Modern Rodding TECH
InTheGarageMedia.com
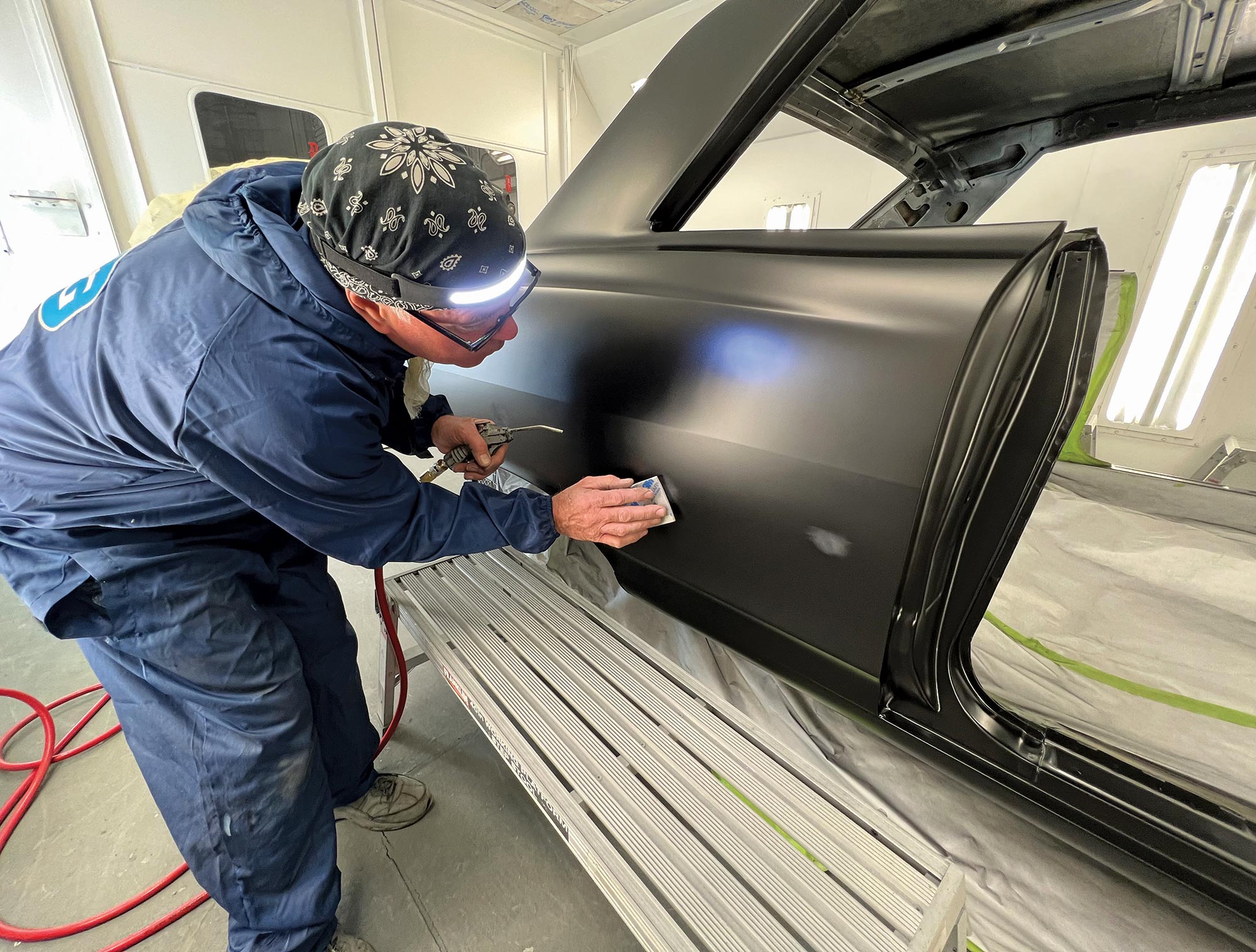

f you’re reading this, chances are you read the first entry of this two-part series in the Nov. ’23 issue. And if you read that, you probably got a little miffed that we cut off smack-dab in the middle of the process required to take a body from straight to perfect. But you know … space limitations and all.
Just like the real world of sanding, this month is more of the same. But we’re projecting beyond where most sanding stories end. Instead of closing at paint, we’re following through the post-production phase.
With technology available today, it’s possible to create a glassy, wet-look finish right out of a gun. But as good as a gun finish can look, it can be better—a whole lot better.
No matter how good a finish lays out, it will always have flaws. They might be barely perceptible, but they’re there. These are the bulges at seams and edges, steps caused by tape lines in graphics, the light ripples across an otherwise-flat surface, and even nibs caused by that one speck of dust left in the booth.
Part of what differentiates the finishes produced by masters like Charley Hutton, Alloway’s Hot Rod Shop, Darryl Hollenbeck, and Zane Cullen is the work they put in after the paint dries—and by work we mean more sanding. The grits differ but the process remains basically the same: remove anything that interrupts a smooth, consistent finish. Color sanding eliminates flaws/imperfections, just on a much finer scale. Where we drew the line, though, is at the polishing stage. That’s its own subject.
It may take a trained eye to spot the flaws that we can eliminate by sanding. But the training is well worth it. From across a parking lot, even a rank amateur can tell the difference in the finished product. And it’s those little differences that really matter.
