Modern Rodding TECH
InTheGarageMedia.com
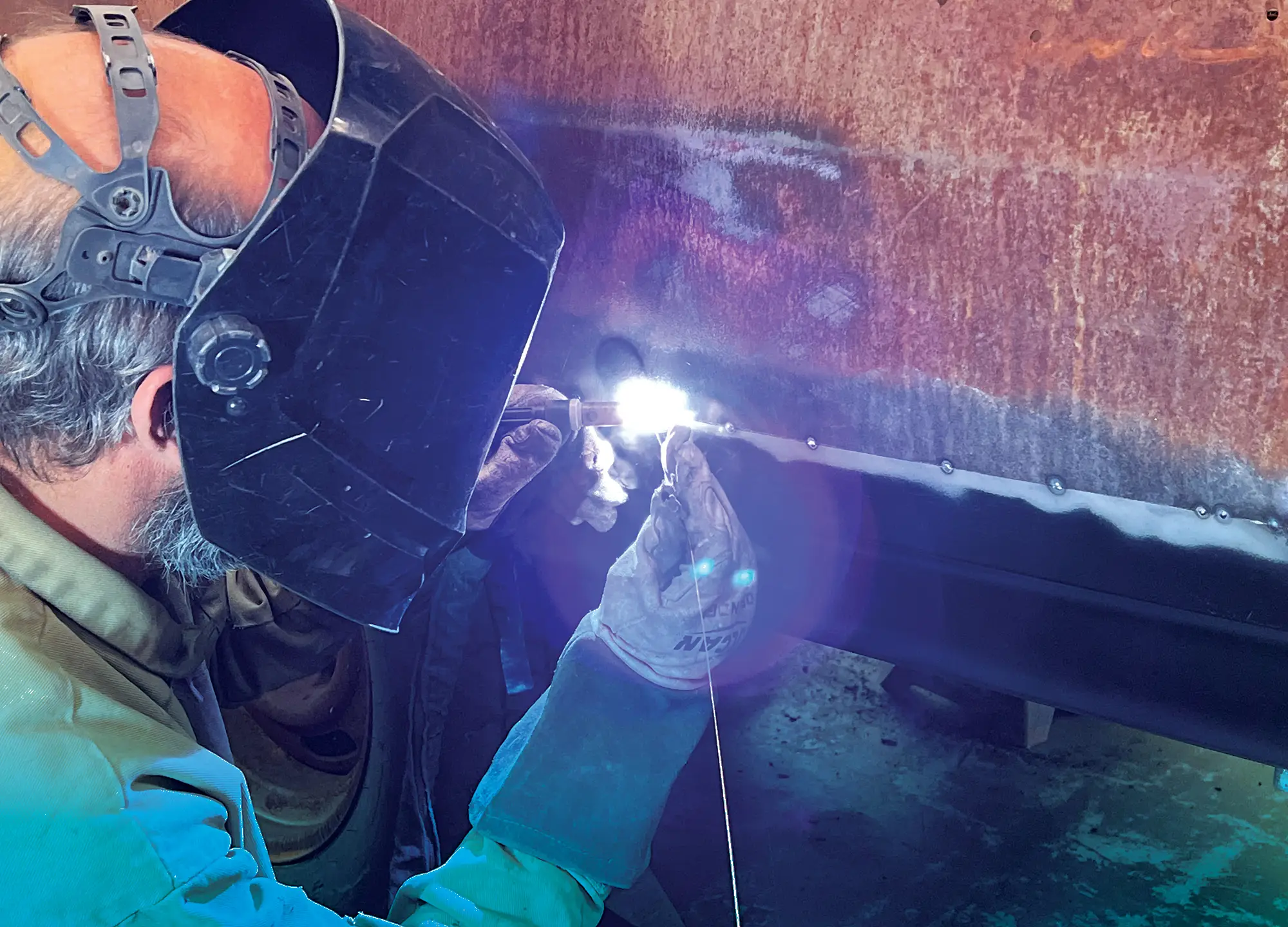
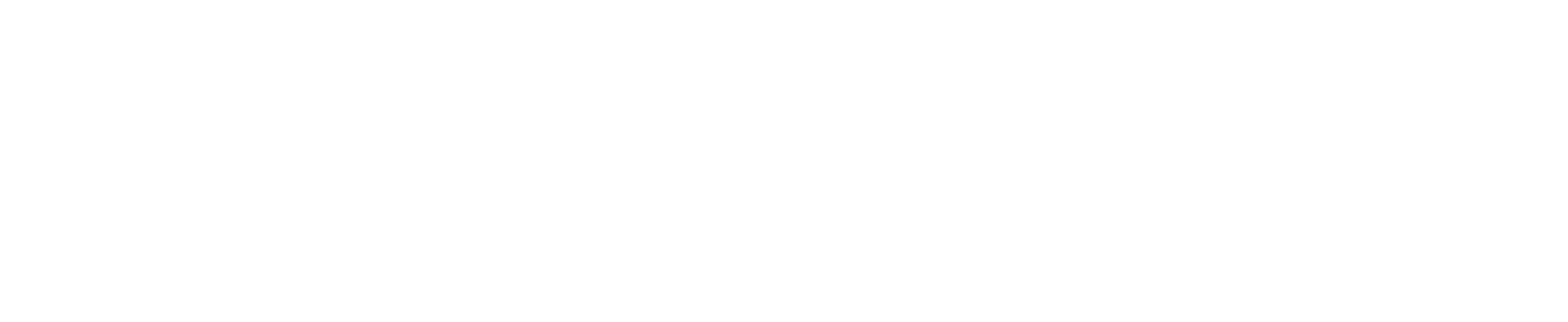

ust repair is often a part of any vintage car project. While it is possible to make a patch panel of any size and shape, there are ready-made panels available for a lot of popular cars, which can ease the job and save considerable time. Unless you are proficient at metal shaping, the ready-made patch panels are likely to have a better fit and finish than a handmade panel.
Hot Rods by Dean (HRBD), in Phoenix, was recently tasked with repairing rusted areas on the lower quarter-panel of a ’65 Chevelle and chose to use patch panels made by Golden Star Classic Auto Parts. Geoff Jones of HRBD is the man who did the installation, and as you will see the work was done in a very professional manner.
As you look through the photos, you’ll see each of the important steps needed to prepare, fit, and attach panels like these. For this job, the patch panels are joined with a butt joint and TIG welded, but the process would be very similar for an overlapped joint and for MIG welding. The flanges on the front and lower edges of this panel were originally spot-welded into place. A good way to reattach a new panel is to drill or punch a hole in the flange and plug weld through these holes into the metal behind the panel. Done properly, this will exceed the strength of a spot weld, and when ground down flush these plug welds become nearly invisible.
