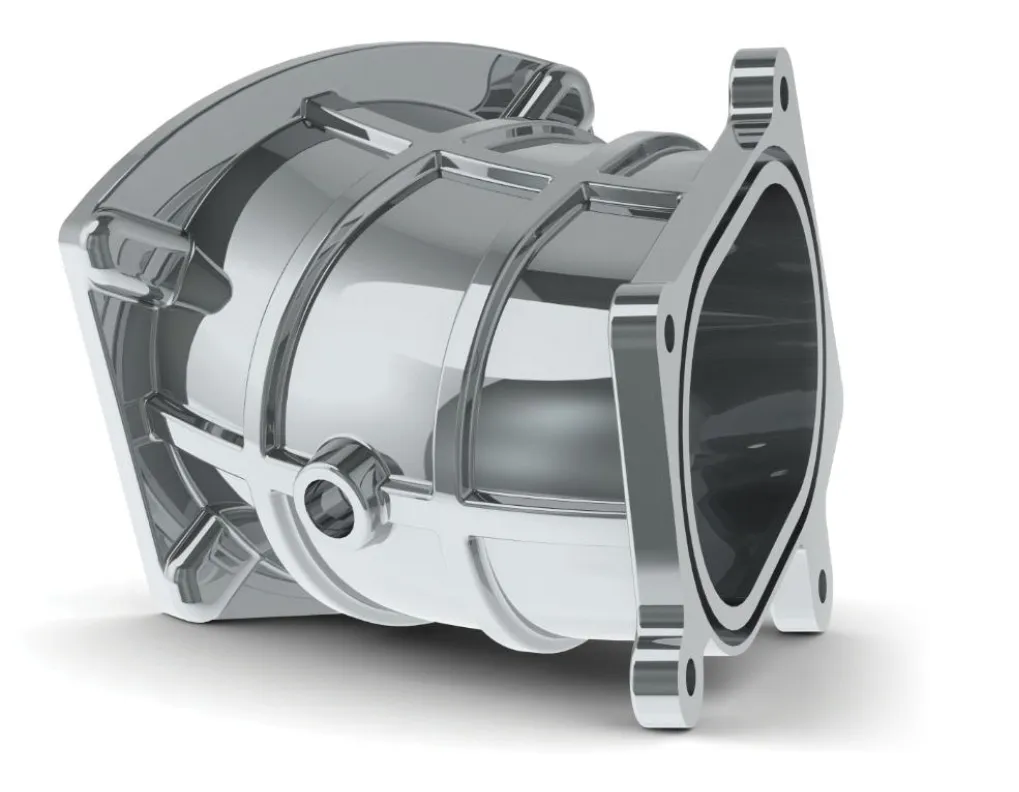
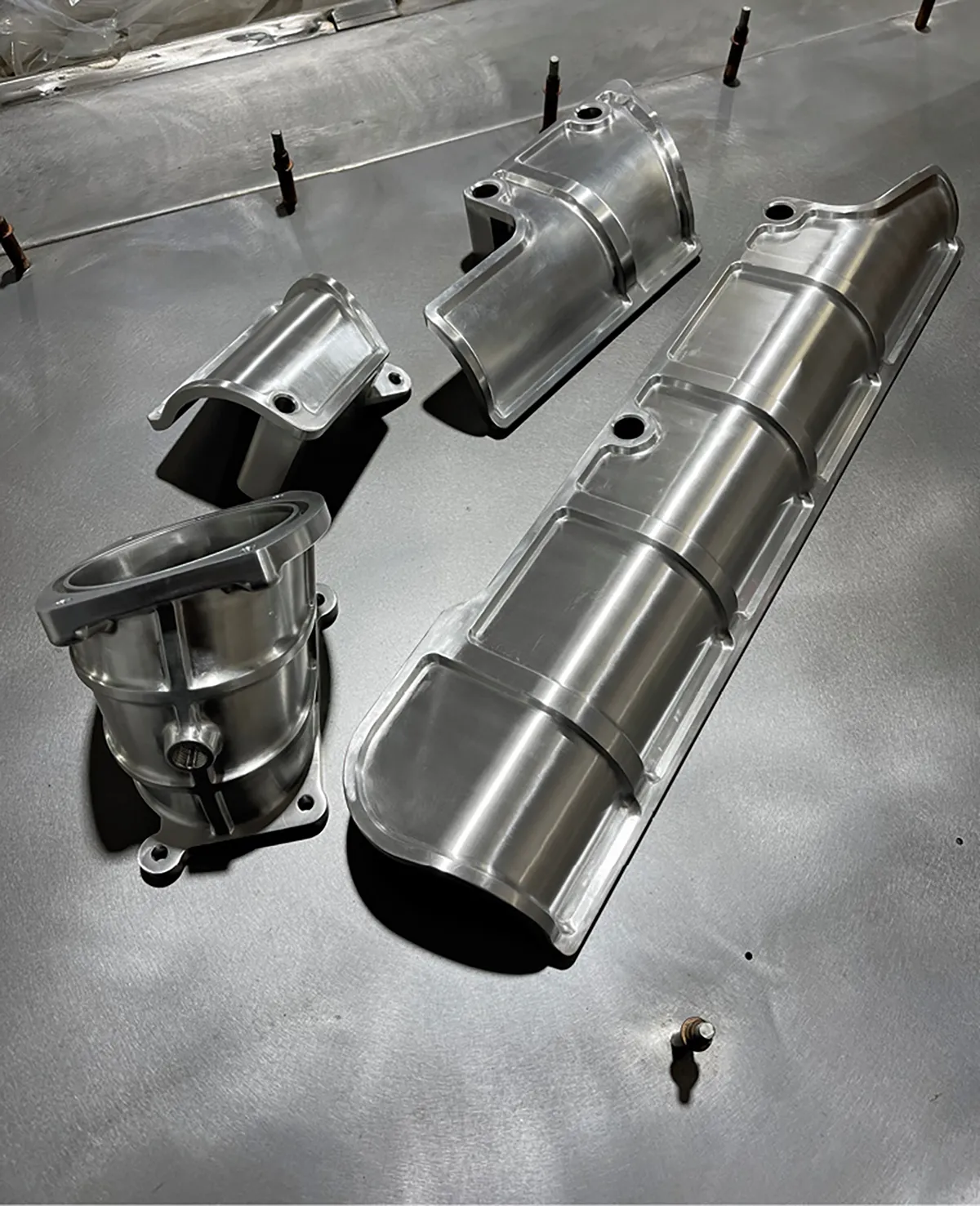
