
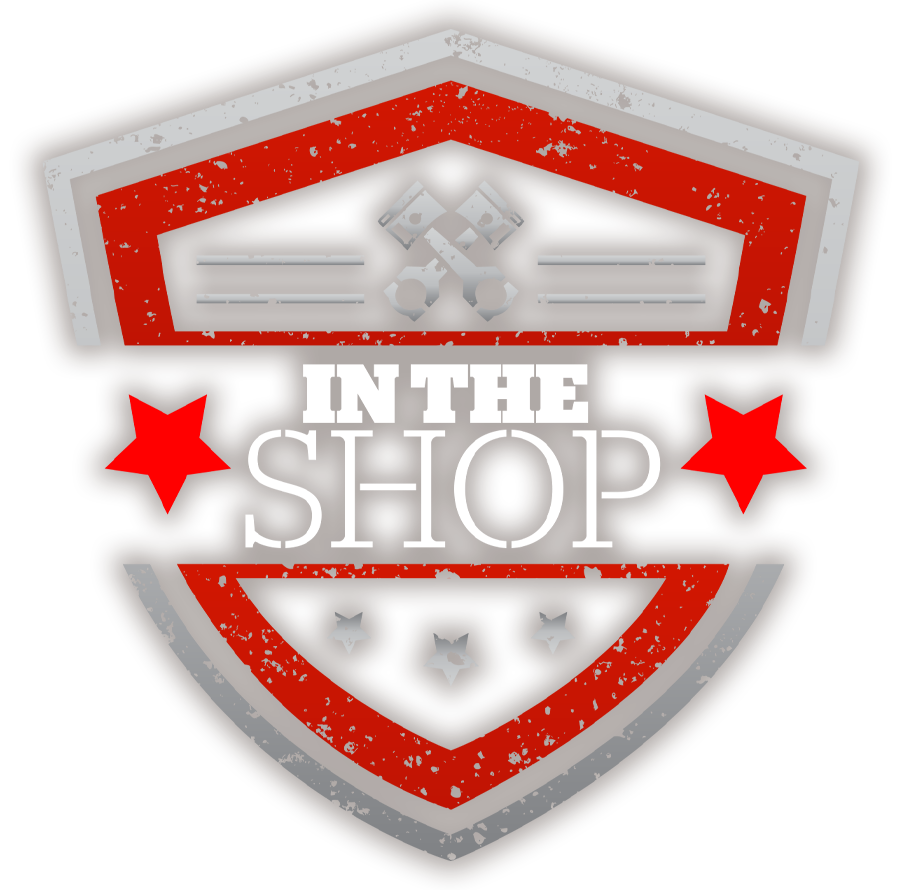
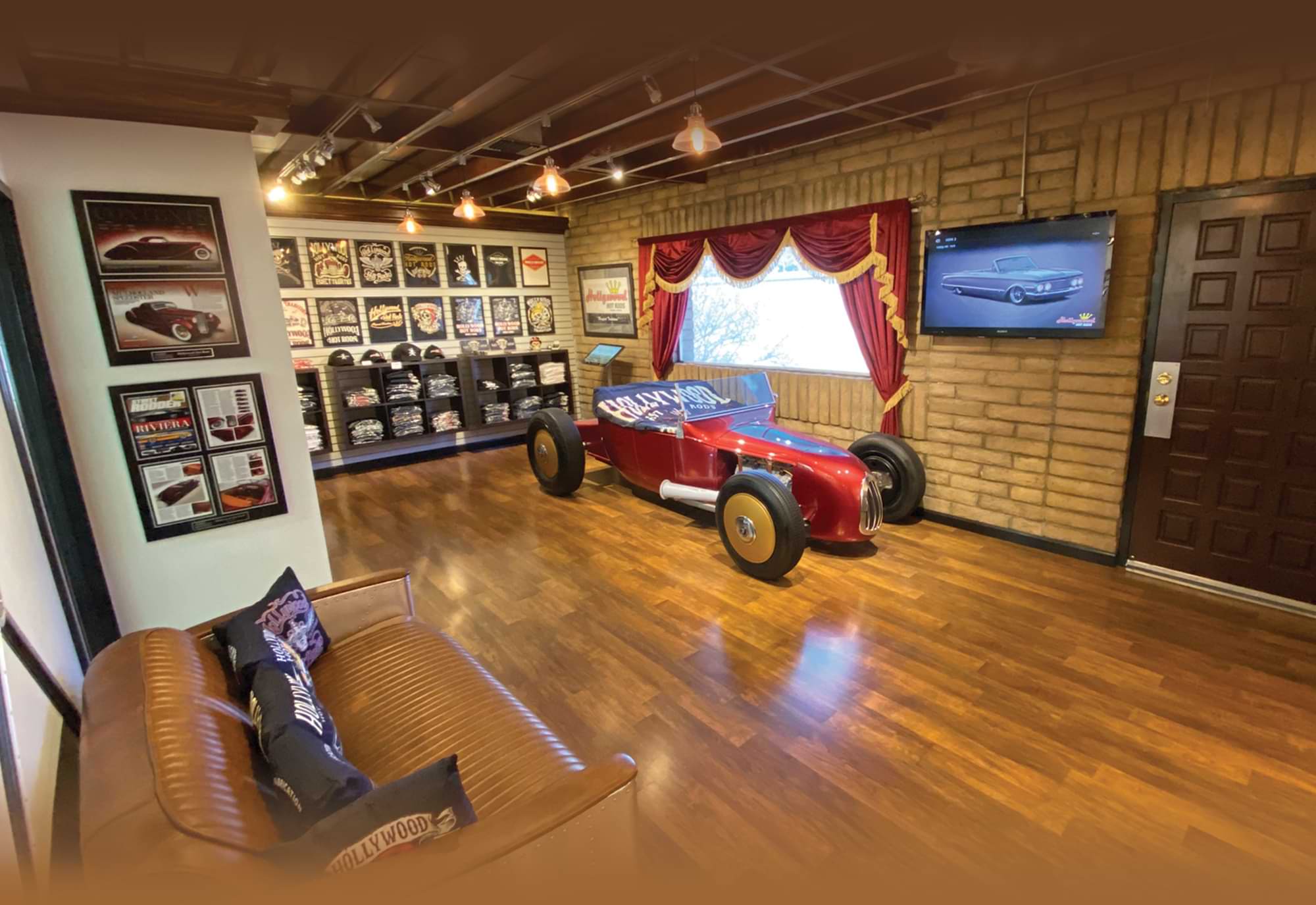


ollywood Hot Rods’ mantra “Respect Tradition” doesn’t mean hot rods the Burbank, California, shop builds have to adhere solely to the way things were once done; to the contrary, it’s a mission statement to guide the future. The handcrafted steel bodies of Hollywood Hot Rods’ creations exude nostalgia with styling cues evoking an era gone by—but focus on the underpinnings and it’s a story of modern upgrades concealed in a traditional-appearing package.
