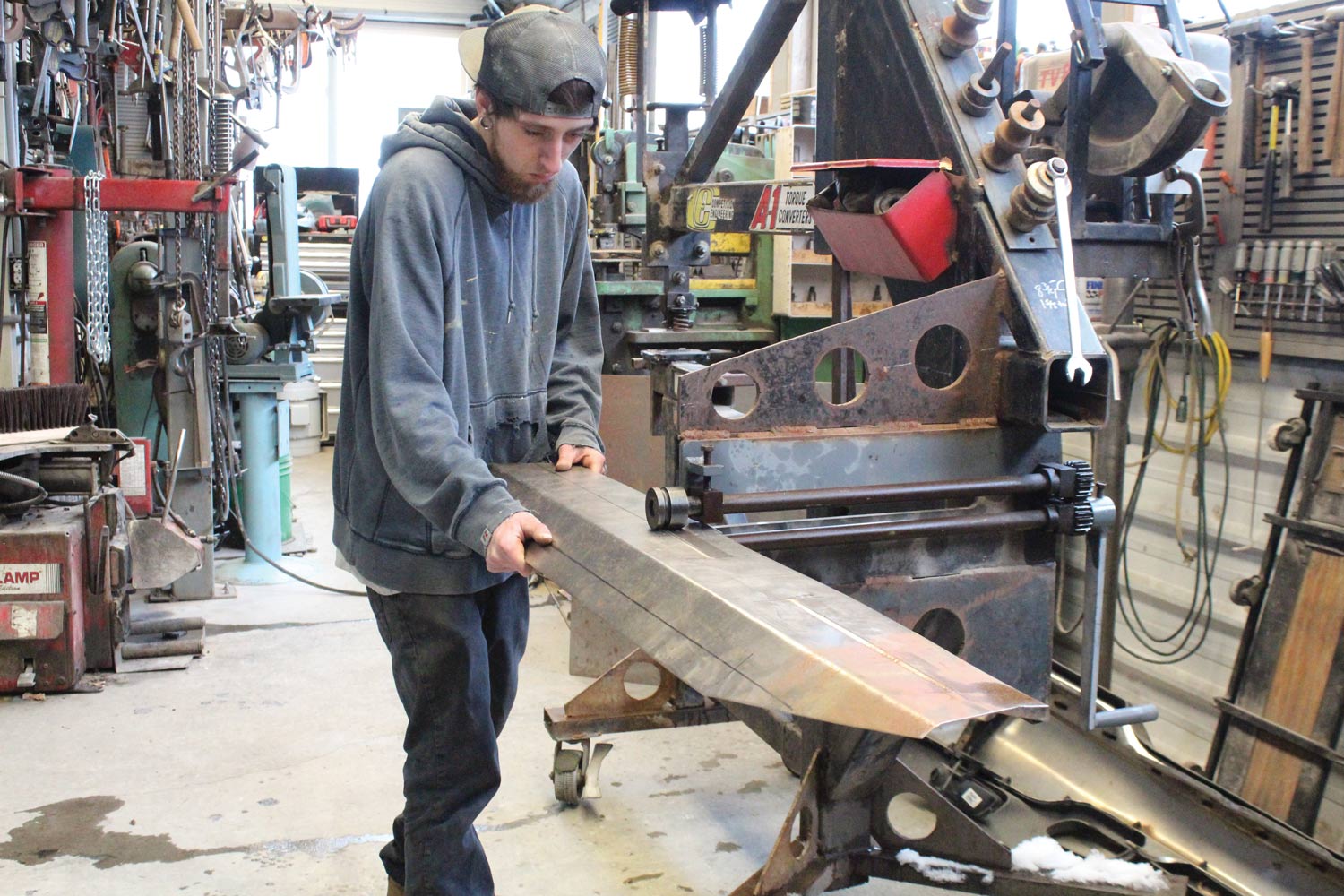
1. Using 18-gauge sheetmetal, Tate Radford fashioned the upper portion of a replacement firewall for Colin and Sue Radford’s ’57 Ford wagon.

e’ve been following along as Colin and Sue Radford’s ’57 Ford Del Rio Ranch Wagon has been undergoing the transformation from a Leave It To Beaver–era grocery-getter to a contemporary hot rod. With the capable, helping hands of grandsons Tate and Caden, the original front suspension was tossed out and replaced with an Art Morrison Enterprises (AME) Bikini Clip. The Y-block was set aside to make room for a Ford Performance Coyote V-8, which brings us to where we are now: making a little bit more room for the replacement powerplant with a new firewall and installing the Flaming River steering components.
With the heater plenum issue resolved, a new flat firewall was fabricated. Thanks to the generous dimensions of the stock Ford transmission tunnel no modifications to the floor above the Gearstar transmission case were required, although new toeboards and the bellhousing tunnel were needed.
Despite the size of the Coyote V-8, routing the steering shaft from the Flaming River tilt column to the rack-and-pinion was a straight shot and would only require two universal joints. To connect those U-joints a conventional, solid, 3/4-inch Flaming River double D shaft could have been used, however, it was decided to incorporate a slip shaft to accommodate any movement between the body-mounted steering column and the chassis-mounted rack-and-pinion. This was accomplished by sliding a section of 1-inch double D tube over a short piece of 3/4-inch double D shaft and welding them together (the weld just keeps them from slipping apart). That section of the steering shaft is attached to the U-joint on the steering column. On the lower end of the assembly a length of solid, 3/4 double D shaft attaches to the steering gear with a U-joint and fits well into the 1-inch double D. The result is a slip shaft that will absorb any movement between the body and frame and can’t come apart.
To mount the steering column at the bottom a Flaming River “blank slate” swivel mount (PN FR20101BLS) was used (this universal floor mount is designed to be used in a street rod build that will include a new firewall). At the upper end a Flaming River factory-style 2-inch dash mount (PN FR20114PL) was modified to fit the stock Ford dash bracket. For rigidity, a support that ties the steering column, brake pedal, and master cylinder/booster assembly was fabricated from flat stock and tubing.
Building the ’57 Ford Del Rio has been a real family affair for the Radfords, which is fitting considering station wagons were once the ultimate utilitarian family vehicle. Who knows, cool as this one is turning out they may be again.
