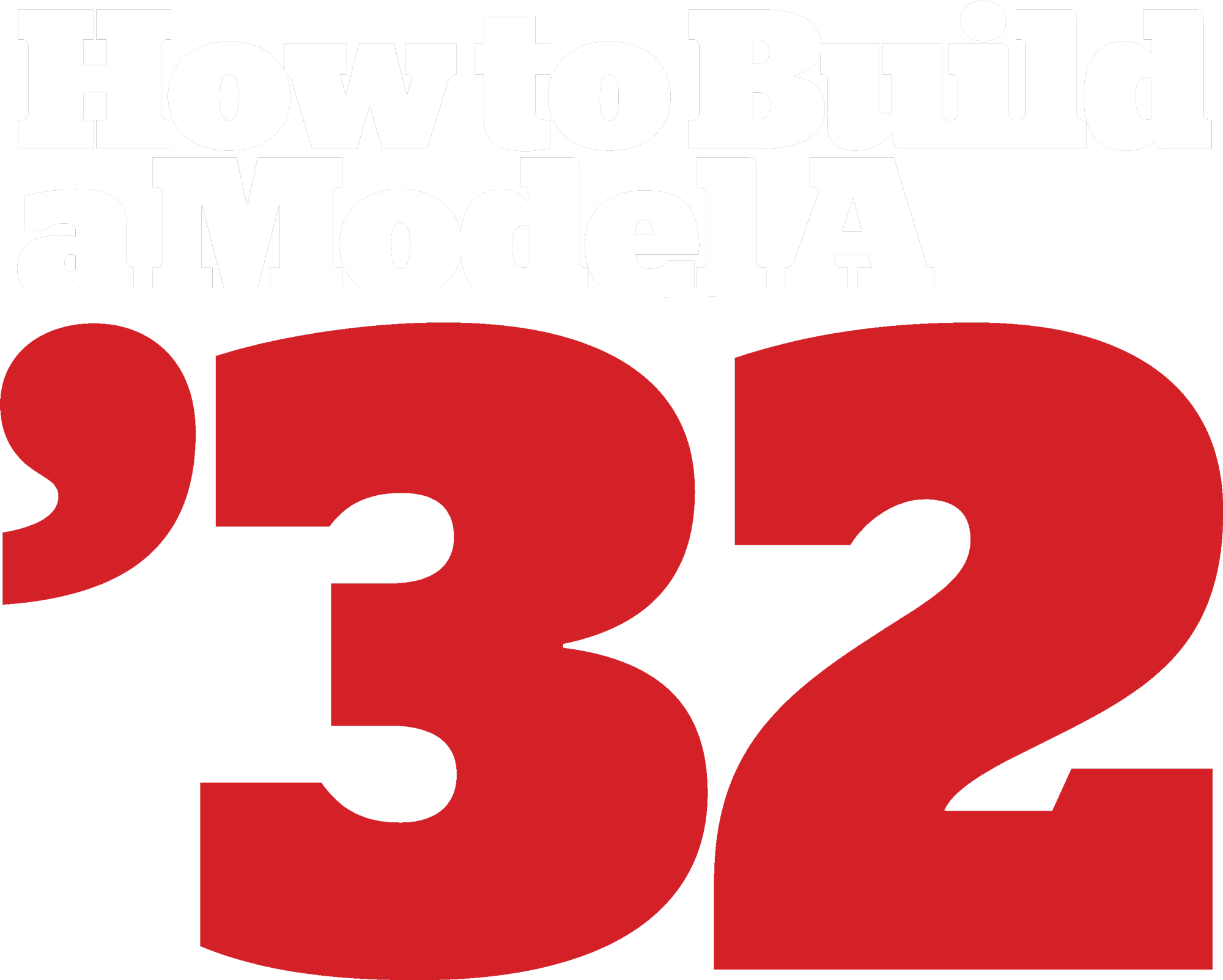

very hot rodder knows one of the most special things about the ’32 Ford is it has many one-year-only features. Designer Eugene “Bob” Gregorie was tapped by none other than Edsel Ford to be in charge of the new look Ford vehicles would soon take, which would use both streamline and European styling cues.
In the early ’30s, vehicle manufacturers would introduce new looks almost every year, setting themselves apart from their competition, and