Modern Rodding TECH
InTheGarageMedia.com
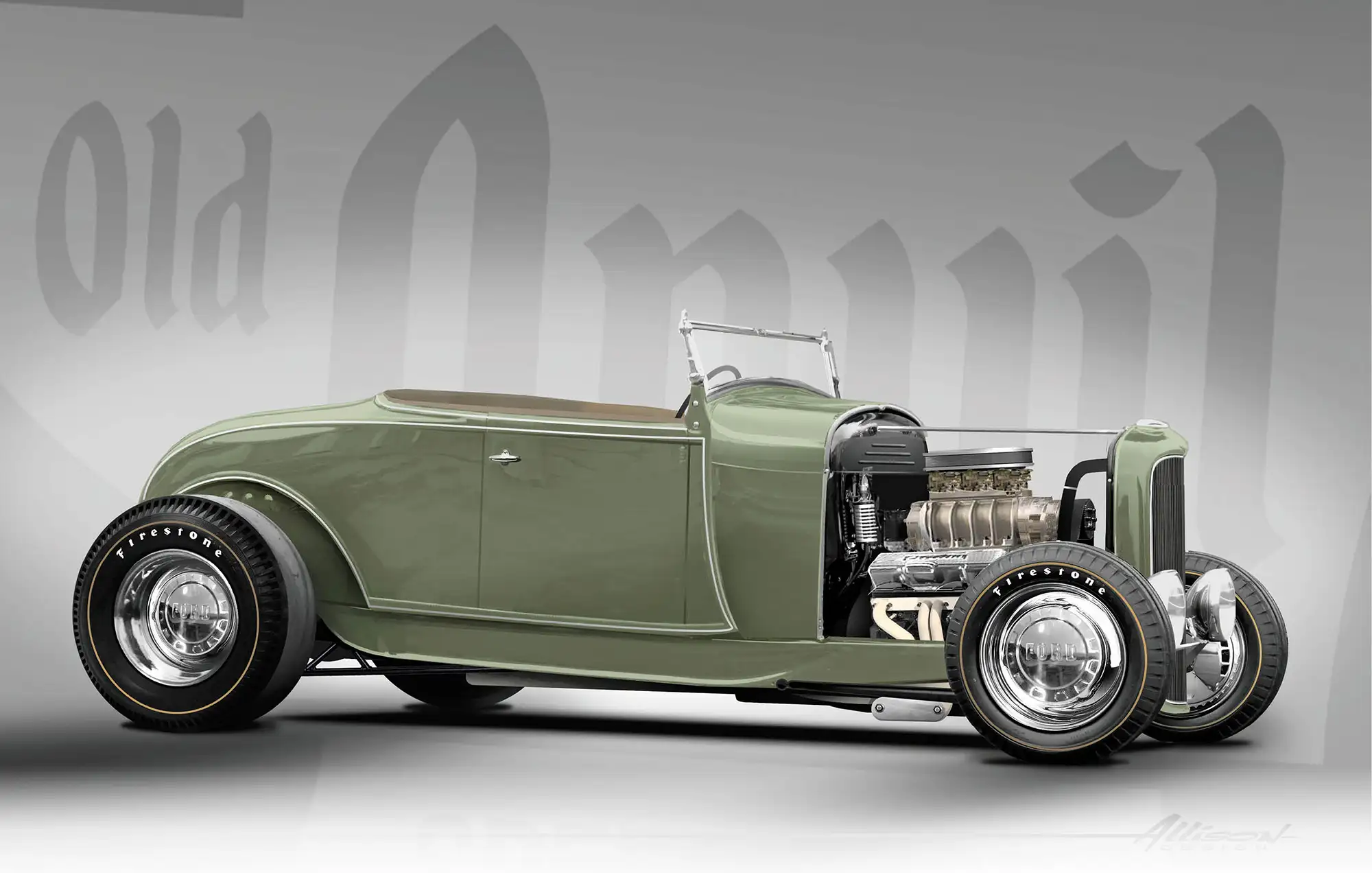

ver the years Jason Scudellari has built several muscle cars and classic trucks and he often displays his talents in Modern Rodding technical stories. But despite his lengthy involvement in most things hot rod, he’s never built a traditional roadster of his own—until now.
When it comes to hot rods, few are more traditional than what is often described as an A/V-8, a Model A Ford body on a ’32 Ford frame—in this case the body is from Brookville and the frame is from Speedway Motors (PN 91657007). This amalgamation does require some tweaking to make the two come together, in this case the necessary modifications to the shape of the framerails were made by Old Anvil Speed Shop. In addition, they reinforced the framerails with Speedway’s boxing plates (PN 9108969) and weld-in tubular crossmember kit (PN 91657029). All of this was documented by Ryan Manson in the Sept. ’23 issue of Modern Rodding.
With the necessary changes to the frame wrapped up, Scudellari turned his attention to the suspension. Up front is a laundry list of traditional suspension components from Speedway, including a dropped I-beam axle, reversed eye spring, and ’48-52 Ford F-1–style shock brackets. Holding the axle in place is a pair of Speedway (PN 91645127) split wishbones made from 12-gauge steel with forged ends—in the rear are 11/16-18 threaded bungs (Ford tie-rod end size). The bolt-on steering arms are Speedway 3-3/4-inch drop (PN 7022756), for use with split radius rods. Also available are 1-3/4 inch dropped arms for hairpins and four-bars (PN 7022754).
Another tradition that Scudellari chose to stick with was the use of drum brakes rather than modern discs. The fact is not all drum brakes were created equal, so the decision was made to use the more effective Lincoln self-energizing style that was once a common swap for early Ford brakes. Not surprisingly, original Lincoln brakes are hard to find, but all is not lost as reproductions are offered by Speedway. Several variations of these brake upgrades are offered that can be used with ’37-41 or ’42-48 Ford spindles (’37-41 spindles have a round flange; the ’42-48 spindle have a square backing plate mounting flange and use longer kingpins). When using original spindles up some material may need to be removed on the top of the spindle. However, to make things easy Speedway now offers new, modified, ’37- to ’41–style spindles that are ready-to-use (PN 910-3211). Self-energizing rear brake kits are also available for ’37-48 Ford cars and ’37-47 Ford pickups with original rear axles.
There are two basic options when choosing Speedway’s Lincoln-style brakes: they can be had with 12×1.75 or 12×2 shoes. Reproduction 12-inch stock-style drums with 5-on-5.5 bolt circle are available in 1.75- and 2-inch widths—also available are new 2-inch-wide Buick aluminum brake drums. In this case Scudellari opted for the complete brake kit (PN 91604052) that included Buick drums, backing plates, hubs, spindles, kingpins, bearings, and seals.