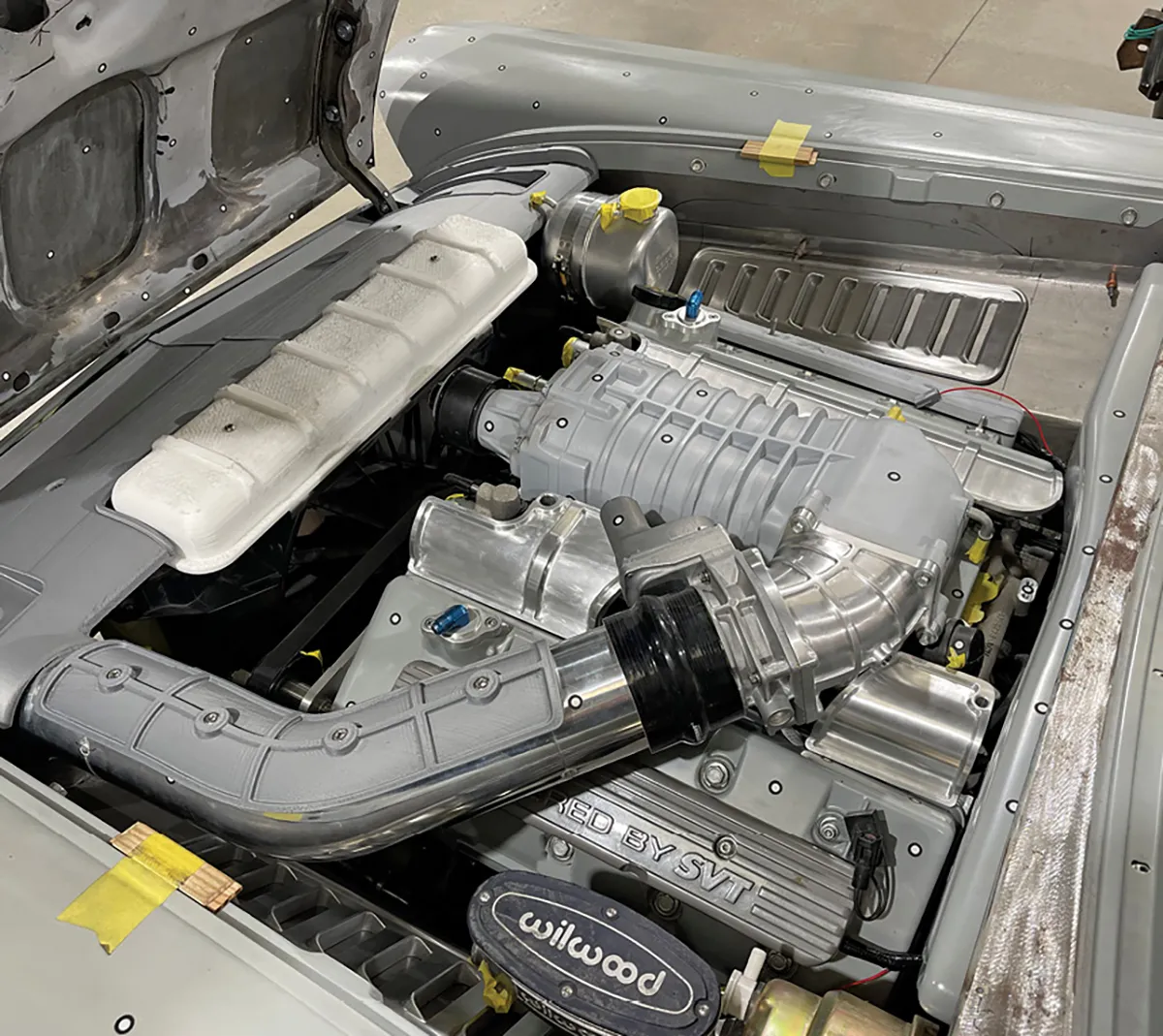