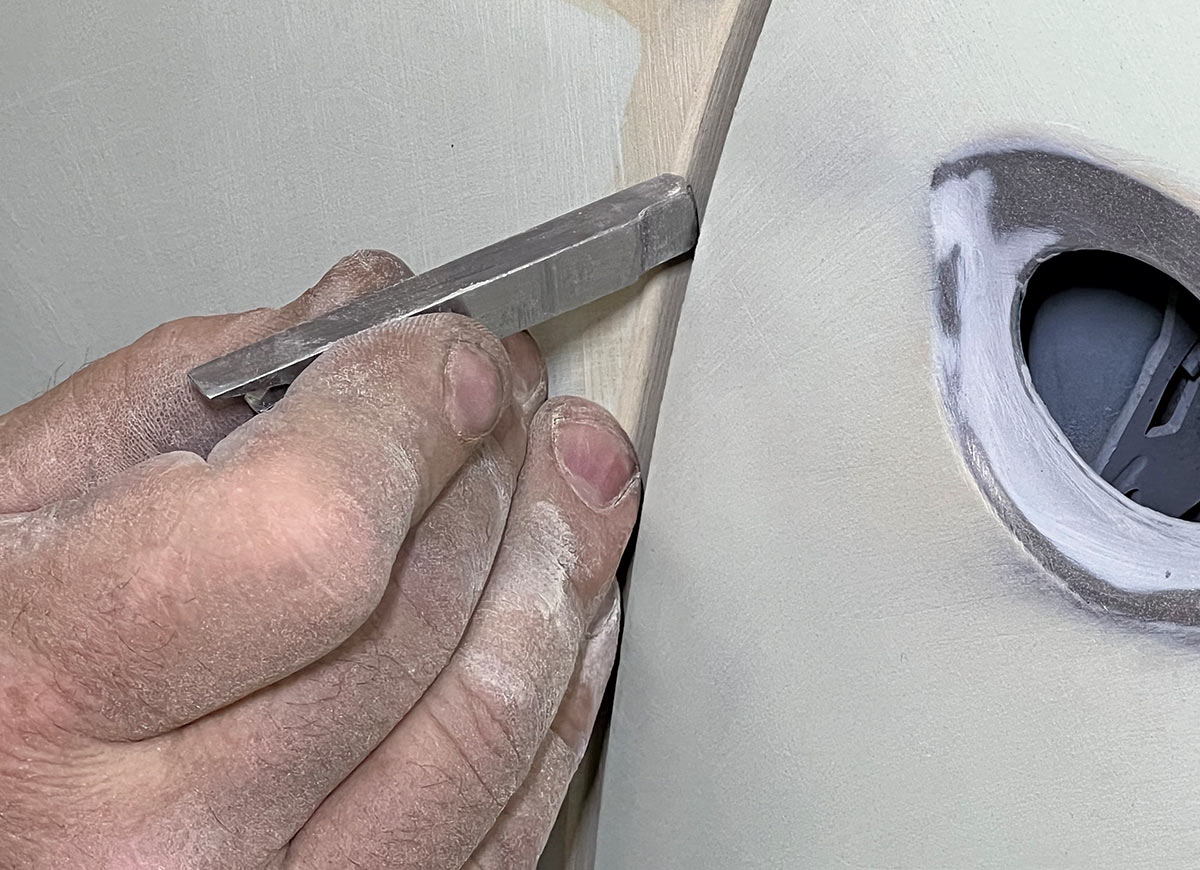


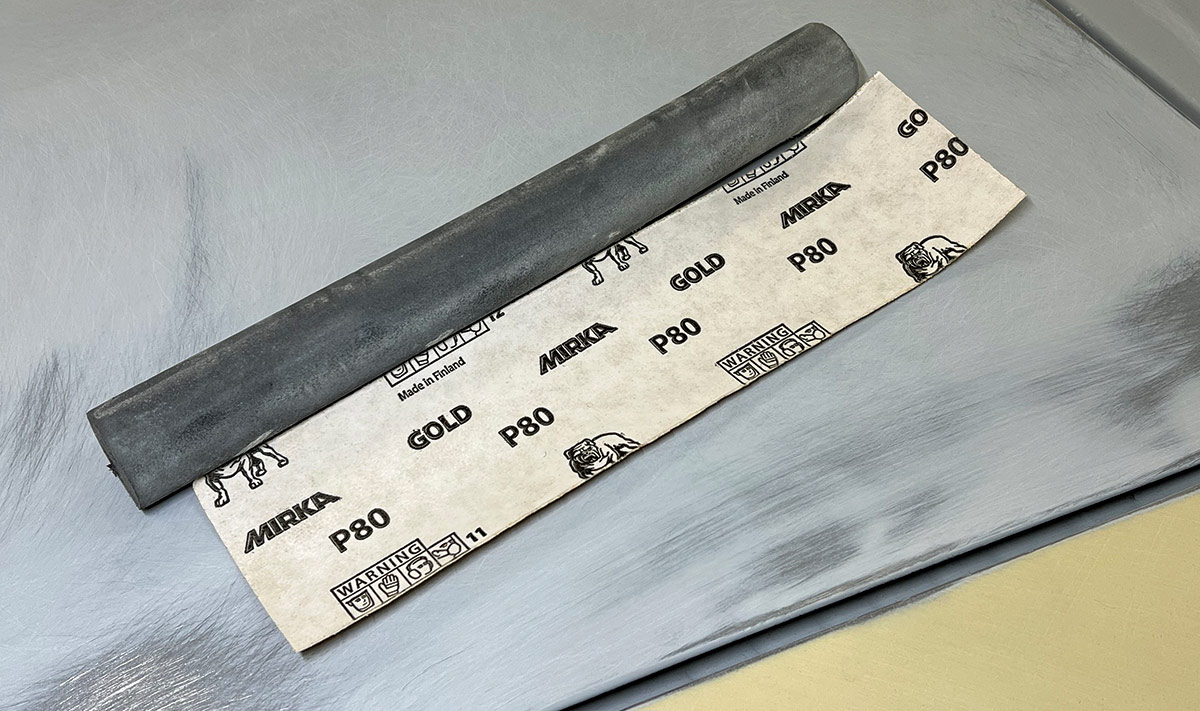
