
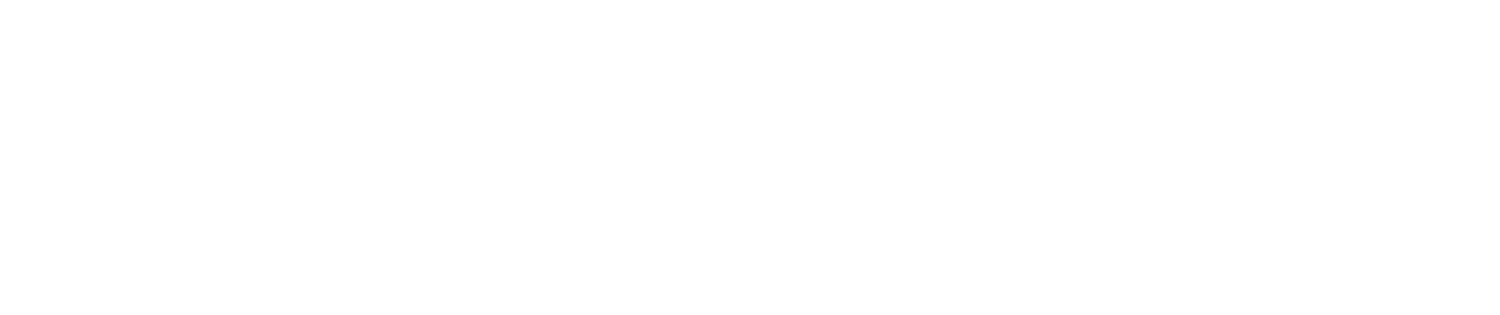
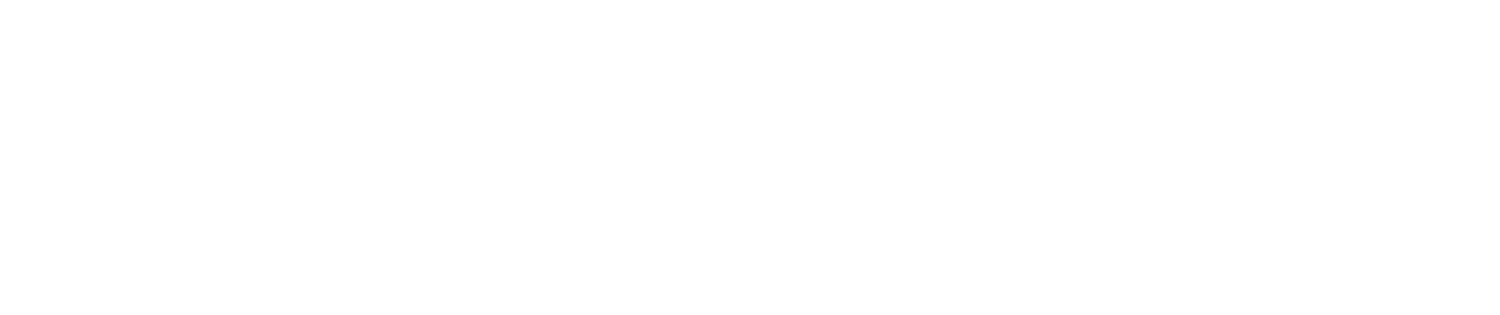

uilding a hot rod of any era is a stream of choices—some big, some small—but they all contribute to the finished package. One thing we learned early on was to pick a theme and make every decision fit that style. My latest project is a 1936 Ford phaeton being built as an early ’50s hot rod/custom. Many cars of that era blurred the lines between rod and custom with performance under the hood and some custom touches and paint on the outside. That is the very theme of our 1936, with a built Flattie underhood and a conservative custom approach on the outside.
We’ve recently been doing the bodywork and while stacking parts on the shelf (all neatly marked for the memory impaired) we came across the original grille ornament. The ornament was in overall good condition with the V-8 emblem intact. However, two holes drilled in the piece told us a greyhound had once adorned the piece. While greyhound ornaments are cool, in keeping with the theme of the car, we thought a simple bullnose ornament from Speedway Motors would be a quick-and-easy solution. But then we began to think about making our own bullnose piece, but with a custom twist. We wondered about grinding down the finned portion of the ornament to a lower profile giving us a “semi-bullnose” look.
Some marking with a Sharpie seemed to indicate we could trim the piece to eliminate the two holes and achieve our desired lower profile. A die grinder and cut-off wheel took off most of the die-cast piece and we finished shaping with files and sandpaper. Since the hood ornament is die-cast, removing metal is easy—so easy you must work carefully not to remove too much material. We sanded the ornament down to a 400-grit finish and spent some time viewing it from various angles. The piece flowed nicely but we now had the problem of filling the resulting openings caused by removing the V-8 emblem and removing the top of the fin.
Working with die-cast material is difficult, but working with copper is relatively straight-forward. So, the trick is to convert this die-cast piece into a copper piece. We spoke to our friends at Advanced Plating earlier to make sure we could send the piece to them for copper plating, then have it returned to us where we would solder copper filler pieces in place before returning it to Advanced Plating for more copper and final chrome plating. It should be mentioned that Advanced Plating is fully equipped to do the entire filling process and this type of repair and modification can be done on virtually any die-cast piece. We opted to do this at home for two reasons: One, we enjoy doing these little projects that make a big difference; two, we’re cheap and wanted to save a little money.
And so, satisfied with the final shape it was carefully boxed up and shipped to Advanced Plating for stripping of the remaining original chrome plating followed by copper plating. Our piece fell into the production line and a couple of months later the grille ornament returned, glistening in all its copper glory. Remember to plan ahead for chrome plating as all good chrome shops have a backlog of parts to plate. Generally plan on at least a couple months to get chrome done and a simple call to the plating shop will give you an idea of how long it may take to complete your job. In this drive-thru window, overnight-shipping world, there are still some things that just take time.
