

ll of us grew up knowing how to change a spare tire or we learned quickly while parked on the side of the road. Odds are we haven’t changed many flats in recent years as a result of tire technology, better roads, and the cell phone that have transformed the way we live. So, what to do with the spare tirewell in our ’50s and ’60s cars as they, for the most part, no longer comply to the specs of our new tire sizing and wheels of choice. Of course that doesn’t mean you shouldn’t be prepared, but that’s a story for a different page.
The 1955 Chevy wagon in these photos is Modern Rodding’s very own project car with the work to be handled in our In The Garage Media Tech Center. (We will also be unveiling our Model A roadster in the coming months.) This will be the first of a long string of stories that will deal with everything from removing the spare tirewell that now provides for a larger gas tank mounted underneath to upgrading the tailgate and the surrounding sheetmetal. A little background on the 1955 Chevy wagon as it is offered in both two- (Nomad) and four-door wagons. Our four-door is a six-passenger, seven-window wagon that’s in need of a lot of help.
Chevrolet made a dramatic change to its body design in 1955 with the new smooth straight panels on the hood and sides. This was a noticeable change from previous years, which was still reminiscent of the prewar styling. Aside from the flatter panels, the wrap-around windshield and rear glass, and the noticeably different taillights, the new look clearly distinguished itself from early models. It was also the first-year style and performance were combined through the introduction of the 265-inch V-8. As you can tell from the photos our 1955 Chevy wagon has seen better days. In other words, patina is alive and well and lots of work will be needed to bring our 1955 Chevy wagon back to summertime drivetime specs while keeping the “character” years of use and abuse have produced.
