Modern Rodding TECH
InTheGarageMedia.com
By Gerry Burger Photography by Art Fortin
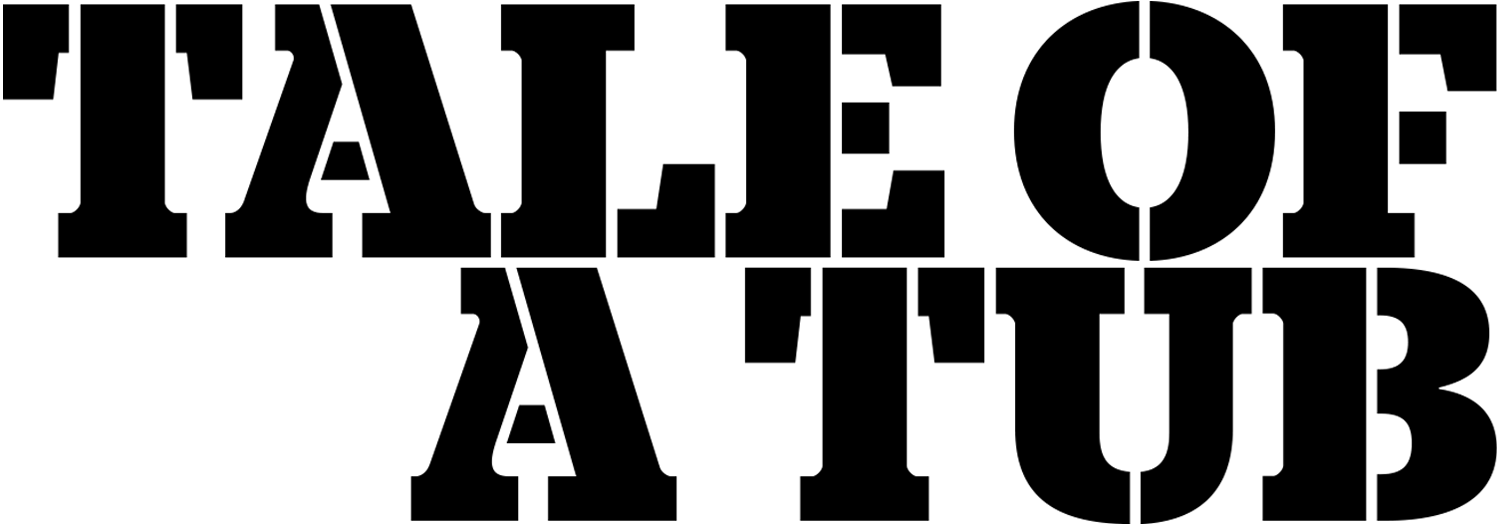
hen Art Fortin decided he had “one last build” he knew he wanted something traditional yet different, so he settled on a Model A DeLuxe phaeton. The DeLuxe phaeton is the Tudor model, while the standard phaetons are all Fordor models. Now, we all know deciding on the body you want and locating that body can be challenging. The ’30-31 DeLuxe phaeton is relatively rare by Ford standards, so much so Fortin had resigned himself to using an old Gibbons glass body he bought at a swap meet with plans to possibly use it as a template for new steel panels. When a steel body presented itself the fiberglass body was sold.