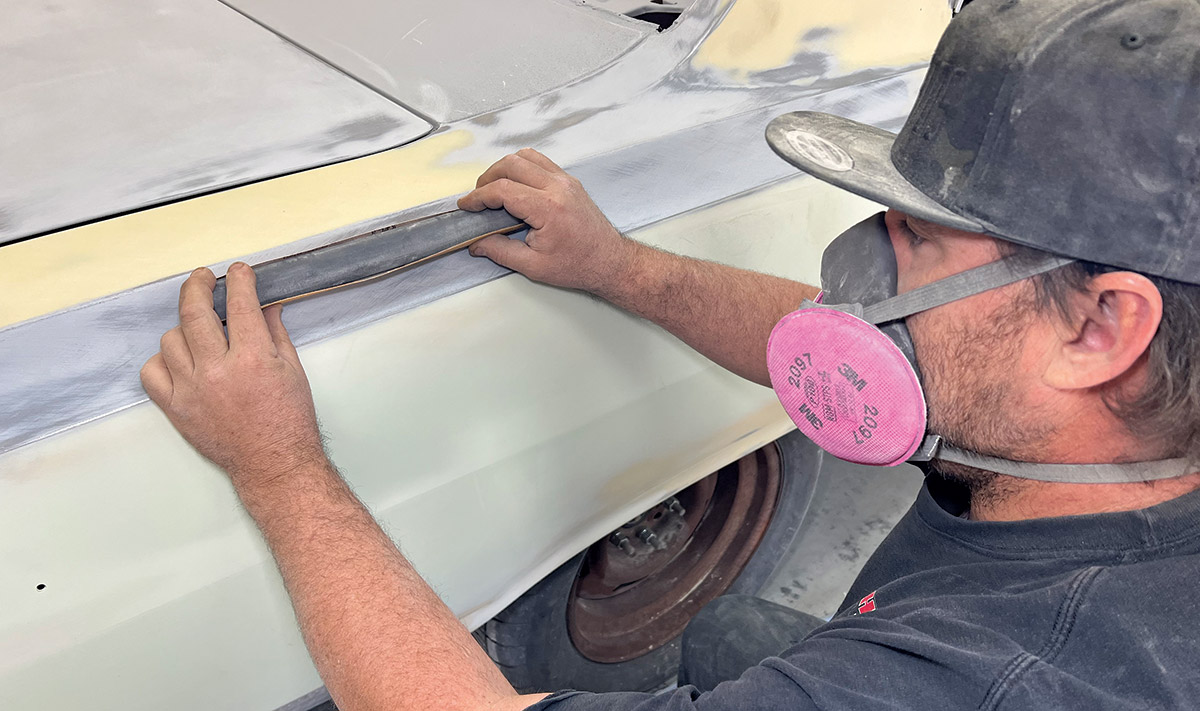