The saga of Hollywood Hot Rods is one that began for Troy Ladd at age 16 when he was given a 1966 Ford Mustang that needed a lot of work. At this point in Troy’s life he wasn’t a gearhead, but that was soon to change. Had Troy’s first car been something along the lines of a stodgy Rambler four-door sedan there might never have been a Hollywood Hot Rods, but fortunately the coolness of owning a V-8–powered Mustang in high school sparked Troy’s interest in cars.
At age 19 Troy knew hardly anything about a 1936 Ford but he bought one because it was “old and cool.” Troy’s engine of choice based on bigger is better was a 400-inch small-block Chevy. Building hot rods was fun but Troy came from a family of scientists and engineers. His grandfather’s work ethic to Troy was get a college degree and take steps up the corporate ladder to establish a lifelong career. Troy took his grandfather’s advice and enrolled at California State University, Fullerton, then transferred to Vanguard University where he completed a bachelor’s degree in business. Troy landed a series of corporate jobs where every move garnered a better position with a higher salary.
Troy’s love for the car hobby never waned and in every spare moment he attended autobody courses at Golden West College and shared a rented garage workspace at the South Pointe apartments with his buddy Chris Shelton. For only $200 a month it was a perfect spot where Troy could wrench on his hot rods at night. Perfect that is until tragedy struck when a neighbor renting an adjacent garage kicked over a candle and started a fire. The two interlopers ran for their lives leaving Troy and Chris to put out the fire. Eviction followed and Troy’s next chapter was renting an industrial unit in Stanton, California, behind Bernt Karlsson’s shop. By now Troy had built over half a dozen cars and was well versed in every phase of constructing a hot rod. In 2002 his girlfriend convinced him he should quit his corporate job and open a hot rod shop.
In 2017 Troy bought an industrial building with all the right elements to conduct an automotive business and moved Hollywood Hot Rods 1 mile away from its original location. The move shaped Hollywood Hot Rods’ operation into a perfect working environment. Troy said with a five-man staff of craftsmen that sometimes grows to seven, he will never want to expand his staff further or increase his shop’s overhead.
Flashing back in time it was Troy’s 1936 Ford that gave him his first taste of magazine exposure when it appeared in Street Rodder’s Jan. ’91 issue with event coverage of the 1990 Labor Day Cruise at the Orange County Fairgrounds. That was all it took; now Troy was really hooked on the hot rod lifestyle. Troy told us reading the tech articles in Street Rodder was how he learned volumes about how to build a car. Troy and Hollywood Hot Rods’ relationship with Street Rodder grew exponentially with years to follow of car features, tech articles, and ultimately constructing three iconic cars to lead Street Rodder’s annual Road Tour for 2012, 2015, and 2019.
The number count of hot rods and custom cars that have entered and left Hollywood Hot Rods’ portals likely exceeds 100. The known number of builds includes the “Mulholland Speedster” 1936 Custom Coach–built Packard, the “Long Beach Legend” 1936 Ford roadster, “Full Metal Jacket” 2014 Ford Mustang GT convertible, the Street Rodder Road Tour 1940 Ford Coupe, the “Zulu T” 1927 Ford Tall Model T coupe, the “Brooklands Special” 1932 Ford roadster, Coyote Comet convertible, the Raybestos Coyote-powered 1932 Ford roadster pickup, the “Platinum Bomb” 1932 Ford roadster, “Ruby Deluxe” 1935 Ford coupe, “El Correcaminos” 1931 Ford roadster pickup, the “Black Widow” 1926 Ford roadster pickup, and the “Respect Tradition” Hemi-powered 1932 Ford roadster.
Future builds for Hollywood Hot Rods includes a 1965 Chevelle convertible coming in for a full electric- powered conversion with instructions to incorporate regenerative braking, neck-snapping performance, the latest developments in EV efficiencies, and, of course, styled with the utmost respect for tradition.