Finding copper material to fill the voids proved to be fairly simple. Since the piece is basically hollow, a simple piece of 1/8-inch copper tubing was gently shaped to fill the long void on top of the ornament. This involved bending it by hand and then squeezing it in a vise to slightly flatten the copper tube. The tubing was fit from the underside to the ornament and then we soldered one end in place; think of this as a “tack solder,” much like a tack weld. This allowed us to gently tap the copper tube up into the void. The operative word here is GENTLE; die-cast is not known for its strength so you must be careful not to damage the piece. With the tubing fit to the opening it was soldered from the top to fill the seams between the tubing and the hood ornament. Allow the solder to build up above the piece. Since the lead solder is very easy to work, fill it high and then carefully file it down to the proper profile. Once the filing has formed the initial shape, finish the piece with a soft sanding block and sandpaper. We first sanded with 320-grit and finished the work with 400-grit.
The front opening is a bit irregular but using the same tubing technique (this time we used 1/4-inch tube) we shaped a filler piece and soldered it in place followed by more of the filing and sanding to smooth the piece. Satisfied with the shape and finish of the piece it was returned to Advanced Plating for final finish, copper, and chrome plating. When we received the piece back in finished chrome plating, we were more than pleased. The plating was impeccable but beyond that we were pleased with