It was during a bench racing session at the 2010 Goodguys Pleasanton event that a fellow rodder mentioned he knew of a genuine steel body, but it was located in New York. Phone calls were made and there was an agreed price, but now the challenge was how to get the body home from the East Coast. The owner said the body could be brought to the huge Hershey Swap Meet for delivery. As fate would have it, Fortin is friends with Bill Perry, owner of All Ford Parts and they go to Hershey every year hunting for great vintage parts. They rent a huge van and several people rent space on the van to get their parts home. Bill was looking for a driver, and Fortin and his pal Ben Barnhart jumped at the opportunity to drive coast to coast, take in a great swap meet, and pick up the ’31 Model A tub in the process.
In our last issue (Apr. ’22) of Modern Rodding we showed the chassis construction, a beautifully homebuilt frame based on a set of original ’32 framerails. The entire build is themed on the ’58-60 time period and the gutted body was the perfect start for this highboy project. Well, maybe perfect isn’t exactly correct. The body was showing rust in the wheelwells and other lower extremities, there was no floor, but it had a very nice firewall. Yes, it was a bit rough around the edges, but it was a great start.
Like the chassis, the bodywork would be completed in Fortin’s home shop. Work began at the rear of the body as it was imperative that the wheelwells were centered on the rear wheels. Fortin took a unique approach to the body, assembling it in three independent pieces, beginning with a newly fabricated floor in the rear portion of the body from the B-pillar back. The doors determined the distance between the rear portion of the body and the cowl section and a new floor section was fabricated to the proper door opening. The cowl section had a new floor fabricated to fit the contours of the ’32 chassis. The original Model A uses wood headers to connect the front and rear body sections and while new wood was