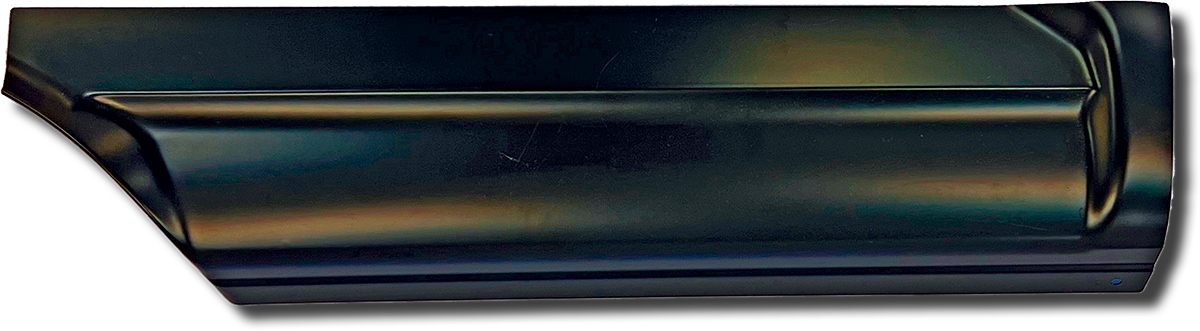
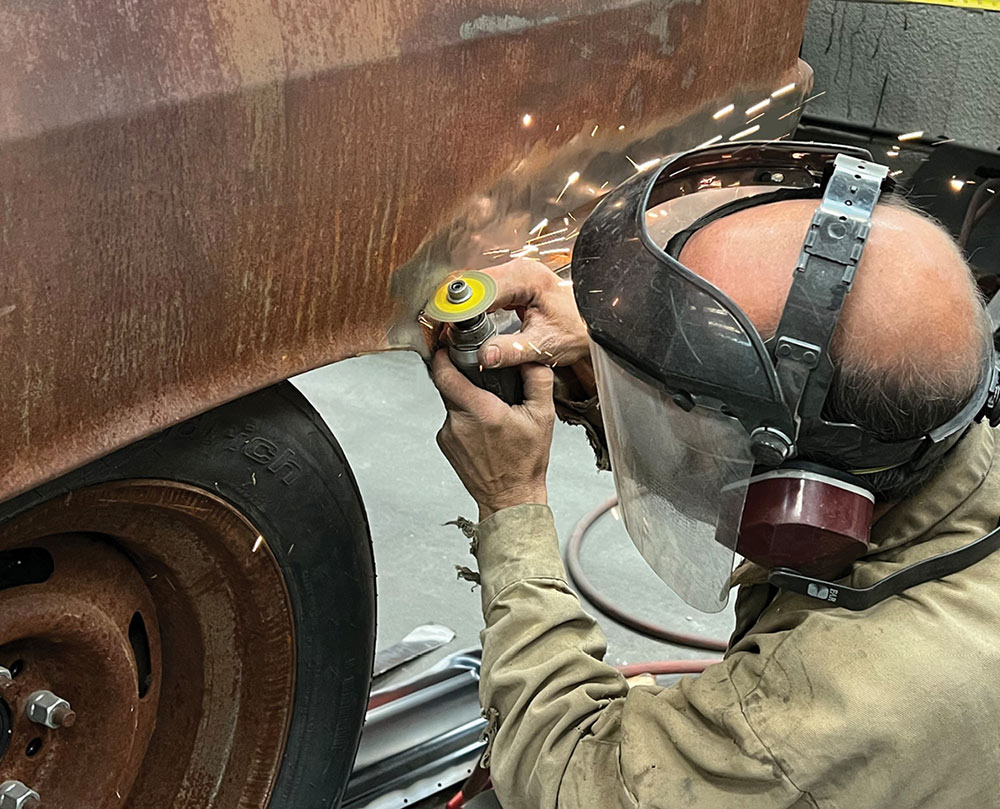