Ford was no different. The look of Fords from 1931 to 1937 drastically changed seven times in that short time span, and it was an abrupt change each time. Whereas there wasn’t much of a radical change between 1933 and 1934, the changes between the ’31 Model A and the ’32 Ford five-window are pretty obvious.
So, when Derryll Gehring, the owner of a ’31 Model A coupe (a car he has owned since he was 15) stopped in to talk to Paul Bosserman of Old Anvil Speed Shop in Orange, California, about a chop for his soon-to-be hot rod, the talk soon turned to adding a ’32 five-window roof to the A as well as the chop.
Though this modification has only been attempted a couple of times in the past by a few builders, there certainly wasn’t a template to go by, nearly all of this work was going to be done by eye—in other words what looked right to Bosserman. At first Bosserman thought he’d be using most of the new top section but, as work progressed, he discovered that much of the original Model A roof could be retained.
The work was done in three stages: first the rear section (from the B posts back) was chopped, which was a pretty straightforward task. But the tricky part was determining not only where the transition would be from the roof to the door top, but if it would be the Model A or the ’32 piece.
Bosserman was surprised on how close the ’32 roof fit to the old Model A roof—like hand-to-glove in many areas. It turned out the ’32 roof would be cut into four sections: the piece above the windshield, the left and right door top sections, and the middle section (the whole rear section of the ’32 with the window was not used at all).
What turned out to be true is the amount of work it took to get this roof redo to look “right” might not yield the response from the general public it deserves. It’s so subtle only die-hard ’32 or Model A fanatics will get what happened, and chances are they’ll only see a portion of it—the work really is just that subtle.