included with the body, those headers would not work on the Deuce frame, so Fortin decided on the three-piece approach with steel connecting headers rather than wood. This also allowed him to perfectly gap the doors.
The rust repair involved replacing one wheelwell and fabricating a new doorskin for the passenger side door. Other lesser rust was repaired around the lower extremities of the body. The center of the rear section now has a nice cutout formed to expose the vintage Halibrand quick-change rear. A pair of recessed ’46 Ford taillights are found on either side of frenched license plate. A mild recess was formed in the firewall for distributor clearance and the entire body was braced with box tubing. It was decided early on to eliminate the rear seat in the car and use that space as storage. It would also locate the gas tank and the battery, and it is all covered with a very cool hard tonneau cover. The original Model A gas tank was cut out and the front panel is now the basis for the custom dashboard.
The doors and the hinge pillars are still framed in wood to facilitate the original hinges and latches. A ’32 Ford windshield is laid back and while Fortin found the Deuce windshield fit better than a Model A in the laid-back configuration, it also required a set of custom-fabricated windshield posts that Fortin mentioned “was a ton of work.”
When all the fabrication was complete routine bodywork followed with the custom-mixed maroon paint being laid down by Henry Rossi, and while there are many more details, we’ll save that for the final feature story, for now let’s dig into how to rescue a 91-year-old body in a home shop.
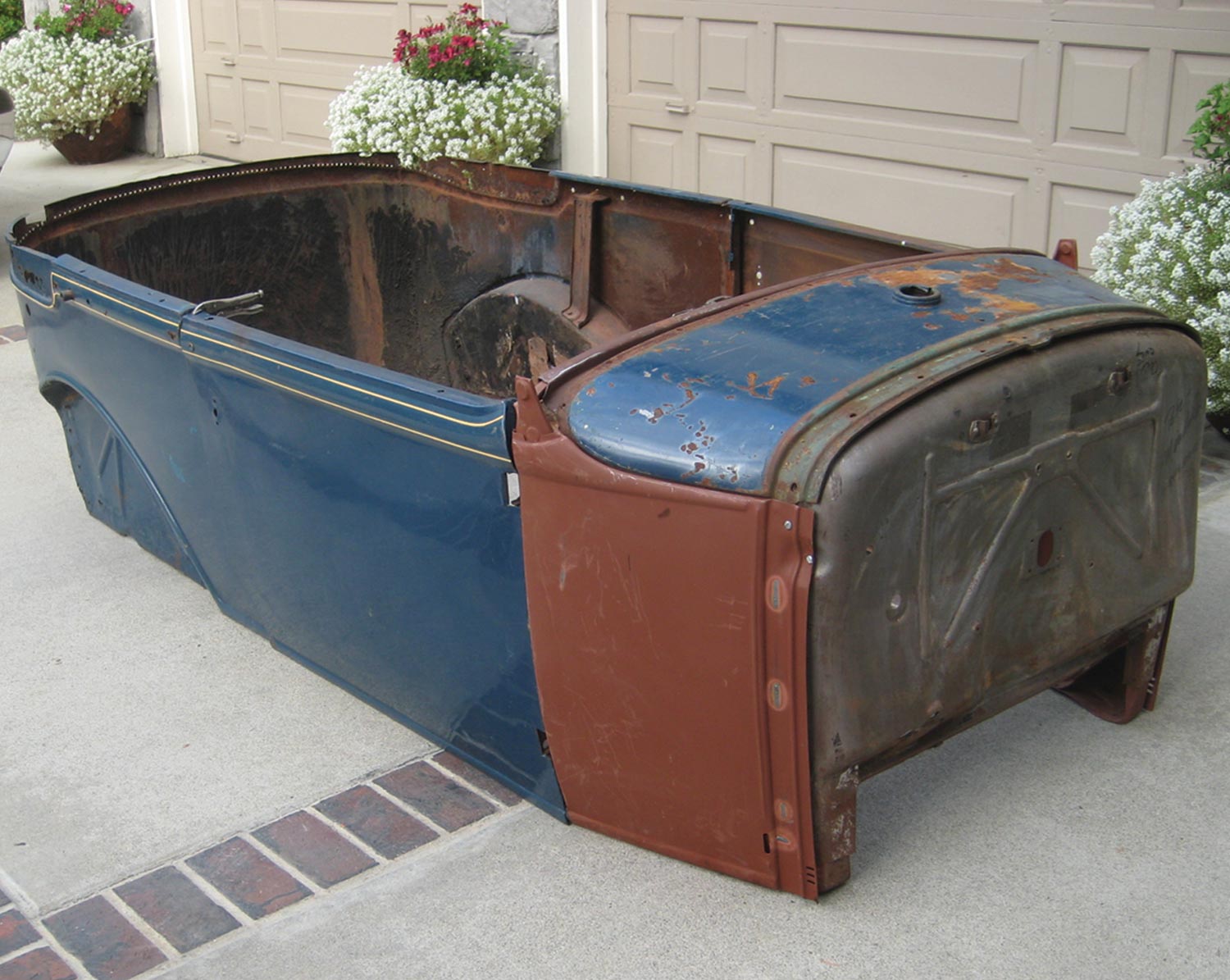
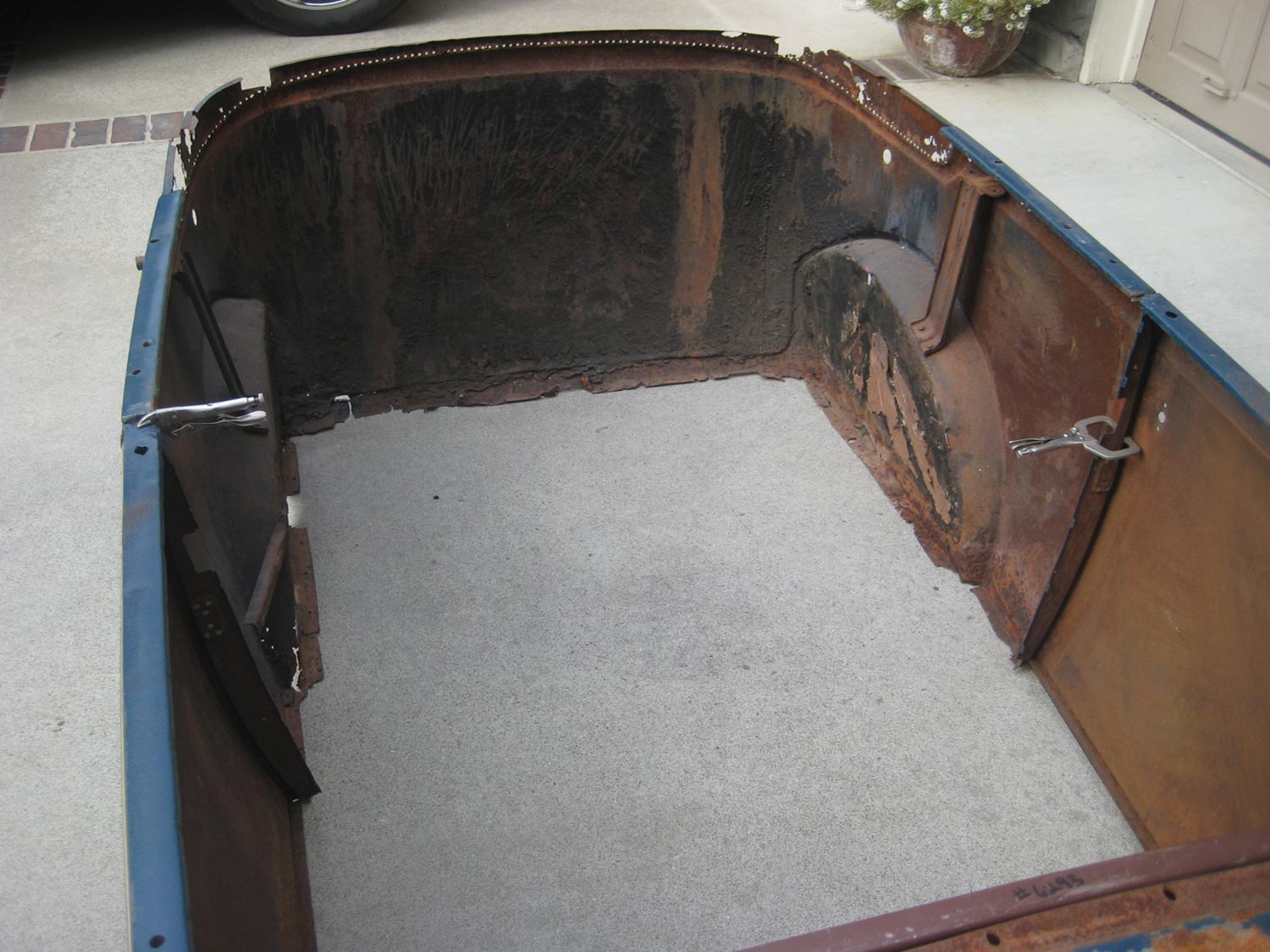
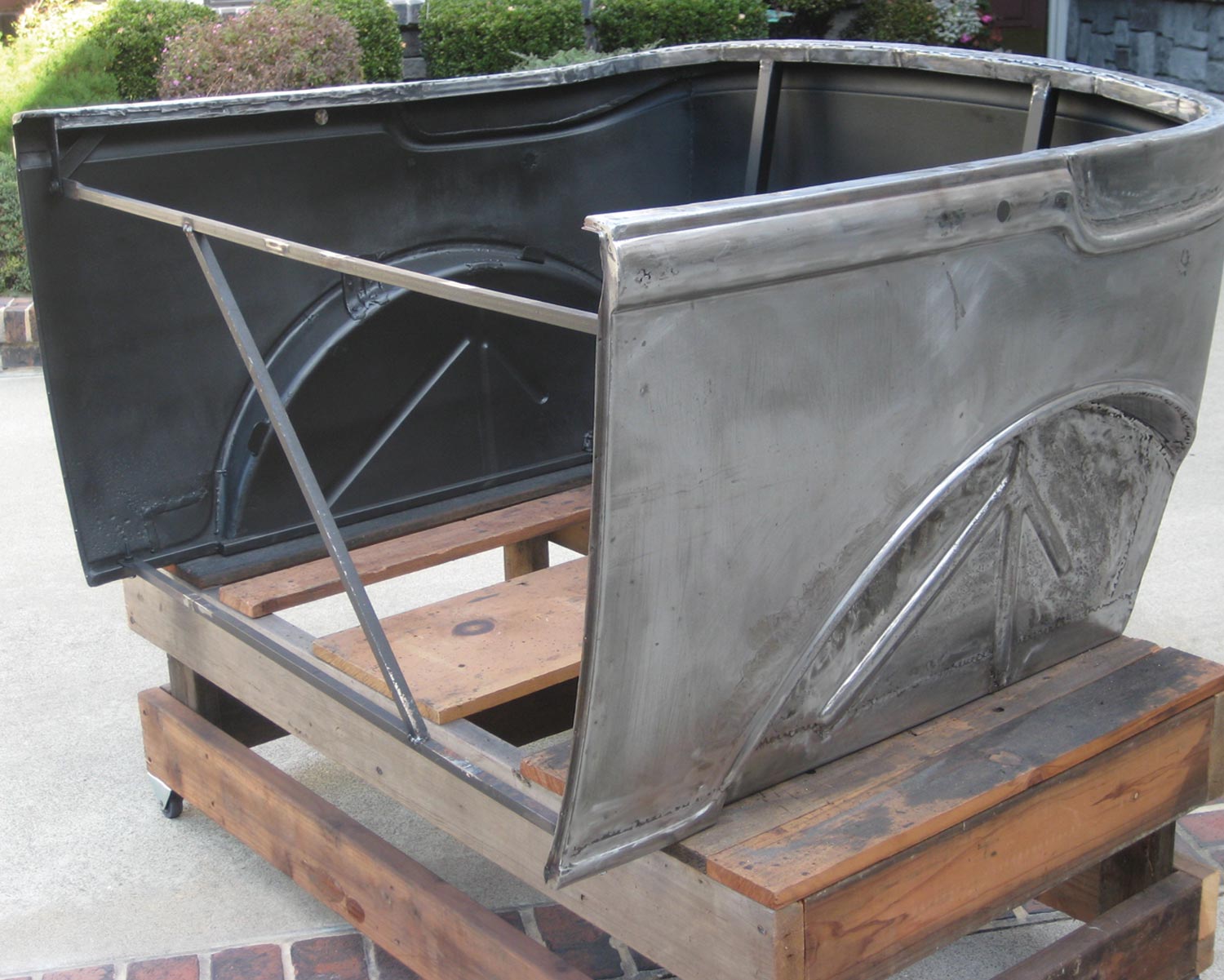
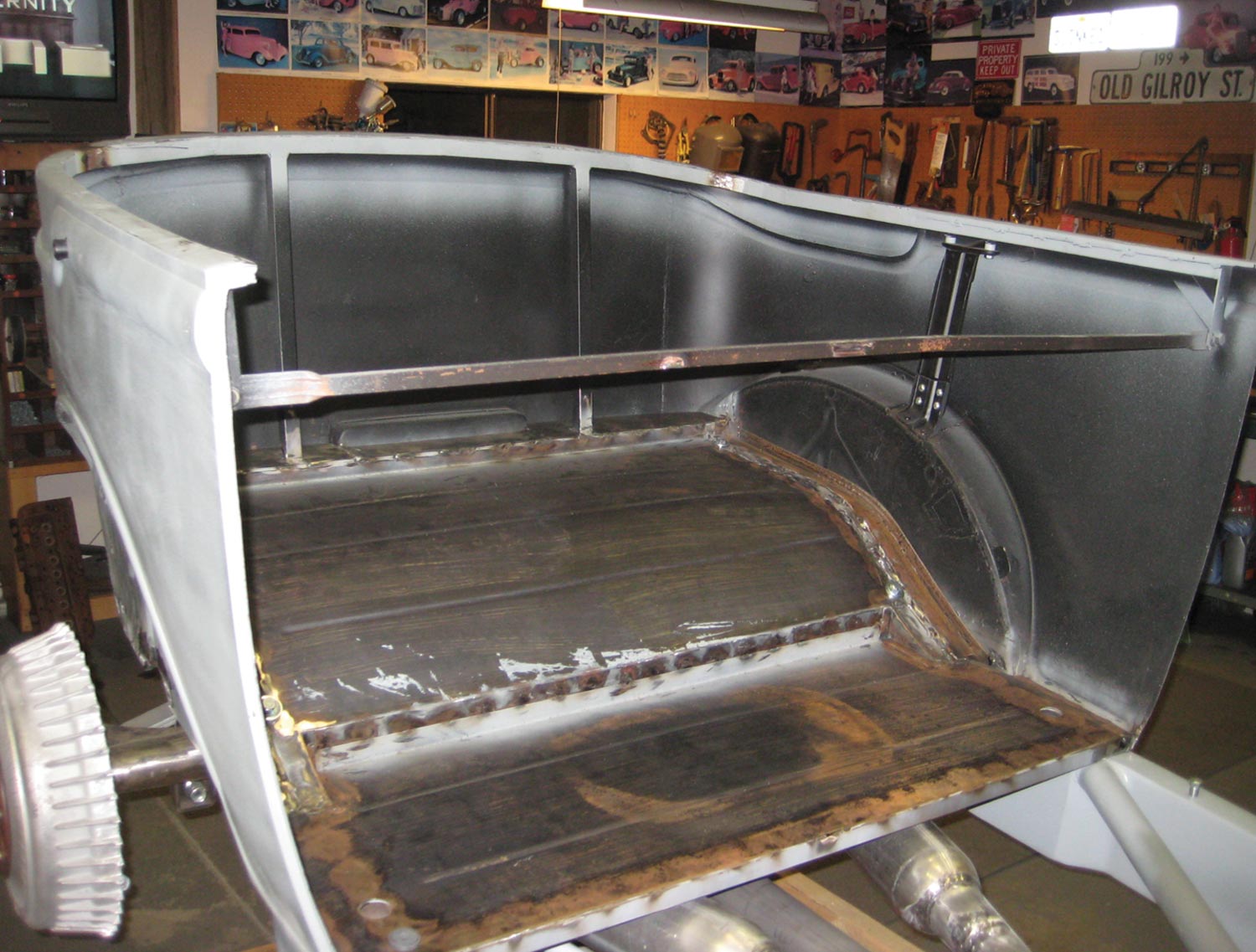
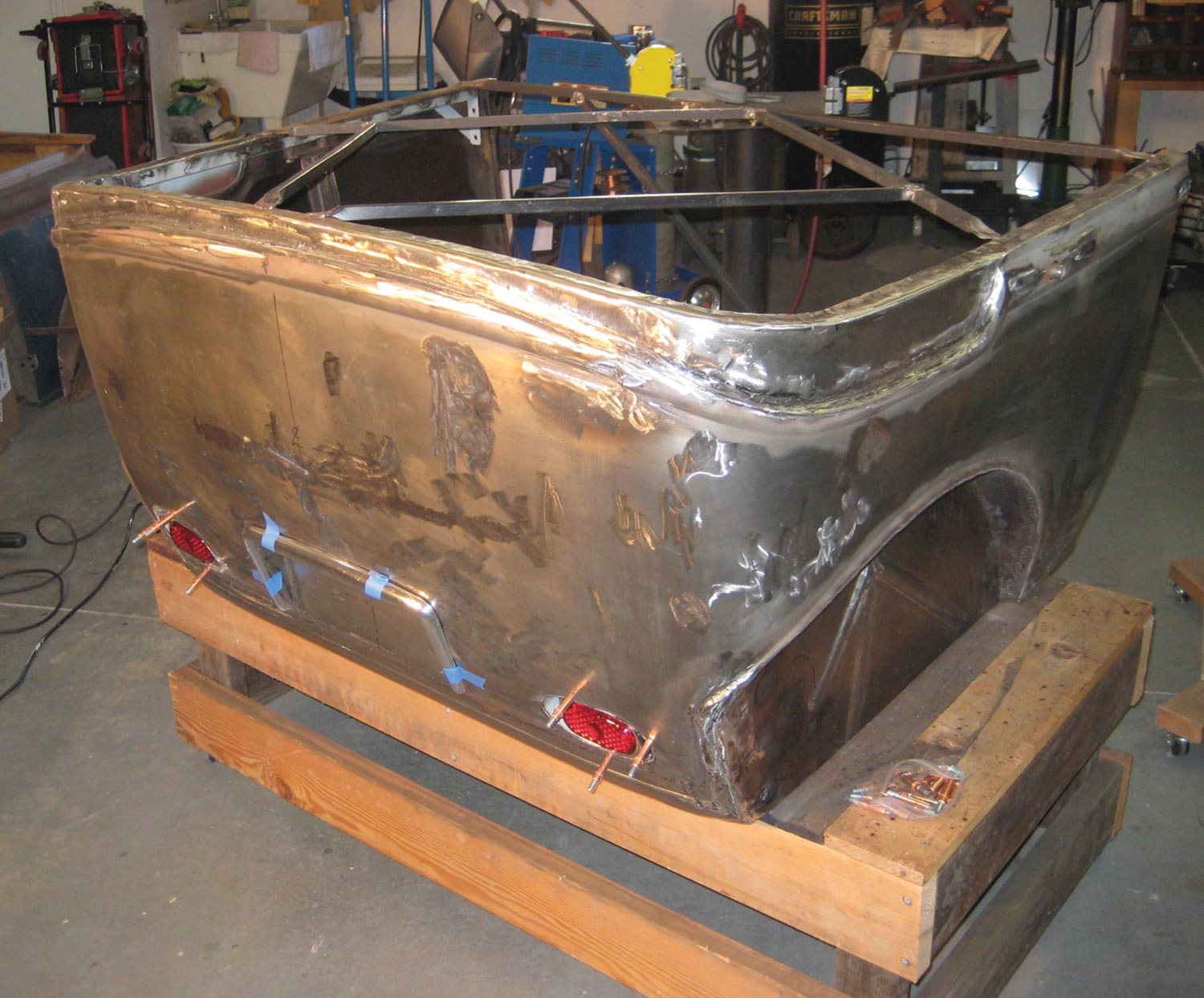
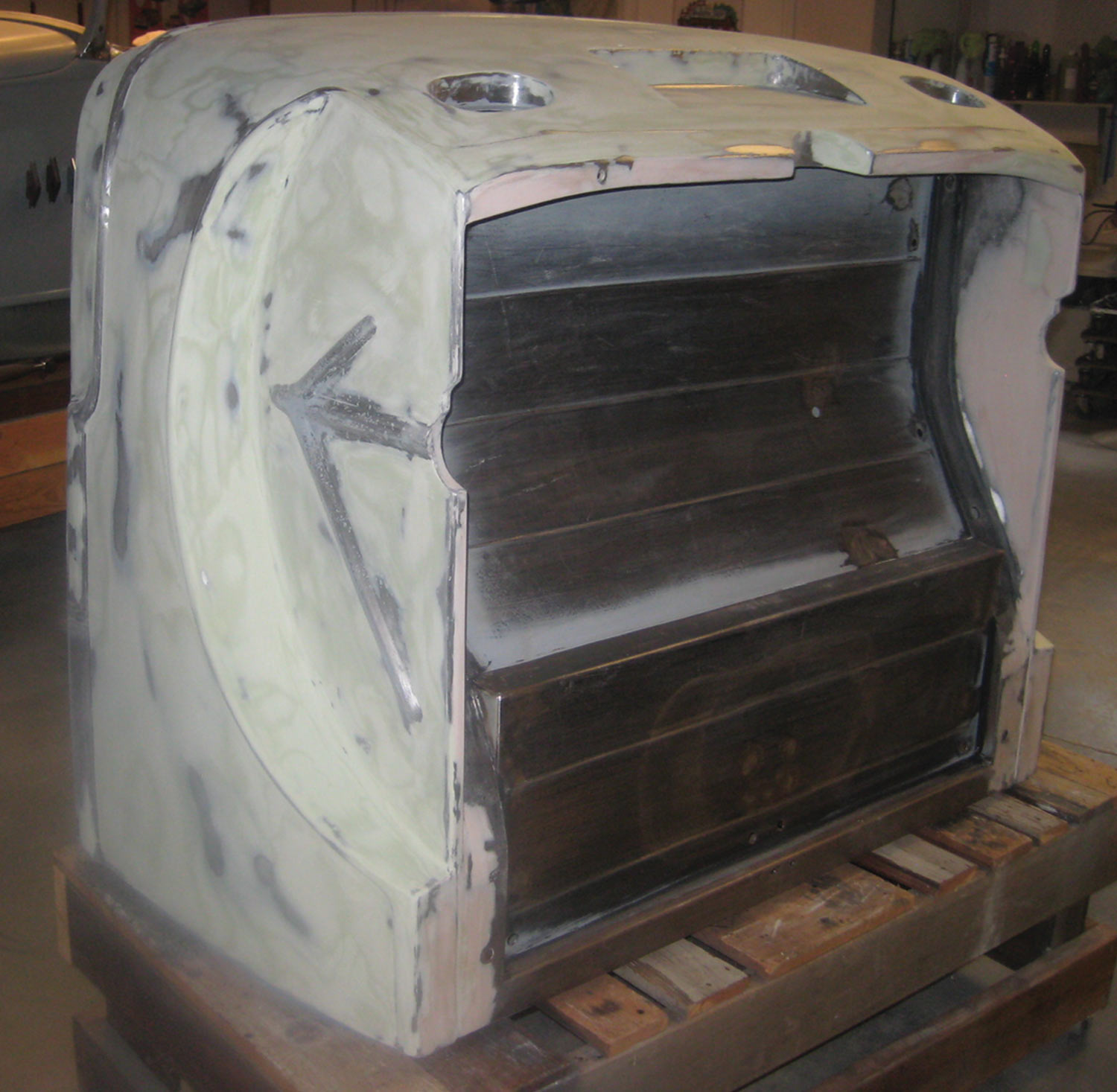
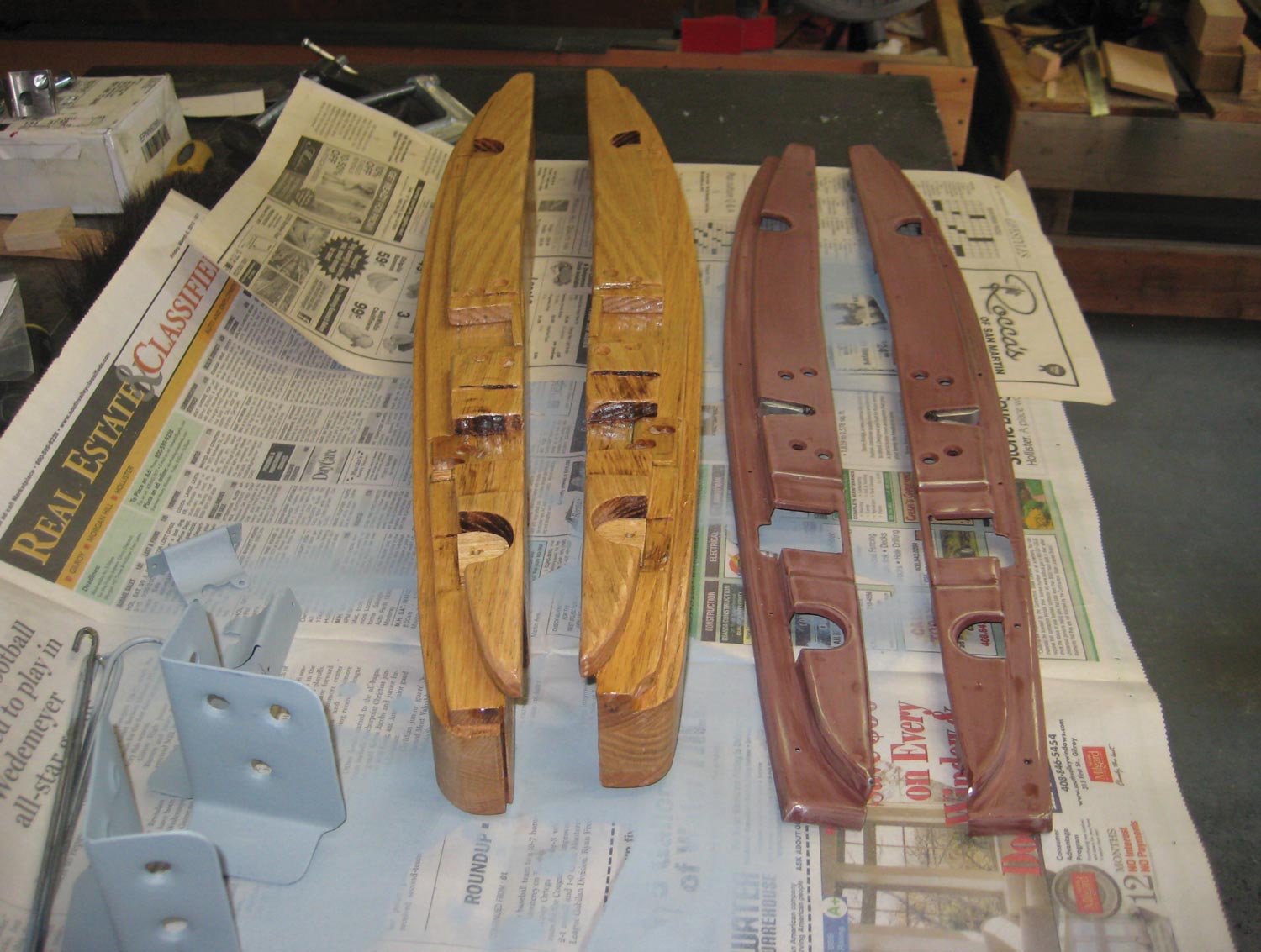

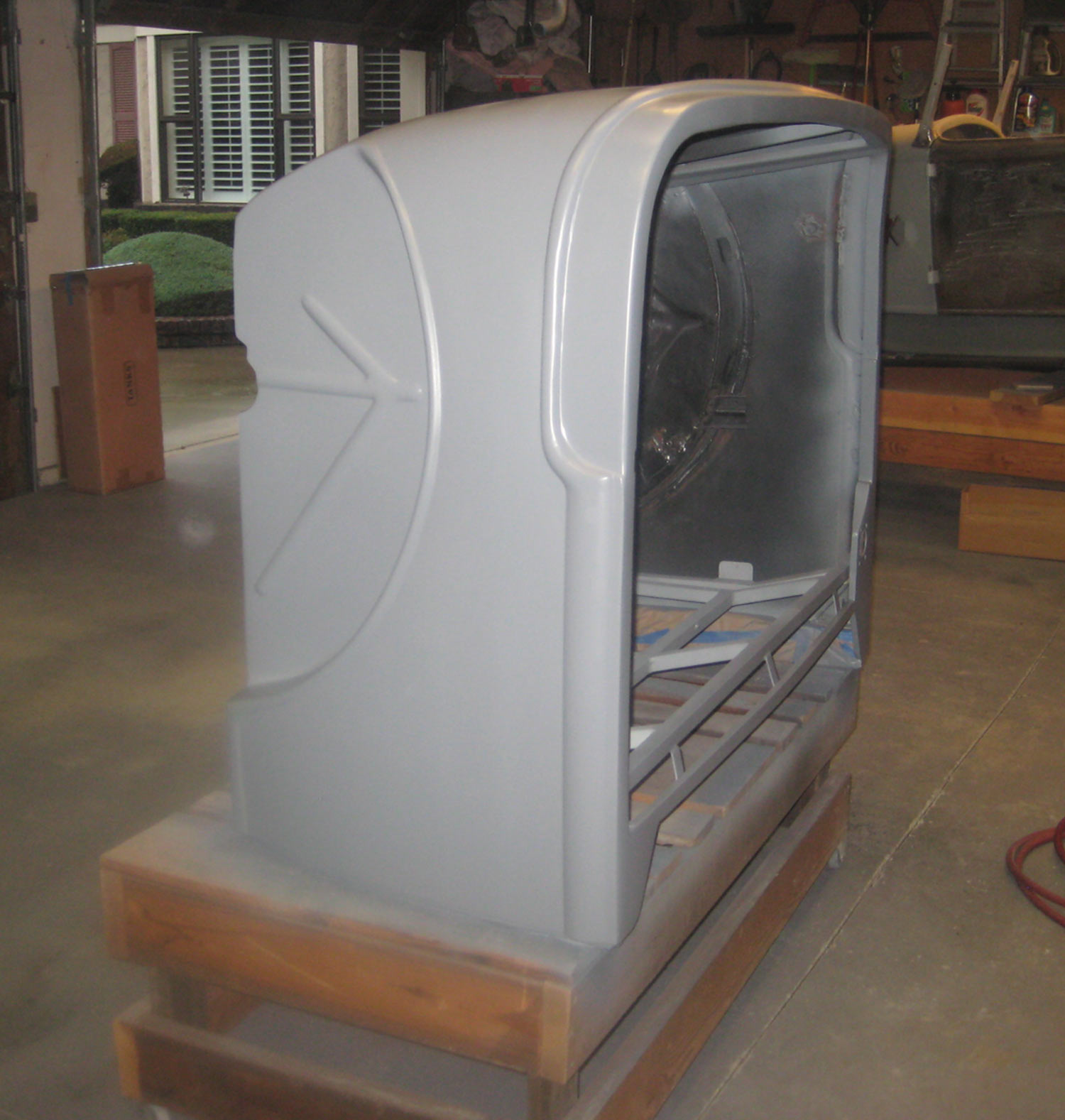
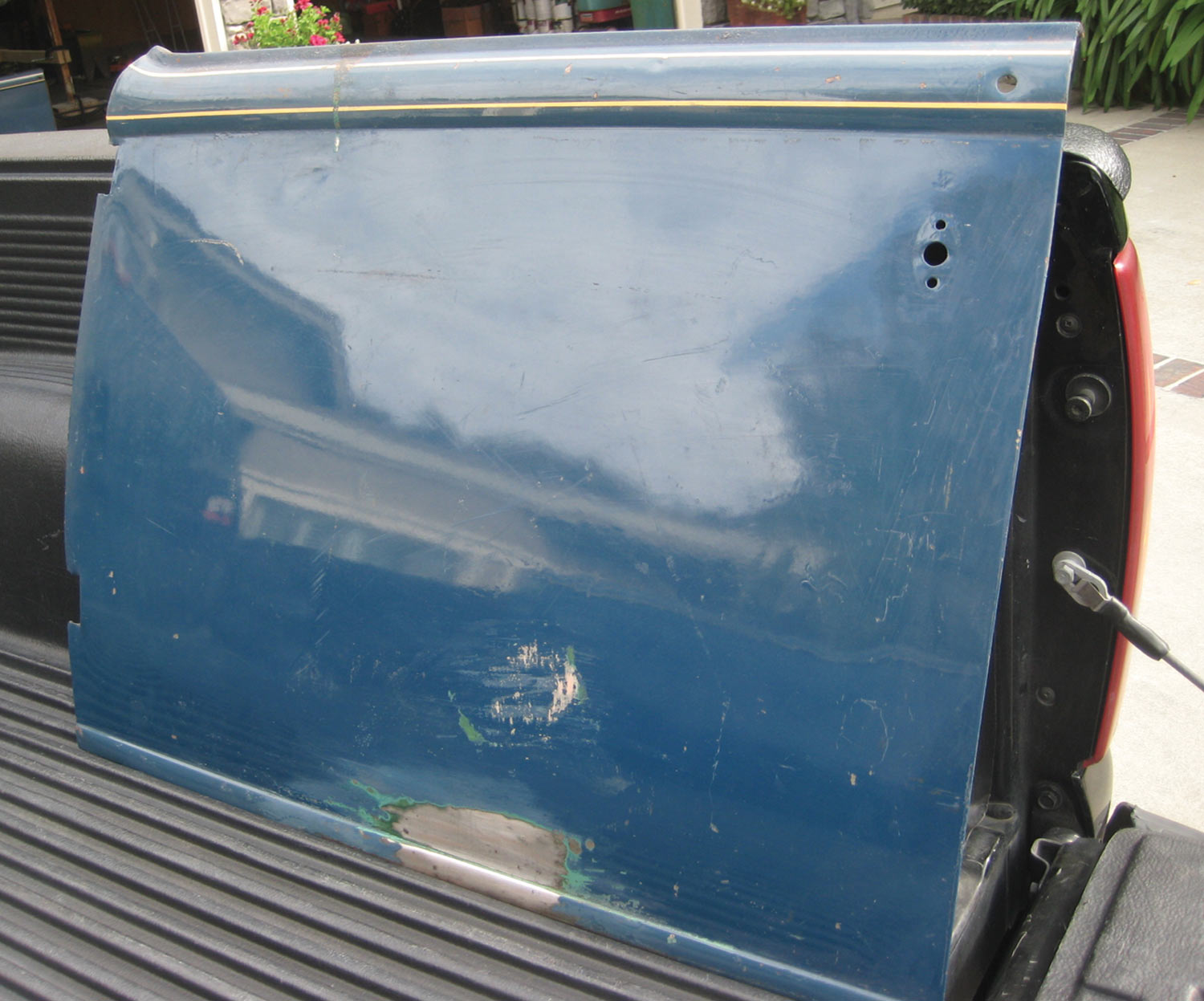
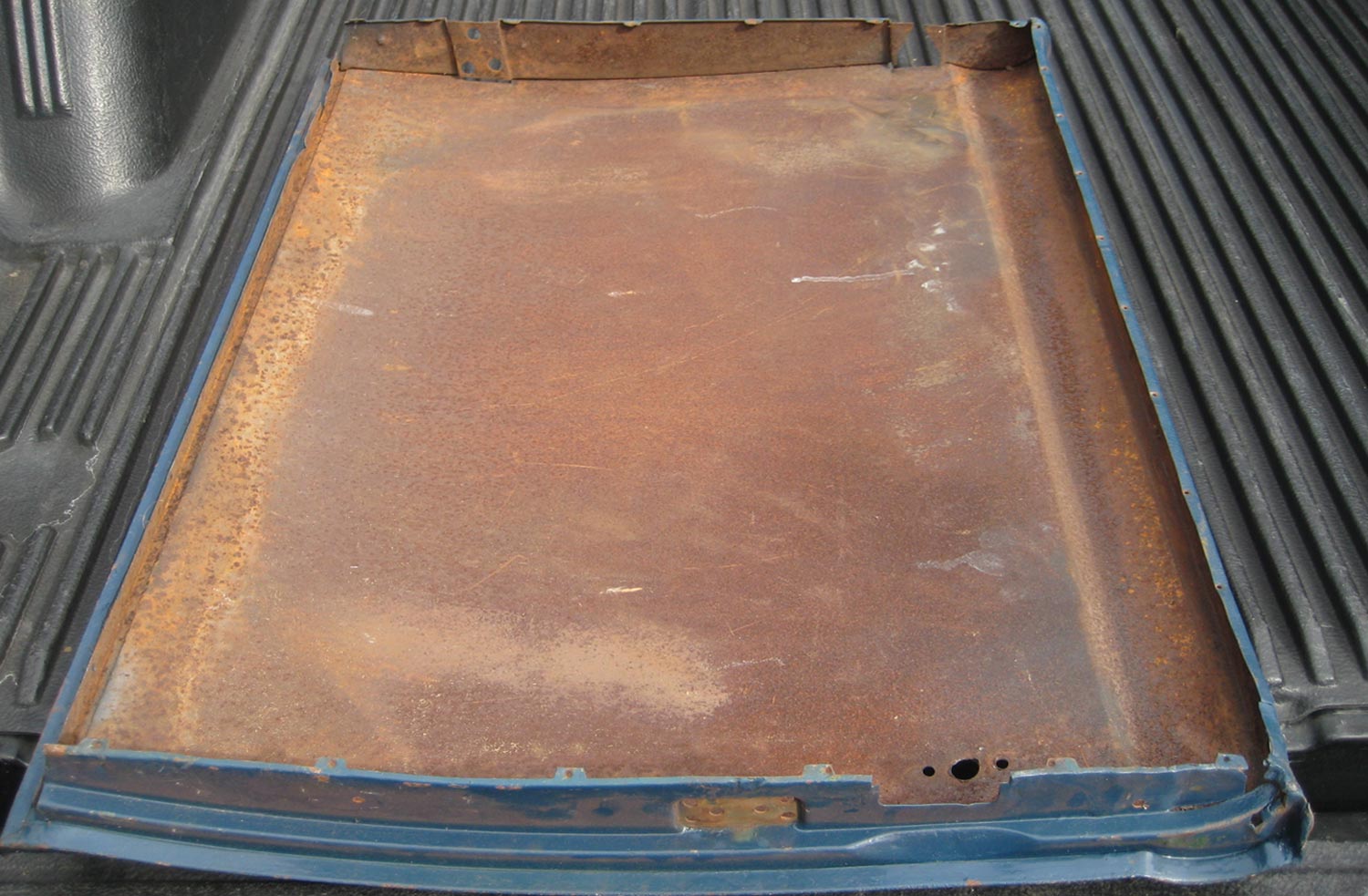
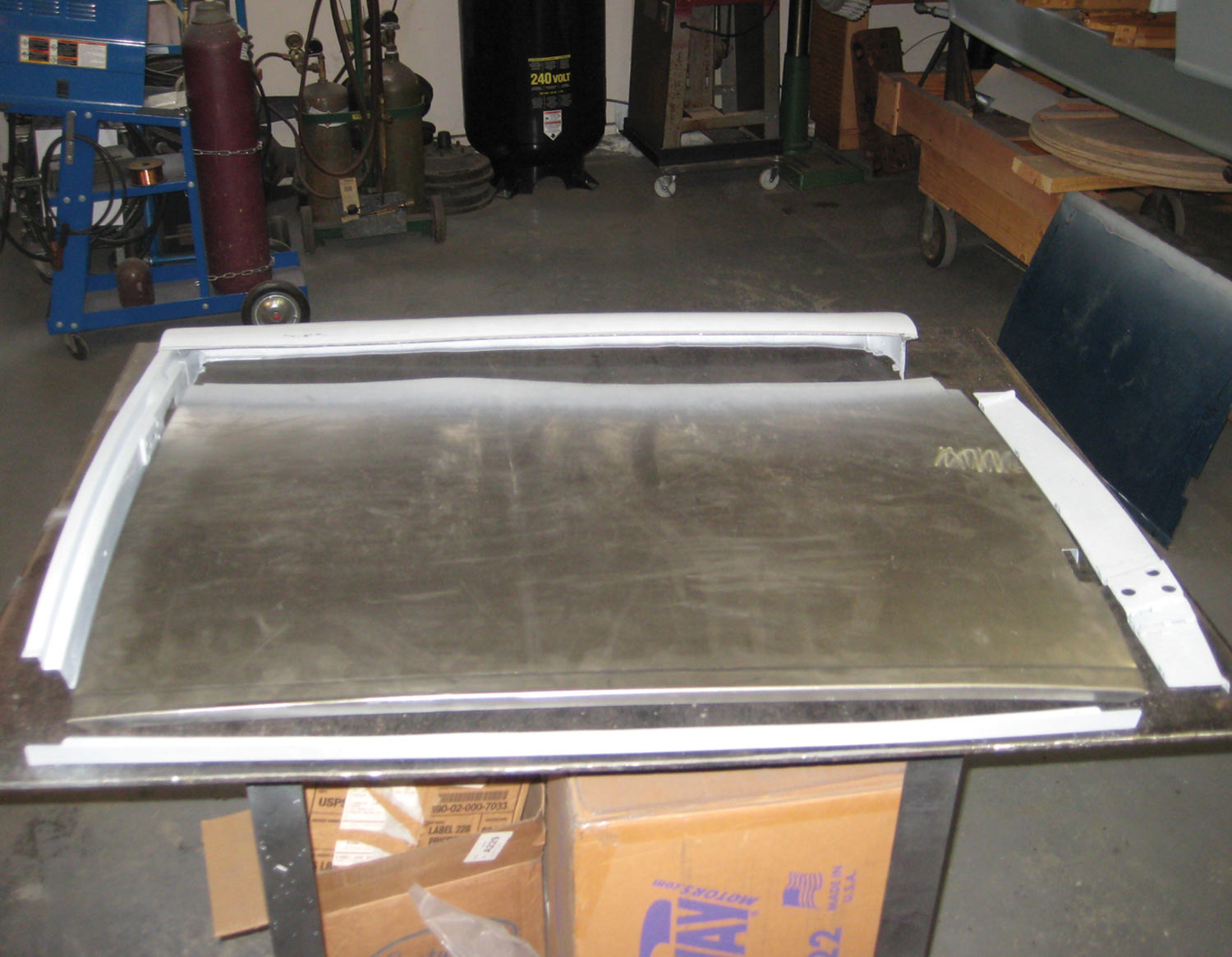
