Modern Rodding TECH
InTheGarageMedia.com




n the early days of forced induction, almost all the blowers adapted by rodders were ingeniously based on compressors not designed for pumping more power out of the Ford Flathead. In fact, not even the famous “Jimmy” Roots-type blowers were designed to increase output of the diesel engines on which they were originally fitted.
The GMC 71-series blowers were developed as air compressors to pull in fresh air and push out exhaust gases on Detroit Diesel two-stroke diesel engines. A 6-71 blower was a compressor on a six-cylinder engine, while a 4-71 was a four-cylinder application. Hot rodders adapted the GMC blowers to their four-stroke engines. It should be noted that the number “71” represents the number of cubic inches per cylinder.
In Italy, however, at the start of the ’50s, fledging manufacturer Italmeccanica Co. developed a Roots-type positive-displacement supercharger specifically for Ford Flathead engines. The original goal was to sell cars with the supercharged powertrains, but while the cars didn’t sell as expected, the blower package drew attention. Kits were developed and exported to the United States.
Interest was strong, but the build quality of the early blowers was lacking, particularly when it came to porosity issues with the case casting and design problems with its one-piece driveshaft. The company dissolved and was reborn as Supercharger Company of Turin (S.Co.T.). The quality of the supercharger improved significantly, but by the time reborn blower kits were hitting their stride, Ford was abandoning the Flathead for the Y-block OHV engine family. Nevertheless, the S.Co.T. and early Italmeccanica blowers have been inextricably linked with Flathead performance.
The S.Co.T. blower went out of production but reconditioned compressors remained a popular period speed part for decades. In 2006, California-based H&H Flatheads resurrected the S.Co.T. supercharger with all-new castings and design enhancements that addressed the original’s flaws. The reborn blower looked virtually identical to the original, down to the Italian origin castings in the front and rear plates, but all made in the USA.
That’s what we’re looking at with this story: The installation of a modern, H&H-produced supercharger system on a Flathead—a 276-inch 8BA (1949-53), to be exact. It powers David Weinberg’s Model A and the installation was performed by Flathead guru Bill Jagenow, at Brothers Custom Automotive in the Detroit area.
On an engine that already had a comparatively low compression ratio of about 7:1 and the kit’s approximate 5 pounds of boost, the blower would pump up the Flathead by an estimated 50 additional horsepower. Not too shabby considering the naturally aspirated engine breathing through a pair of 97s was making about 160 or 170 hp—but it’s also a kit designed more for its nostalgic look than maximum, high-rpm horsepower.
“With the V-belts driving the blower and its modest boost, this isn’t the setup to run the dry lakes,” Jagenow says. “But it nails the traditional look and delivers a serious performance boost to the engine, which is great for the street.”
The kit includes the compressor itself, along with the intake manifold, crank pulley, water pump pulleys, and a belt tensioner. That leaves a few things to be sourced, including the drivebelts. While the manifold and compressor bolt on easily enough, it’s not exactly a bolt-on project from start to finish.
“There are almost countless variables with Flathead engines,” Jagenow says. “That’s especially true with all the different factory and aftermarket cylinder heads, which means a variety of potential clearance issues to deal with during the installation.”
That’s exactly what Jagenow encountered after initially test-fitting the blower and manifold. The bulge of the blower case protruded into the real estate for the thermostat housings of the Harrell cylinder heads, which had early style central water outlets, compared to the front-positioned outlets on a factory-style 8BA design.
There were a couple of other clearance issues, too, which are detailed in the accompanying photos, but the bottom line is trimming, fabrication, and some other on-the-fly engineering adjustments should be expected.
“With the front-mounted water outlets and top-mounted distributor, the 8BA is probably the easier Flathead design for one of these installations, but they all have their minor challenges to overcome,” Jagenow says. “Every Flathead combination is a little different, so the procedures will vary from engine to engine.”
Of course, there are also fuel and ignition timing adjustments to be made, but that’s the case with every supercharged engine. The highlights are outlined in our photos, which are intended to provide an overview of what’s involved.
The basic kit from H&H Flatheads with a polished case starts at $8,500 plus shipping. With the additional components needed for the installation, including the belts and miscellaneous hardware, there is probably $10,000 in the parts tally. Jagenow estimates a professional installation would take 16-20 hours, including the final tuning.
That’s not chump change, but nostalgia has its price. In this case, that vintage look is accompanied by a reengineered supercharger system designed for greater durability and long-term performance—and that adds value.