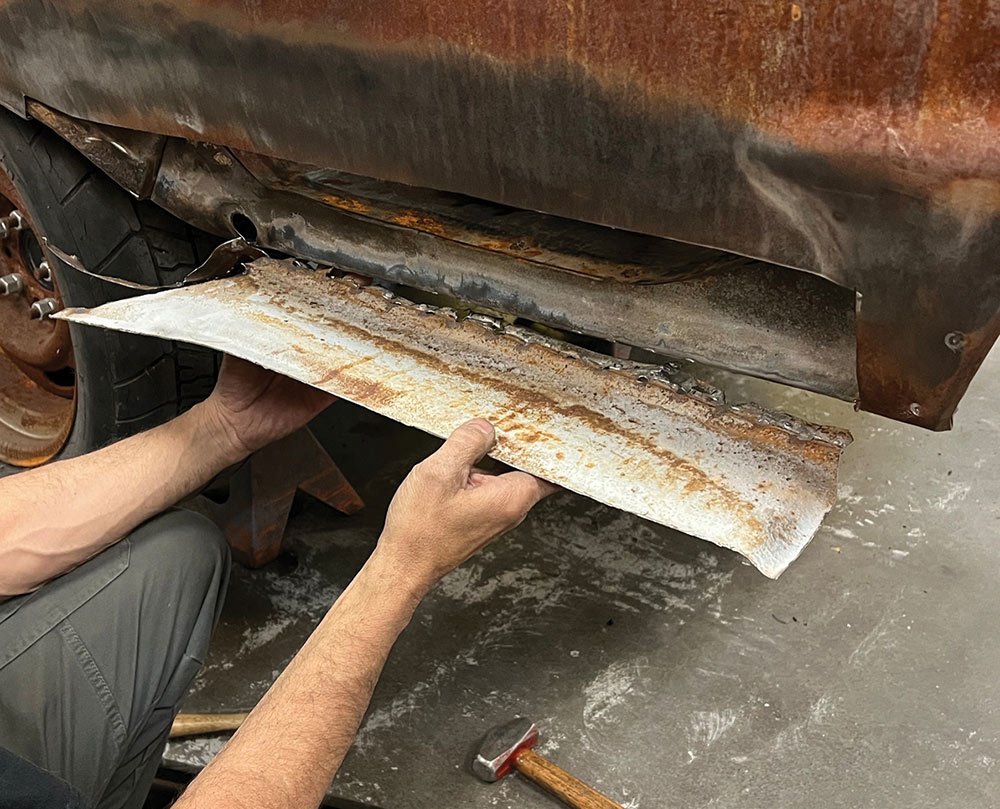
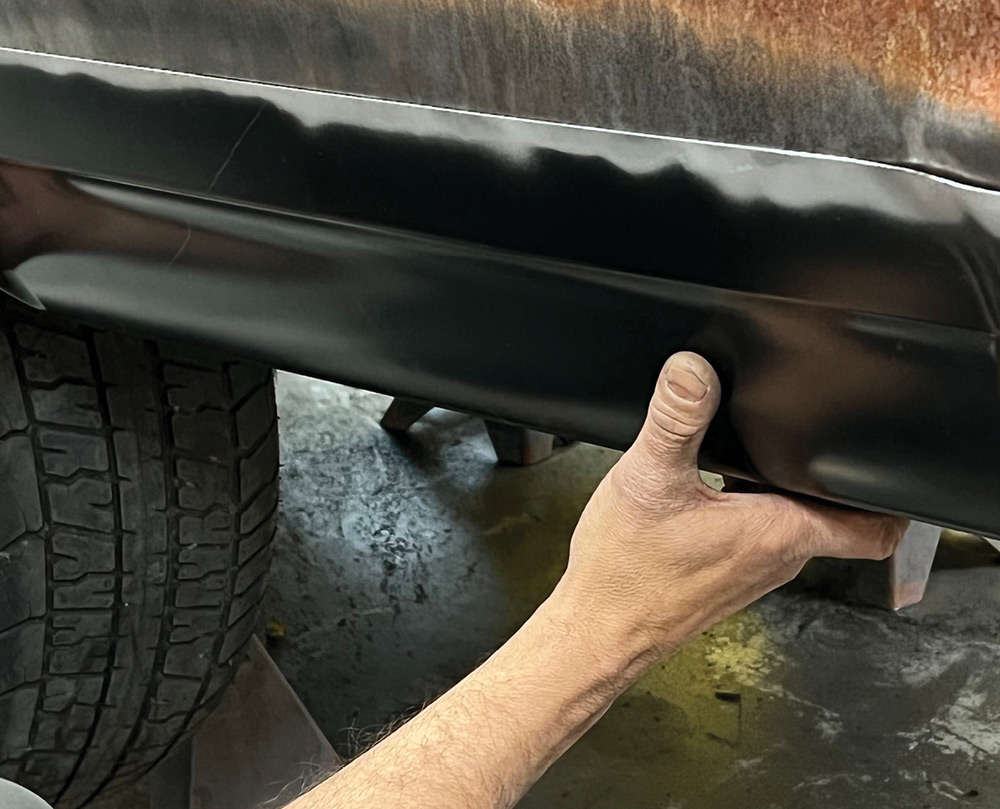