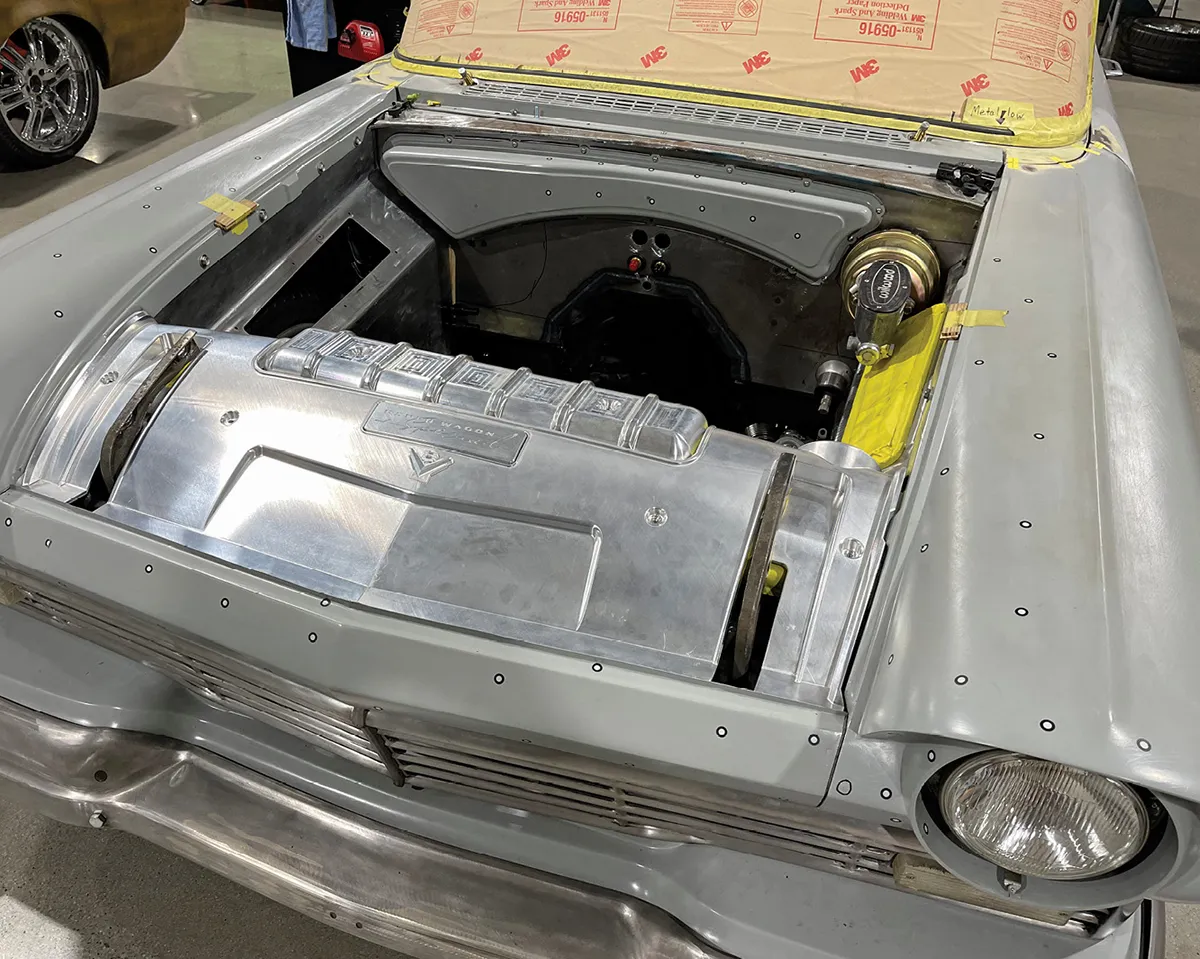
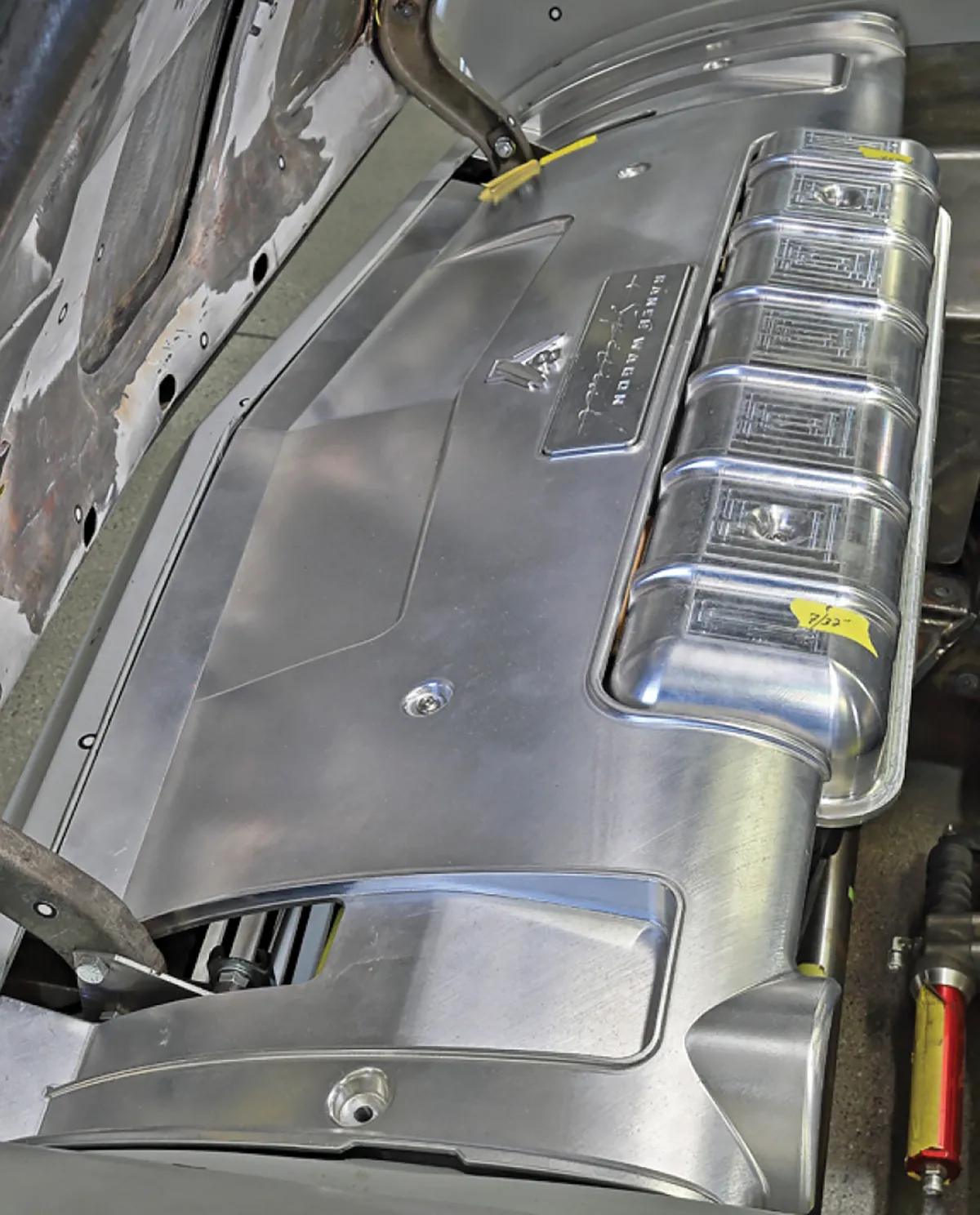