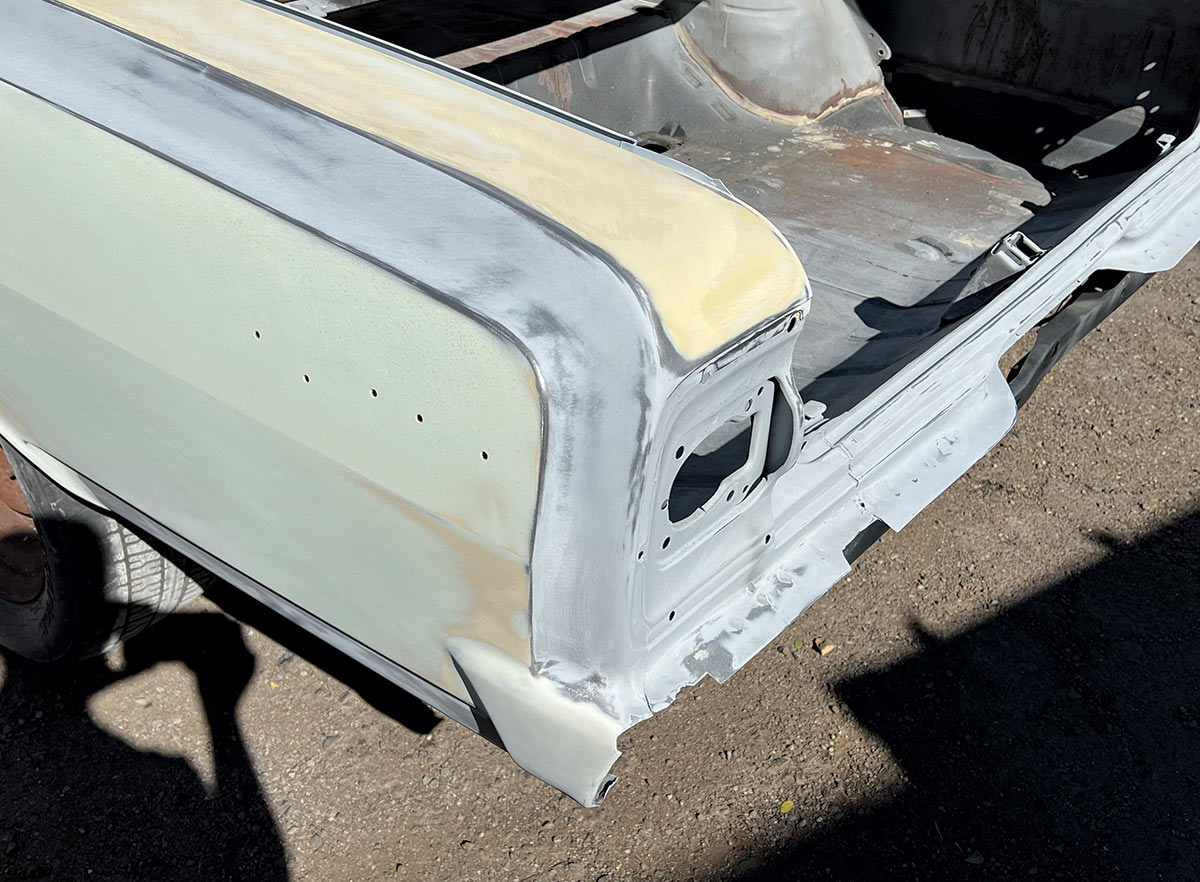
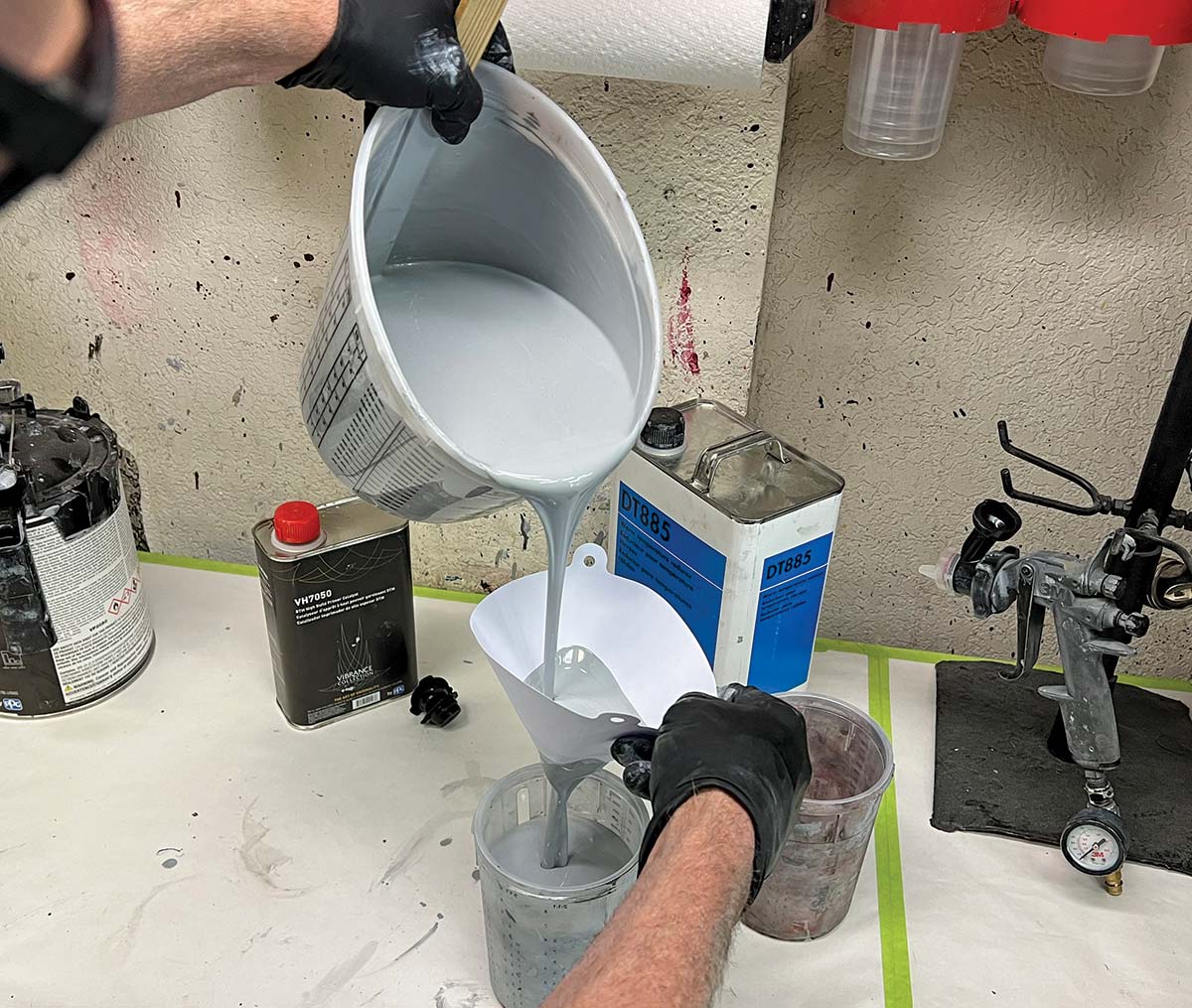