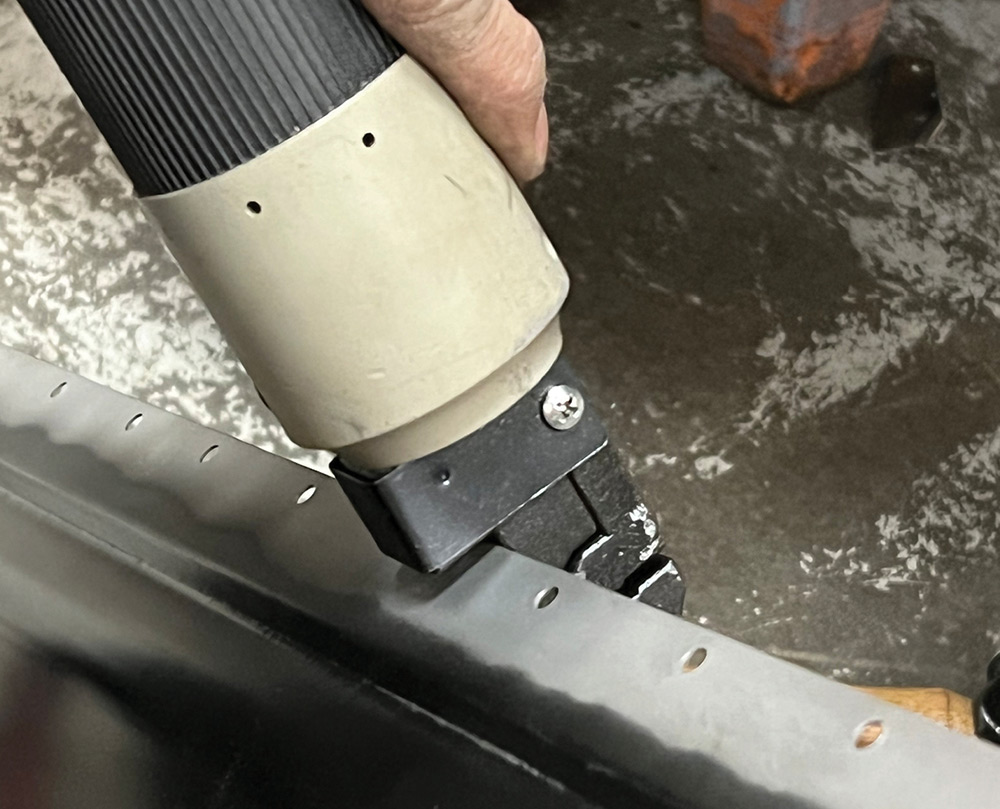