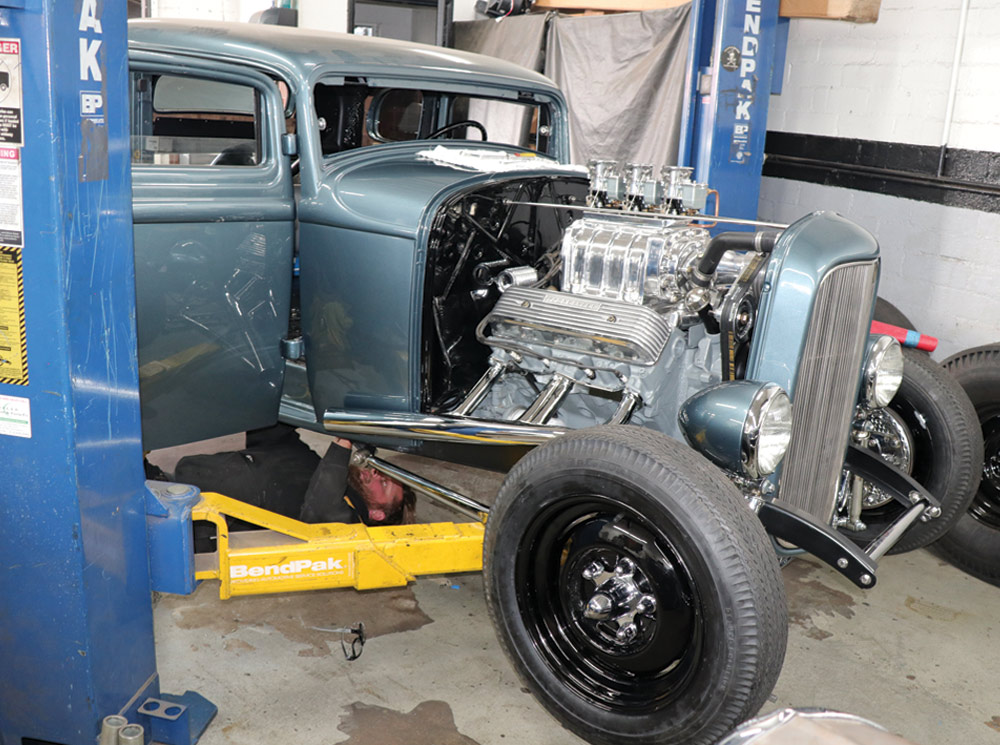
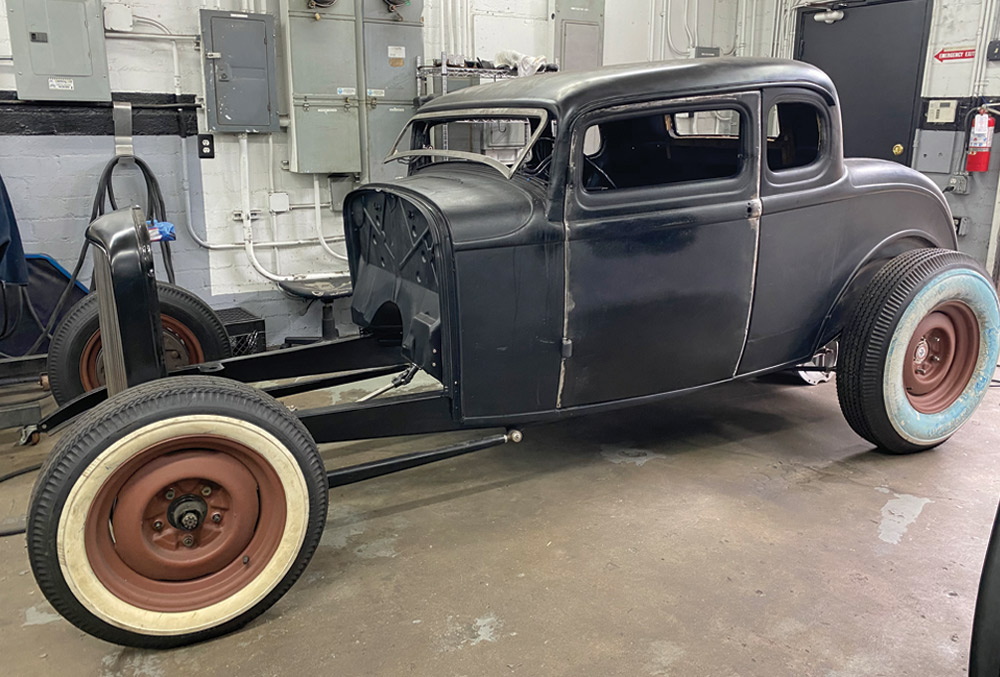
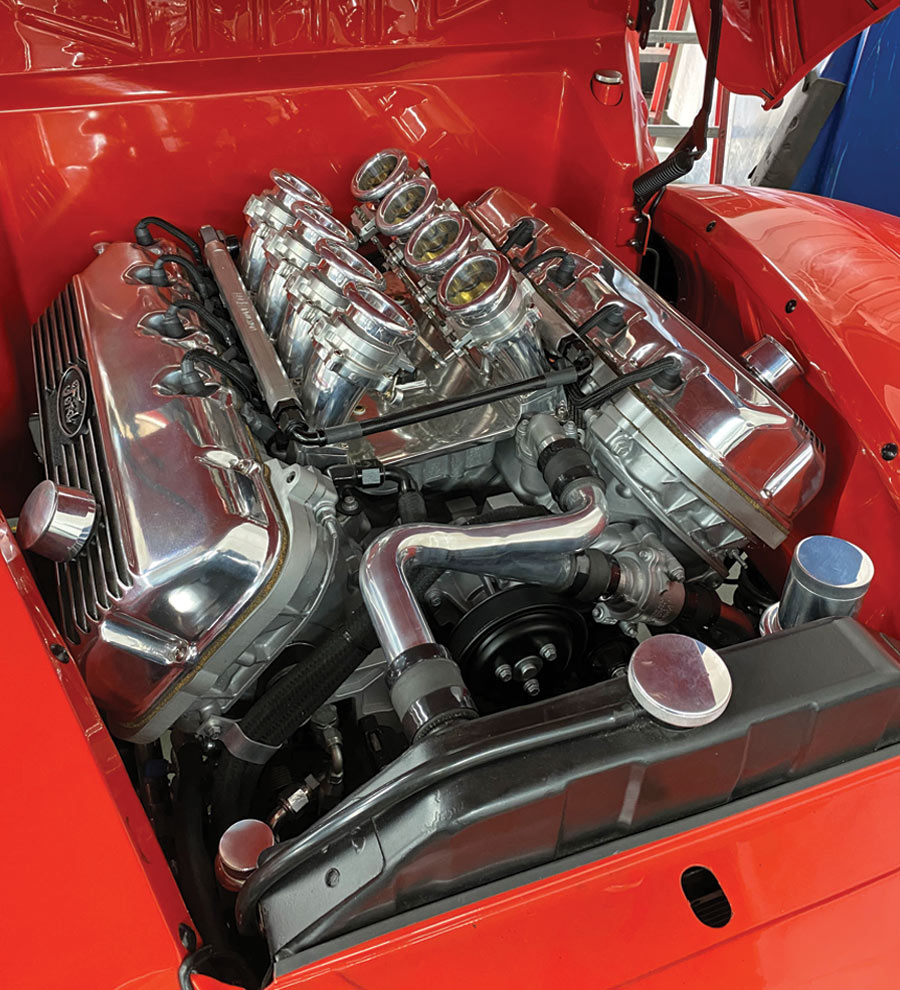

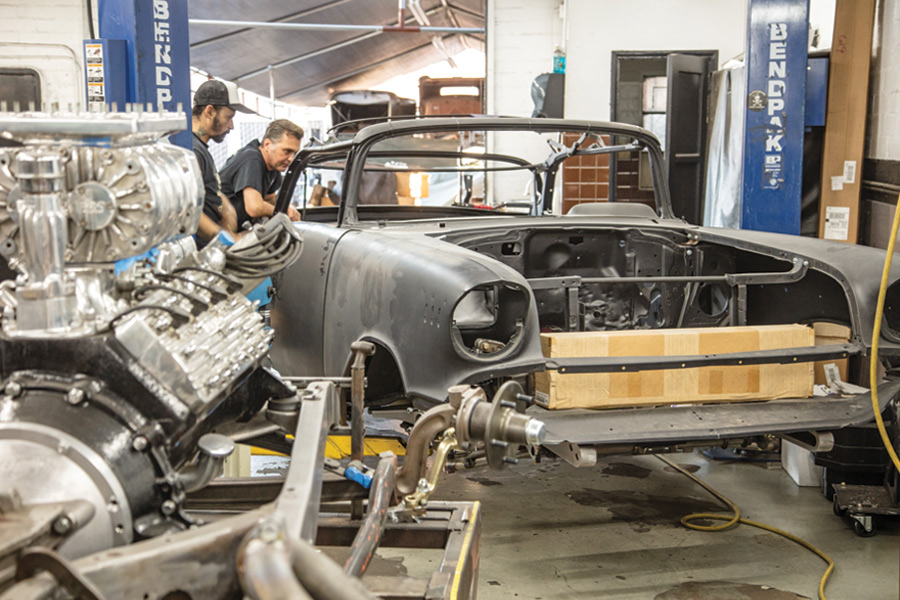
