Modern Rodding TECH
InTheGarageMedia.com
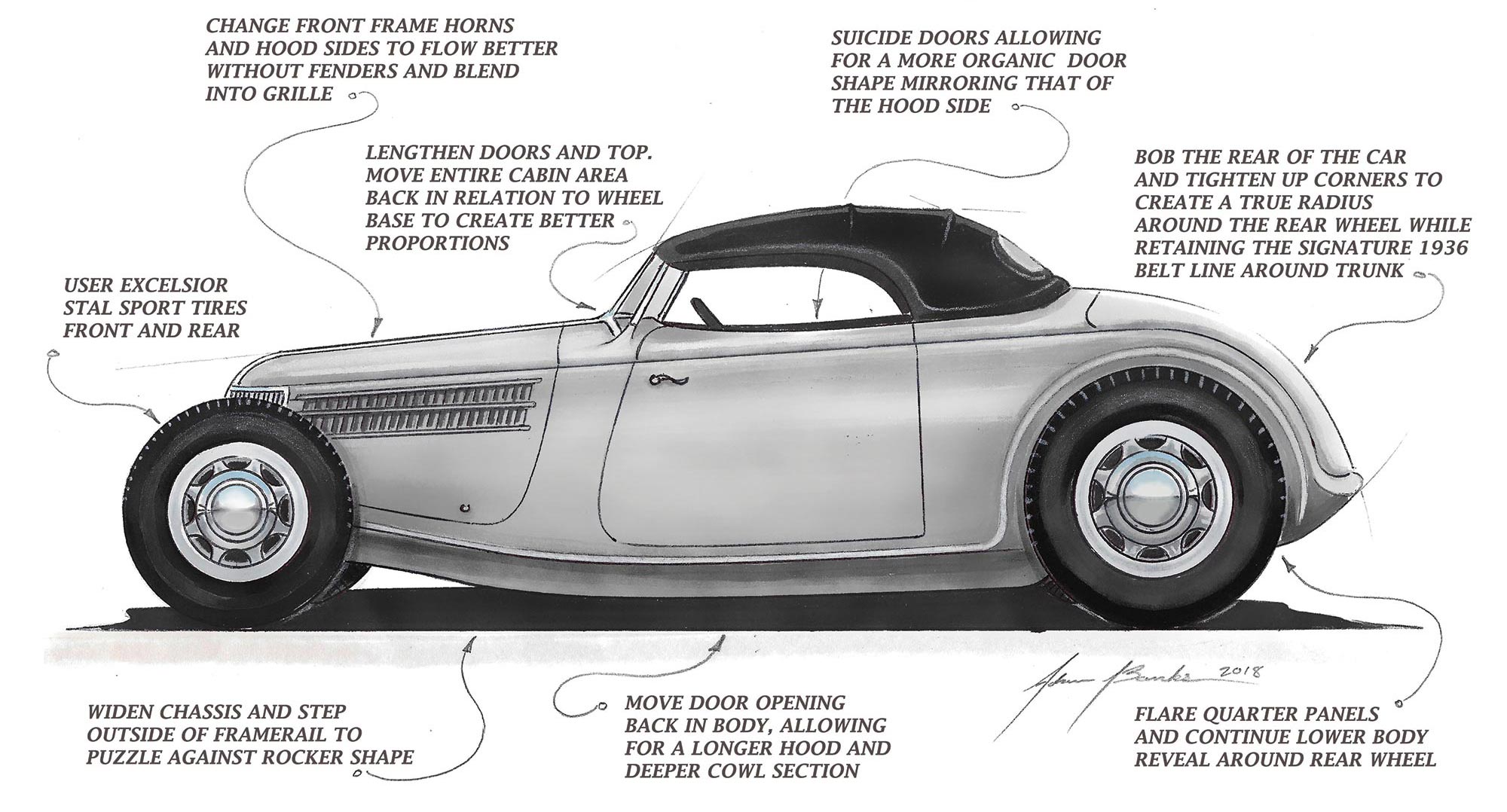

e previously looked at how the crew at Rad Rides by Troy, through the efforts of Adam Banks, scratch-built a body for Ross Myers’ ’36 fenderless roadster. While a new (or modified) body is most often fitted to an existing frame, they took a different approach here: waiting to design the frame until the shape of the body and