As one of the first dedicated supercharger systems developed for the Flathead, the classic Italian-designed S.Co.T. blower, will always look bellissimo between the heads of one. The improved design of H&H Flatheads’ system makes it a more practical choice than a vintage unit for a hot rod intended to be driven regularly. The kit will simply need some fettling and additional components before it’s ready to force-feed the Flatty.
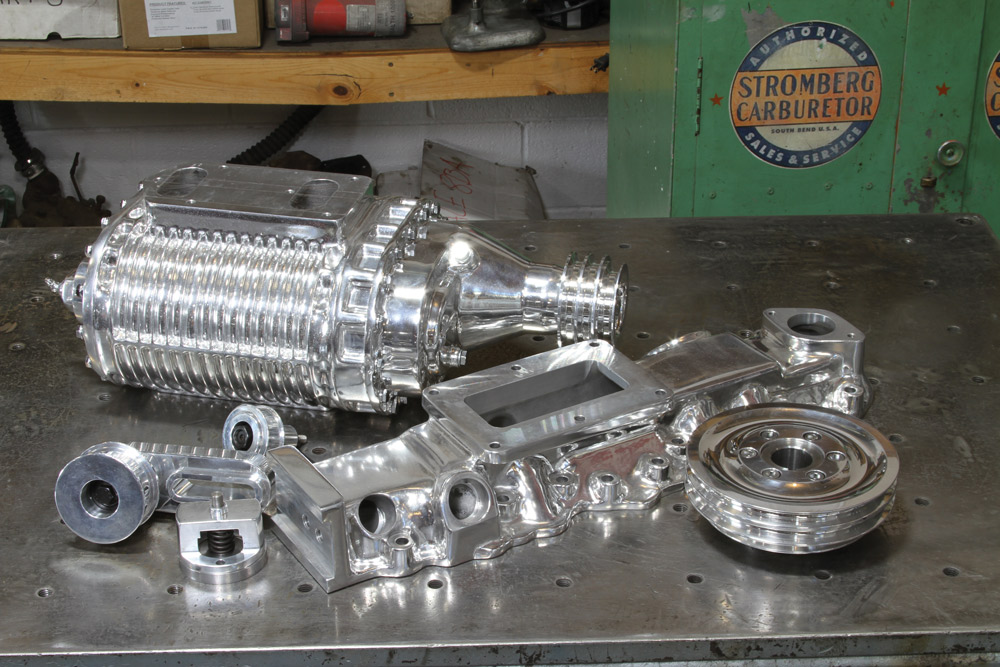
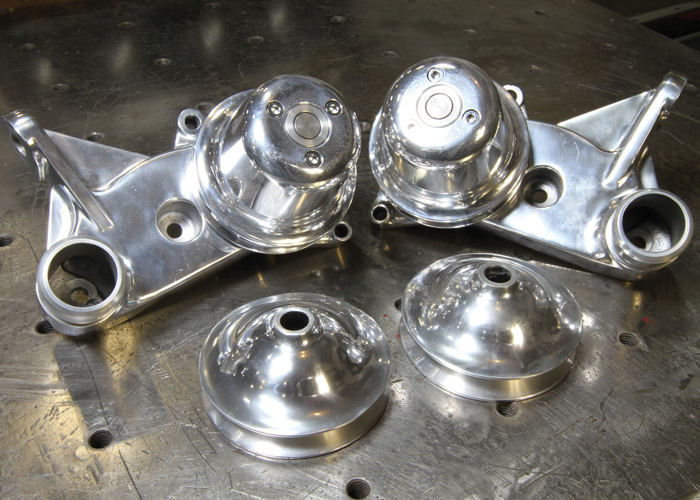
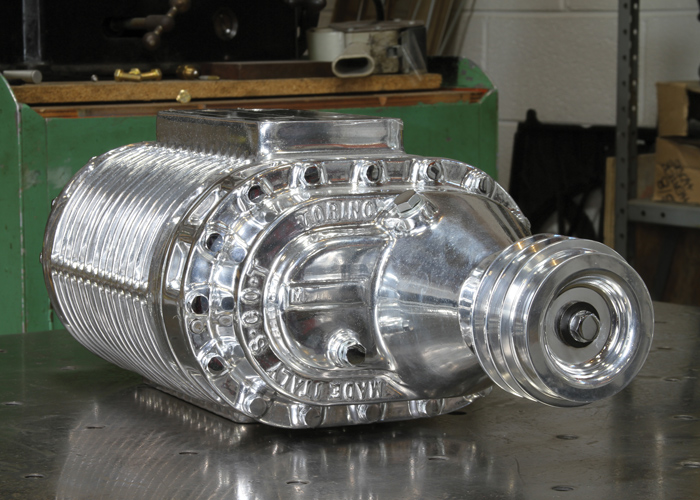
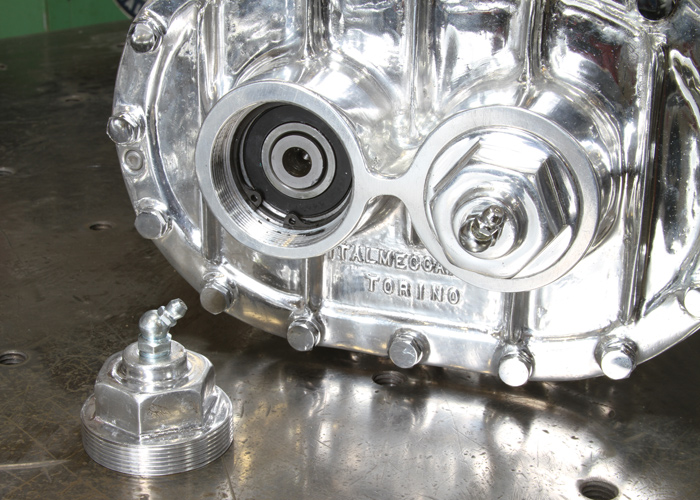
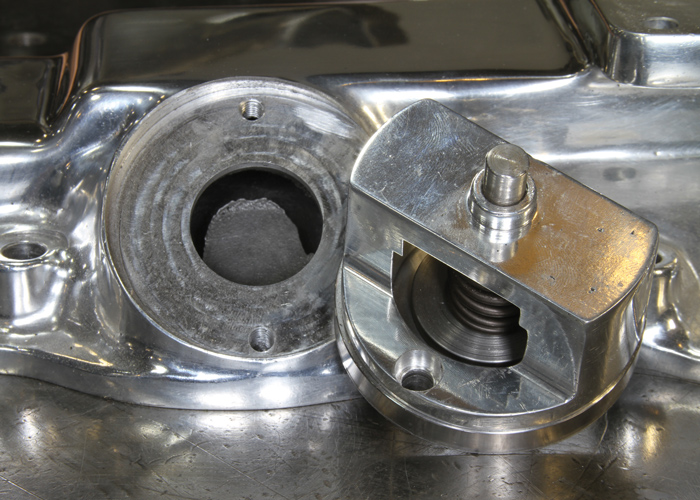