the overall shape of the piece. It will be one of those things that most people may never notice, but such subtle changes are what make a car special and we are pleased knowing our hood ornament is one of one.
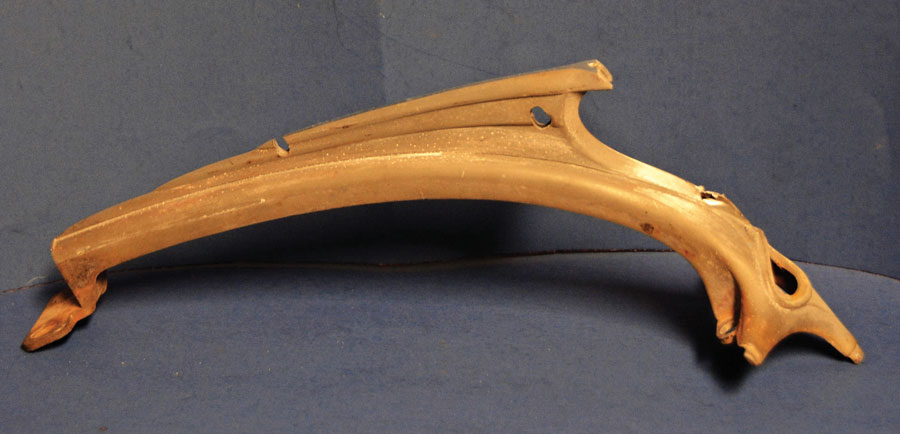
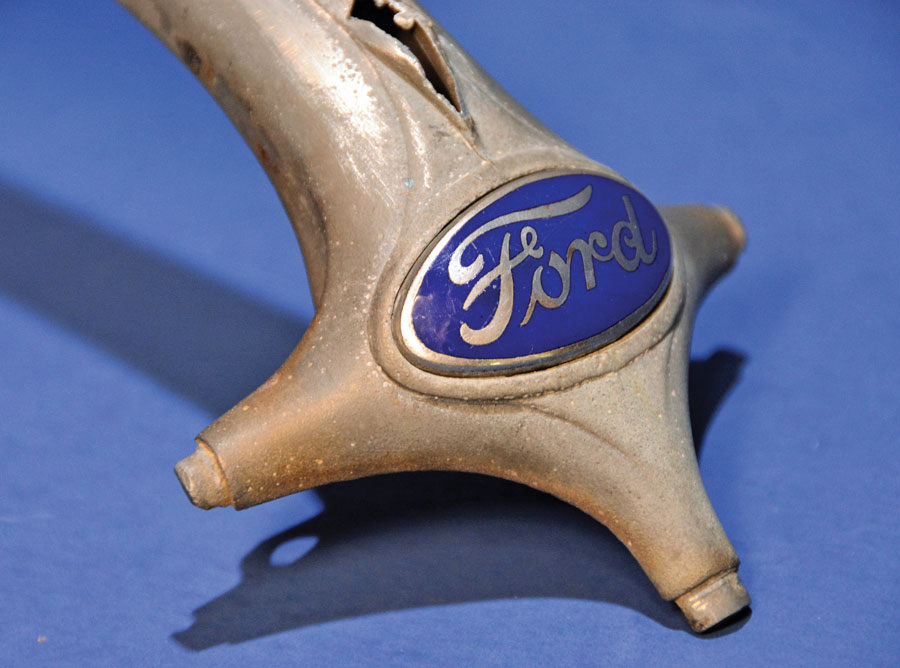
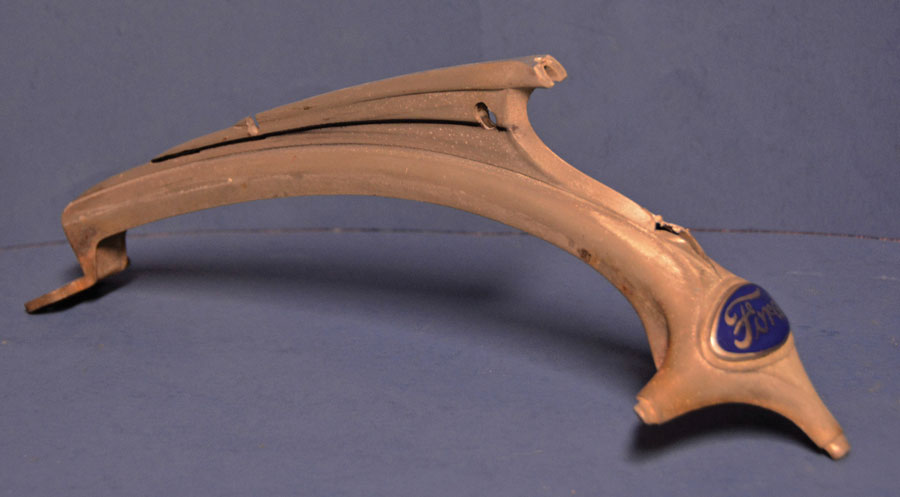
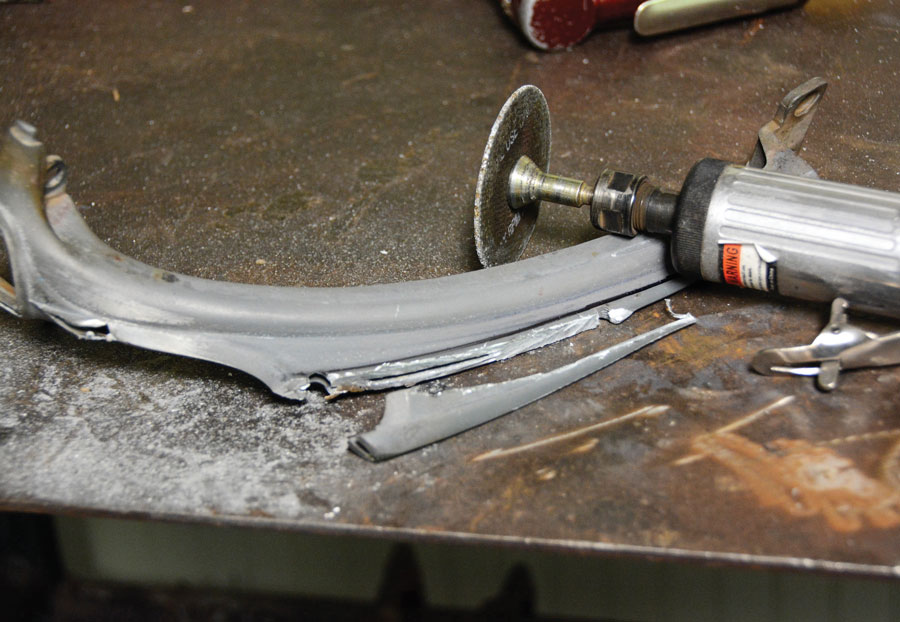
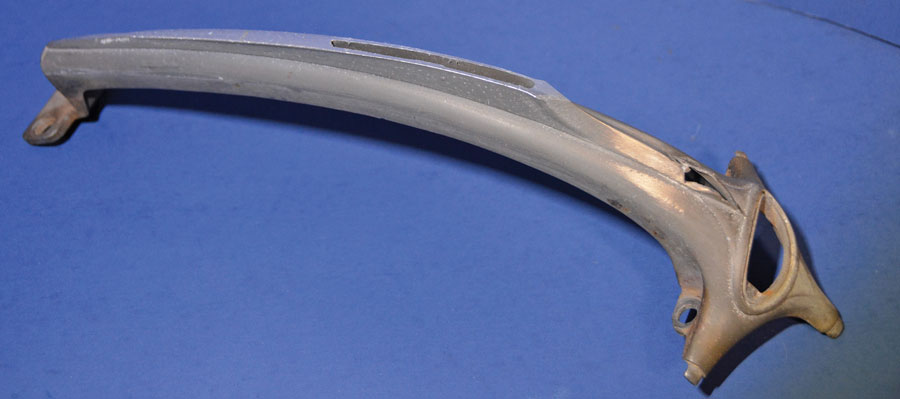