grille shell were finalized. This allowed them to do an exceptional job of integrating the fit and contours of the two components.
The grille itself was completely scratch-built from steel, and while it retains the “flavor” of a stock ’36 grille, it is sectioned 4-½ inches, and a complete shell has been built from 18-gauge steel to surround the grille. As you’ll see in the photos, this was a massive undertaking. The grille of a car really sets the essence of the build, so this was a component they had to get right.
Since this will be a fenderless car and much of the frame will be visible, they decided to add a “rib” to the bottom of the framerails, somewhat like the detail on a ’32 Ford. Special dies were made for a Pullmax machine to shape this unique detail. This will become one of the many striking features of this cutting-edge project.
Another unusual feature this car has is a removable X-member. This was done to ease the job of painting and detailing every square inch of the chassis to an impeccable level. If you’ve ever tried spraying, blocking, and polishing the paint on an X-member, you can appreciate how beneficial it would be to disassemble these components, allowing much better access to all the nooks and crannies. The X-member was formed as two channels, with a length of ½-inch bar welded to the inner edges. This gives the components additional strength and a more-finished look.
Torq-Set aircraft-grade fasteners are used to hold these components together. Troy has used these on some of the Bonneville cars he has built, and they are made to extremely high standards for both fit and strength.
We think you’ll love seeing all the detailed work being lavished on this car, and you can look forward to many more articles showing the later stages of construction.
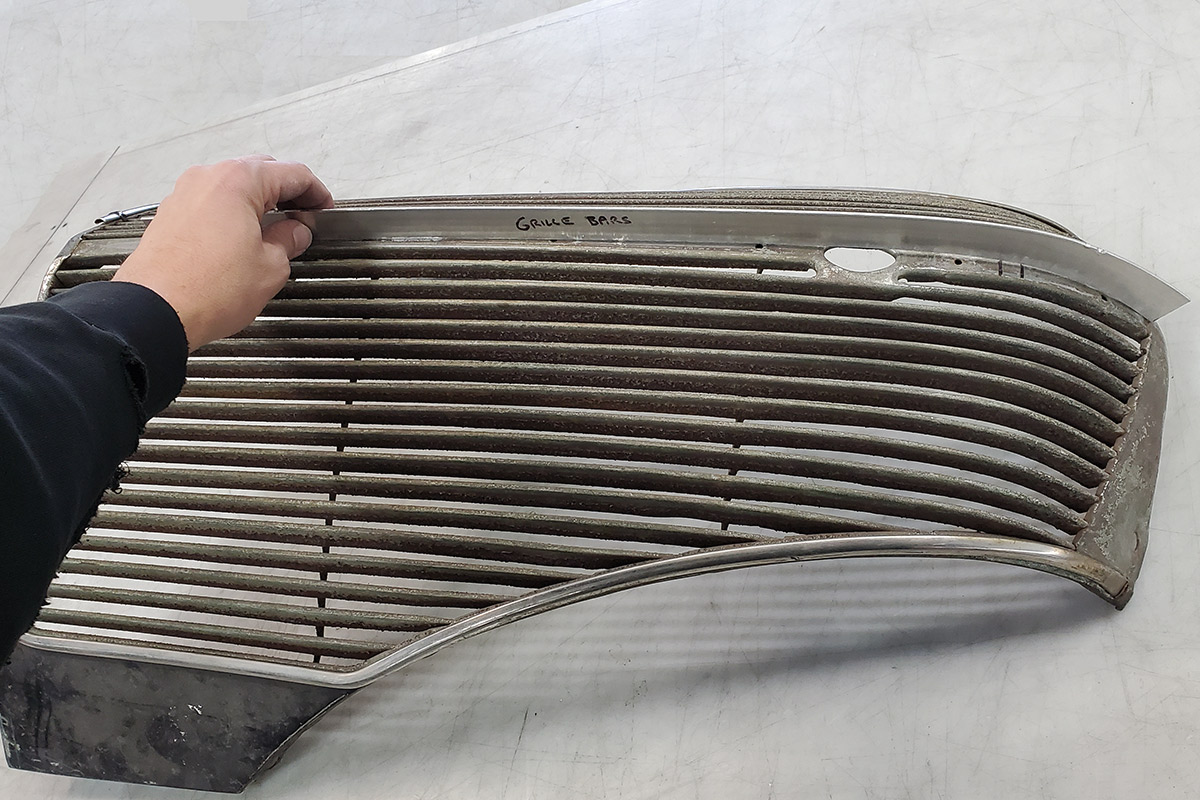
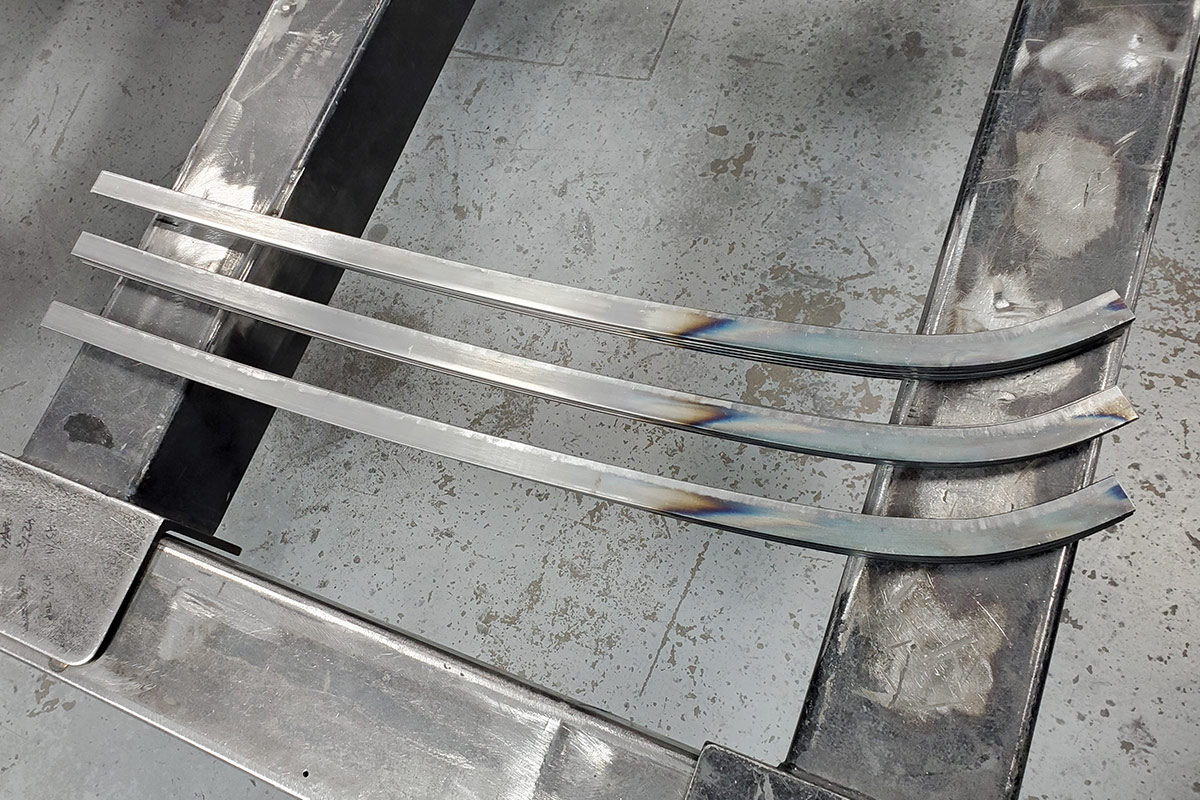
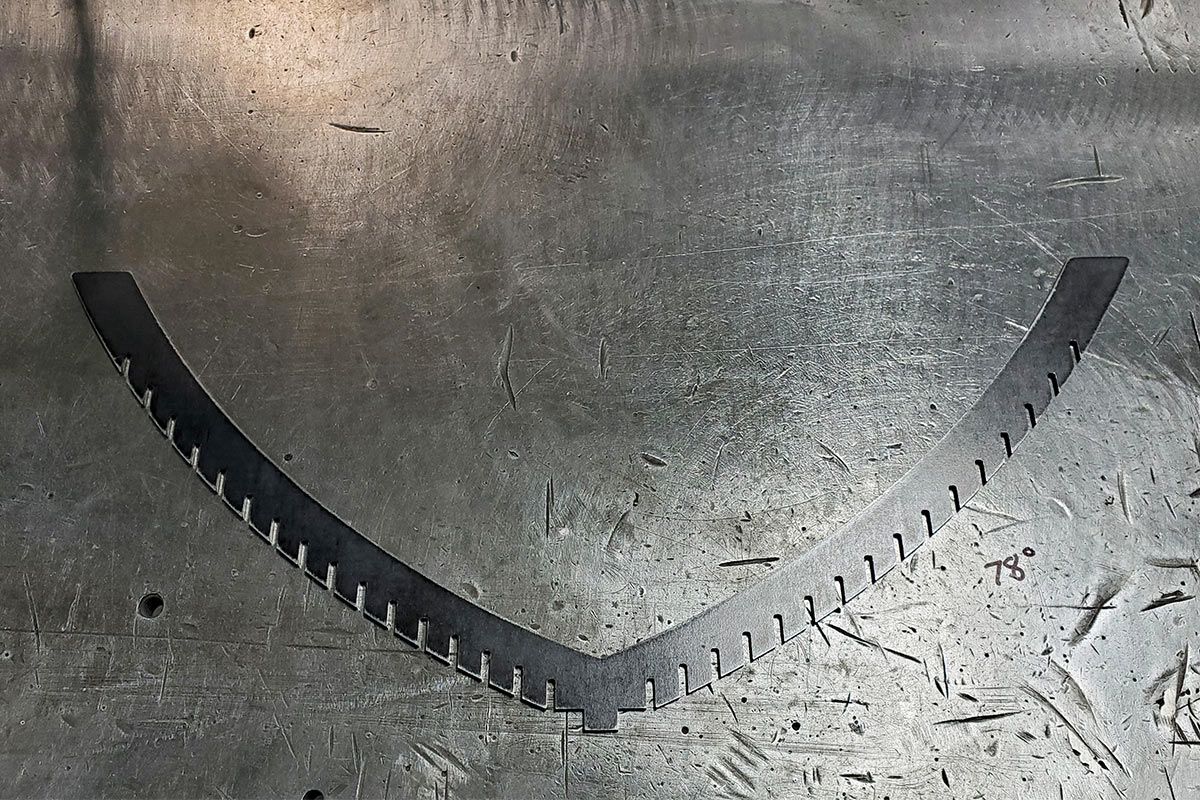
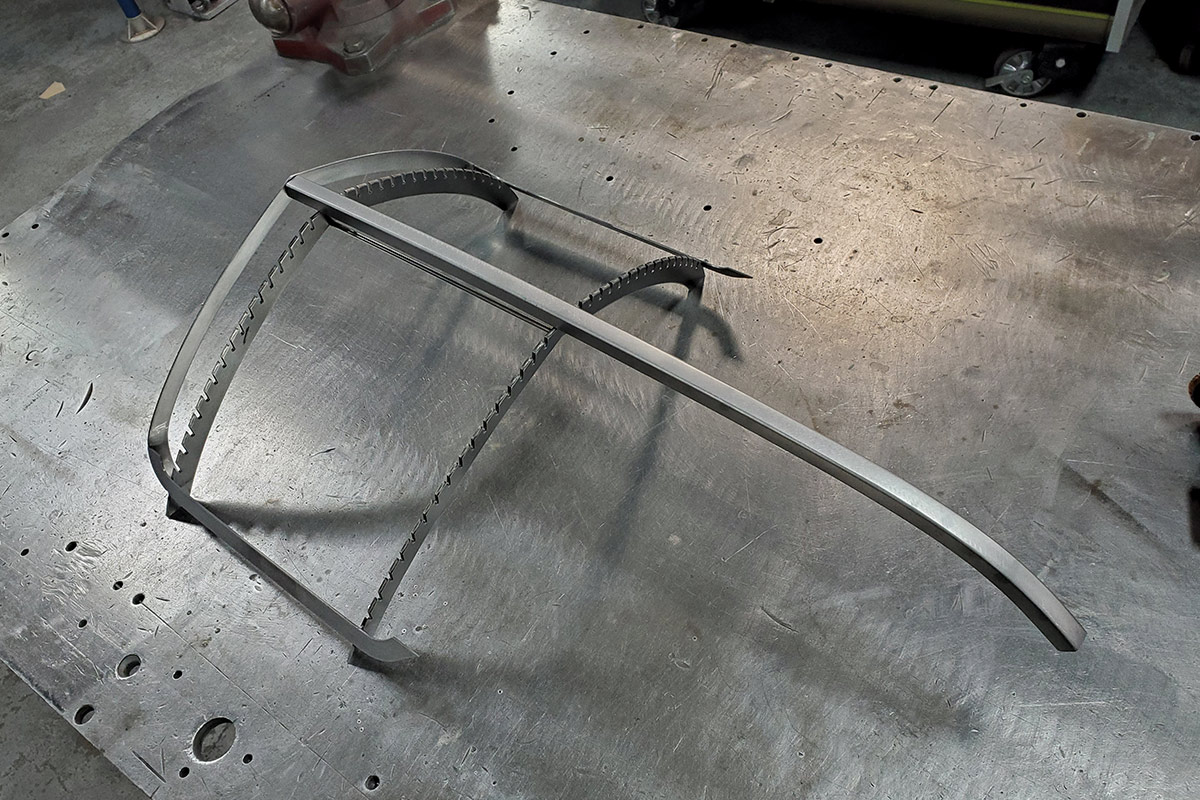
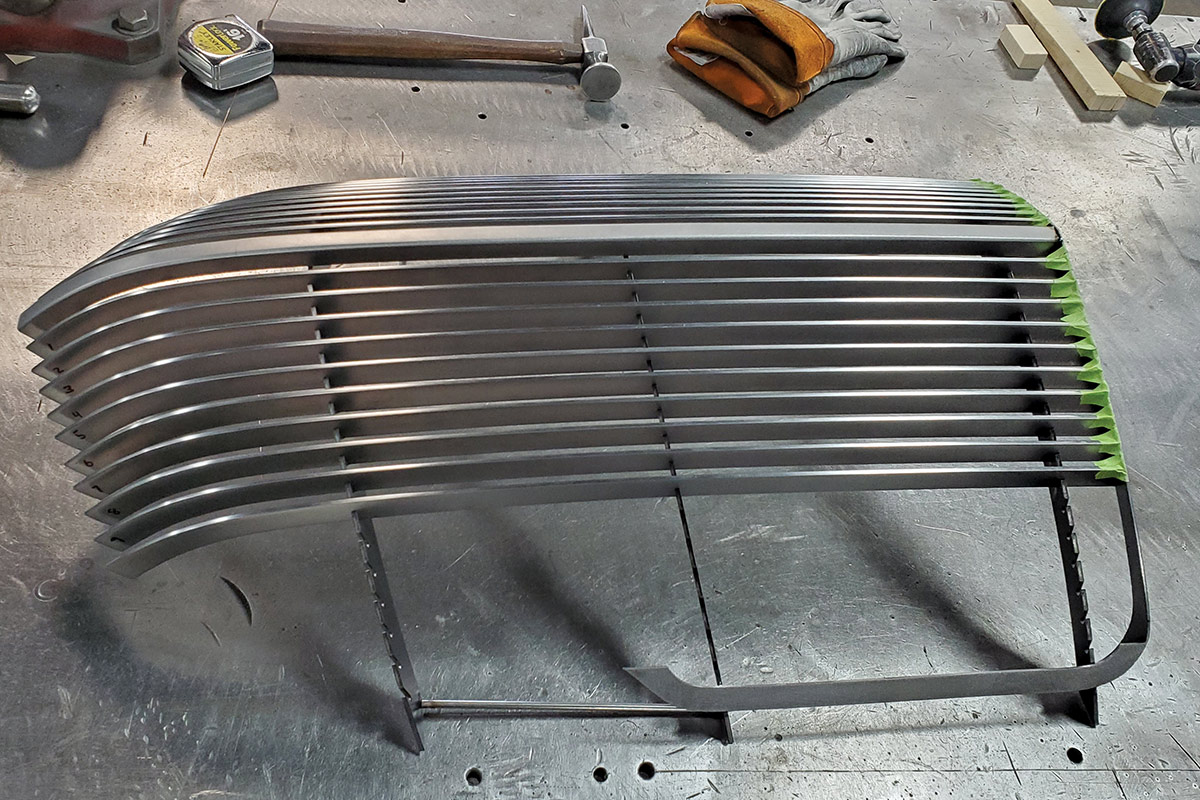
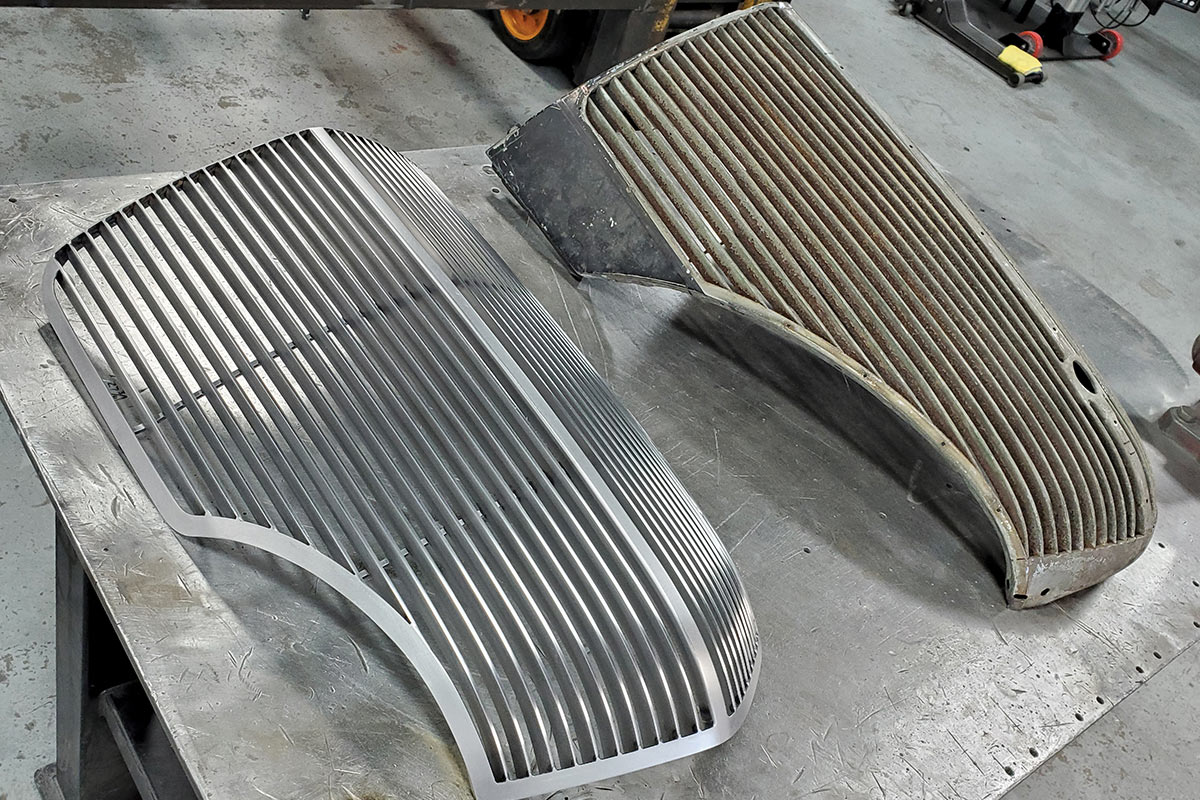