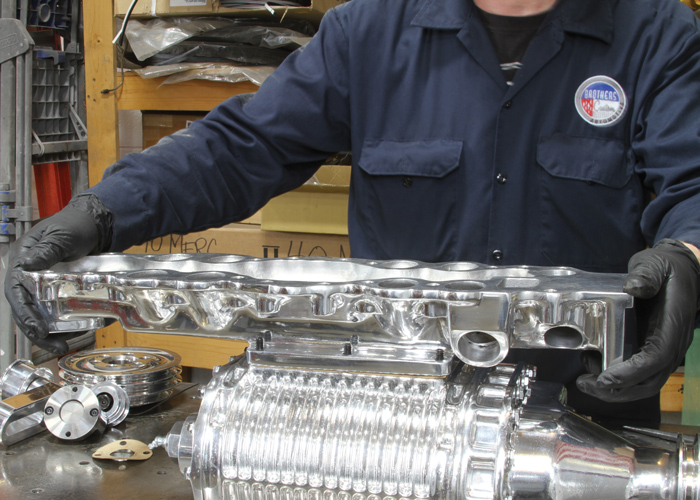
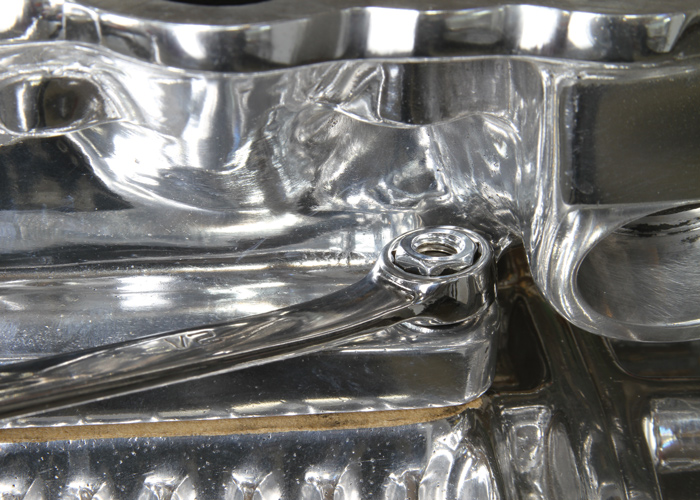
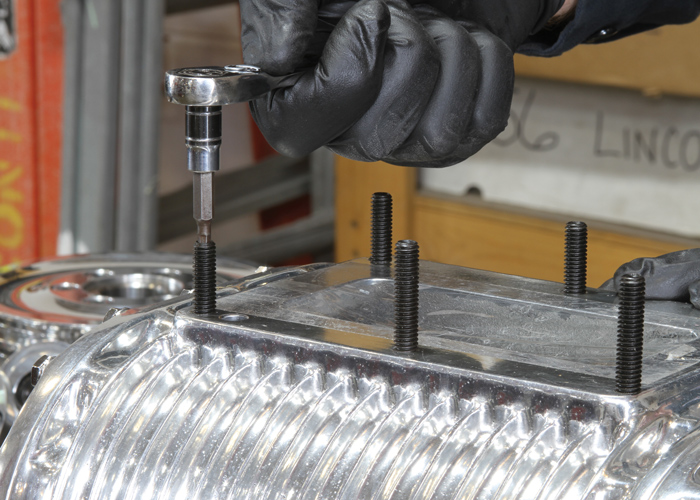
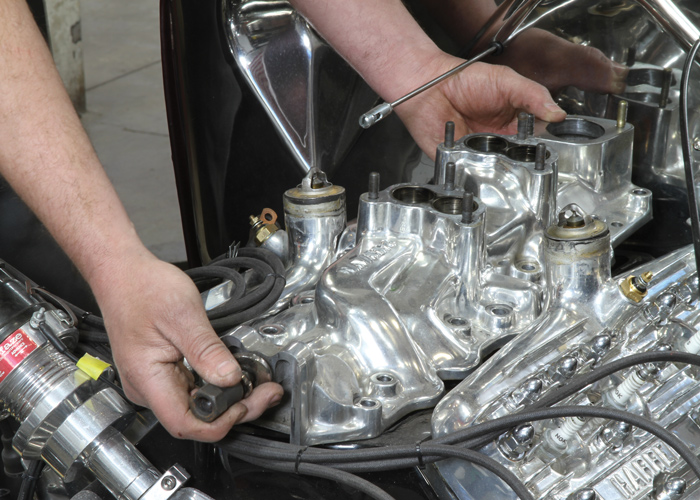
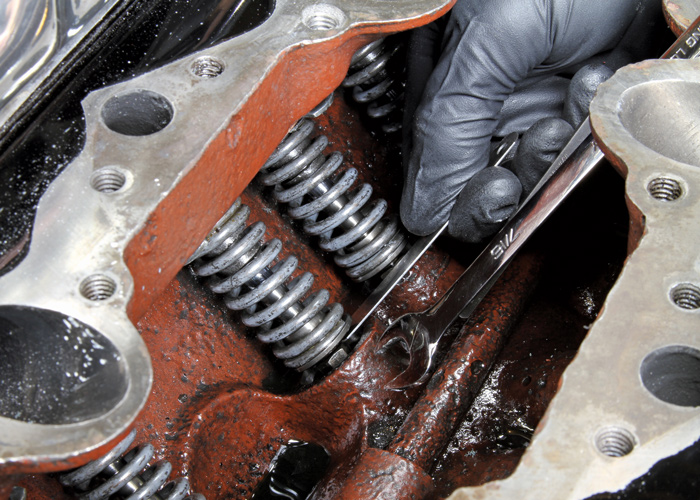
