InTheGarageMedia.com
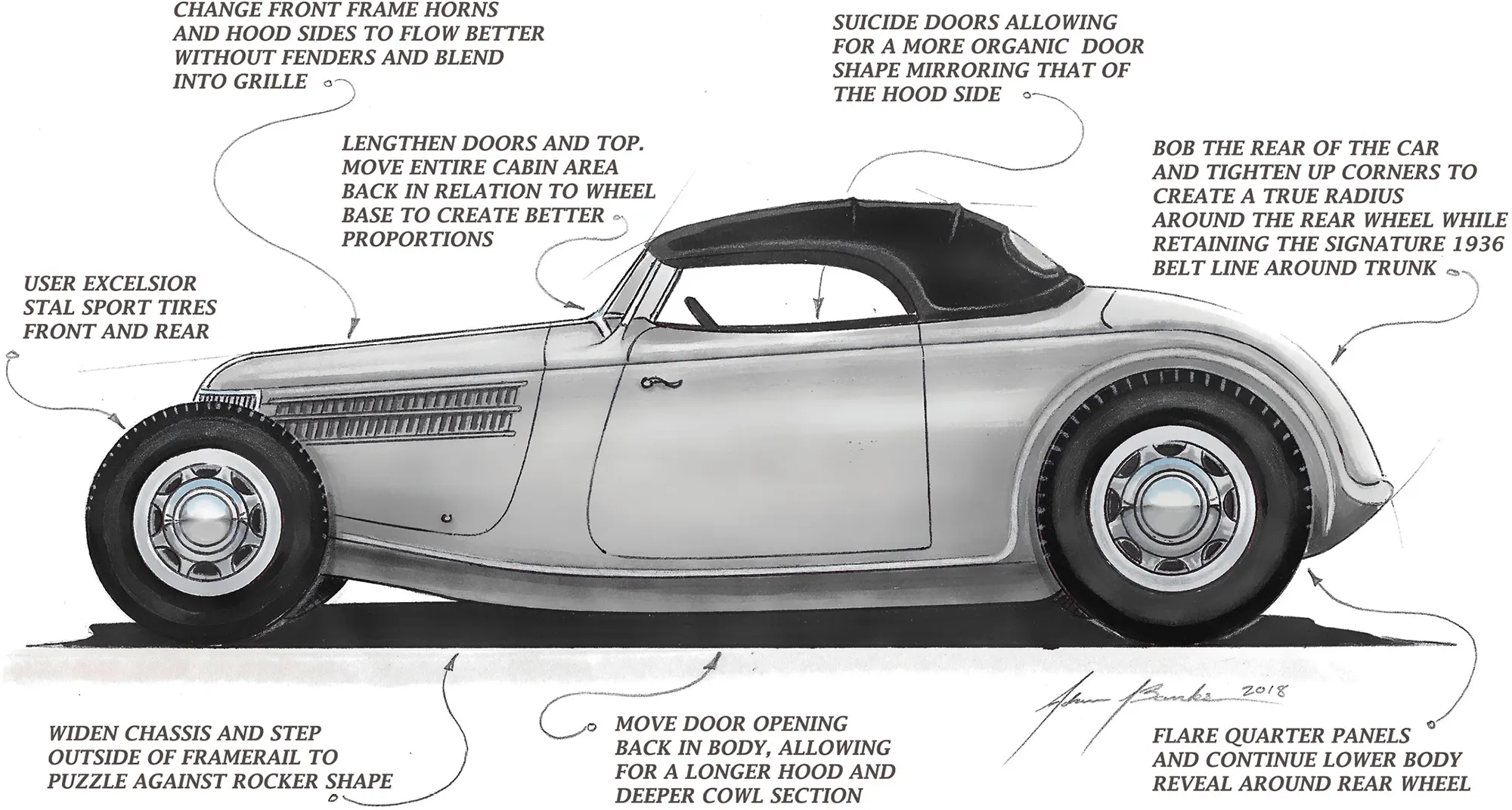

tremendous amount of work goes into building a car from the ground up. In past installments we followed the Rad Rides by Troy team through the construction of the frame and major body components for this fenderless ’36 Ford roadster being built for Ross Myers. With those components largely completed, it was