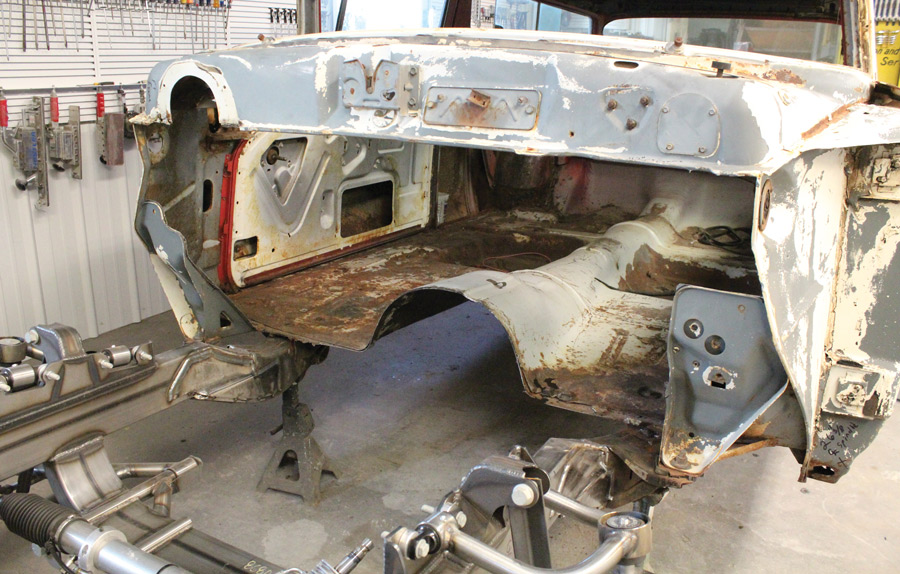
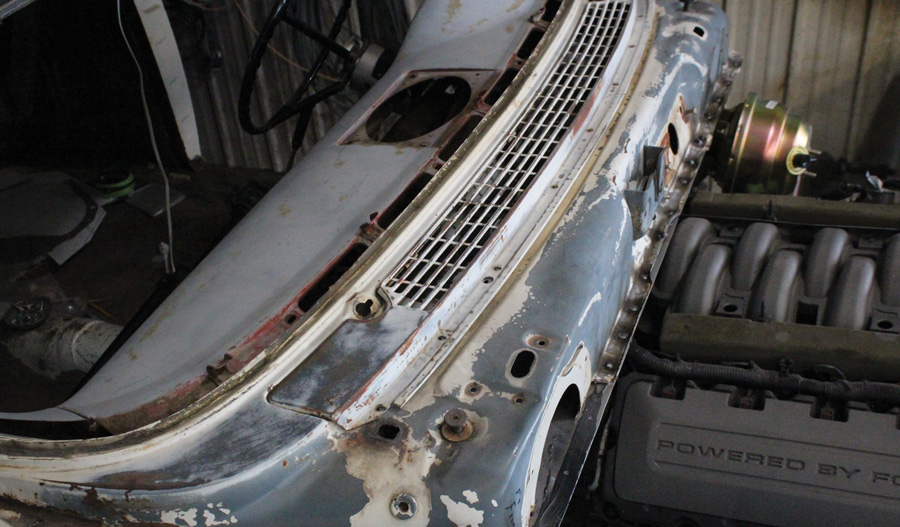
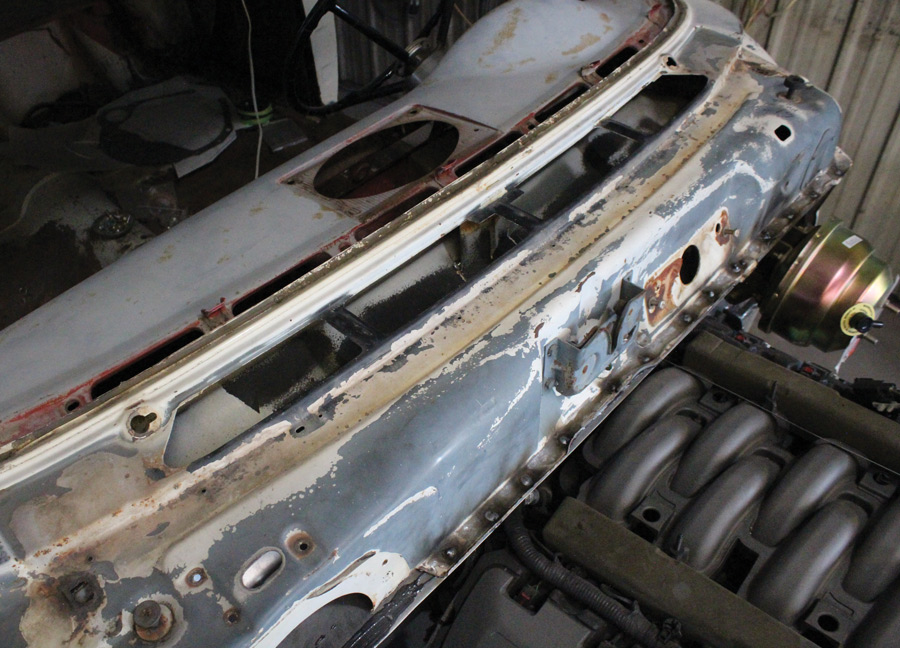
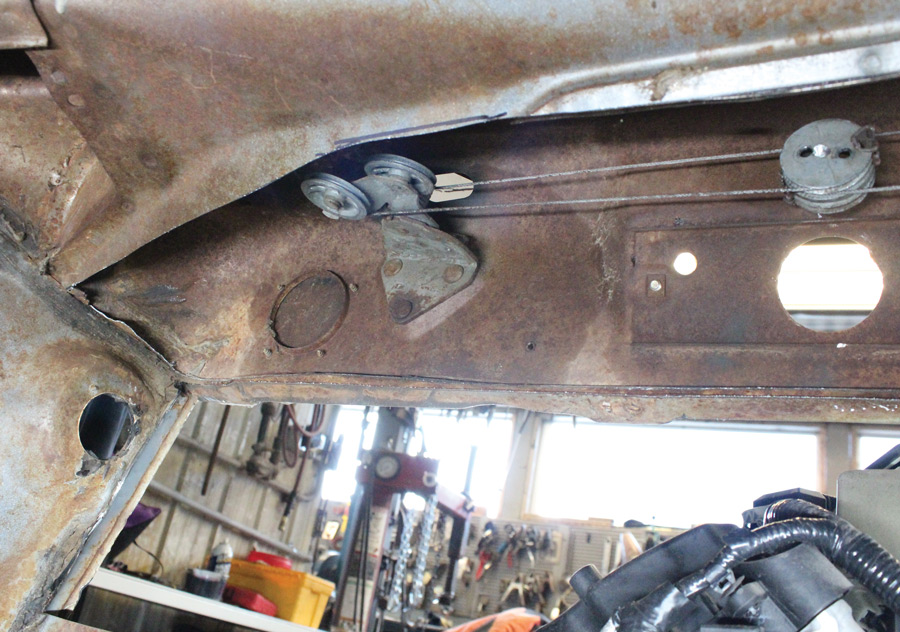