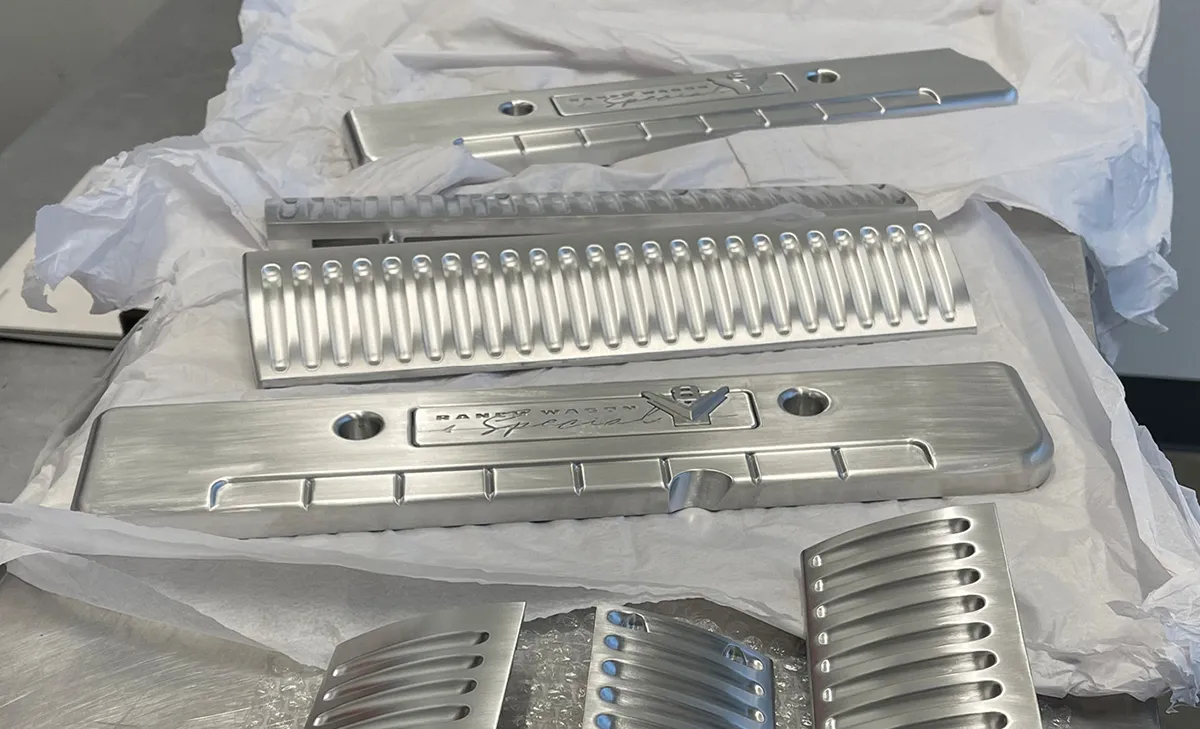

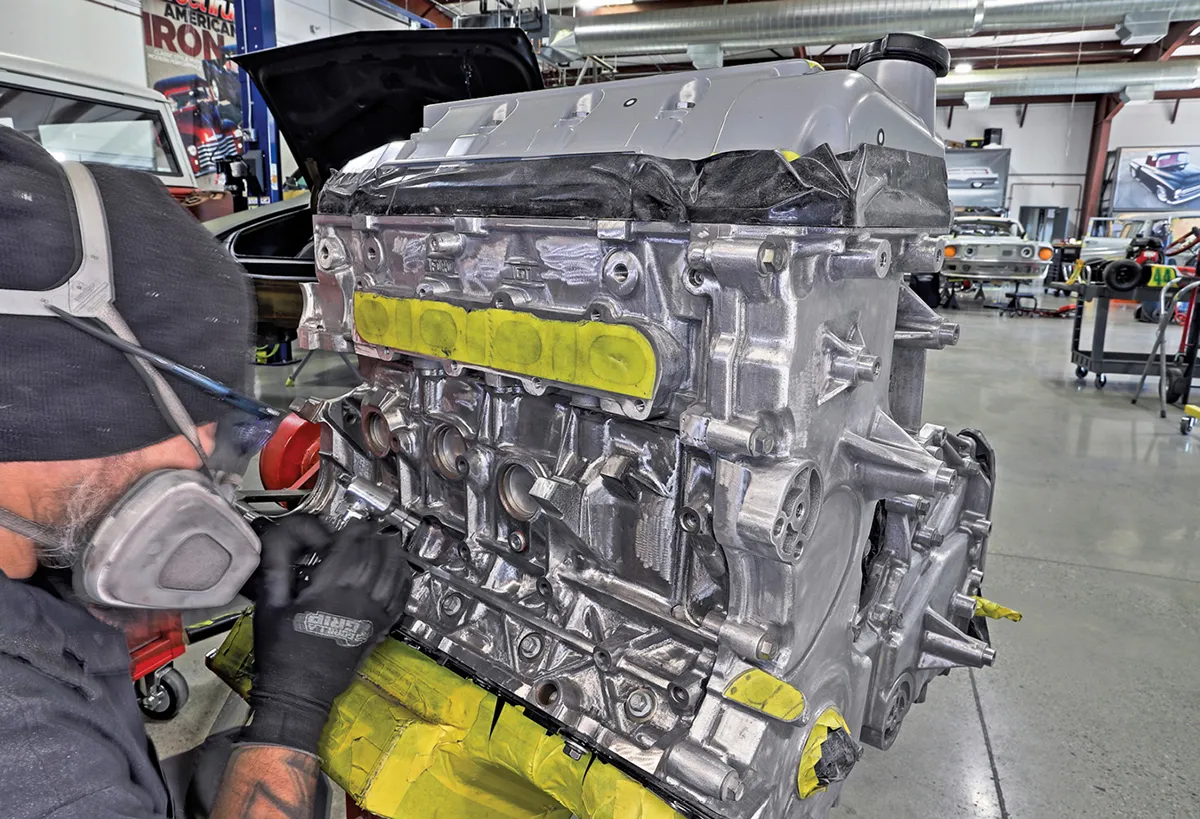