time to fit the engine and drivetrain and to design and fabricate the suspension system.
A Ford Y-block engine was selected and fitted with vintage-looking components that were cleverly updated to provide the functionality of a modern car. A McCulloch VS57 supercharger was used, but Pat Fleischman from Lubbock, Texas, was called on to equip it with the internal components from a Paxton supercharger. The engine will have fuel injection but the Autotrend EFI throttle bodies look very much like vintage Stromberg carburetors. Rad Rides has a reputation for building cars that perform at the highest level, but on a car like this, maintaining a vintage look is part of the discipline.
Torsion bars were used on both ends of the car, longitudinal in the front and transverse in the rear. A lot of thought went into positioning the suspension components so they tuck neatly into the chassis, providing an exceptionally clean appearance and leaving as much open space as possible. On an open-wheeled car like this, these details can make a huge difference.
Special radius rods were machined for the front and rear axles. These are highly detailed components, incorporating a ribbed design element. A great deal of planning went into making them blend visually with the other components while retaining the vintage look of a straight-axle car.
Special shock mounts were made for both axles. In front where they are more visible, the Rad Rides team found a way to hide the top half of the shock inside the headlight. This required some rather complex fabrication and machining, allowing the highly loaded components to be easily assembled and disassembled, but the results are well worth the extra effort.
If you are enjoying this series, look for the next episode where the fabrication and fitting of some of the more complex sheetmetal components will be covered.