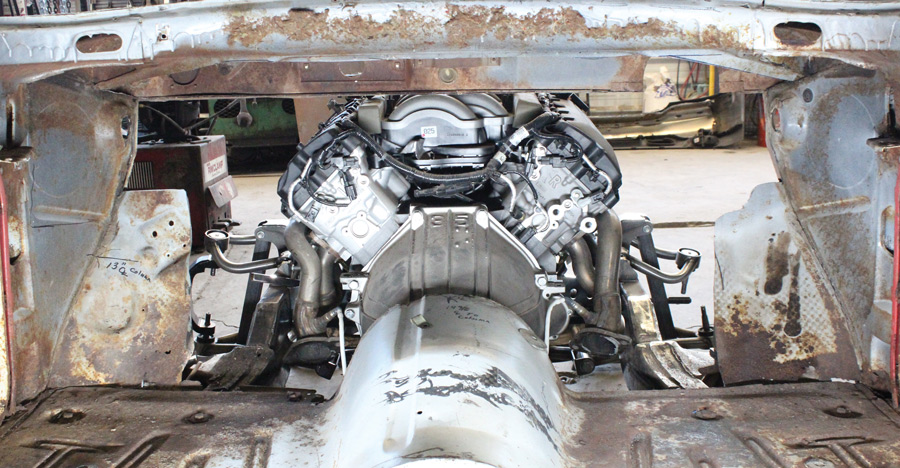
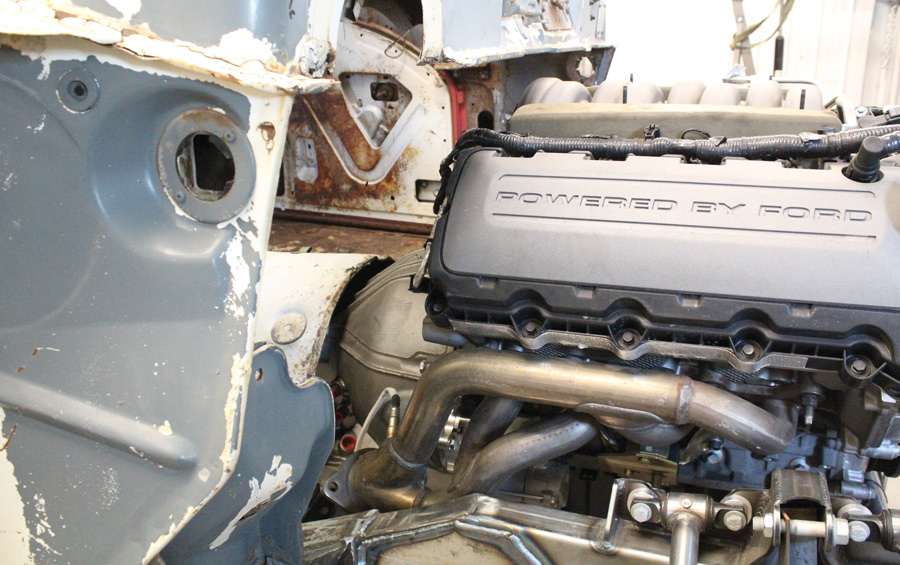
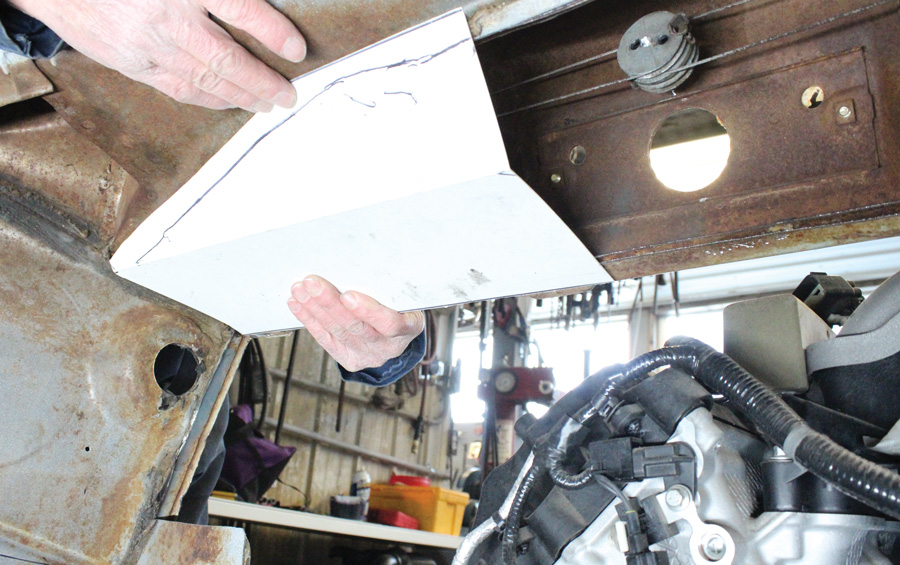