This is Part 1 of 2 on how it was done and how the work evolved as Bosserman surgically added and took away just the right amount of metal to create a chopped ’31-1/2 Model A.
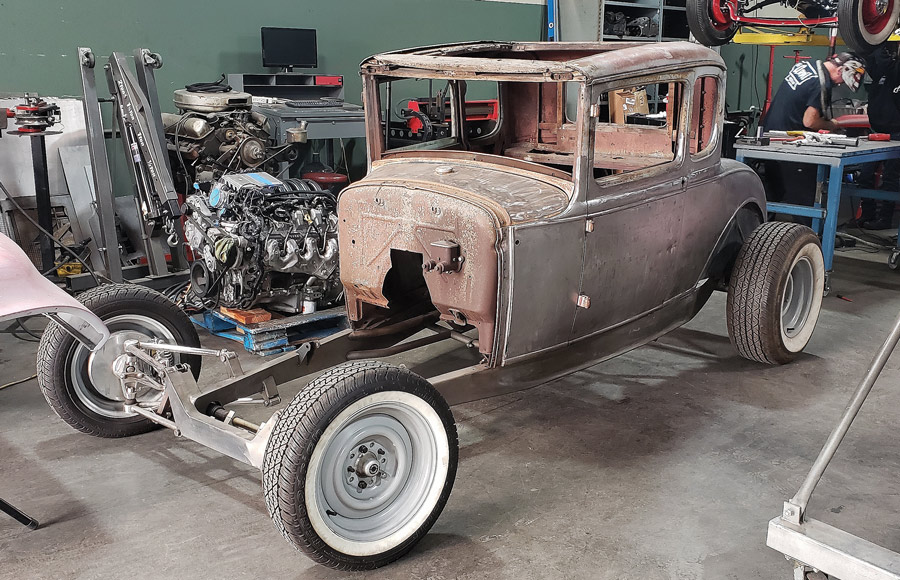
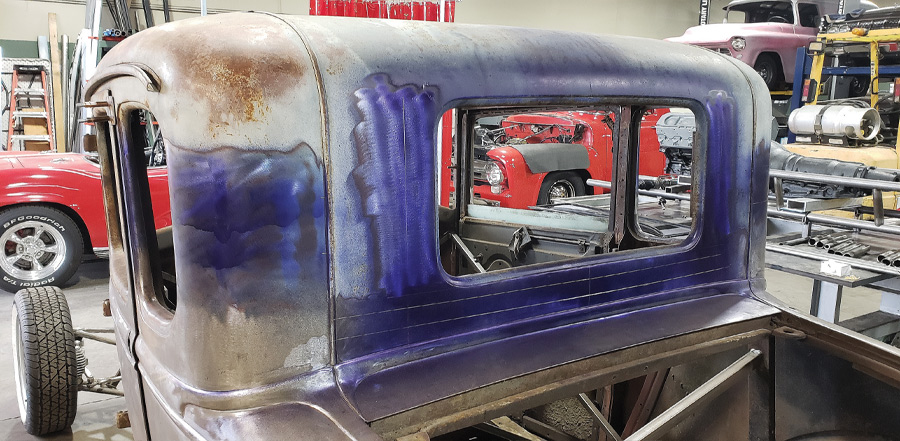
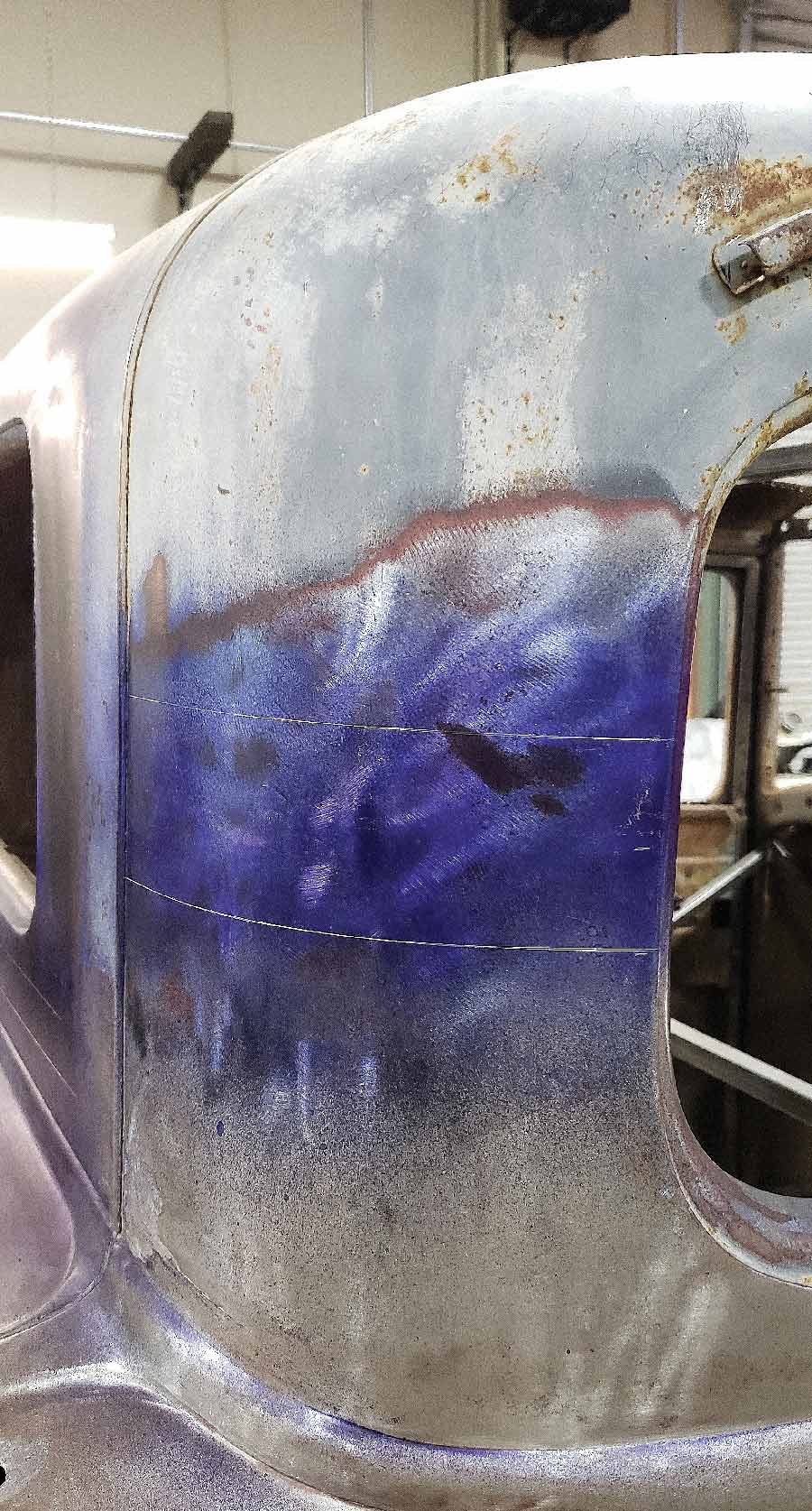
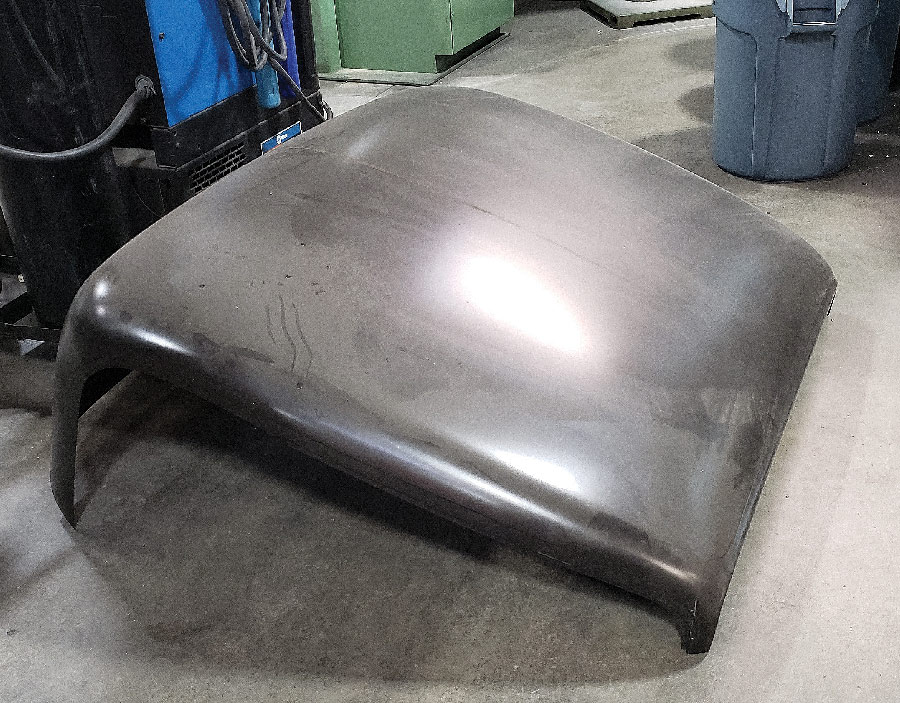
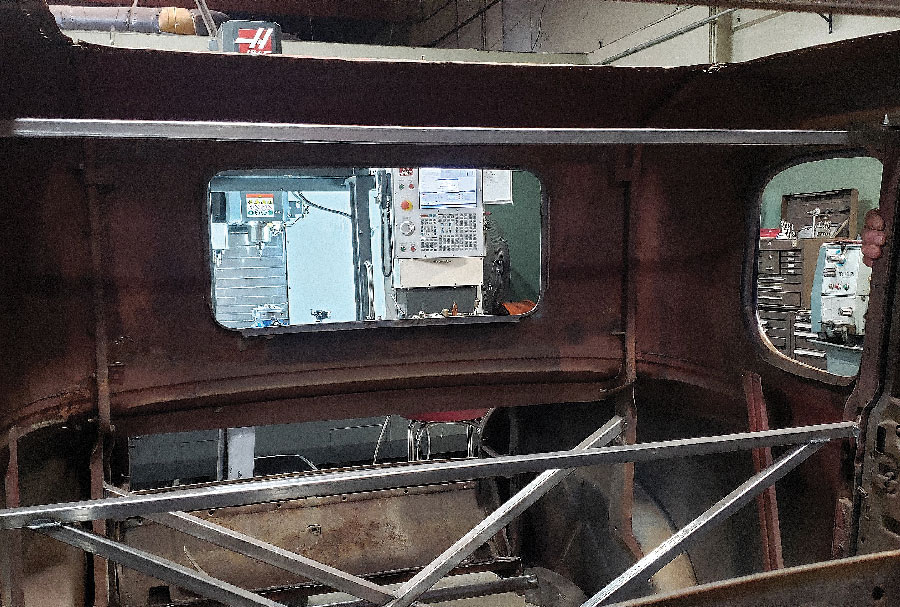
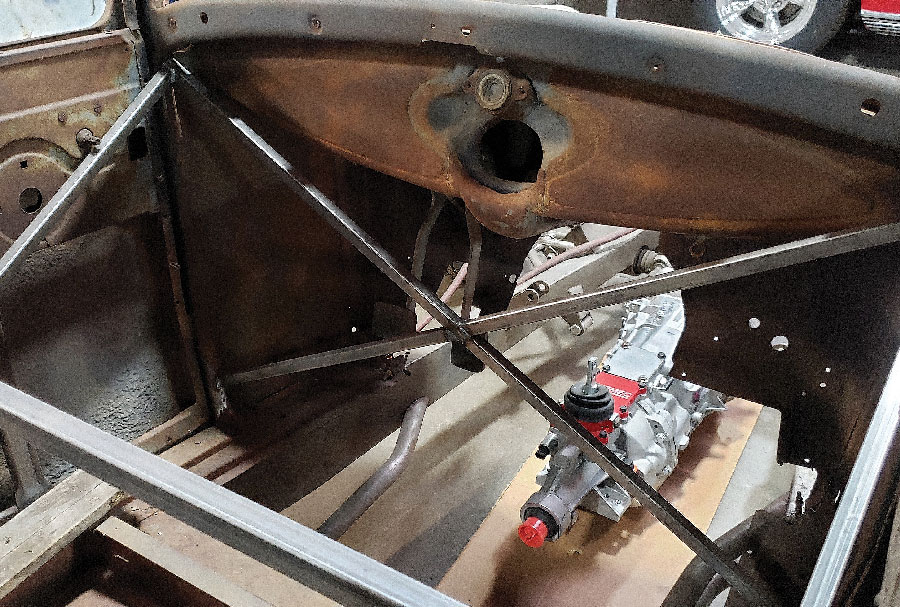