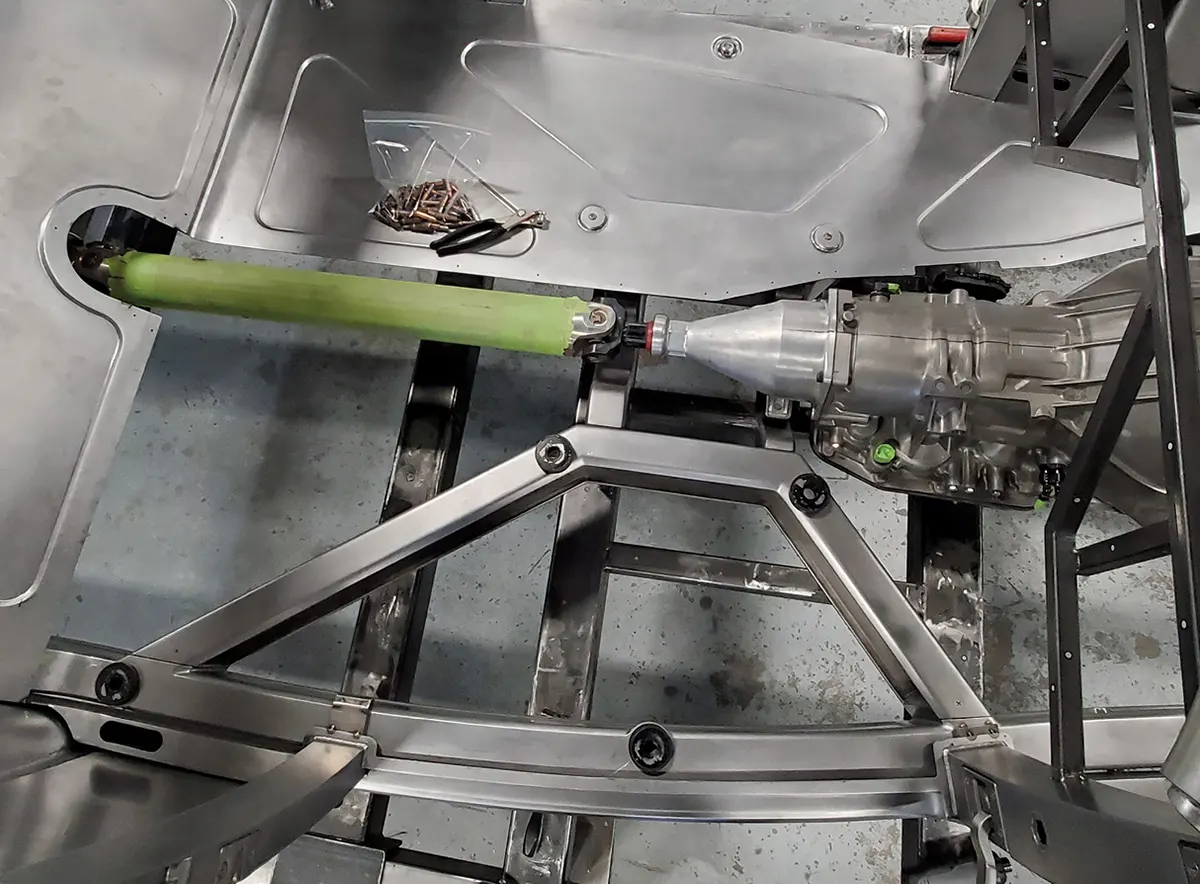
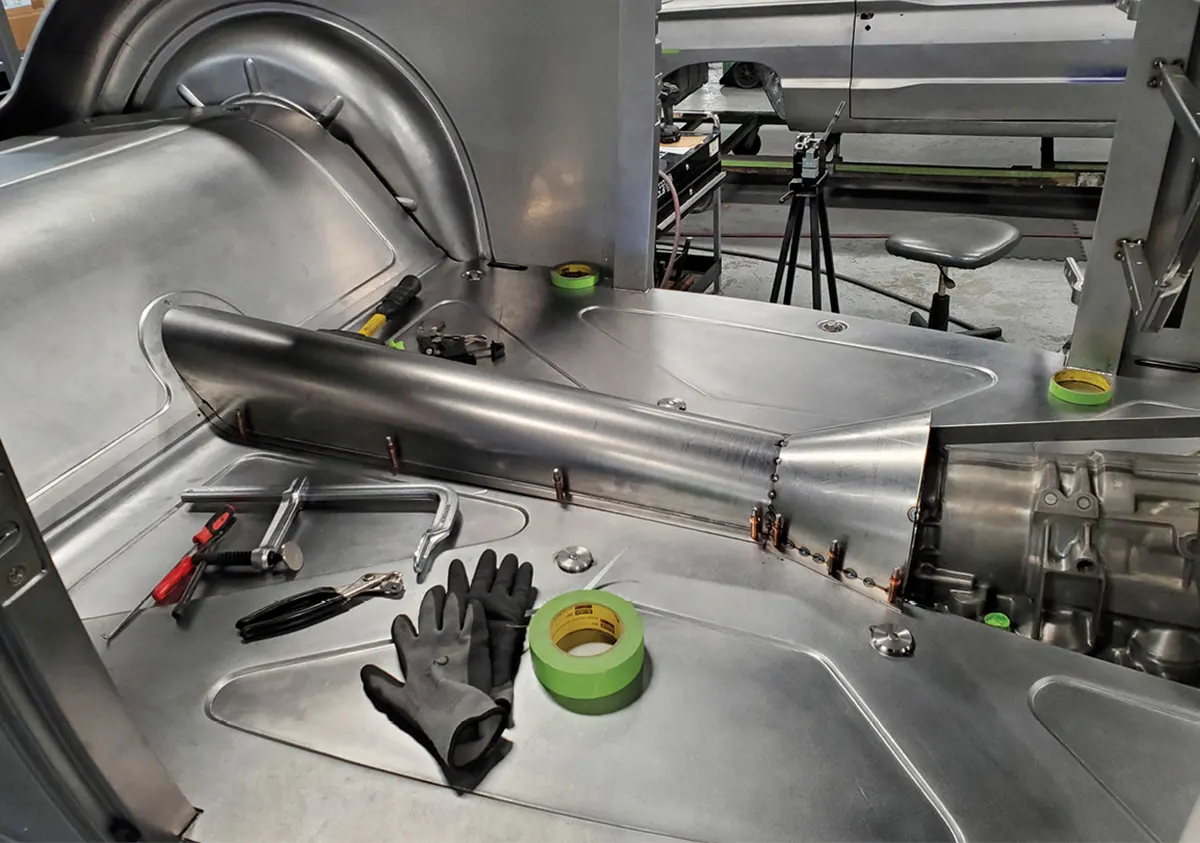
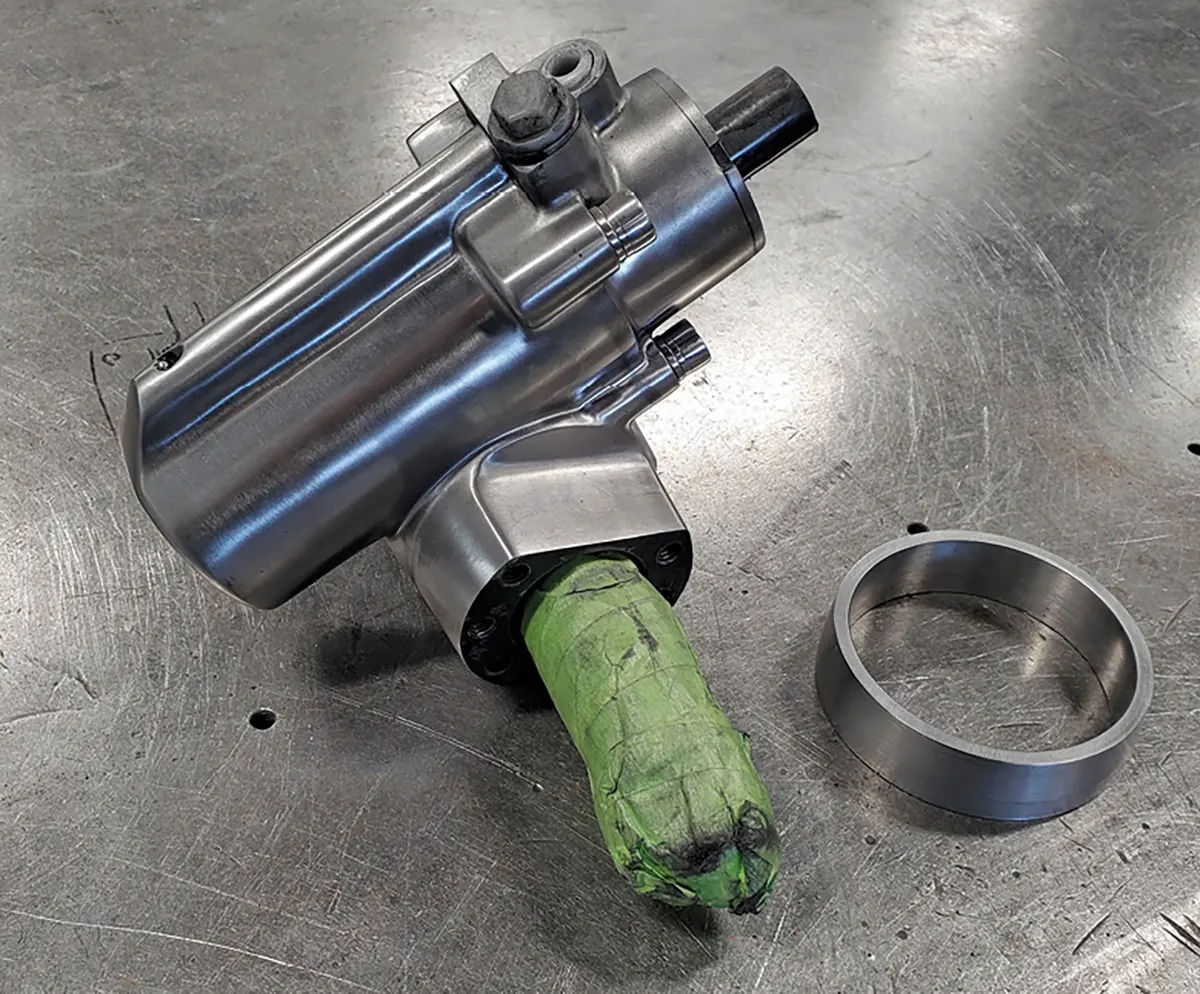
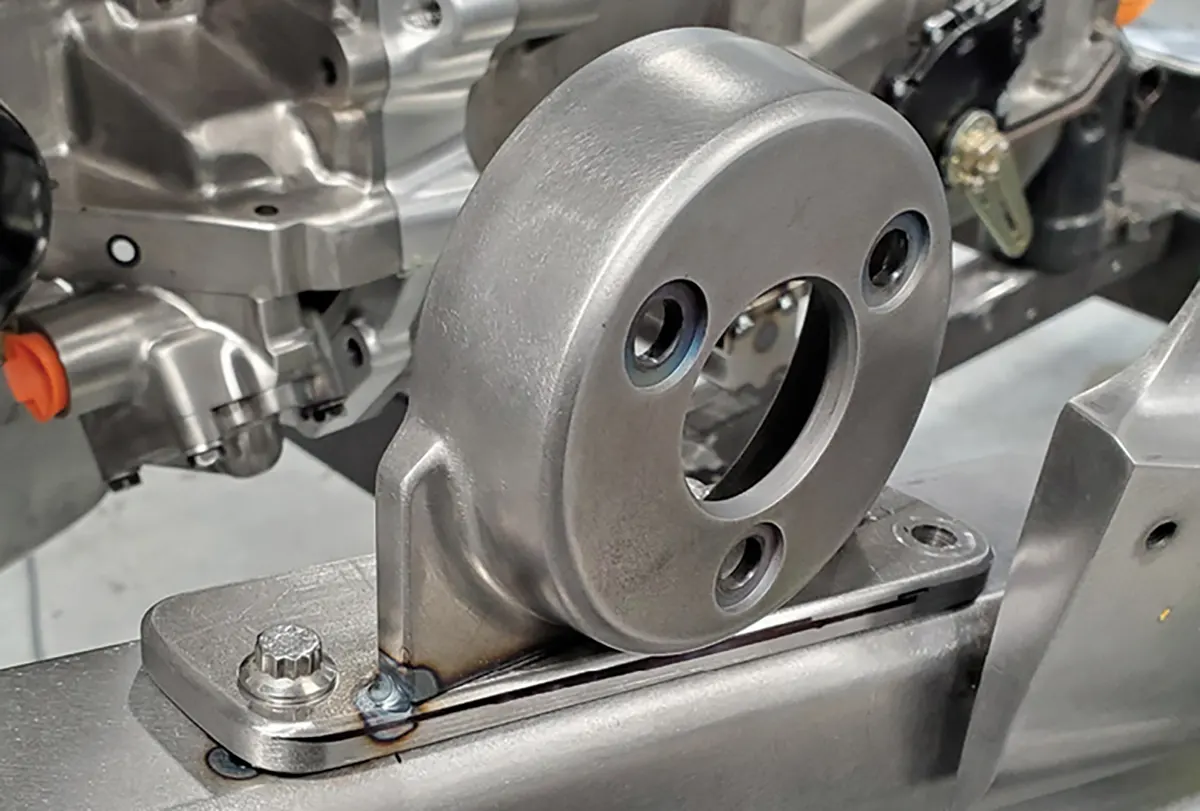
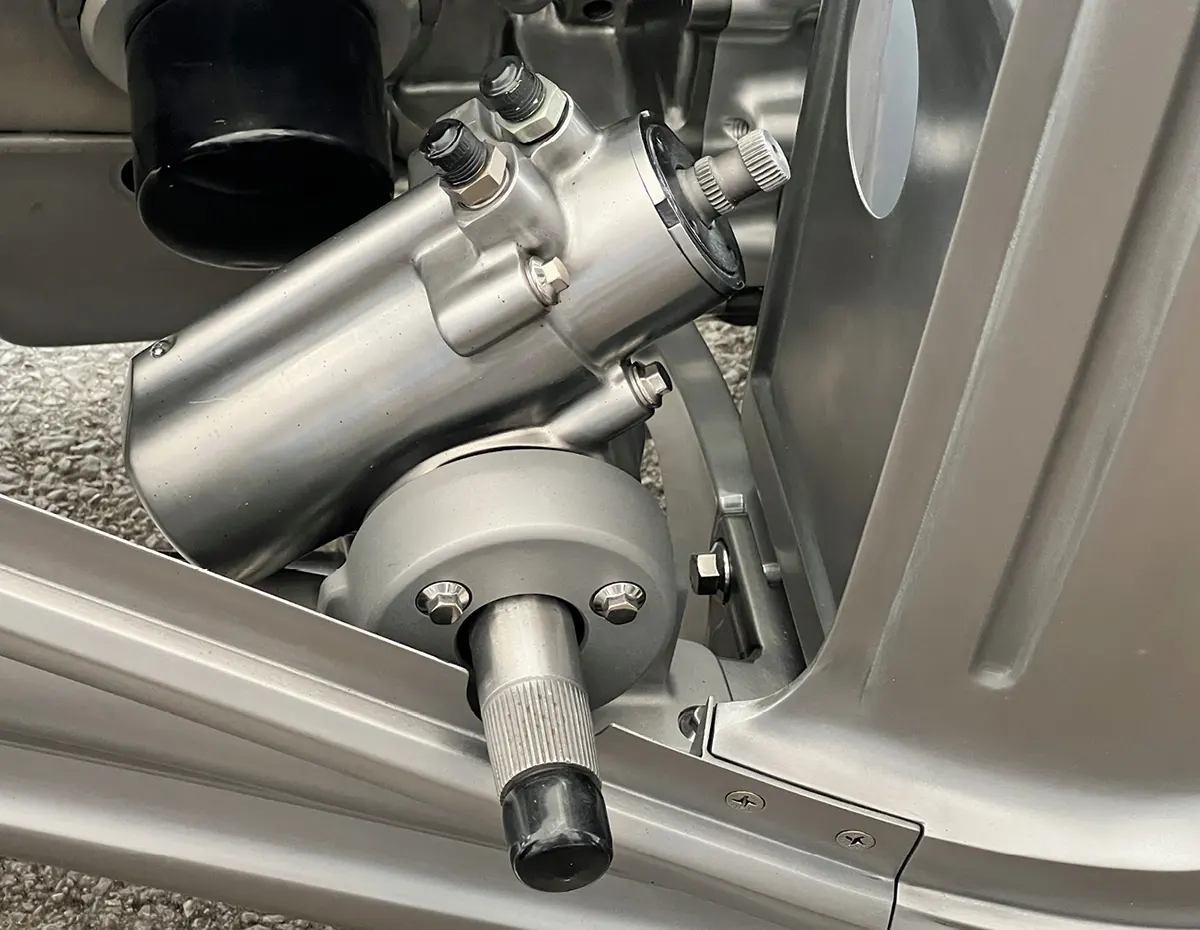
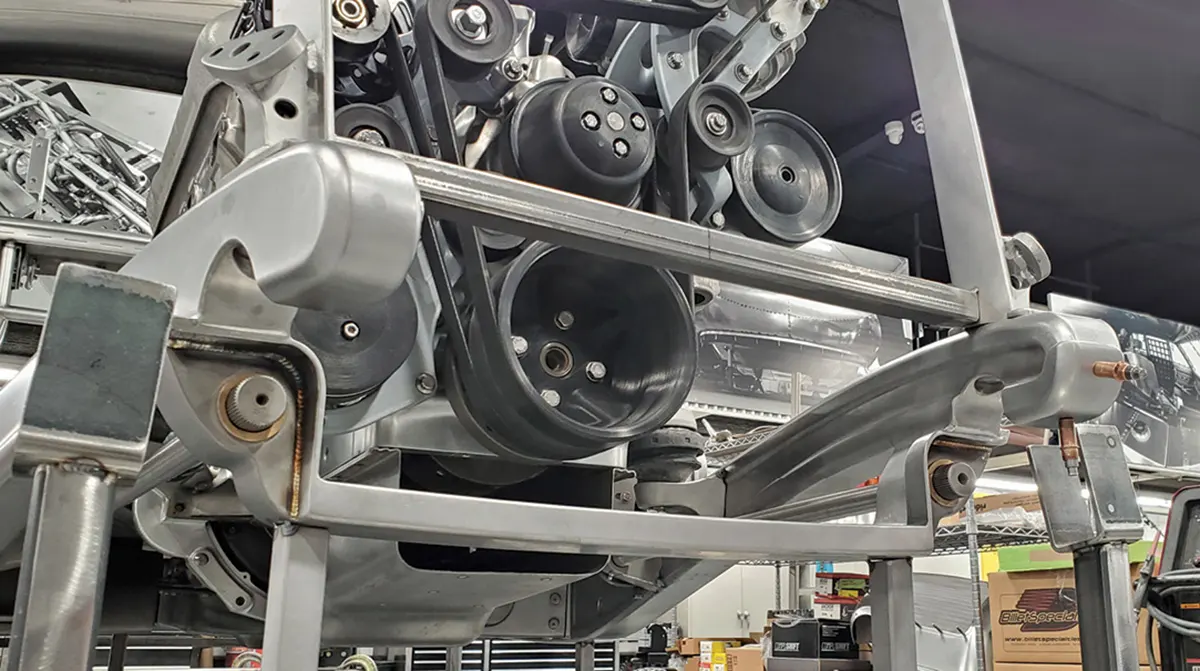
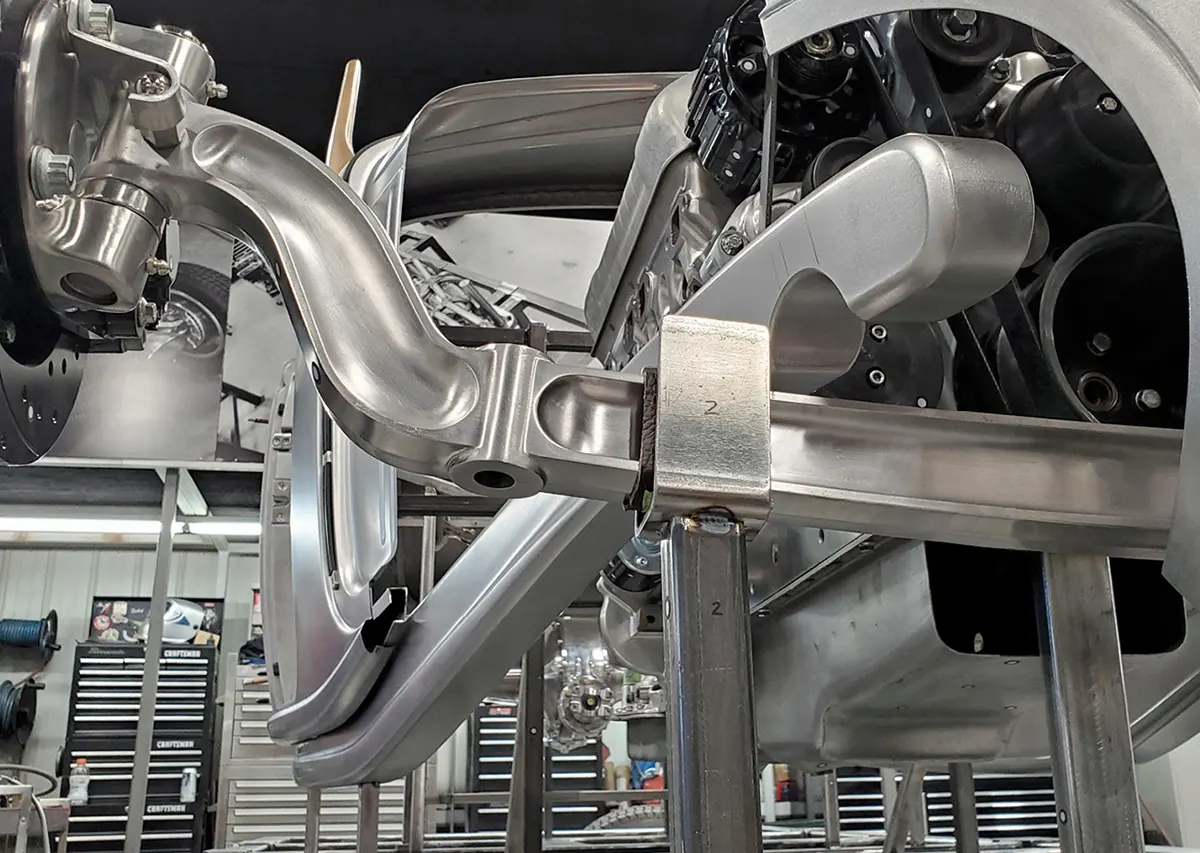
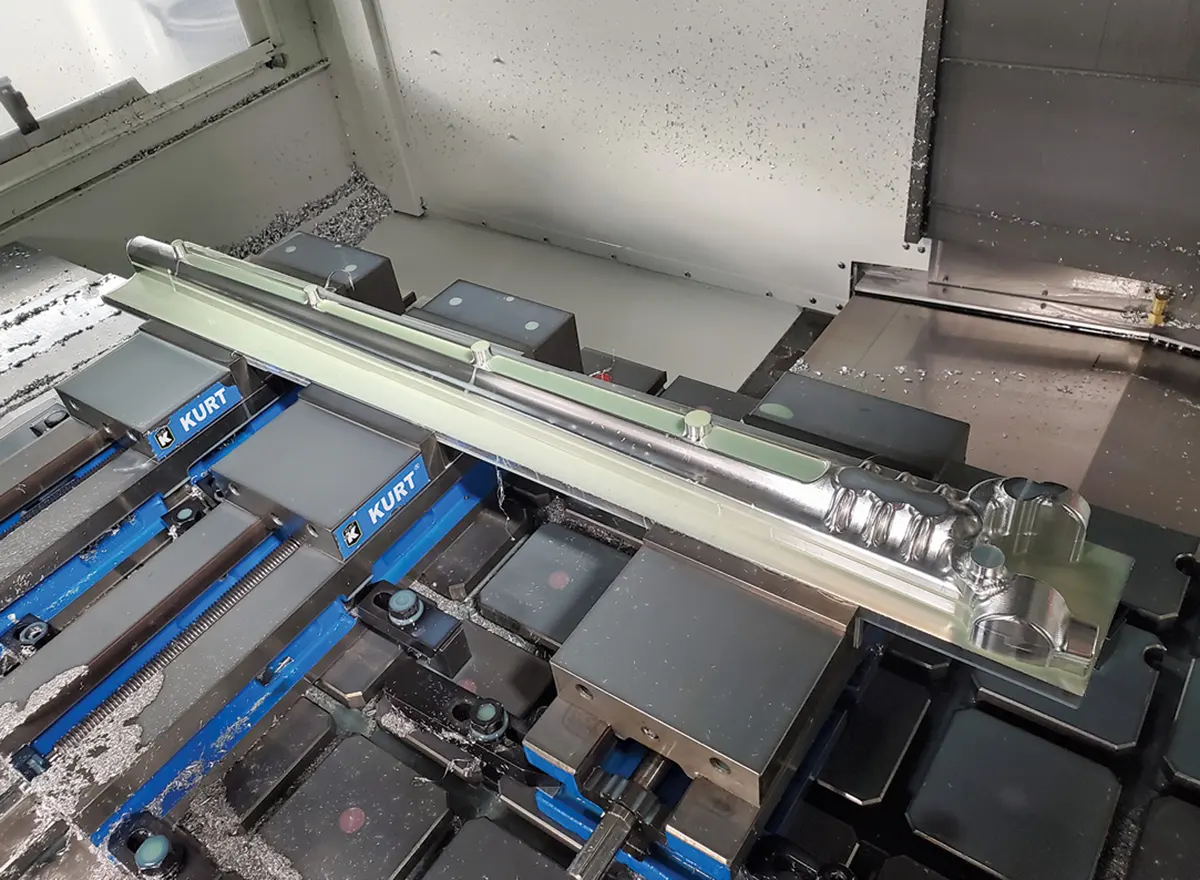


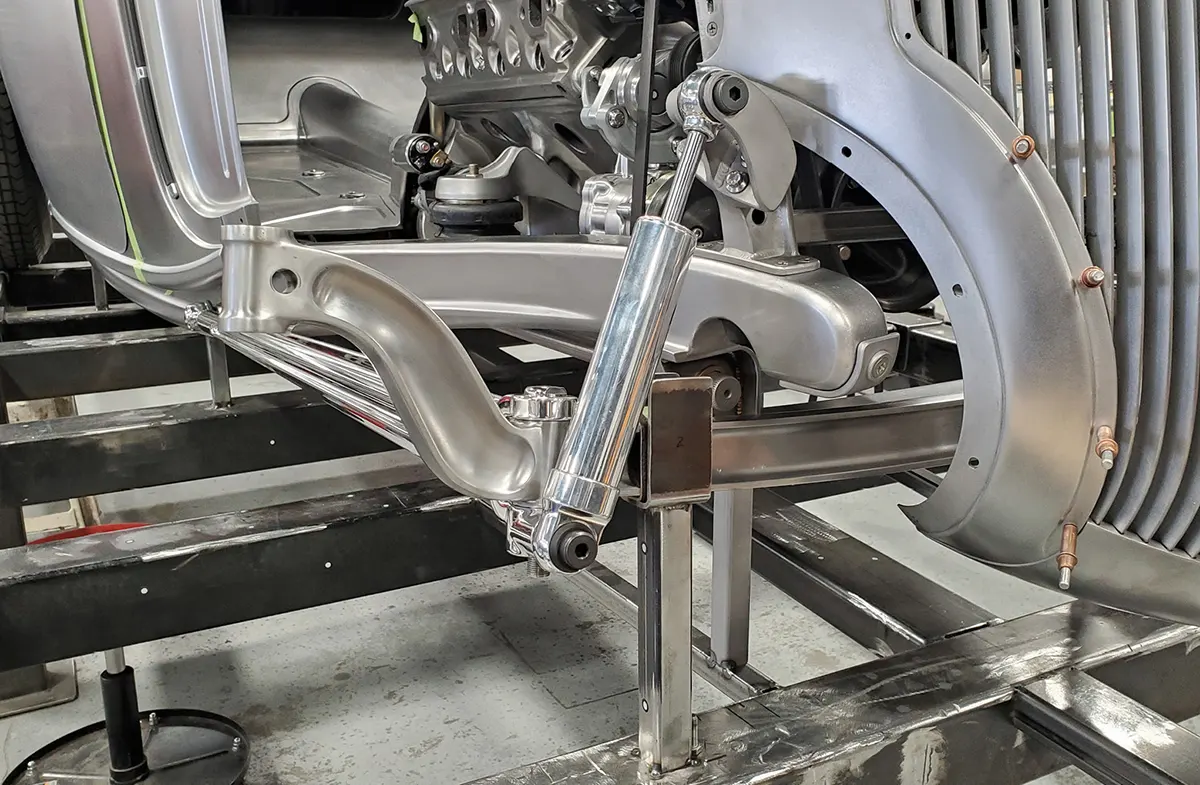