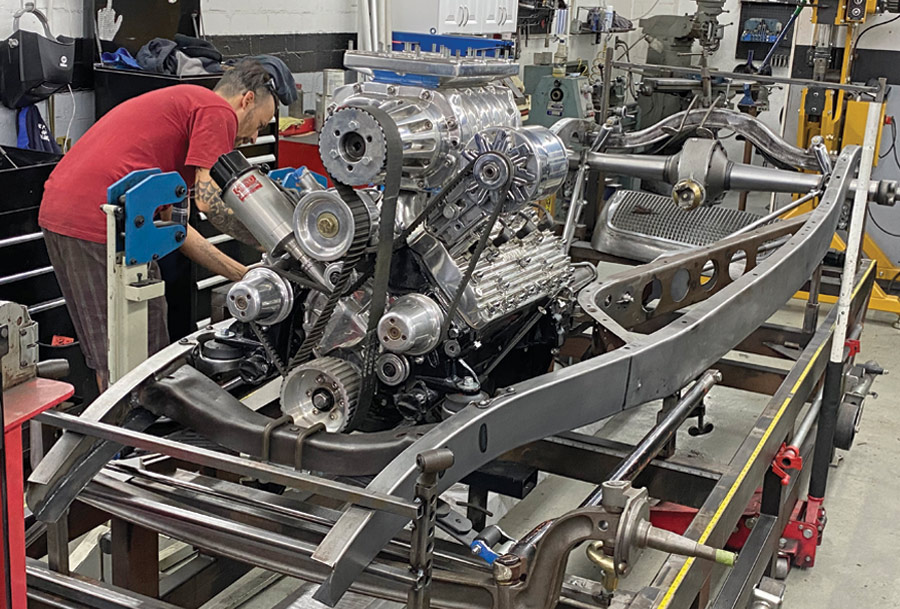
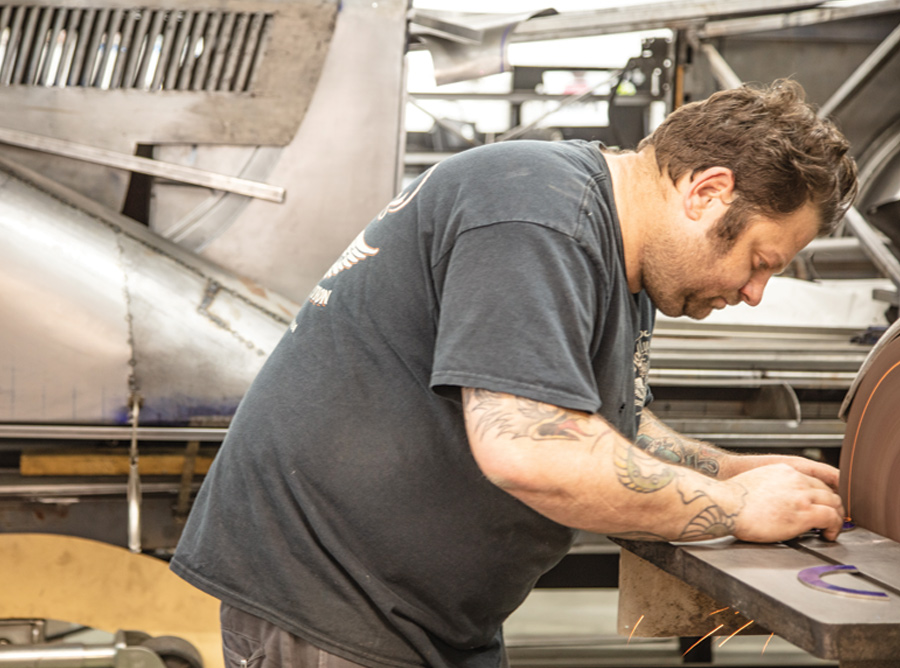
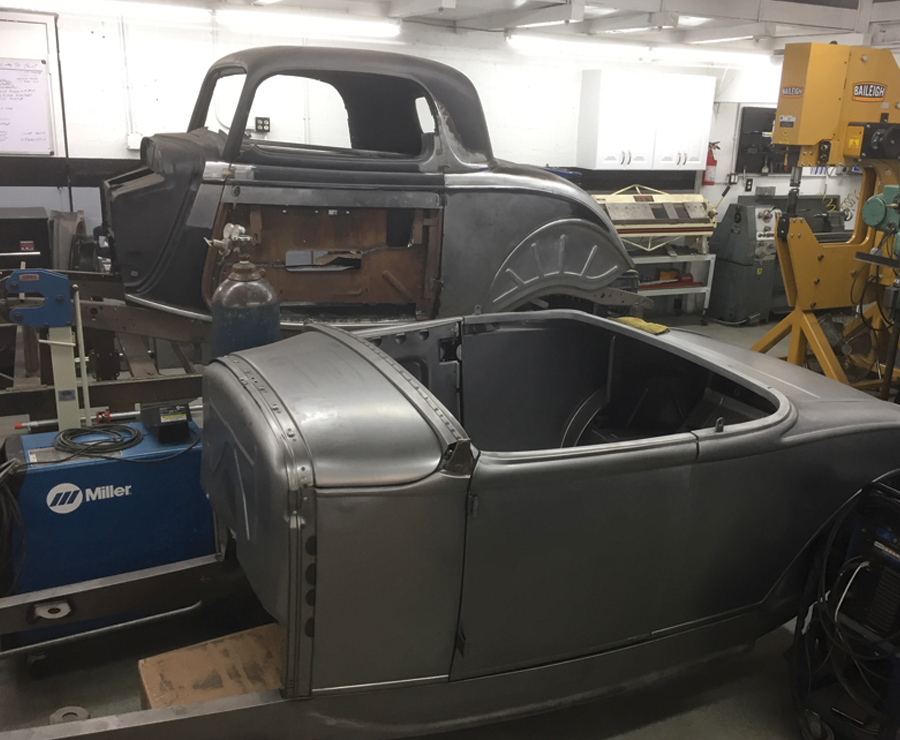