The first step, in our many steps forward, is to remove the spare tirewell, as it’s no longer needed and what’s needed is a larger gas tank. It just so happens that the space underneath the floorboard via the spare tirewell removal will afford us the space required to install a 29-gallon Classic Performance Products gas tank, ideally suited for cross-country drives.
We also brought into service our HFT Central Pneumatic high-speed metal air saw (10,000 spm), ideal for cutting through plastic and, in our case, sheetmetal. It will handle 16-gauge metal.
We were also going to need a cordless electric impact driver capable of installing and removing small hardware. In this application we selected an HFT Hercules 20V lithium battery 20V Lithium-Ion Cordless Compact 1/4-inch hex impact driver. It’s capable of 1,500 in-lb of torque and 0-3200 IPM, making it very capable to handle a wide range of fastening.
We also found ourselves requiring an air punch and flange tool and this time we selected the HFT Central Pneumatic unit that is capable of cutting 16-gauge sheetmetal and punching a 3/16-inch hole. We would need these holes punched into the spare tirewell panel at precise locations where we would install sheetmetal screws for fastening and holes for spot welds.
Lastly, of the major tools, we needed an angle die grinder. Here we selected the HFT 1/4-inch Professional Mini Air Angle Die Grinder. Called the Chief, it has a compact aluminum body for working in tight spaces. It comes with a 90-degree head, again ideal for tight spaces, and front exhaust, which blows debris away from the work area. It’s ideal for grinding, deburring, sanding, and polishing.
You can follow along for a step by step on how we removed the spare tirewell and installed the new floorpan, tail pan, and swapped out for the new tailgate in the accompanying photos and video.