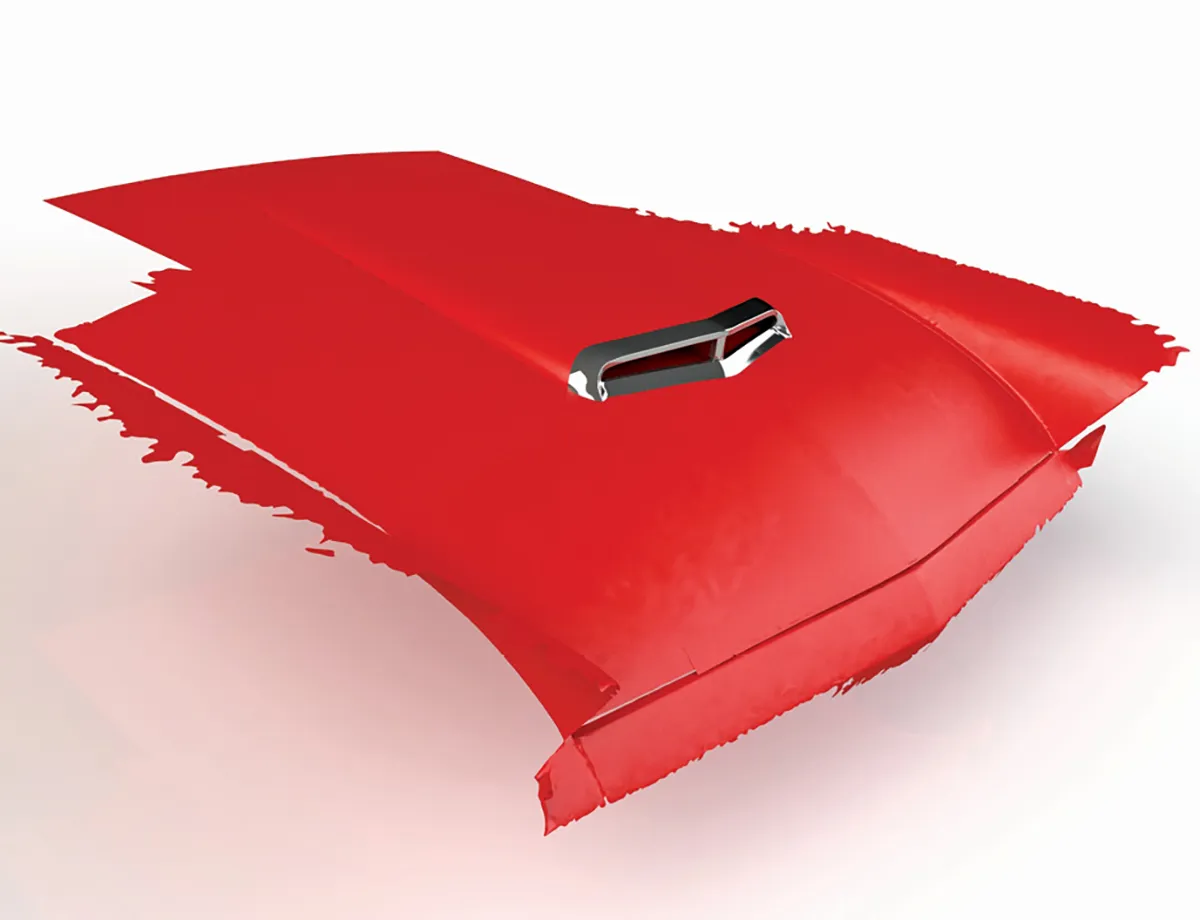