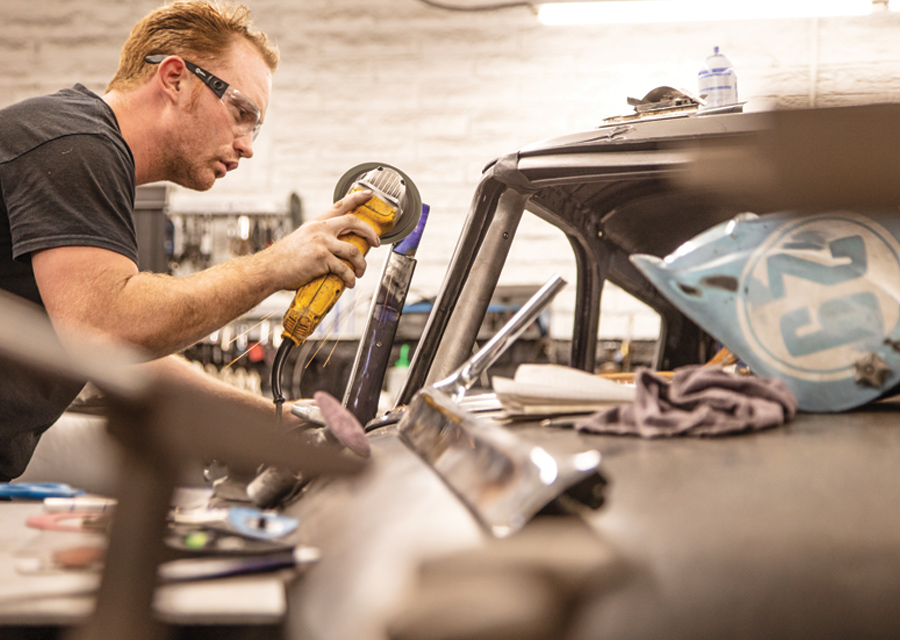
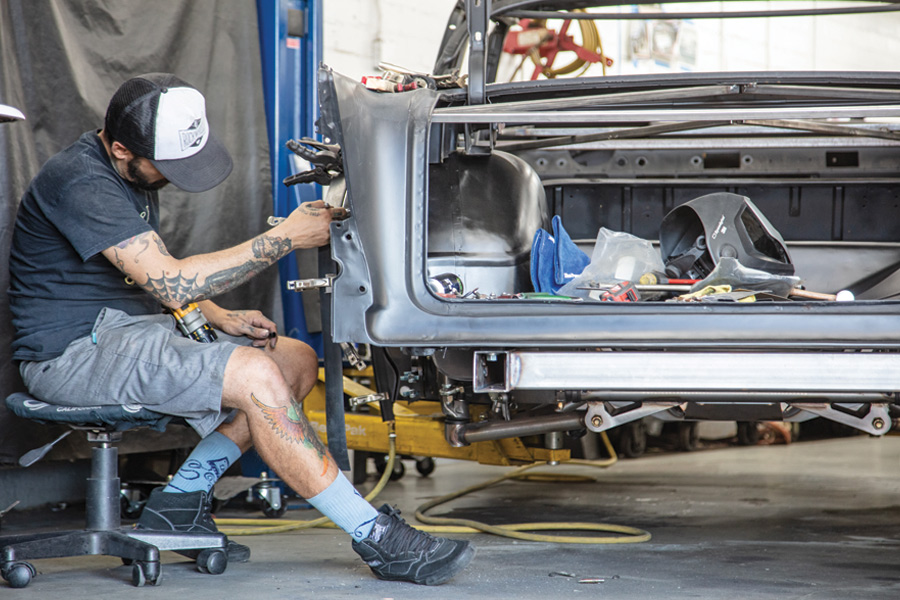
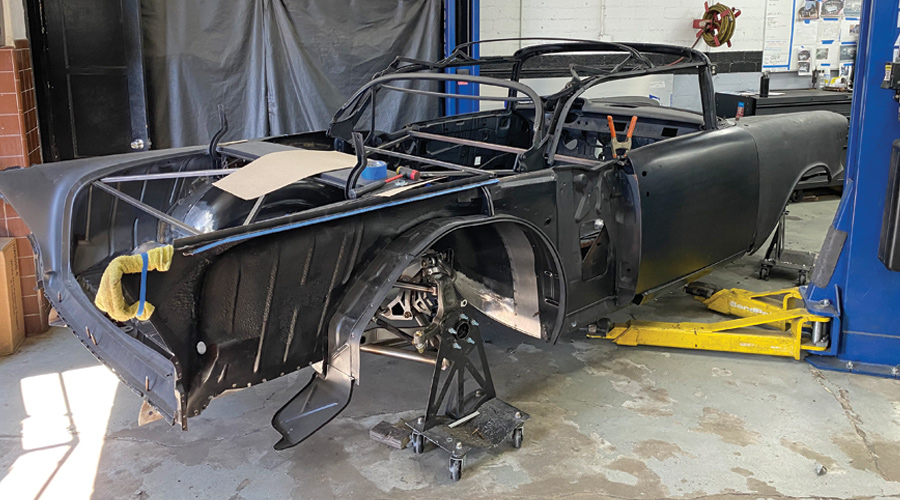
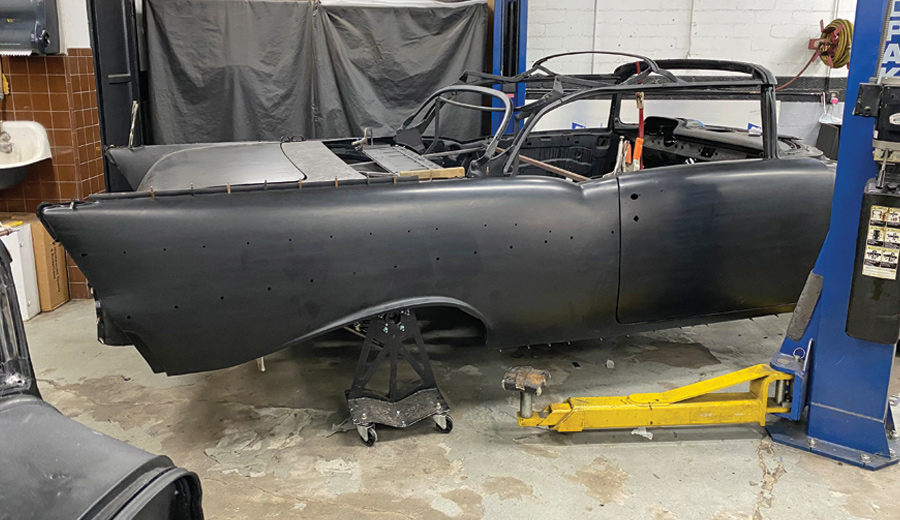