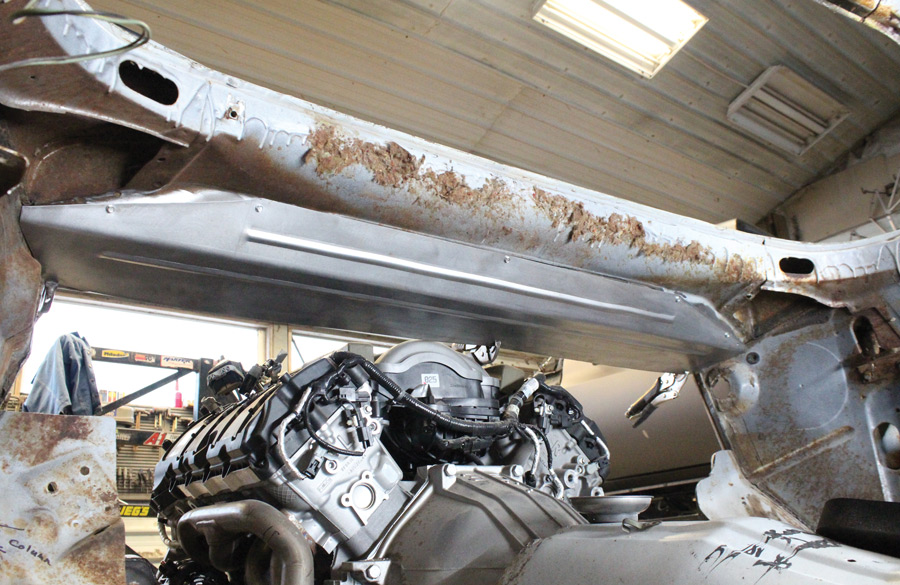
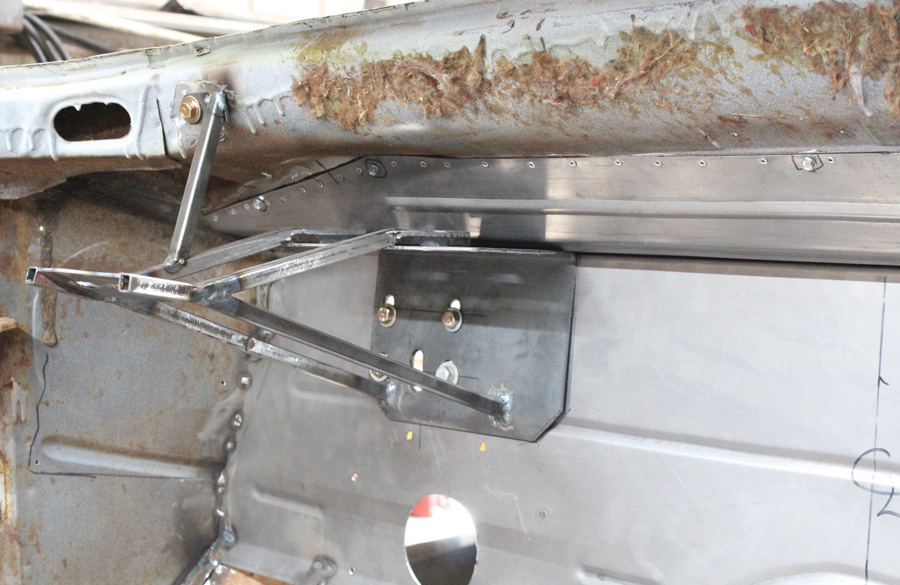
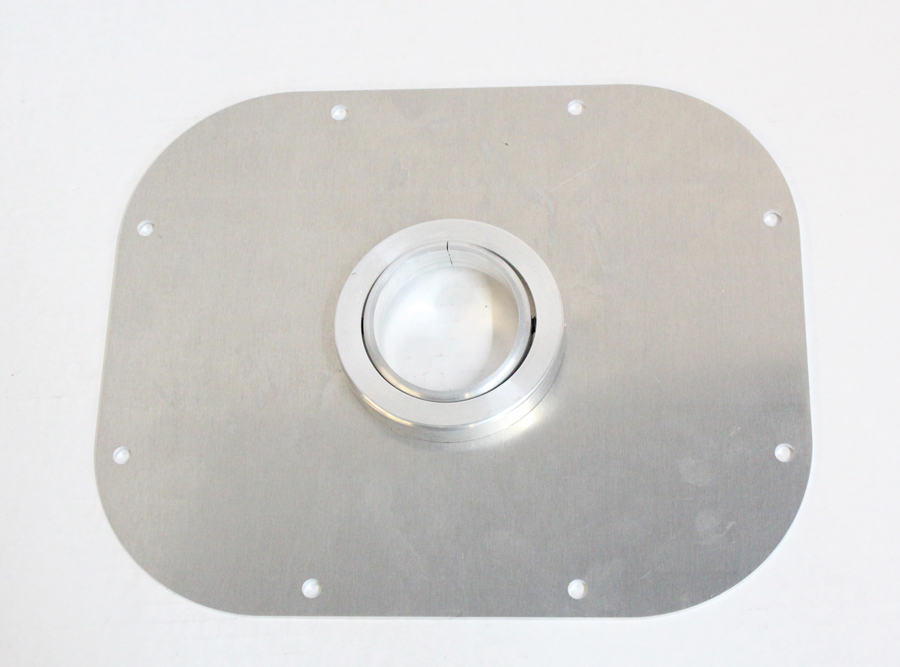
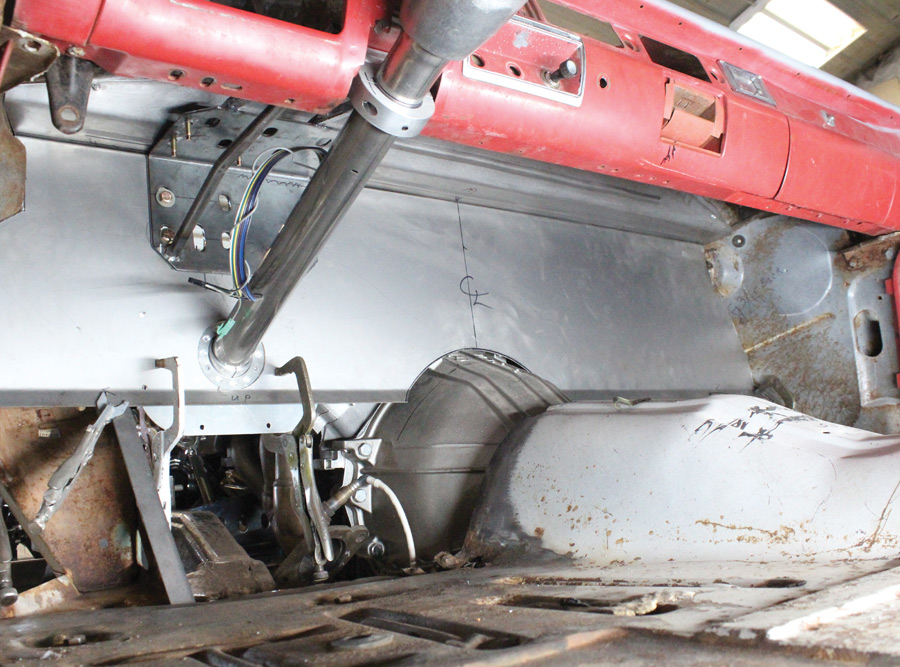