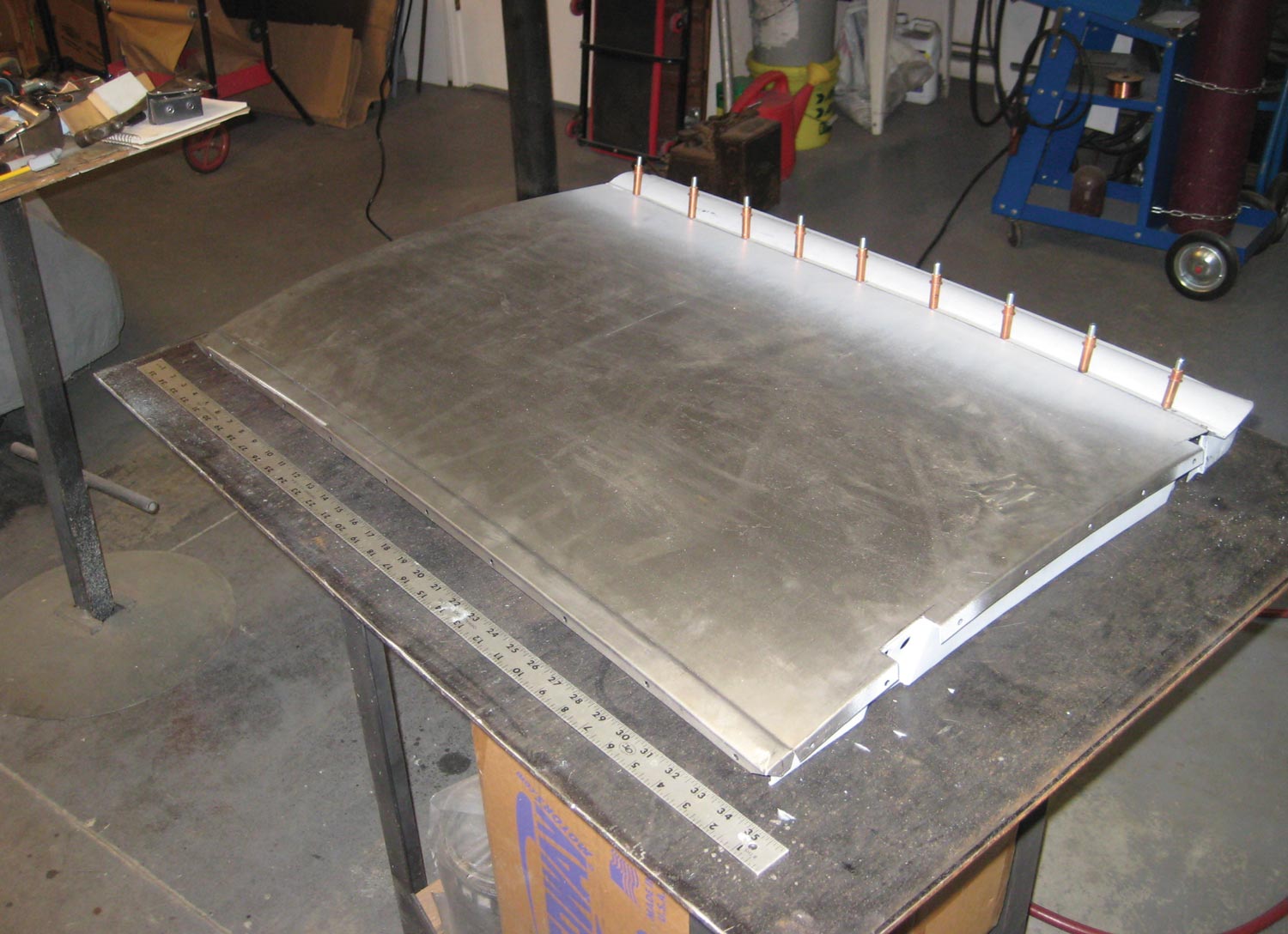
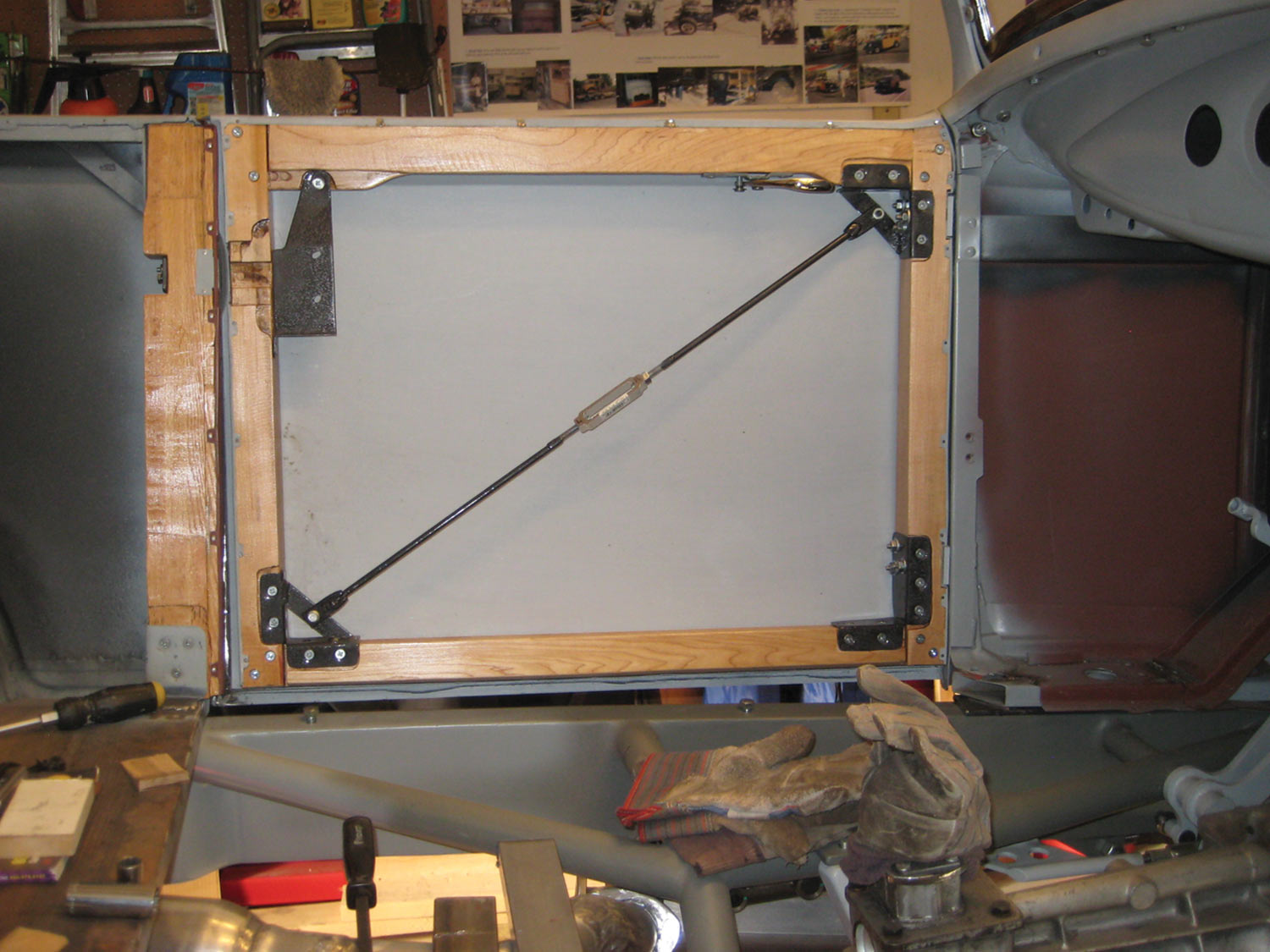
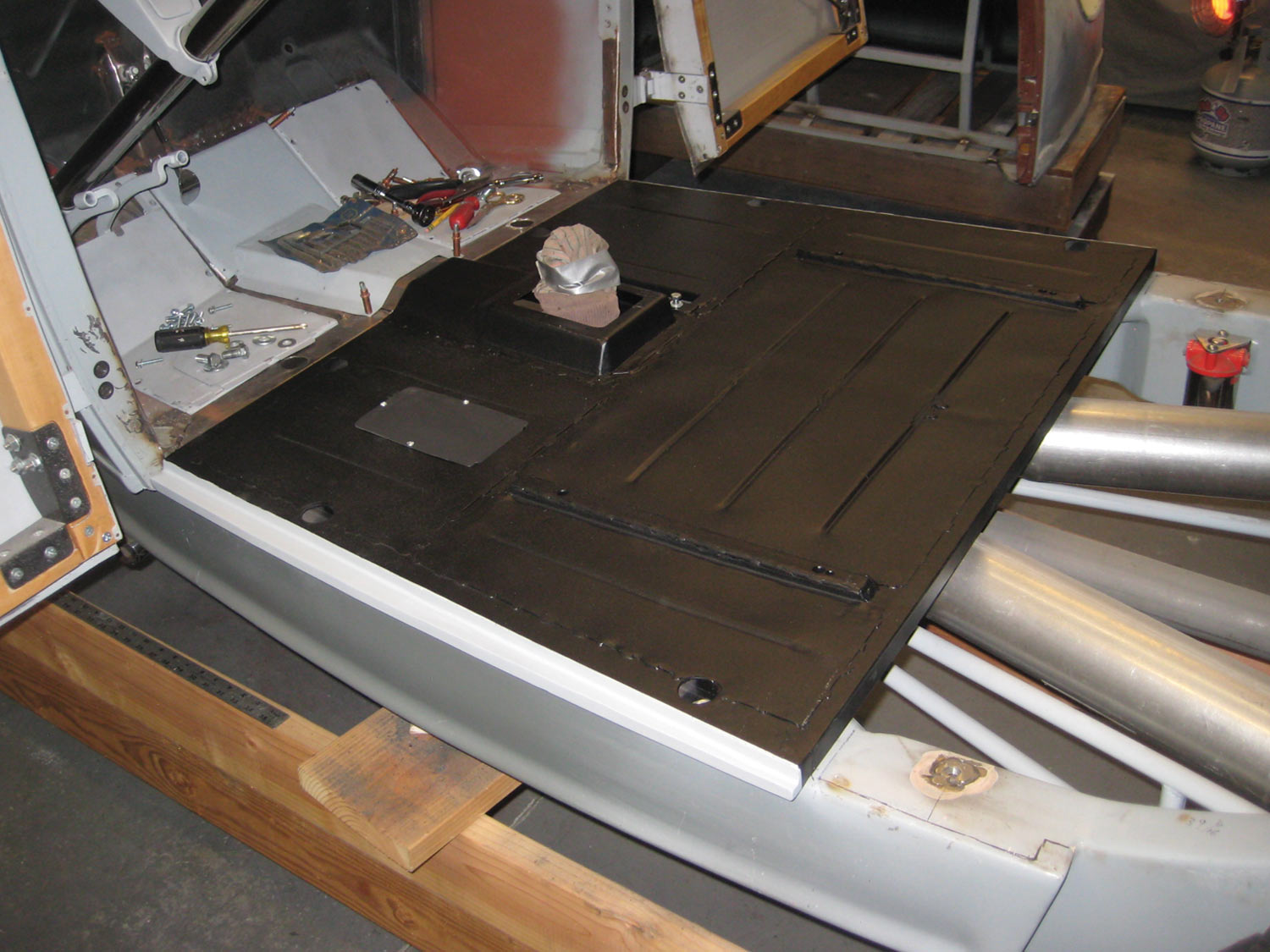
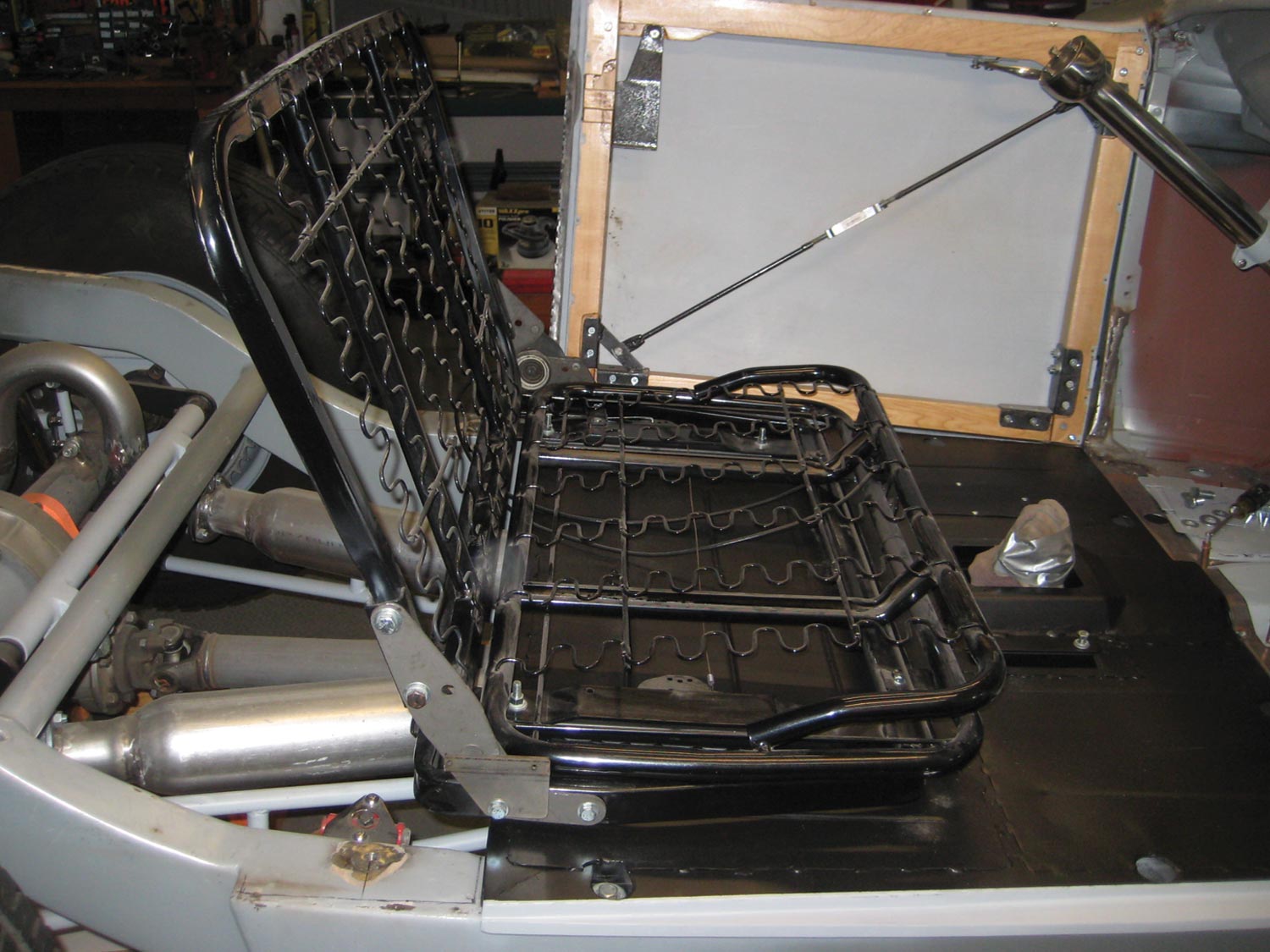
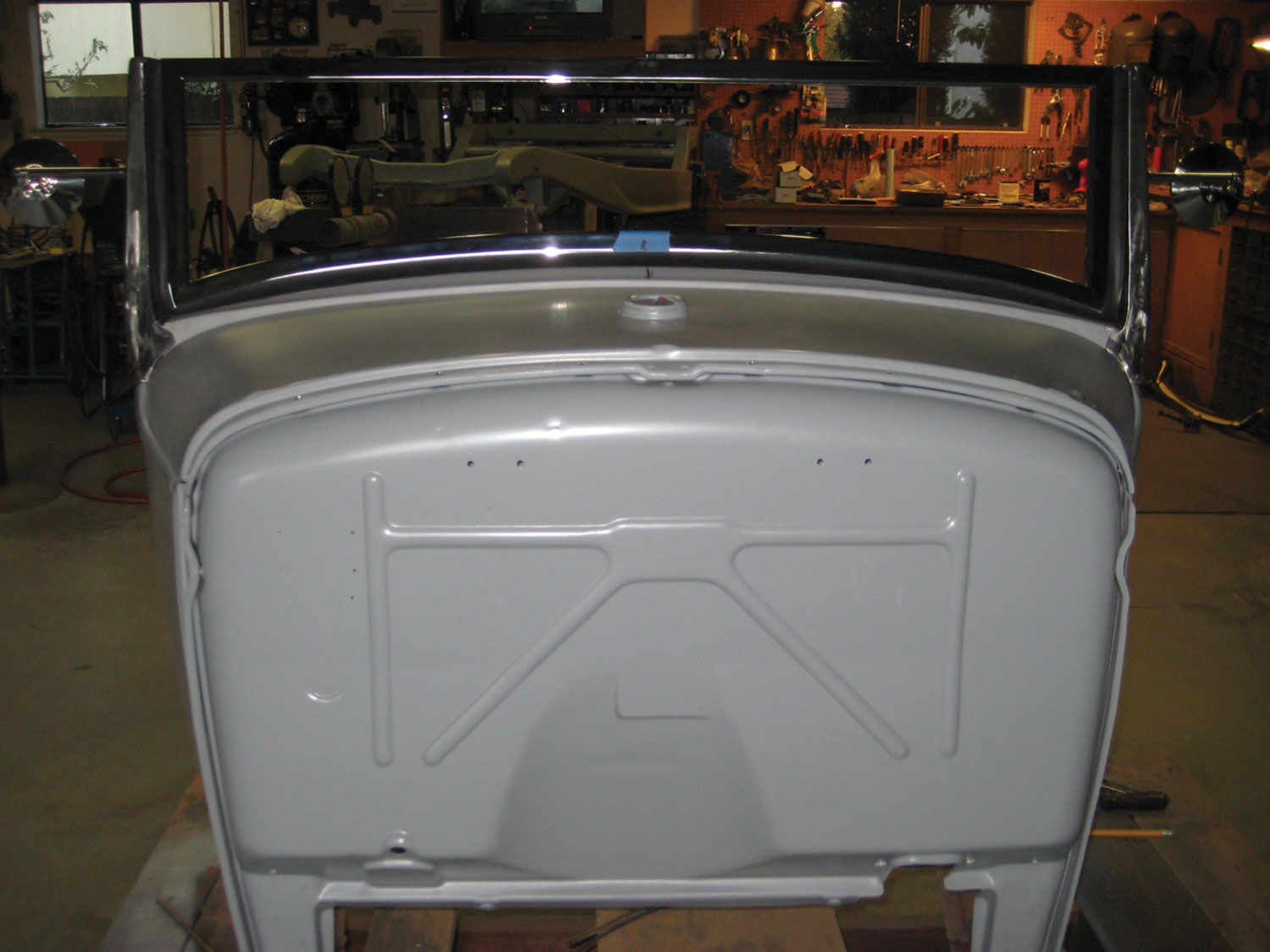
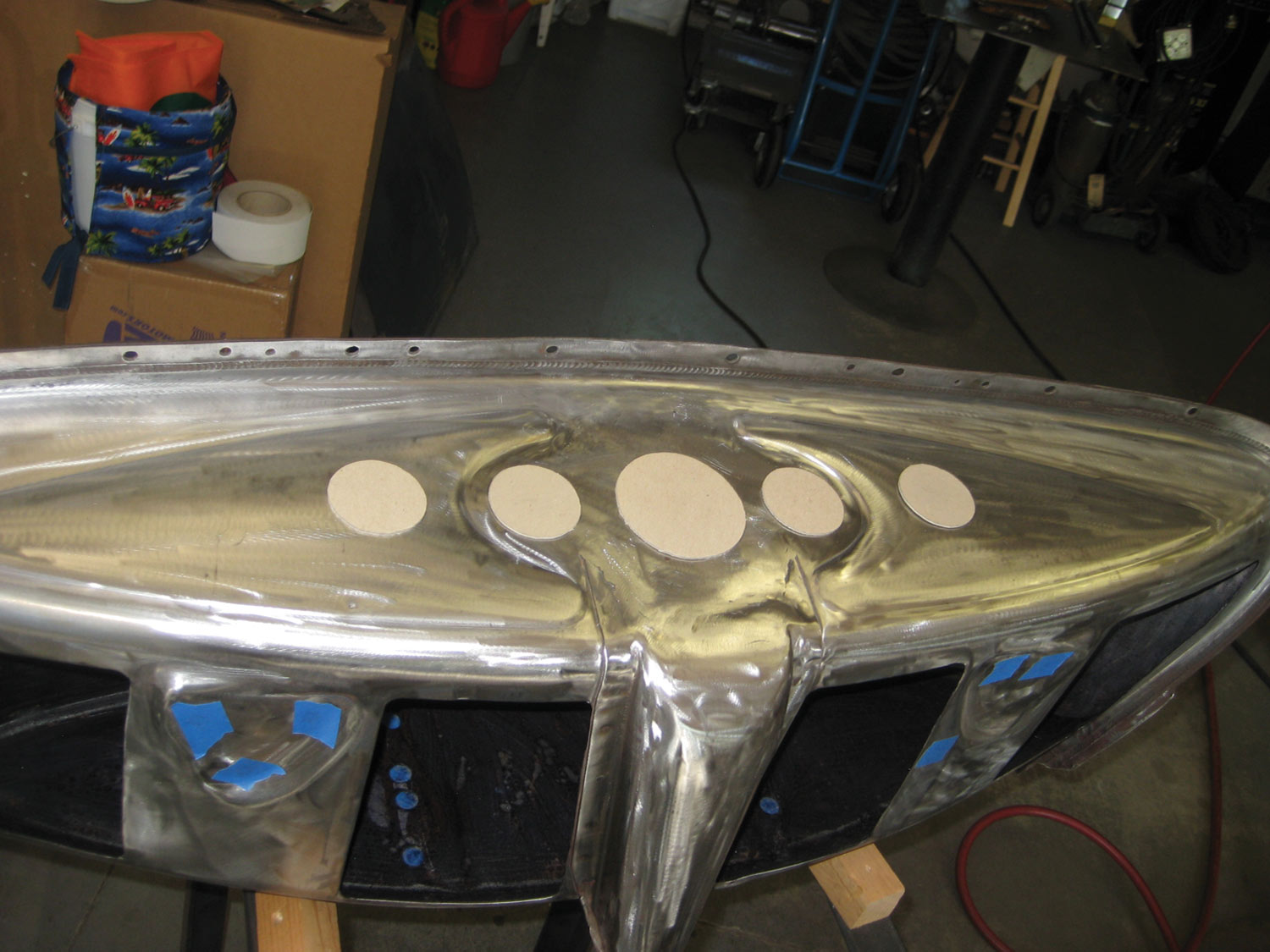
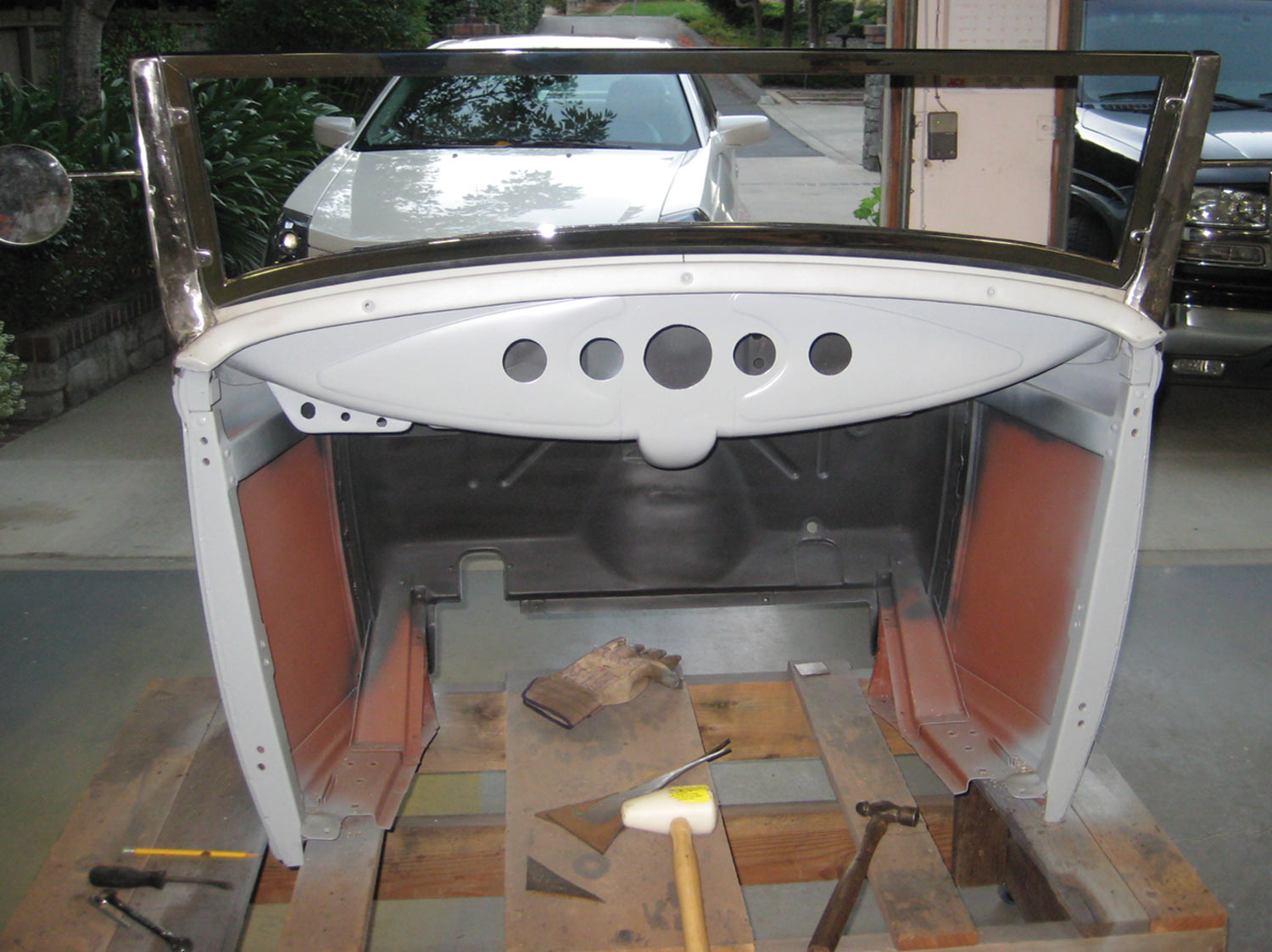
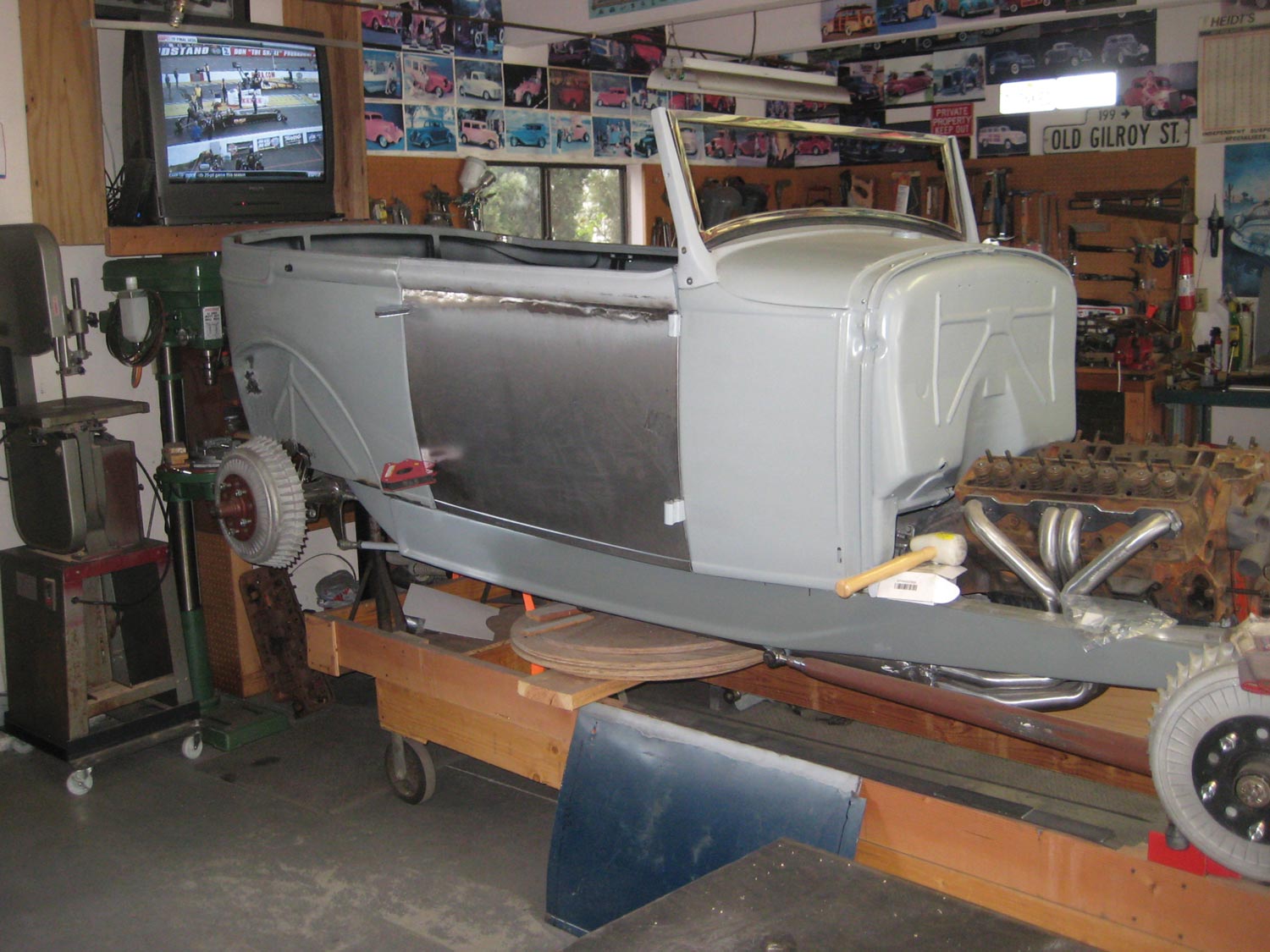
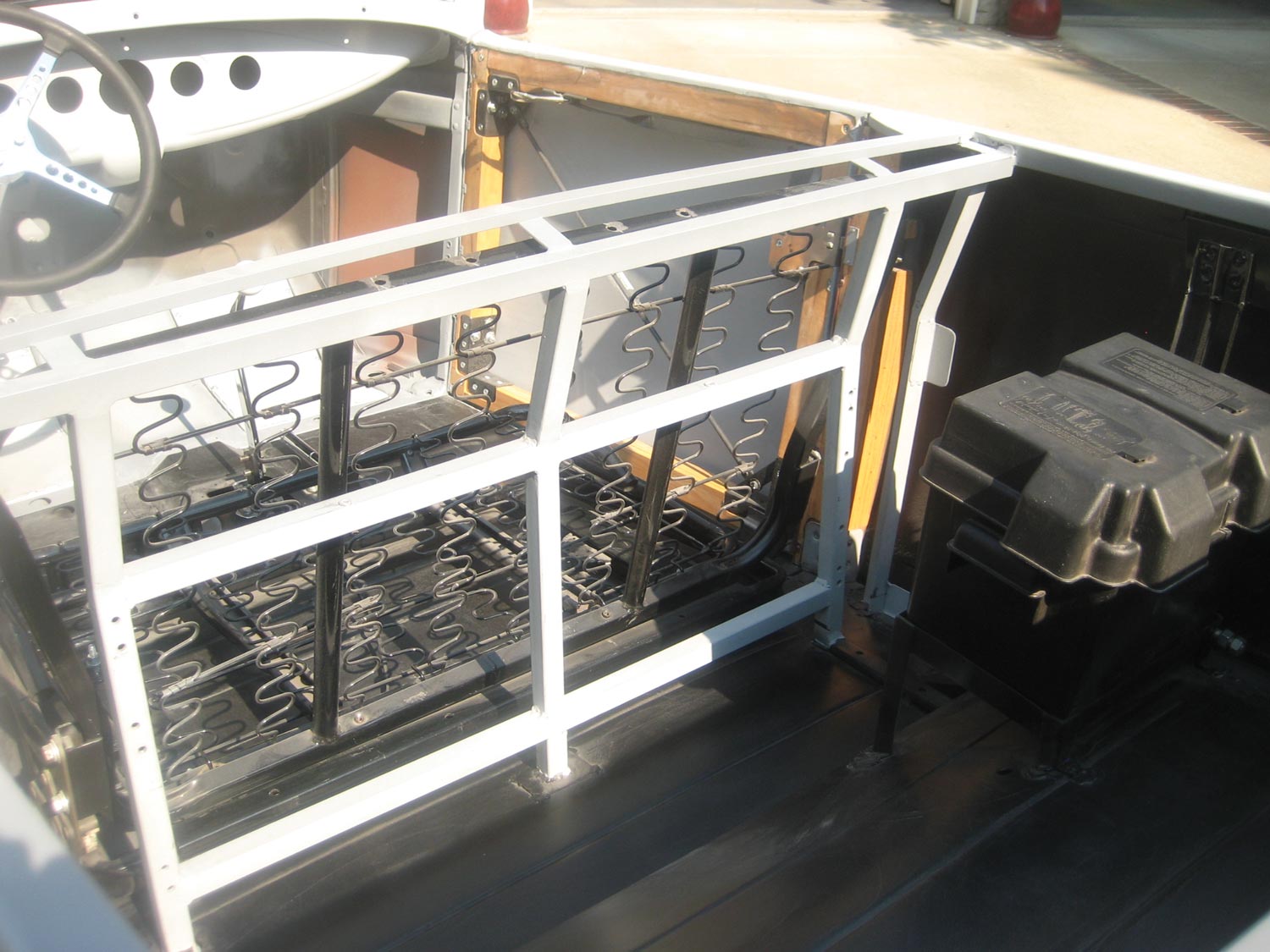
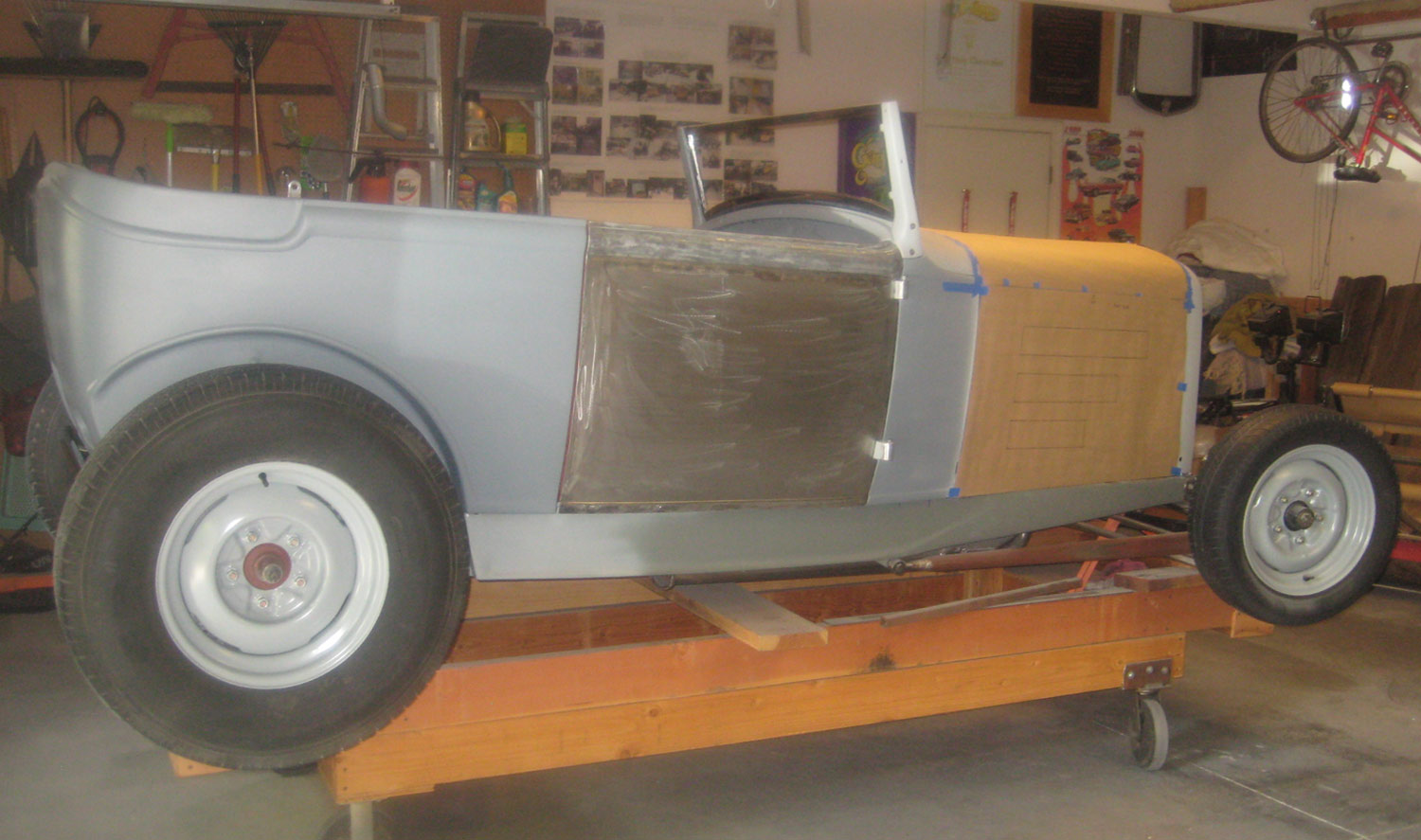
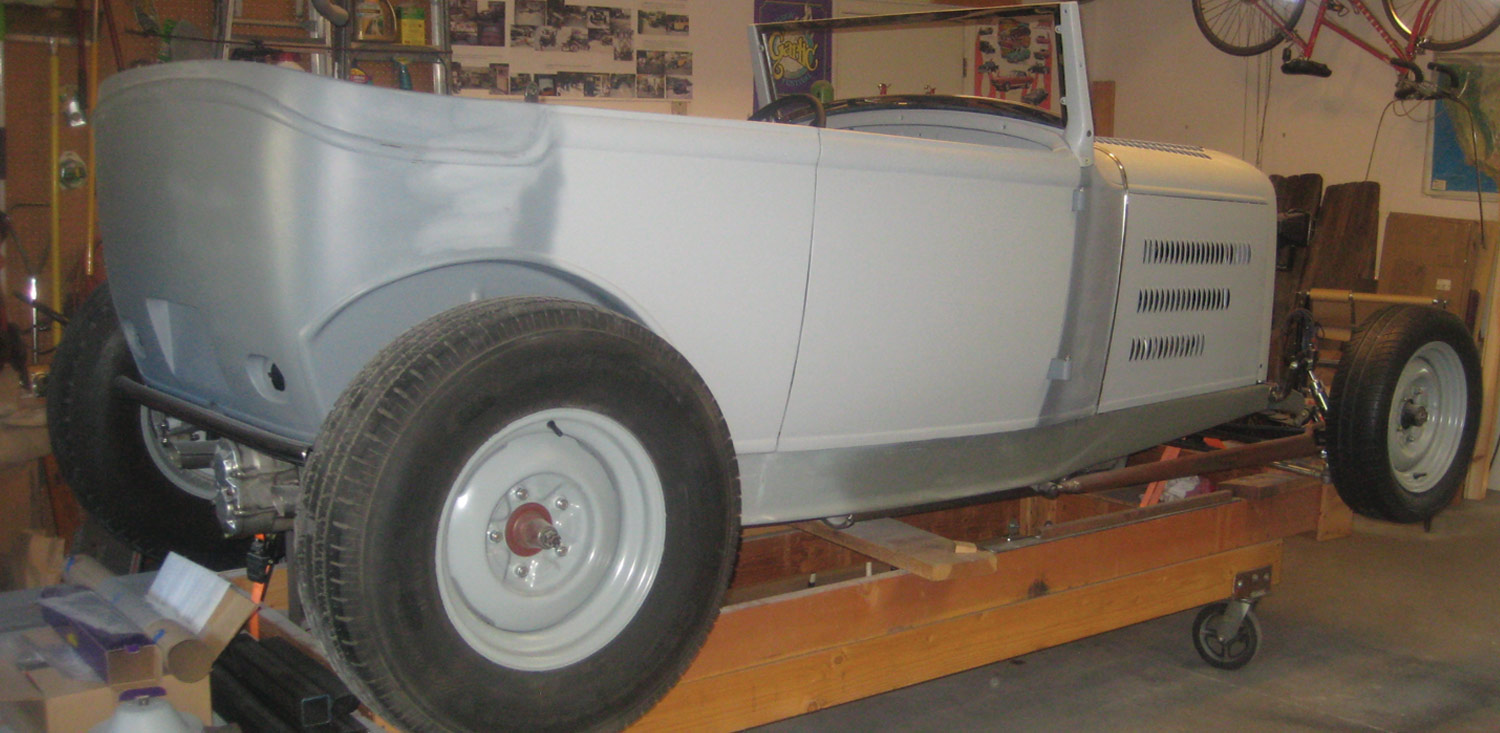
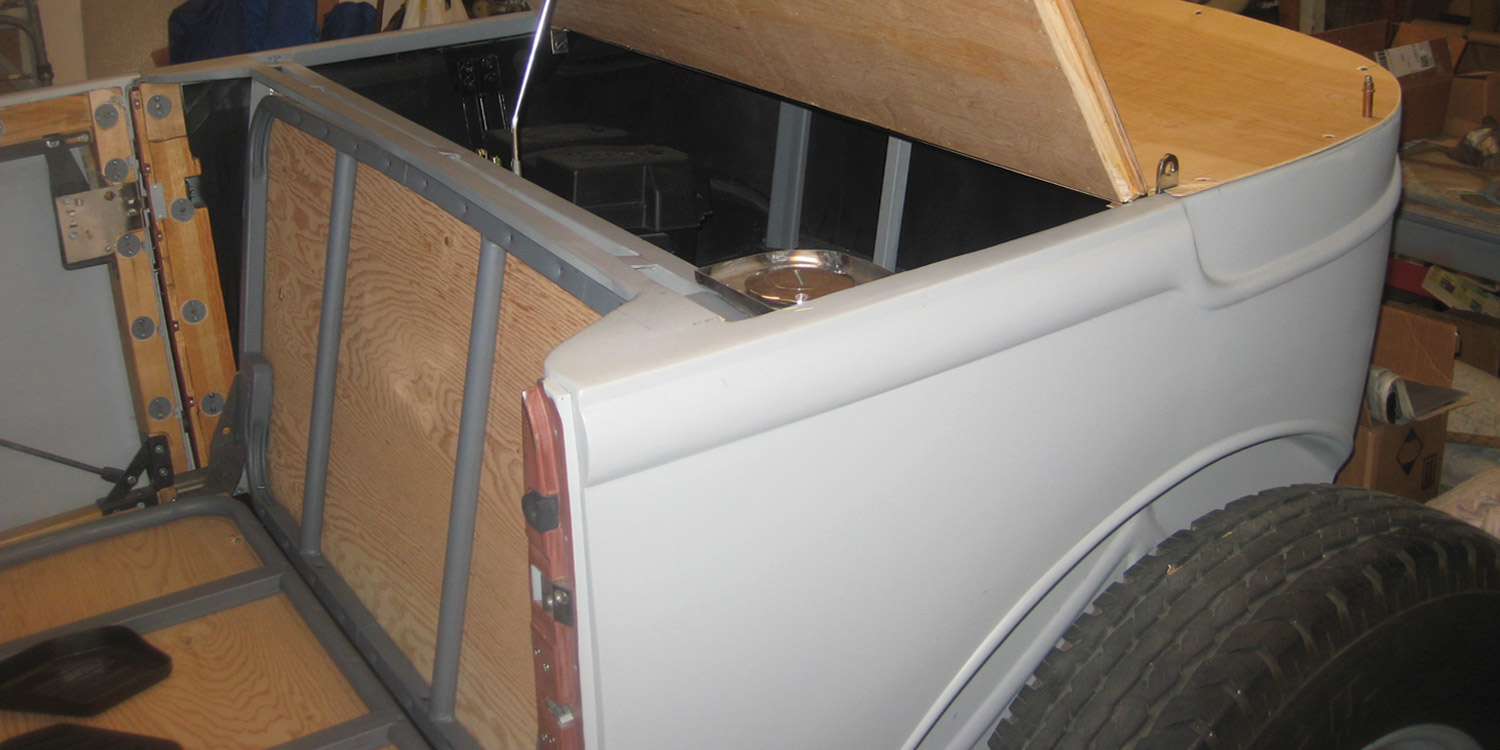
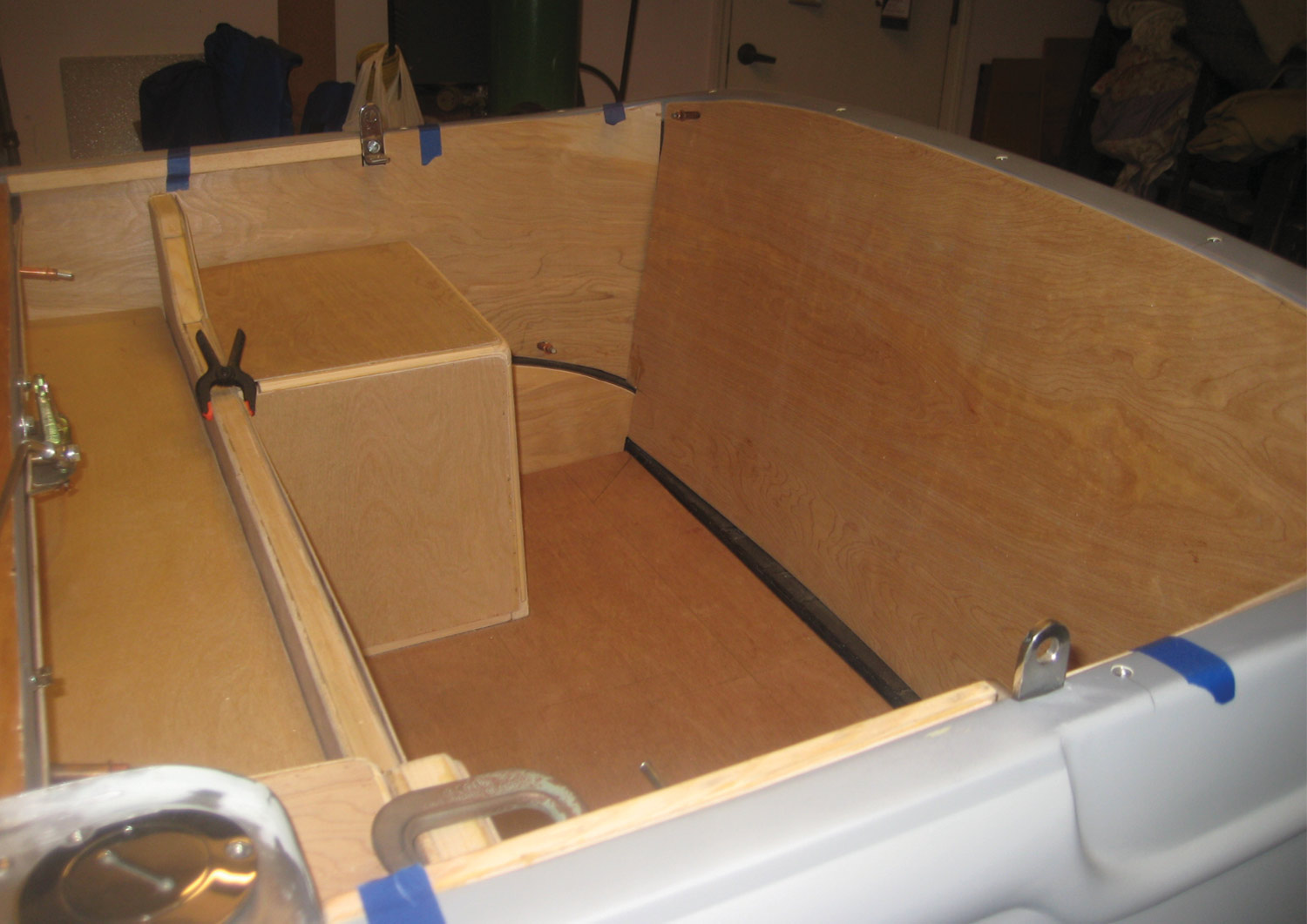
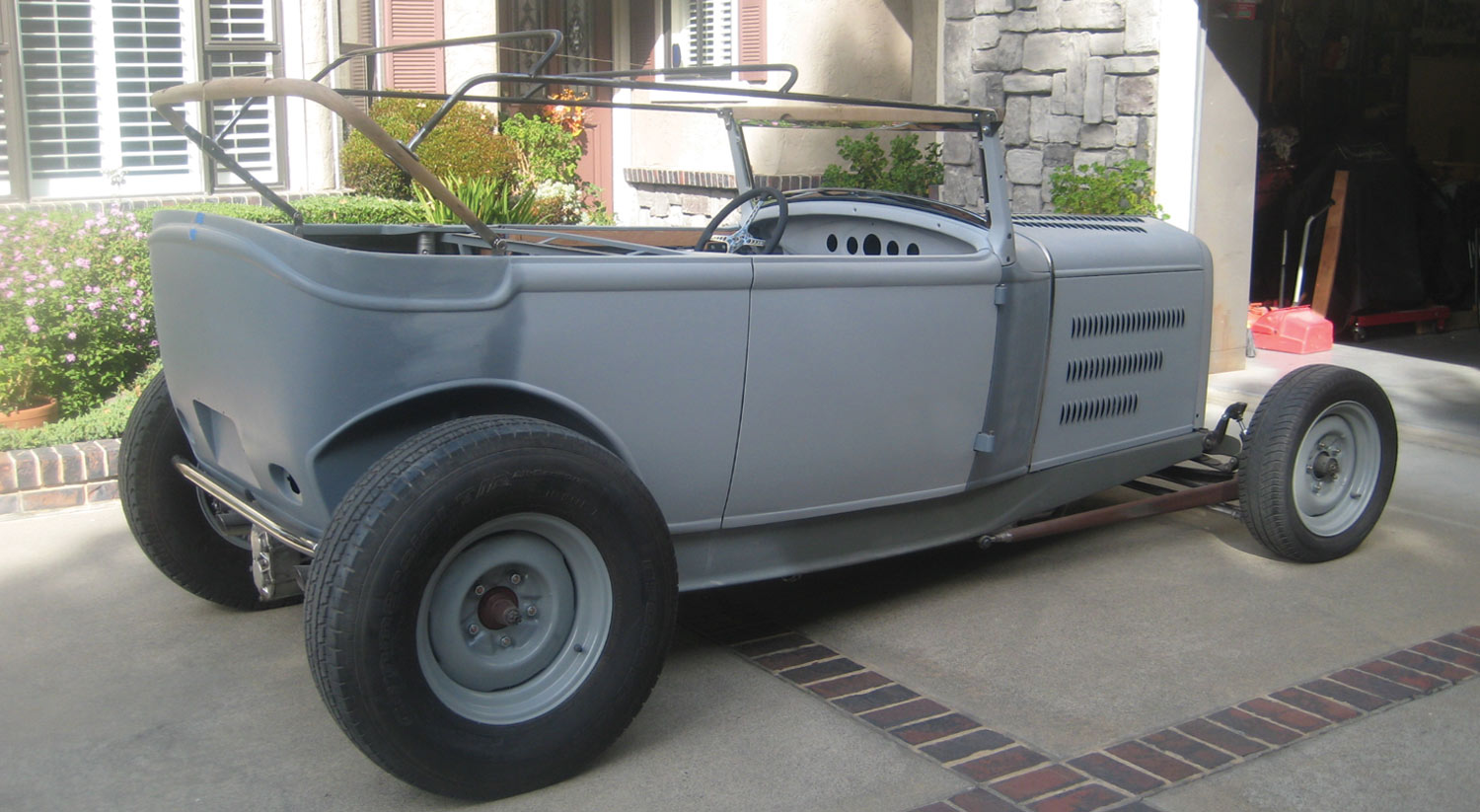
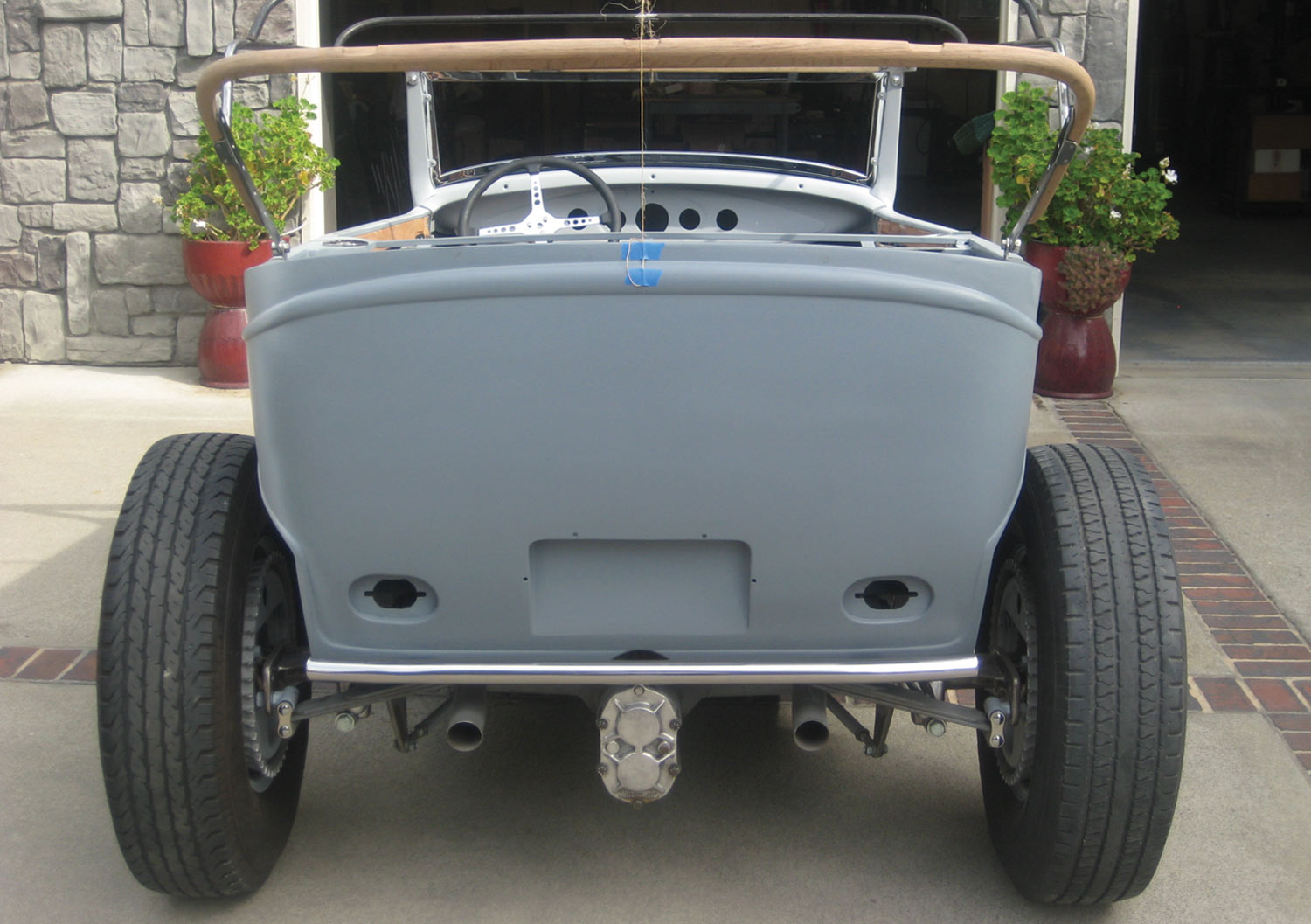
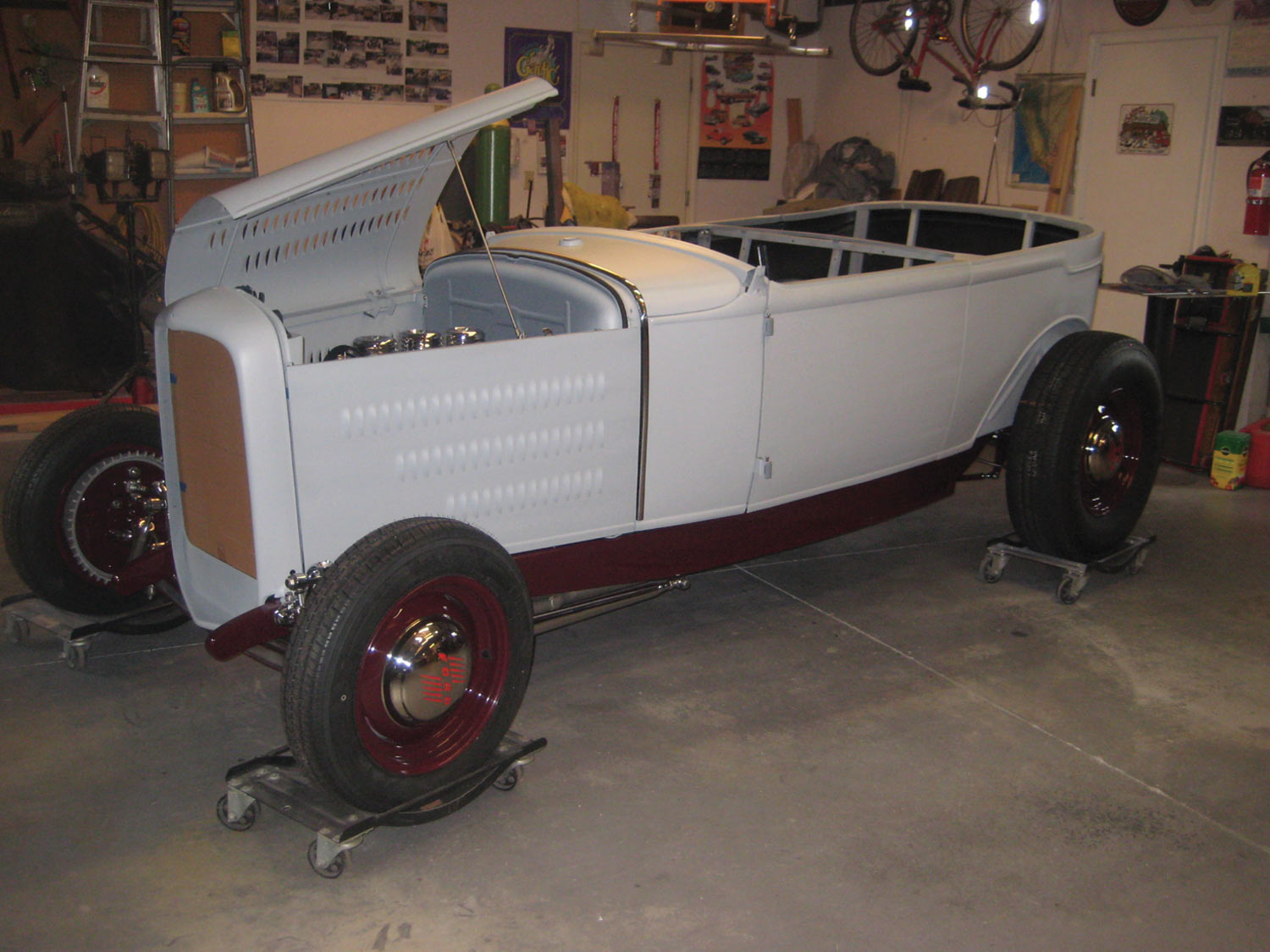
VOLUME 3 • ISSUE 20 • 2022