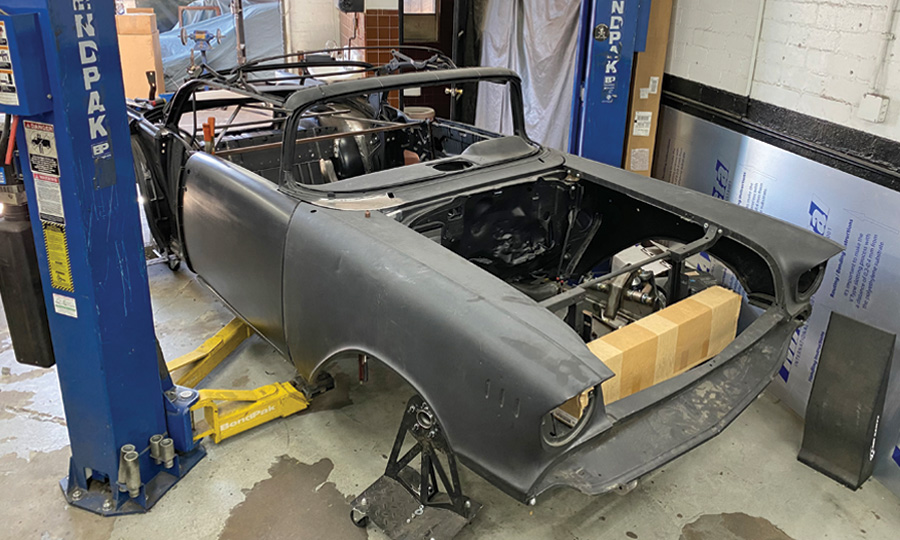
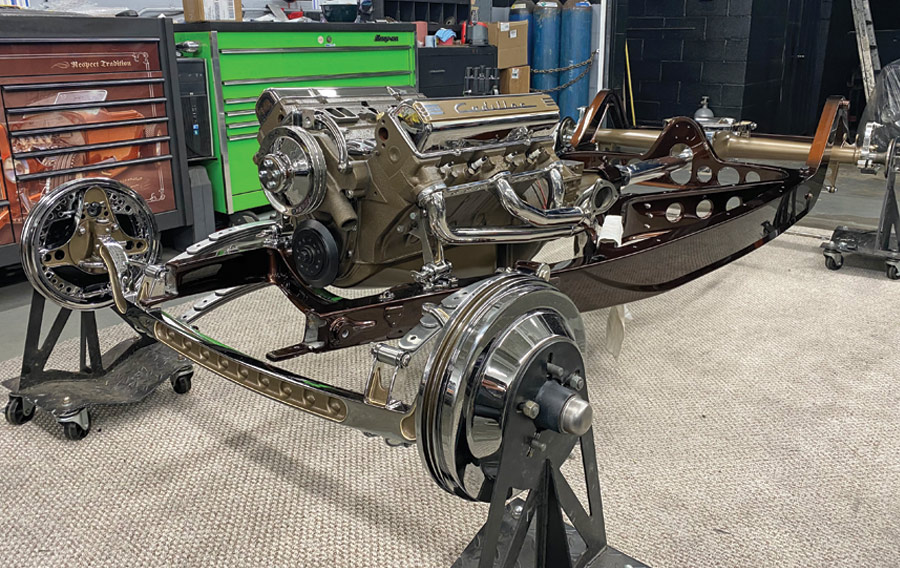
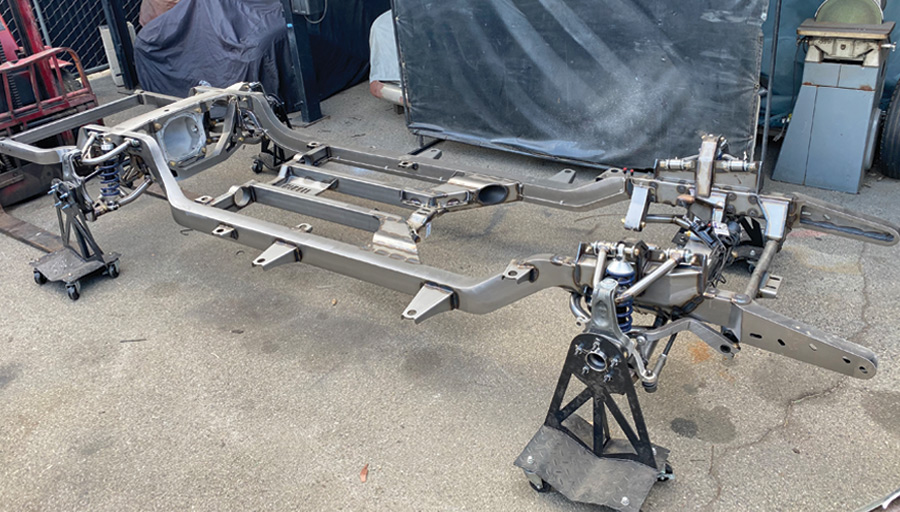
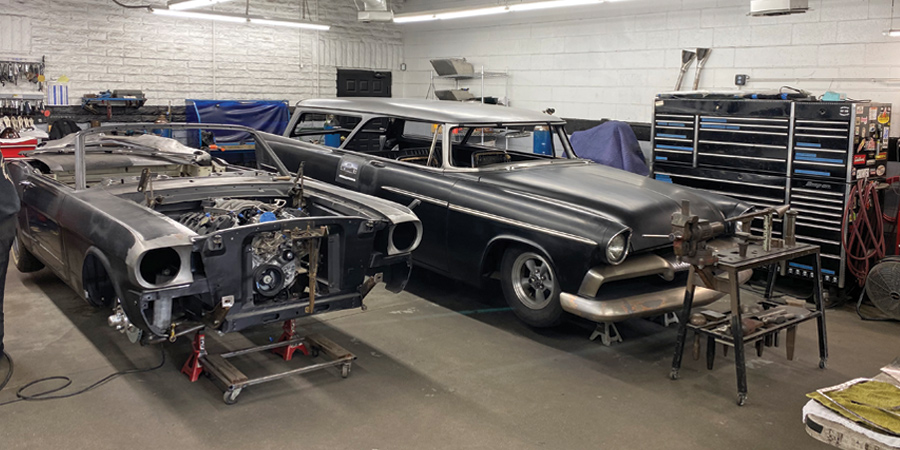