In the rear a John’s Industries rearend assembly is combined with Speedway’s universal ladder bars, Panhard bar, transverse spring, and Aldan shocks. Rear stopping power is supplied by 10-inch-diameter drum brakes.
The final step in completing the chassis was to have Kings Powder Coating apply the super-smooth semigloss black finish to the framerails. All the suspension components were covered with Cerakote by Cerakote SoCal. This black, thin film ceramic finish provides corrosion abrasion resistance with a unique look. ARP fasteners were used throughout.
Scudellari has proved two things with the construction of his A/V-8: traditional hot rods are still alive and well and they can be built with all new parts. Tradition really is timeless.
Bendix brakes were used on a variety of vehicles, oddly enough Ford chose them from 1939-on for Lincolns, Fords and Mercurys had them from 1949-on. Bendix brakes differ from the Lockheed design in that they are self-energizing, which basically means the brake shoes work together. When Bendix brakes are applied the shorter front shoe contacts the revolving drum and tries to rotate it. That movement is transferred through the adjuster to the longer rear shoe, pushing it into the drum with increased force. Simply put, Bendix brakes generate far more stopping power than the Lockheed design with equivalent hydraulic pressure.
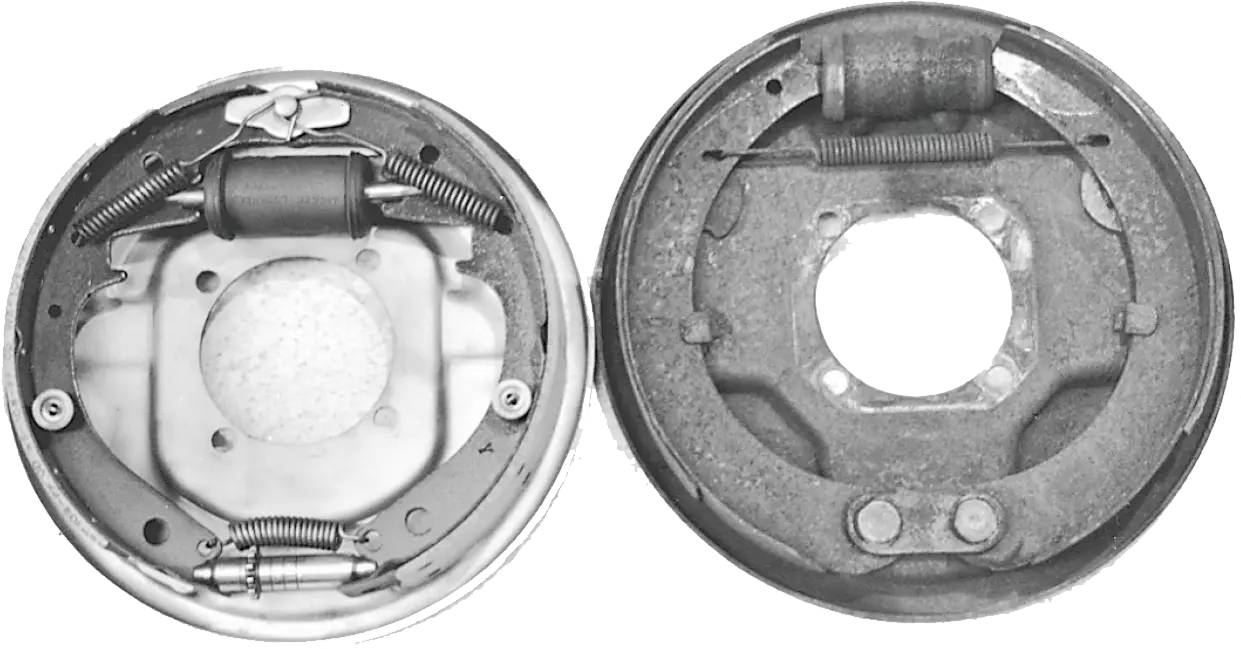
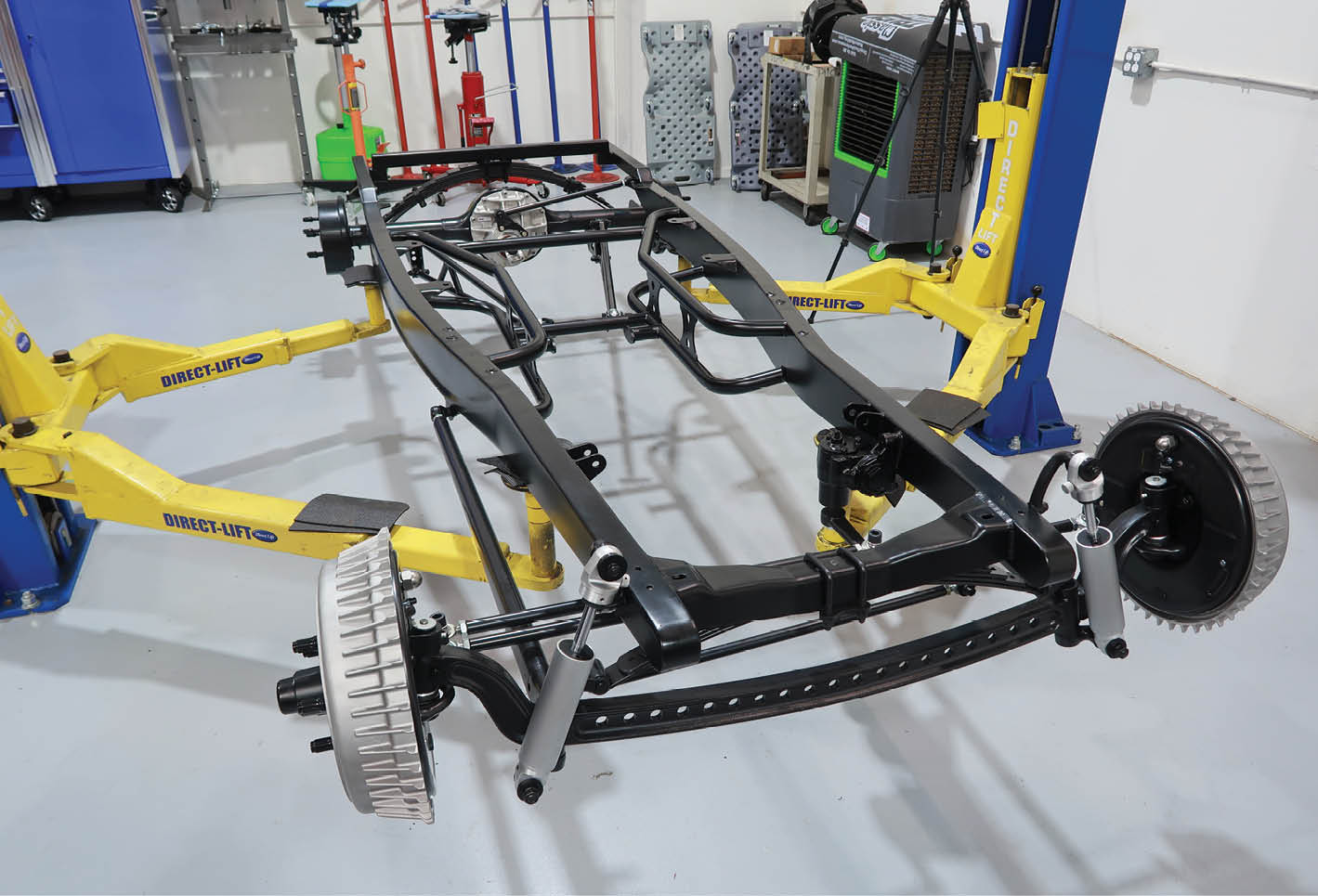
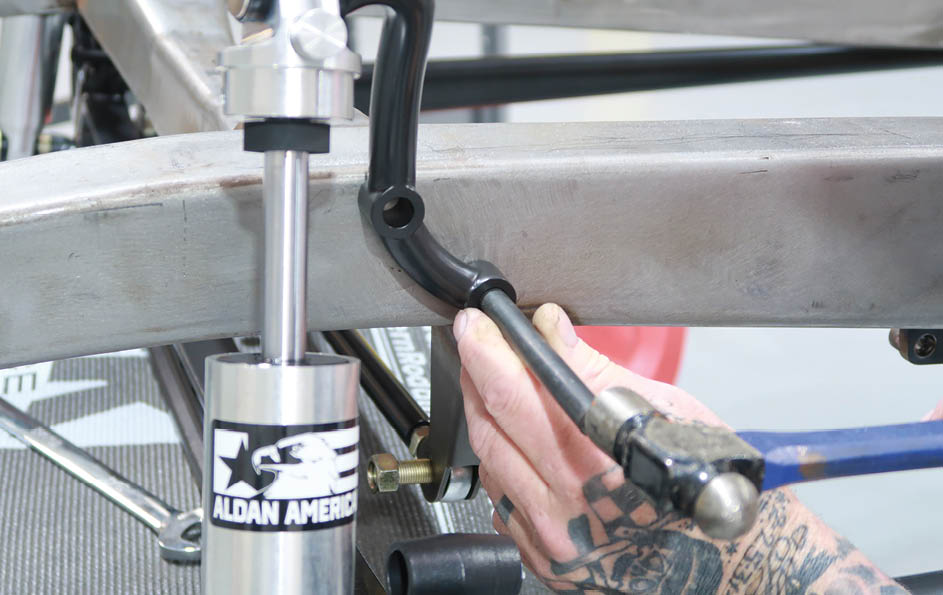
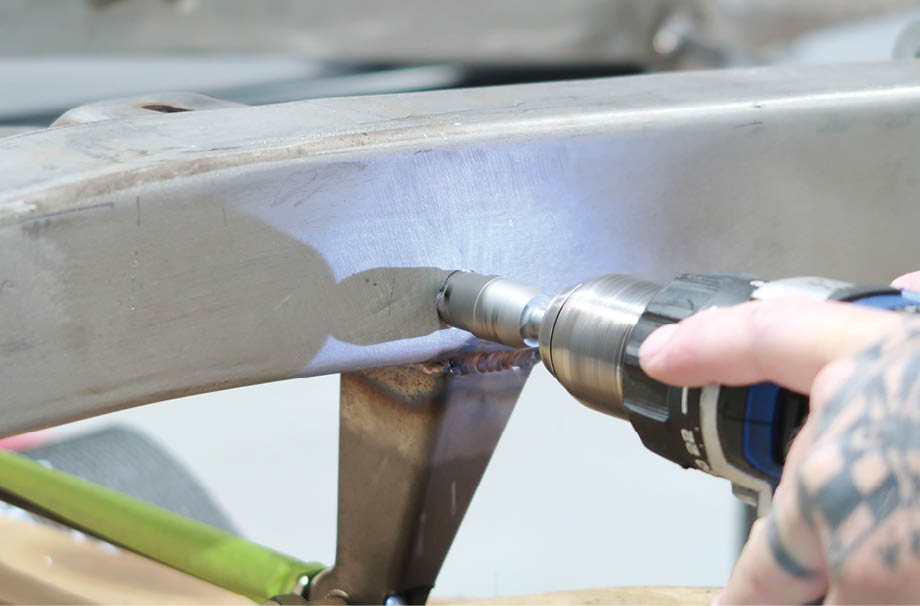