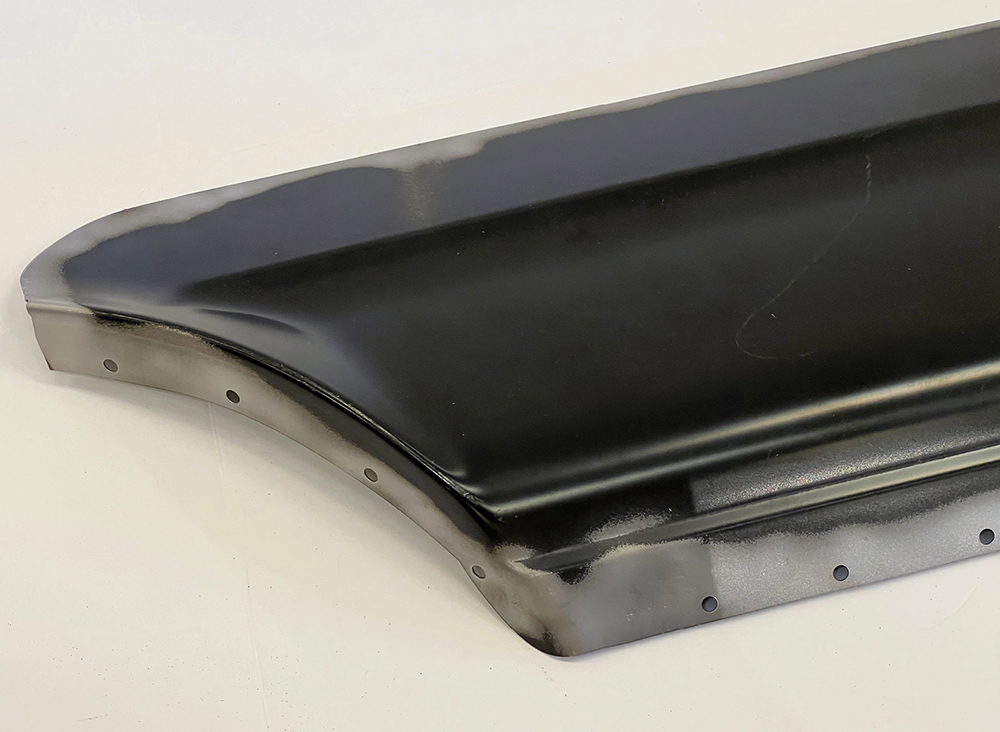
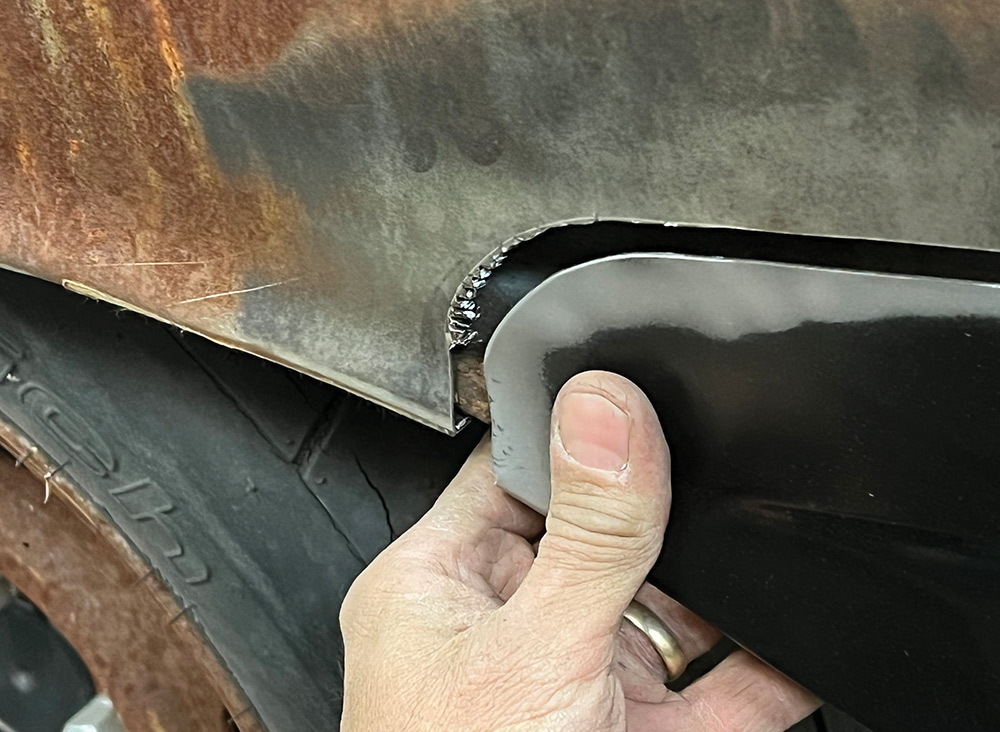