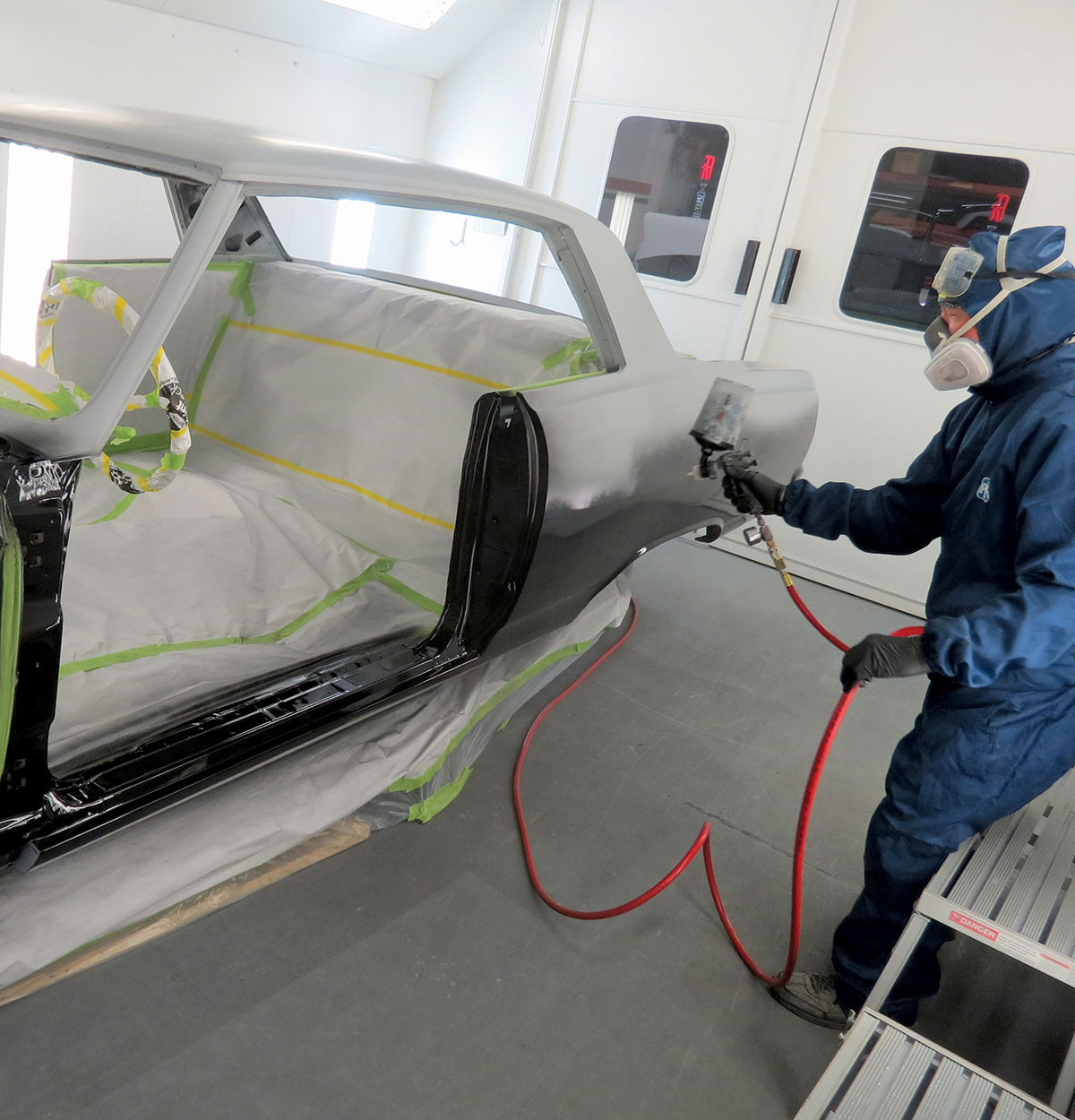

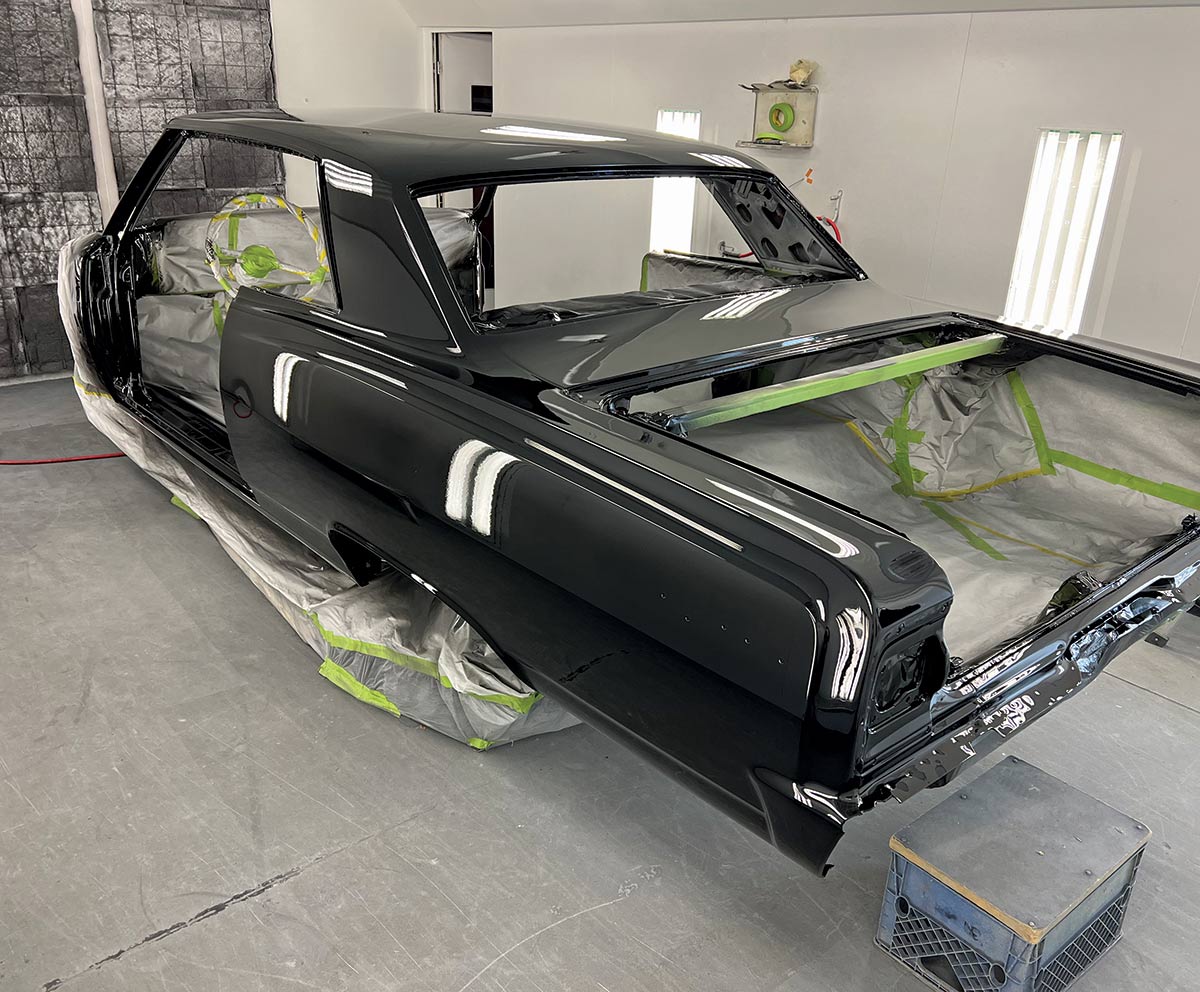