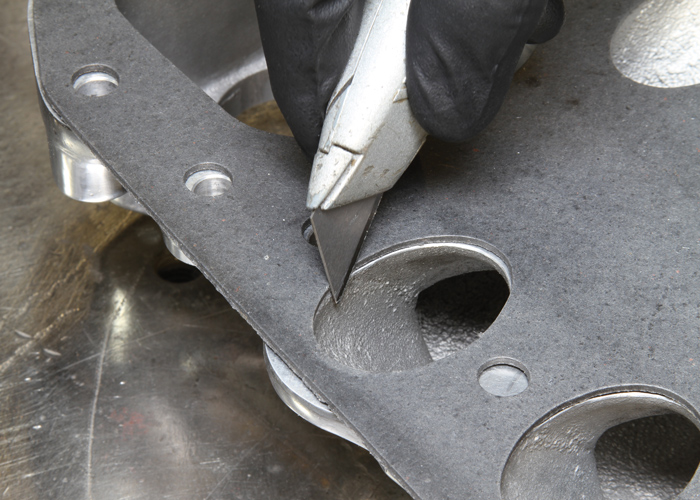
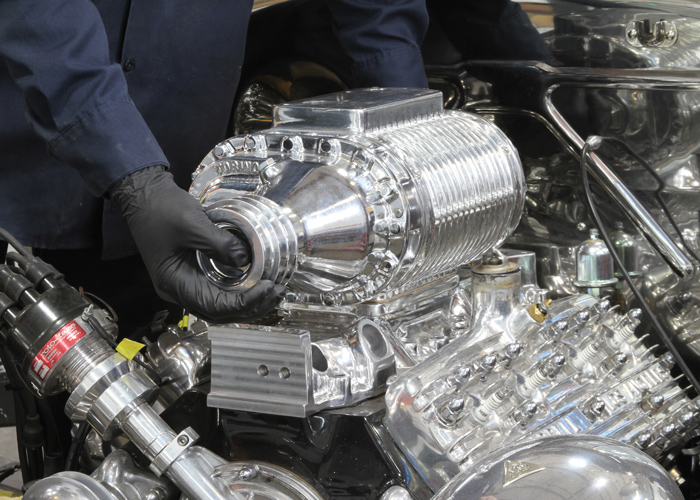
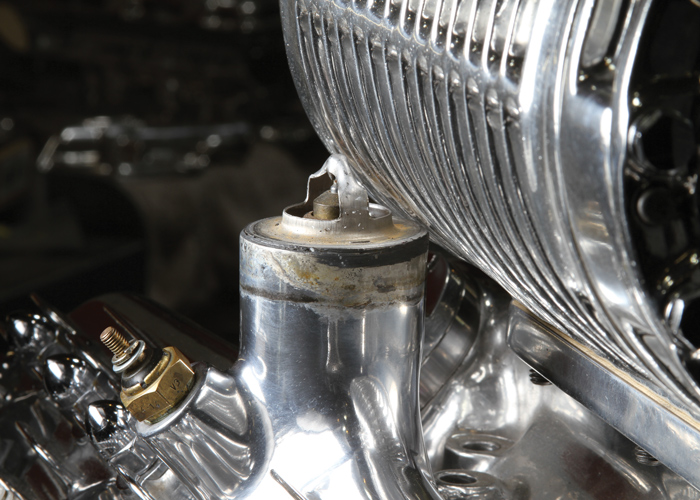
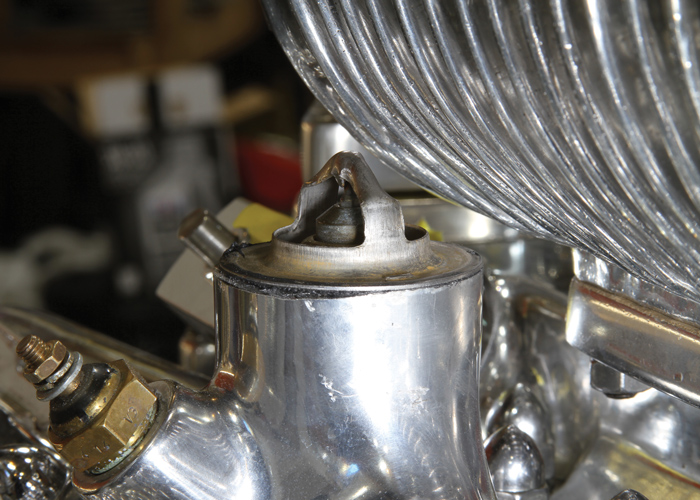
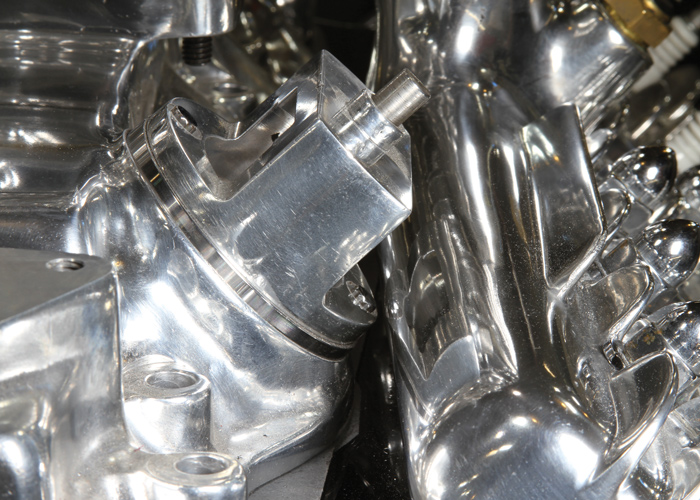
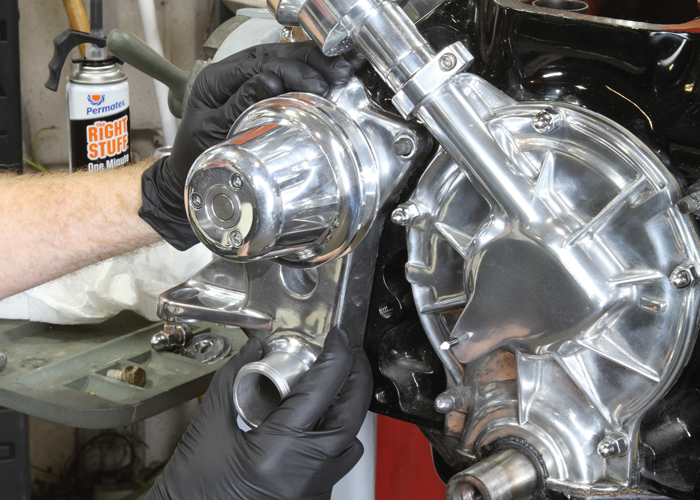