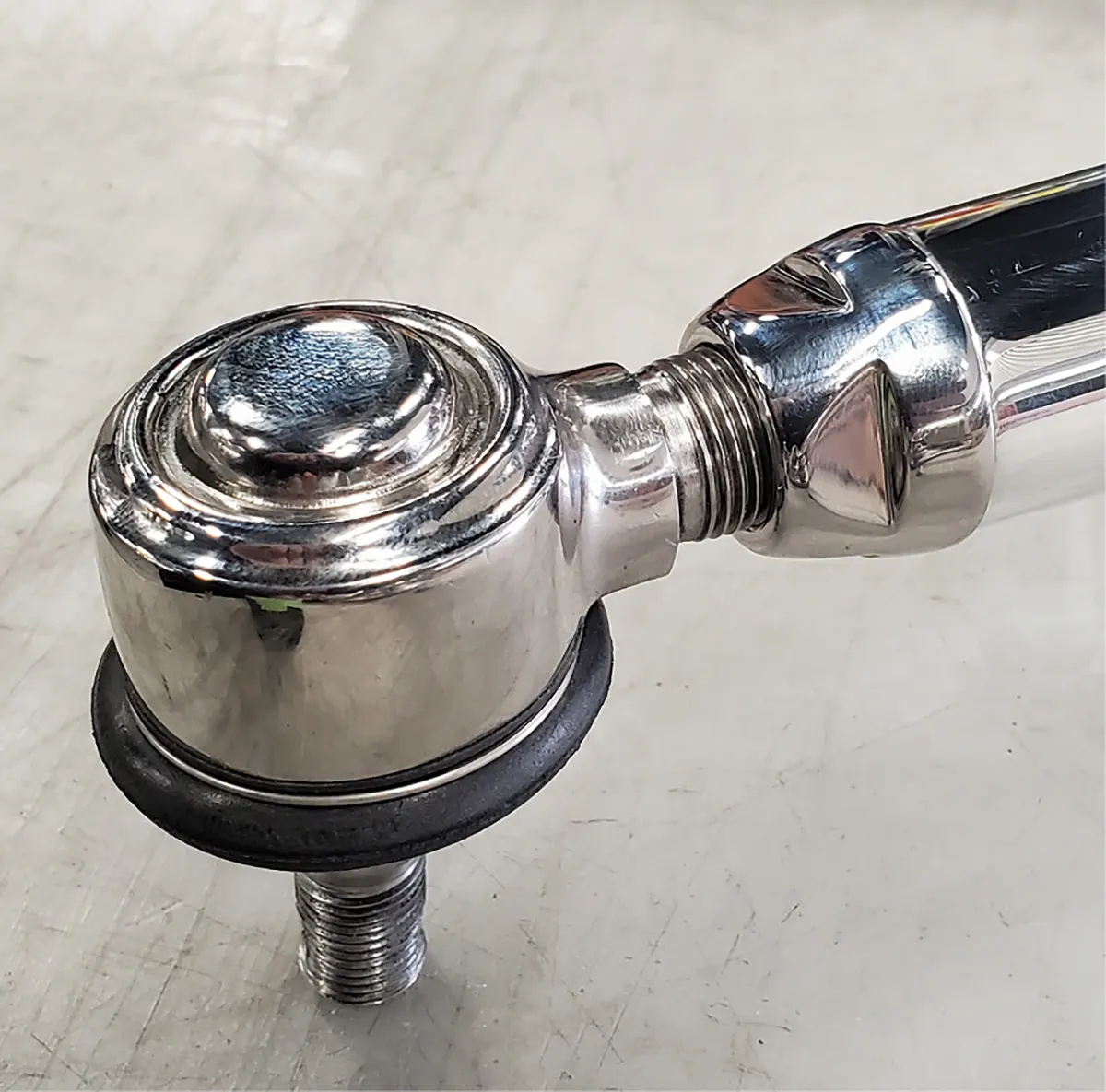
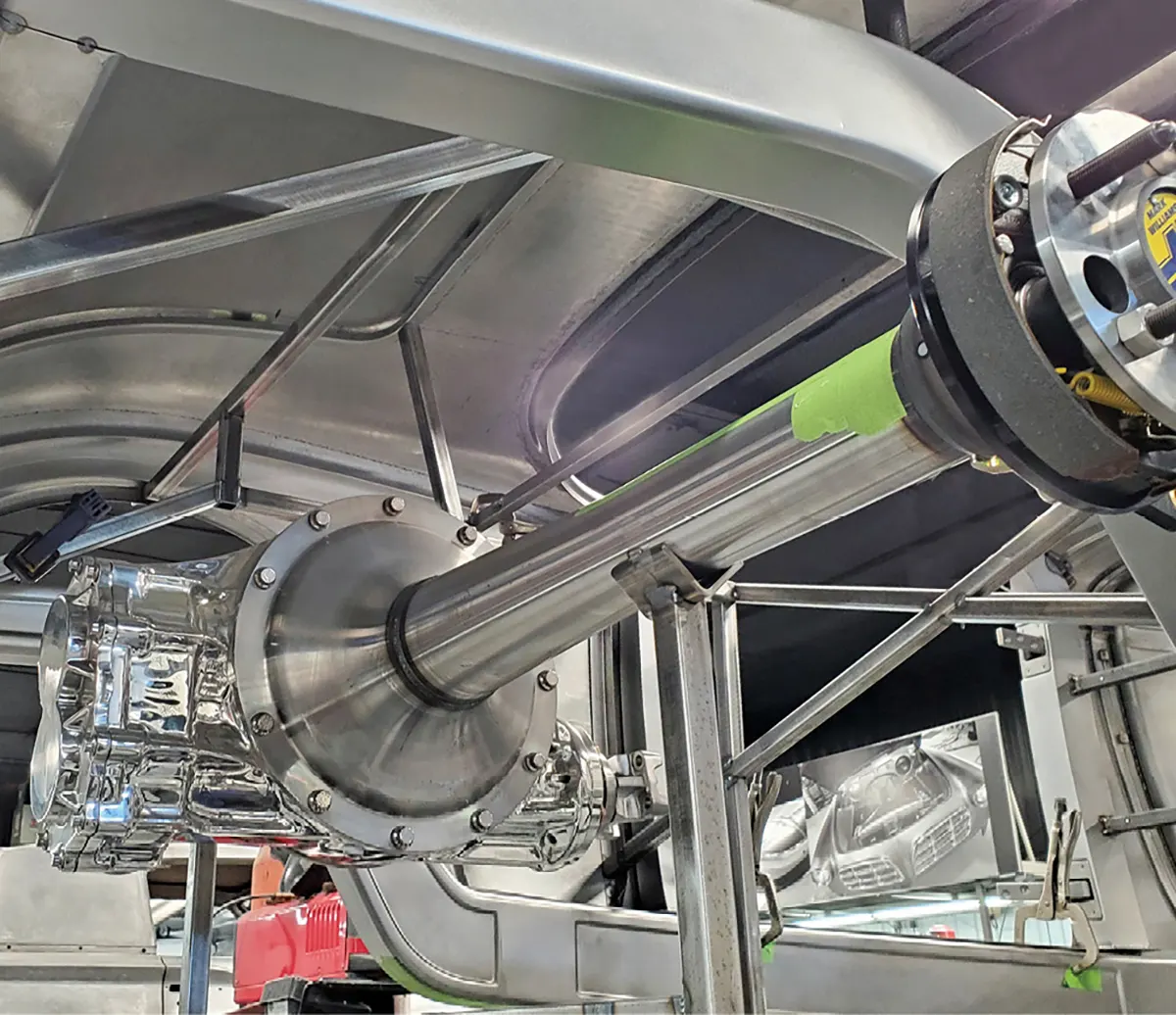
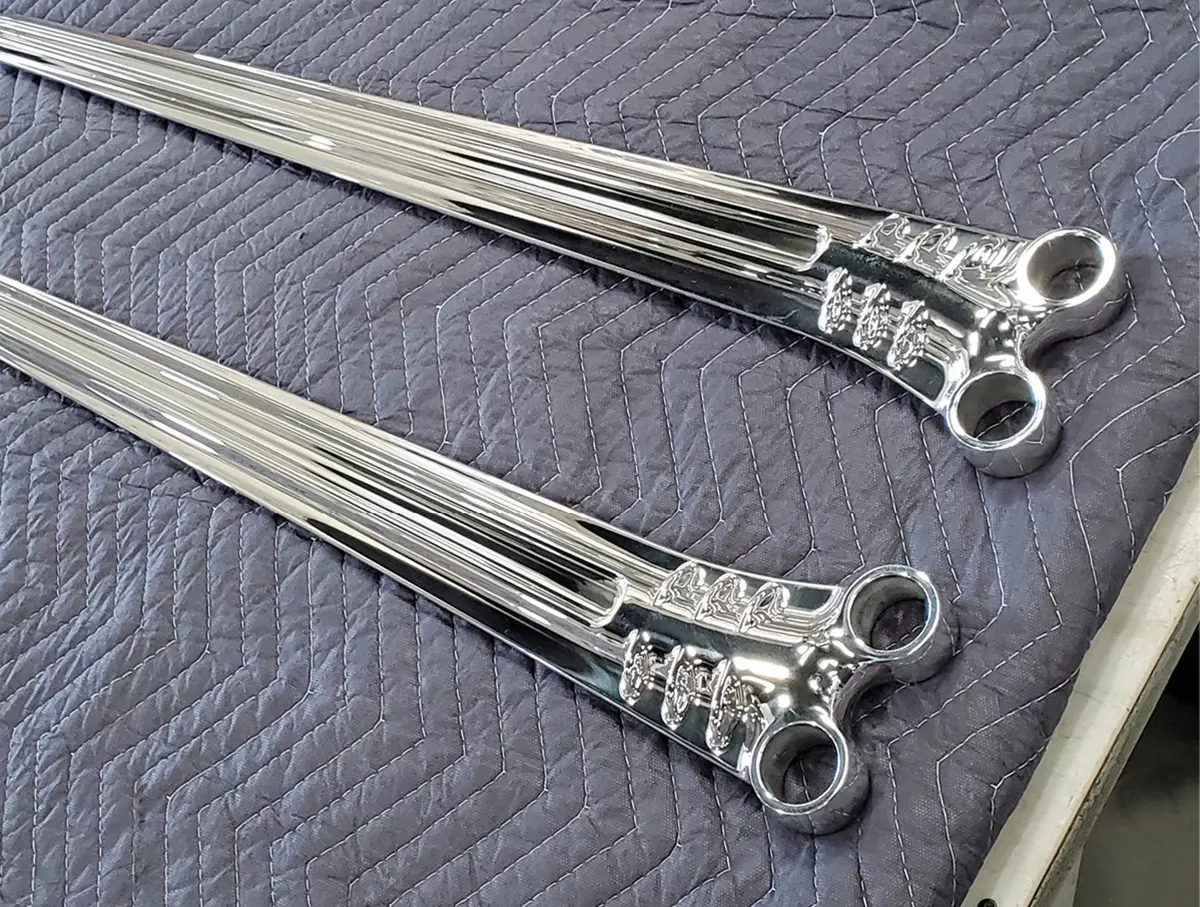
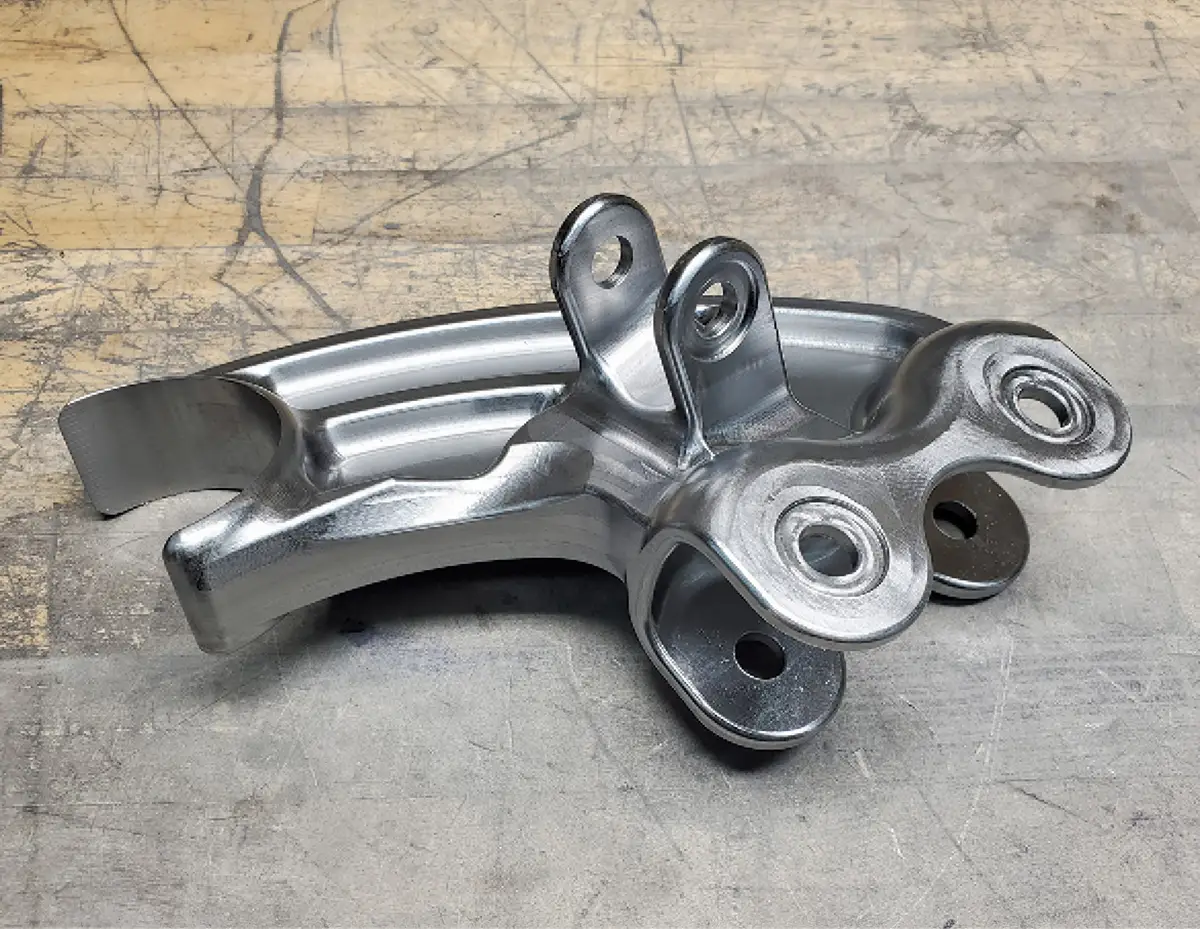


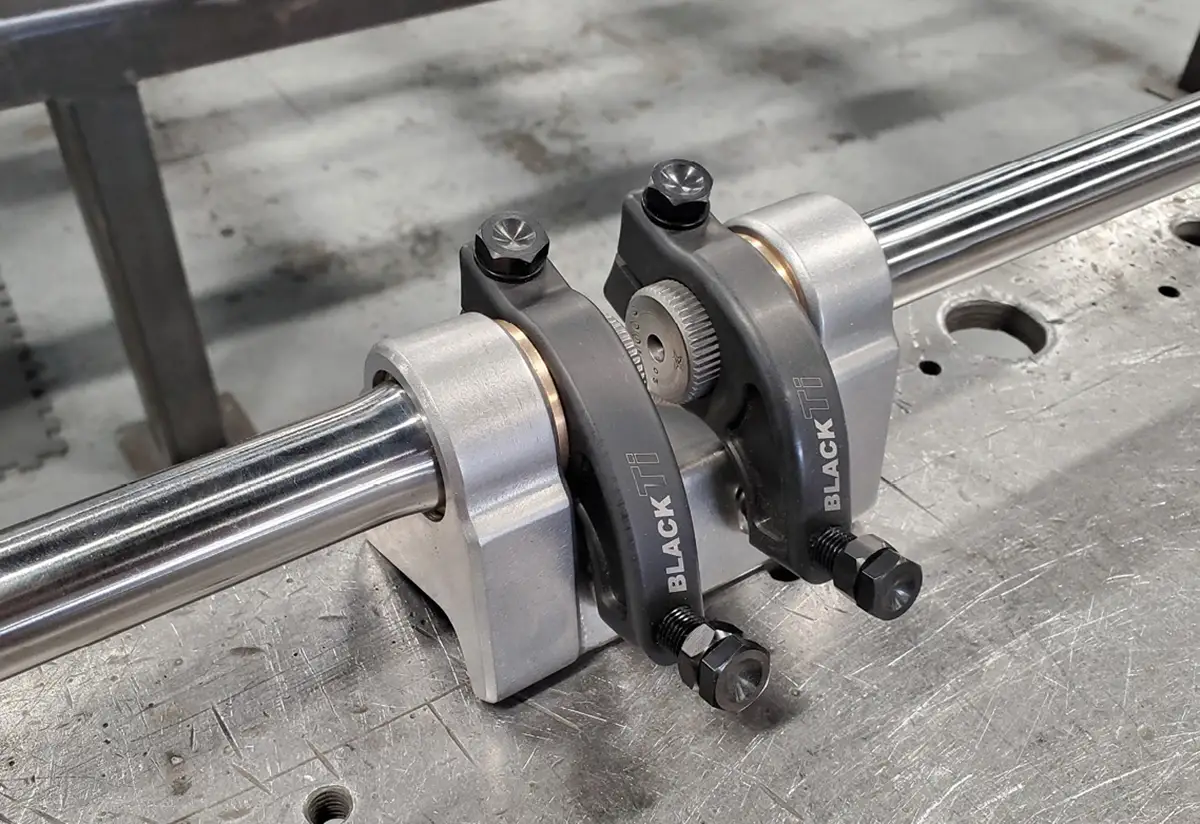
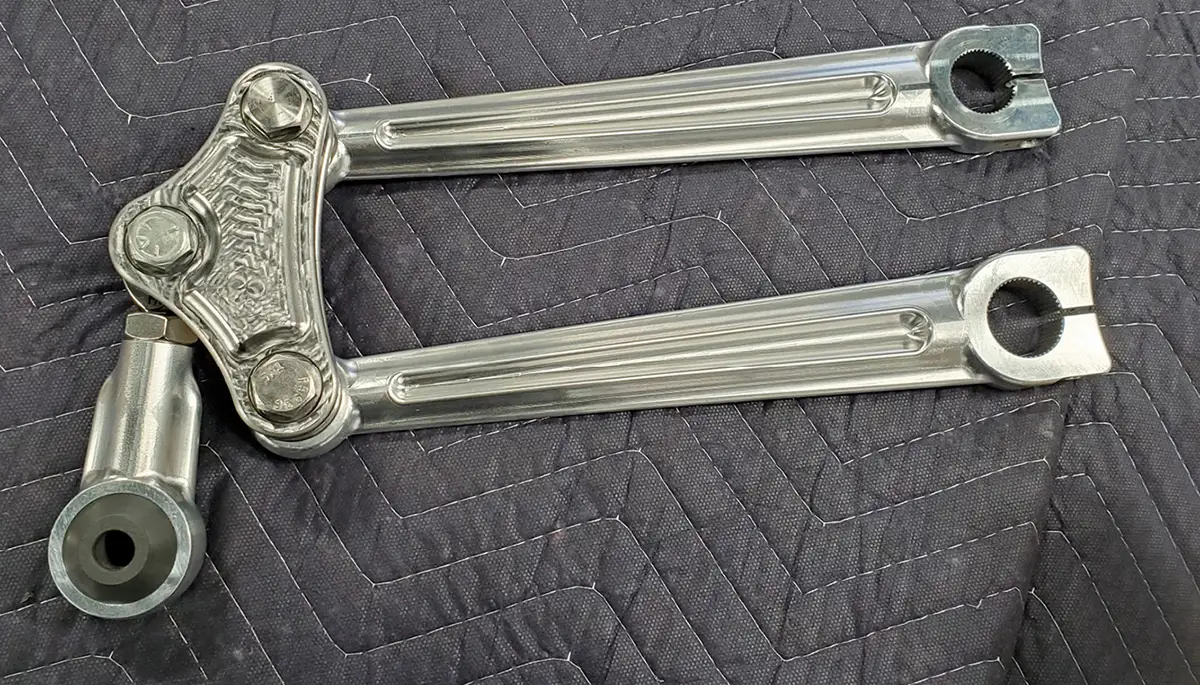
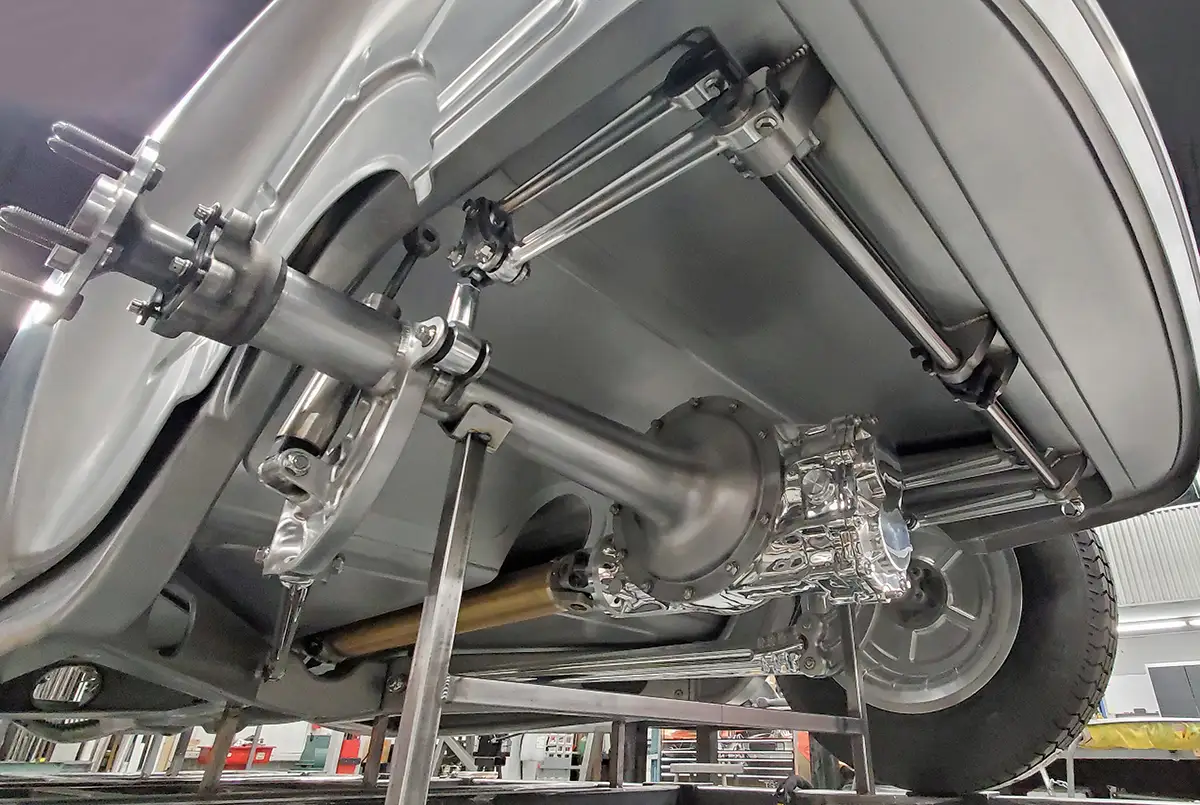
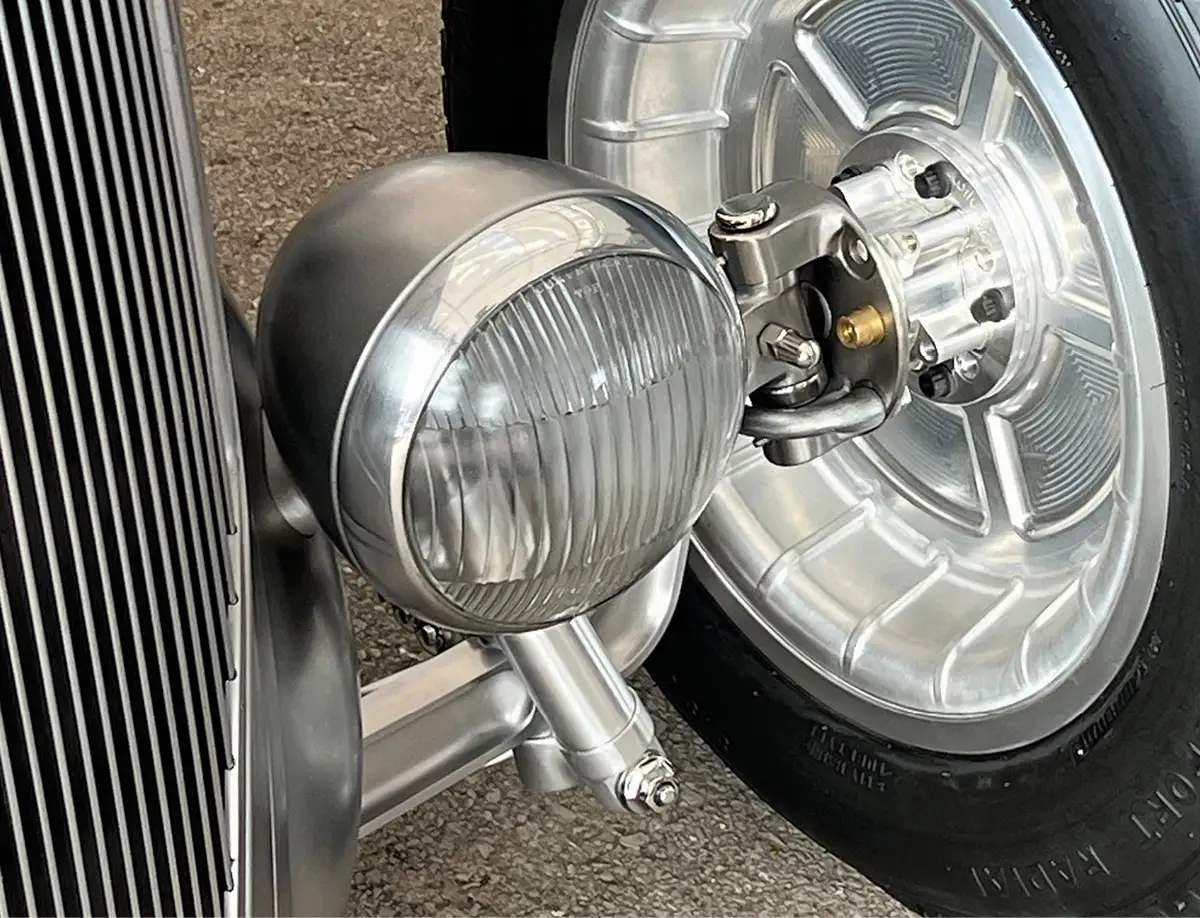
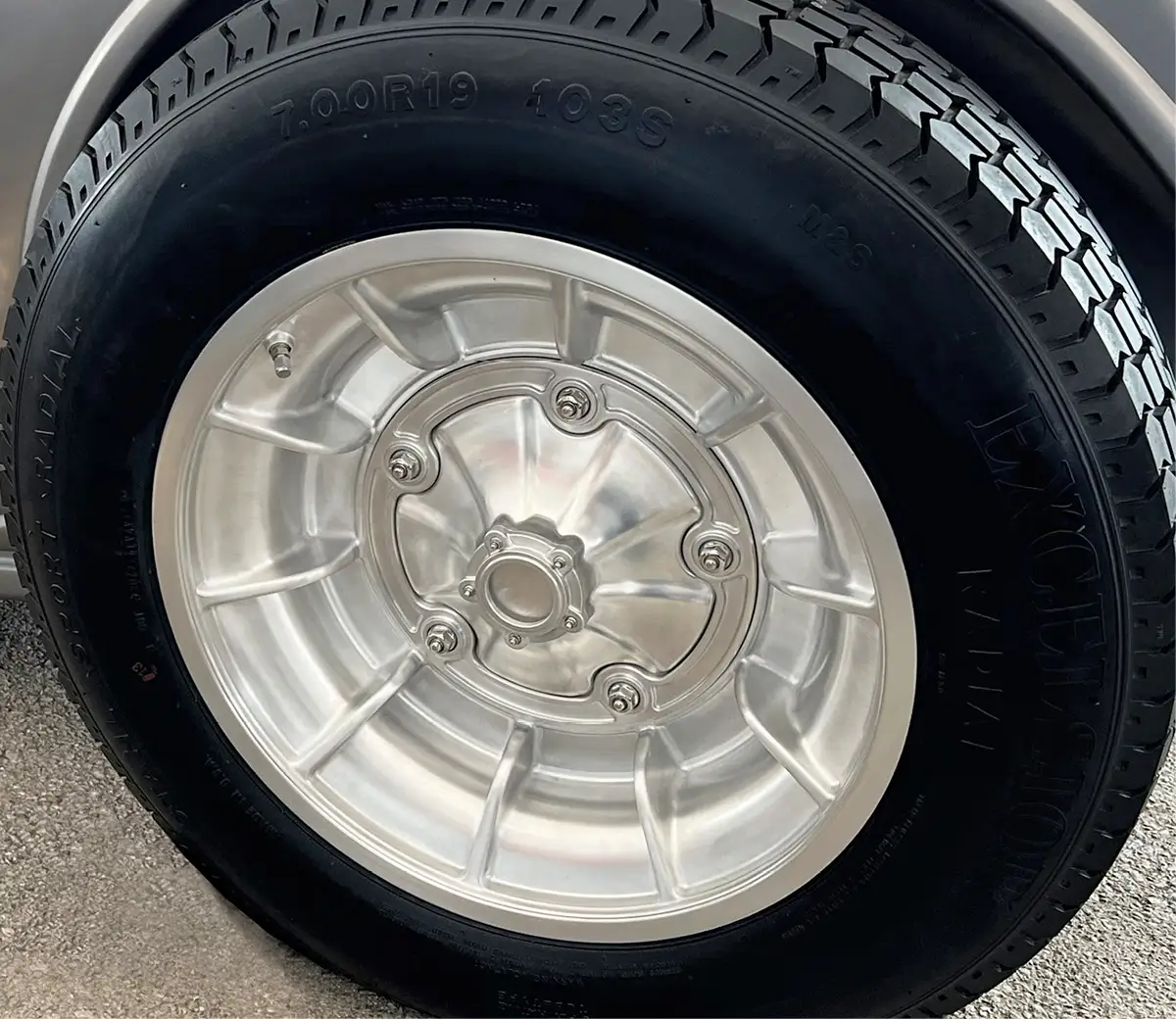