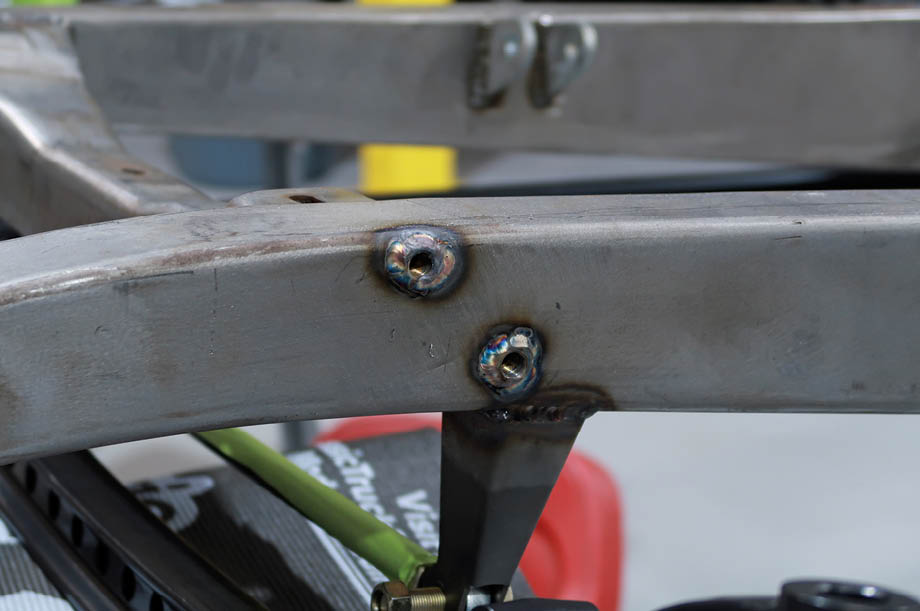
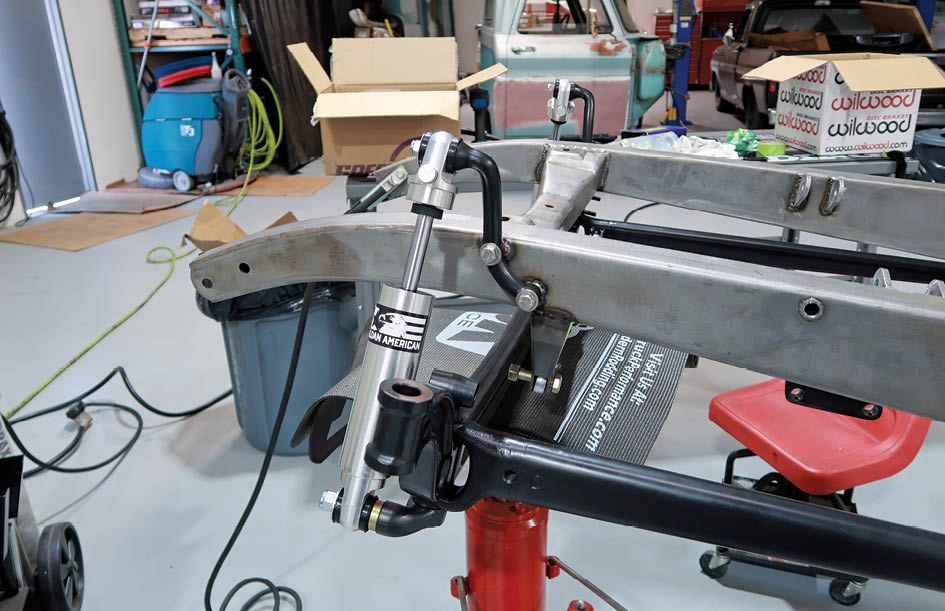


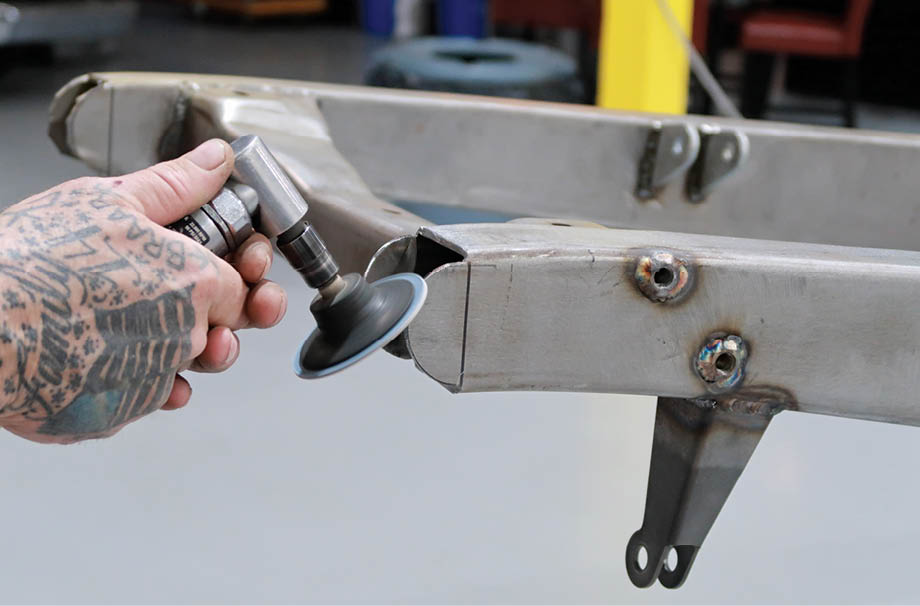
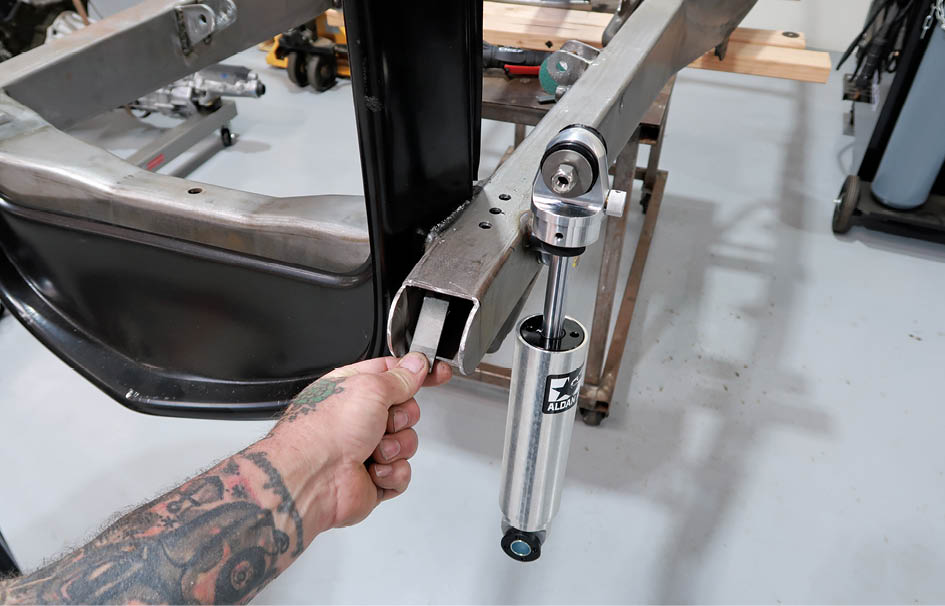
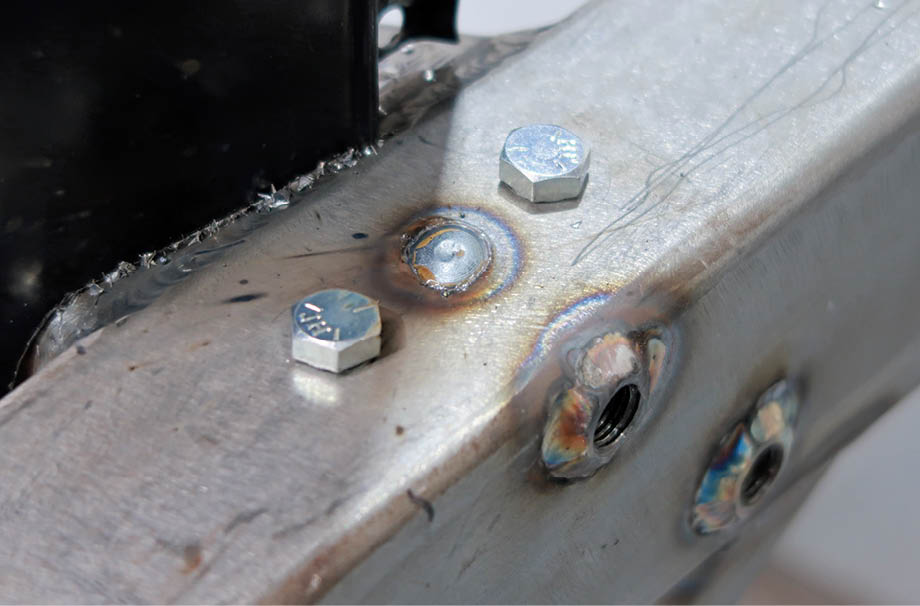
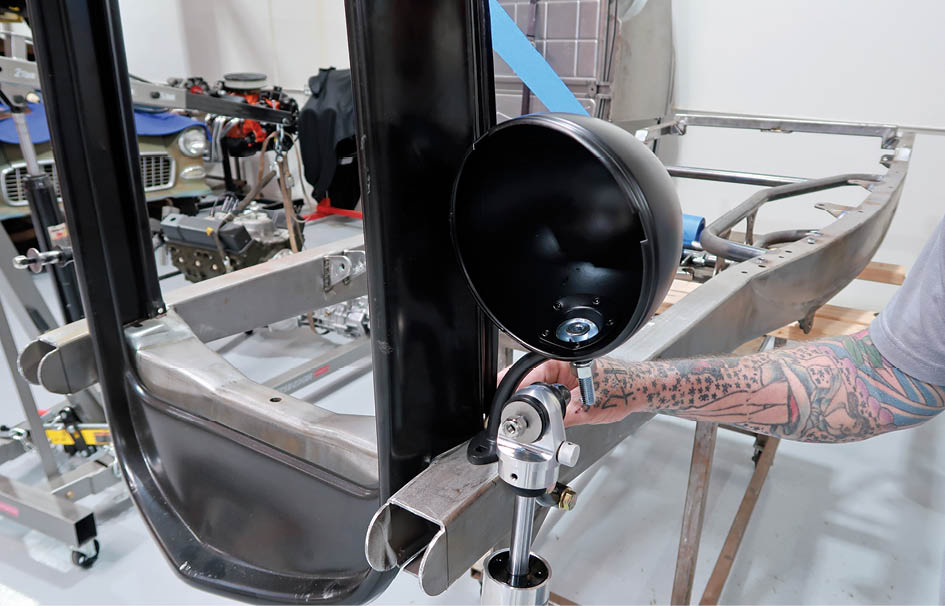

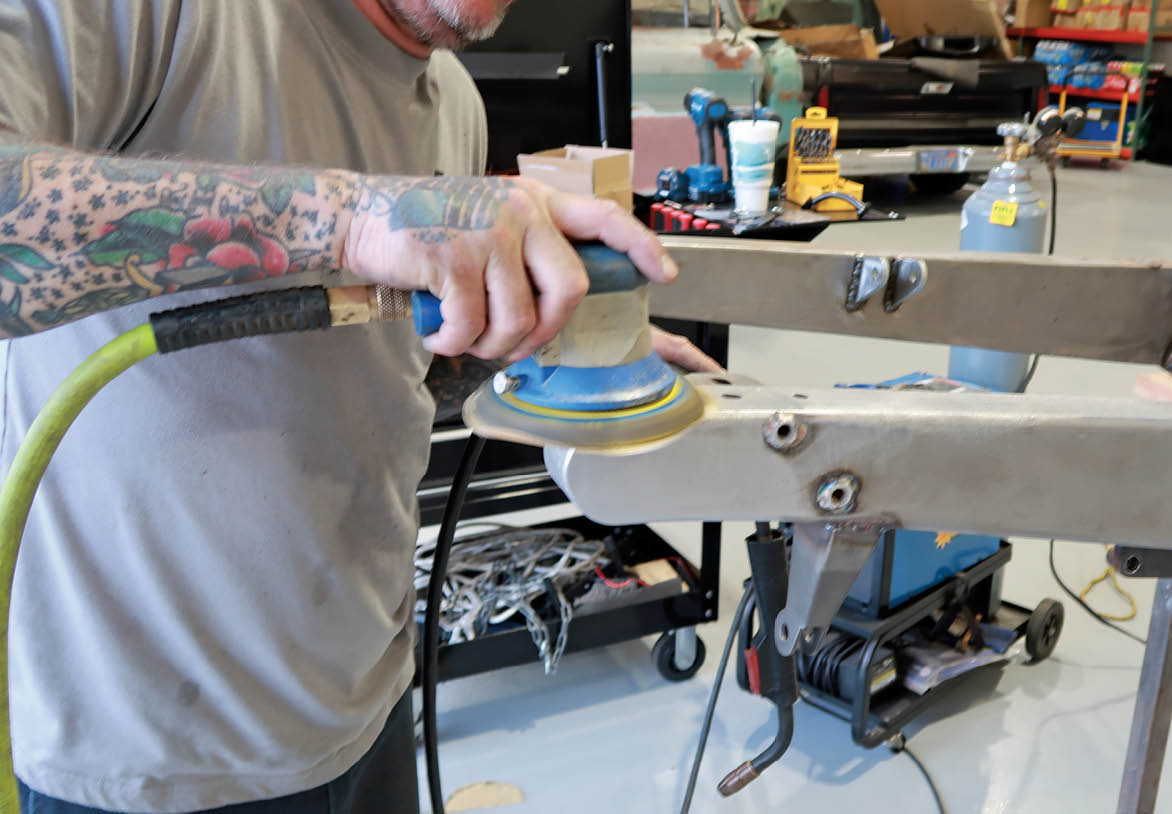
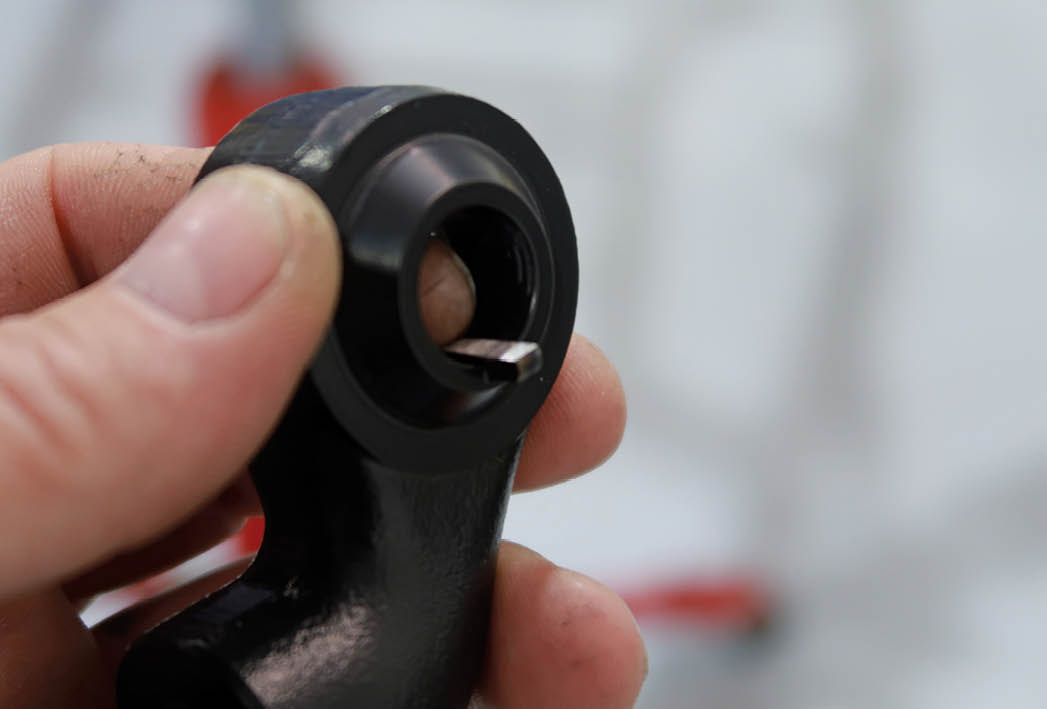