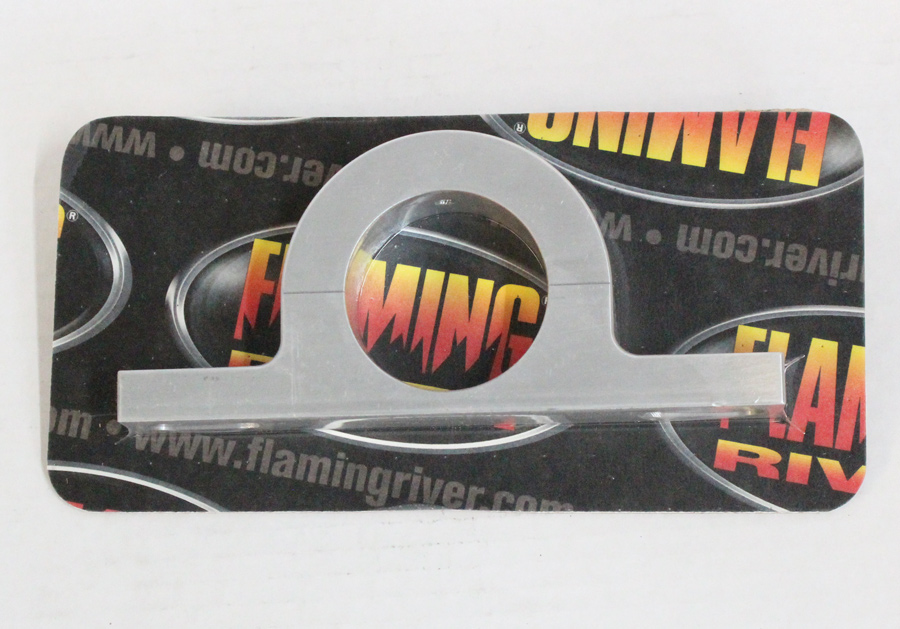
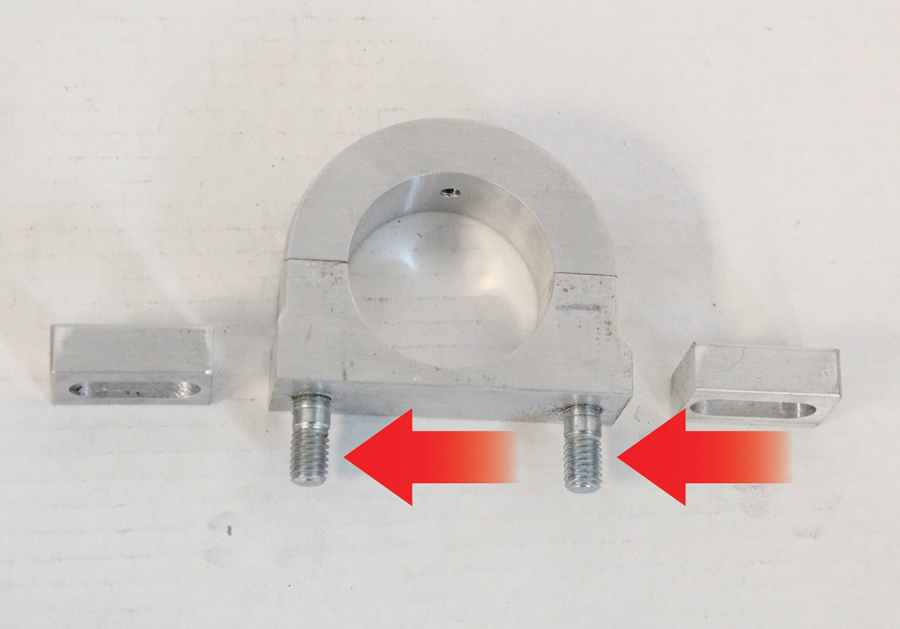
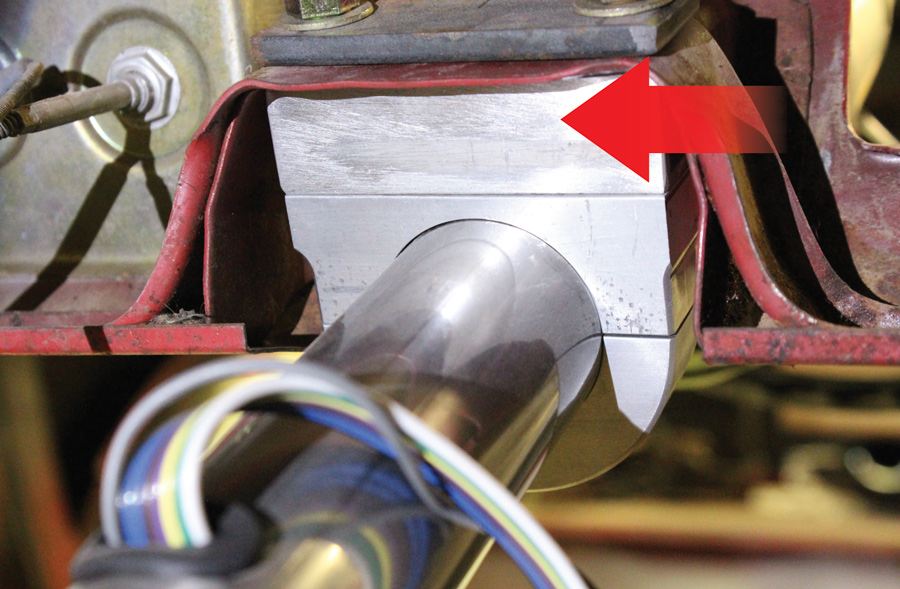
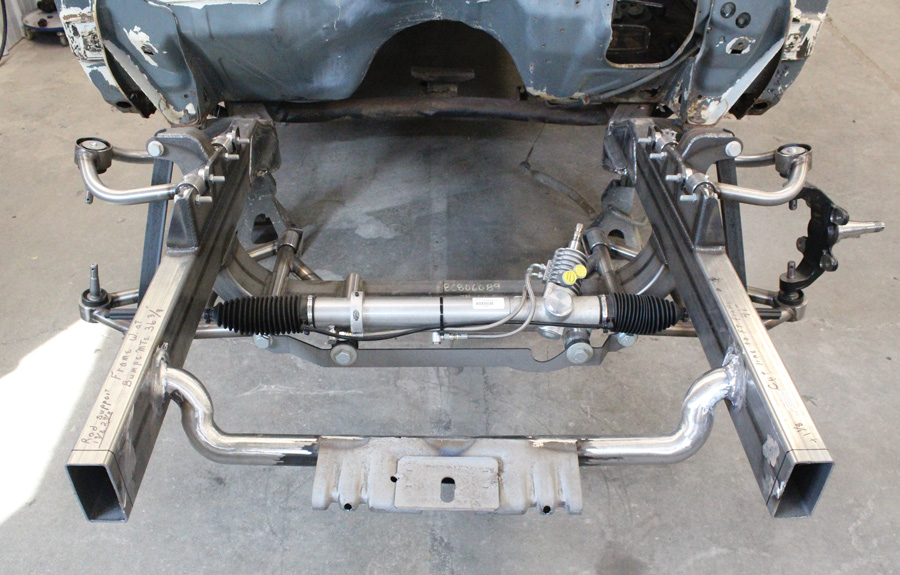