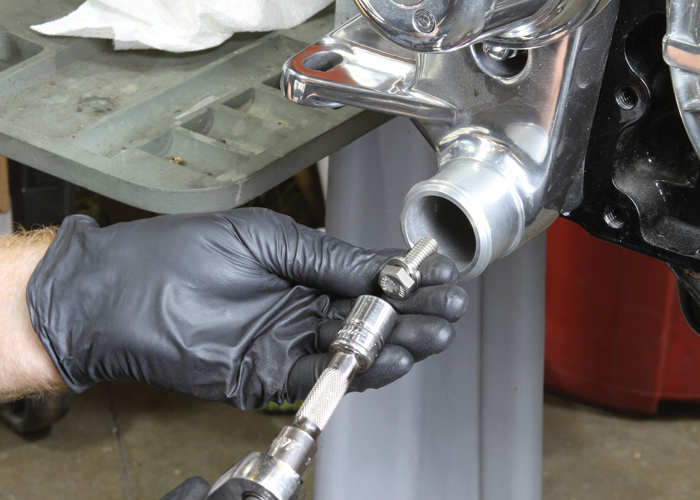
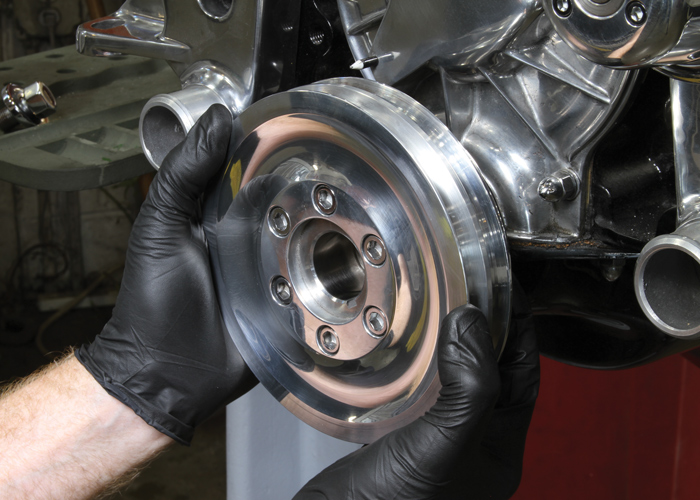
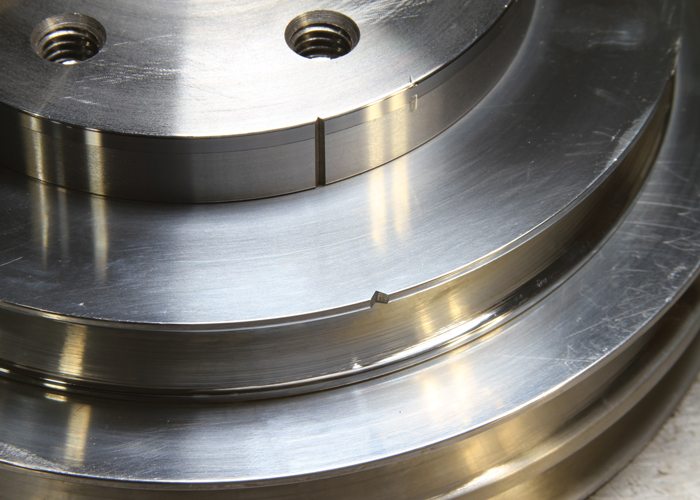
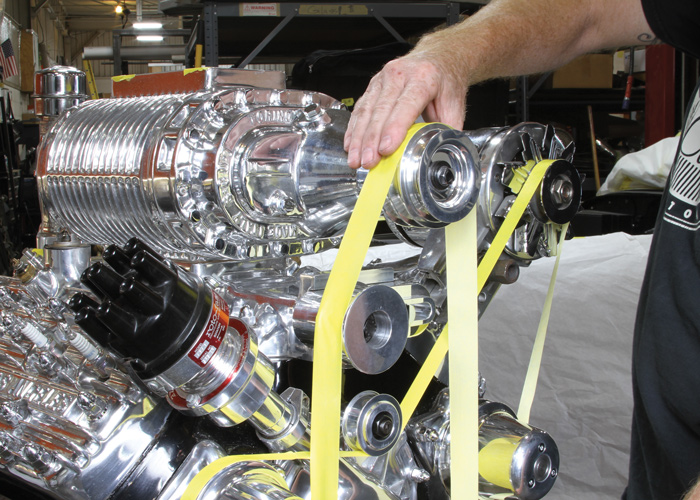
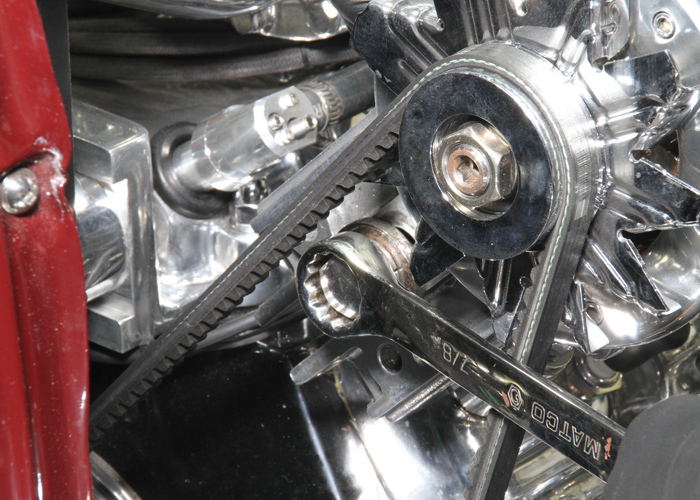