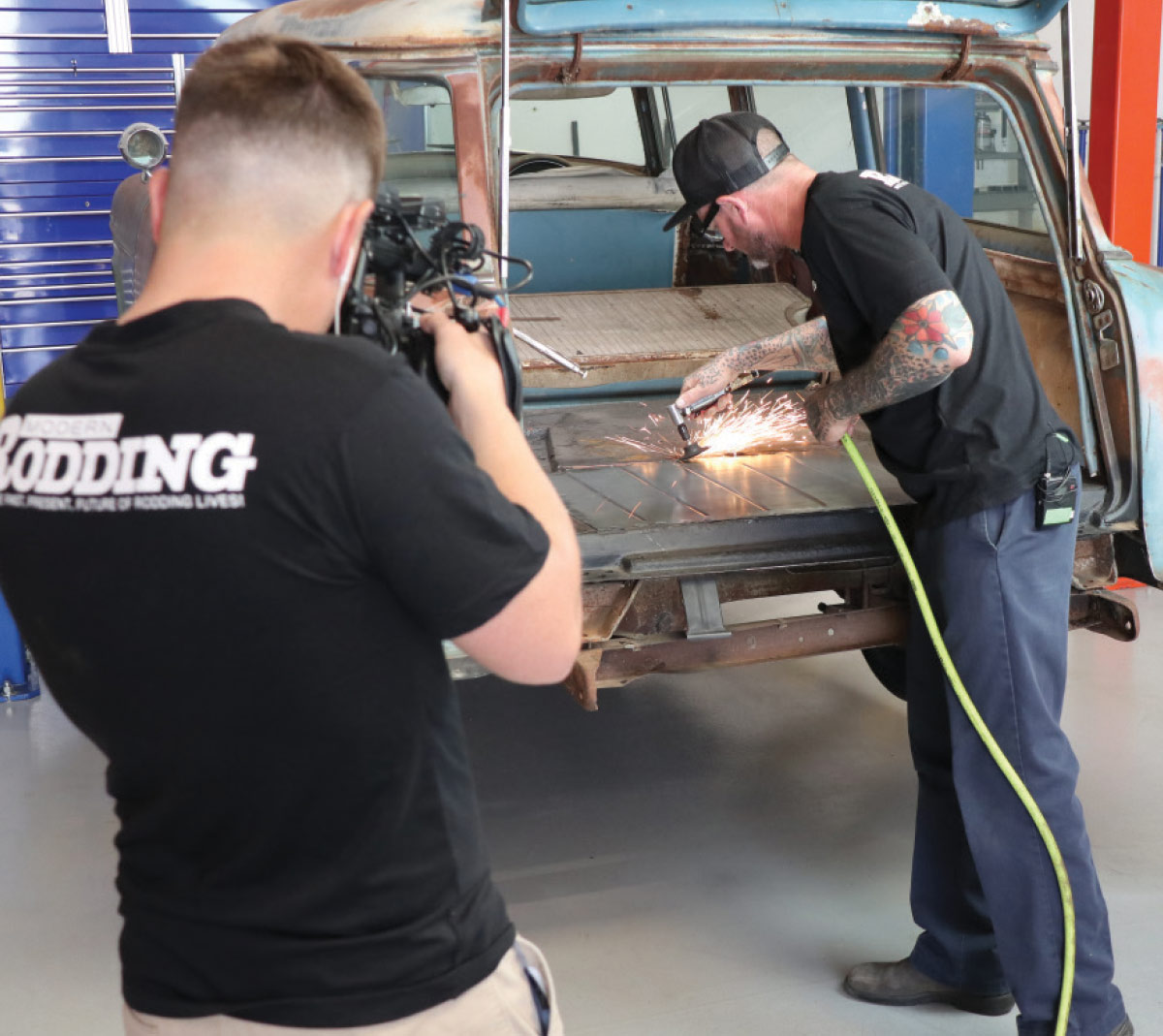
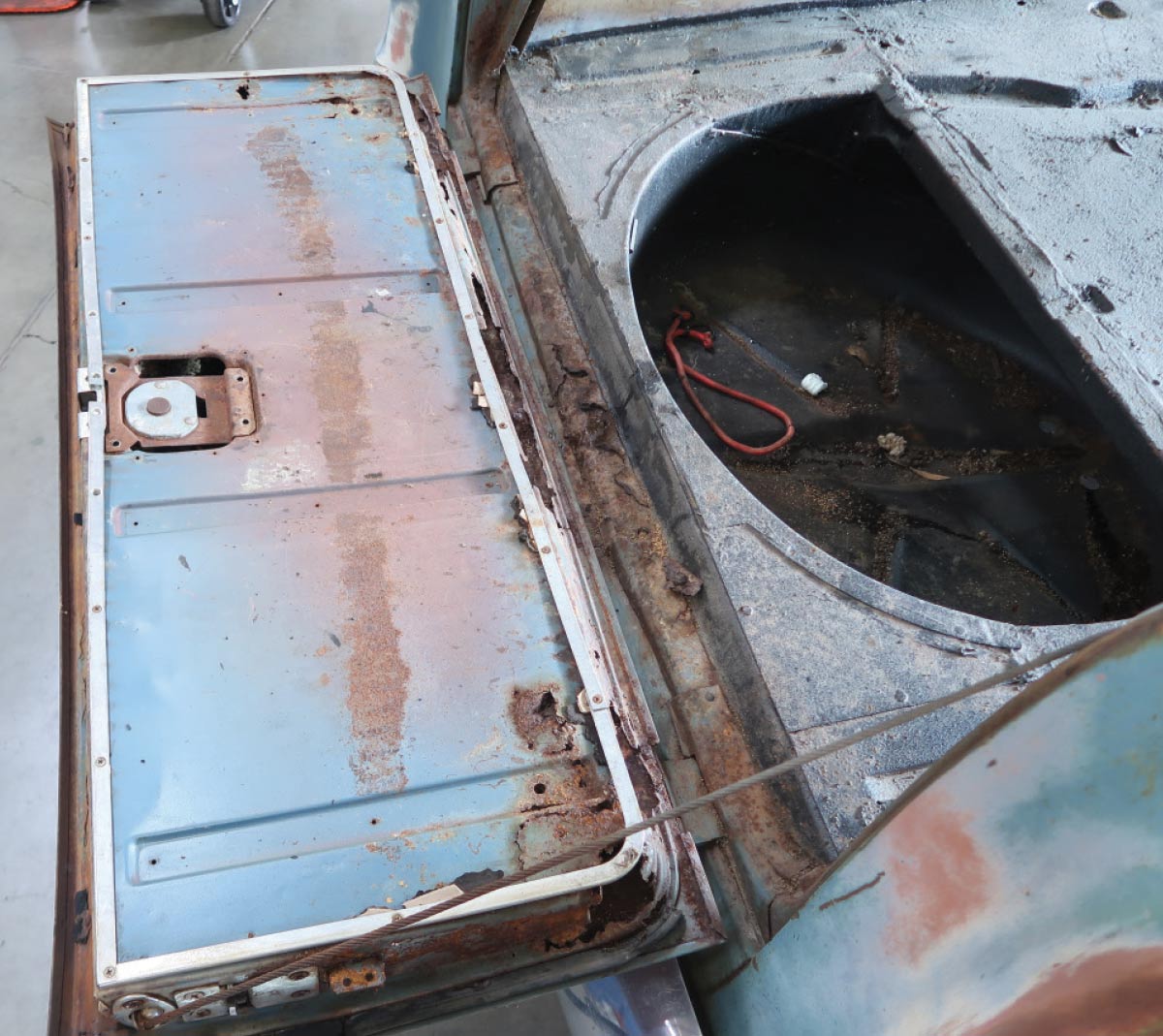
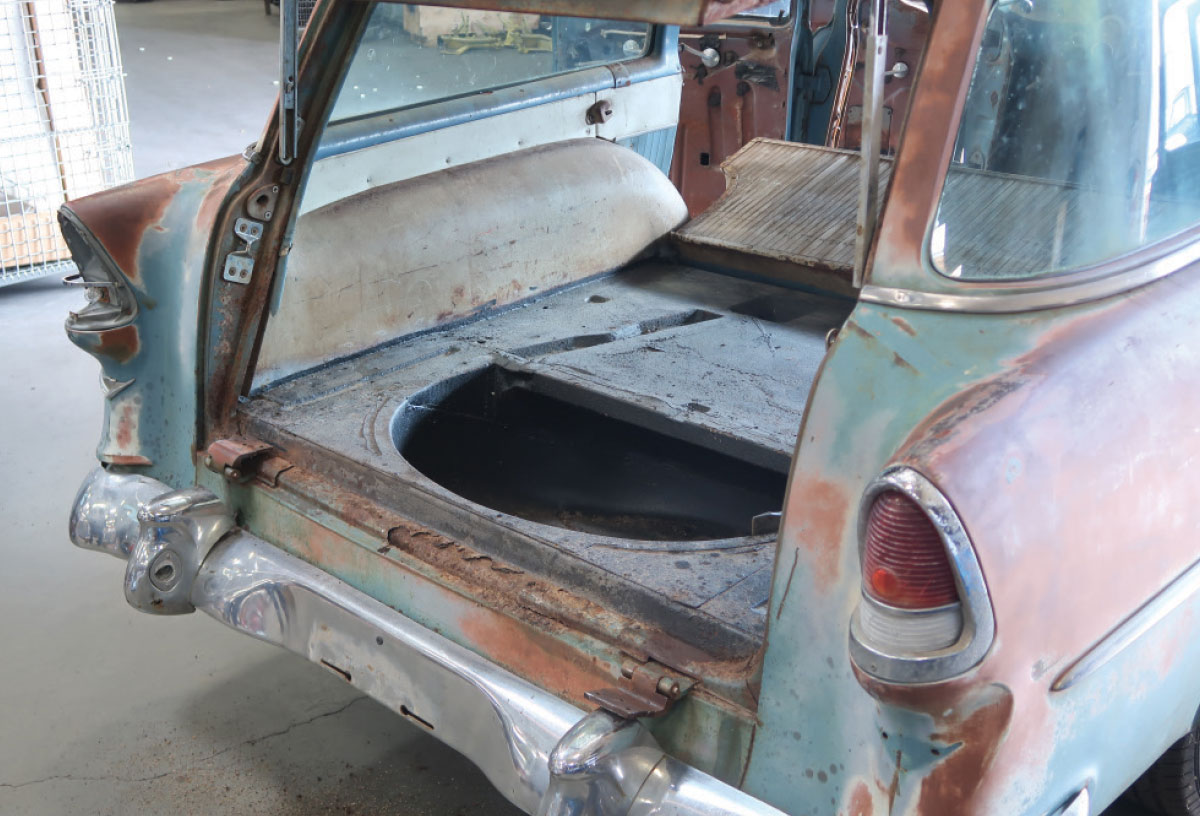
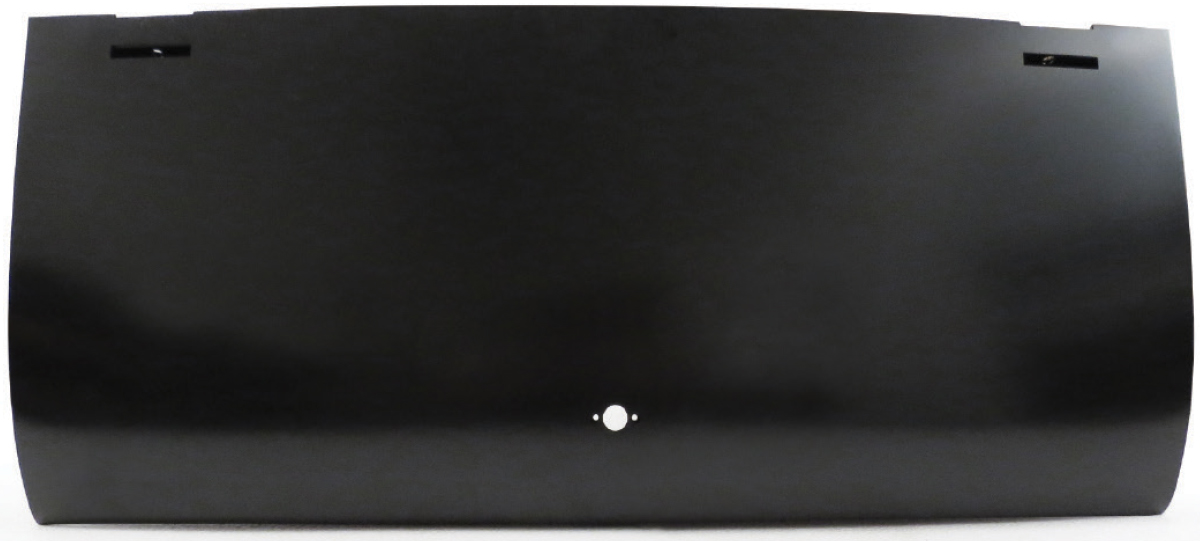

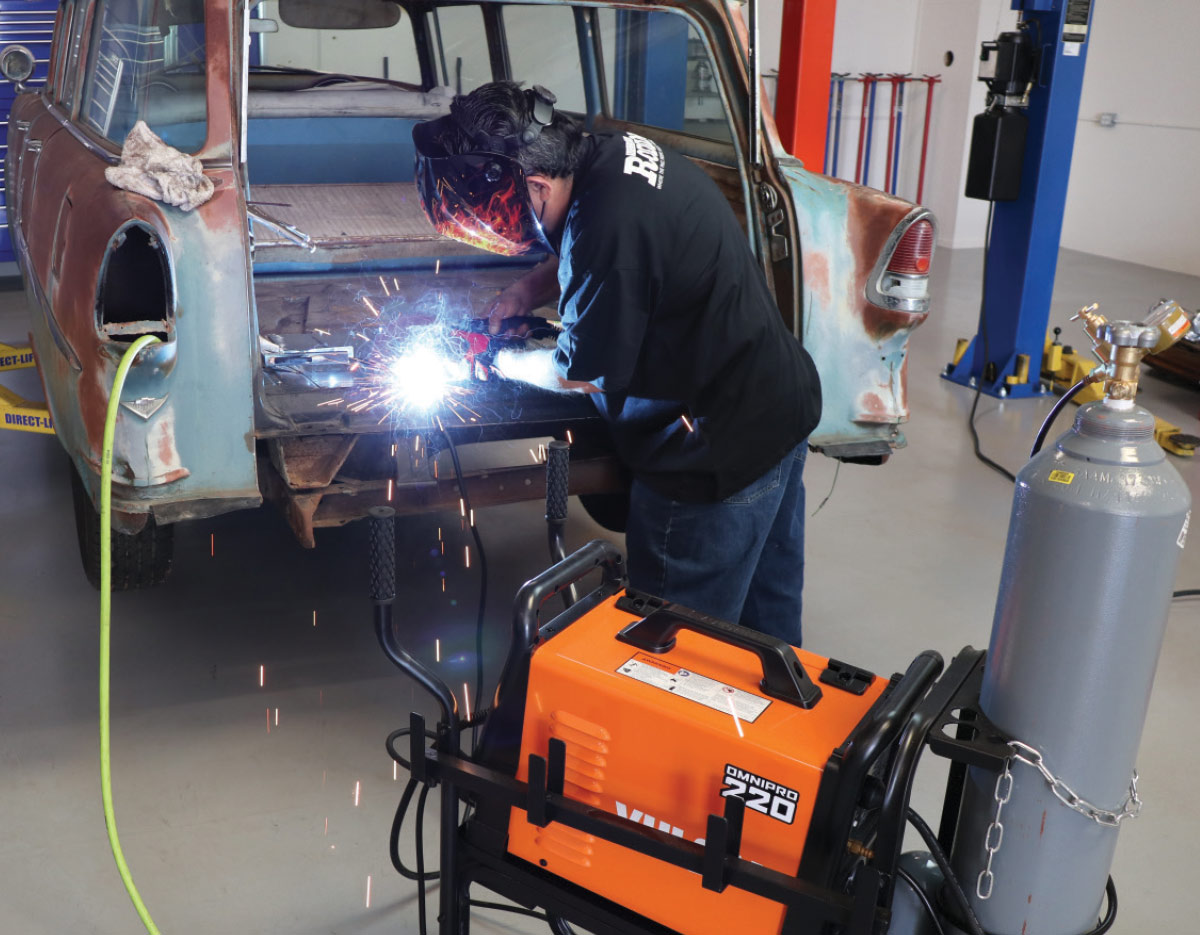
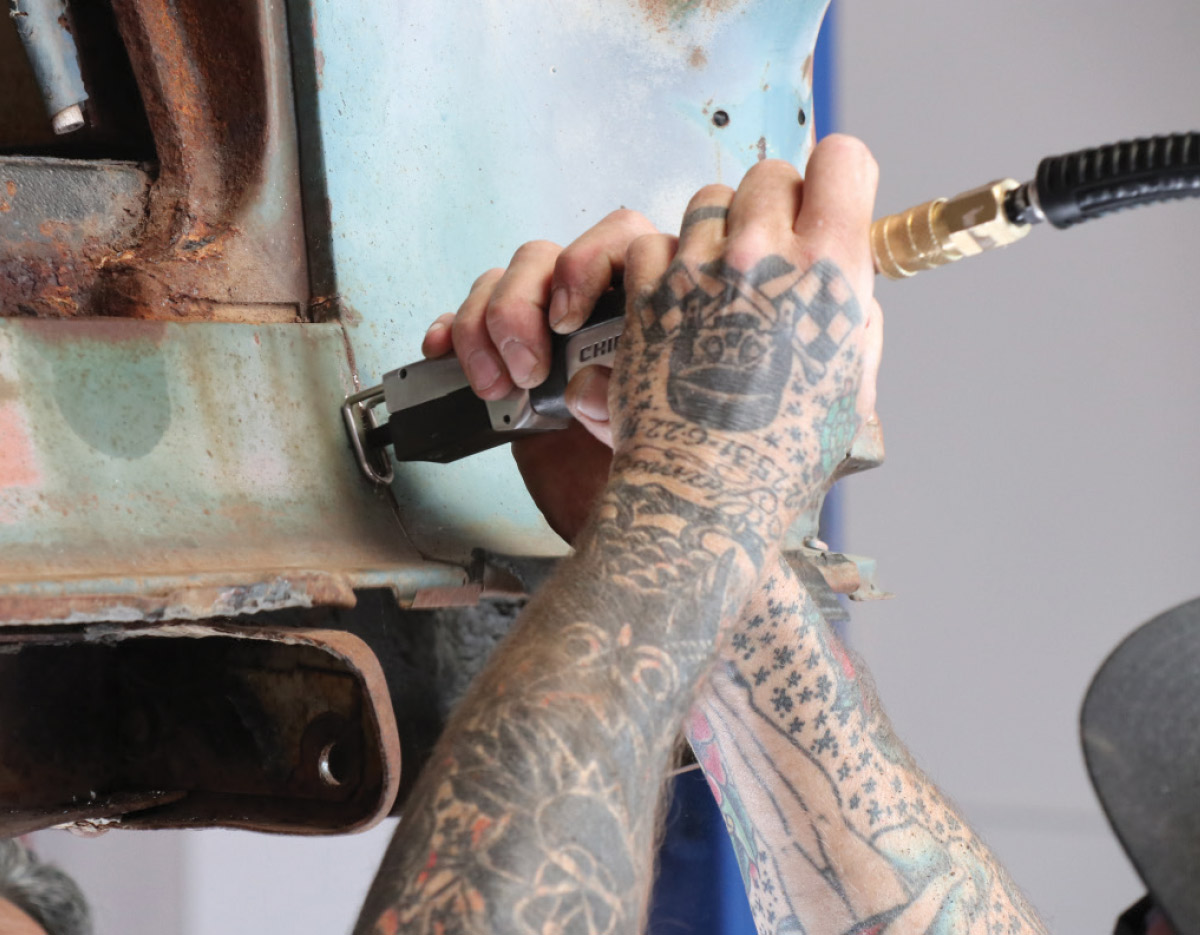
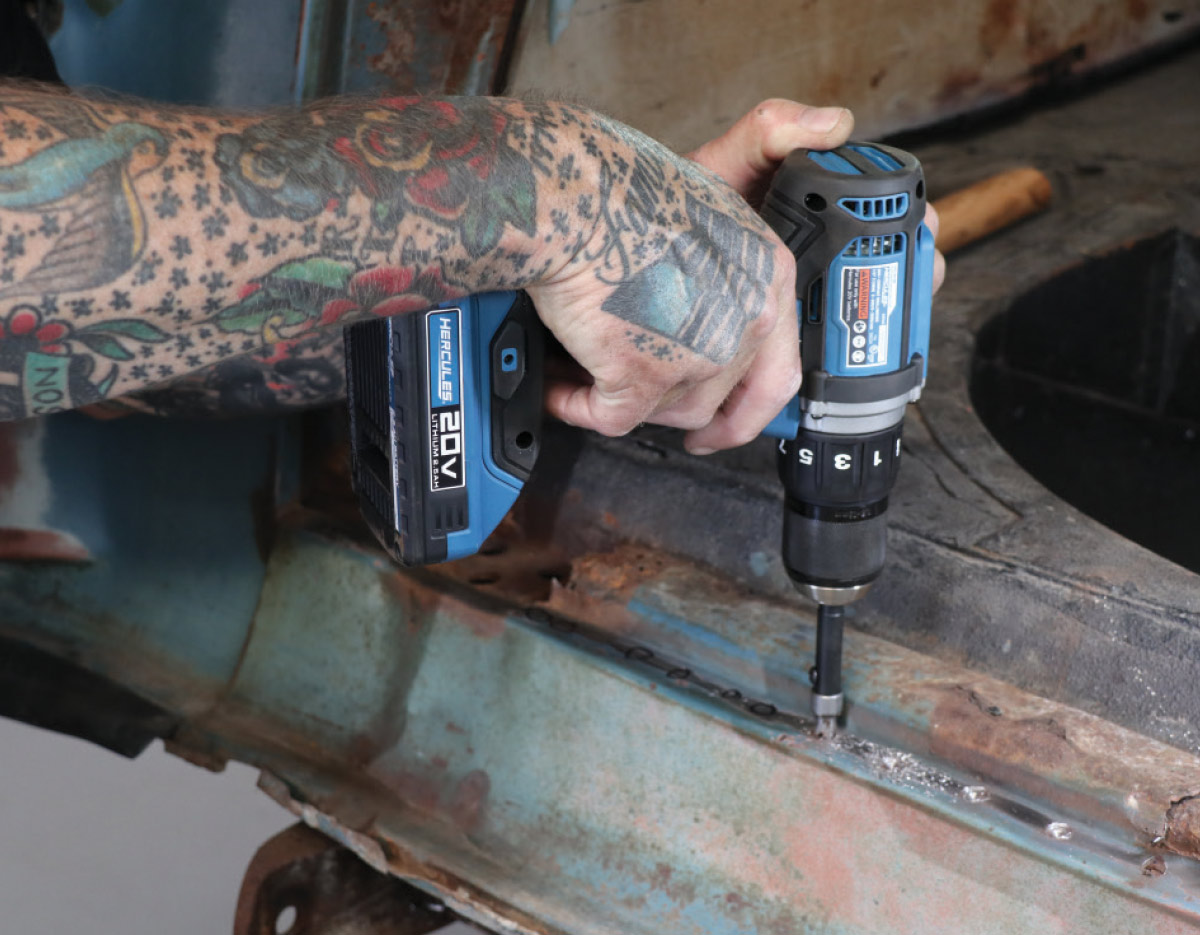
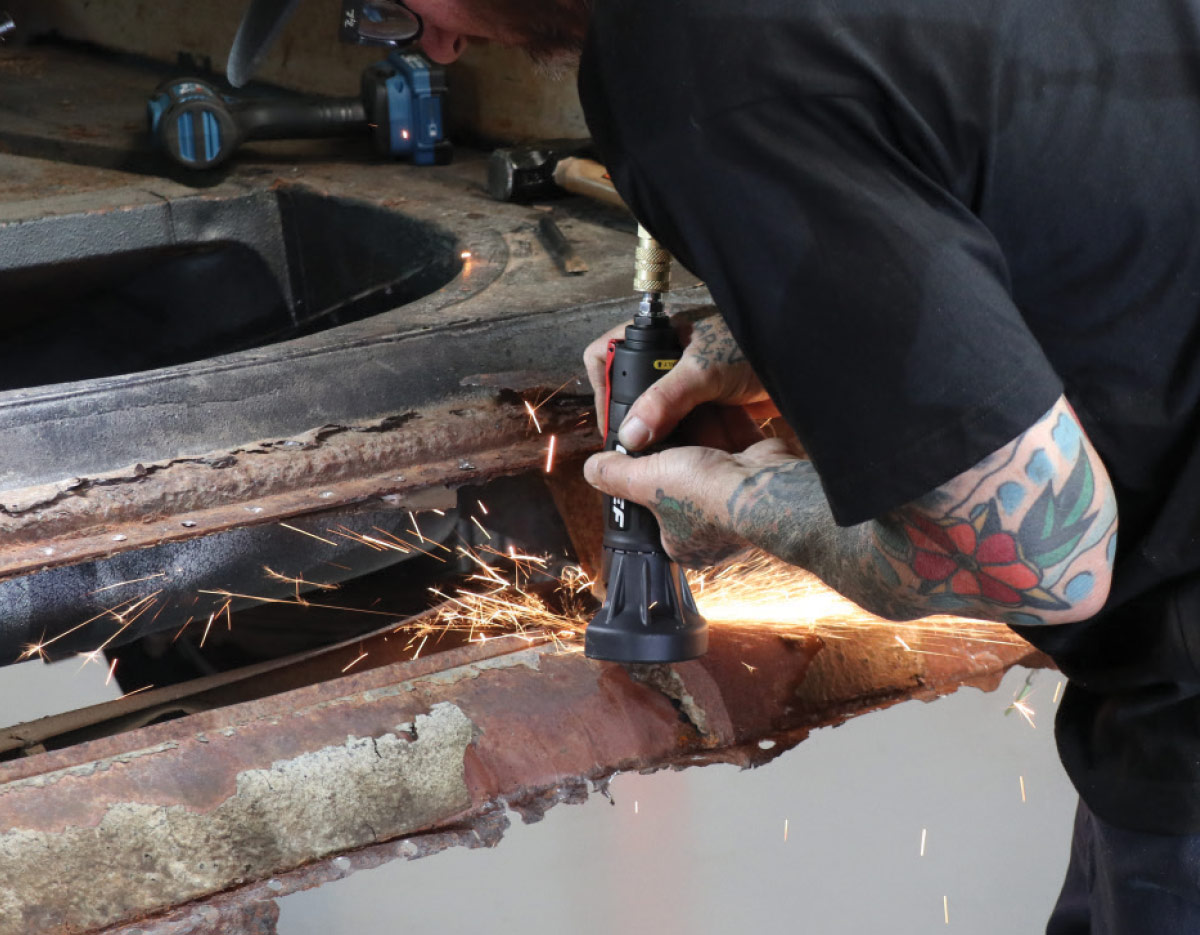
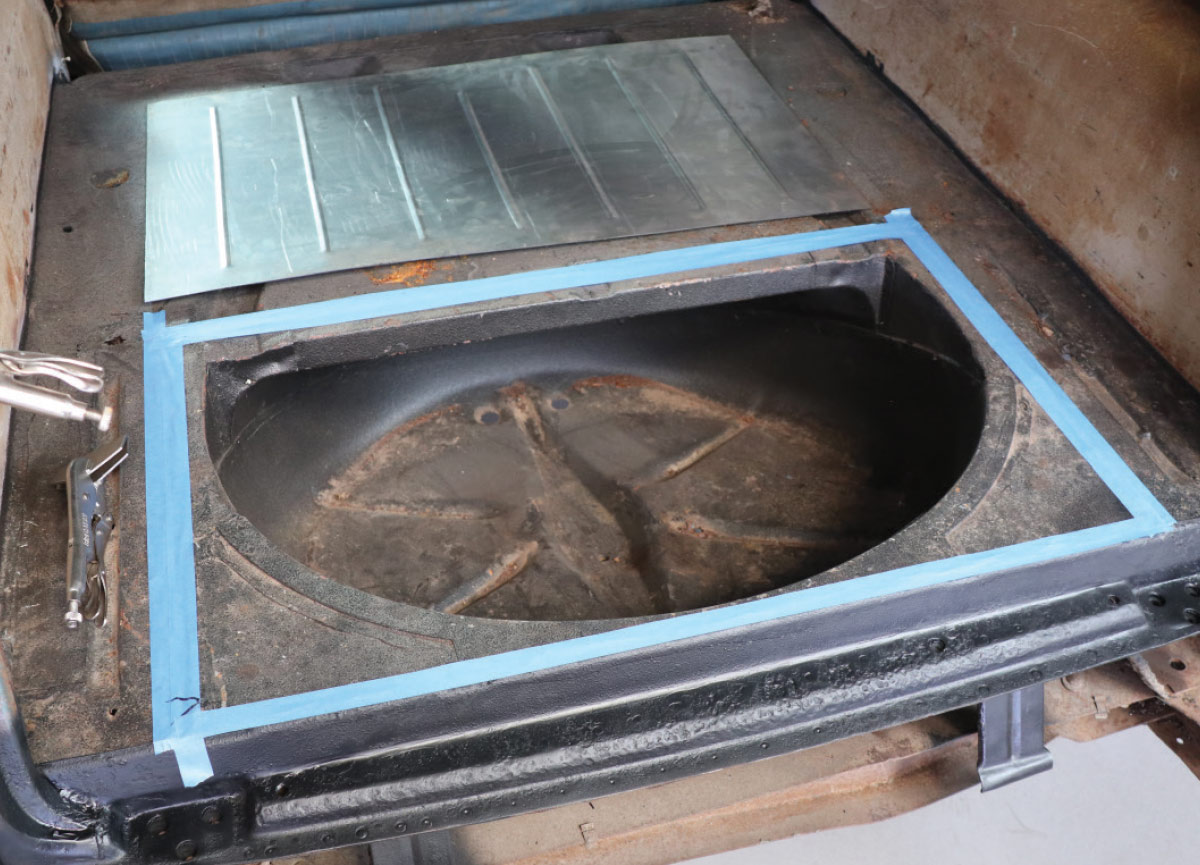
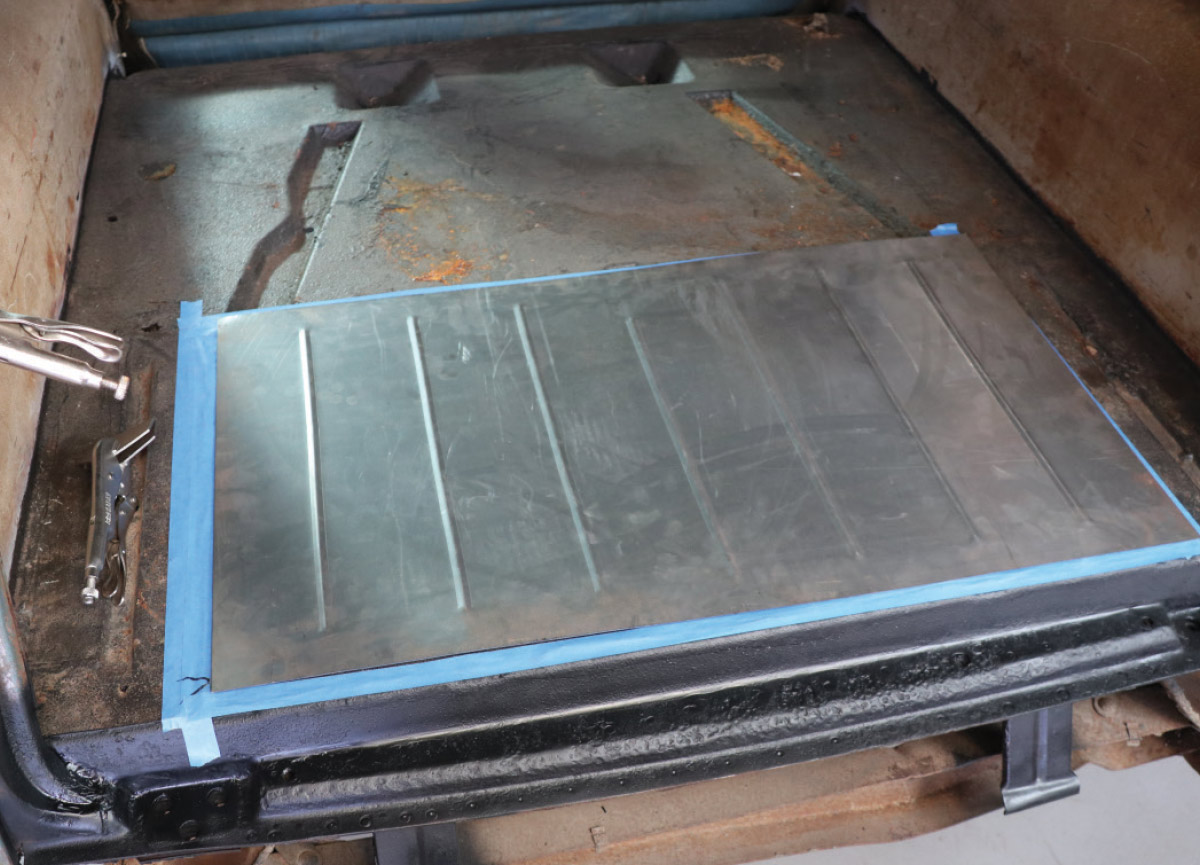
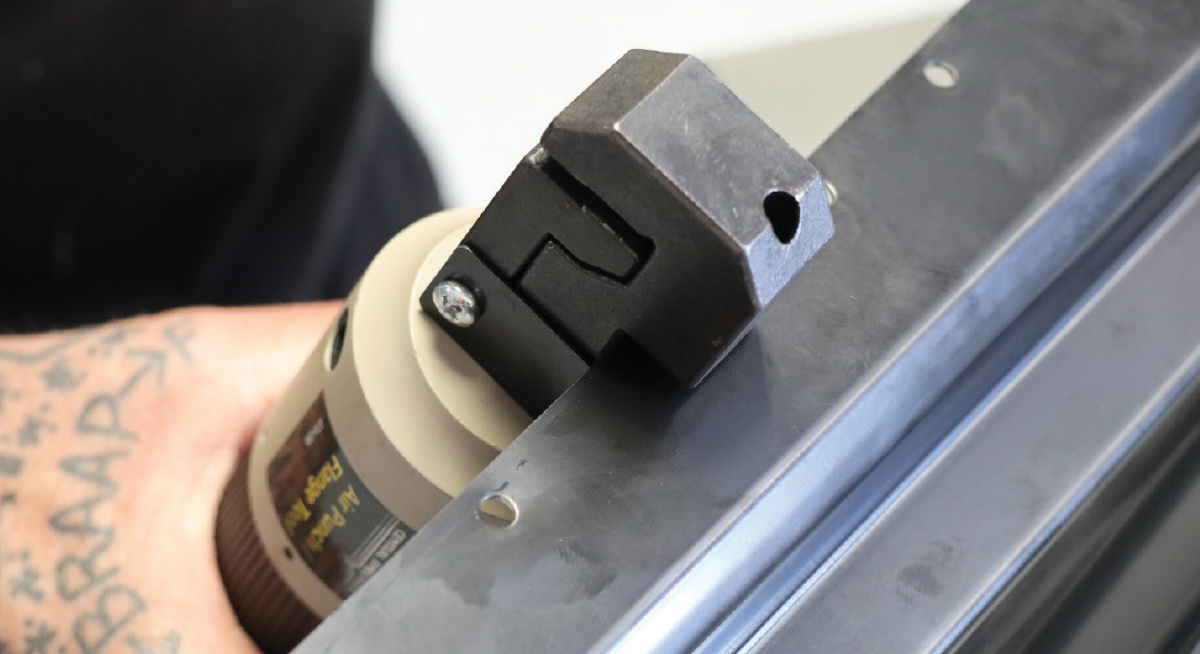
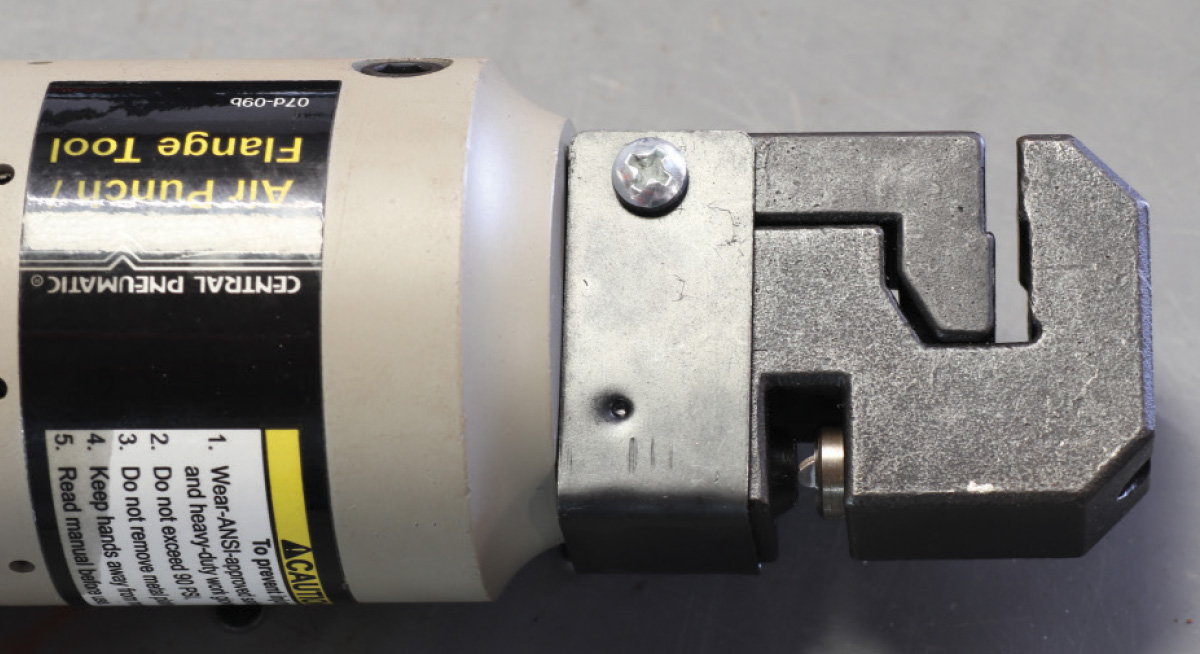
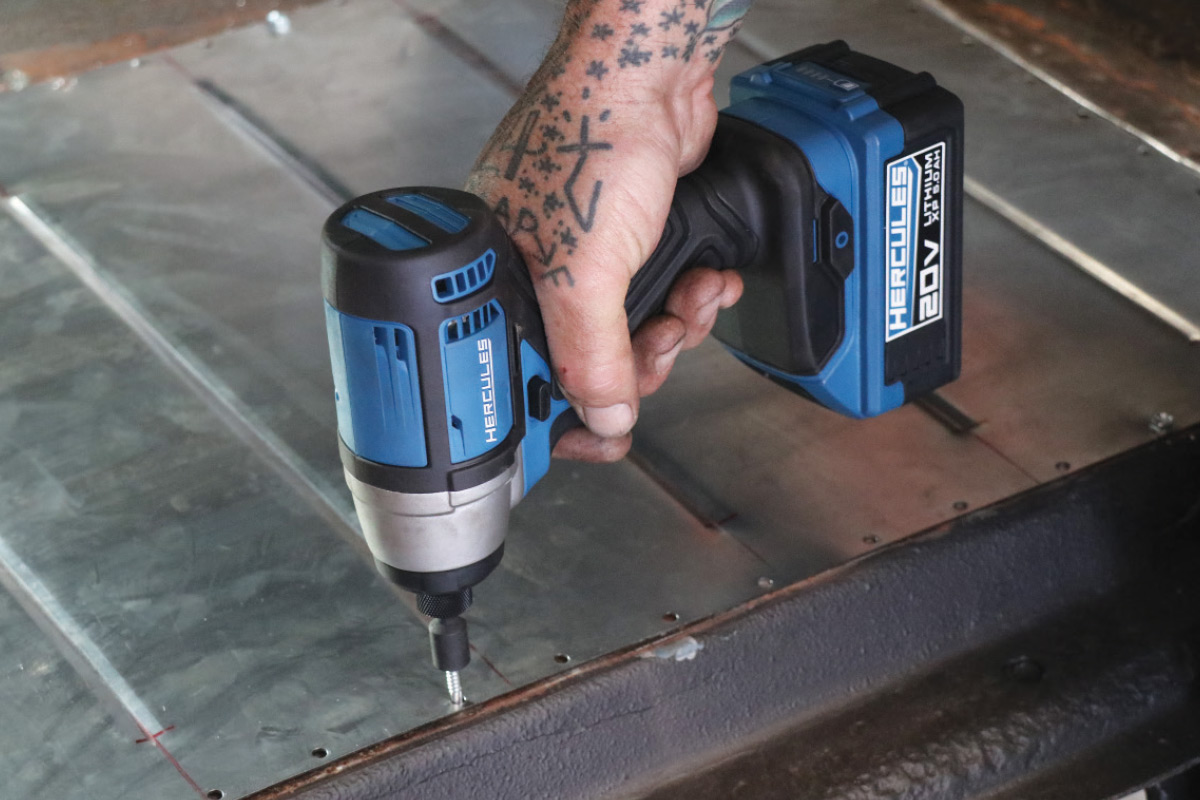
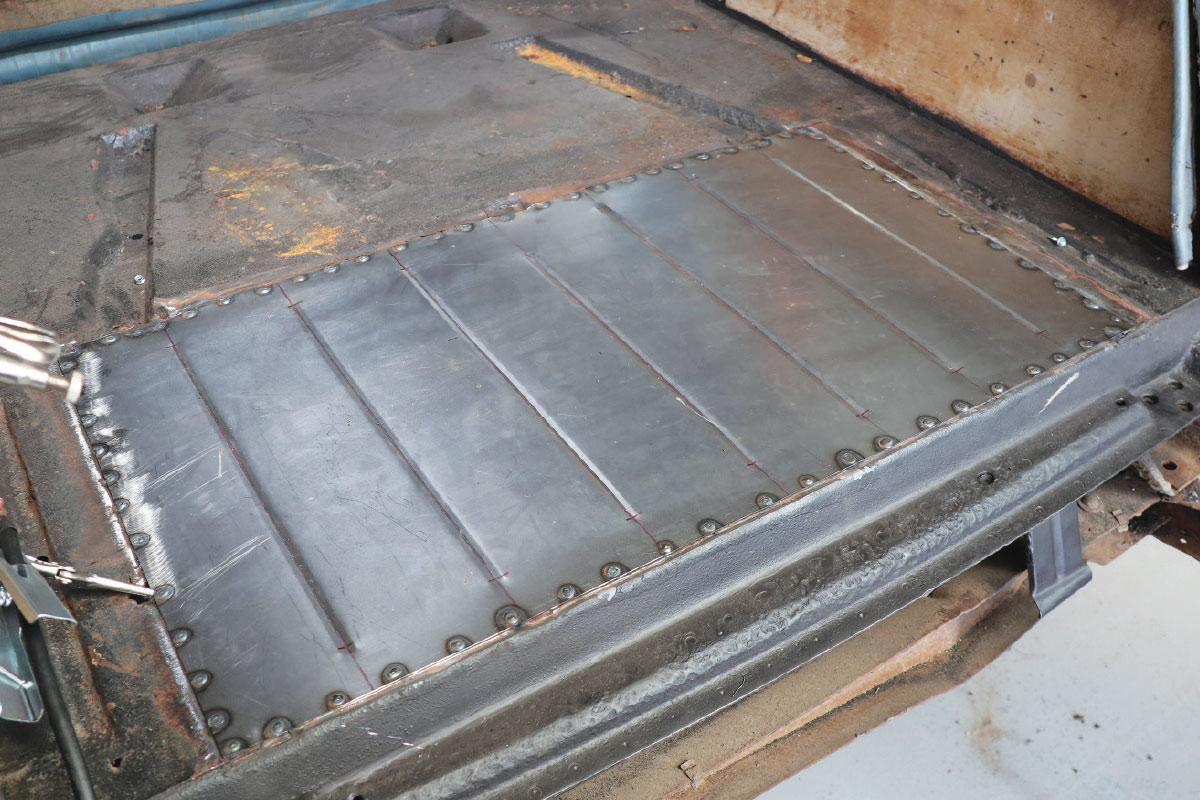
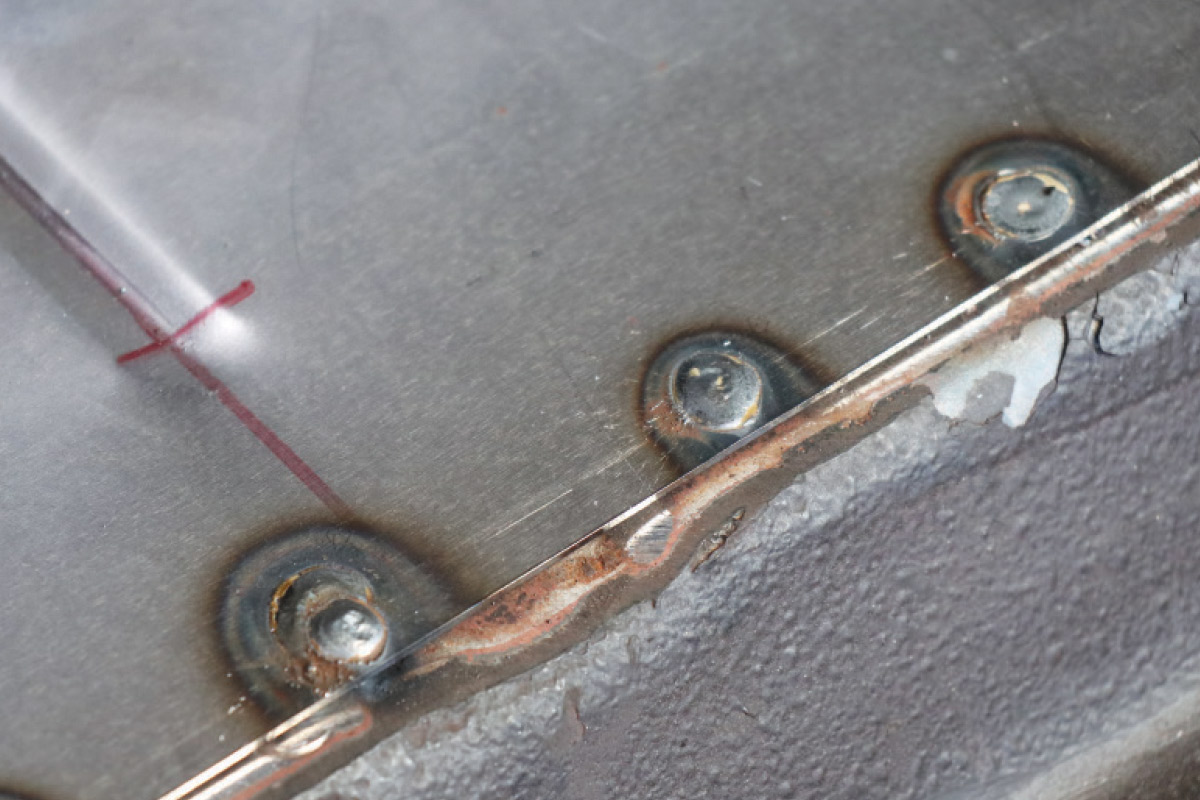
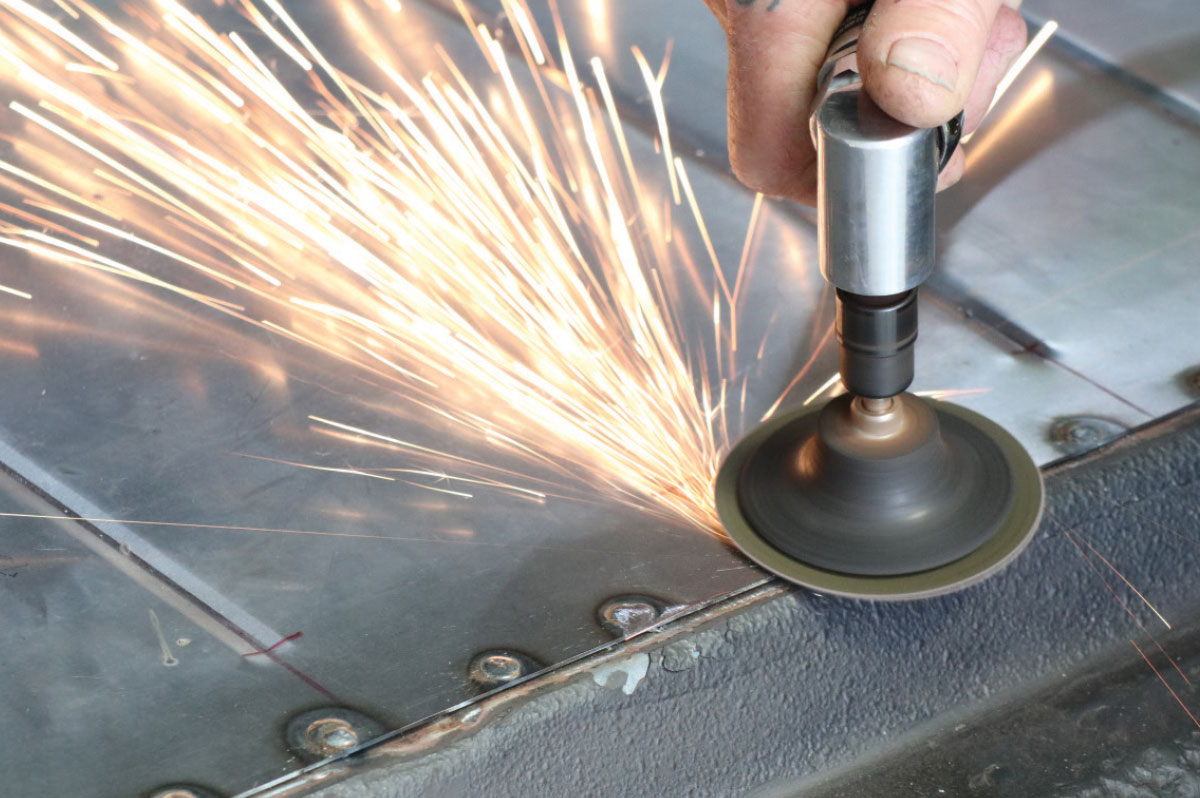