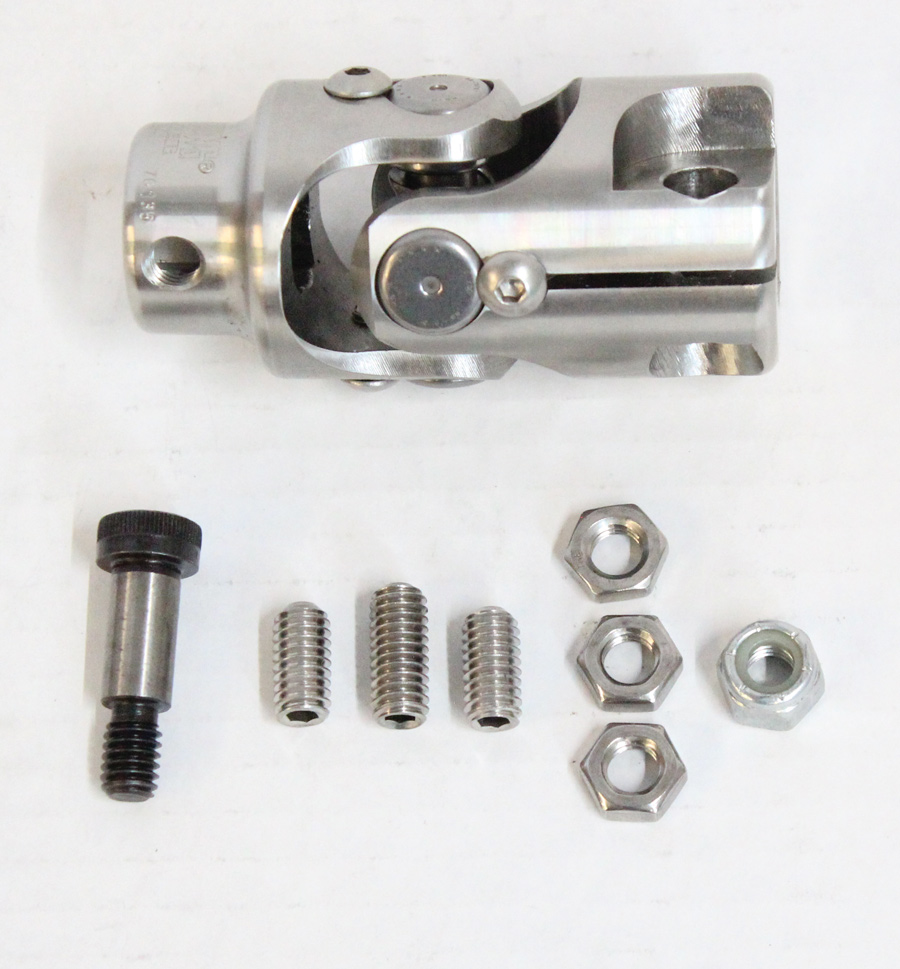
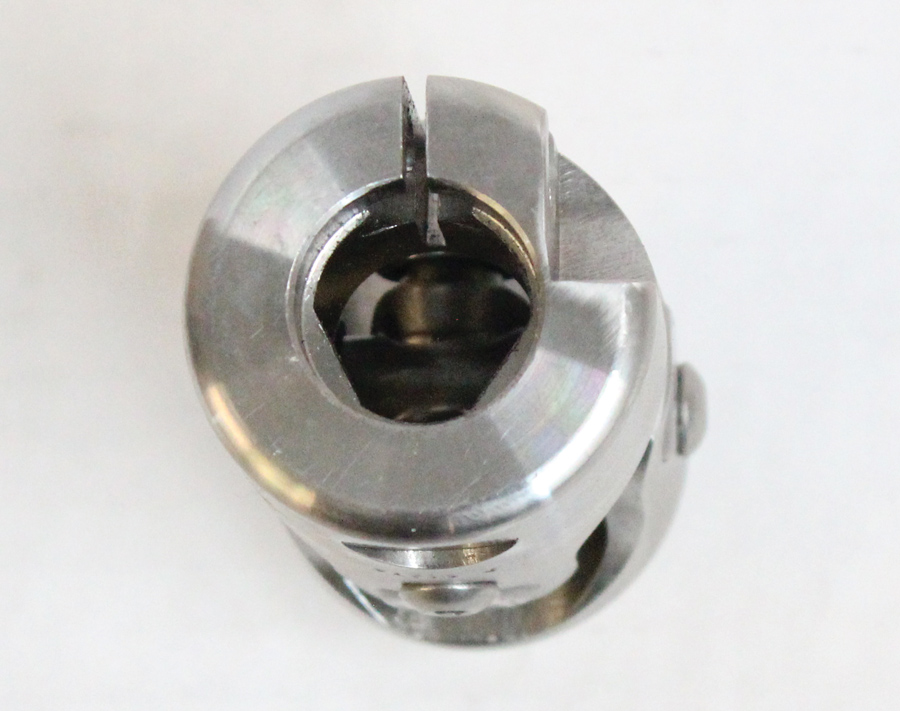
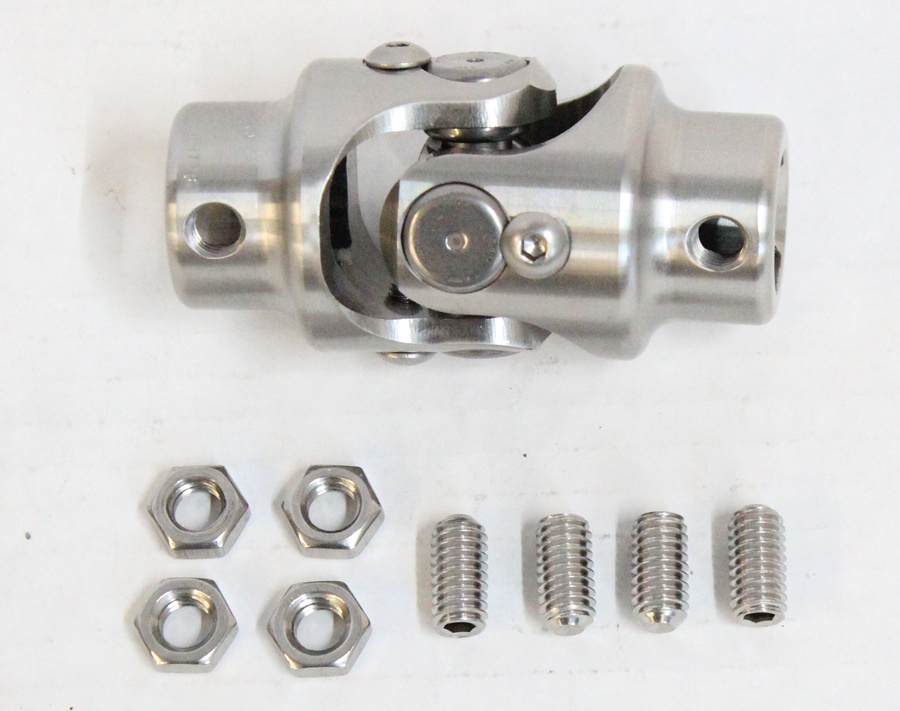
(PN 2517 DD).