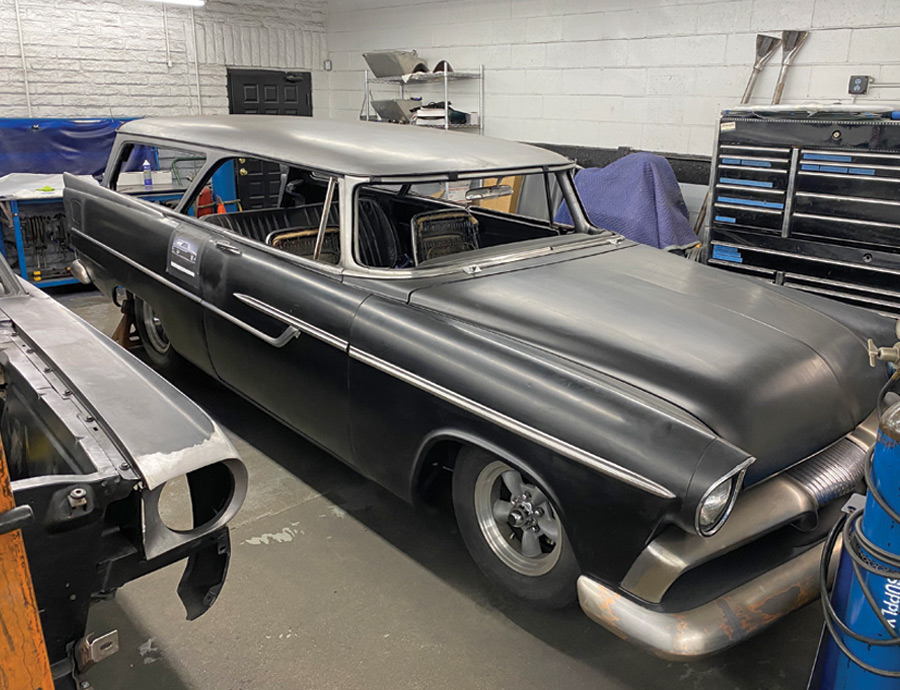

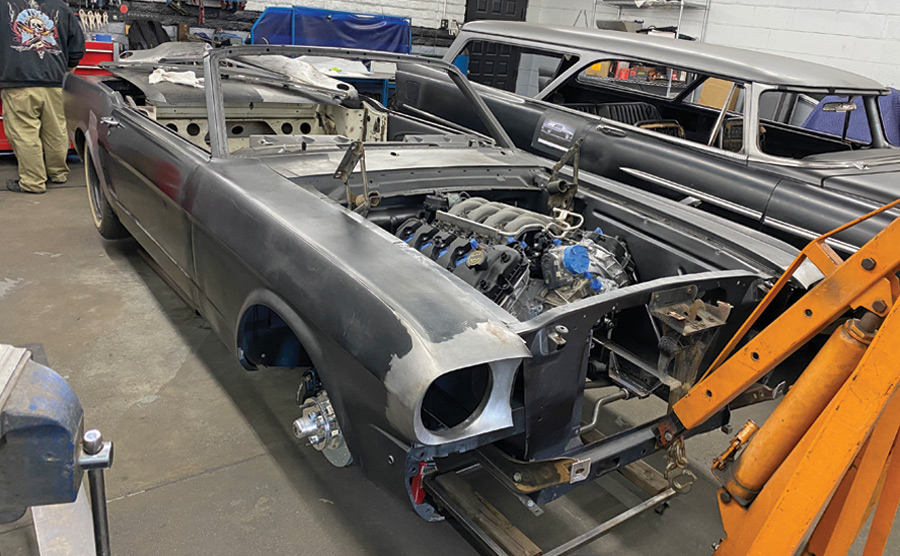
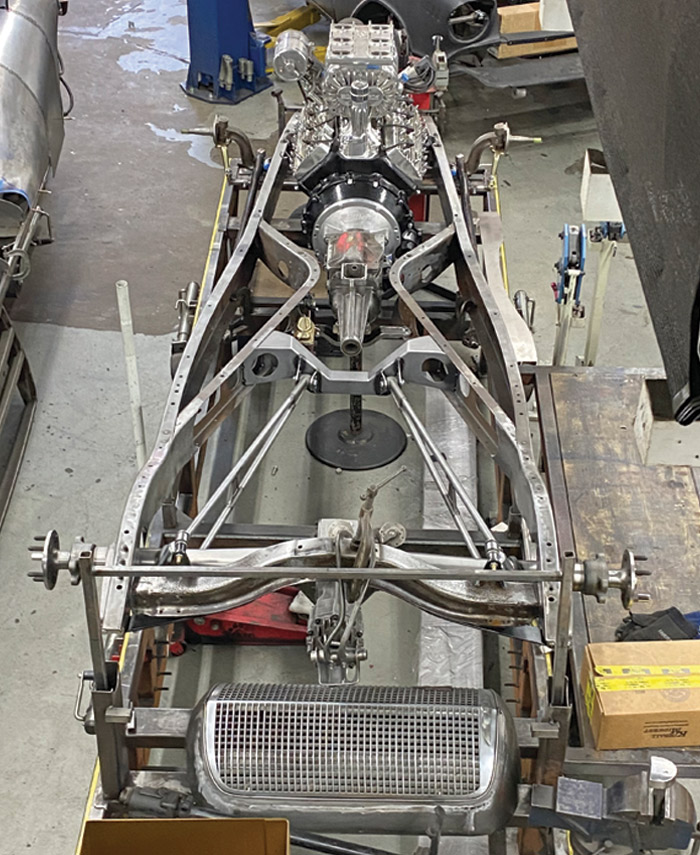
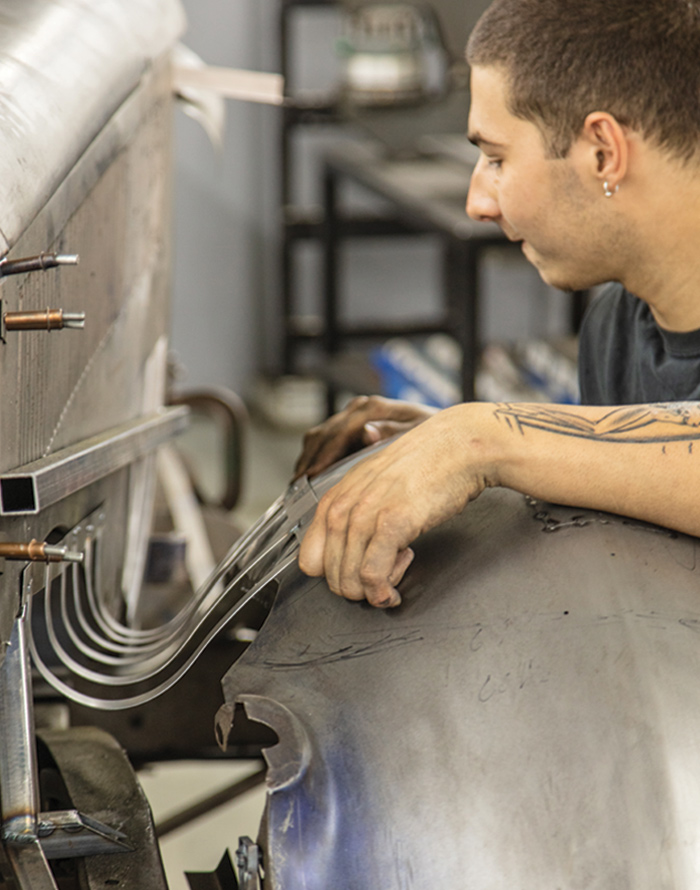