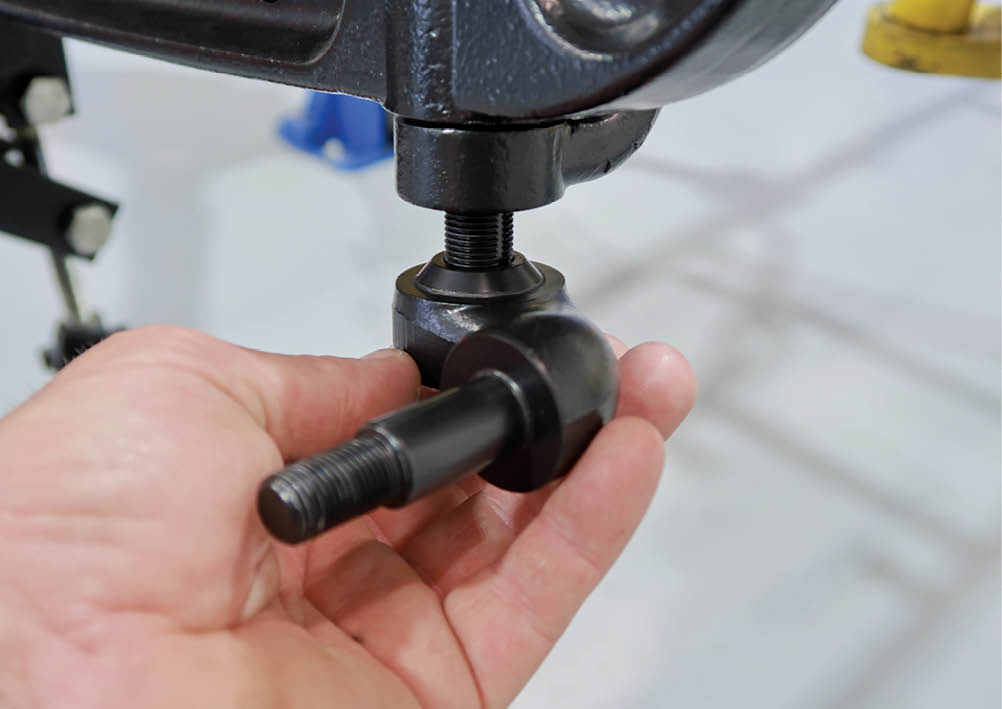

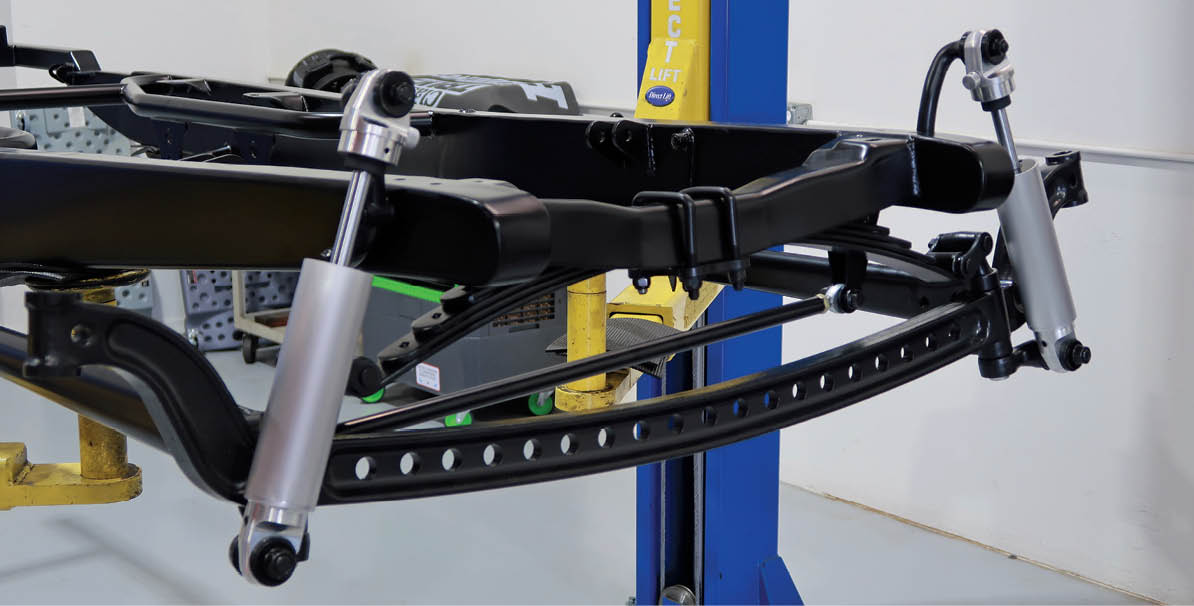
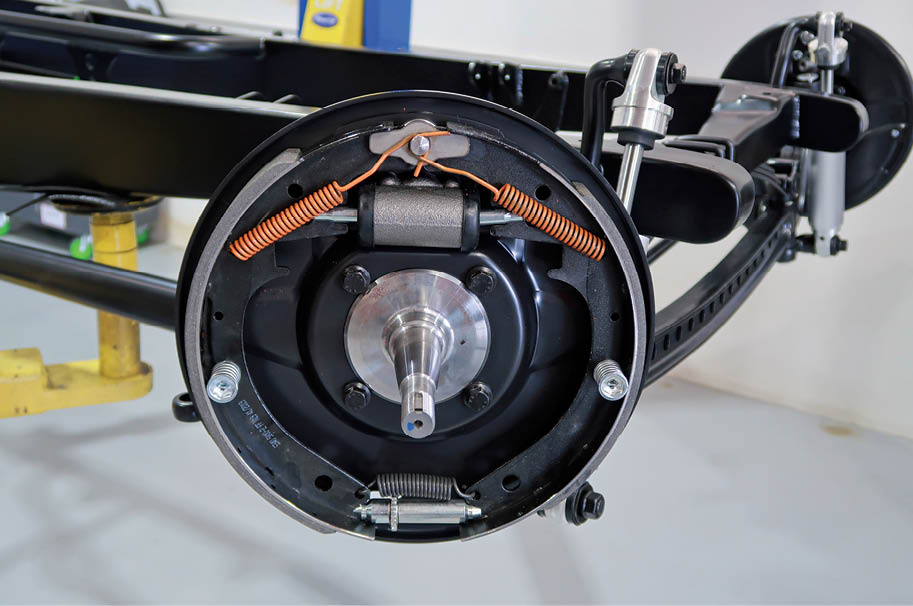

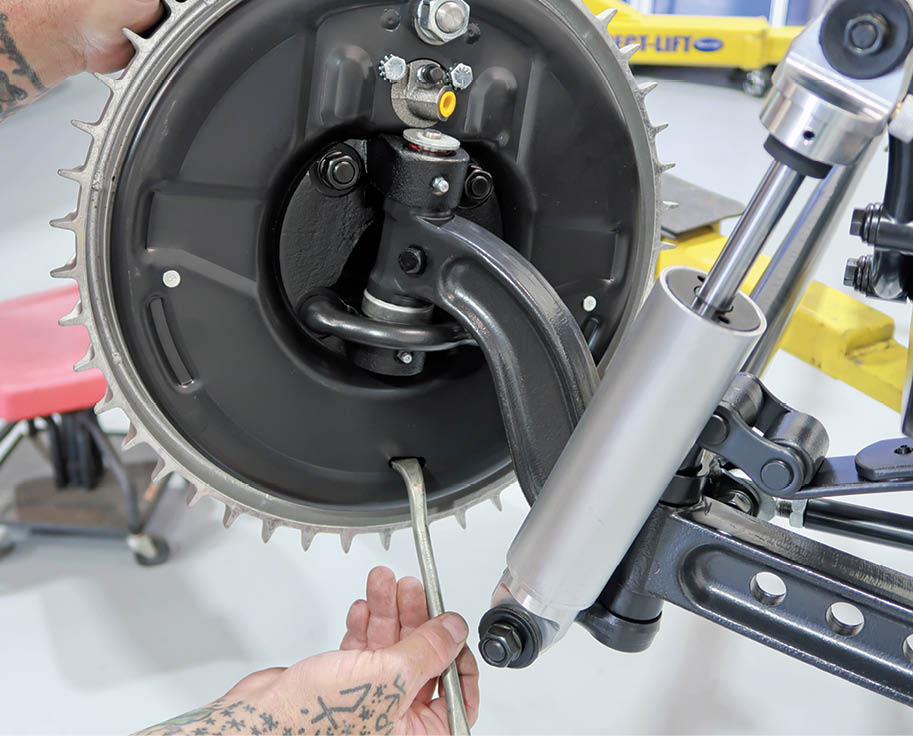

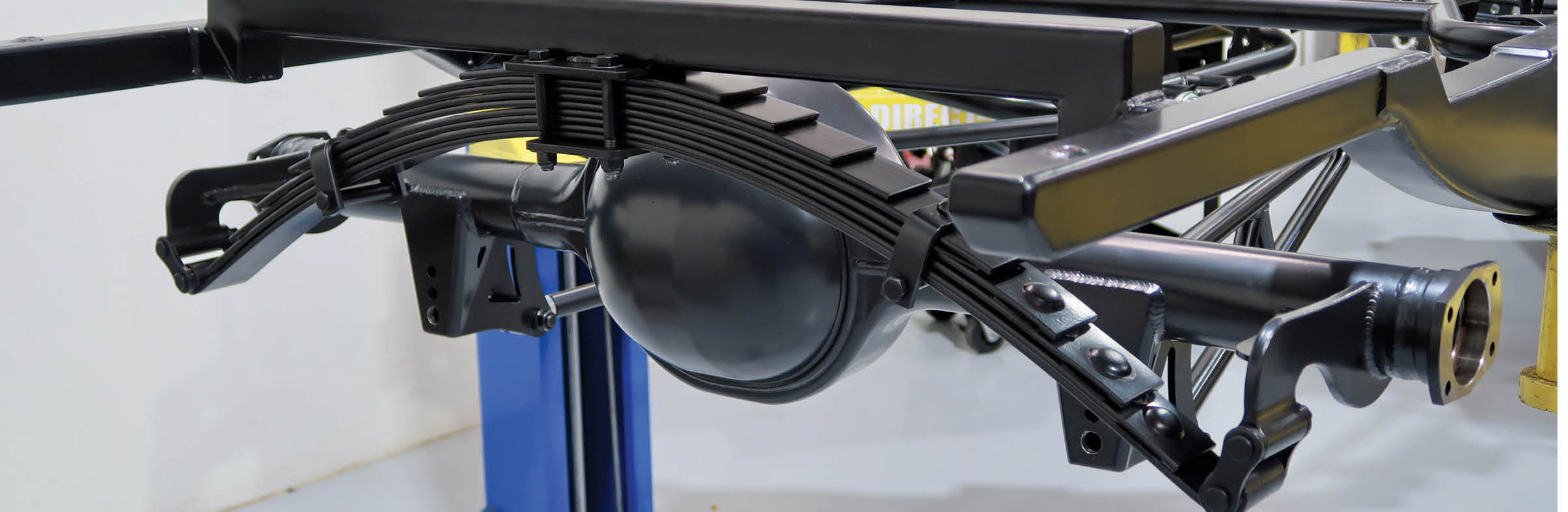

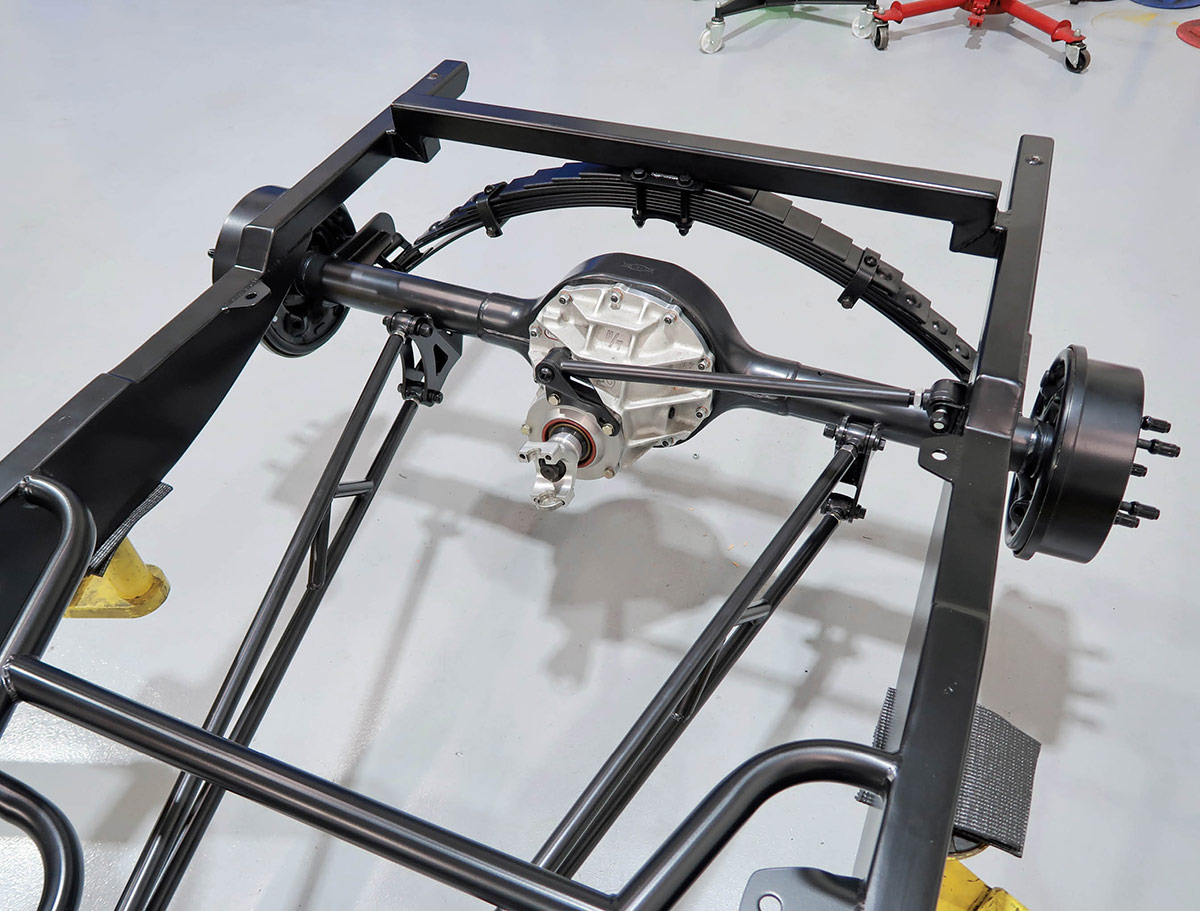
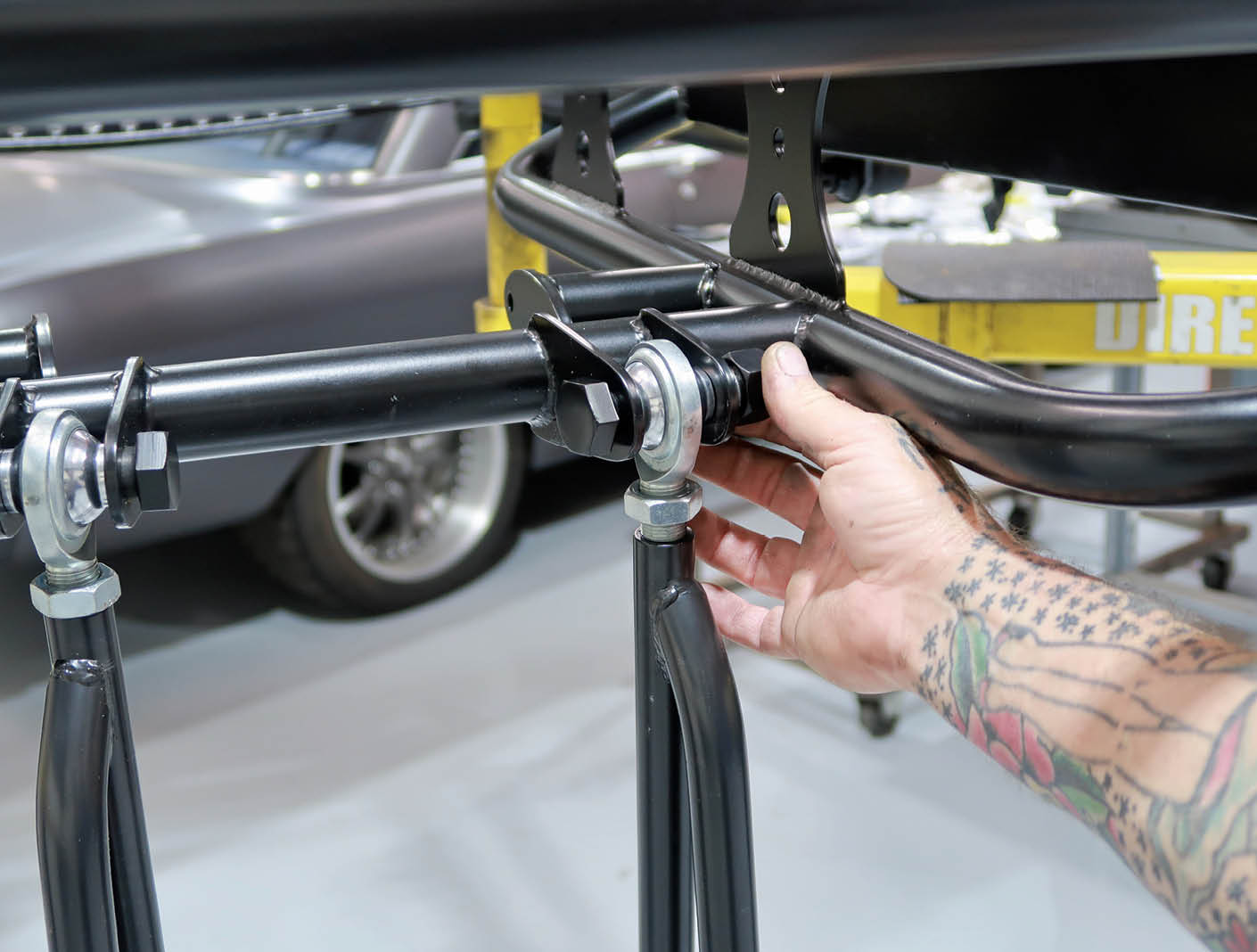