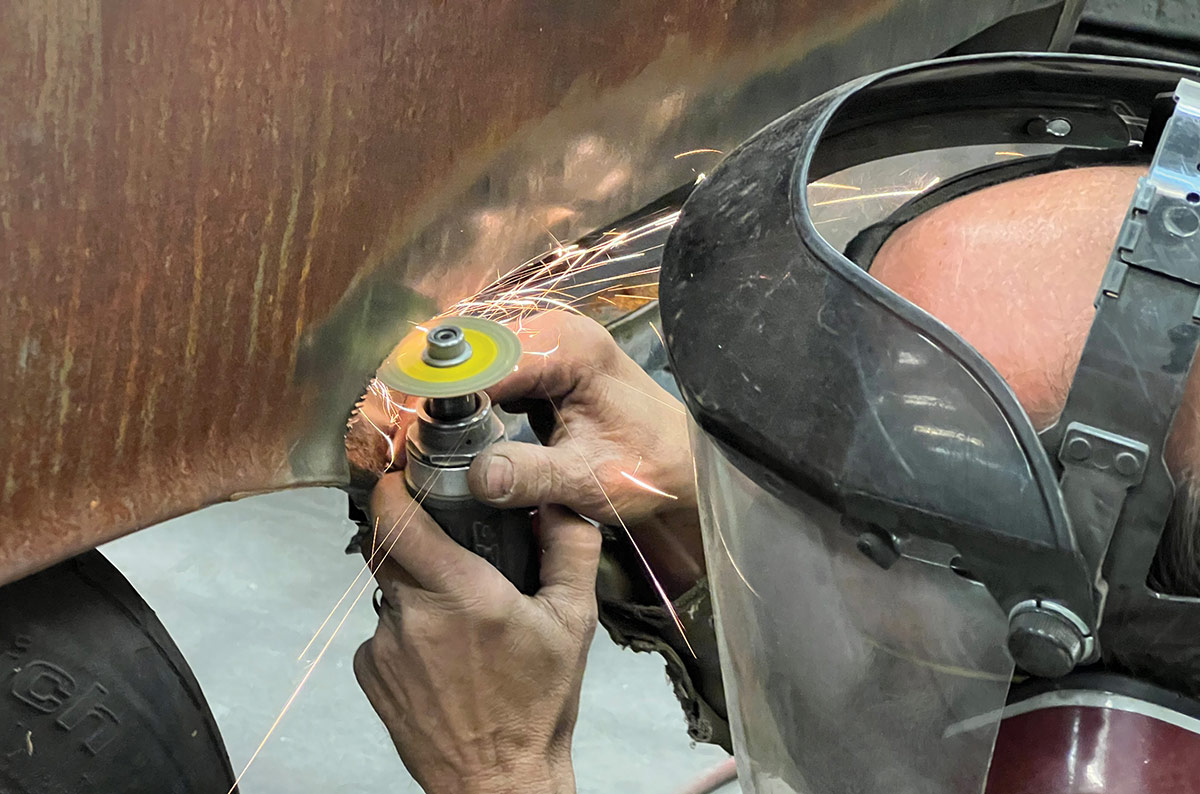

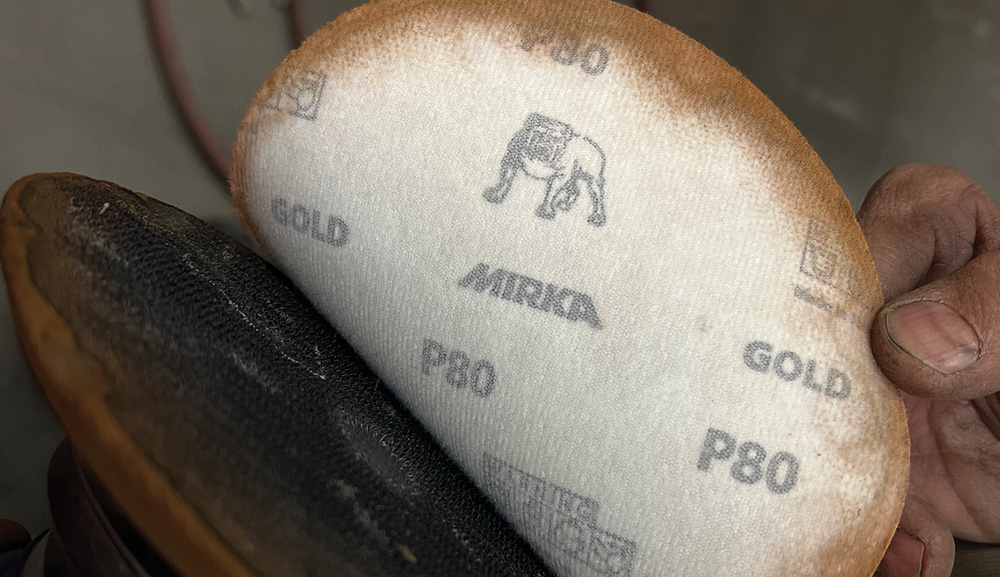