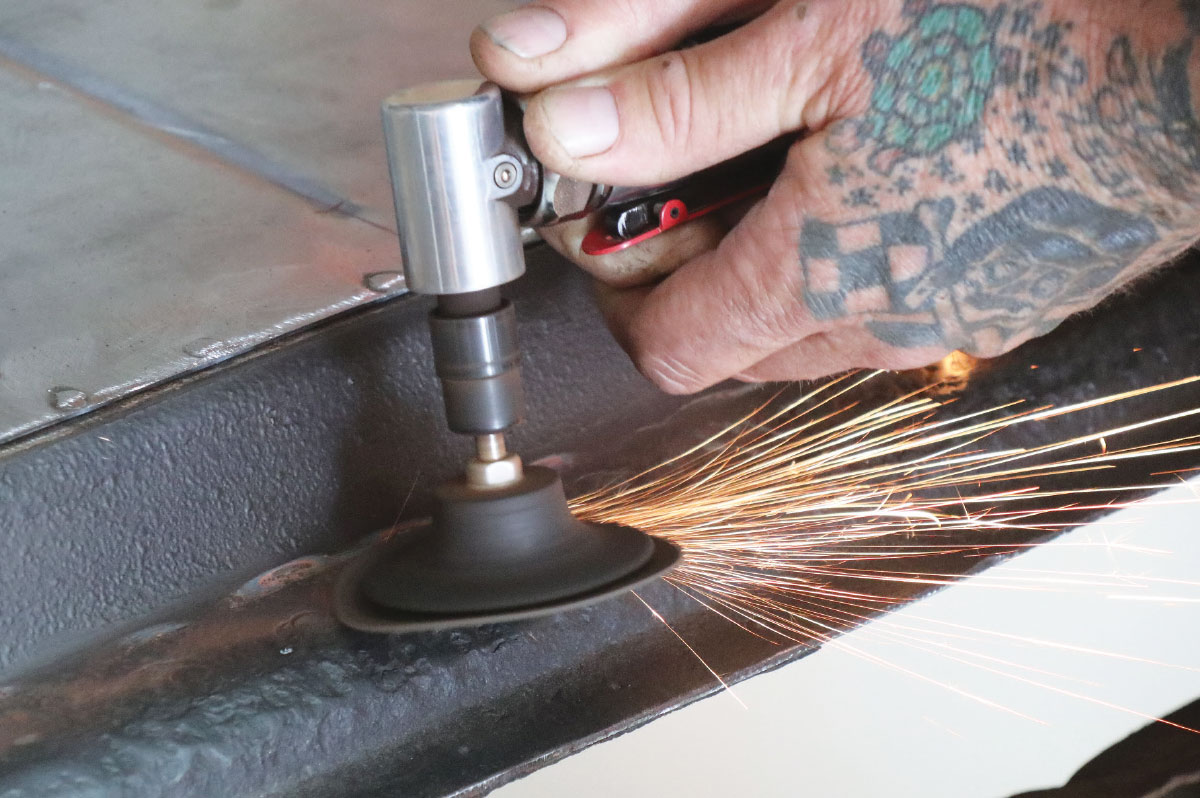
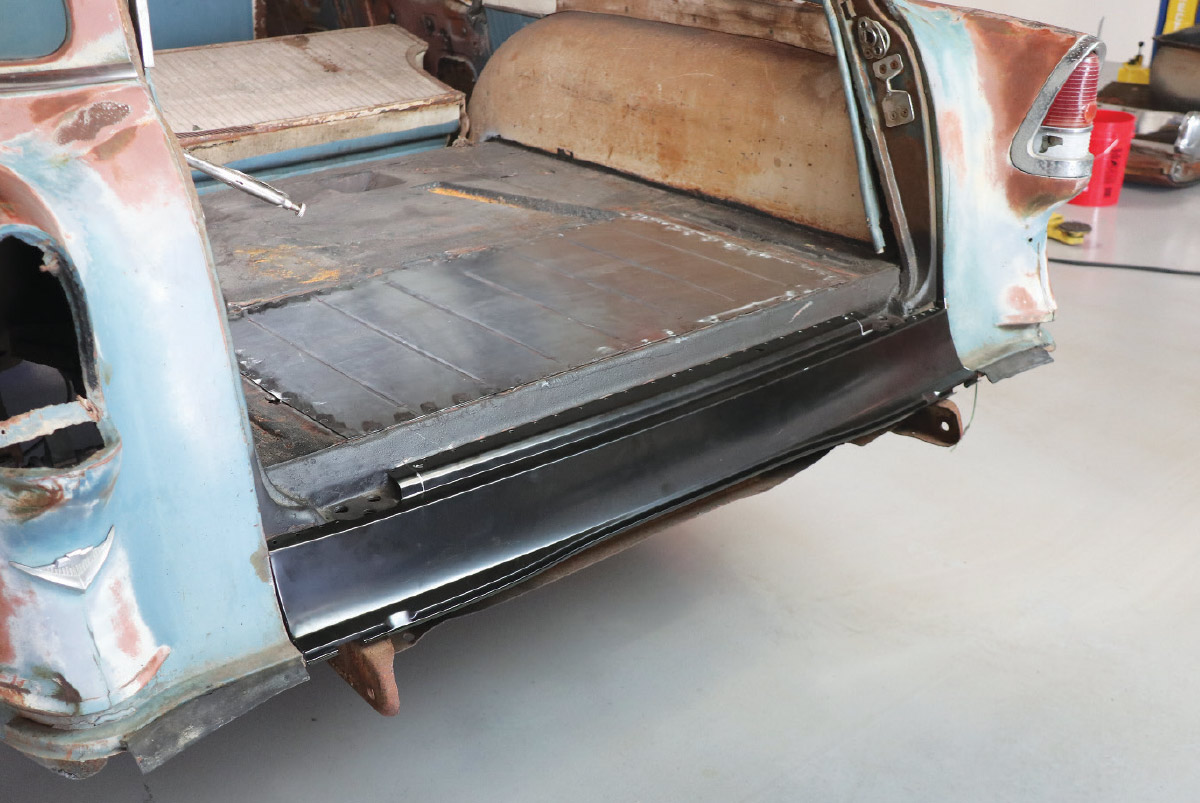
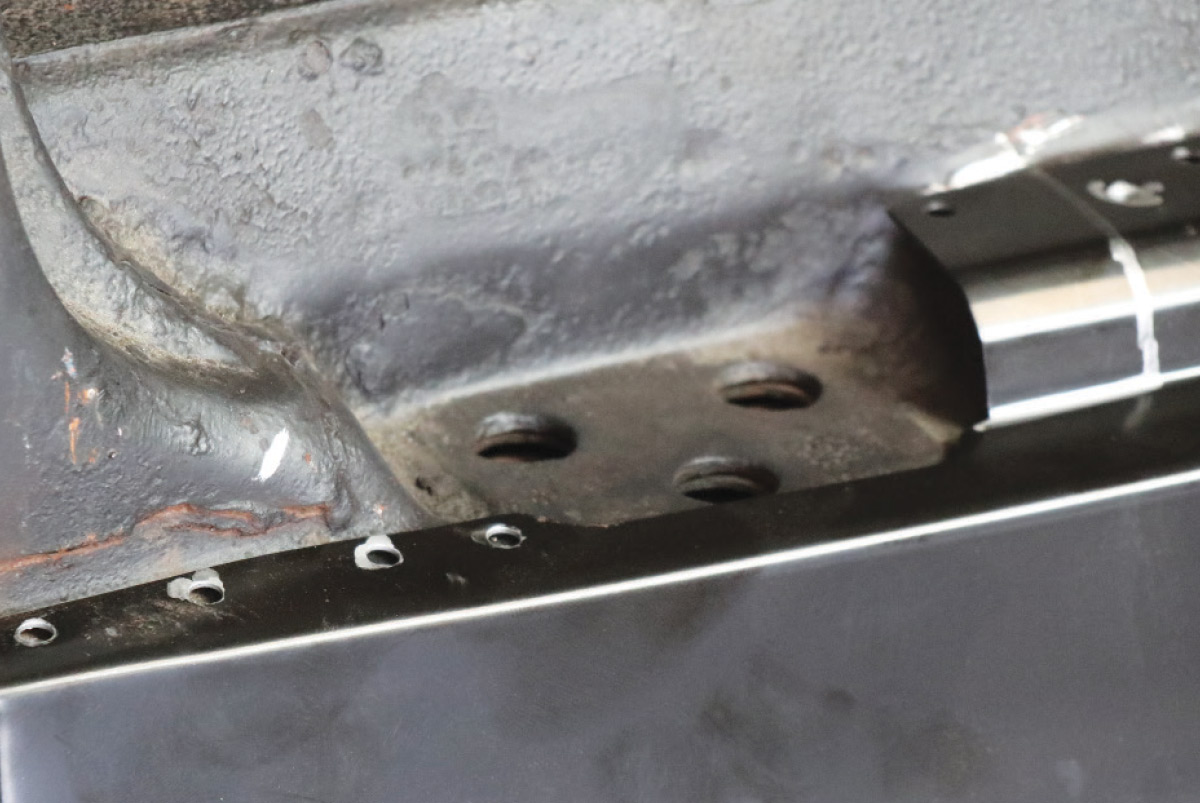
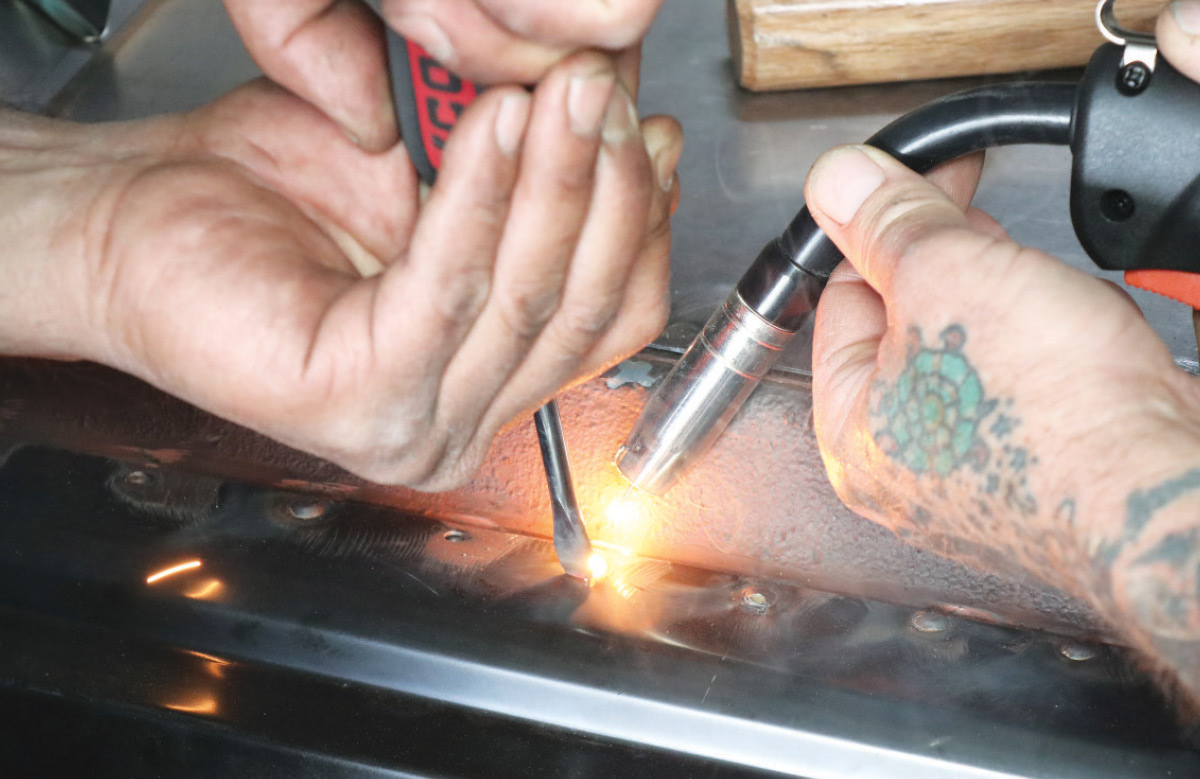
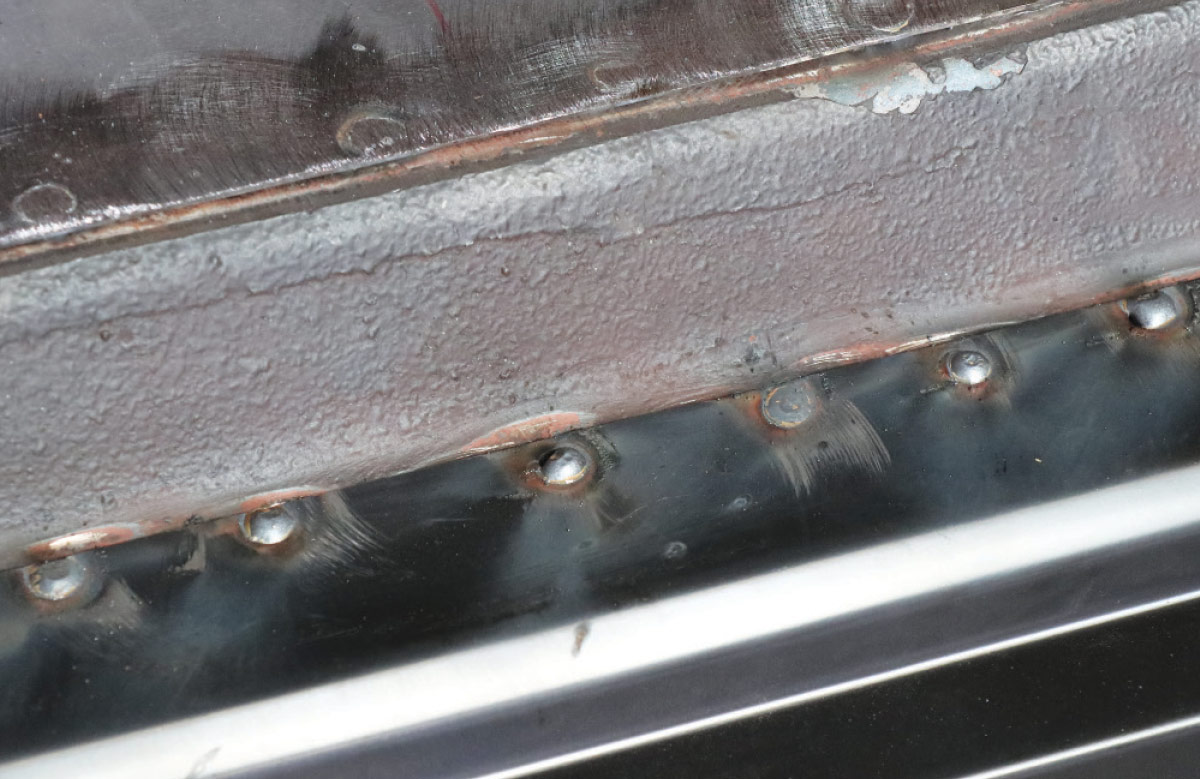
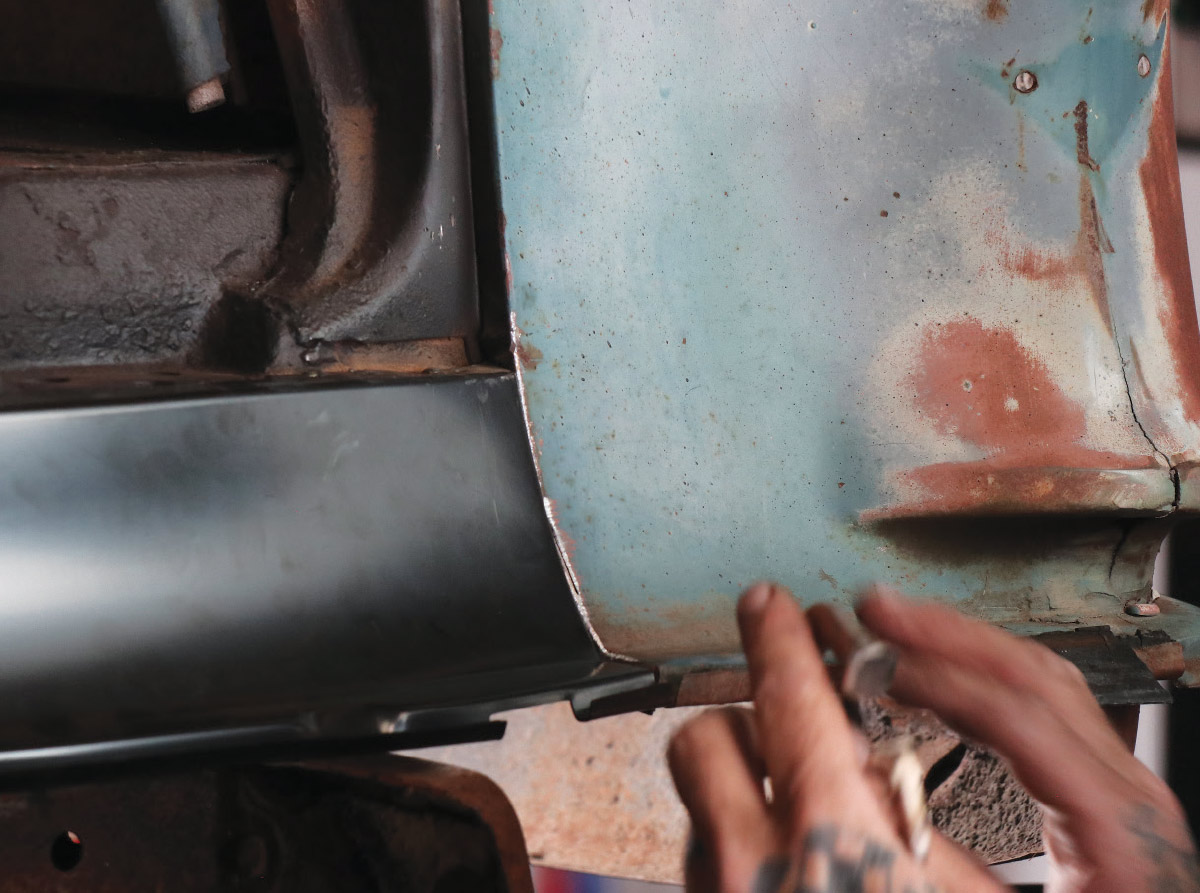
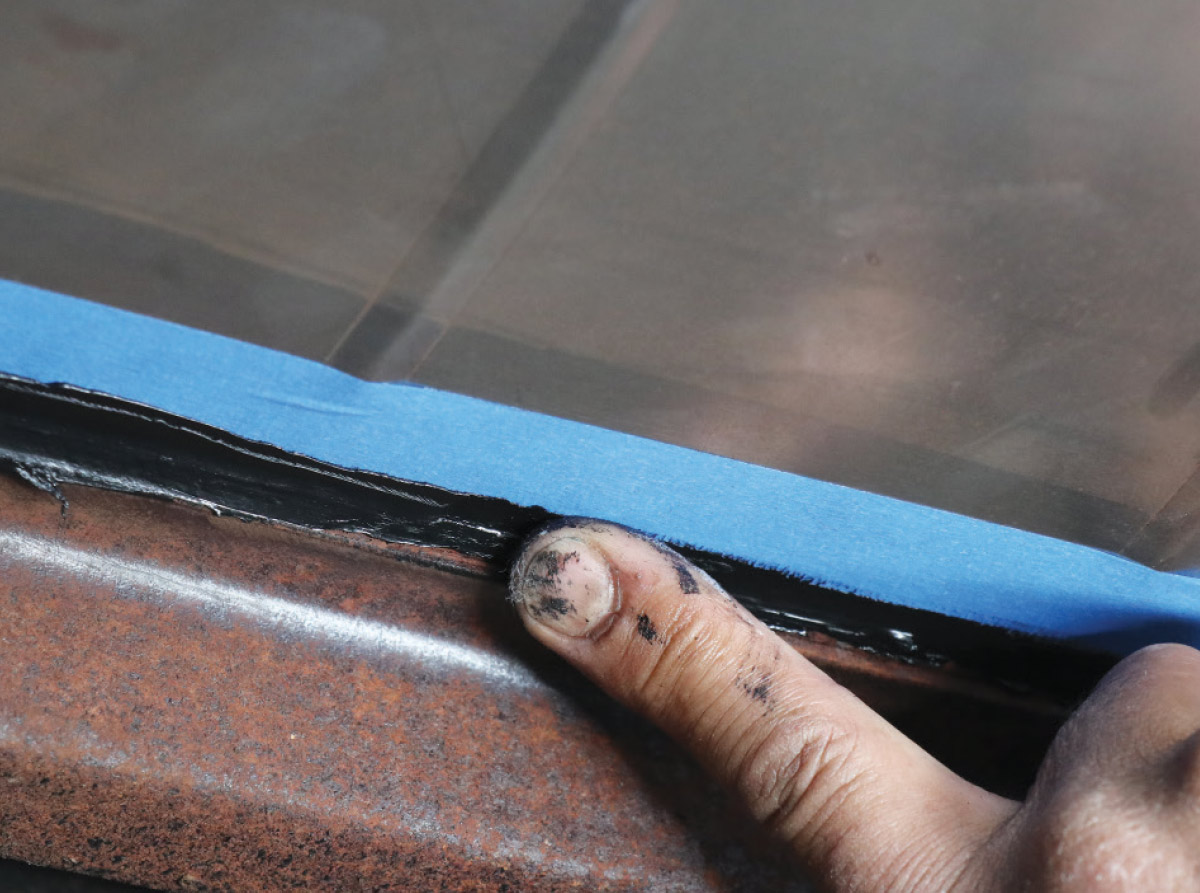
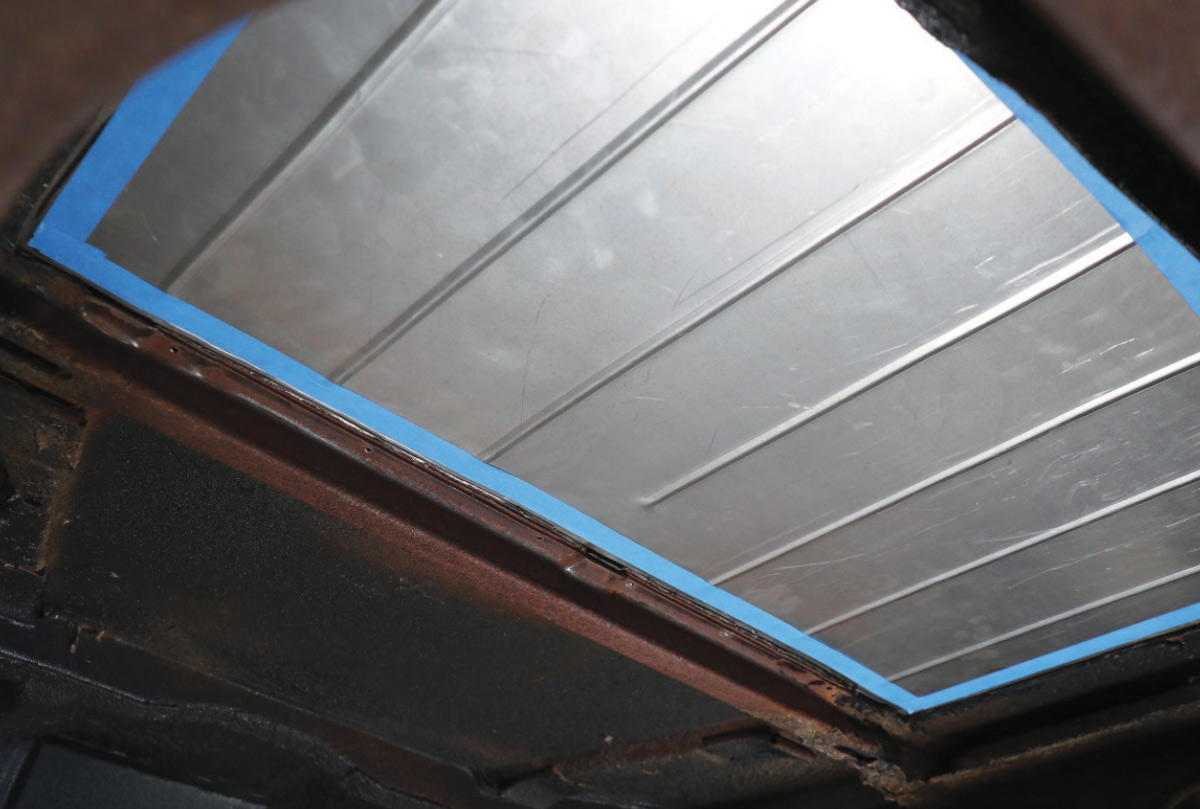
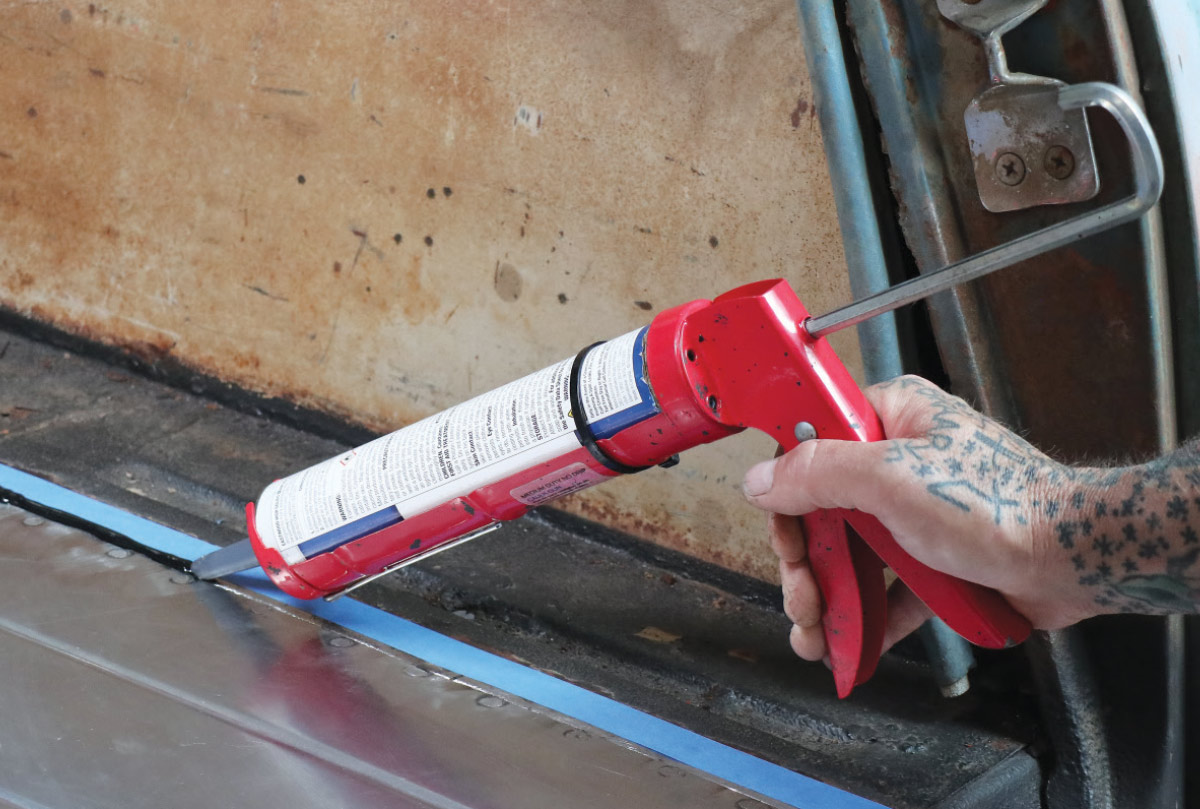
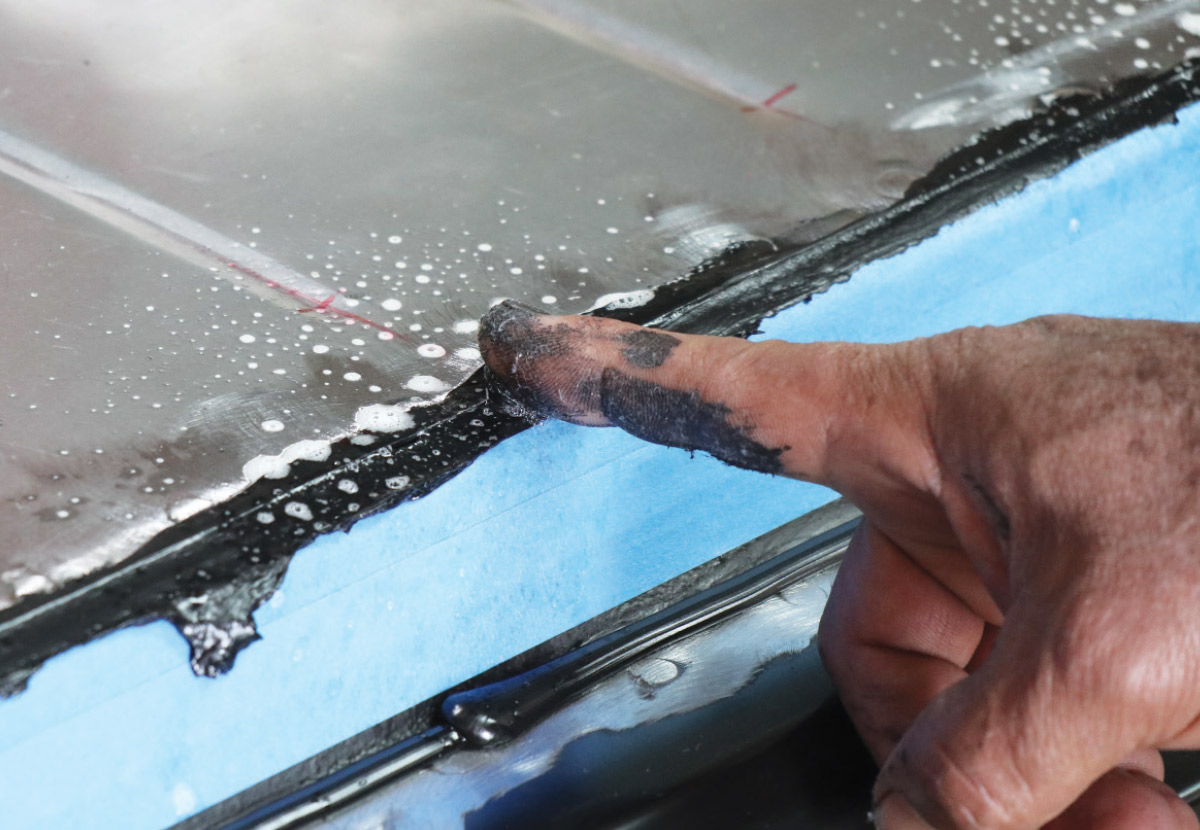
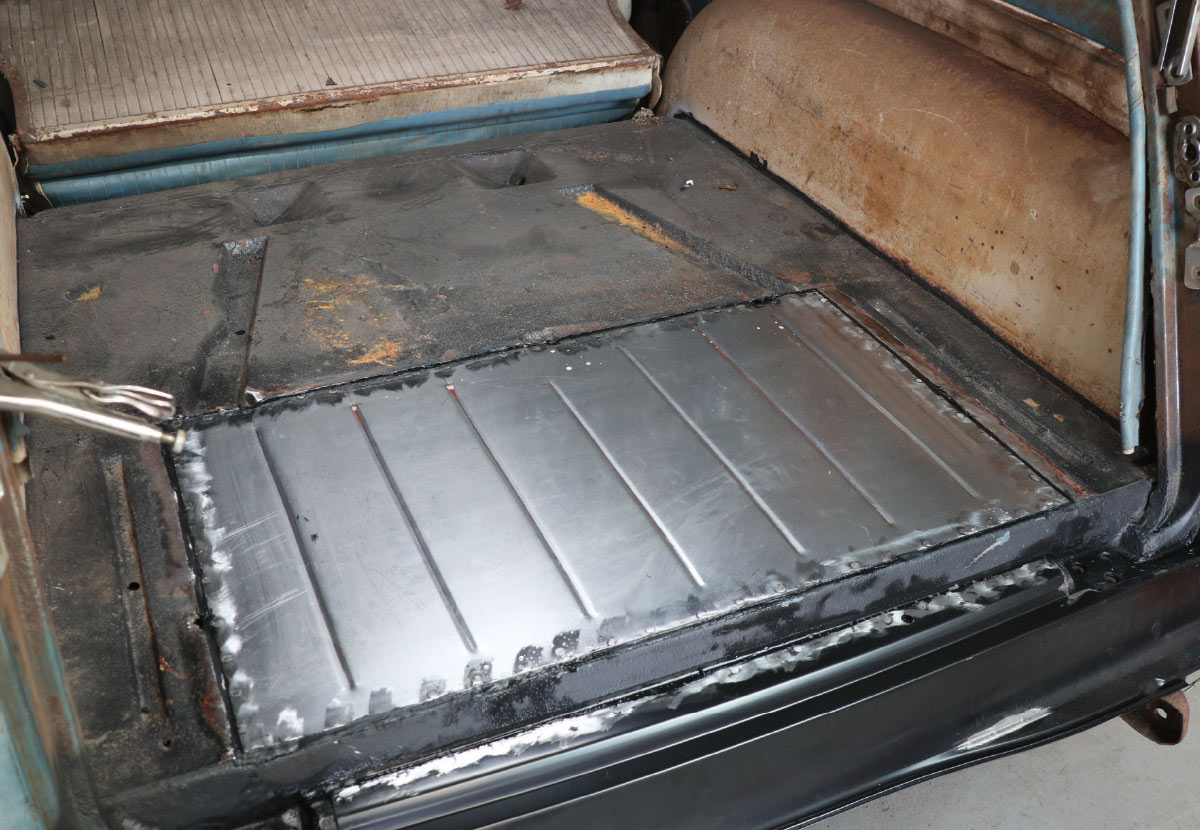
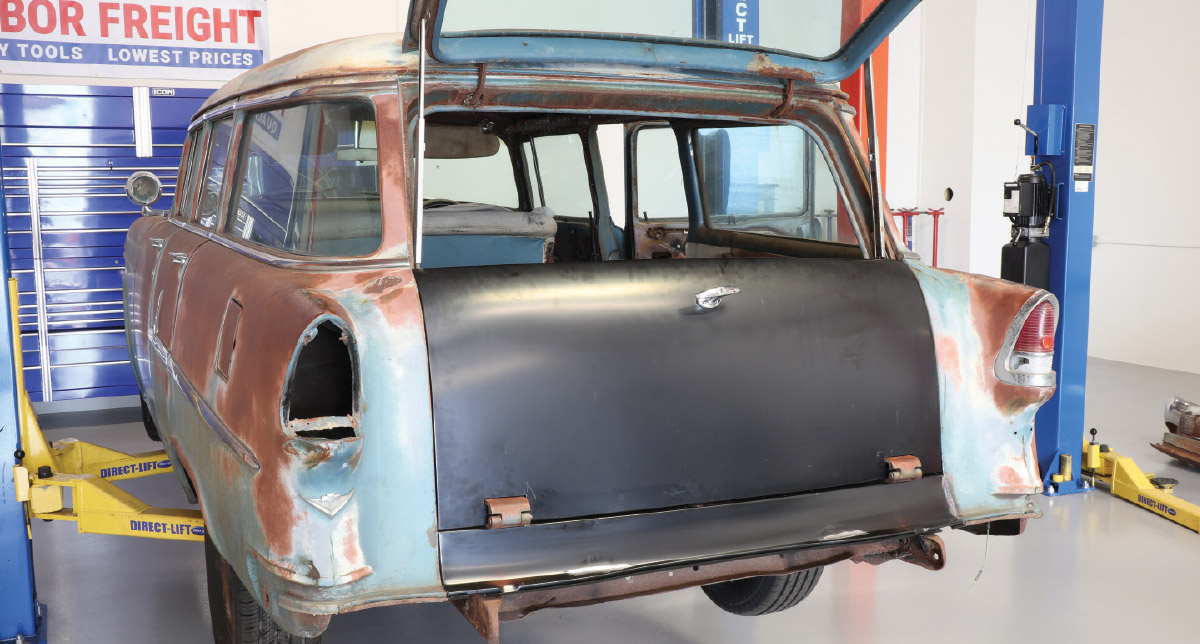
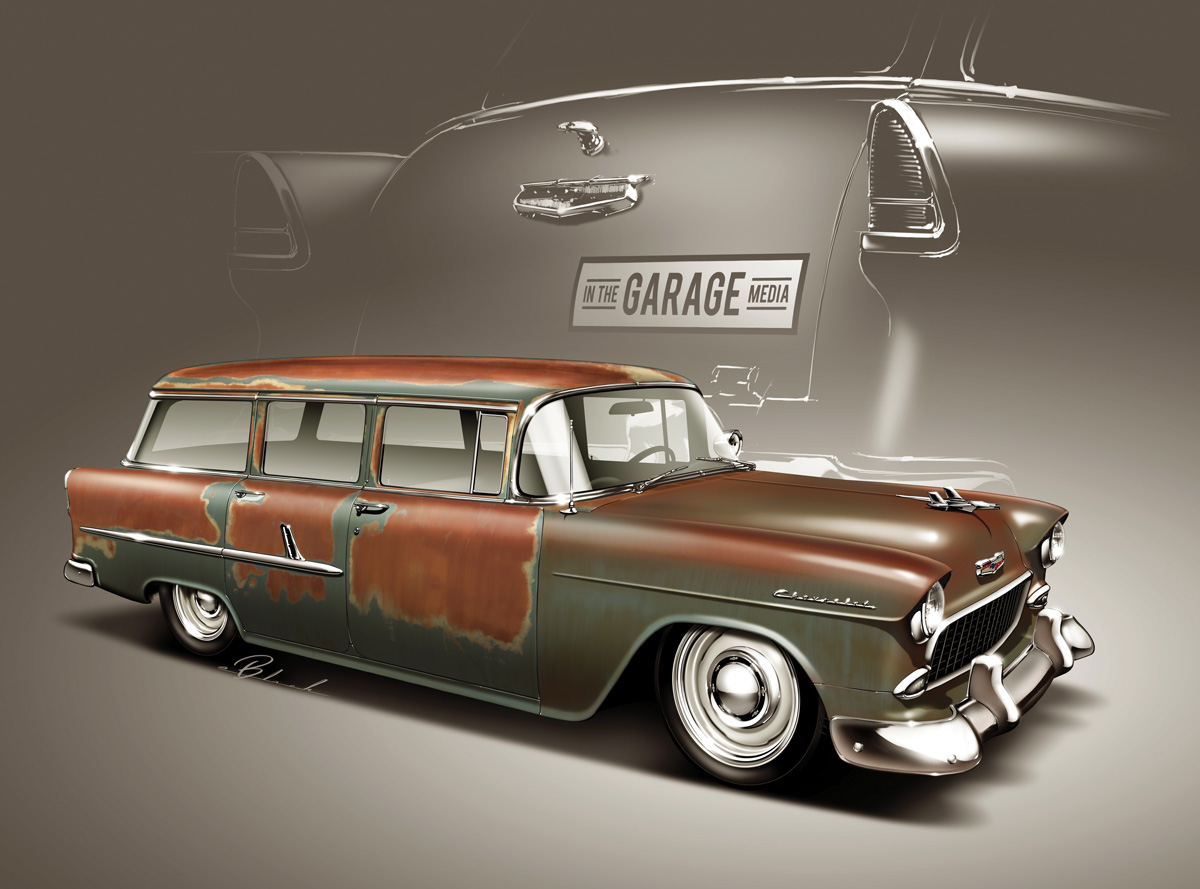
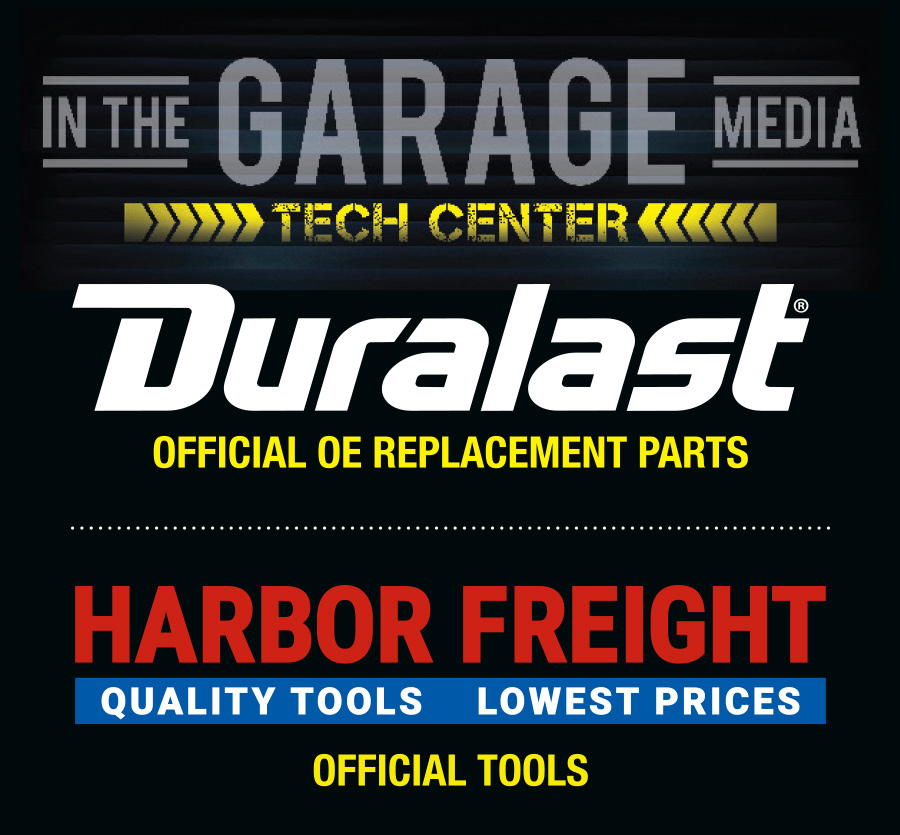

Real Deal Steel
(407) 585-1957
realdealsteel.com