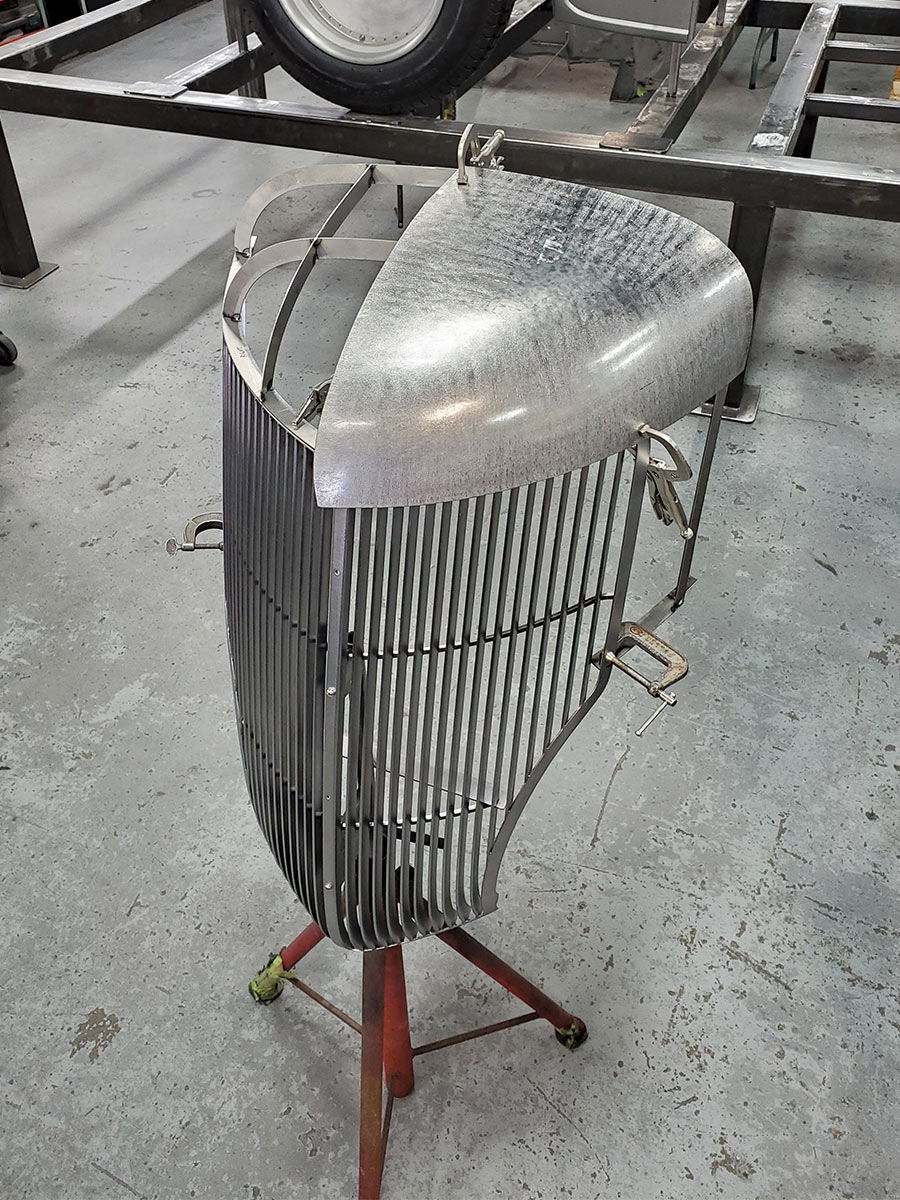
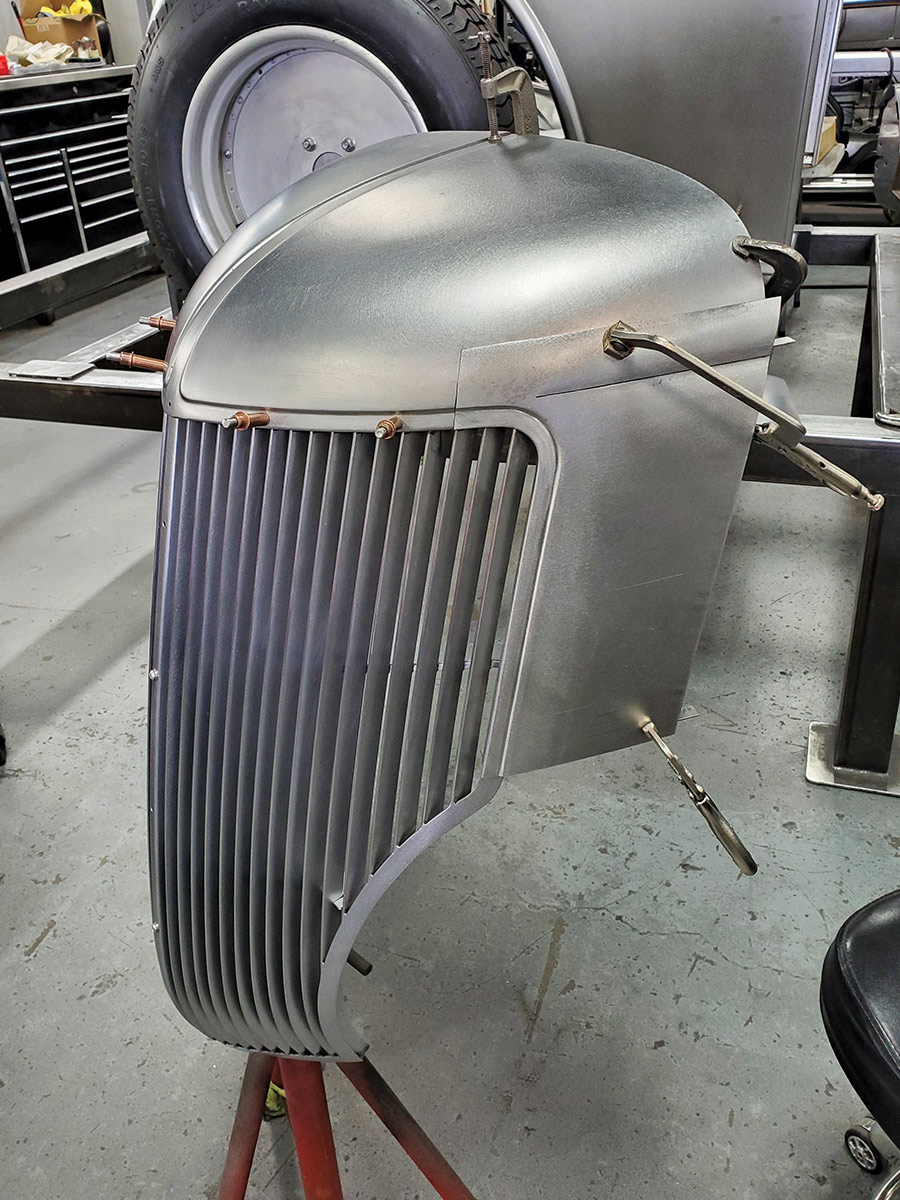
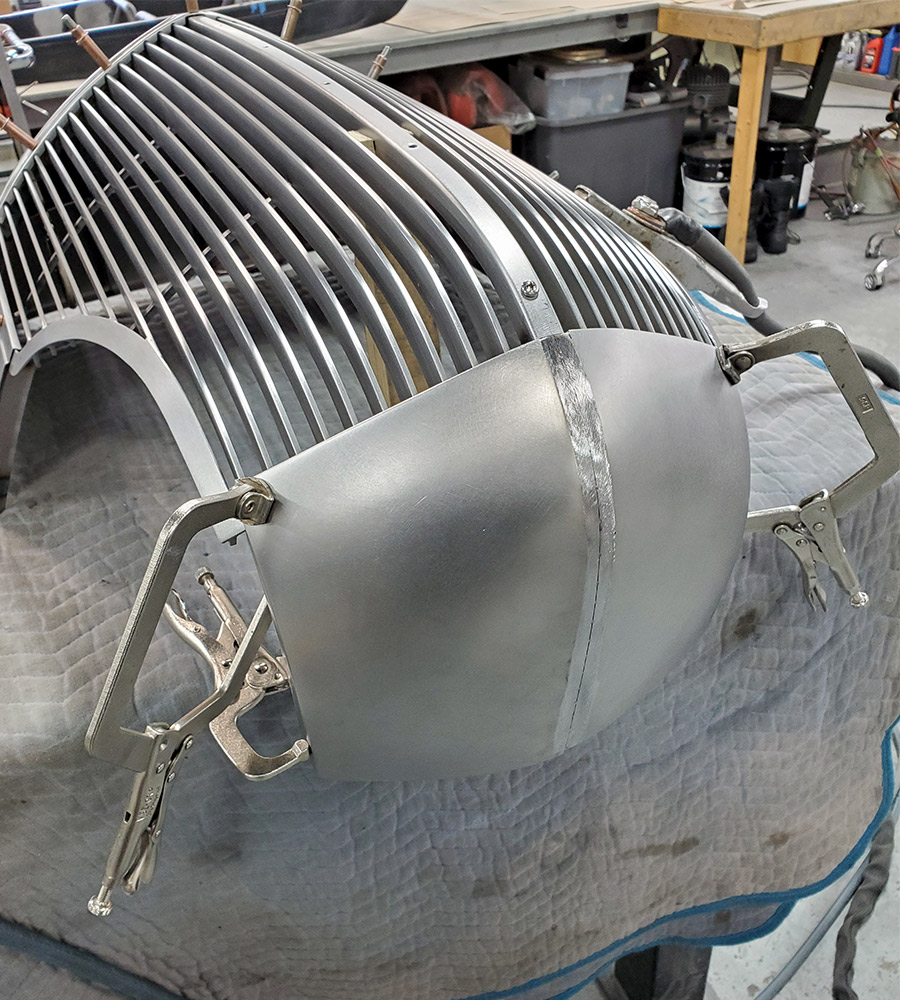
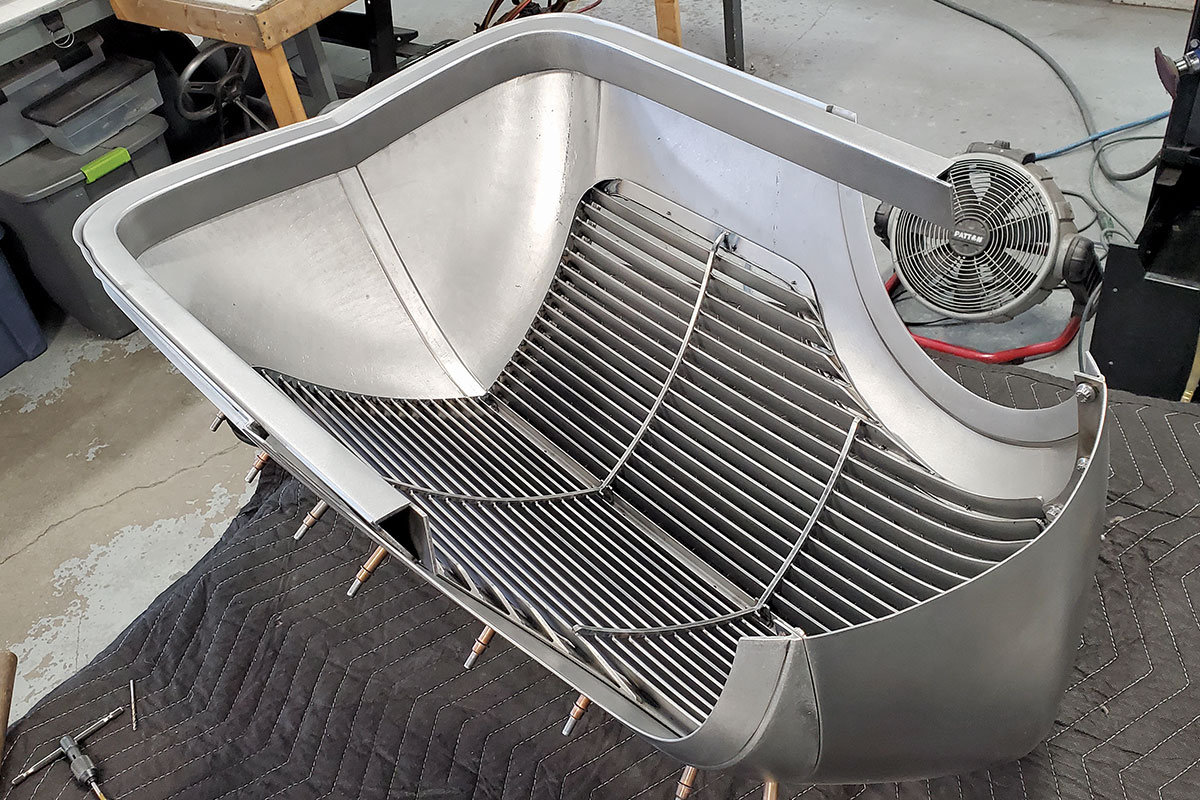
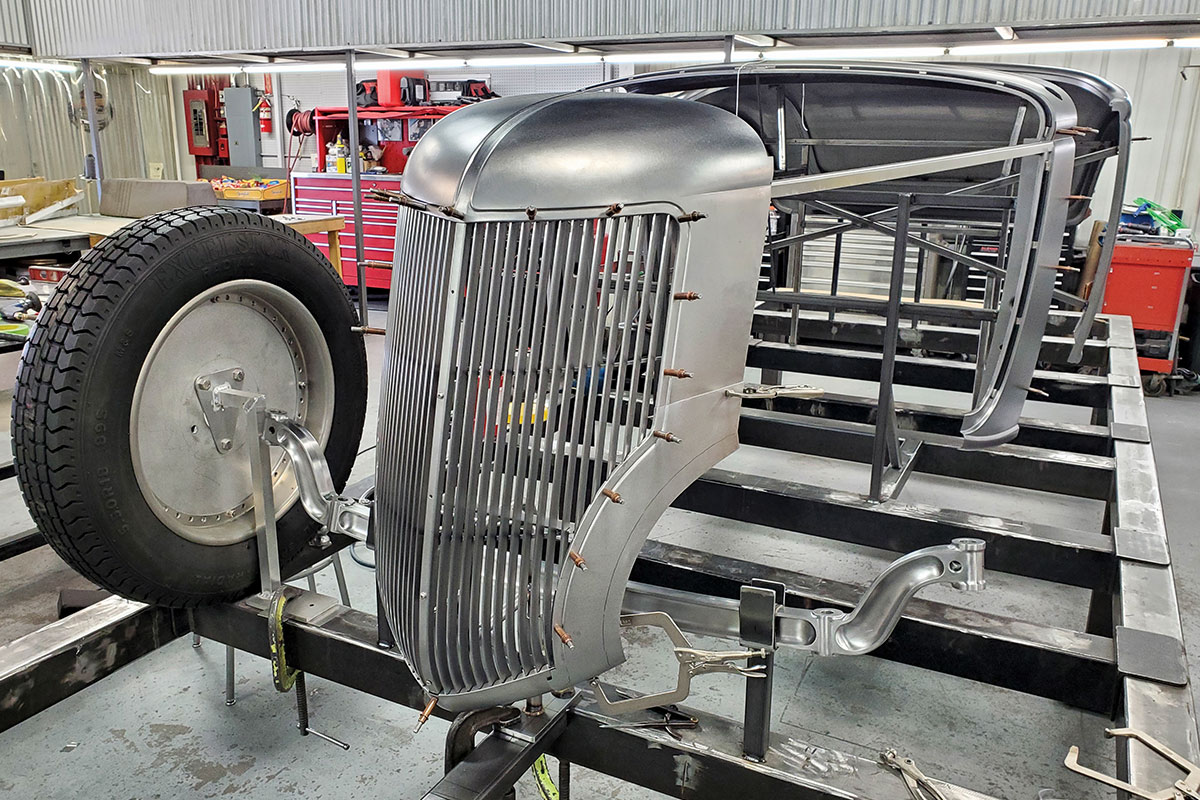
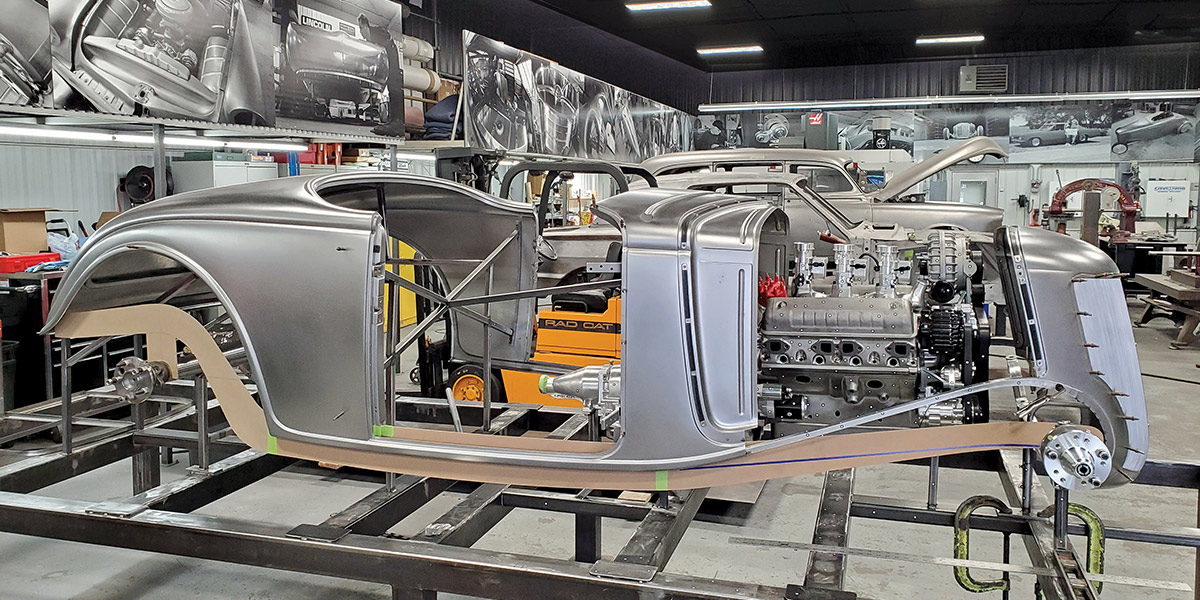
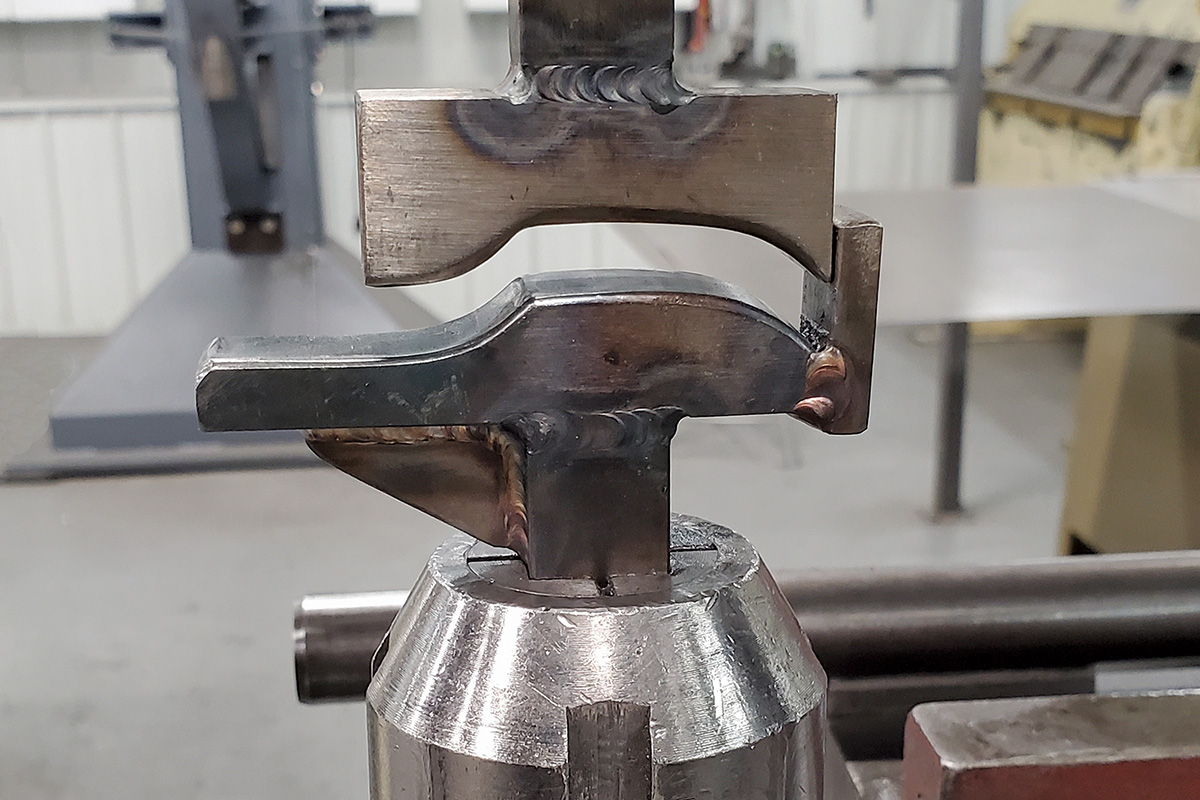
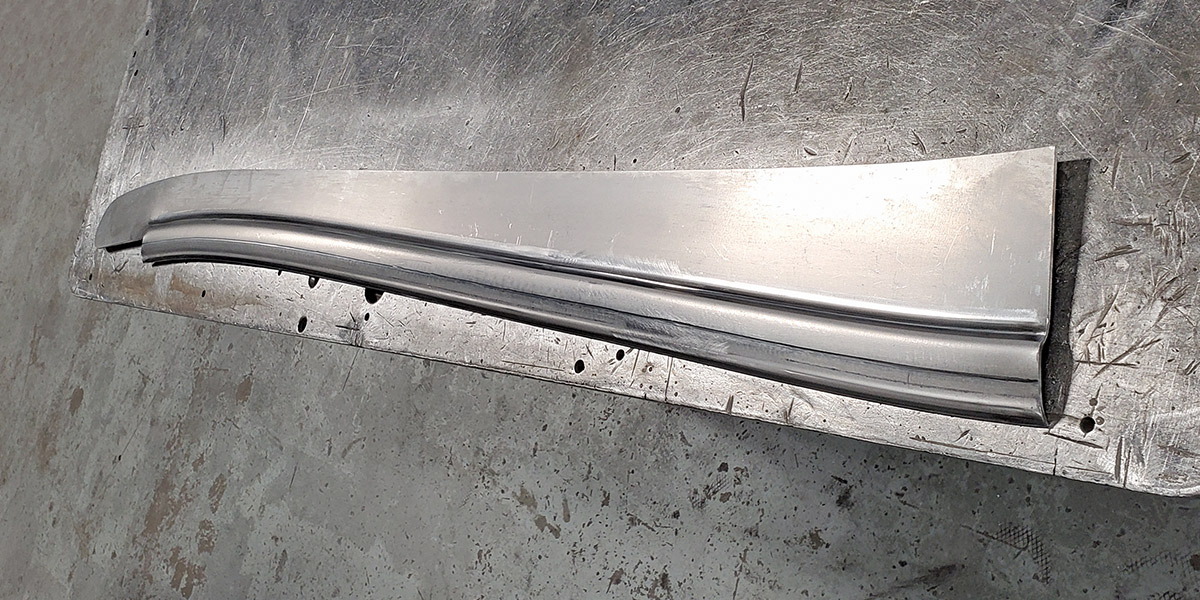
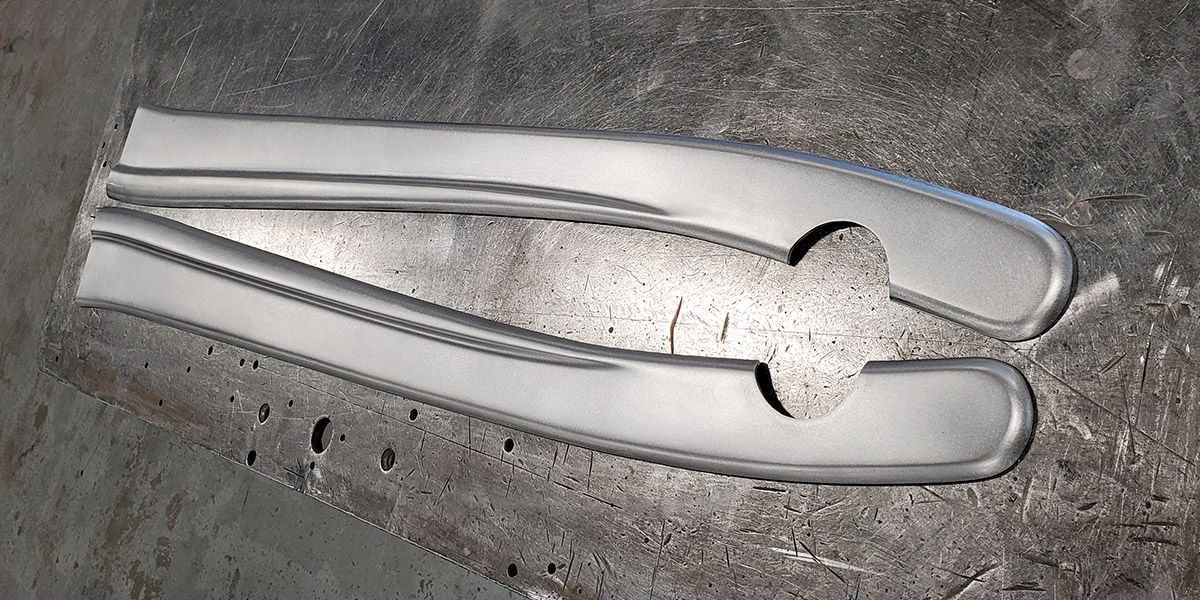
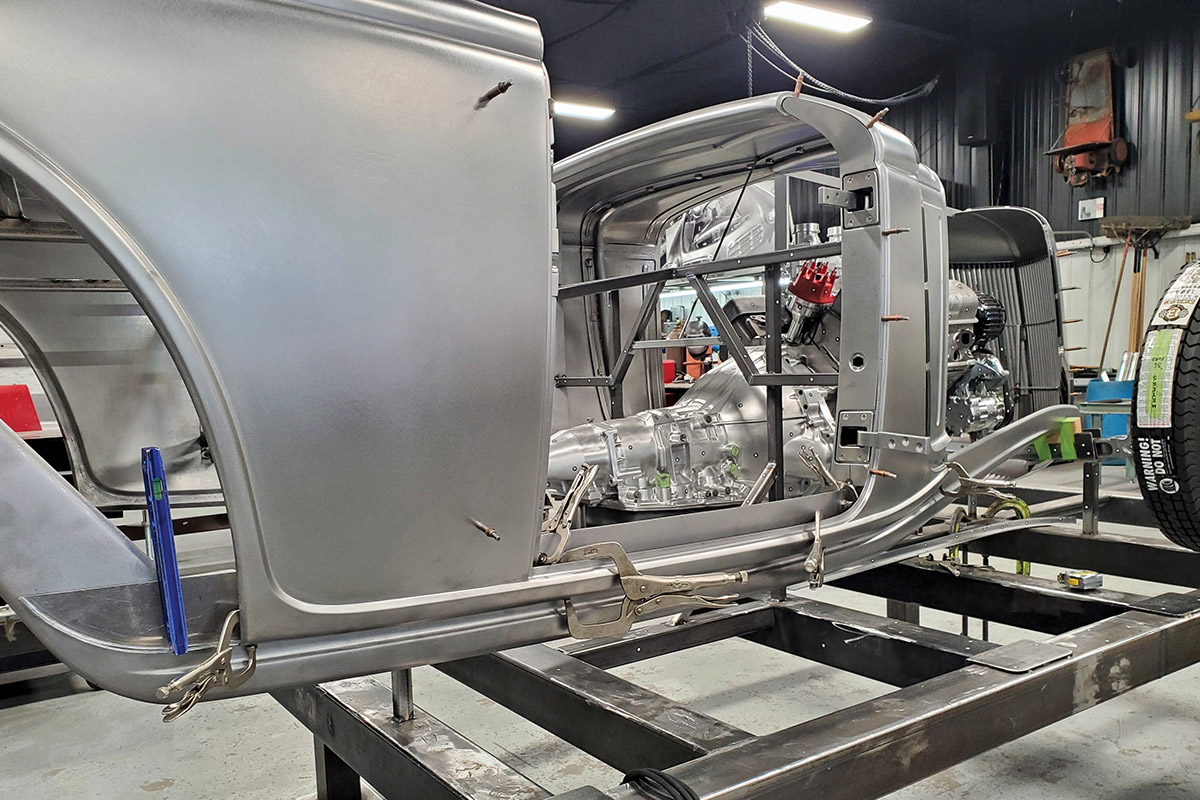