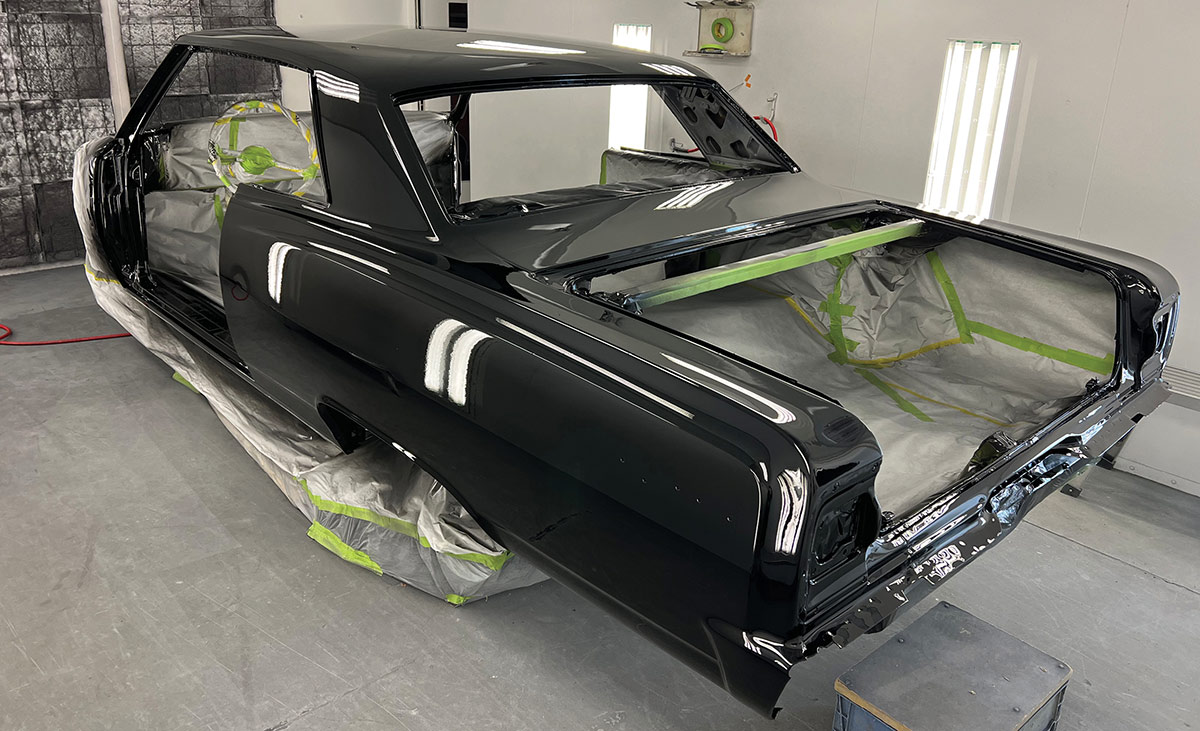

VOLUME 4 • ISSUE 39 • 2023