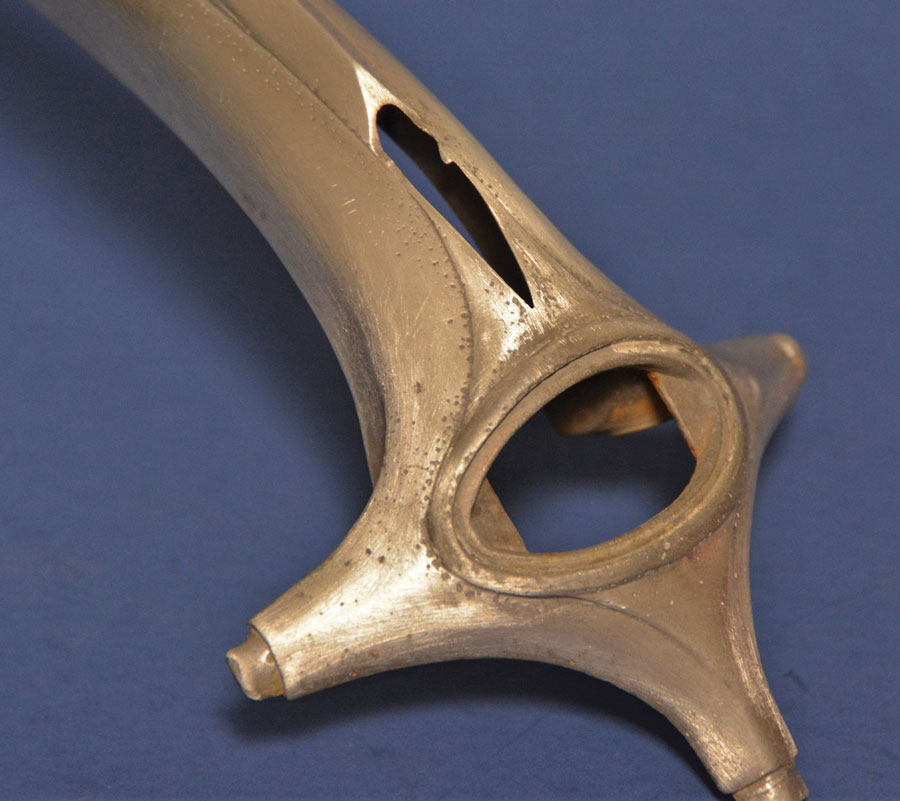
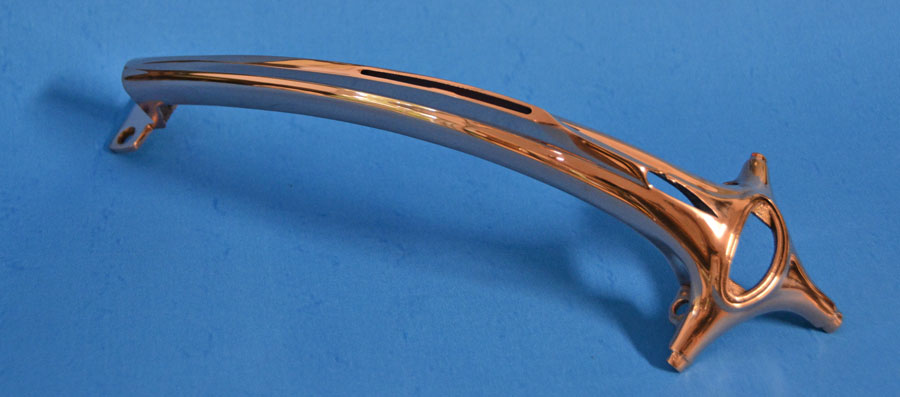
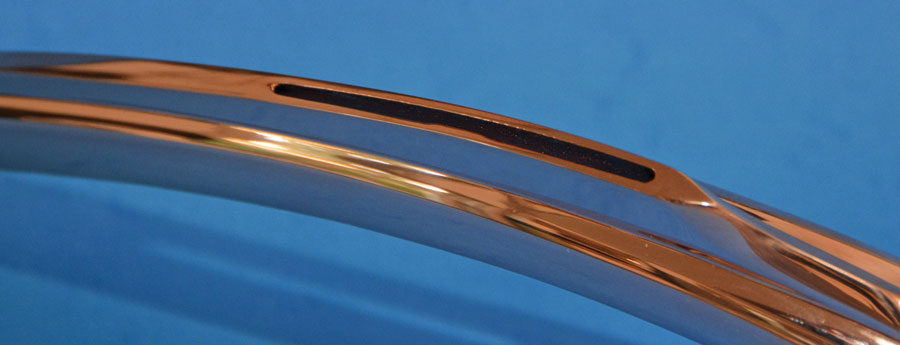
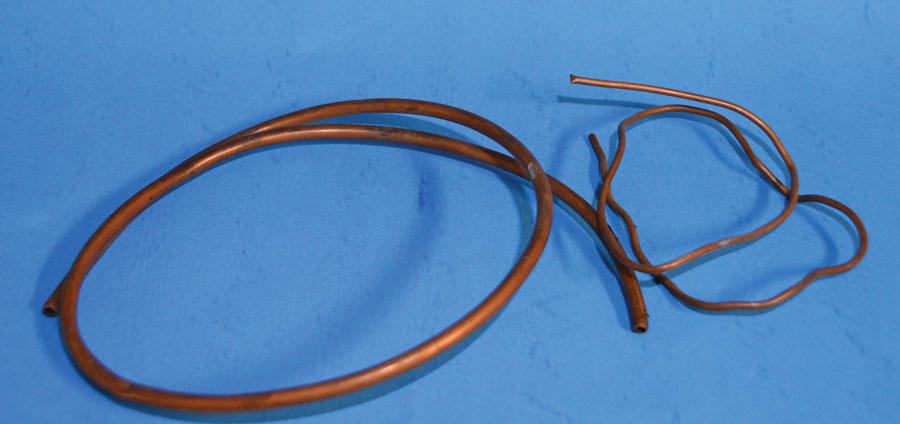
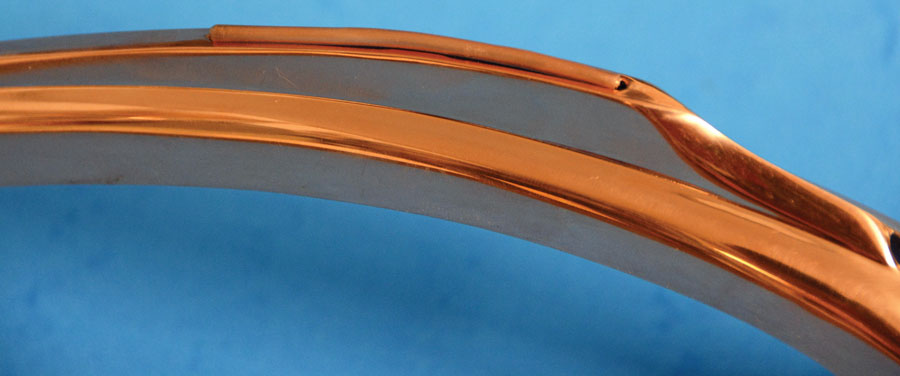
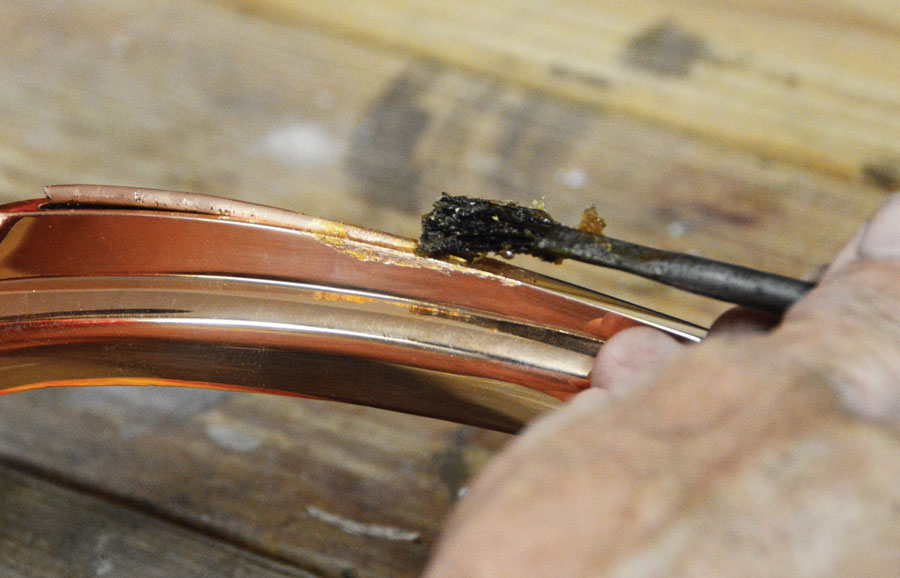
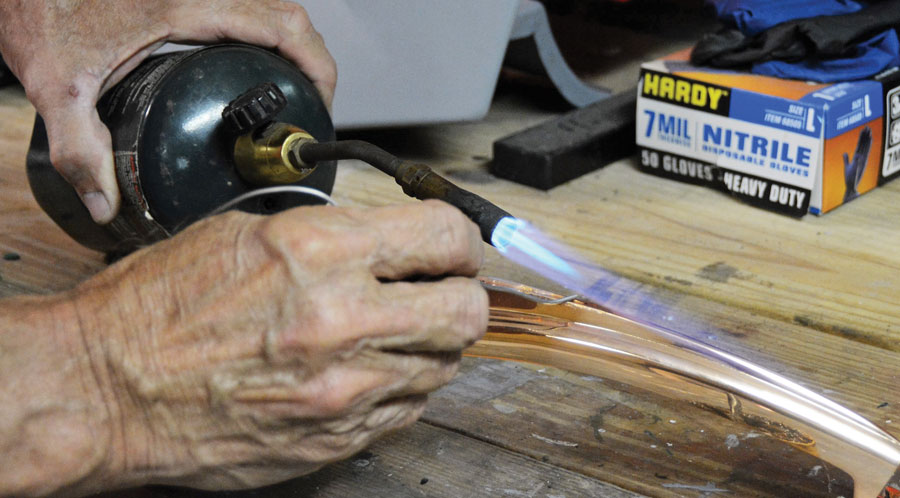
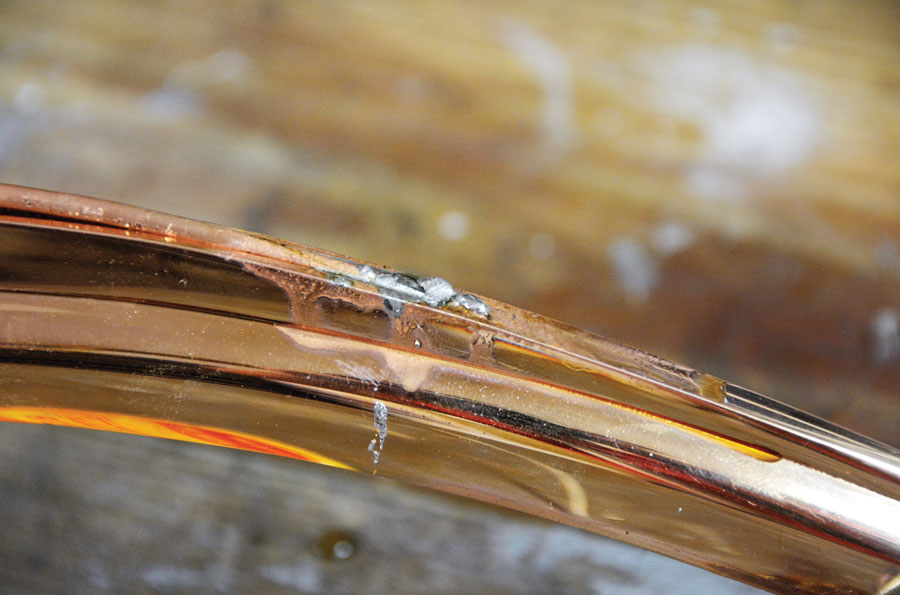
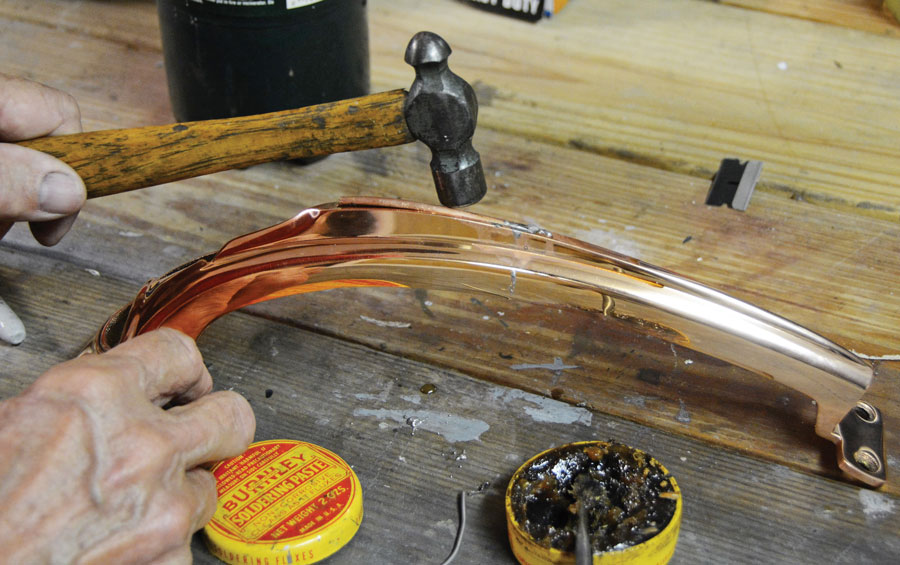
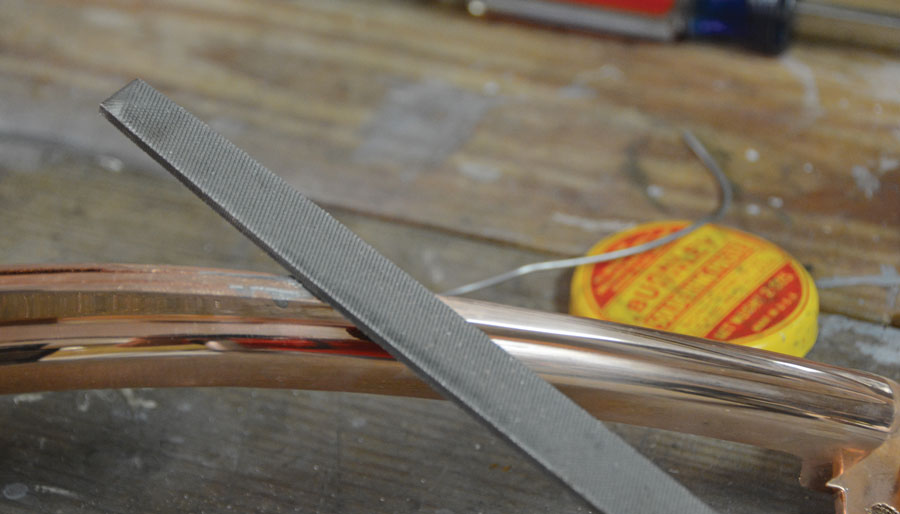