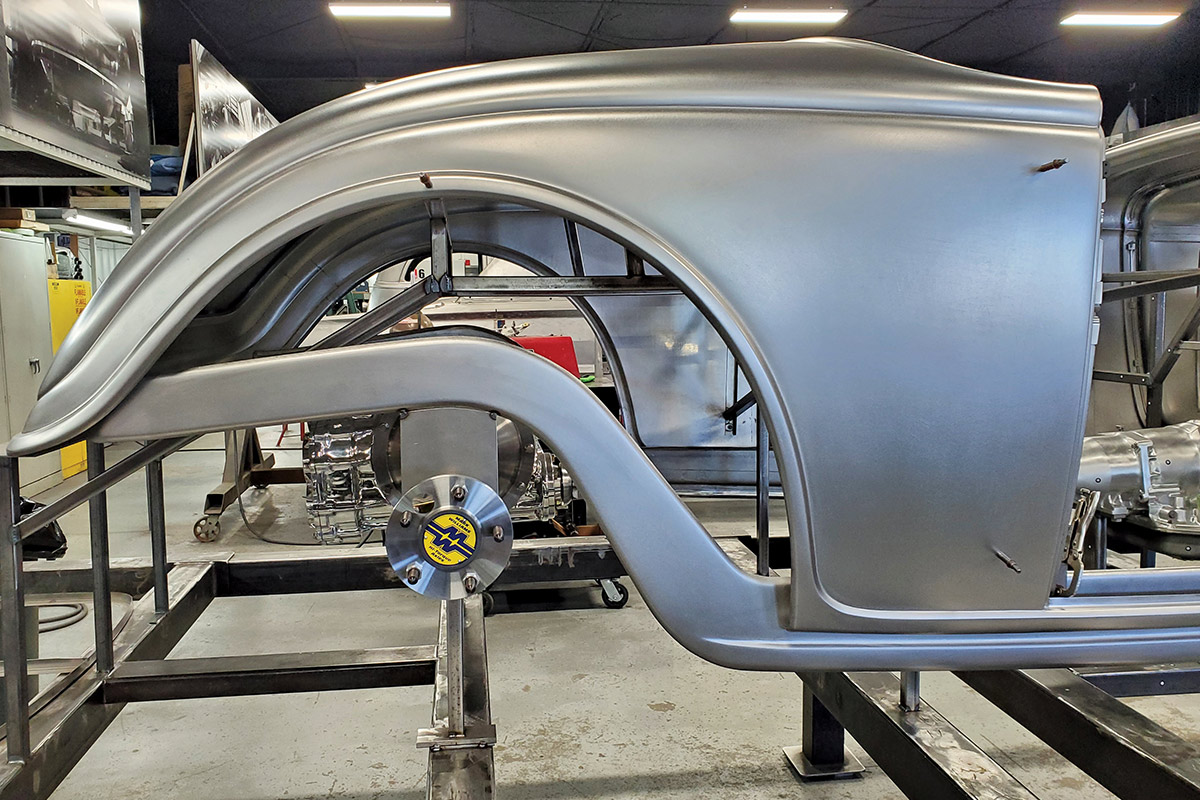
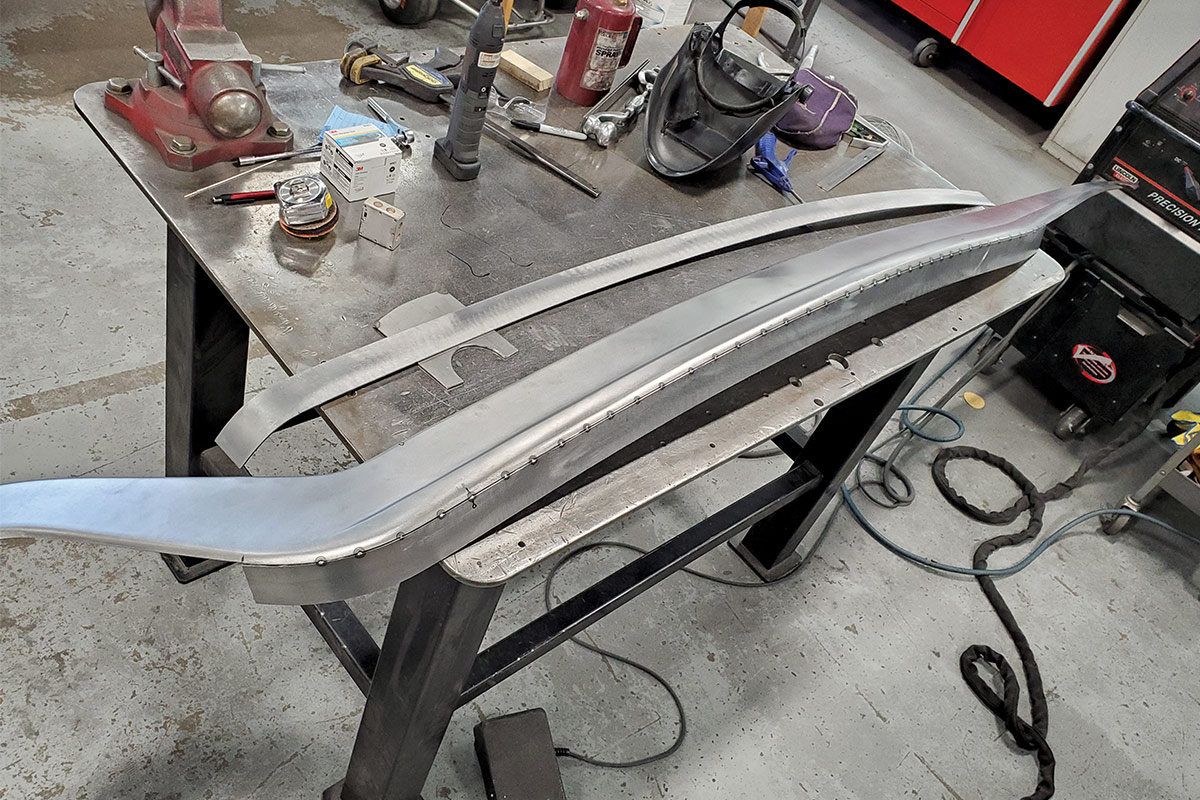
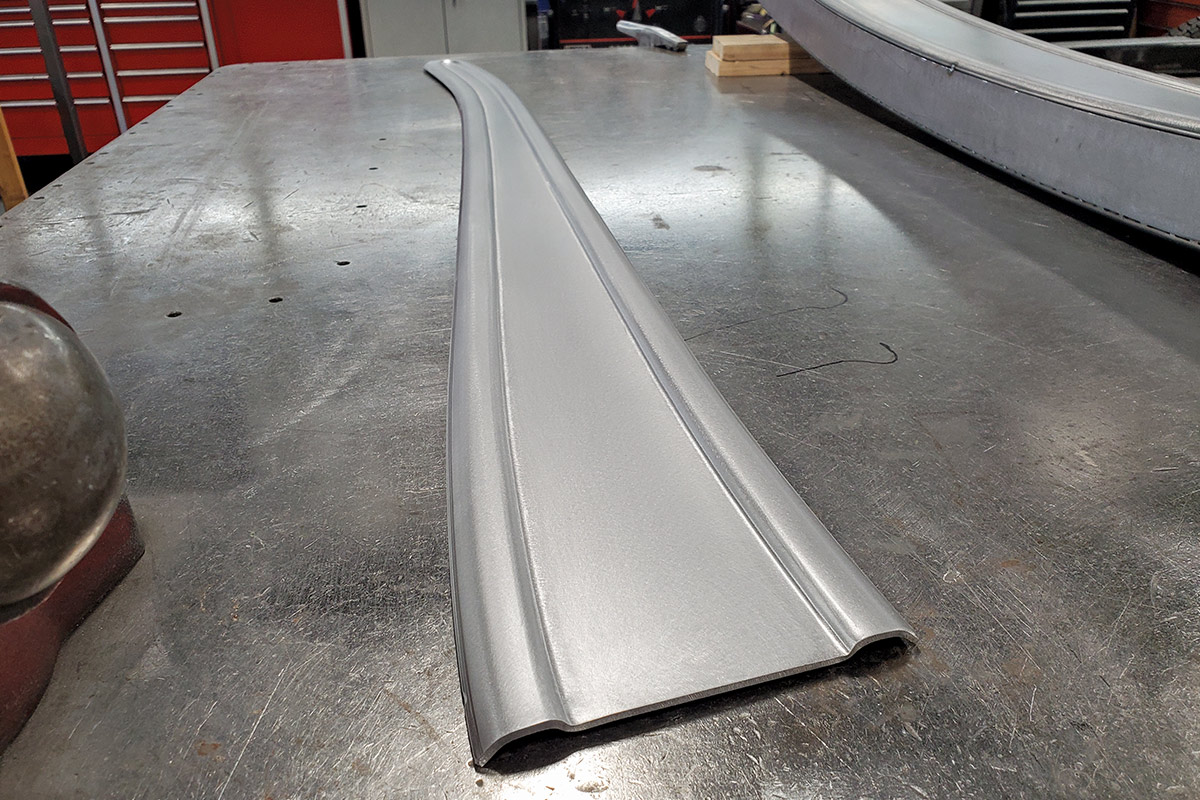
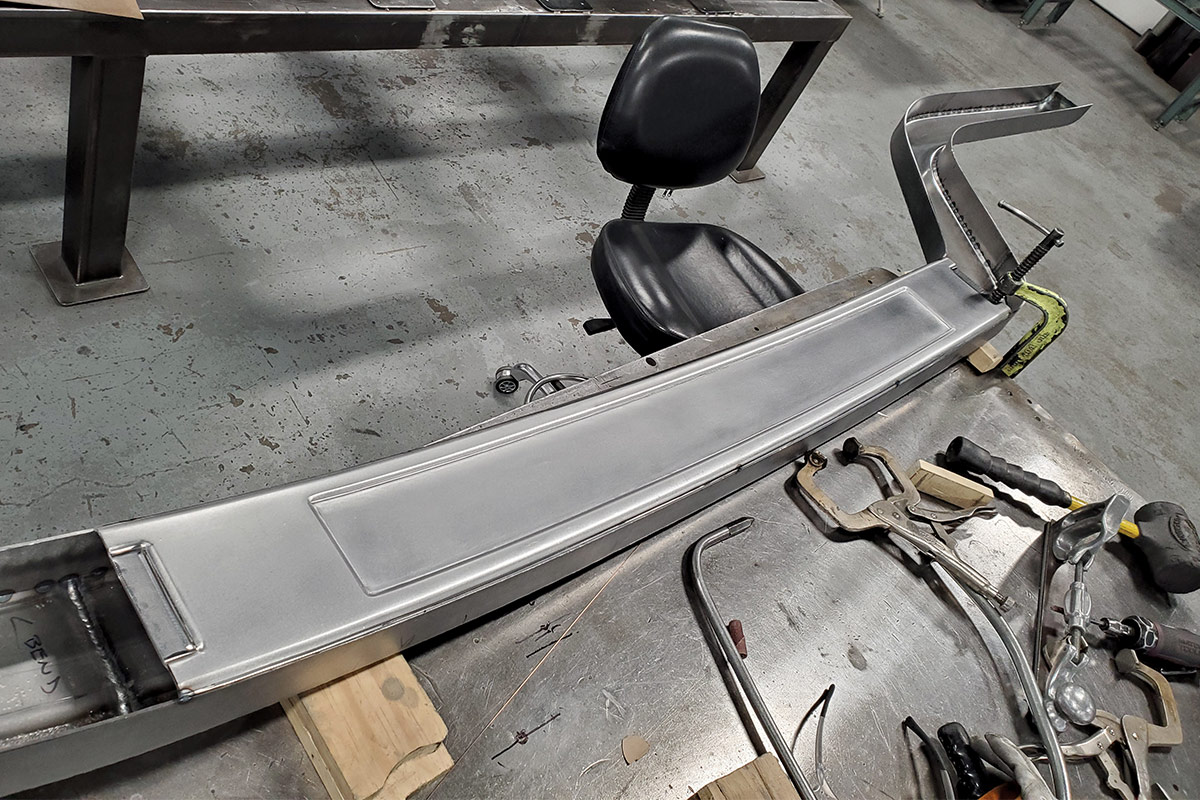
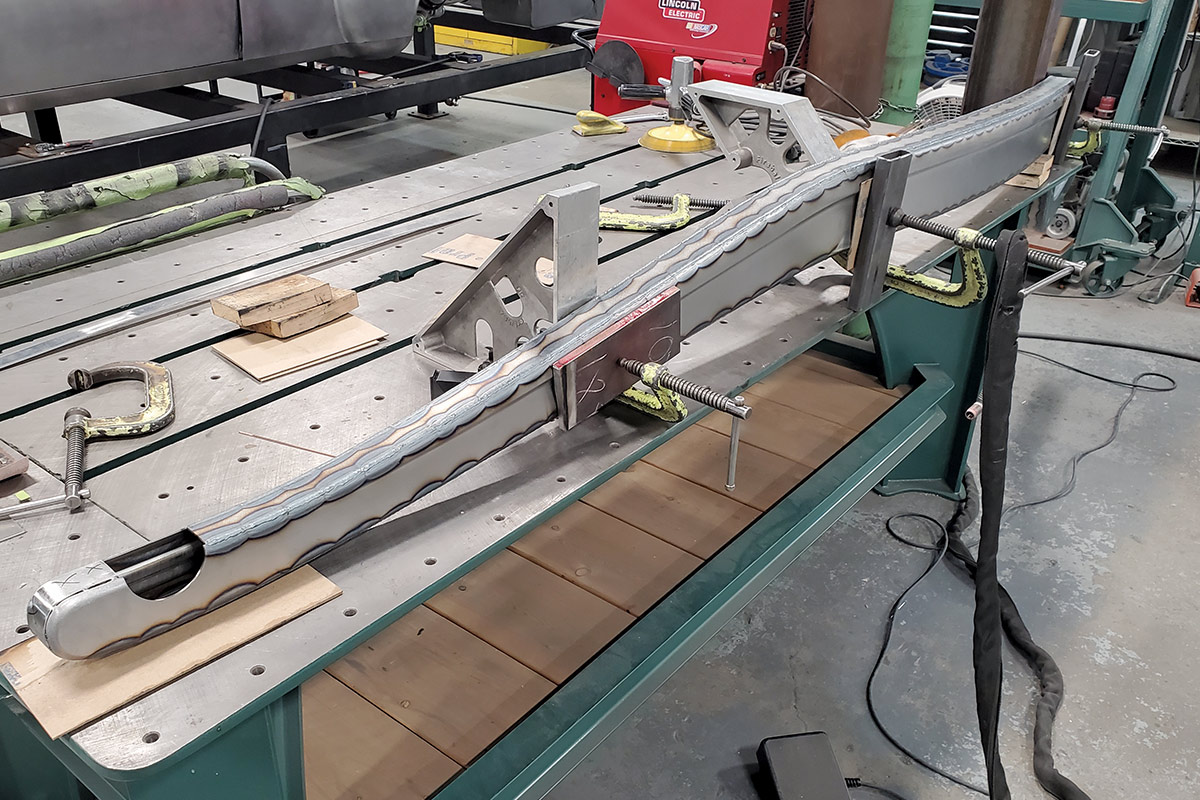
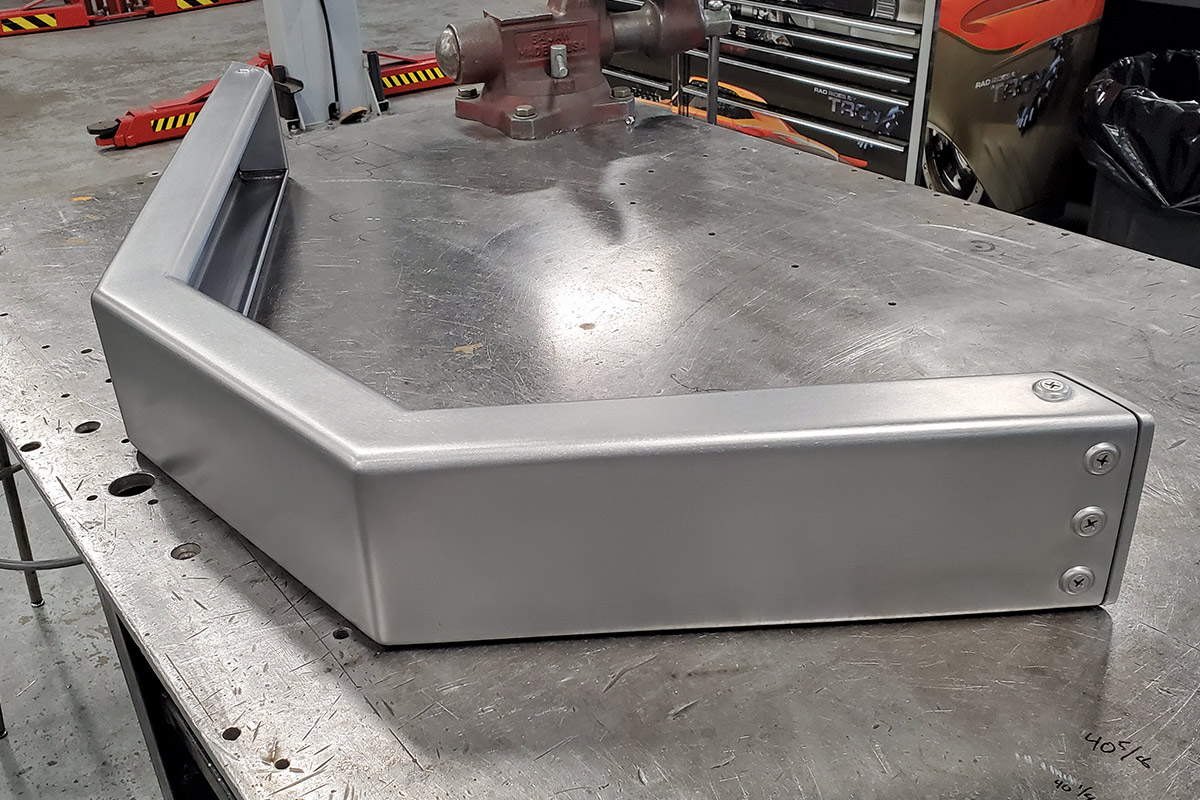
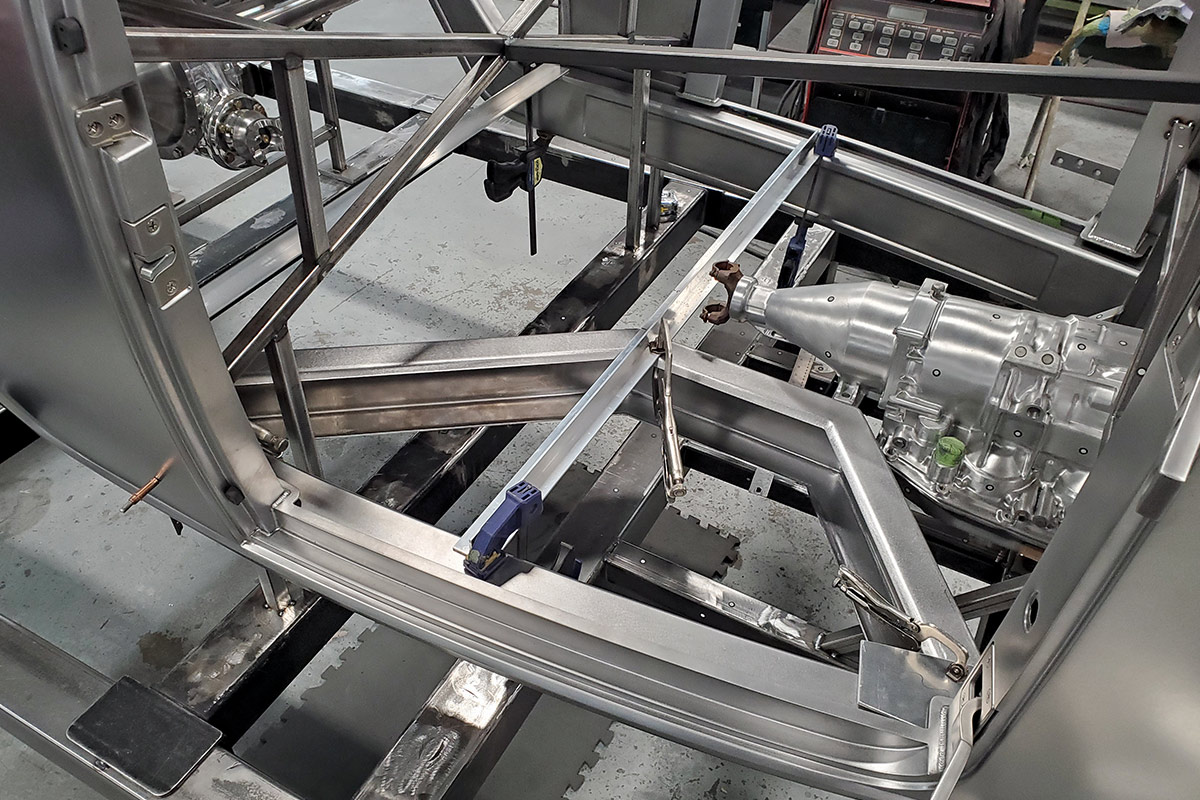
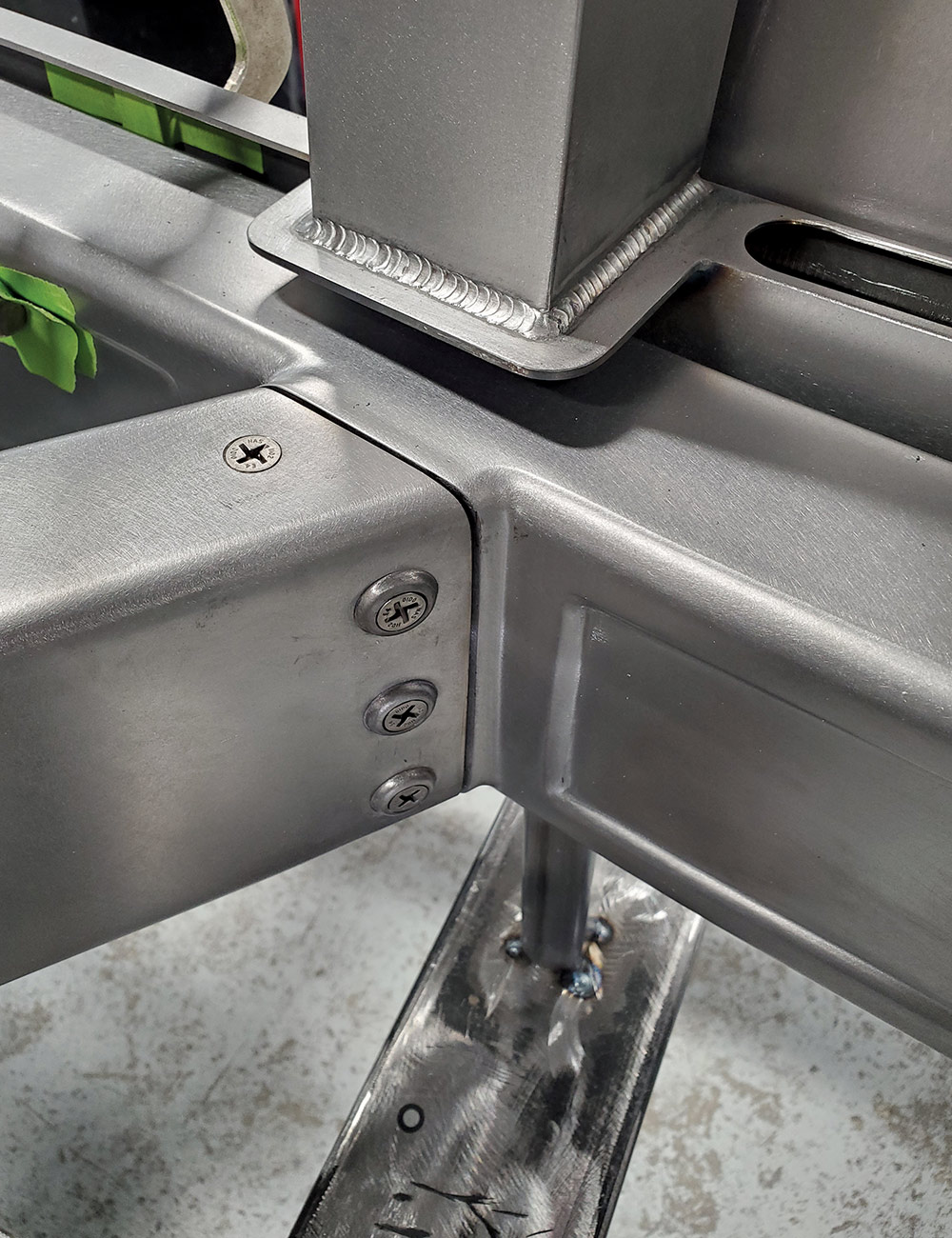
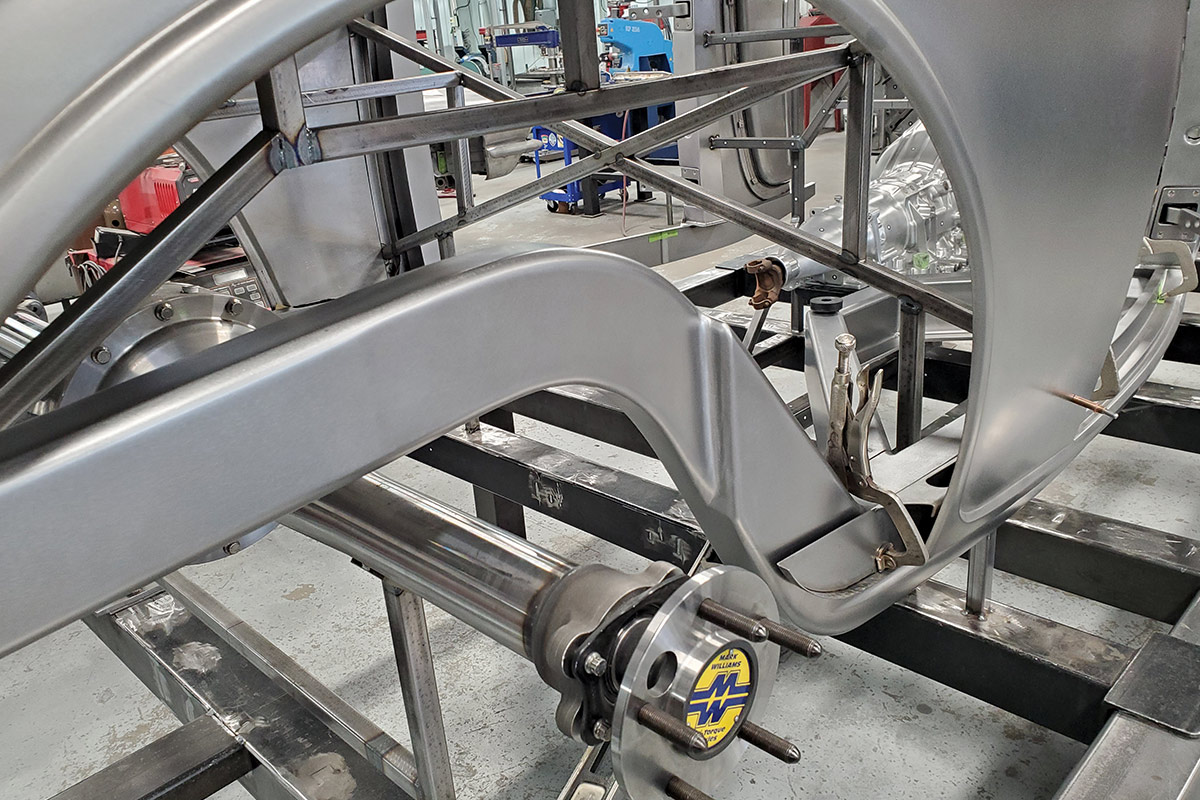
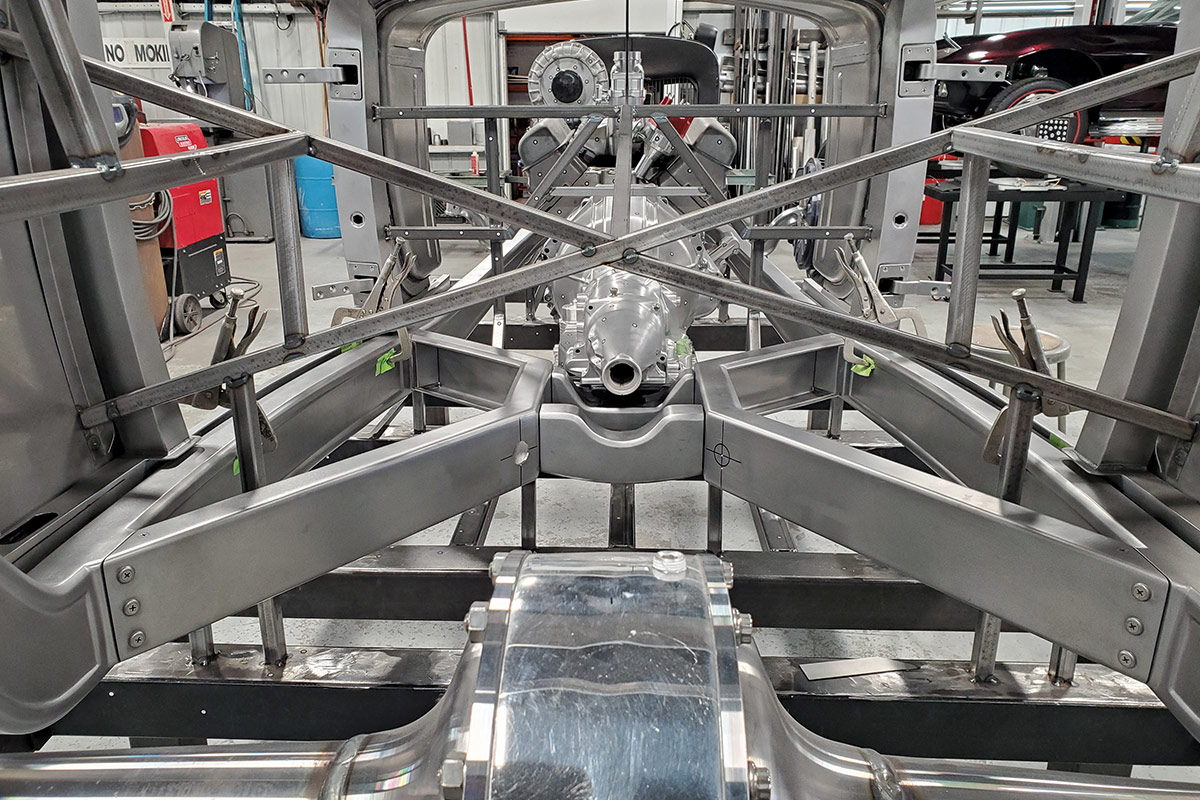