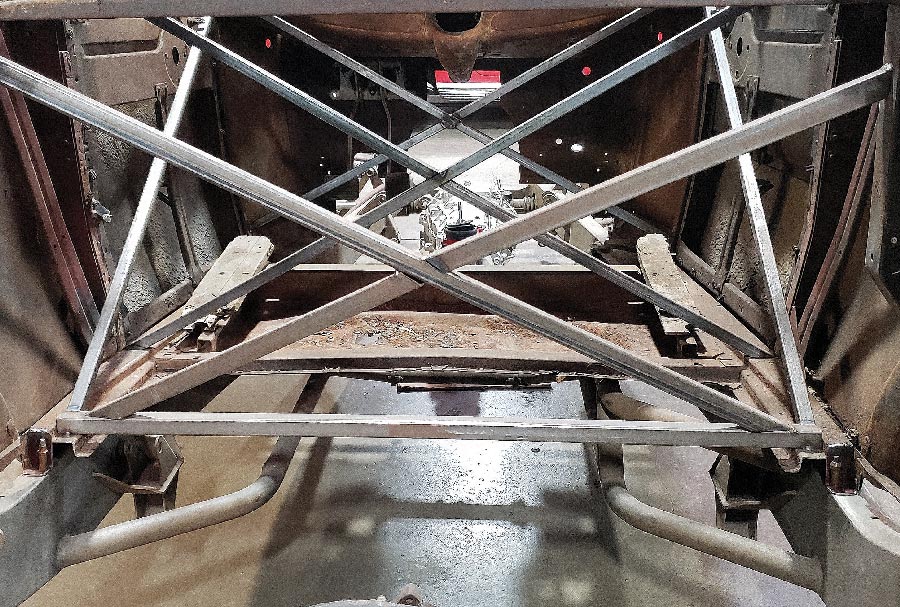
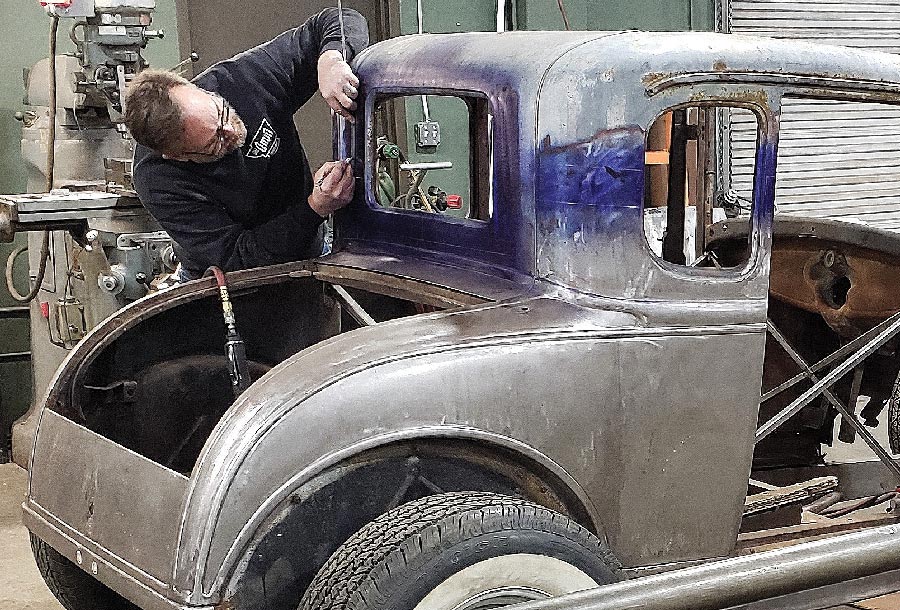
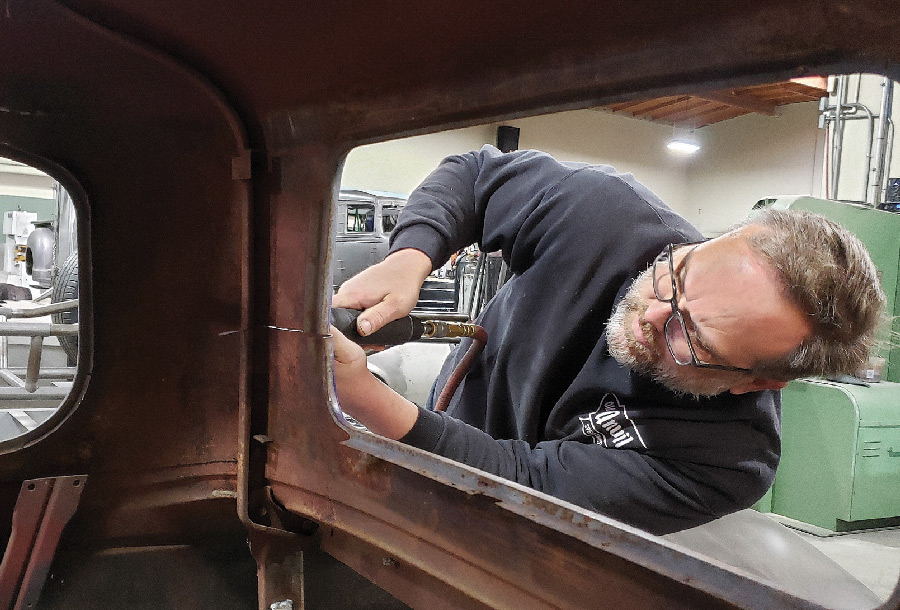
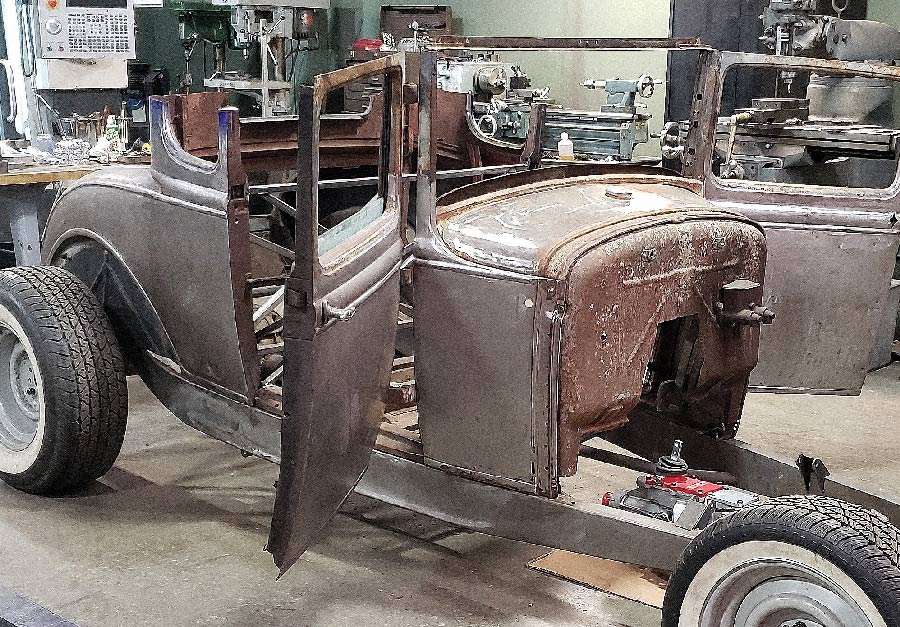
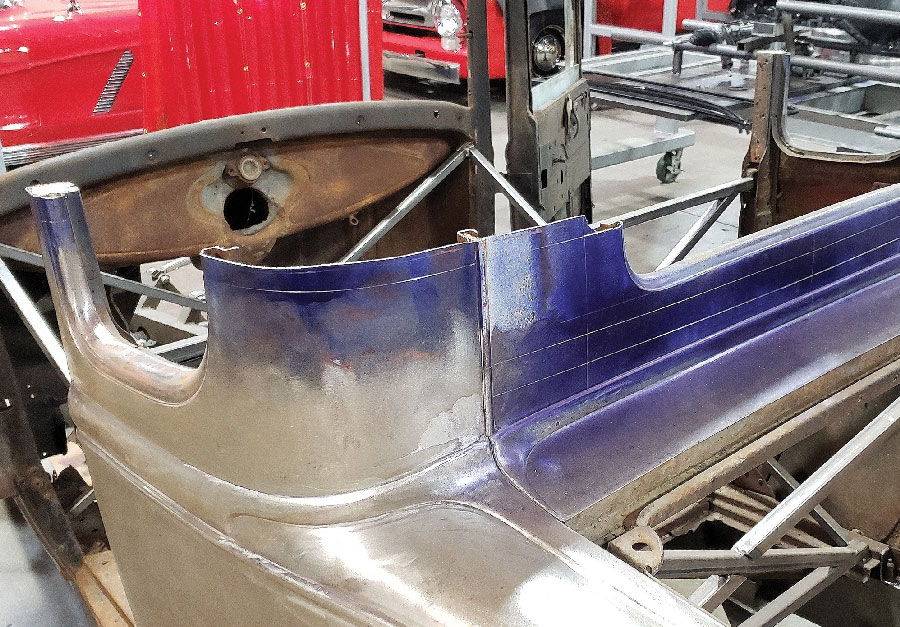
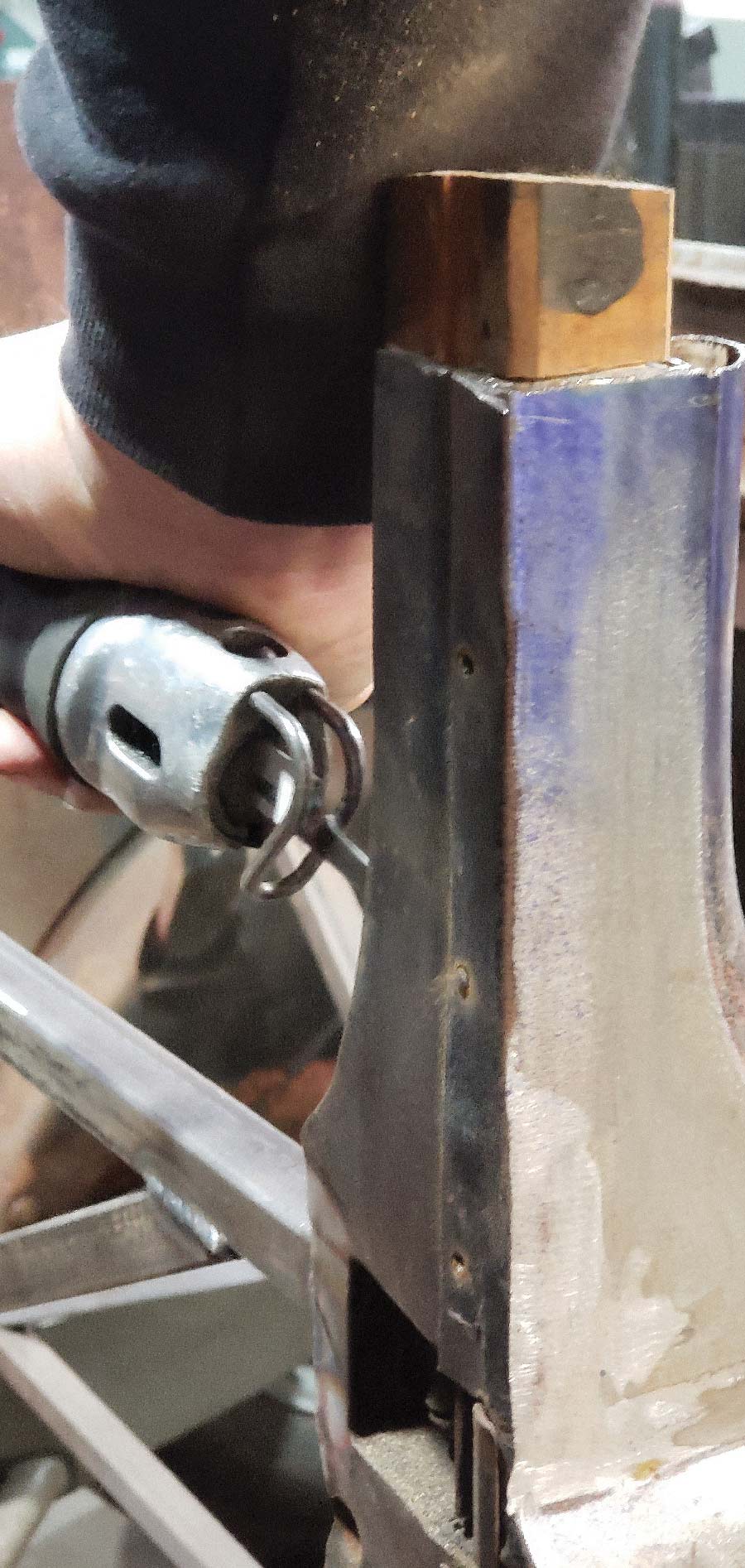
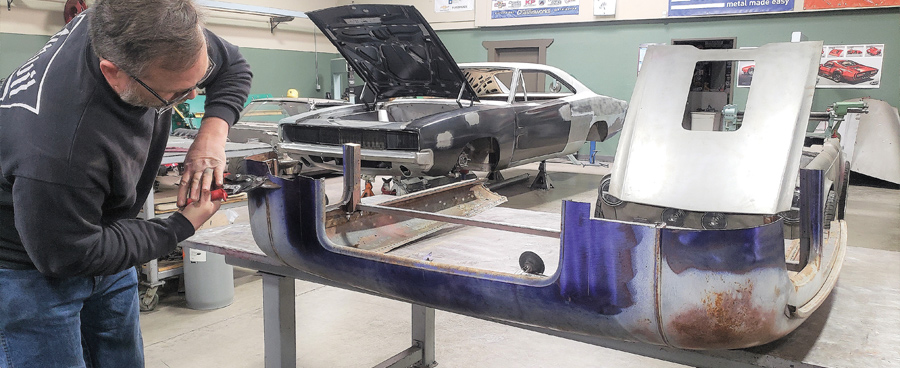
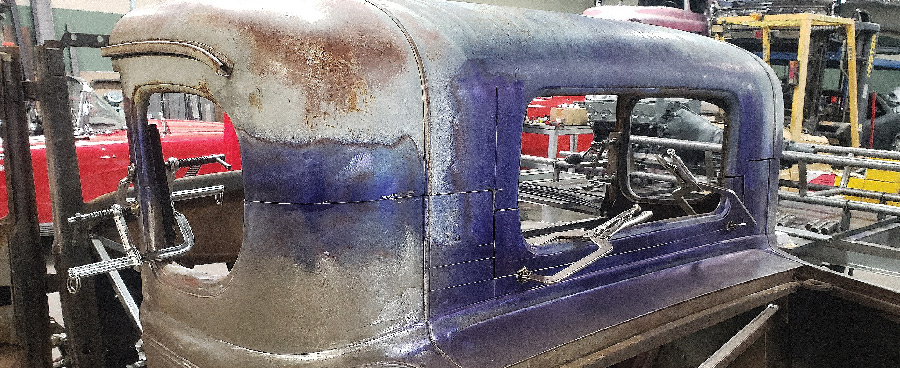
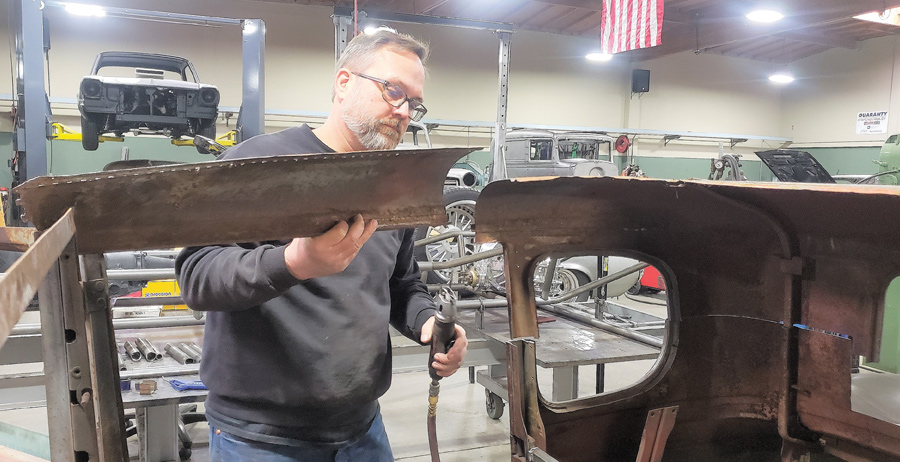
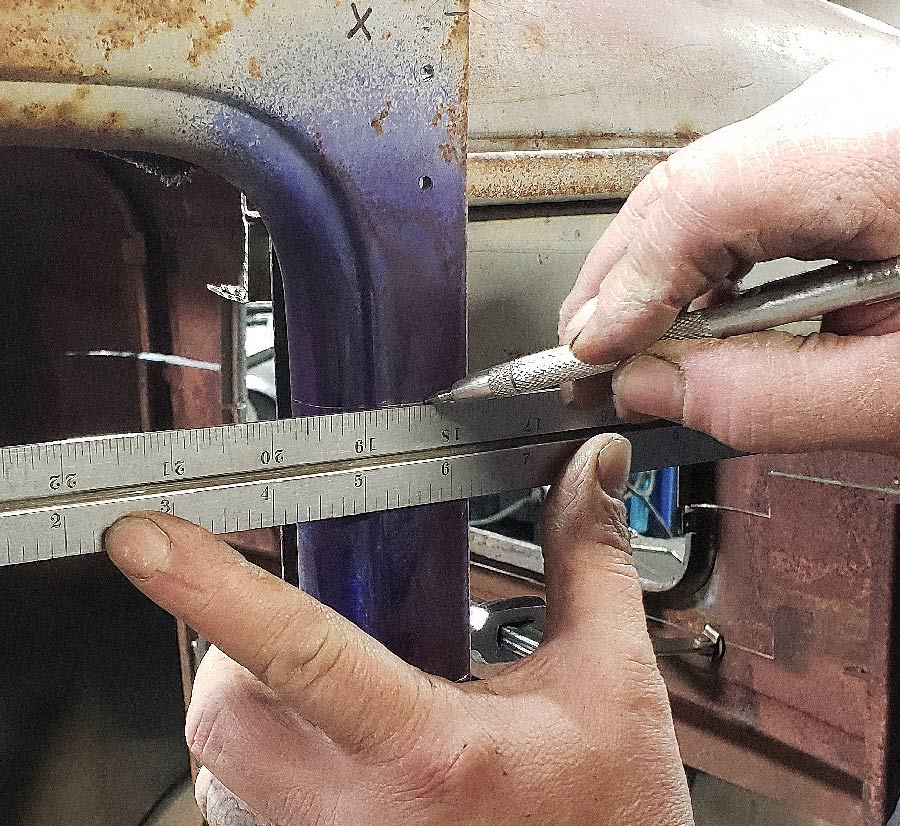
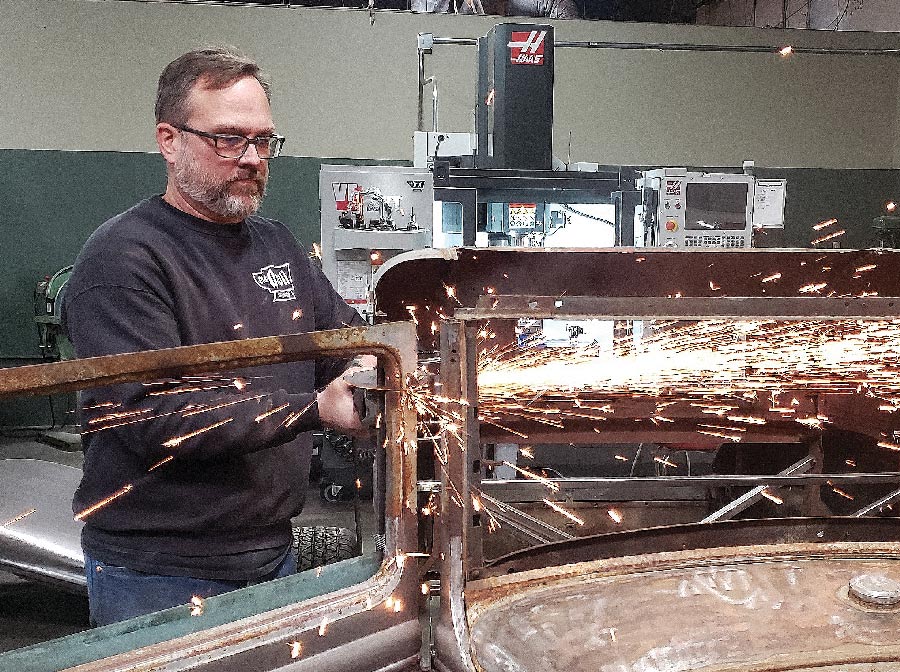