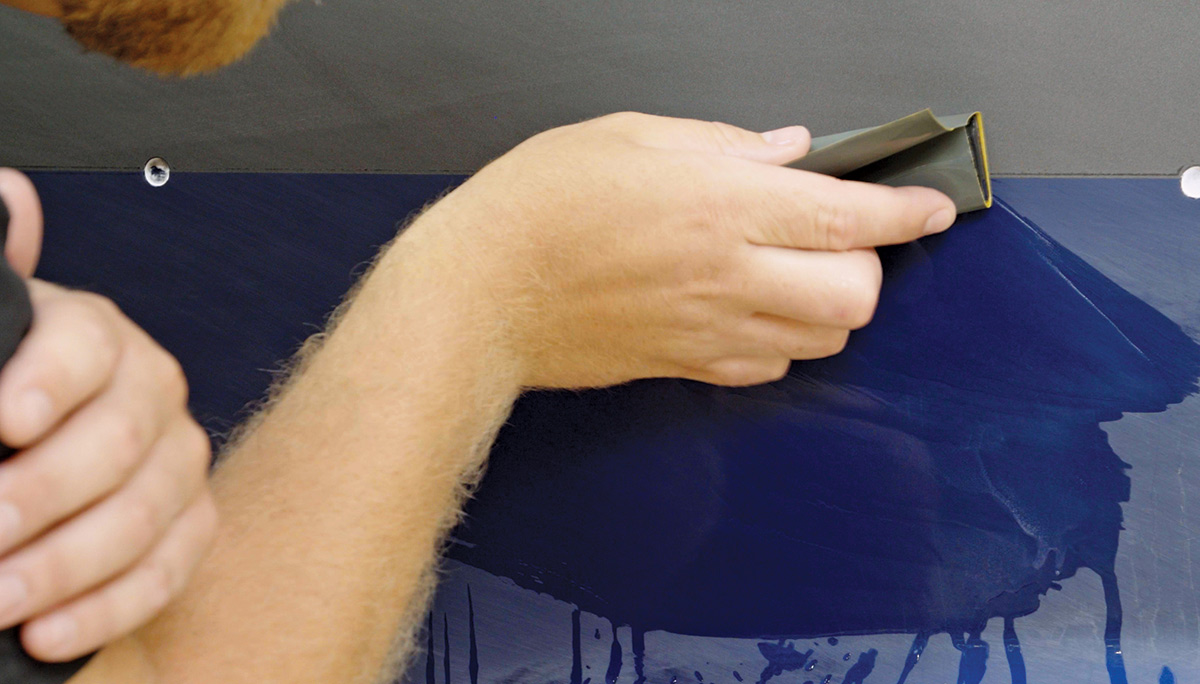
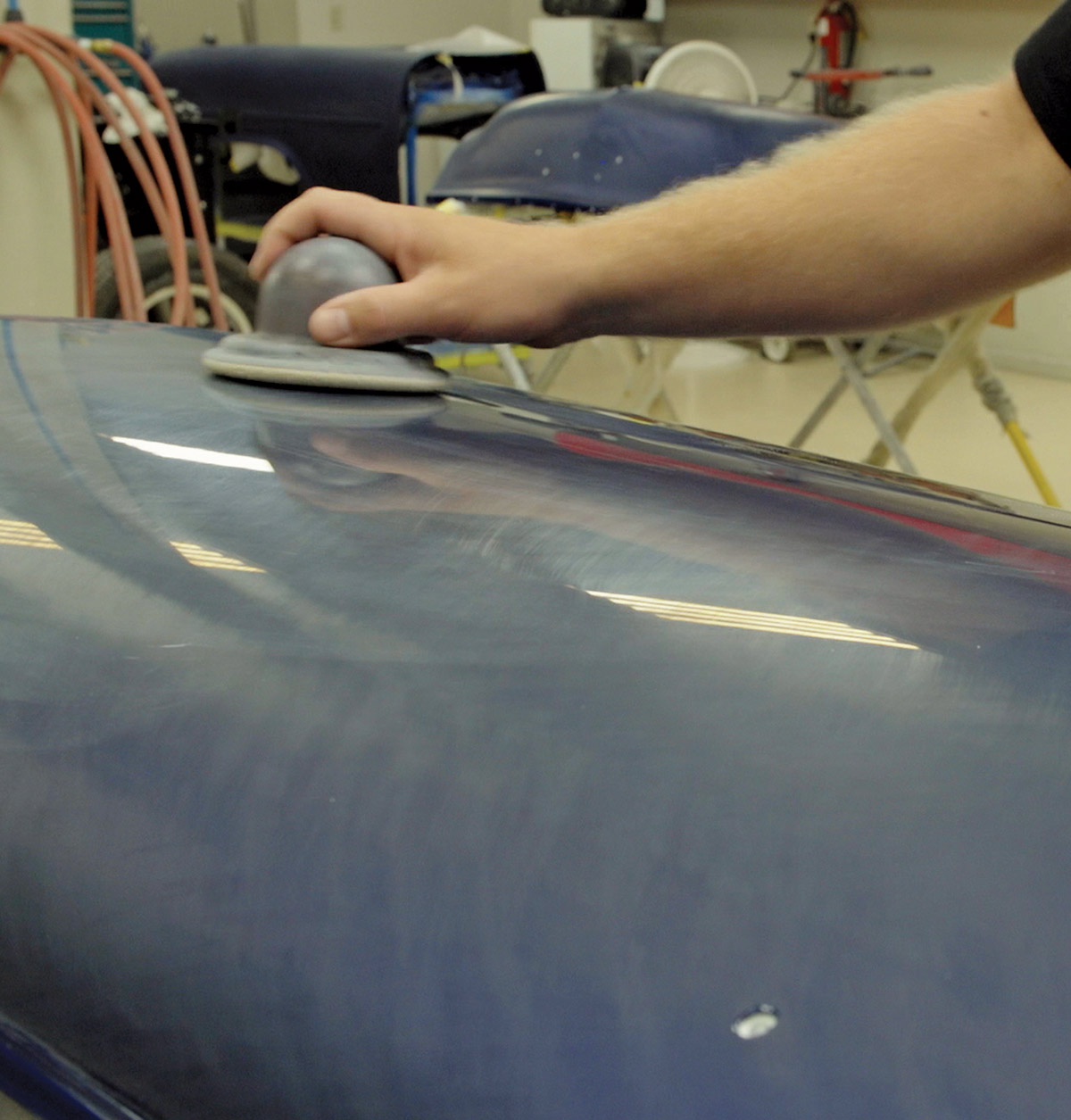