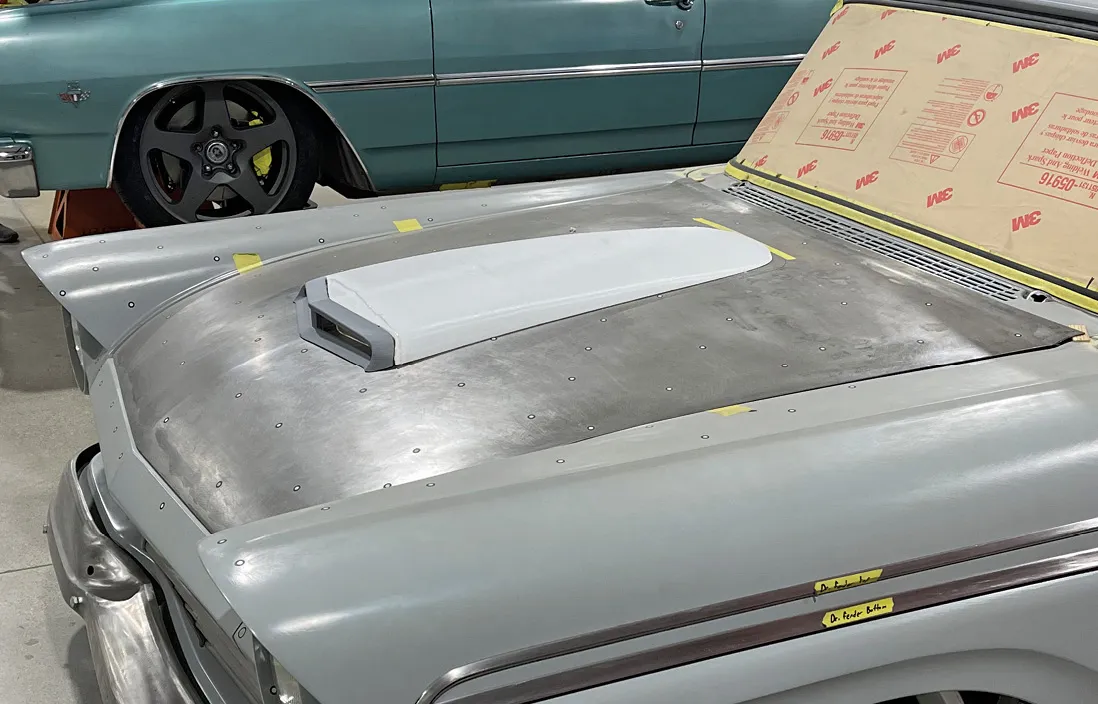

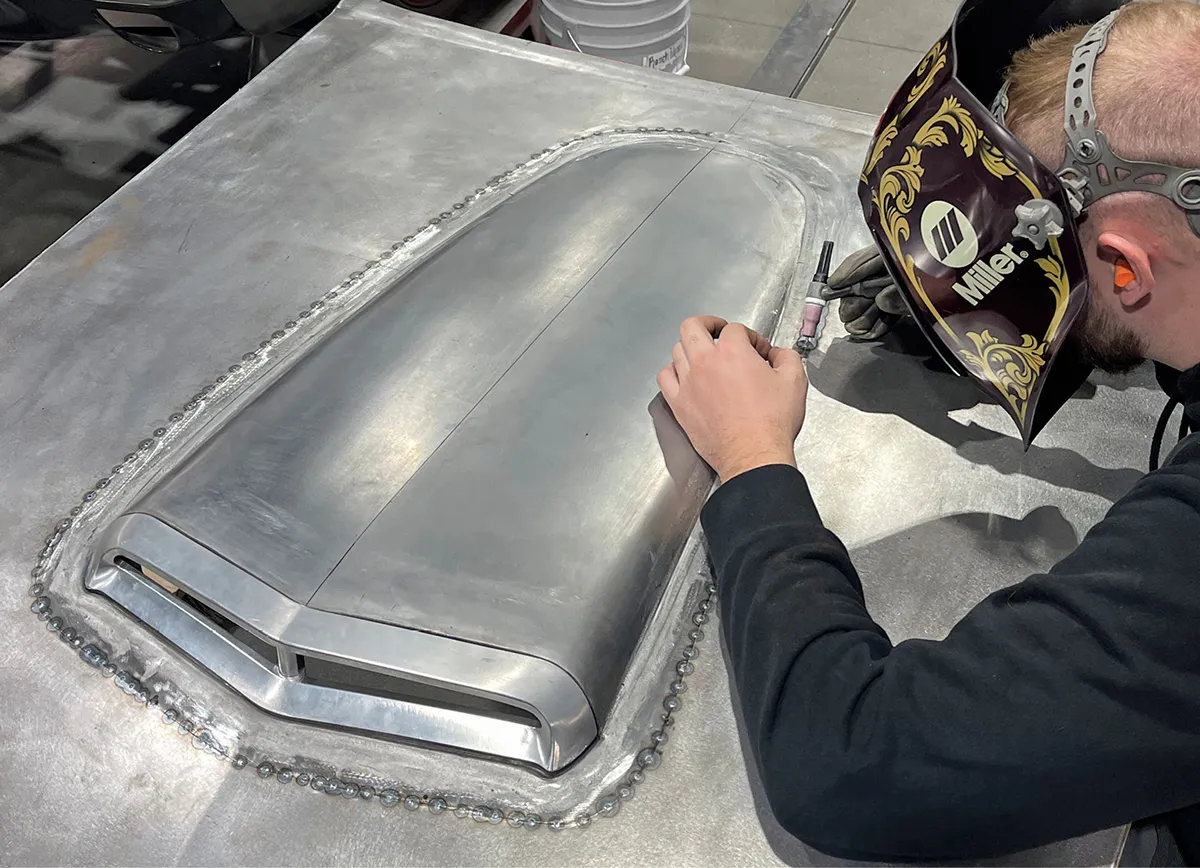