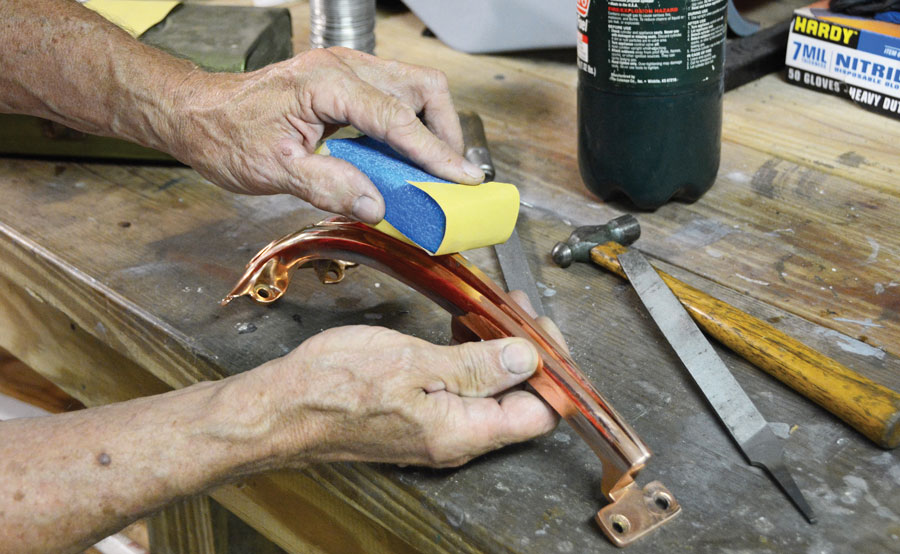
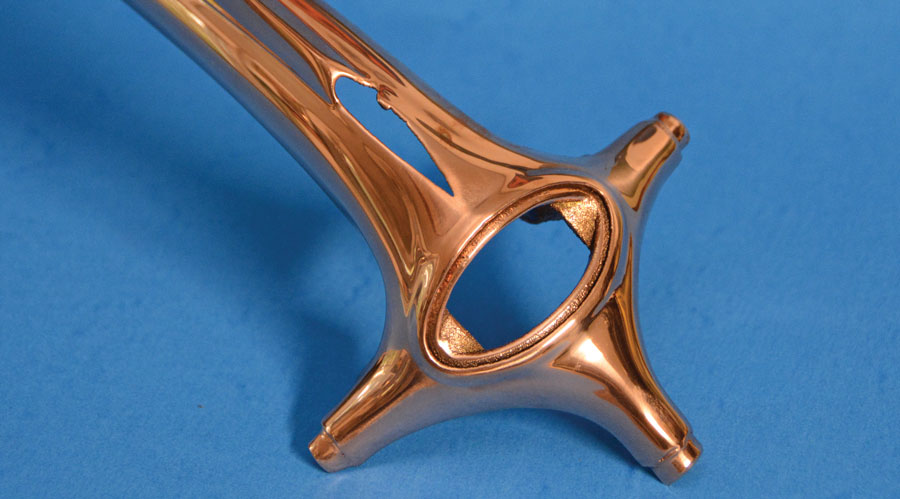
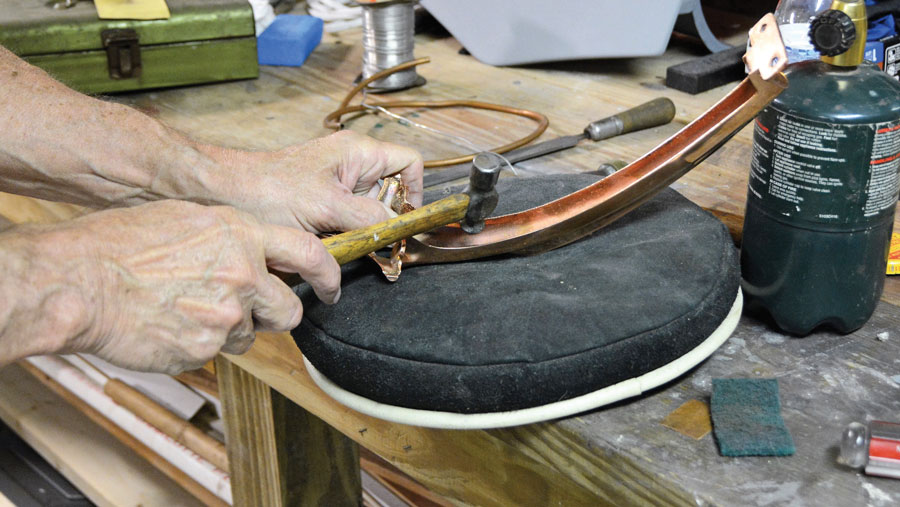
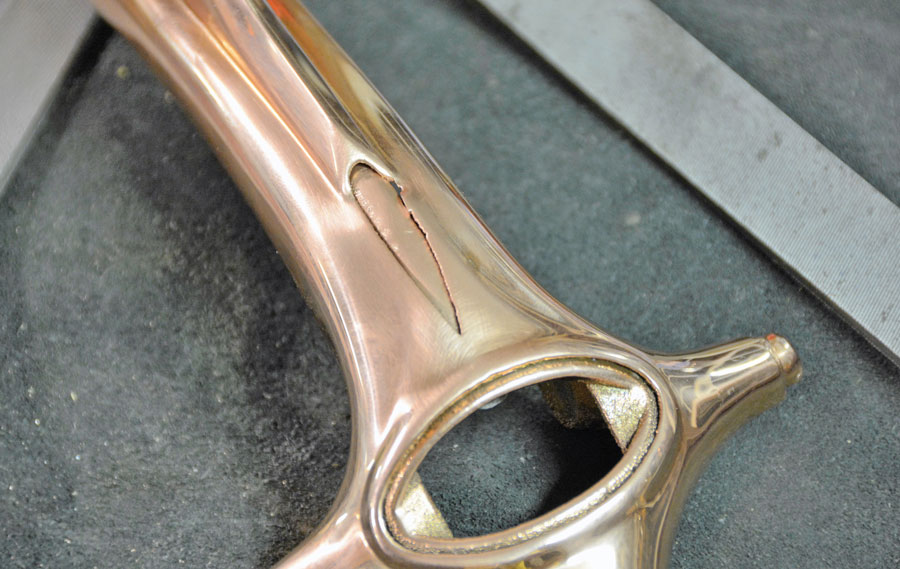
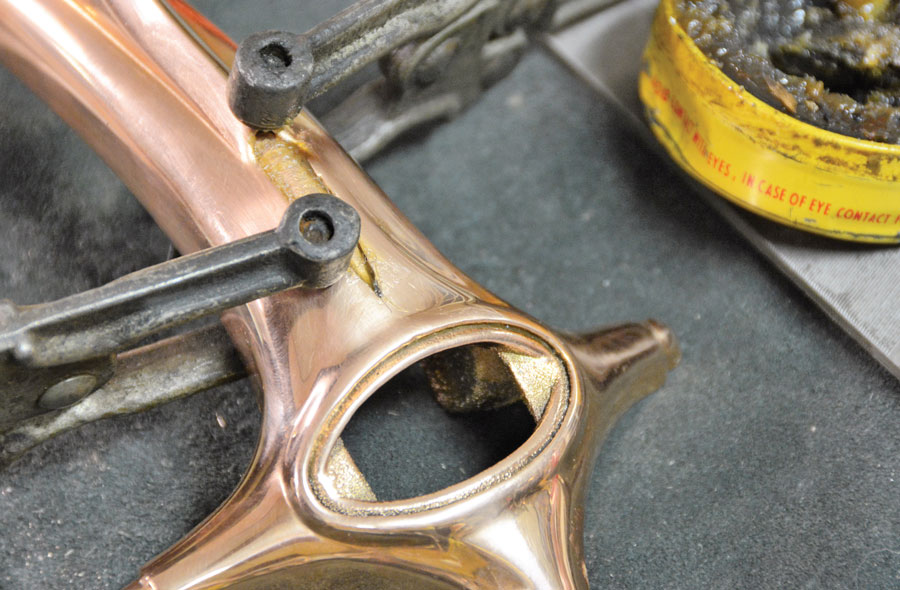

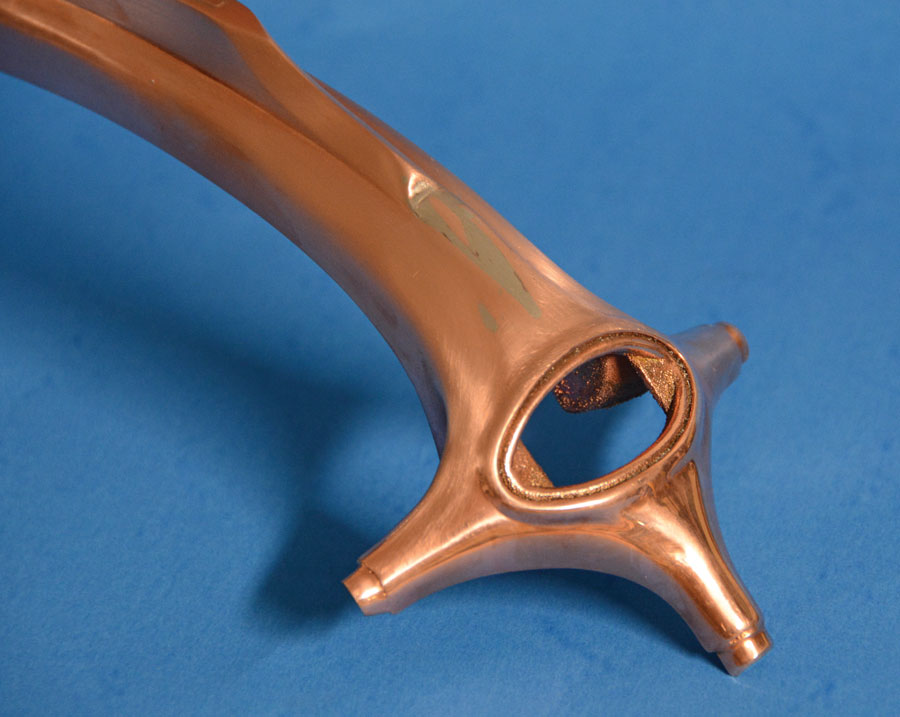
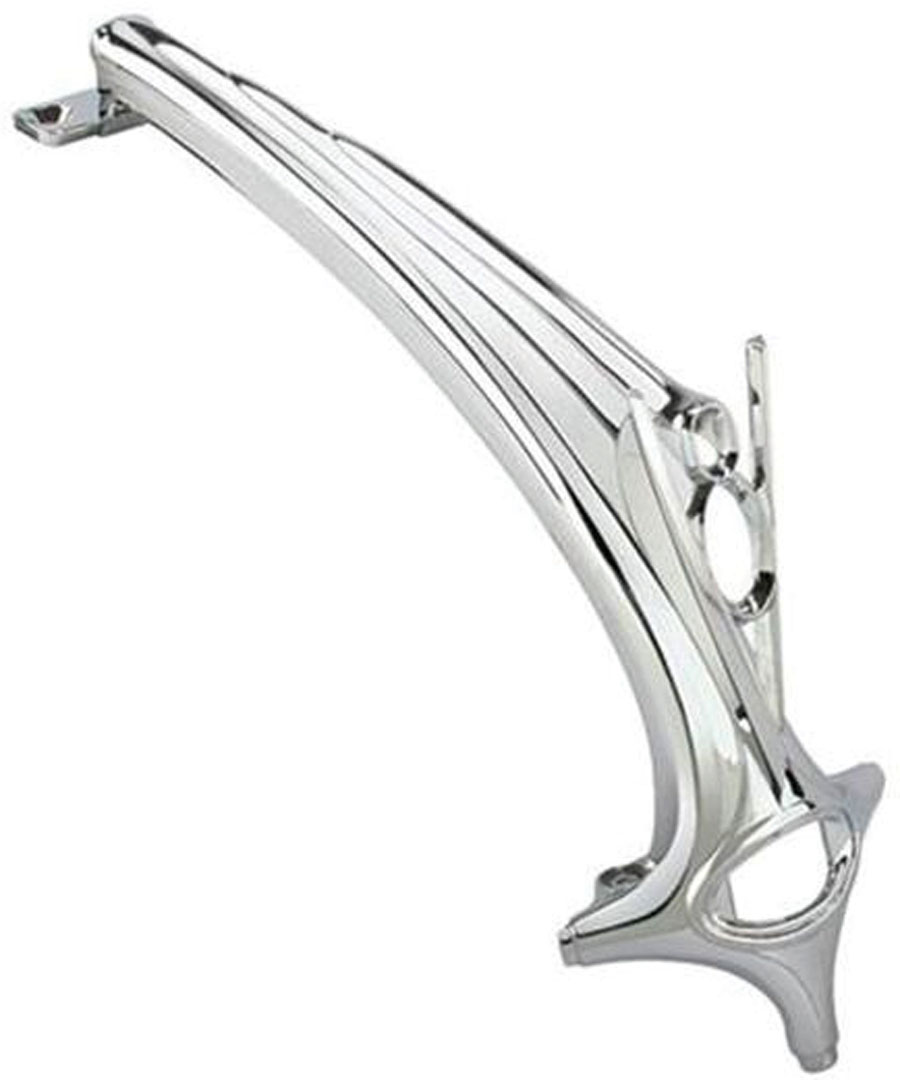
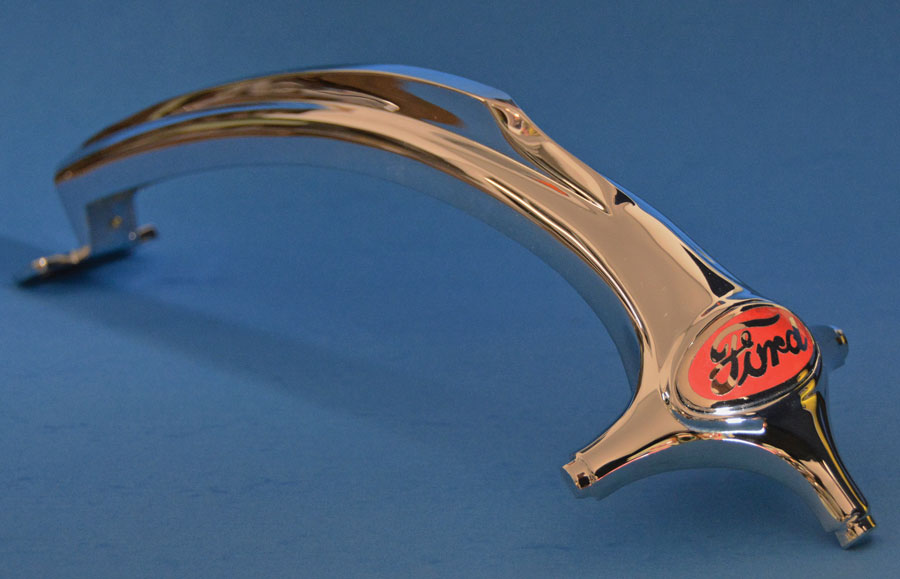

Speedway Motors
(800) 979-0122
www.speedwaymotors.com