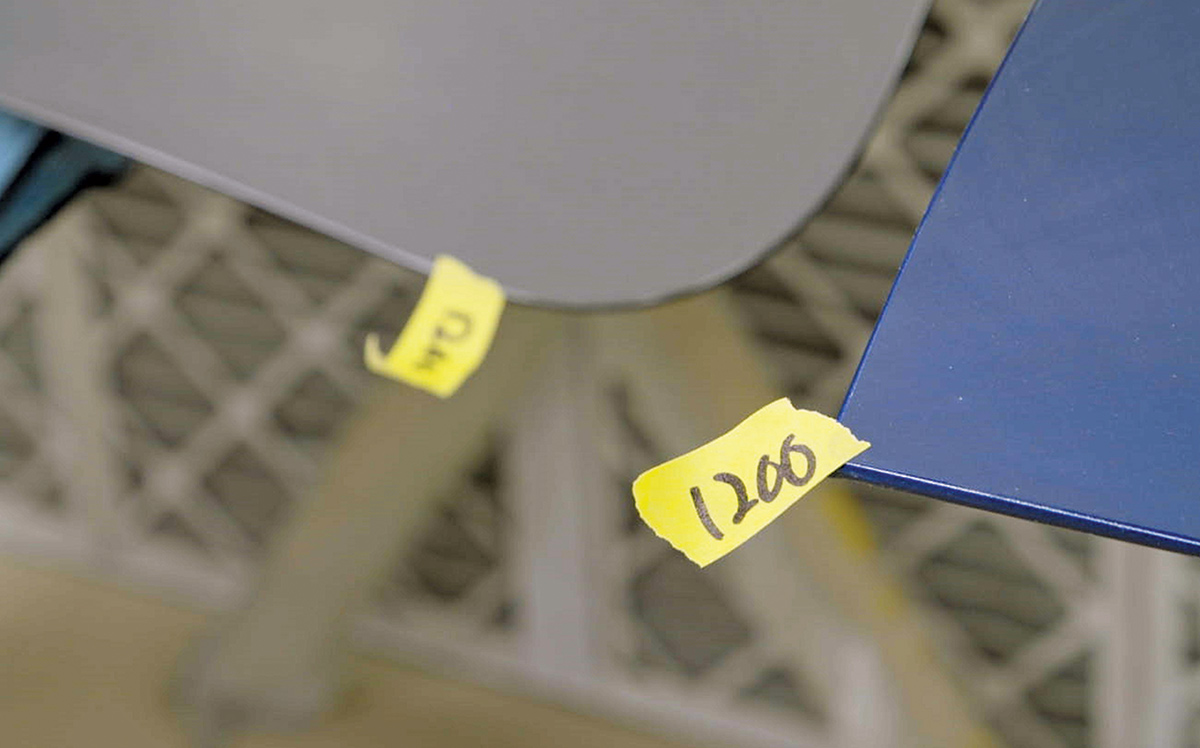