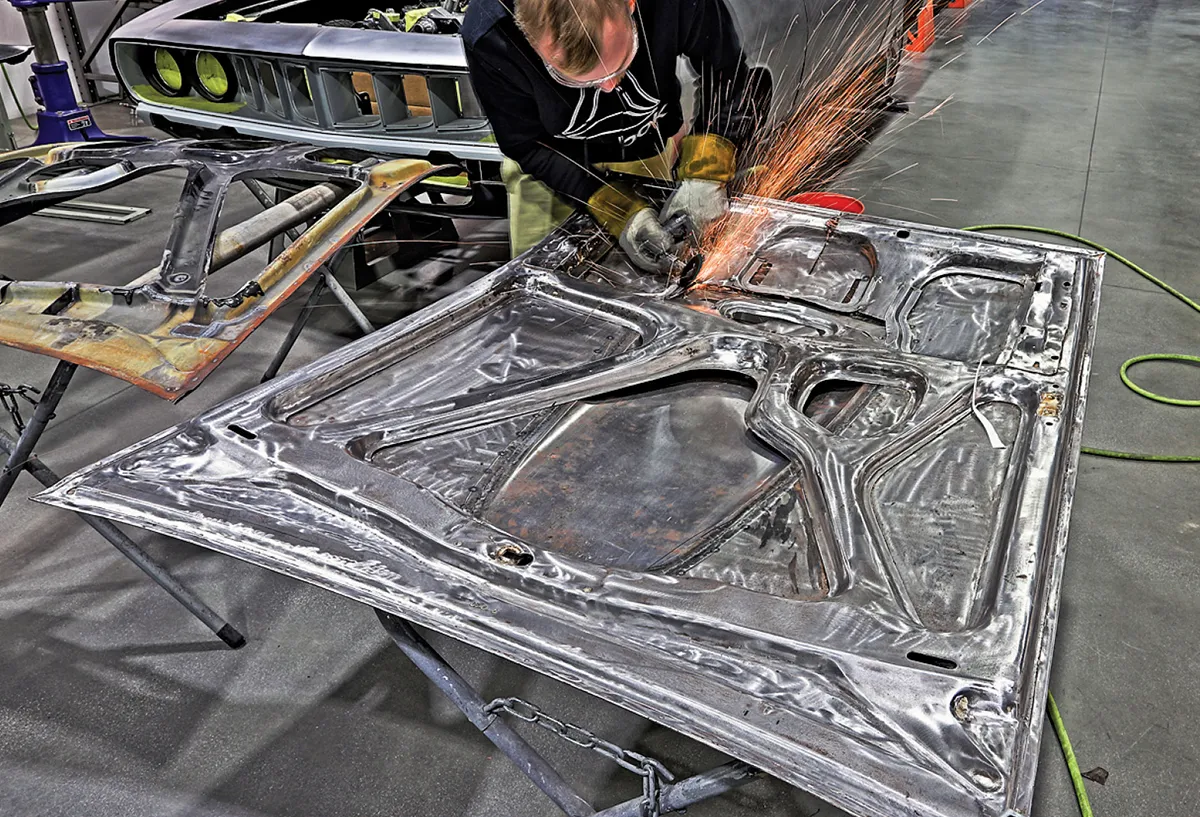