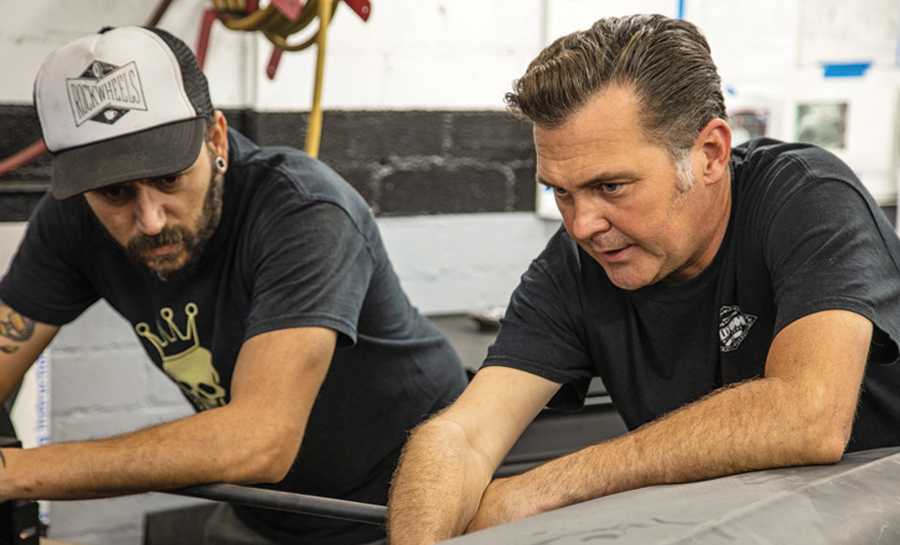
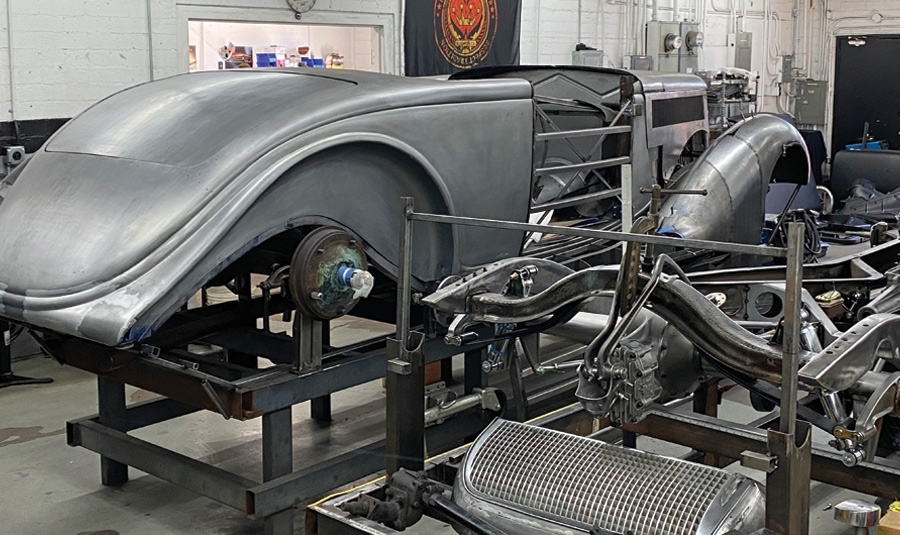

HOLLYWOOD HOT RODS
(818) 842-6900
hollywoodhotrods.com