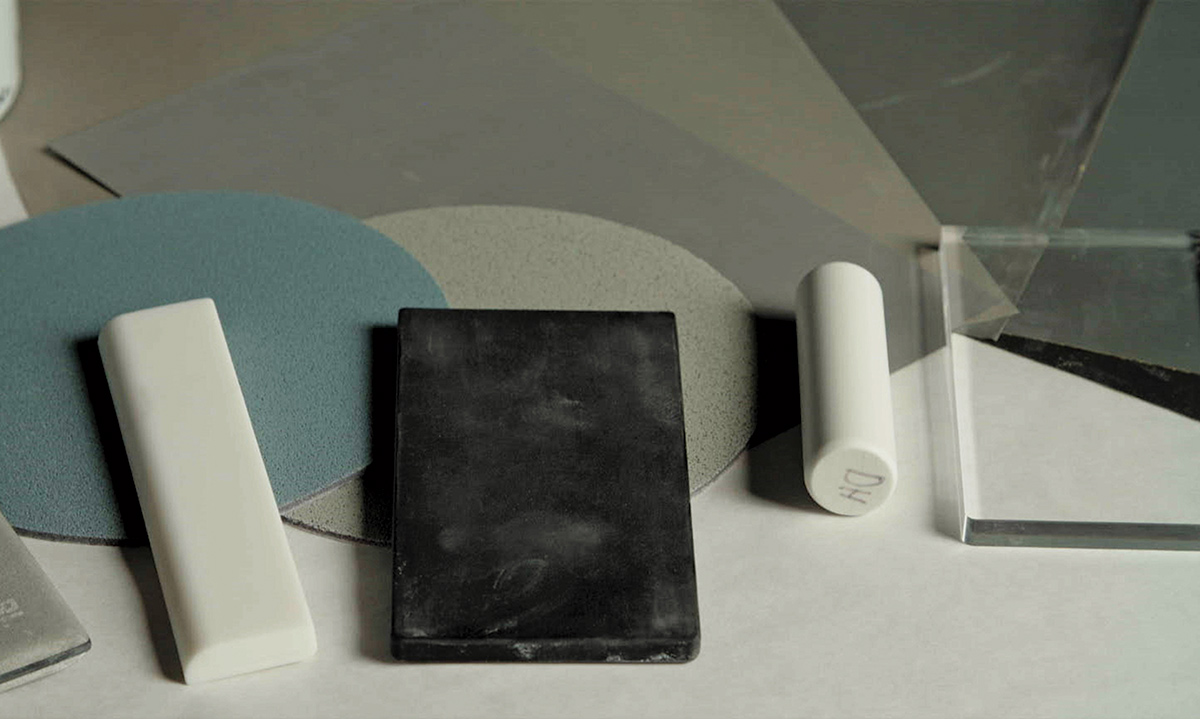

(208) 745-1350
VOLUME 4 • ISSUE 39 • 2023