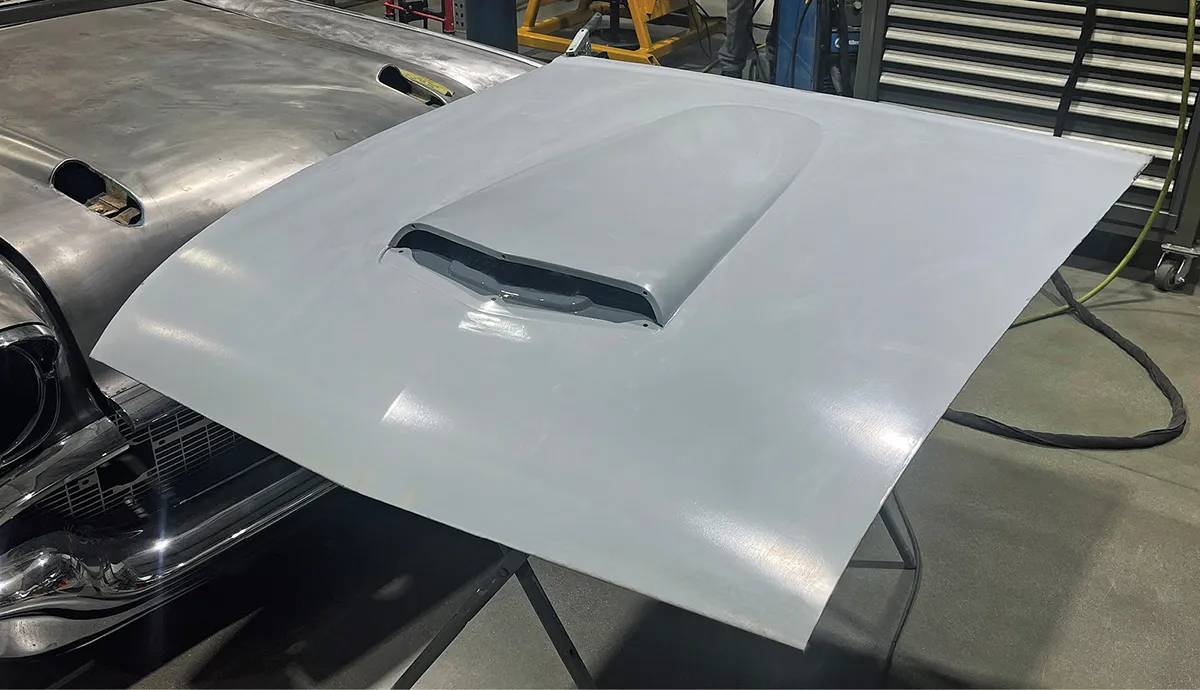
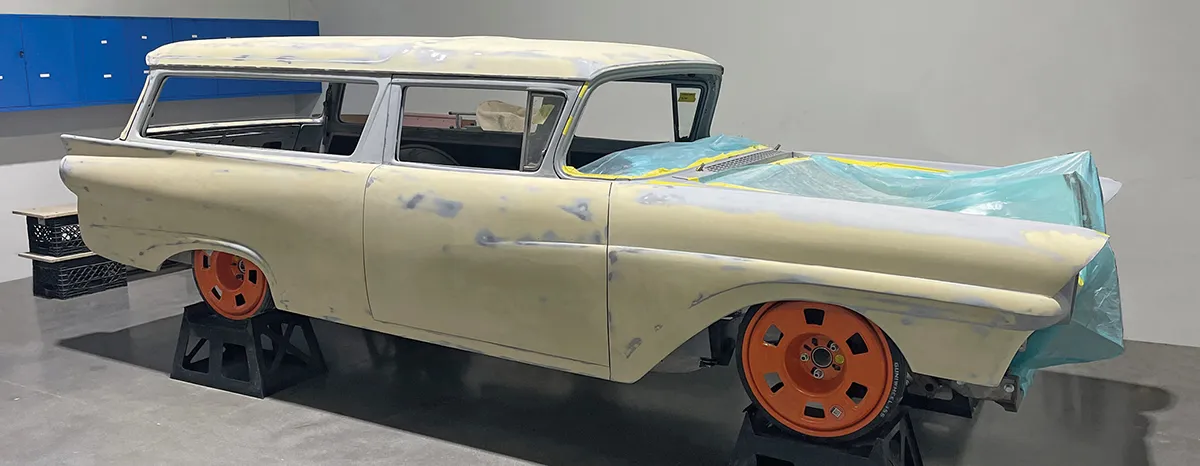