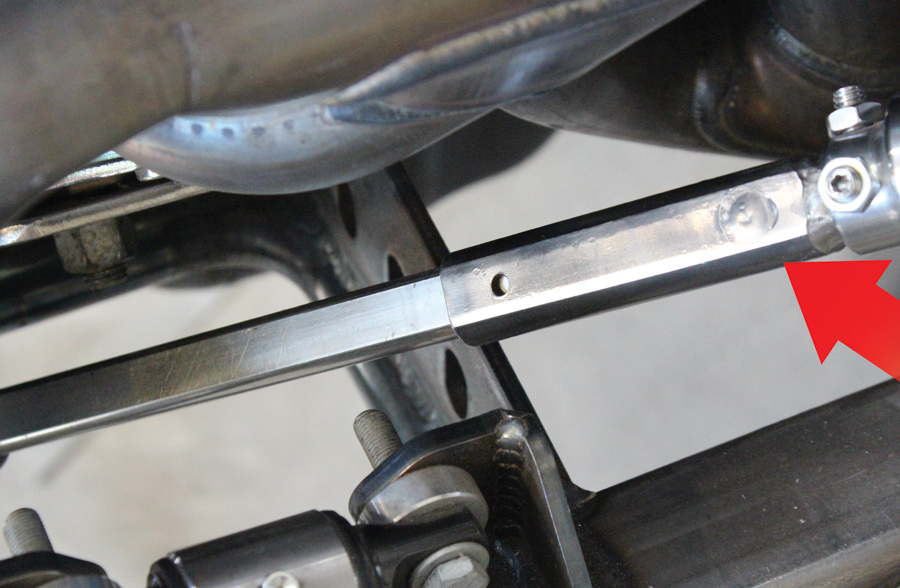
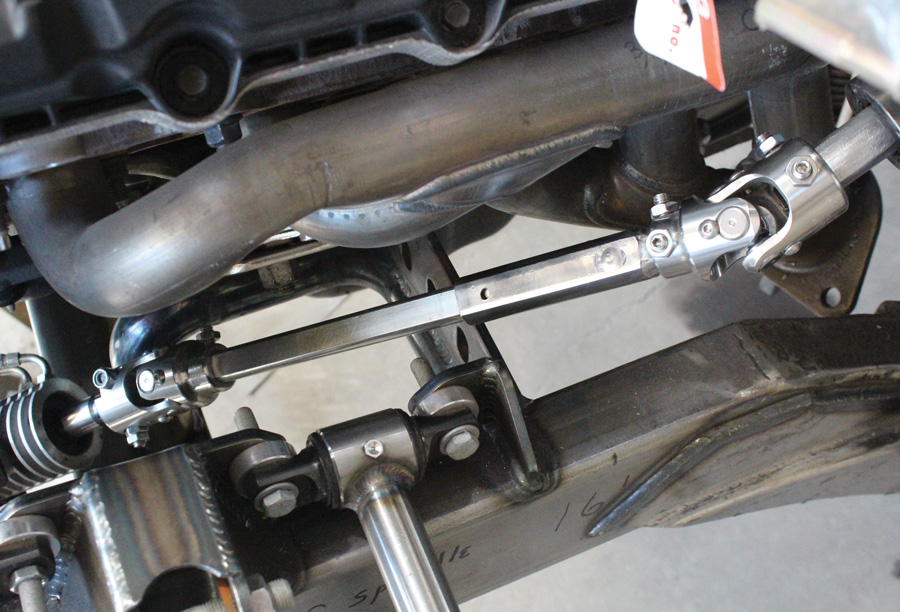
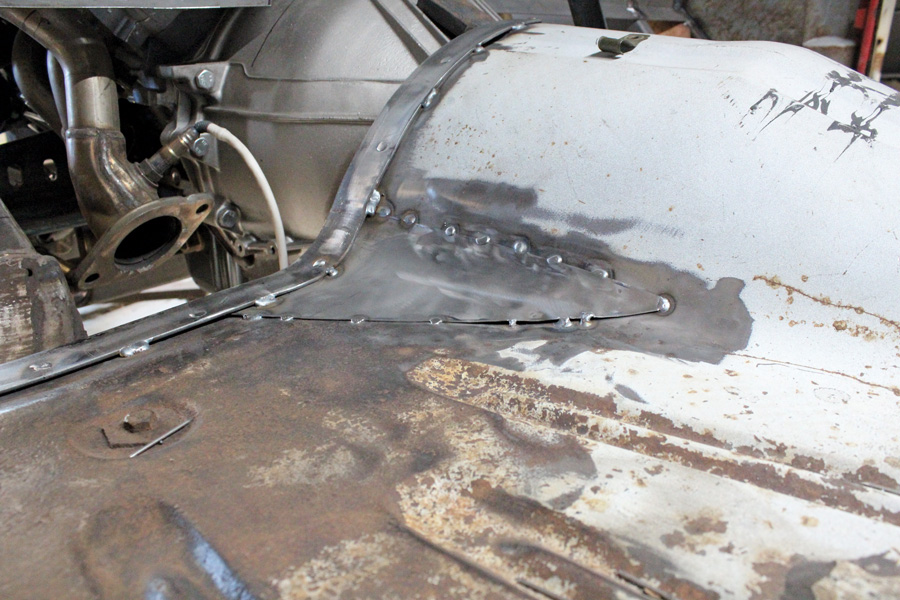
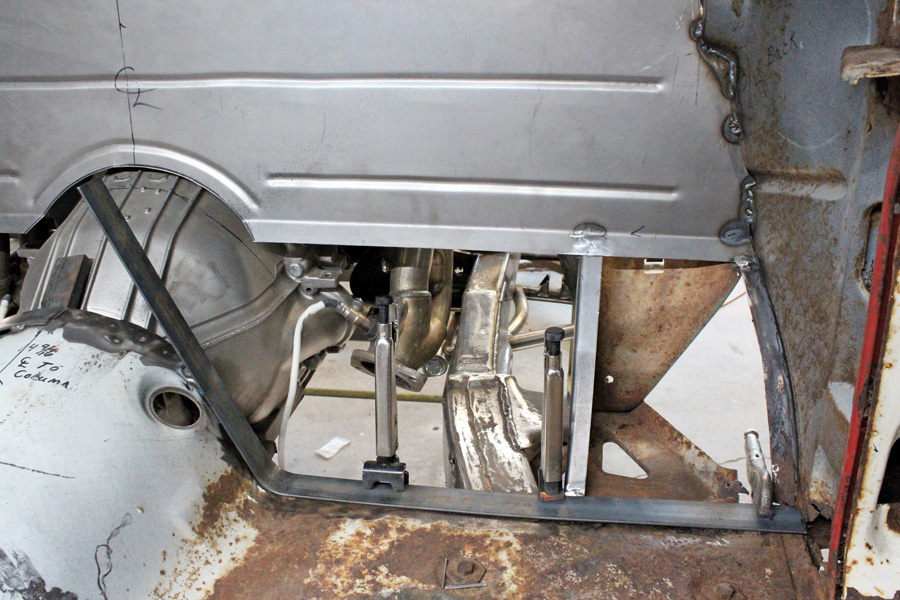