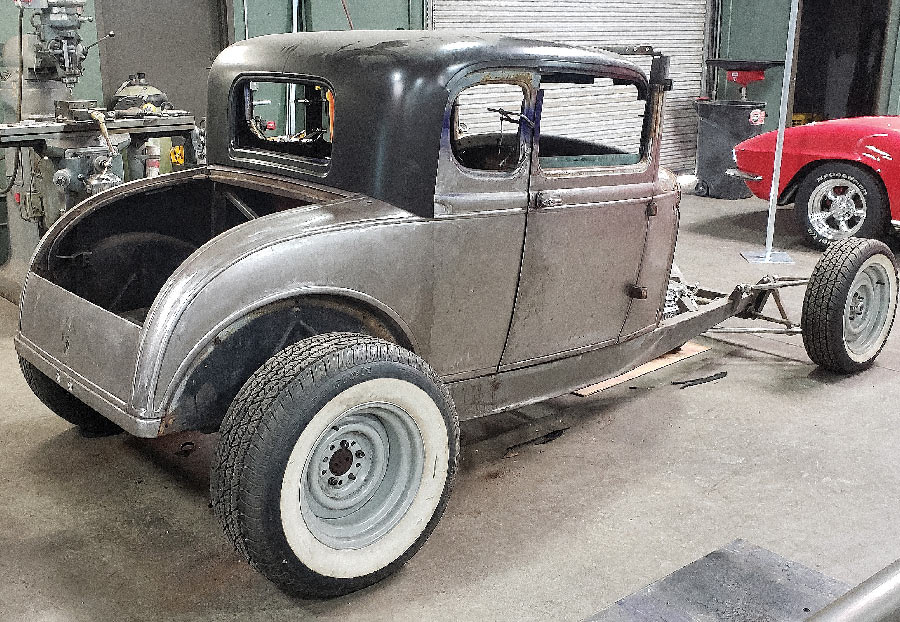
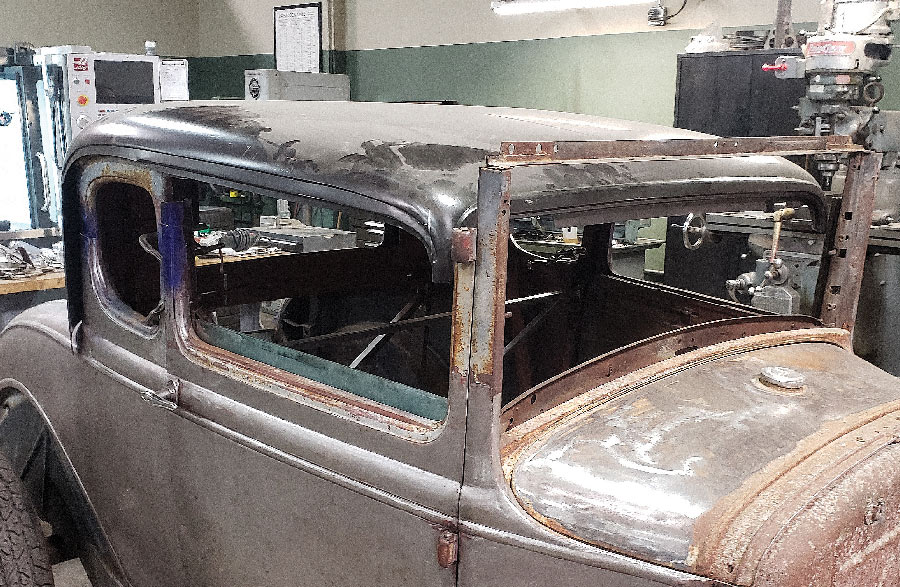
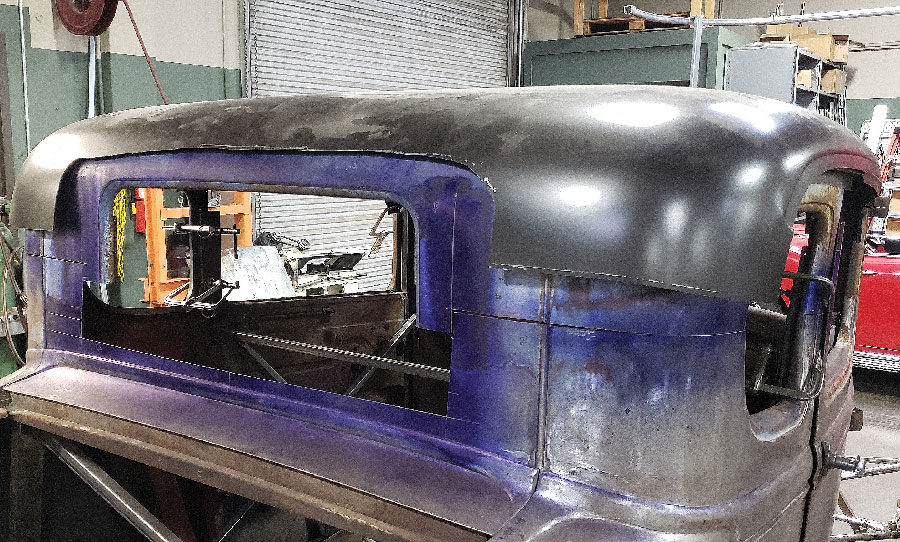
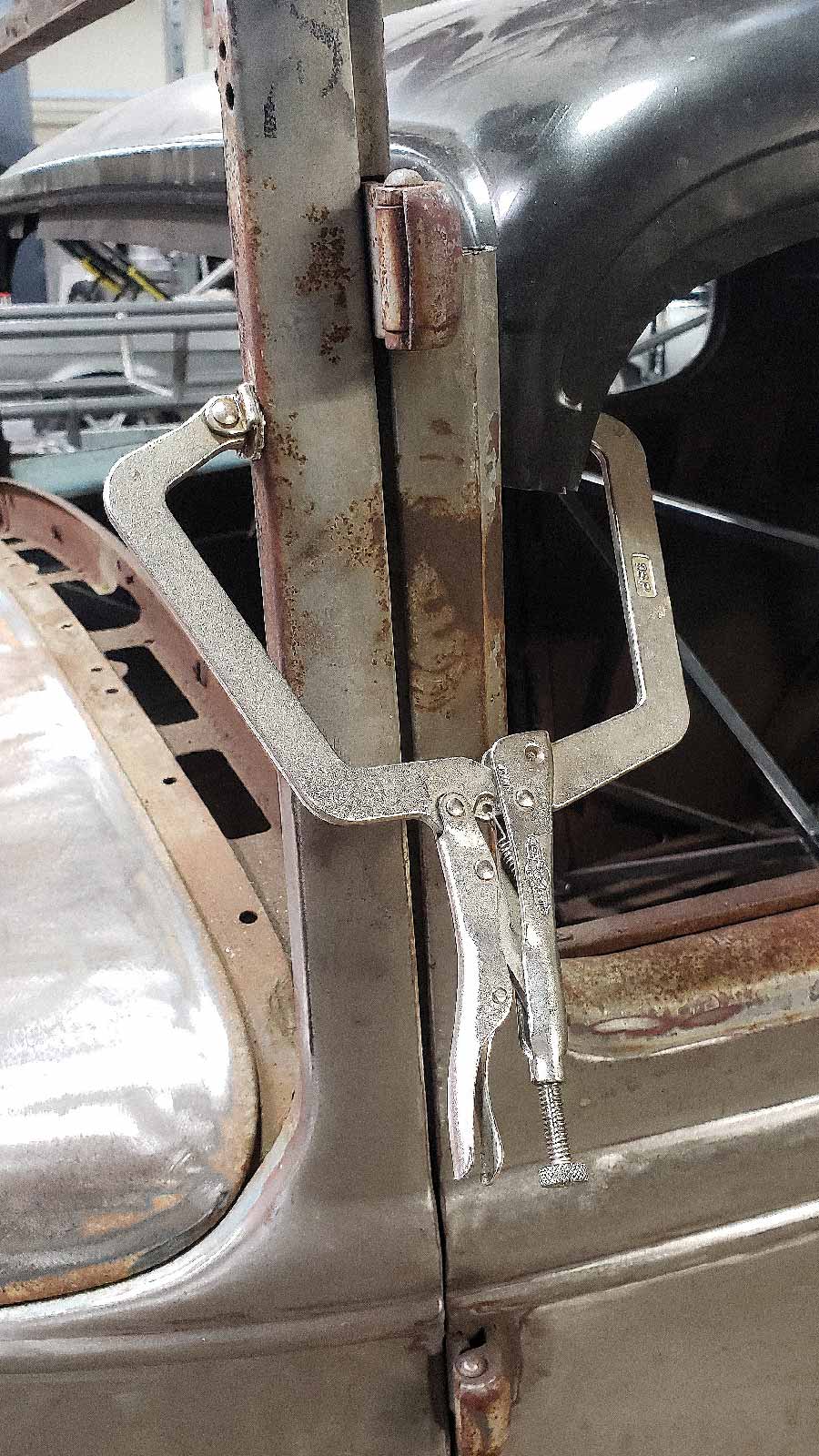
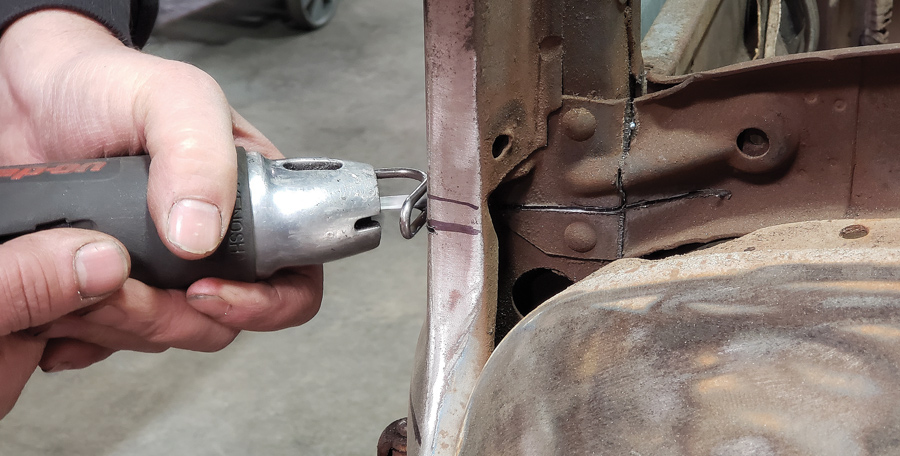
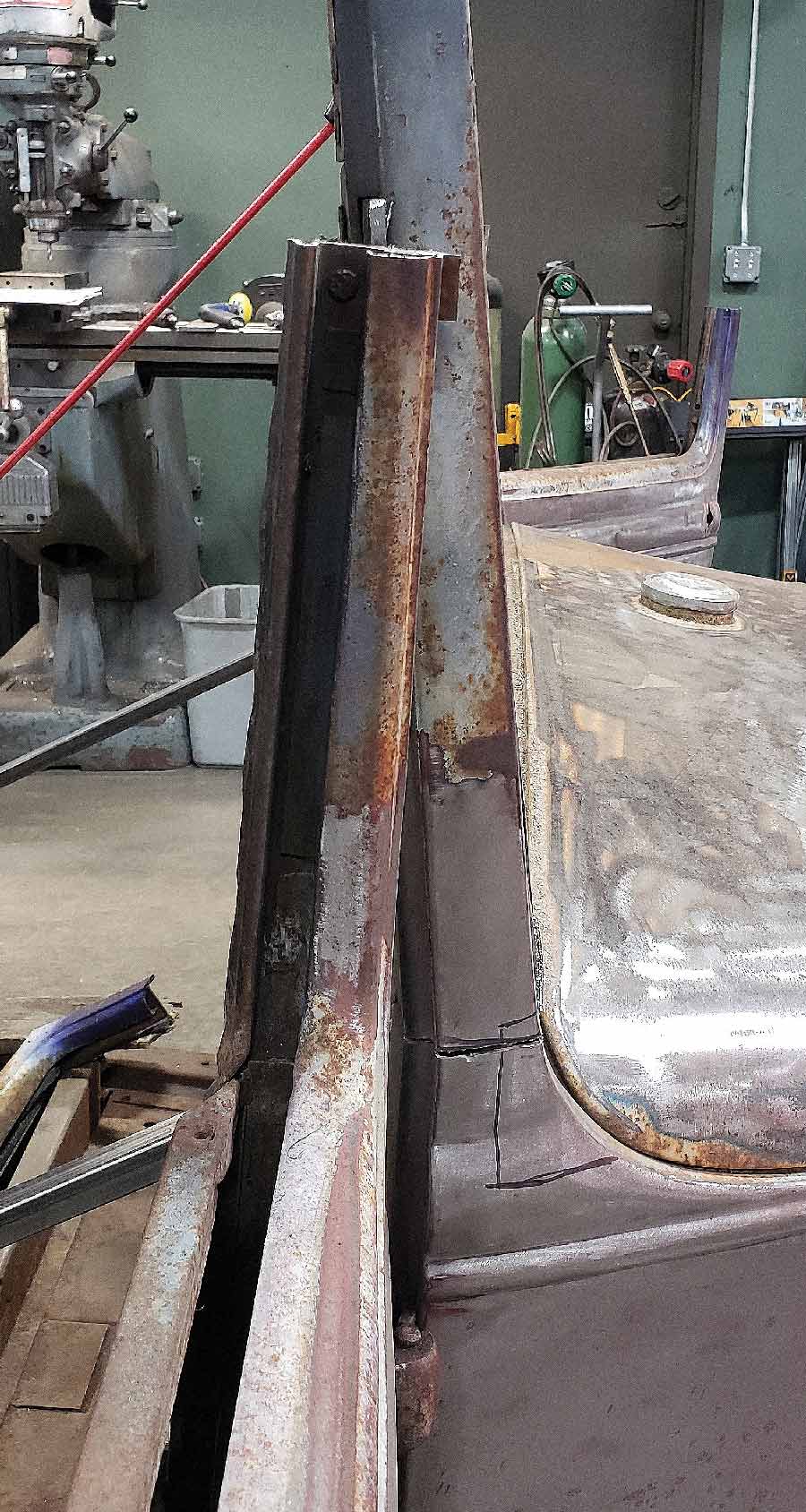
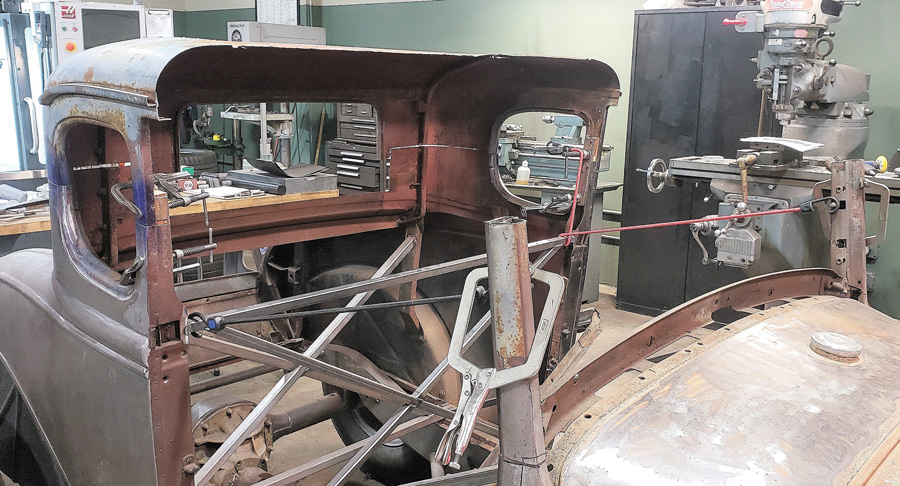
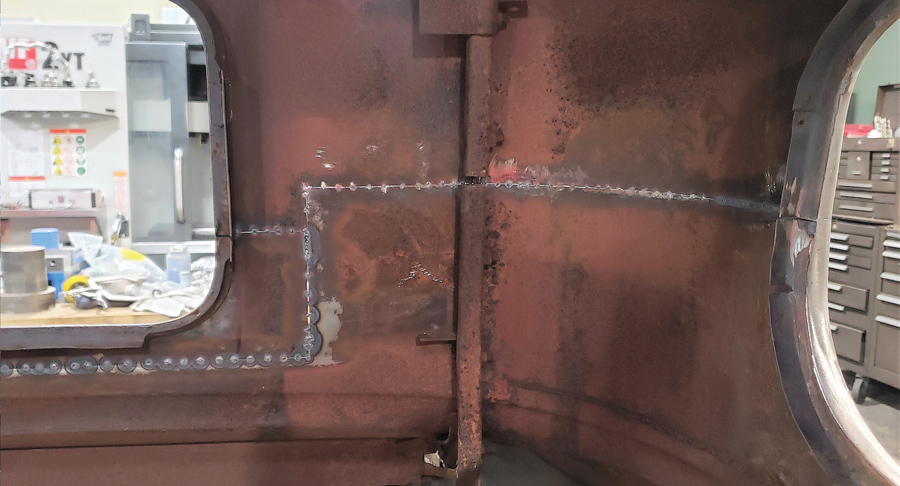
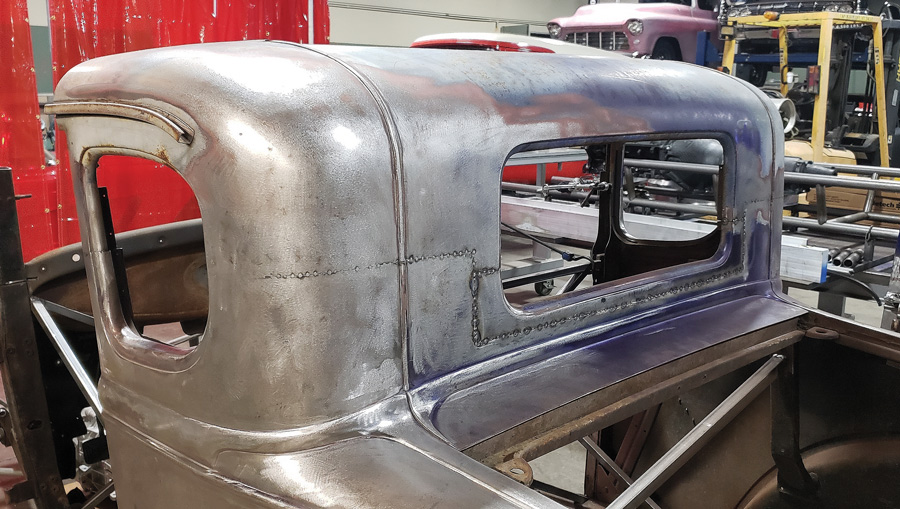
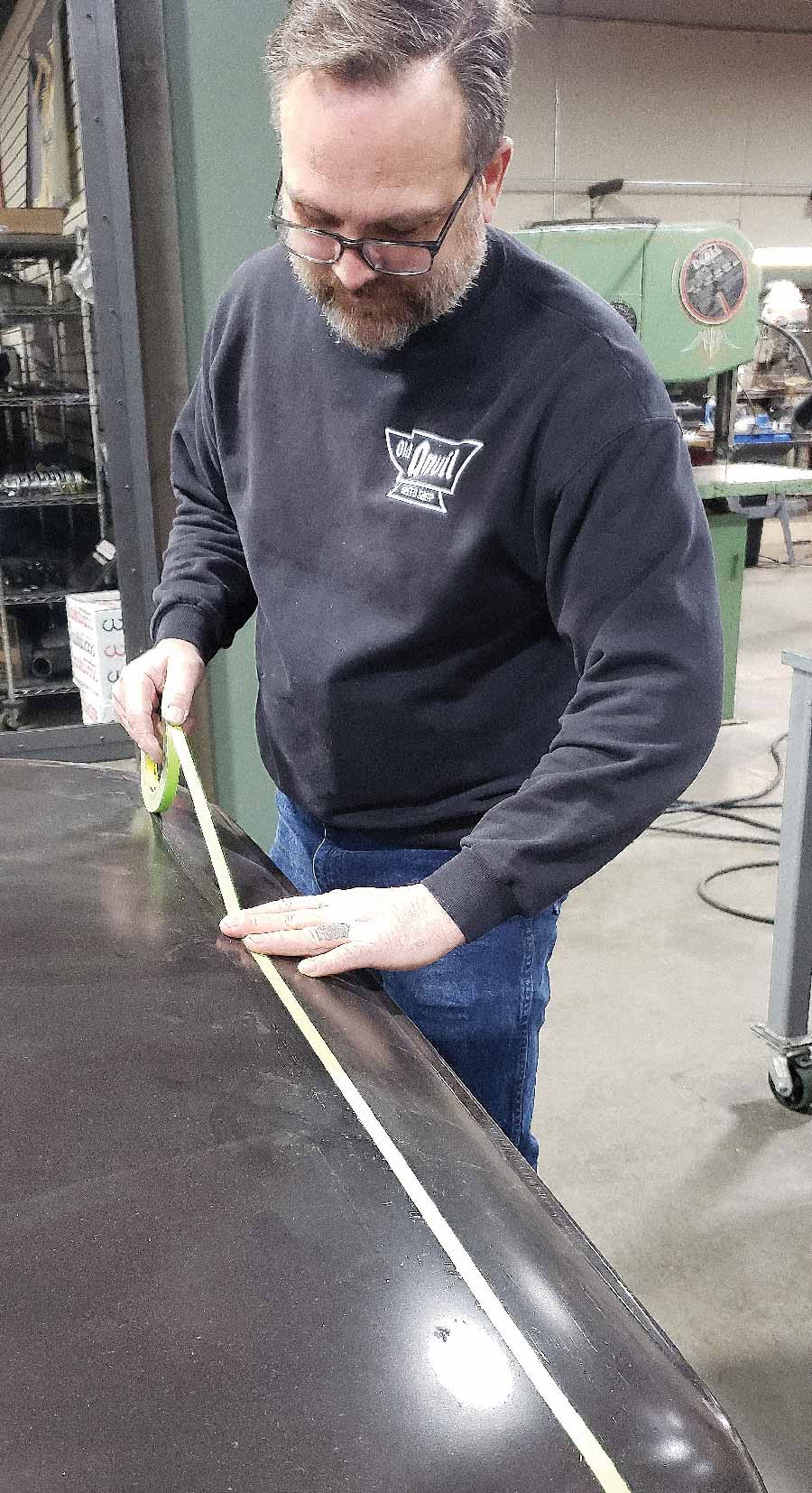
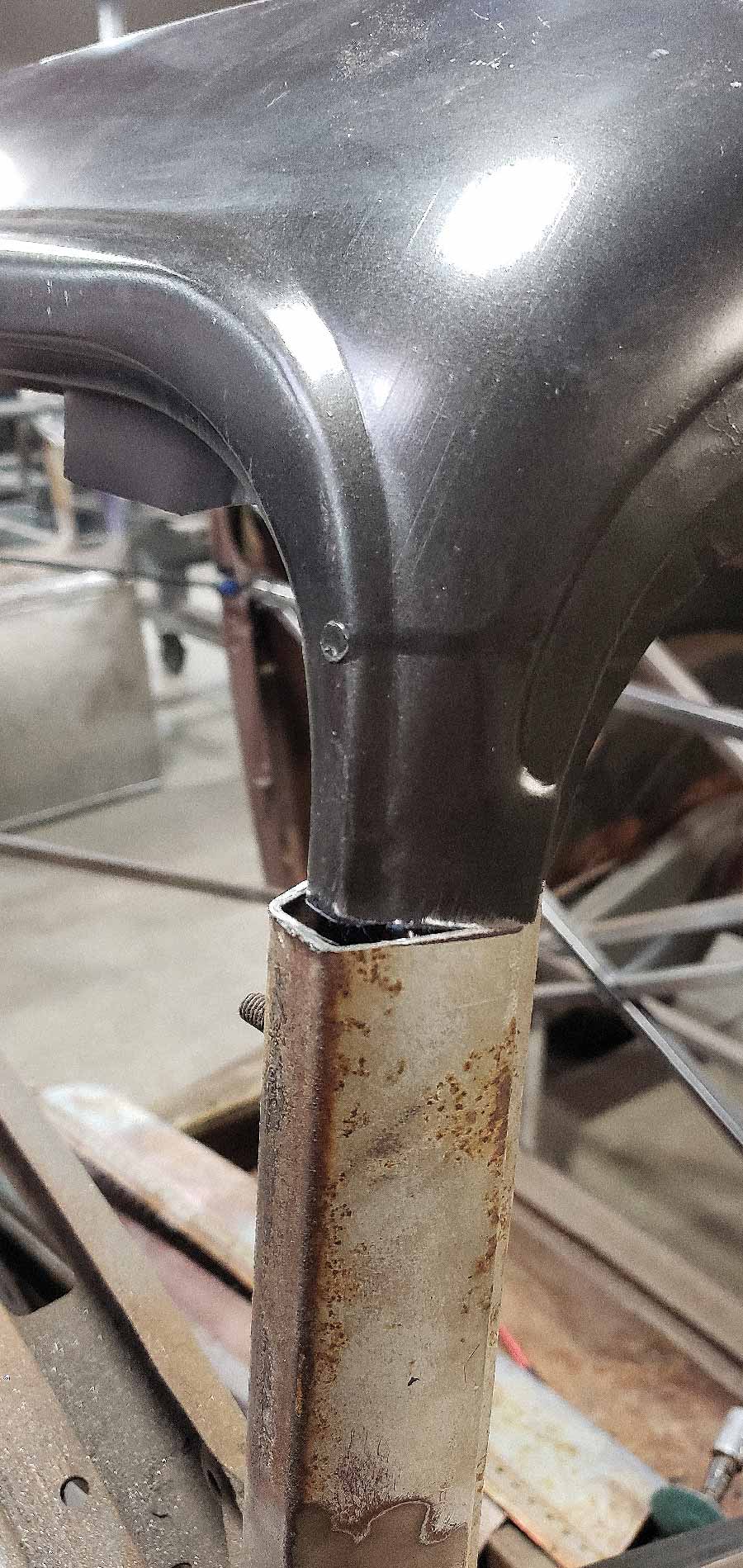
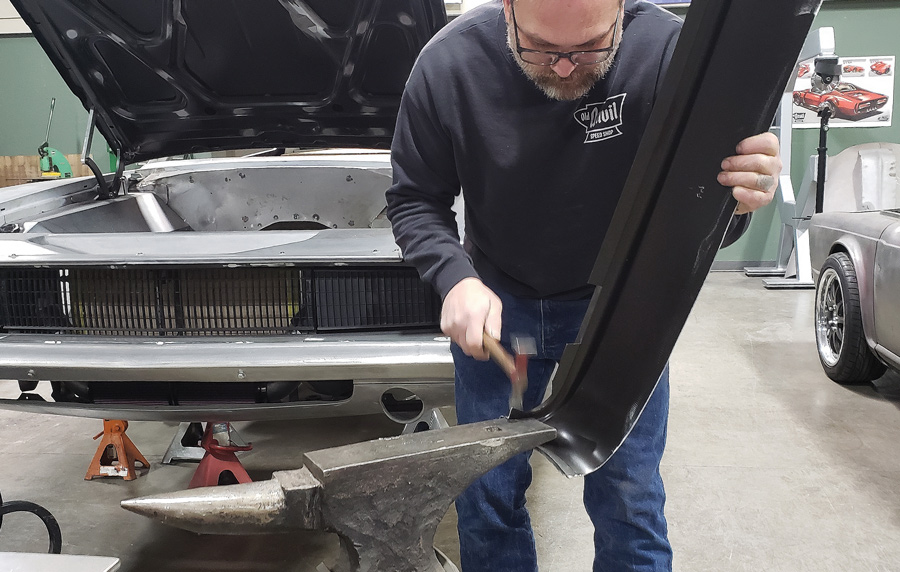