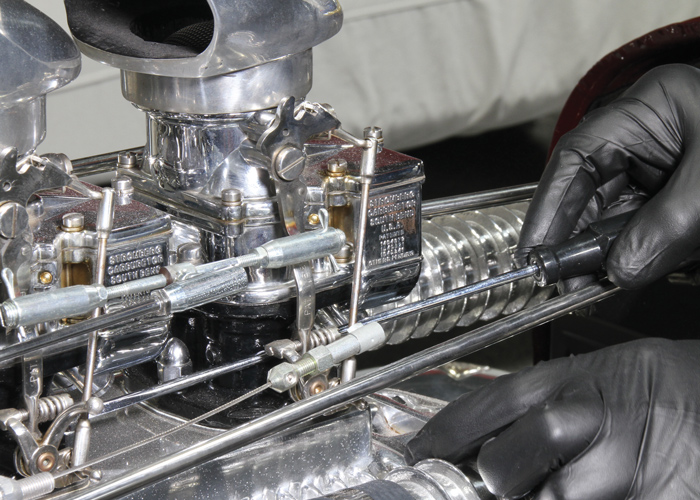
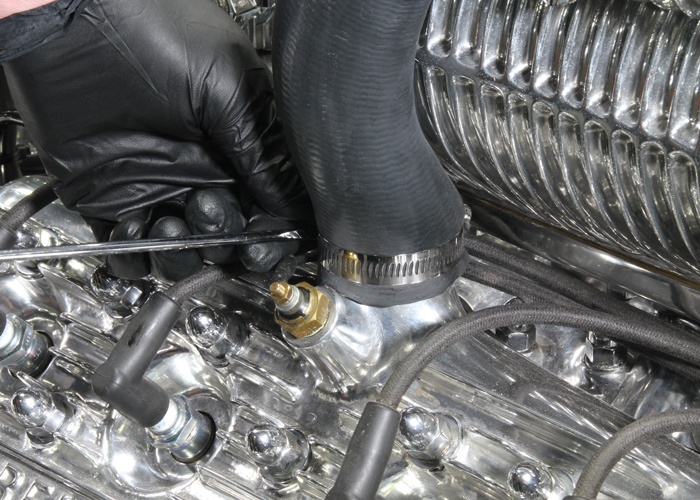
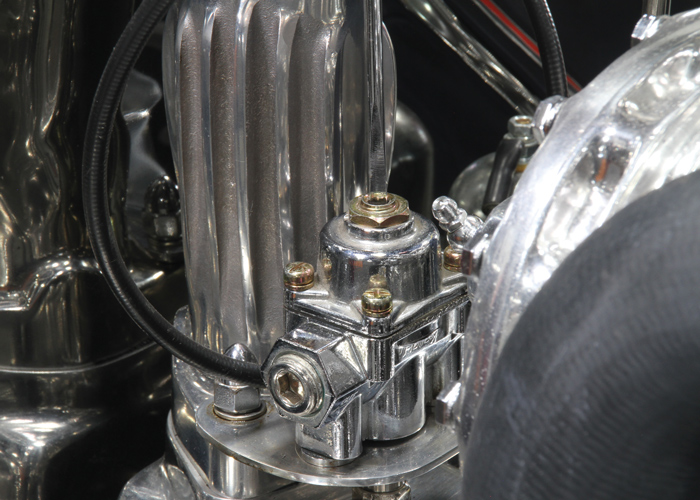
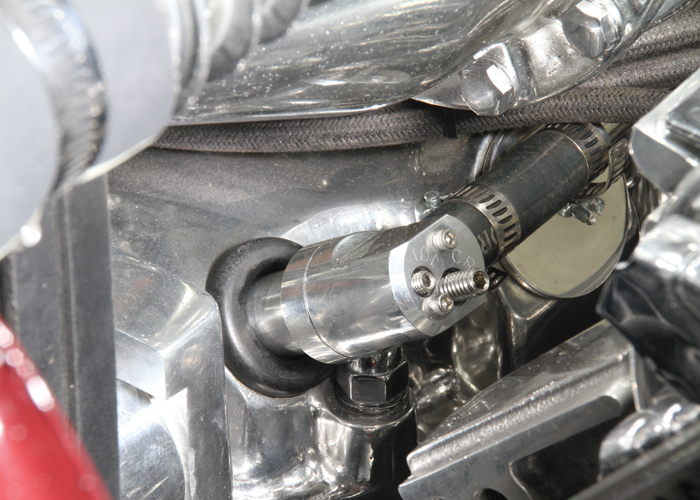
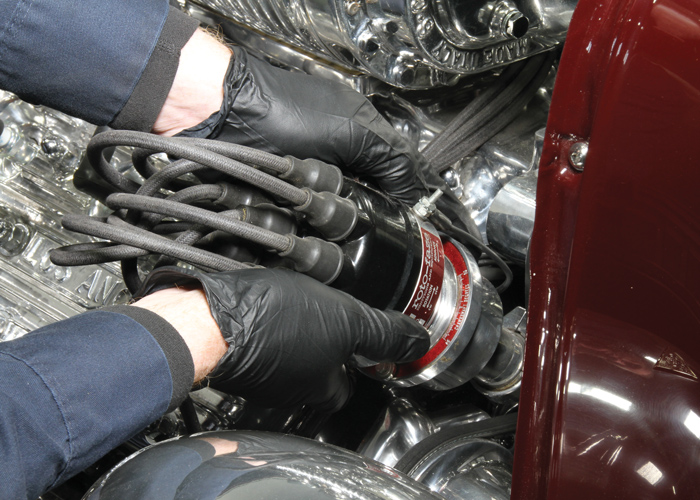