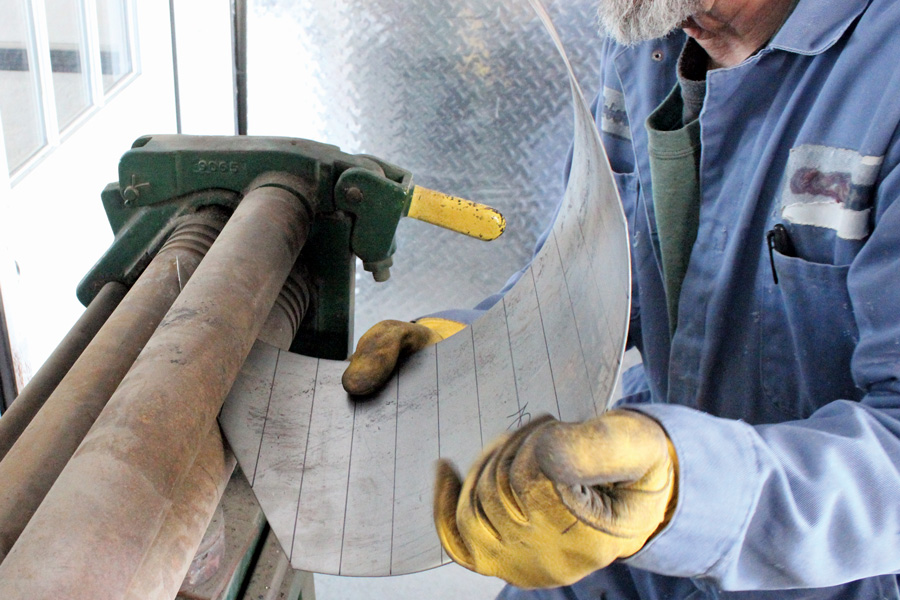
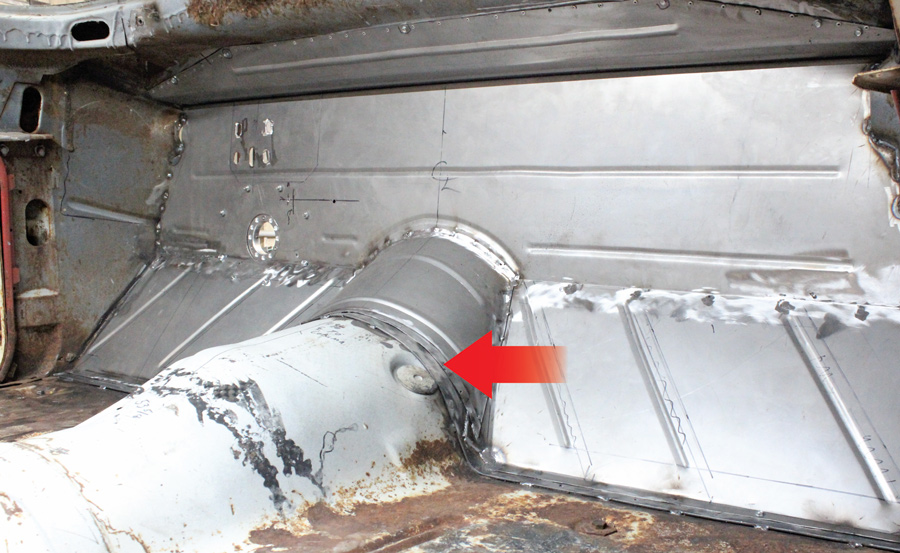
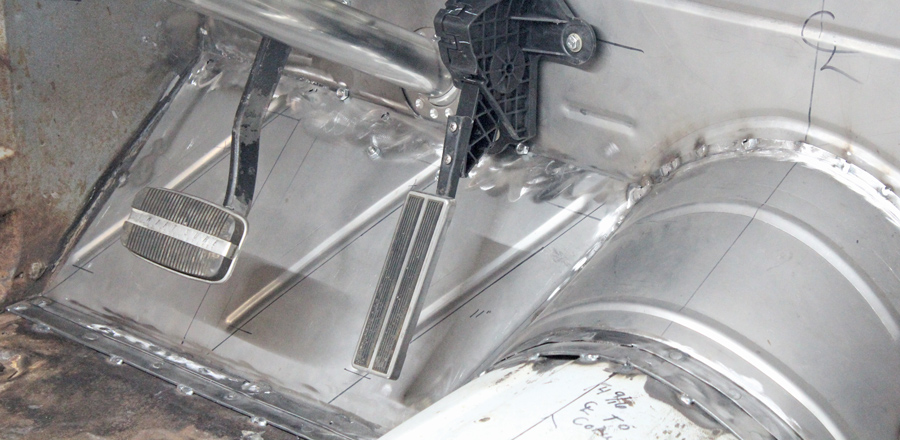

(208) 745-1350